淬火获得马氏体组织,是钢件达到强韧化的重要基础。由于钢的种类、成分不同,以及热处理条件的差异,会使淬火马氏体的形态和内部精细结构及形成显微裂纹的倾向性等发生很大变化。这些变化对马氏体的机械性能影响很大。因此,掌握马氏体组织形态特征并进而了解影响马氏体形态的各种因素是十分重要的。
1 马氏体的形态
通过薄膜透射电子显微技术,人们对马氏体的形态及其精细结构进行了详细的研究,发现钢中马氏体形态虽然多种多样,但就其特征而言,大体上可分为以下几类:
1 板条状马氏体
板条状马氏体是低、中碳钢,马氏体时效钢,不锈钢等铁系合金中形成的一种典型的马氏体组织。低碳钢中的典型组织如图1所示。
图1 低碳合金钢(0.03%C,2%Mn)的板条状马氏体100X
因其显微组织是由许多成群的板条组成,故称为板条状马氏体。对某些钢因板条不易浸蚀显现出来,而往往呈现为块状,所以有时也称之为块状马氏体。又因为这种马氏体的亚结构主要为位错,通常也称它为位错型马氏体。这种马氏体是由若干个板条群组成的,也有群集状马氏体之称。每板条群是由若干个尺寸大致相同的板条所组成,这些板条成大致平行且方向一定的排列。从图2看出板条状马氏体的特征为板条内有密度很高的位错。
图2 低碳合金钢(0.03%C,2%Mn)的薄膜透射显微组织 20000X
此外,在板条内有时存在着相变孪晶,但只是局部的,数量不多,不是主要的精细结构形式。板条状马氏体与母相奥氏体的晶体学位向关系是K-S关系,惯习面为(111)γ,而18-8不锈钢中的板条状马氏体的惯习面是(225)γ。
根据研究,板条状马氏体显微组织的晶体学特征可以用图3表示。
图3 板条状马氏体显微组织的晶体学特征示意图
其中A是由平行排列的板条状马氏体束组成的较大的区域,称为板条群。一个原始奥氏体晶粒可以包含几个板条群(通常为3~5个)。在一个板条群内又可分成几个平行的像图中B那样的区域。当用某些溶液腐蚀时,此区域有时仅显现出板条群的边界,而使显微组织呈现为块状,块状马氏体即由此而得名。当采用着色浸蚀时(如用100ccHCl+5g CaCl2+100ccCH3CH溶液),可在板条群内显现出黑白色调。同一色调区是由相同位向的马氏体板条组成的,称其为同位向束。按照K-S位向关系,马氏体在母相奥氏体中可以有24个不同取向,其中能平行生成板条状马氏体的位向有六种(见图4)。
图4 钢中马氏体(111)γ面上形成时可能有的取向
而一个同位向束就是由其中的一种位向转变而来的板条束。数个平行的同位向束即组成一个板条群。有人认为,在一个板条群内,只可能按两组可能位向转变。因此,一个板条群是由两组同位向板条束交替组成,这两组同位向束之间可以大角晶界相间。但也有一个板条群大体上由一种同位向束构成的情况,如图3中C所示。而一个同位向束又由平行排列的板条组成,如图3中D所示。这种情况可以用电镜观察到,如图5所示。
图5 Fe-0.2%C合金中板条状马氏体同位向束内的一部分组织(透射电子显微照片)
根据Fe-0.2%C合金中的研究结果,板条宽度分布为图6 所示的对数正态分布。
图6 薄膜和复型技术的板条状分布
由图中可见,出现频率最大的板条宽度为0.15~0.20μm,并且分布曲线非常偏向于小尺寸板条一边,但也有一小部分的板条宽度达到1~2μm。图7表明,较大的板条往往贯穿整个板条束分布,这是板条束显微组织的一个重要特征。
图7 Fe-0.2%C合金板条马氏体部分显微组织(透射电子显微照片)
实验证明,改变奥氏体化温度,从而改变了奥氏体晶粒大小,对板条宽度分布却几乎不发生影响。但板条群的大小随奥氏体晶粒的增大而增大,而且两者之比大致不变。所以一个奥氏体晶粒内生成的板条群数大体不变。由薄膜电镜技术测得,在单位马氏体体积中板条边界的面积约为65000cm?/cm。板条束中的小角晶面积约为大角晶界面积的5倍。
在以18-8不锈钢为基础的Fe-Cr-Ni合金中也会生成板条状马氏体,同时也会生成ε'-马氏体(密排六方点阵),其显微组织与上述Fe-C合金的情况大不相同见图8 。
图8 Fe-15%Cr-12&Ni(Ms=-90°)合金板条马氏体显微组织(王水,甘油腐蚀)
它不存在板条群和同位向束,而是呈现为细的板条集团围绕着薄片状的ε'-马氏体(图中平行分布的长条)形成。但这种板条马氏体的电镜组织与Fe-C,Fe-Ni合金中完全一样。
2 片状马氏体
铁系合金中出现的另一种典型的马氏体组织是片状马氏体,常见于淬火高、中碳钢及高Ni的Fe-Ni合金中。高碳钢中典型的片状马氏体组织如图9所示。
图9 T12A钢的过热淬火组织400X(1000℃加热,水淬)
这种马氏体的空间形态呈双凸透镜片状,所以也称之为透镜片状马氏体。因与试样磨面相截而在显微镜下呈现为针状或竹叶状,故又称为针状马氏体或竹叶状马氏体。片状马氏体的亚结构主要为孪晶,因此又称其为孪晶型马氏体。片状马氏体的显微组织特征为片间不相互平行。在一个成分均匀的奥氏体晶粒内,冷至稍低于Ms 点时,先形成的第一片马氏体将贯穿整个奥氏体晶粒而将晶粒分割为两半,使以后形成的马氏体大小受到限制。因此,片状马氏体的大小不一,越是后形成的马氏体片越小,如图10所示。
图10 片状马氏体显微组织示意图
片的大小几乎完全取决于奥氏体的晶粒大小。片状马氏体常能见到有明显的中脊(见图11 )。
图11 片状马氏体(有明显的中脊,T12钢1200℃渗碳5小时淬水,180℃回火)
关于中脊的形成规律目前尚不十分清楚。片状马氏体的惯习面是(225)γ,或(259)γ,与母相的位向关系是K-S关系或西山关系。从图12 可见,马氏体内的许多细线是相变栾晶,中间接合部分的带状薄筋是中脊。
图12 片状马氏体的透射电镜组织
相变栾晶的存在是片状马氏体组织的重要特征。栾晶的间距大约为50?,一般不扩展到马氏体的边界上,片的边际则为复杂的位错组列。一般认为这种位错是沿[111]α?方向呈点阵状规则排列的螺型位错。片状马氏体内的相变栾晶一般是(112)α?栾晶。但在Fe-1.82%C(c/a=1.08)合金中,也发现(110 )α?栾晶会与(112)α?栾晶混生。
由上述片状马氏体内部亚结构的差异,可将其分为以中脊为中心的相变孪晶区(中间部分)和无孪晶区(在片的周围部分,存在位错)。孪晶区所占的比例随合金成分变化而异。在Fe-Ni合金中,含Ni量越高(Ms点越低)孪晶区越大。根据Fe-Ni-C合金的研究看出,即使对同一成分的合金,随着Ms点降低(如由改变奥氏体化温度引起)孪晶区所占的比例也增大。但相变孪晶的密度几乎不改变。孪晶厚度始终约为50?左右。
板条状马氏体和片状马氏体是钢和合金中两种最基本的马氏体形态,他们的形态特征及晶体学特点对比列于表1 。
表1 铁碳合金马氏体类型及其特征
3 其他马氏体形态
3.1 蝶状马氏体
在Fe-Ni合金或Fe-Ni-C合金中,当马氏体在某一温度范围内形成时,会出现具有特异形态的马氏体,如图13所示。
图13 碟状马氏体的显微组织
这种马氏体的立体形状为细长杆状,其断面呈蝴蝶形,故称蝶状马氏体或蝴蝶状马氏体。现已发现,Fe-31%Ni 或 Fe-29% Ni-0.26%C合金在0~-60℃范围内形成蝶状马氏体,电镜研究确定其内部亚结构为高密度位错,看不到孪晶。与母相的晶体学关系大体上符合K-S关系。在0~-20℃之间主要形成蝶状马氏体,而在-20~-60℃之间则与片状马氏体共存。可见,对于上述两合金系,蝶状马氏体的形成温度范围是在板条状和片状马氏体的形成温度范围之间。
蝶状马氏体的两翅接合部分很像片状马氏体的中脊。有人设想是从此处开始向两侧沿不同位向长成的马氏体(大概为孪晶关系),才呈现蝴蝶状。蝶状马氏体的接合部分,类似爆发形成的马氏体的两片接合部分,但其内部看不到孪晶,这与片状马氏体有很大的差别。而从内部结构和显微组织看,蝶状马氏体与板条状较相近,但它并不成排地产生。到目前为止,关于蝶状马氏体不清楚的问题还很多。但它的形态特征和性能介于板条状和片状马氏体之间,则是令人感兴趣的问题。
3.2 薄片状马氏体
这种马氏体是在Ms点极低的Fe-Ni-C合金中发现的。它呈非常细的带状(立体图形为薄片状),带相互交叉,呈现曲折、分枝等特异形态,如图14 c)所示。
图14 Fe-Ni-C合金冷至Ms点不同温度时形成的马氏体的显微组织
这种马氏体的电镜组织如图15所示。
图15 薄片状马氏体的电镜组织(Fe-31%,Ni0.23%C,Ms=-190℃,冷至-196℃)
它是由(112)α? 栾晶组成的全栾晶型马氏体,无中脊,这是它与片状马氏体的不同之处。研究指出,Fe-Ni-C系马氏体的形态随着形成温度的下降,将从透镜片状转化为薄片状。
碳含量约为0.25%的Fe-Ni-C合金中,当Ms=-66℃时,组织为爆发形成的片状马氏体,见图14a);当Ms降低到-150℃时,开始出现少量薄片状马氏体,见图14 b);而Ms点降至-171℃时,则全部为薄片状马氏体组织见图14 c)。并由此发现,从透镜片状向薄片状的转化温度随碳含量的增加而升高。碳含量达0.8%时,-100℃以下即为薄片状马氏体形成区。随着转变温度的下降,薄片状马氏体转变进行时,既有新马氏体片的不断形成,同时又有旧有马氏体片的增厚。旧马氏体片的增厚在片状马氏体中是看不到的。
3.3 ε'马氏体
上述各种马氏体都是体心立方或体心正方结构的马氏体(α' ),在奥氏体层错能较低的合金中,还会形成密排六方点阵的ε'马氏体。这种马氏体易于在高Mn-Fe-C合金中形成。而在以18-8不锈钢为代表的Fe-Cr-Ni合金中却经常与α'-马氏体共存。ε'马氏体也呈薄片状见图16 。沿(111 )γ 面呈魏氏组织状态形成,其亚结构为大量的层错。
图16 Fe-16.4%Mn合金的马氏体显微组织(硝酸酒精腐蚀)
2 合金的化学成分与马氏体形态及其内部亚结构的关系
钢中合金元素的含量对马氏体形态有显著的影响。Fe-C和Fe-Ni合金的马氏体形态随合金含量的增加而从板条状变成为片状即为典型的例子。例如,Fe-C合金中,0.3%C以下为板条状,1%C以上为片状,0.3~1.0%C之间时两者共存。但是,不同资料中,关于板条马氏体过渡到片状马氏体的浓度界限并不一致。这与淬火速度的影响有关,淬火速度增加时,形成孪晶马氏体的最小碳浓度降低。
图17示出碳含量对Fe-C合金马氏体类型和Ms点及残留奥氏体量的影响。
图17 碳含量对Ms点、板条马氏体量和残余奥氏体量的影响(碳钢淬火至室温)
由图中可见,碳含量小于0.4%的钢中基本没有残留奥氏体,Ms点随碳含量的增高而下降,而栾晶马氏体量和残留奥氏体量则随之升高。铁系二元合金的马氏体形态和合金成分的关系归纳如表2 。
表2 Fe系二元合金的马氏体形态
由表中可见,缩小γ区的合金元素,全部形成板条马氏体。扩大P区的合金元素,随含量增加,一般Ms 点显著降低,马氏体形态也发生变化。例如,在Fe-C、Fe-N,Fe-Ni、Fe-Pt等二元合金中,随合金元素含量的增加,马氏体形态从板条变为片状。而Mn、Ru和Ir可显著降低奥氏体的层错能,所以在这些元素的二元铁合金中,随合金元素含量增加,马氏体的形态不是从板条状变为片状,而是变为ε?马氏体。Fe-Cu和Fe-Co合金是扩大γ区元素中的两个例外情况。
Cu虽属扩大Y区元素,但由于在Fe中固溶量少,Ms点降低不多,因而表现出与缩小γ区型合金相同的倾向。Fe-Co合金与其他合金不同,随Co含量增加,Ms点反而上升,所以它的情况特殊。通常钢中含有的合金元素种类颇多,但如在Fe-C或Fe-Ni合金中加入第三元素,当加入量很少时,可以认为马氏体形态与二元合金时基本相同。
前已述及,在Fe-Ni-C合金中可以形成板条状、蝶状、透镜片状和薄片状马氏体。这四种形态的马氏体的形成温度与碳含量及Ms 点的关系见图18 。
图18 Fe-Ni-C系合金的马氏体形态与碳含量及Ms点的关系
按图中所示,透镜片状和薄片状马氏体的形成温度都随碳含量的增加而升高。图中影线区表示蝶状马氏体的形成区域。
铁系合金中马氏体的形态和亚结构及其晶体学特征的关系归纳如表3 。
表3 Fe系马氏体的特征
在钢中,一般认为碳含量<0.20%的板条状马氏体为体心立方点阵。而碳含量大于这个值的马氏体为体心正方点阵。有人认为体心立方马氏体就相当于低碳钢中的位错型马氏体,而体心正方马氏体则相当于高碳的孪晶型马氏体。但是,在Fe-Ni合金中,栾晶型马氏体也是体心立方的。所以,关于晶体结构和亚结构的关系尚不能肯定。
3 影响马氏体形态及其亚结构的因素
上面讨论了合金成分变化时引起马氏体形态发生变化的规律。至于这种变化受到什么因素影响,目前议论颇多,尚无统一见解。较多的人认为形态变化归根到底是亚结构的变化,典型的观点列举如下:
1 Ms点
持这种观点的人认为马氏体的形态取决于Ms点。他们认为在Fe-C合金中,含碳量增加Ms点降低,当低于某一温度(300~320℃)时,容易产生相变孪晶,因而便形成片状马氏体。碳钢的马氏体形态和晶体特征与碳含量及Ms温度的关系列于表4 。
表4 碳钢的马氏体形态和晶体学特征与钢的碳含量及Ms点的关系
马氏体形态随Ms点的下降从板条状向片状转化的原因可作如下解释。由表4中可以看到惯习面和马氏体的形态存在一定关系。一般认为,低碳马氏体形成温度高,这时以切变量较大的(111)γ为惯习面,同时在较高的温度下滑移比栾生易于发生,而且在面心立方点阵中的{111}γ晶系较少,因此形成马氏体的起始位向数少,所以有利于在同一奥氏体中形成群集状马氏体。而随着Ms 点温度降低,孪生变得比滑移更易于发生,同时以{225}γ或{259}γ为惯习面形成马氏体,由于晶系较多,形成马氏体的起始位向数增多,因此在同一奥氏体中易于形成相邻马氏体片互不平行的李晶片状马氏体。研究证明,如果在高温下形成马氏体,即使对奥氏体进行强烈的强化,也不能形成孪晶片状马氏体。
对Fe-Ni-C系合金可通过改变奥氏体化温度而使Ms点发生变化。利用这种现象,可以在同一成分合金中获得不同的Ms点。观察冷却到稍低于相应的Ms点时生成的马氏体形态变化,结果发现,随着Ms点的降低,马氏体的态会发生从蝶状→片状→薄片状的变化。而且同是片状马氏体,随着形成温度降低相变孪晶区也逐渐增大。同样,研究同一合金在Ms点以上的各种温度下形成的形变诱发马氏体的形态,结果表明,形变温度(即形变诱发马氏体的形成温度)改变,马氏体的形态也会发生与上述情况完全相同的变化。这个试验至少确定了这类合金的马氏体形态和内部结构只单纯地与Ms 点有关。
此外,高压下Ms点降低,这时也容易产生相变孪晶,也发现马氏体形态由板条状向片状变化的现象,如图19 所示。这也是支持Ms点说的实验事实。
图19 4000MPa压力对铁磁合金Ms点及马氏体亚结构的影响
实际组织中很多马氏体都是在Ms点和Mf 点之间的各个温度下相继形成的,各马氏体晶体的实际形成温度并不一样,因此各自的内部结构和形态当然也不尽相同。所以严格说来,影响马氏体形态或内部结构的不应说是Ms 点,而应说是马氏体的形成温度。
2 奥氏体的层错能
这是由Kelly等提出的假说,他们认为奥氏体的层错能愈低,愈难于生成相变栾晶,愈趋向于形成板条状马氏体。18-8不锈钢和Fe-8%Cr-1.1%C合金的层错能都低,即使是在液氮温度下也只是形成位错型马氏体,这个现象难于用Ms点假说来解释,但却可以用这一假说来说明。另外,在Fe-30~33%Ni合金的片状马氏体中,随Ni含量增加相变孪晶区增大。由于Ni被认为是提高奥氏体层错能的合金元素,所以,这又是支持这个假说的一个实验现象。当然,这个实验现象用Ms点说也可以解释(因为Ni 降低了Ms 点)。
3 奥氏体和马氏体的强度
这是由Davis和Magee等最近提出的假说。他们用合金化的方法改变奥氏体的强度,研究了马氏体形态变化和奥氏体强度变化之间的对应关系。结果表明,马氏体形态是以Ms 点处的奥氏体屈服强度(约为206MPa)为界限而变化,在这个界限以上,形成惯习面为{259}γ的片状马氏体,在这个界限以下,形成惯习面为{111}γ的板条状马氏体或惯习面为{225}γ的片状马氏体。由此,他们认为奥氏体强度是影响马氏体形态(惯习面)的决定性因素。他们还进一步研究了马氏体的强度。当奥氏体的强度低于206MPa时有两种情况,形成的马氏体强度较高时,为{225}γ马氏体。而形成的马氏体强度较低时为{111}γ马氏体。用这个假说可以很好地说明因合金成分或Ms 点的改变而引起的形态变化,特别是Fe-Ni合金中{111}γ→{225}γ,Fe-C合金中的{111}γ→{225}γ→{259}γ等惯习面的变化。这个假说对以往还不太清楚的{225}γ马氏体也有了一个明确的概念,它是在弱奥氏体转变为强马氏体的情况下形成的。C对奥氏体的强化作用不大,但却是显著强化马氏体的元素,而{225}γ马氏体大部分都是在碳含量比较高的合金系中出现的。这个假说是建立在这样的基础上的,即如果马氏体内相变应力的松弛只以挛晶变形方式进行,则得到惯习面为{259}γ的马氏体,如果相变应力的松弛一部分在奥氏体内以滑移方式进行,一部分在马氏体内部以孪晶方式进行,则得到惯习面为{225}γ的马氏体。如果在马氏体内也以滑移方式进行,则得到惯习面为{111}γ的马氏体。从许多实验结果看,上述假说有一定的正确性,但还不能断定,今后仍需进一步研究。
另外,这种假说所强调的奥氏体和马氏体的强度,必然与合金成分、种类、Ms 点、奥氏体层错能等因素有密切关系,所以这种假说也不是孤立的。
4 马氏体的滑移和孪生变形的临界切应力大小
这种假说强调马氏体内部结构取决于相变时的变形方式是滑移还是孪生,所以归根到底是受二者的临界切应力大小所支配。图20 示意地表示出马氏体滑移或孪生的临界切应力和Ms、Mf 温度对形成的马氏体形态的影响。
图20 引起马氏体滑移或孪生的临界切应力和Ms-Mf温度对形成的马氏体形态影响示意图
图中的箭头表示相应线条可能移动的方向,这种移动是因为合金成分变化引起的。线条的移动将导致滑移-孪生曲线交点的移动。由图中可见,对低碳钢(Ms 点和Mf 点均较高),引起滑移所需要的临界切应力低于引起孪生所需要的临界切应力。因而得到含高密度位错的板条马氏体。相反,如果是高碳钢(Ms 和Mf 均较低),引起孪生所需的临界切应力较小,从而得到含有大量孪晶的片状马氏体。如果碳量中等,Ms 和Mf 恰如图中所示之位置,在马氏体相变过程中,先形成板条马氏体,然后又可形成片状马氏体。即形成了两种马氏体的混合组织。
这种见解从本质上看似乎是正确的。但是,究竟哪些因素会引起切应力的变化,另外,合金成分或Ms 点是如何影响马氏体滑移或孪生临界切应力的,这些问题都还不清楚。还有其他一些观点,如相变驱动力增加会引起向片状马氏体转化。对Fe-C合金,马氏体形态变化的驱动力界限为1318J/mol,对Fe-Ni合金为1255~1464J/mol。还有人认为马氏体中C、N含量增加引起的有序化与形态转化有密切关系,等等。
4 Fe-C合金片状马氏体显微裂纹的形成
高碳钢淬火时,容易在马氏体内部形成显微裂纹。过去认为显微裂纹是由于马氏体相变时比容增大而引起的显微应力造成的。近年来的金相观察表明,显微裂纹是由于马氏体成长时相互碰撞而形成,如图21所示。
图21 两个Fe-C马氏体片相碰撞形成显微裂纹的示意图(截面A-A表示其中一个马氏体片的横截面,扩散到两个马氏体片)
马氏体形成速度极快,相互碰撞或与奥氏体晶界相撞时将因冲击而引起相当大的应力场,又因为高碳马氏体很脆,不能通过滑移或孪生变形来消除应力,因此容易形成撞击裂纹。这种先天性的缺陷使高碳马氏体钢附加了脆性,在其他应力(热应力和组织应力)作用下,显微裂纹将发展成为宏观裂纹。同时,显微裂纹的存在也将使零件的疲劳寿命明显下降。
Fe-C合金片状马氏体中的显微裂纹常出现在几个马氏体针组成的放射状交接处或出现在马氏体针叶之中,如图22 所示。
图22 Fe-1.39%C合金马氏体中的显微裂纹光学显微特征
通常以单位马氏体体积中出现的显微裂纹的面积作为马氏体内形成显微裂纹的敏感度,以Sv表示。实验指出,马氏体形成显微裂纹的敏感度受下列因素影响:
1 淬火冷却温度的影响
随淬火冷却温度的降低,钢的淬火组织中残留奥氏体量(以γR表示)减少,马氏体的数量增多,形成显微裂纹的敏感度增大,如图23 所示 。
图23 Fe-C马氏体形成显微裂纹敏感度和淬火温度的关系(1.39%C,1200℃加热1小时)
2 马氏体转变量的影响
图24表示马氏体转变量对形成显微裂纹敏感度的影响。
图24 Fe-1.86%C合金马氏体形成显微‘裂纹敏感度(SV)与每片马氏体的平均体积(V)及单位体积中马氏体片数(NV)和马氏体转变量之间的关系
由图中可见,随马氏体转变量增加,形成显微裂纹敏感度Sv增大,但当转变份数(f)大于0.27时,Sv不再增虽然单位体积中马氏体的数目Nv不断增大,但因奥氏体被不断分割,这时所形成的马氏体片尺寸(以一片马氏体的平均体积V表示)将减小。所以,马氏体片的大小(V)对形成显微裂纹的敏感度Sv可能有一个临界值,大于这个临界值时,形成显微裂纹的敏感度Sv将随转变份数的增大而增大。因此,裂纹的形成在很大程度上决定于马氏体片的大小。虽然马氏体转变量增多时总的裂纹数目和面积可能增多,但在早期形成的马氏体片较大,故裂纹主要还是在转变早期形成的。
3 马氏体片长度的影响
实验已直接观察到马氏体形成显微裂纹敏感度随马氏体片长度(即片的最大尺寸)的增大而升高,如图25 所示。
图25 形成显微裂纹敏感度与马氏体片长度之间的关系(点旁的数字为马氏体含量%)
这是因为长尺寸的马氏体片受到其他马氏体片碰撞和冲击的机会多。同时,它又往往横贯奥氏体晶粒,因此碰遇晶界的机会也大。
很多实验观察已证实,显微裂纹主要是在粗大的马氏体中形成的,而当马氏体非常细小时则很少出现显微裂纹。由此看来,对于马氏体形成显微裂纹应该存在一个临界马氏体大小。如果奥氏体成分比较均匀,也将存在一个临界奥氏体晶粒大小,低于这个临界值,显微裂纹将不发生。细小奥氏体晶粒可减少淬火高碳钢的显微裂纹,这一观点已被应用于生产实际之中。目前还不清楚的是,显微裂纹敏感度究竟是取决于马氏体片本身的大小还是取决于临界尺寸的马氏体片成长时所引起的应力场。
4 奥氏体晶粒大小的影响
在奥氏体比较均匀的情况下,初期形成的马氏体片的长度和奥氏体晶粒大小有关。粗大的奥氏体晶粒形成粗大的马氏体,易促成显微裂纹的形成。图26 的实验结果证实了这一点。这说明高碳钢在较高温度下淬火时容易形成裂纹。因此,通常高碳钢淬火均应选择较低的淬火温度。
图26 碳钢(1.22%C)奥氏体晶粒大小对现场显微裂纹敏感度的影响
5 马氏体中碳含量的影响
马氏体中碳含量对形成显微裂纹敏感度的影响如图27 。
图27 马氏体含碳量对显微裂纹敏感度的影响
由图中可见,形成显微裂纹的敏感度随马氏体中碳含量的增高而增大。当奥氏体内碳含量大于1.4%时,形成显微裂纹敏感度反而减小,这和马氏体转变时晶体的惯习面有关。由于钢中的碳含量大于1.4%时马氏体的形态改变了,片变得厚而短,马氏体片之间的夹角变小了,撞击机会和应力都有所减少,故显微裂纹敏感度反而降低。在1.39%C钢中测得显微裂纹敏感度随马氏体中碳含量降低而显著减少,结果列于表5 。
表5 马氏体中碳含量对形成显微裂纹敏感度的影响(晶粒度3级)
金相观察表明,显微裂纹敏感度的降低与显微组织中出现较多的平行长大的板条状马氏体有关。板条状马氏体具有较好的塑性和韧性,且因相互平行生长而使相互撞击的机会减少,故而显微裂纹敏感度低。
由上述可见,高碳钢过热淬火容易开裂就是因为奥氏体晶粒粗大和马氏体碳含量过高之故。因此,生产中趋于采用较低的加热温度和较短的保温时间,以减少马氏体中的碳含量,并获得细小的晶粒。通常过共析钢采用不完全淬火获得隐晶马氏体,不易产生显微裂纹,是其具有良好的综合性能的原因。
免责声明:本网站所转载的文字、图片与视频资料版权归原创作者所有,如果涉及侵权,请第一时间联系本网删除。
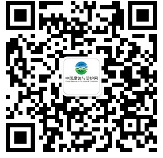
官方微信
《腐蚀与防护网电子期刊》征订启事
- 投稿联系:编辑部
- 电话:010-62316606-806
- 邮箱:fsfhzy666@163.com
- 腐蚀与防护网官方QQ群:140808414