导读: 在韧性断裂界,最令人困惑的争议之一是在剪切主导加载过程中,预测的应变-破坏值与实验观察到的应变-破坏值之间存在很大差异。目前提出的解决方案侧重于更好地解释偏应力状态如何影响空洞生长,或者侧重于在微观尺度而不是宏观尺度上测量应变。虽然这些方法是有用的,但它们并没有解决问题的一个重要方面:通常考虑的唯一断裂微机制是空洞成核、生长和聚并(对于拉伸主导加载),以及剪切局部化和空洞聚并(对于剪切主导加载)。因此,当前的现象学模型侧重于基于材料的应力状态和应变硬化能力来预测这些机制之间的竞争。通过对铜、镍和铝这三种具有中高层错能的高纯度面心立方(FCC)金属的断裂过程进行表征,解决了这些问题。对于给定的应力状态和材料,几种机制经常以顺序的方式共同作用,导致断裂。破坏机制的选择在很大程度上受到撕裂开始前发生的塑性诱导的微观结构演变的影响,这可能会产生或消除空隙成核的场所。在宏观尺度上,观察到不涉及破裂或孔隙生长的破坏机制有助于随后的孔隙生长和聚并过程。虽然本研究的重点是纯金属的损伤积累,但这些结果也适用于理解工程合金的失效。
随着20世纪断裂力学的出现,许多断裂问题变得相对容易预测。目前,基于线弹性断裂力学和弹塑性断裂力学的概念被广泛用于预测韧性金属的破坏。此外,许多基本问题,如拉伸和剪切主导载荷之间延性的相对差异,仍然没有答案。在这种情况下,本研究的目的是研究韧性断裂的机制和控制它们的因素。
在目前的研究中,我们提出骨折通常是由多种机制的顺序发展控制的。此外,我们假设这些机制不仅相互竞争,而且可以相互促进。一个经典的,但经常被忽视的例子是结构金属的杯锥破坏。大多数拉伸杆的断口表面既表现为中心平坦的“纤维”韧性韧窝区,又表现为向外围剪切唇区明显的过渡。
为了验证这些假设,Philip J. Noell团队采用中断变形实验和各种表征方法表征了高纯铜、镍和铝的断裂过程。这三种材料都是面心立方(FCC),在准静态、室温变形时通过滑移变形,表明并非所有FCC金属失效的机制相同。选择了两种应变硬化能力截然不同的材料(铜和镍)。选取高纯铝,研究动态再结晶对断裂过程的影响。在纯度为99.99%或更高的样品的室温变形过程中,该材料观察到动态再结晶[60e62]。本研究的重点是这三种材料的片材试样在单轴拉伸下的破坏,但也对每种材料的丝材试样的断口表面进行了表征,以了解各向同性约束状态下的损伤进展。
虽然这项研究仅限于高纯度金属,但这些结果也与含有第二相颗粒的金属有关。在纯金属中,空洞在晶界和变形引起的位错界等部位成核,而在大多数工程材料中,第二相颗粒是主要的空洞成核部位。第二相颗粒可能会加速空洞成核过程,并且在许多材料中都支持基于空洞的破坏机制。因此,纯金属的破坏过程比在大多数工程材料中观察到的更广泛的破坏机制,同时提供了关于基于空洞的破坏机制之间竞争的信息。
相关研究成果以“The mechanisms of ductile rupture”发表在Acta Materialia上
链接:https://doi.org/10.1016/j.actamat.2018.09.006
图1(A)给出了Al 2024-T351试样在不同应力三轴性(σm/σe)下的断裂应变图。
(b)中的图像显示了矩形Ti-6Al-4V试样的拉伸断裂面示例,该试样在第二次Sandia断裂挑战中进行了单轴拉伸测试。在许多大块金属中,有两种明显而典型的机制:一个扁平的纤维带,通常与空洞成核、生长和聚并有关,另一个是外围剪切唇。
在应力三轴性约为1/3时,他们观察到破坏应变随着应力三轴性的减小而减小,在纯剪切条件下达到最小值(应力三轴性为0),在负应力三轴性下迅速增加。这种关系如图1 (a)所示。随后的几项研究报道了破坏应变与应力三轴性之间的类似关系[17e19]。因此,建立了剪切修正的Gurson、Mohr-Coulomb和其他[13,23e26]模型来捕捉剪切主导荷载的影响
图2 7种不同宏观韧性断裂机制的示意图如下:(a)空隙缩缩,(b)空隙剪切,(c)空隙片状,
(d) Orowan交替滑移(OAS)机制,(e)缩缩至某一点导致试样分离,
(f)和(g)分别显示了单平面和多平面突变剪切导致试样分离。文中提供了每种机制的详细定义。
图3给出了由(a)空隙缩缩、(b)空隙剪切、(c)空隙片化、(d) OAS机制、(e)缩缩至某一点、
(f)单平面突变剪切和(g)多平面突变剪切控制试样的断裂过程的SEM图像。
表1提供了本研究测试材料的参考列表。对于每种材料,列出了线径或片厚,以及与之相关的数字。如果在材料中观察到夹杂物,则报告这些夹杂物的平均直径。描述了七种不同的材料:一种铝线材料、两种铝片材料、一种铜线材料、一种铜片材料、一种镍线材料和一种镍片材料。
图4工程应力与工程应变数据表明,5N-Al、3N-Cu和4N-Ni片材的流动行为存在显著差异。原理图显示了板材拉伸试样的方向。这些工程应变数据是用立体DIC测量的。在3N-Cu拉伸试样的图像上显示了一个示例DIC数据集。在这种情况下,当流动应力降至极限拉应力(UTS)的30%时,拉伸变形被中断。
在0.127 mm/s的恒定位移速率下,采用位移控制对板材拉伸试样进行试验。图4给出了3N-Cu、4N-Ni和5N-Al片材拉伸试验的典型工程应力与工程应变数据。应变测量采用立体数字图像相关(DIC),使用子集尺寸为35像素,步长为9像素,长度为2.35 mm的数字应变片。根据零负荷基线实验,DIC延伸计测量噪声水平为±0.004%。用于这些应变测量的延伸计如图4所示,其中包含3N-Cu拉伸试样的DIC数据。该图还显示了板材拉伸试样的三个主轴:拉伸方向(TD)、长横向(LTD)和短横向(STD)。在所有情况下,STD都平行于原始薄片的厚度方向。
表2提供了对5N-Al、3NCu和4N-Ni片材进行的中断拉伸试验摘要。两个5N-Al板材材料的拉伸试样在10%的UTS处中断。
表3总结了每种材料在损伤积累过程中控制断裂的机制和相应的应力三轴性。OAS机制是指通过交替滑移过程形成空腔;通过OAS机制未观察到孔洞成核。高局部应力三轴性定义为1/3(单轴拉力)或更大,例如,在剪切带形成之前颈规区域的应力状态。低局部应力三轴性定义为介于0到1/3之间(剪切和拉伸混合),例如在剪切带形成后颈规区域的应力状态。
图5(a)铝、(b)铜、(c)镍三种高纯度导线的断口表面。
对于每种材料,提供以下(从左到右):断裂面横截面的电子通道对比(ECC)图像,断裂面的二次电子图像(与断裂面垂直),以及断裂面的说明性草图。这些图像突出了这三种金属丝材料断口表面的显著差异。
图6给出了两种不同高纯铝材料的断裂过程。
如图(a)和(c)所示,多晶5N-Al材料因间隙颈缩而失效。
如图(b)所示,动态再结晶(DRX)在5N-Al片材中产生了新的无应变晶粒。
如图(d)和(e)所示,低晶4N-Al材料因缩颈到一点而失效。
图7 3N-Cu薄片材料的断裂过程用六个不同试样的中间截面图像来说明,
这些试样在(a) 60%, (b) 55%, (c) 50%, (d) 40%, (e) 30%和(f) 5%的UTS处中断。
覆盖在每张图像上的草图突出了断裂过程中此时的主要断裂机制:
(a)扩散颈中的间隙颈缩导致的空洞成核和生长,(b)剪切带中空洞片形成的新空洞成核,
(c)到(e)空洞片形成的空洞合并,以及(f) OAS机制导致该材料的最终断裂。
图8提供了图7(c)所示的腔体的高倍图像。作为参考,在图7(c)中标记了(a)和(b)所示的区域。(a)中的图像突出显示了合并形成空腔的空腔两侧的拉伸空洞。
(b)中的二次电子图像是在样品的STD倾斜后拍摄的,显示这些拉伸空洞通过空洞片聚集在一起。这可以从空腔两侧的一排排剪切凹陷中得到证明。
图9破裂的3N-Cu薄片试样的宏观断口图如图(A)所示。
(b)和(c)中的图像是(A)中突出显示的区域的高倍图像。
这些图像显示,断裂表面的中心覆盖着拉伸韧窝,韧带覆盖着剪切韧窝。然而,该断口的倾斜边缘基本上是无韧窝的,这表明中心空腔是由OAS机制形成的。
图10 4N-Ni片材的断裂过程使用四个不同试样的中间截面图像来说明,
这些试样在(a) 50%, (b) 25%, (c) 20%和(d) 10%的UTS处中断。
叠加在每张图像上的草图突出了断裂过程中此时的主要断裂机制:
(a)宏观剪切带的形成,
(b)材料的两半相互剪切,通过与(a)中的图像进行比较可以看到,剪切带中空洞的成核,随后这些小空洞聚并导致(c)通过间隙剪切形成中心空洞,
(d)通过OAS机制形成该空洞。从这些图像来看,从单面突变剪切到间隙剪切的转变似乎是突然发生的,尽管突变剪切过程可能是通过沿剪切轴延长空洞而使空洞合并的。
图11提供了如图10(c)所示的空腔内部的二次电子图像。这些图像是在标本倾斜STD后拍摄的,以便对腔体内部进行成像。这些图像突出显示了空洞边缘的部分,这些部分要么被剪切凹陷覆盖,要么没有凹陷。
图12(A)是4N-Ni片试样破裂的宏观断口图。
(b)和(c)中的图像是(A)中高亮显示区域的高倍图像。
这些图像显示,断口表面的中心覆盖着近似平行的韧窝,而边缘基本上没有韧窝。
图13给出了镍和铜的空隙体积分数(VNv)与von Mises应力(s)的关系图。
由于铜具有比镍大得多的应变硬化能力,对于给定的von Mises应力,铜中空隙间剪切所需的空隙体积分数明显大于镍。
图14给出了断裂机理图的两个概念性例子。
(a)中的图大致基于在4N-Ni材料中观察到的破坏顺序,4N-Ni材料具有高的空穴成核阻力和低的空穴生长阻力。
(b)中的图显示了材料失效过程的一个例子,其中空洞成核几乎完全被抑制,例如本研究中使用的5N-Al丝材料。
本研究通过表征高纯铝、镍和铜的断裂,研究了这些不同破坏机制之间的相互作用,探究了这些材料从扩散颈形成到最终试样分离的整个破坏过程。主要成果如下:
(1)失效过程经常涉及到若干机制的连续发展。当这种情况发生时,一种失效机制通常会促进随后出现的机制。
(2)在破坏前的变形过程中发生的微观组织演变可以消除或产生材料中的空洞形核位点。这可以显著影响不同失效机制之间的竞争。
(3)间隙剪切与空隙板的竞争取决于应变硬化能力,低应变硬化能力有利于间隙剪切,高应变硬化能力有利于空隙板。
(4)据推测,在剪切主导载荷下,应变到破坏的差异不仅是由于应变测量的空间分辨率和破坏定义的差异,而且还由于特定材料/条件下主导机制的差异以及可能导致破坏的多种机制的代表性不足。
免责声明:本网站所转载的文字、图片与视频资料版权归原创作者所有,如果涉及侵权,请第一时间联系本网删除。
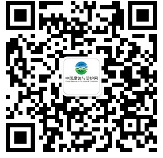
官方微信
《腐蚀与防护网电子期刊》征订启事
- 投稿联系:编辑部
- 电话:010-62316606
- 邮箱:fsfhzy666@163.com
- 腐蚀与防护网官方QQ群:140808414