永磁合金又称硬磁合金,主要用于制造电动机、仪器、仪表中的永久磁铁。对它的基本要求是矫顽力He大,剩磁感应强度Br 高,最大磁能积(BH)m大(因而磁滞回线宽,去磁曲线凸起系数大),性能的稳定性高。此外,还希望加工性良好。
永磁性能中最主要的是矫顽力。磁晶各向异性常数K和磁致伸缩系数入大时,合金磁矩转动退磁的阻力大,矫顽力高。形成固溶体时矫顽力提高不多;而形成固溶体加第二相时可使矫顽力大大提高。第二相弥散度越大,矫顽力提高越多。加工硬化或相变引起的内应力、晶粒细化和导致合金组织偏离平衡状态的过程,都能阻碍畴壁的移动,显著地提高矫顽力。合金化和热处理淬火,是改善硬磁合金性能的主要方法。
常用硬磁合金主要有高碳钢、铁镍铝和铝镍钴合金、铁钴钒和铁铬钴合金、铂钴合金、稀土钴合金以及稀土铁合金等。
1 高碳钢
1.1 高碳碳钢
高碳碳钢是最早的永磁合金。它淬火后可形成马氏体、弥散剩余碳化物和残留
奥氏体组织。碳含量越高,淬火后内应力越大,剩余弥散碳化物越多,非磁性的残留奥氏体越多,矫顽力越大,但使剩磁感应强度降低,如图1所示。
▲图1 碳钢的磁性能与碳含量的关系
碳钢同时具有较高矫顽力和剩磁感应强度的碳含量w(C)在0.8%左右。马氏体磁钢的碳含量w(C)一般为1.0%~1.5%。为了在保持剩磁感应强度不降低的条件下提高矫顽力,常采用三重热处理:在Ac以上20~30℃加热淬火;在500℃左右高温回火;在Ac,以上30~50℃进行最终淬火。由于性能稳定性差和脆性较大,高碳淬火磁钢现已较少应用。
4.1.2 高碳合金钢
钨使弥散碳化物增多,溶于马氏体中可引起晶格畸变。降低钨钢中碳的含量,可使矫顽力、剩磁感应强度和最大磁能积都增大。但钨含量过高时饱和磁感应强度降低。钨钢一般含w(W)6%,w(C)0.7%。
铬钢的情况与钨钢基本相同。铬和碳对磁性能的影响如图2所示。铬提高钢的淬透性。常用铬钢的碳含量w(C)为1%左右,铬含量w(Cr)有3.5%和6%两种。
▲图2 铬钢在850℃(a)和900℃(b)淬火时铬含量和碳含量(图中数字表示w(C))对磁性能的影响
钴钢的剩磁感应强度、矫顽力和磁致伸缩系数随钴含量的增大而提高。钴不形成碳化物,为了用弥散碳化物更多地提高矫顽力和最大磁能积,钴钢中常加入w(W)3%~8%和w(Cr)3%~5%。
钨钢、铬钢、钴钢的退磁曲线如图3所示。它们的热处理与高碳磁钢相似,也采用三重热处理。由于它们的淬透性较好,第一重热处理在加热之后,可以采用较慢的冷却速度(空冷)。为了减轻碳化物分布不均匀的状况,加热温度应该较高(但钨钢较易过烧)。第一重热处理中最重要的是获得均匀的奥氏体组织。第二重
热处理是进行高温回火,温度在700℃左右,保温时间不能过长,以免碳化物长大。第二重热处理的目的是使马氏体-奥氏体分解为均匀的回火托氏体。第三重处理是最终淬火。为了防止加热时碳化物凝聚和淬火后残留奥氏体量过多,淬火温度不宜过高(钴钢的温度可以高些),保温时间不宜太长,同时要控制炉气,避免发生表面脱碳。冷却在油中进行,以减轻畸变和开裂。为了增大磁性能的稳定性,淬火后常进行100~120℃时效处理。
▲图3 钨钢、铬钢、钴钢的退磁曲线1-铬钢 2-钨钢 3-铬钴钢 4-铬钴钼钢
钨钢、铬钢、钴钢的成分、热处理和性能见表1 。
▼表1 钨钢、铬钢、钴钢的成分、热处理和磁性能
2 铁镍铝合金和铝镍钴合金
铁镍铝基合金曾经是风行一时的铸造永磁合金。它的矫顽力和最大磁能积高,性能稳定,温度系数小,广泛应用于电器仪表和通信器械,曾经是永磁合金中最重要的一族。近几十年来,由于铁氧体、稀土钴和可变形永磁合金等材料的开发,加之它本身脆性较大而且难以加工,用量日趋下降。
以铁镍铝为基础的永磁合金品种较多,最重要的是不含钴的FeNiAl系合金(AlNi型合金)和含钴的FeAlNiCo 系合金(或AINiCo型合金)两大类。我国生产的铁镍铝铸造永磁合金的牌号、成分和性能见表2。
▼表1 我国铁镍铝铸造永磁合金的牌号、成分
2.1 铁镍铝合金
2.2.1 铁镍铝合金的成分
铁镍铝合金的矫顽力与铝含量和镍含量的关系如图4所示。矫顽力和磁能积以含w(Ni)26%~30% 和w(Al)11%~15%的合金为最好。在这样的成分范围内,镍、铝含量增大时He值提高,但Br降低(见图5)。.这个成分范围约相当于摩尔分数为25%A1、25%Ni和50%Fe。重要的是镍、铝原子百分比保持1:1的关系。
▲图4 FeNiAl合金的矫顽力He与铝、镍含量的关系w(Ni)含量:1-15% 2-20% 3-22.5% 4-25% 5-27. 5% 6-30% 7-32%
▲图5 FeNiAl合金的剩磁感应强度Br与铝、镍含量的关系w(Ni)含量:2-20% 3-22.5% 4-25% 5-27.5% 6-30%
2.2.2 铁镍铝合金的组织
图6为典型铁镍铝合金相图的垂直截面。著名的MK合金[w(Ni)24%~28%,w(AI)12%~14%,其余为Fe]在1300~900℃范围内是单相α固溶体,具有体心立方结构。冷却到900℃以下时,α相发生调幅分解,生成α1和α2两相。全部过程表现为:在整个α固溶体区域内,同时交替发生铁原子的富集和镍、铝原子的富集。富铁区的周围是富镍、铝区,而富镍、铝区的周围为富铁区,并由此连续发展成富铁的α1相和富镍、铝的α2相的相互交替状态。α1相为铁基固溶体,具有体心立方结构,原子排列无序,是强磁性相;α2相为以NiAl相为基的有序相,也具有体心立方结构,是弱磁性相。α1和α2两相的晶格常数十分接近,相差不大于1%。α1与α2以(100)晶面共格相连,无明显的分界面。调幅分解的α1相常在α2相基体中呈隔离的片条状分布,形成特殊的所谓调幅结构。
▲图6 FeNiAl合金相图的一个垂直截面(Ni22%)
调幅结构的高矫顽力主要来自α1的形状各向异性。因此,α1相必须为细长的单畴片条,α1相片条应相互平行,α1相与基体α2相的成分相差要大。调幅结构的磁能积(BH)m则取决于α1相有序分布的程度。
2.2.3 铁镍铝合金的热处理
为了获得完善的调幅结构,根据具有调幅分解的合金的相图(见图7),必须使合金冷却时在调幅分解线以下发生分解,而不能在溶解度线和调幅分解线之间发生分解。随着成分的不同,铁镍铝合金存在原则上不同的两种热处理方法。
▲图7 具有调幅分解的二元合金相图(示意图)
1)连续冷却处理
由图7可见,含Fe约50%(摩尔分数)的合金,在成分上处于调幅分解区的中心,只需要简单的连续冷却,即可发生调幅分解。由图8 可以看出,合金从约1100℃的α单相区以适当的冷速冷却时,在调幅分解温度以下分解为α1+α2。分解初期温度较高(约800℃),α1相总量少于α2相。随着温度的下降,铁原子向α1相富集,使α1相的铁磁性增强,总量增多;镍、铝原子则向α2相富集,结果α1和α2相的成分及磁性相差越来越大,最后形成单畴α1相片条散布于弱铁磁性的α2相基体中的结构,使合金具有较高的He值。
▲图8 FeNiAl永磁合金连续冷却处理示意图
冷却速度必须控制恰当,过快时两相分解达不到适当的程度,He值不高;太慢时α1相易长大粗化,超过单畴尺寸,使He值降低。图9 表明,对于含w(Ni)27%和w(Al)15%的铁镍铝合金,当冷速约10℃/s时,He值最高,达到40kA/m以上。一般称使合金获得最佳永磁性能的冷却速度为临界冷却速度VC。
▲图9 FeNiAl合金(w(Ni)27%、w(Al)15%)的He值与冷速的关系
合金的临界冷却速度主要与其成分有关。镍含量增加时,临界冷却速度增大;铝含量增加时,临界冷却速度减小,如图10-59所示。铜可代换部分镍,使He和Br提高而vc 降低,并降低vc 对成分波动的敏感性,有利于提高性能的一致性。FeNiAl合金中一般都加入3%~4%Cu(质量分数)。硅也降低vc和对成分的敏感性,常在大铸件中少量加入。锰、碳扩大奥氏体范围,有利于高温下γ相的出现,使磁性能恶化。一般要求w(C)<0.03%,w(Mn)<0.35%,w(P)<0.025%。钛、锆、铌能与碳化合,减弱其有害作用。合金的理想成分是使它的临界冷却速度接近于在空气中的自然冷却速度(约10°C/s),以便合金铸件在空气中冷却即可获得较高的永磁性能,而不需要进行热处理。
▲图10 镍、铝含量对FeNiAl合金最佳冷却速度的影响
采用临界冷却速度冷却,主要是为了获得最大的矫顽力和磁能积。为了提高剩磁感应强度,合金冷却到室温后,有时要在500~600℃回火若干小时。
2)淬火和回火,
由图7可知,铁含量与50%(摩尔分数)偏离较大的合金,不能采用连续冷却处理,而要采用淬火加回火处理。例如,含Fe大约35%(摩尔分数)的合金,淬火可使α相不发生分解,而后在调幅分解线以下回火获得调幅结构。但是必须合理选定回火温度和回火时间,控制α1相单畴尺寸,使合金成为形状各向异性的单畴的集合体,而具有较高的矫顽力。
2.2 铝镍钴合金
2.2.1 铝镍钴合金的成分
为了进一步提高铁镍铝合金的磁性能,加入钴而产生了铝镍钴合金。
钴的作用是:
①提高合金的He、Br值,调幅分解的富钴α1相,比无钴α1相具有更高的饱和磁化强度;钴还能显著地提高磁能积(BH)m,钴含量越高,合金的永磁性能越好。
②提高合金的居里温度te,同时降低调幅分解温度Tα,这都有利于采用磁场处理,发挥磁场处理的效果,使合金沿原外磁场方向获得较高的He、Br和隆起度γw。
③降低α相的分解速度,使临界冷却速度降低,增大合金的磁淬透性,有利于铸造大型磁铁。
铁镍铝合金中加入钴后,一般要适当降低镍和铝的含量w(Ni)<21%、w(Al)<11%),并应配入适量的铜,才能使Br、He和(BH)m值同时提高。铝镍钴合金的牌号有许多种(见表2 ),最主要的是AlNiCo5和AlNiCo8两种。
▼表2 AlNiCo5和AlNiCo8合金中的相
合金的性能与其晶粒形态有关,图11 示出晶粒形态对退磁曲线的影响。合金的晶粒形态可由铸造时的凝固过程来控制。利用定向结晶技术控制凝固过程,可以得到沿(100 )相互平行的粗大柱状晶结构的合金,其沿柱状晶轴向的永磁性能很好。
▲图11 晶体形态对AINiCo5和AINiCo8 合金退磁曲线的影响
2.2.2 铝镍钴合金的组织
图12 是AlNiCo5合金相图的截面。
▲图12 AlNiCo5合金相图的截面
可见在1200℃以上是单相α固溶体;在900℃以下发生α→α1+α2调幅分解。α1为体心立方结构,富Fe、Co,饱和磁化强度高;α2同样为体心立方结构,富Ni、Al。在1200~850℃范围内冷却时,α相中可能析出γ相。在600℃以下长期加热,还可能析出γ‘相。γ和γ’相皆为面心立方结构,属于有害相(见图13 )。
▲图13 γ相对AlNiCo8合金磁性能的影响
为了保证合金的永磁性能,必须抑制γ和γ‘相的析出。AlNiCo5的γ相在1050℃左右析出最强烈,而AlNiCo8的γ相在1100℃左右析出最强烈。
AlNiCo8的情况与 AlNiCo5相近,它们的组织转变及组成相见表3。和 FeNiAl 合金一样,AlNiCo合金较理想的结构也是具有显著形状各向异性并充分弥散有序分布的α1+α2调幅结构。
2.2.3 铝镍钴合金的热处理
铝镍钴合金热处理的要点是,防止在高温发生α→α+γ转变;使α→α1+α2充分完成;增大α1相的形状各向异性及择优取向,以获得最佳的永磁性能。AlNiCo5 和AlNiCo8的典型热处理过程如图14 所示,主要包括固溶处理(或淬火)、磁场处理和回火三种工序。
▲图14 AlNiCo5 (a)和AlNiCo8(b)的典型热处理过程示意图
1)固溶处理
合金的成分特别是Al的分布应该十分均匀(生产中的许多质量事故往往与Al的不充分合金化有关)。固溶处理的目的是加热获得单相α固溶体,使铸态的γ相完全溶解,并使成分均匀化。加热温度应高于α→α+y转变温度,但不能高于α单相区的上限。图15表明AlNiCo5的磁性能与加热温度的关系,其中有两个最佳温度范围,一般选用高温范围(1200℃以上);AlNiCo8则选在1250℃以上。加热到固溶温度后,根据产品尺寸适当保温,使产品内外都达到固溶温度。
▲图15 AlNiCo5经不同温度固溶处理(磁场处理)后的磁性能
有些合金的α相稳定性高的温度范围相当狭窄(925~850℃之间),如果处理前的原始组织中没有残余γ相,也可以采用中温处理,这时加热时间不必过长。硅能抑制γ相的析出,改善合金的淬透性,含w(Si)0.2%~0.4%的大型磁铁,适宜采用中温处理。
合金加热获得完全的α相后,为抑制γ相析出,应以不造成过大内应力的临界冷却速度冷却到室温(如图143b中虚线所示),或者冷却到约900℃,接着进行磁场处理。
2)磁场处理
w(Co)>15%的各向异性AlNiCo合金,一般都采用磁场处理工艺来提高永磁性能。具体方法是:将被冷却到居里点以上50~100℃(即900℃左右)的合金置于磁场中,以一定的速度继续冷却,或者在热磁处理炉中保温一定时间,依靠磁场的作用,使调幅分解形成的α1相沿接近外磁场的易磁化方向排列,形成磁织构,以获得高的矫顽力。在磁场中的冷却速度不宜过快,以便α→α1+α2充分完成;但冷却速度也不能太慢,以保证α1相的高度弥散分布。图16 表明冷却速度对各向异性的AlNiCo5磁性能的影响,可以看出冷却速度为0.8~1℃/s时磁性能较好。具体合金在磁场中的临界冷却速度皆由试验来确定。
▲图16 各向异性AlNiCo5 合金在磁场中的冷却速度对磁性能的影响(经600℃回火)
w(Ti)>3%的铝镍钴合金(例如AlNiCo8),α→α1+α2分解较慢,必须进行等温磁场处理。等温处理温度与时间的确定,以分解充分完成、产物获得最佳形态为原则。AlNiCo8的等温磁场处理温度为800℃左右,约比a→α1+α2的分解温度50℃。保温时间一般为10~20min,时间不得过长,以免析出相长大,磁性能降低。
对于在磁场中控制冷却的无钛少钛合金(例如 AINiCo5),磁场强度应不小于120~160kA/m。磁场有效作用的温度范围一般都很窄,常常为20℃左右。为了保证铁磁性相α1析出时立即受到磁场的作用,以发挥磁场处理的效果,多在较宽的范围(一般为850~750℃,有时为900~650℃)内施加磁场。对于w(Ti)>3%的合金(例如AlNiCo8),等温磁场处理的磁场强度应大于200kA/m,磁场在开始保温时施加。
3)回火
低钴(w(Co)<12%)合金和无钴合金一样,在固溶加热和以临界冷却速度连续冷却之后,为了提高剩磁感应强度,进行一次回火,回火温度为500~600℃。
w(Co)>15%的合金,进行固溶加热及随后的磁场处理时,由于钴含量较高,调幅分解不可能一次到底,为了进一步提高矫顽力和磁能积,必须进行回火。回火的目的是使调幅分解继续发生,进一步调整α1和α2中的合金元素含量,使a1中的铁、钴含量增高,铁磁性增强;并使a2中的镍、铝含量增多,铁磁性减弱,结果使矫顽力显著增大。
为了获得更好的效果,AlNiCo5采用二级回火,而AlNiCo8甚至要求采用多级回火。第一级回火的温度为600~650℃,保温时间为2~10h。第二级回火温度比第一级低30~50℃,保温15~20h。回火温度越低,最佳保温时间越长。保温时间过长要发生过回火。如果过回火是可逆的,进行一次温度略低的第二次回火可以使性能
恢复;若过回火是不可逆的,则必须重新固溶处理和磁场处理,然后再进行正确的回火。
为了提高铝镍钴合金的机械加工性能,可以进行退火。具体工艺是:加热到1000~1150℃,保温3~6h,空冷。因有y相析出,合金退火后的硬度降低,但塑性和韧性提高(不发生α→y+α转变的、无Co的FeNiAl合金,或此种转变被抑制的、含Ti 和Si 的AlNiCo合金不进行退火处理)。FeNiAl 和 AINiCo合金的典型热处理工艺制度见表3 。
▼表3 铸造铁镍铝和铝镍钴永磁合金的典型热处理工艺制度
3 铁钴钒合金和铁铬钴合金
铁钴钒和铁铬钴合金是两种用量较大的变形永磁合金。
3.1 铁钴钒合金
铁钴钒合金为相变型变形永磁合金,是重要的磁滞合金。一般w(Co)=51%~53%,w(V)<13%。加钴的目的是保证最高的矫顽力和剩磁感应强度;加钒的目的是抑制α相的有序化,改善加工性能。可用铬代替一部分钒。合金在淬火状态下塑性很好,可加工成薄带或丝材。它的磁性能主要依靠淬火后的冷变形和回火来控制。
合金的热处理和冷加工工艺一般为:900~1100℃淬火→变形量90%以上的冷加工→560~660℃回火。表4 中给出了各向异性铁钴钒磁滞合金的回火制度。
▼表4 各向异性铁钴钒磁滞合金的回火制度
图17和图18 所示是冷变形量和回火温度对磁性能的影响。变形对硬磁性能有利;在600℃左右回火可获得最佳磁性能。
▲图17 铁钴钒(含w(Cr)2%~3%)合金的冷变形量对磁性能的影响
1-冷变形 2-冷变形后600℃回火
▲图18 回火温度对铁钴钒(w(Co)52%,w(V)13%)合金磁性能的影响
铁钴钒合金具有aγ转变,淬火组织为α’。经大量冷变形后,可能残留的γ相可完全转变为α‘相,它呈长条状分布并形成织构。回火时发生a’→α+γ转变,非磁性的面心立方γ相呈薄片状,在磁性的体心立方α相边界析出,将原α‘相分割为大量细小的α相磁块,其大小皆小于单畴临界尺寸,并处于被隔离的磁绝缘状态。由于保留和产生了晶体与形状的各向异性,合金的He大大提高。此时纵向和横向磁性能相差很大(见图17 ),纵向性能比横向好得多。
铁钴钒合金的饱和磁致伸缩系数λ,较大[(40~80)×10E-6],回火过程中施加应力(应力回火),可以获得类似于磁场处理的效果。
3.2 铁铬钴合金
铁铬钴合金是20世纪70年代发展起来的一种析出型变形永磁合金。它具有较好的韧性,可以冷、热加工,轧带拉丝,也可以由铸造和粉末冶金方法生产。合金在较低的温度范围内发生α→α1+α2调幅分解,形成富铁、钴的强铁磁相α1和富铬的非铁磁相α2,使合金具有很好的永磁性能。
图19 为含w(Nb)1%、w(Al)1. 5%的Fe-Cr-Co15合金相图截面。铬含量低时易出现γ相,严重损害磁性能。含量过高则易形成α相(FeCr金属间化合物),严重损害韧性。铬使饱和磁感Br和居里点Tc降低。钴能提高合金的调幅分解温度,扩大分解温度范围,同时提高Br和T并在一定的成分范围内保证合金有高的He和Br。加人钼、硅等可改善加工性能和热处理工艺性能,且提高磁性能。目前,铁铬钴合金的成分主要为w(Cr)27%~28%、w(Co)23%~26%、w(Mo)3%,或w(Si)0.7%~1.0%。
▲图19 FeCrCo合金含w(Co)15%的纵截面图
铁铬钴合金的典型热处理和加工工艺为:1300~1330℃固溶处理(水冷)→冷加工→620~640℃磁场处理→时效处理(多级时效)。几种常用合金的热处理工艺与性能见表5。
▼表5 几种常用铁铬钴合金的热处理和磁性能
从1300℃以下快冷,是防止γ相和a相析出,获得单一的α相组织。在居里温度Tc(660~680℃)以下的调幅分解区(510~640℃)进行磁场处理(一般为610~650℃,磁场强度应大于160kA/m)。由于α→α1+α2分解比σ相的析出快得多,σ相不析出,而α1弥散析出,呈细长条状沿磁场方向与α2相形成调幅结构。磁场处理温度越高,析出相的粒子越粗大。保温时间越长,两相的成分差也越大。为了使两相大小适中,而成分差尽可能大,以提高永磁性能,一般进行分级时效处理。新的研究表明,铁铬钴合金高矫顽力的获得,主要决定于调幅结构所产生的畴壁钉扎效应,而不是孤立状单畴颗粒“一致转动”的作用。
3.4 铂钴合金
铂钴合金为有序转变型变形永磁合金,具有很高的矫顽力和磁能积;良好的塑性,可加工成细丝和薄带,可任意加工而磁性不变,极耐腐蚀,耐火,适用于微型或超微型磁系统,可制造形状复杂的元件,例如计时、医疗和飞机航行记录仪表中的磁元件等。
铂钴合金形成连续固溶体,硬磁性能以大约等量铂、钴摩尔分数(相当于w(Co)23%~26%)时为最好,如图20 所示。
▲图20 PtCo合金的永磁性能与钴含量的关系
这样的合金,在825℃以上为无序的面心立方结构;825℃以下为有序的面心正方结构,同时表现出铁磁性。825℃既是该合金的有序转变温度,也是合金的居里点。
为了获得良好的永磁性能,必须恰当地控制合金的有序度,因为完全有序时矫顽力太低。有序相的畴壁能高,当无序相中弥散分布有有序相时,畴壁横切有序相,会使畴壁能升高,使畴壁被钉住,矫顽力增大。有序相颗粒尺寸以20~50μm为最好。
铂钴合金的热处理一般是:加热到1000℃左右,获得无序结构,以大约150℃/min的冷却速度冷至室温,然后在600℃左右进行时效,使合金达到要求的有序化程度。图21 所示是时效处理时间对合金磁性能的影响。表6 中给出了几种铂钴合金的热处理工艺和所得的磁性能。
▼表6 几种铂钴合金的成分、热处理和磁性能
▲图21 不同钴含量的PtCo合金经淬火(1000℃加热,以78℃/min的速度冷却)后在600℃时效时磁性能与保温时间的关系1-w (Co) 46.5% 2-w (Co) 48% 3-w (Co) 54%
3.5 稀土钴合金
稀土钴合金是20世纪60、70年代出现的以稀土元素与钴金属之间形成的金属间化合物为基体的新型永磁合金。其磁化强度高,磁晶各向异性大,居里点高,磁能积的大小较传统的永磁合金有突破性的提高,被认为是比较理想的永磁材料。已应用于电子工业中的元器件,如制作雷达行波管内电子聚焦的周期永磁体阵列、微波器件和电子手表的永磁体;飞机及飞船电动机和仪表;限制器、隔离器和集成电路隔离器;磁泡储存器的永磁薄膜;以及微型马达、微型继电器、医疗器具等。我国的稀土钴合金见表7 和表8,这类合金的发展并不有悖于我国的资源,条件,但原材料较稀缺和昂贵仍然是存在的主要问题。
▼表7 我国稀土钴永磁合金的磁性能
▼表8 我国稀土钴永磁合金的其他物理性能
钐钴合金是最基本的稀土钴合金,其相图见图22。Sm’与Co生成一系列金属间化合物,其中Sm2Co5和Sm2Co17最重要,分别构成两种钐钴合金的基础。目前,两种稀土永磁合金皆主要采用粉末冶金的方法生产,其工艺流程为:原材料→冶炼→制粉→磁场取向与压力成形→真空烧结与热处理→机械加工→表面处理→检测。也可以采用还原扩散、树脂粘结、熔体急冷、铸造、机械合金化等方法进行生产,且各有其特点。
▲图22 Sm-Co 合金相图
3.5.1 SmCos型合金
简单表达为1:5(指两种原子数之比)型合金,是以SmCo5化合物为基体的钐钴合金,最早出现于20世纪60年代中,被称为第一代稀土永磁合金。
SmCo5化合物具有CaCu5型六方结构,有极高的磁晶各向异性常数(K1=15~19×10E3 kJ/m),较高的饱和磁化强度(0.8kA/m),由其制成的合金可以获得极大的矫顽力(达1194~3184kA/m)和很高的磁能积(127~183kJ/mm?
以上),磁性能比著名的铸造AlNiCo合金有成倍的提升。这种合金按组织可分为两种:以SmCo5 型化合物为基体的单相合金和在此基体中还析出有少量Sm2Co17型化合物的多相合金。总体上,合金的矫顽力机制主要基于磁畴的形核和畴壁在晶界上的被钉扎。所以合金的晶粒要非常细小(1~10μm),基本上为单磁畴粒子。
SmCos的化学计量成分(质量分数)是33.8%Sm和66.2%Co。其中的钐和钴可相应用其他较便宜的和有特性的稀土元素RE(包括混合稀土金属MM)和过渡族金属TM来取代,于是得到一系列新的合金。单相合金有RCo5[例如SmCo5、PrCo5、(Sm,,Pr)Co5等]、MMCo5以及(Sm,MM)Co5等;多相合金主要是Ce(Co,Cu,Fe)z (z=5~6)等。纯SmCo5 合金的成分,Sm的含量一般都略高于化学计量比(w(Sm)为37.2%),以利于消除工艺过程中氧的影响,提高收缩率和磁性能。(Sm,Pr) Co5合金中,用较经济的Pr取代部分Sm,既使合金更便宜,还可提高磁化强度和磁性能的稳定性。Ce(Co,Cu,Fe),合金中,Ce是资源丰富的元素,Cu代Co可通过沉淀硬化提高矫顽力,而Fe的加入可提高磁化强度。所以合金的磁性能比较高,虽剩磁和磁能积有所下降,但成本大大降低。典型SmCo5型合金的主要性能见表9。
▼表9 SmCo,型合金的主要磁性能
SmCo5型合金一般采用液相烧结法制备:在SmCo5基相粉末中添加富Sm成分(质量分数)(含约60%Sm和40%Co)合金的粉末,混合,球磨,得到细粉料(平均粒径为1~10μm),在磁场中取向和预压,进行等静压成形,然后在真空中加热到1100~1200℃烧结约1h。.烧结时,添加的富Sm合金粉末转变成液相,逐渐被固体基相粉末吸收,并以此加快基相的烧结过程,提高其致密度,且使磁性能改善。表10中的数据表明,烧结温度的提高能全面提高合金的磁性能,但超过1150℃后,由于晶粒长大,晶界对畴壁钉扎的强度降低,矫顽力和磁能积显著下降。所以合金存在一个较合理的烧结温度。
▼表10 SmCo5合金经不同温度烧结后的磁性能
为了改善矫顽力,SmCo5型合金在烧结之后必须进行一种特殊的退火处理:直接从烧结温度缓慢(以不大于3℃/min的速度)冷却至850~950℃,保温一定时间或不保温,然后以较快(不低于50℃/min)的速度冷却至室温。合金的烧结-热处理曲线如图23所示。
▲图23 SmCo5型合金的烧结-热处理工艺曲线
必须注意,退火温度不能低于800℃,并且冷却速度在800~500℃之间一定要很快(一般采取油冷),以免在750℃左右SmCo5相分解或生成较粗大的第二相析出物,而使合金的矫顽力降低。
3.5.2 Sm2Co17型合金
亦简表为2:17型合金,是以Sm2Co17化合物为基体的钐钴合金,20世纪70年代末出现,被称为第二代稀土永磁合金。Sm2Co17化合物在1250℃以上具有Th2Ni17型六方结构,1250℃以下具有Th2Ni17型菱方结构。
与SmCo5相比,磁晶各向异性较低(K1=3.3×10E3kJ/m?),但饱和磁化强度较高(0.95kA/m),且可固溶而能进一步提高,是更有效的高性能永磁合金的基体。Sm2Co17型合金按组织也分两种:以Sm2Co17 型化合物为基体的单相合金和在其基体上还沉淀有SmCo5型化合物的多相合金。单相合金应用者较少,实际上2:17型合金基本上为沉淀硬化的多相合金。其矫顽力机制主要是基于沉淀相粒子在畴壁上的钉扎作用。因此要求合金组织中的沉淀相高度弥散分布和基体成分的高度微观不均匀性。
Sm2Co17 化合物中的Sm 用其他稀土元素(例如Pr,Nd)取代会降低磁晶各向异性,用MM(例如CeLa合金)取代会降低饱和磁化强度。所以在R2Co17 型合金中,Sm是最重要的、难以完全取代的稀土元素。其他稀土元素之所以引入,主要是为了获得较便宜的合金。某些重稀土元素如Er、Gd、Dy、Ho等可部分取代Sm,可制得低温度系数的RE2TM17永磁合金。一般Sm2Co17型合金中Sm的含量比化学计量比低10%~20%(质量分数)。Sm2Co17化合物虽是易C轴的,但其矫顽力还是偏低,难以制作实用的永磁合金。现在,合金在两个方面发展。一是用Fe代部分Co,提高合金的饱和磁感应强度,形成Sm2(Co10xFex)17合金系。在其基础上加入Mn、Cr等来提高磁性能,已开发Sm2(Co0.8-Fe0.05Mn0.15)17 和 Sm2(Co0.8Fe0.09 Cr0.02)17两种。它们为单相合金,矫顽力决定于反磁化畴的形核与长大的临界场。由于其磁性能的温度稳定性差,制造工艺较复杂,在工业上很少应用。二是加入Cu,利用其沉淀硬化作用,形成Sm-Co-Cu系。Cu含量的增加能急剧增大合金的矫顽力,但同时也使饱和磁感应强度很快下降,所以也难得到有实用价值的合金。于是再加入少量能提高饱和磁感应强度的Fe,形成Sm-Co-Cu-Fe系。并且还进一步加入能提高磁晶各向异性的金属(例如Zr、Ti、Hf等),形成Sm-Co-Cu-Fe-Zr系
等性能优异的永磁合金系列。部分Sm2Co17型合金的主要性能见表11。
▼表11 Sm,Co,,型合金的主要磁性能
Sm2Co17型合金的制备过程与SmCo5型合金相近。粉末经磁场取向及压制后进行烧结和热处理。以Sm(Co,Cu,Fe,Zr)z(7.0≤z≤8.5)合金为例,其烧结和热处理的工艺过程如图24 所示。
▲图24 Sm2Co17型合金[Sm(Co,Cu,Fe,Zr),(7. 0≤z≤8. 5)合金]的烧结-热处理工艺曲线及磁滞回线变化示意图
一般采用的烧结温度为1190~1220℃,时间1~2h,得到致密的合金,接着慢冷至固溶处理温度1130~1175℃,保温0. 5~10h,以获得均匀的单相固溶体,并由油淬或氩气流冷却,将固溶体组织保持到室温。为了提高矫顽力,然
后将合金置于750~850℃进行时效处理。时效的时间与合金的成分有关,含Zr低时为20~40min,高时达8~30h.时效之后不可快冷,采取控速冷却,冷速为0.3~1.0℃/min,也可进行分级时效。合金经分级时效处理的矫顽力比经一次时效的要高得多,见图25 。
▲图25 25.5Sm-Co-6Cu-15Fe-Zr 合金一级时效和多级时效时矫顽力的变化
含Zr的合金大多实行分级时效,即再在700℃保温1h,600℃保温2h,500℃保温4h,400℃保温8~10h,之后急冷至室温。含Cr较高的合金,如采用控速冷却至400℃后,一定要在此温度再时效一些时间。在经过750-850℃的时效处理后,合金的单相固溶体转变为两相的细胞状组织。胞粒为含Fe、Zr的2:17型基体相,胞壁是富Cu的1:5型沉淀相,它们之间保持一定的共格关系。合金的矫顽力就决定于沉淀相胞壁对畴壁的钉扎作用,而与两相的磁晶各向异性和畴壁能的差、胞径和胞壁宽度等有关。适当的多级时效可利用其所造成的两相成分及形态的差异的扩大,逐渐地、尽可能地提高合金的矫顽力。
3.6 稀土铁合金
稀土铁合金是20世纪80年代出现的以稀土元素(主要是钕)与铁(或铁硼)形成之金属间化合物为基体的最新型永磁合金(即钕铁硼合金)。它具有比稀土钴合金更大的剩磁(达Br=1.48T)、更高的矫顽力(达He=684.6kA/m)和最大的磁能积[达(BH)m=407.6kJ/m?],为第三代稀土永磁合金,被誉称“磁王”。这类合金的力学性能也比第二代的好,不那么容易破碎,密度也比较小(约低13%),因而更利于实现磁性元件的轻量化,薄型化,小型化和超小型化。另外,一个最大优点是原材料丰富且价格便宜,只相当于钐钴合金的1/2左右。所以钕铁硼得到了极大的重视,正在逐步取代钐钴和铝镍钴永磁合金。
NdFeB合金以Nd2Fe14B化合物为基体。Nd2Fe14B属四方晶体结构,为铁磁性多畴体相,具有很高的磁晶各向异性和优异的内票磁参量。NdFeB的磁性能主要是建立在Nd2Fe14B的这些特性基础之上的,所以合金的成分基本上设计接近于此化合物的成分。但是,单相化合物的永磁性能并非很理想。试验证明,获得最好永磁性能的合金成分必须含有比化合物更多的一些Nd和B,一般为(质量分数)约36%Nd、约63%Fe和约1%B。即合金的组织除了Nd2Fe14B化合物基体相外,还含有一定量的富Nd相和富B相。后两种相基本上为非铁磁性物质,它们的合理含量完全由试验来确定。
图26 为Nd含量对NdFeB 合金磁性能的影响。随含量的增加,富Nd相增多,有利于合金烧结,增大收缩量和致密度,使Br急剧升高。但当w(Nd)≈12%时,因非铁磁性相增多,Br开始迅速下降。合金在x(Nd)=14%~15%时获得最高Br。在Nd含量增大时HCJ一直是增长的,所以由Nd含量的控制可以调整合金的矫顽力。必须指出,Nd含量太高会促进合金晶粒长大,反而使矫顽力下降。
图26 Nd含量对NdxFe92-x-B8合金磁性能的影响
图27 所示为B含量对NdFeB磁性能的影响。
▲图27 B含量对Nd15Fe85-XBX磁性能的影响
B是促进Nd2Fe,4B相形成的关键元素,含量低于x(B)5%时,合金处于Nd2Fe14B+Nd2Fe17+Nd的三相区(见图28 )。
▲图28 Nd-Fe-B三元系(x(B)≤50%)室温截面图
其中Nd2Fe17是易基面相磁性很软,所以合金的HCJ和Br都很低。在x(B)6%~7%时合金的Br和HCJ值最佳。B过量后,过多的非磁性富B相使Br降低。为了获得最大的磁能积,合金的Nd、B的含量还是应尽可能地接近Nd12.4Fe81.6B6.1的成分。目前磁能积最高的Nd12.4Fe81.6B6.0合金的Nd和B的含量只比化合物Nd2Fe4B的相应高(摩尔分数)0.6%Nd和0.02%B。另外,提高Fe的含量能明显提高合金的磁能积(见图29)。
▲图29 NdFeB合金的磁性能随Fe含量的变化
高性能烧结NdFeB合金的磁性能见图30 。
▲图30 高性能烧结NdFeB合金磁性能
NdFeB合金目前还有不足之处。主要是热稳定性较差,居里温度偏低,磁感应温度系数和矫顽力温度系数偏高(见表12 )。
▼表12 钕铁硼合金与其他永磁铁合金温度特性的比较
这些问题的解决直接影响其全面取代稀土钴和铝镍钴合金的进程和范围。在这方面,采取合金化的途径取得了一定进展。如用Co取代部分Fe,可提高居里温度,使磁感应温度系数降低,但矫顽力也有所降低。用Dy取代部分Nd,可提高各向异性场和矫顽力,降低矫顽力温度系数,但会牺牲剩磁和磁能积。复合加入Co和Al、Co和Dy的综合效果较好。此外,少量加入Ga或Nb,也可有效地提高矫顽力和其热稳定性。合金化的NdFeB的性能见表13。
▼表13 合金化NdFeB合金的磁性能
NdFeB的另一个缺点是抗氧化和耐腐蚀性能较差。因此必须采取表面防护,如蒸镀Ni、Cr、Al金属,镀Al-Cr或Cu-Ni合金薄膜,化学沉积Ni-P镀层,涂含氟树脂或环氧树脂等效果都很好。合金中添加Al、Si、P等元素,耐蚀性可以改善,而加人V、Nb、Cr时,除了改善耐蚀性外,还可提高磁性能。
NdFeB合金一般采用与稀土钴合金类似的粉末冶金技术制备。典型工艺是将真空熔炼的铸锭破碎成平均粒度约3μm的粉末,在横向磁场中取向并压制成形,然后进行真空或氩气烧结和热处理。为了保证最好的磁性能,生产过程都采用无氧工艺,以最大限度地降低钕的氧化与损失,使合金中的氧含量不超过1500×10E-6,非磁性相的体积分数小于1%。
合金的性能对烧结和热处理工艺参数特别敏感。烧结温度越高或粉末尺寸越大,则合金的晶粒越粗大而矫顽力越低。若烧结温度过低,则烧结不完全和合金的致密度低而性能不好。所以必须选定合理的烧结温度范围。一般,NdFeB的烧结温度为1060~1100℃,与稀土元素的种类和含量有关,如含La、Ce或混合稀土时,温度应当低些。绕结之后的冷却对性能有影响,以随炉冷却的结果为好。但生产上为了避免炉冷时炉料冷却不均匀而导致产品性能不同,通常在烧结之后采取快速冷却,然后再进行适当的热处理。NdFeB在烧结并快冷的状态下磁性能不高,但可用随后的回火处理来显著提高(见图31)。
图31 NdxFe92-xB7.5合金回火前后磁性能的变化
1-烧结态 2-回火态
采用一次(或一级)磁硬化回火时,一般是将烧结合金加热至570~600℃,保温1h,然后水冷(如图32a所示)。效果较好、应用最多的是采用二级回火。其典型的回火工艺是,将烧结合金加热到900℃,保温2h,以1.3℃/min的速度控制冷却至室温,然后再加热至550~700℃,保温1h,接着水冷。二级回火也可在烧结之后不快冷至室温,而直接降温至第一级回火和第二级回火温度连续分级进行处理,如图32b所示。大量试验表明,获得最佳磁性能的一级回火温度为900℃,与合金成分的变化关系不大;第二级回火的最佳温度与合金的成分有一定关系,由试验来确定,但一般不超过700℃。
▲图32 NdFeB合金的烧结-热处理工艺曲线
a)一级回火 b)二级回火
NdFeB在烧结状态下的显微组织主要为基体相Nd2Fe14B的晶粒,其尺寸远大于其单畴粒子临界大小,晶内极少晶体缺陷,也不存在精细结构。富Nd相熔点较低,大多数以不同厚度膜片状的形式分布在基体晶界上和三叉晶界处,也有少量呈小块状和细粒状散落在基体的晶界上和晶粒内。富B相则大部分以多边形颗粒的形式存于三叉晶界和一般晶界上,个别亦会出现在晶粒内。合金的组织中还可能存在有少量氧化物(主要是Nd2O3)、富Fe物(主要是α-Fe)、外来杂质和烧结残留的空洞。热处理不会改变基体、富B相和其他杂质,热处理能改善合金的磁性能,只与其中富Nd相的形态、分布、数量等的变化有关系。关于NdFeB的矫顽力机制,多数观点认为,是反磁化畴的形核场起控制作用。富Nd相在基体晶界上合理分布能有效地减少反向畴的形核点,同时还可钉扎跨晶界的畴壁,阻碍畴壁运动。NdFeB在900℃的第一级回火处理时,晶粒表面缺陷减少,富Nd相转变为液相,并沿晶界发生合理的再分布,为随后的分解创造有利条件;而在550~700℃间进行第二级回火时,富Nd液相分解,趋于三元共晶成分,形成有利的组织形态,并使晶界上特别是在与富Nd相相接触的基体相表面上存在的BCC相结构层消失,而使合金的矫顽力值大大提高。
end
免责声明:本网站所转载的文字、图片与视频资料版权归原创作者所有,如果涉及侵权,请第一时间联系本网删除。
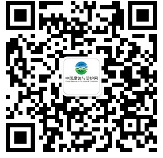
官方微信
《中国腐蚀与防护网电子期刊》征订启事
- 投稿联系:编辑部
- 电话:010-62316606-806
- 邮箱:fsfhzy666@163.com
- 中国腐蚀与防护网官方QQ群:140808414