高速钢是高速工具钢的简称,俗称“锋钢”(因为在空气中也能淬硬,也称“风钢”)。自1898年美国人Fred W?Taylor 及其助手 M?Whiet发明高速钢至今,已走过双甲年华。纵观目前世界上所有的钢种,无论其化学成分、组织、性能之间的复杂关系,还是冶炼、浇注、锻造、辊轧、拉拔、塑性成形和热处理等整个制造过程的难度,高速钢无疑使最难搞的钢种之一。有人说“高速钢奥妙无穷”,也有人说“高速钢变化莫测”。笔者1968年大学毕业后从事高速钢热处理整整50个春秋,积累了比较丰富的实践经验,同时记录了不少失败的教训,现总结出高速钢热处理宝典五则,与同仁们共享,不妥之处请指正。
1.高速钢分级淬火用盐浴
从中国有高速钢盐浴加热淬火以来,就沿用前苏联的5-3-2配方(质量分数,%),即50BaCl2+30KCl+20NaCl,熔点温度560℃,使用温度580~620℃。对于有效尺寸在20mm以下的工具或HSS钢制件,均可达到65HRC以上的高硬度;HSS-E钢制件均可达≥66HRC。我国的工具行业,使用这个分级淬火工艺,创造一个又一个省优、部优、国优,说明它极具生命力。
时代在发展,技术在进步,随着人们对冷却速度重要性认识的深化,发现工件在800?1000℃的平均冷却速度<7℃?s,将有碳化物析出而影响硬度及其他性能,于是不惜巨资从欧美引进钙基分级盐,其配方(质量分数,%)即48CaCl2+31BaCl2+21NaCl,熔点435℃,使用温度480?560℃。国内有的厂为简化配方,改为50CaCl2+30BaCl2+20NaCl,熔点较传统钙基盐略有提高,但分级温度仍维持在480?560℃的水平。
关于Ca基盐浴技术,原苏联在20世纪40年代就公开了,50年代传到中国,60年代不少厂试用过,笔者1974?1978年在桂林工作时,也曾配过Ca基盐浴,由于当时是每周开一次炉,歇炉时间长,盐浴吸湿性太强,被迫淘汰。
有的厂对分级盐浴的冷却速度进行了现场测试,φ40mm工件在800?1000℃于550℃中冷却速度正好为7℃?s,意思说有效尺寸在40mm以下完全可以淬硬,一串φ25mm工件在500℃钙基冷却,800?1000℃的冷却速度为9℃?s。
毫无疑问,580?620℃钡基盐浴工件在1000?800℃的冷却速度肯定比480?560℃钙基盐浴要慢,当工件的有效直径在20?40mm时,钙基盐优越,但尺寸在20mm以下,没有必要换成钙基盐,关键是如何将盐浴温度控制在600℃以下。
对于直径>40mm以上的工件可采用先油冷却后转分级盐冷,然后再到硝盐中分级,这样可以保证热处理后硬度≥65HRC。至于国外的经验,本着“洋为中用、改革创新”的原则,千万不可盲从,外国的月亮不比中国的圆,中国热处理工作者有能力有智慧管好用好分级盐。
2.回火程度及其次数
高速钢淬火后必须回火,而且要及时,回火的目的有4个:
①彻底消除淬火应力。
②促使残留奥氏体充分分解。
③产生最佳的二次硬化效果。
④达到所要求的综合力学性能和良好的使用性能。
回火温度540?560℃,不管是盐浴淬火还是真空淬火,拟选用100%KNO3或100%NaNO3盐浴,保温1h。每次回火后一定要冷到室温方可进行下一次回火。回火次数一般为3次,如果回火不充分,或经等温淬火者,以及高性能高速钢制件,均要进行4次回火。
回火程度一般分三个级别,不是依回火次数为据,而是金相说了算。
一级(充分):金相上表征为黑色的回火马氏体+星星点点的碳化物。
二级(一般):个别区域或碳化物堆积处有白色区存在。
三级(不足):较大部分视场为白色区,隐约可见淬火晶粒。
欲进行蒸气处理、氧氮处理等工具需在回火温度区域表面强化者,回火程度达二级即可,这样可以节能。
检查回火程度用4%硝酸酒精溶液侵蚀,温度18?25℃,侵蚀时间2?4min,500倍显微镜下观察,以最差视场为判据。
3.二次贝氏体处理
为了提高刀具的韧性、强度和切削性能,工具厂往往采取一次贝氏体处理,即中性盐浴480?560℃分级后立即转入240?280℃硝盐浴中等温1?2h;二次贝氏体处理适用于形状极其复杂的特大型刀具(如模数>15的铣刀、滚刀以及有效厚度>100mm的有孔刀具),在第一次贝氏体处理时产生40%?50%的下贝氏体,其余是残留奥氏体及少量的碳化物,在第一次回火过程中,就有大量的残留奥氏体转变为马氏体,第一次回火出炉后不要放在空气中冷,而是直接转入240?280℃的硝盐浴中等温一定的时间,不让残留奥氏体转变成马氏体而转变成贝氏体,即所谓的二次贝氏体处理,这样可以减少和防止大型复杂刀具的开裂倾向。
二次贝氏体处理工艺虽复杂些,但对防止大型刀具热处理开裂很有好处。回火过程要缓慢升温,每次回火应低于500℃入炉,回火出炉后不准风吹,最好静冷。由于二次贝氏体处理,4次回火不一定很充分,应补充一次回火。
4.摩擦焊刀具的热处理
为了节约昂贵的高速钢,国内外普遍采用摩擦焊生产φ10mm以上的杆式刀具。摩擦焊时产生1000℃以上的高温,在焊缝两侧很小的区域产生较大的温差,焊后若直接空冷,焊缝的高速钢一侧发生马氏体转变,而结构钢一侧空冷只发生珠光体转变,由于比体积的差异,将引起很大的组织应力,以致产生开裂。为此,焊后的刀具应立即放到650?750℃的炉中保温,待料罐装满后保温1?2h退火,炉冷至500℃以下出炉空冷。如果生产量很大,不便实施上述工艺,应将焊件保温温度选择在740?760℃,保温时间延长至2?3h,使焊缝两侧充分转变成珠光体+索氏体,随后空冷再退火。
摩擦焊刀具淬火争论的焦点为是否超焊缝加热。超焊缝加热的论据:改善了焊后的原始组织,考验了焊接质量,提高了焊缝强度,充分利用了高速钢;低于焊缝加热的论据:为了防止淬火裂纹,避免质量纠纷。自焊接刀具真空淬火成功后,怀疑盐浴淬火超焊缝加热致裂的声音少了,笔者坚持超焊缝加热的观点,实践证明超焊缝加热跟淬火裂纹没有直接关系。目前工具厂大多采用低于焊缝15?20mm加热,实际上缩短了高速钢的切削长度,造成浪费,很不经济。
超焊缝加热的刀具严禁酸洗,如果一定要酸洗,必须控制好酸的浓度、酸洗的时间、酸液温度三大要素,防止氢脆。
5.深冷处理
高速钢刀具经正常淬火、回火后的组织是回火马氏体+微量残留奥氏体+碳化物。对于要不要消除残存的微量(<5%)残留奥氏体,笔者认为完全没有必要。高速钢刀具正常淬火经550?570℃×1h×3次回火后,热处理已达极致,再经深冷处理有画蛇添足之嫌。奥氏体是钢组织中极软的相,其硬度只有200HBW左右,与高速钢刀具使用硬度65?66HRC相比后可以看出,过多的残留奥氏体显然不会使刀具高硬度。日本学者饭岛一昭等通过试验认为:15%以下的残留奥氏体不会使刀具硬度下降,但能提高钢的塑性和韧性。因此,用深冷处理减少残留奥氏体对韧性肯定是有害的。自20世纪70年代开始一直到21世纪初,国内很多工具厂都曾作过高速钢刀具的冷处理和深冷处理,失败的多,成功的极少,我们嘉龙公司也做过几年的深冷处理,也未见什么成效,于是设备搁置待命。
高速钢刀具与其他超硬材料刀具相比,最大的优势是韧性稍高一点,深冷处理使残存的残留奥氏体再降低,韧性更差,岂不是向伤口上撒盐吗?
实践证明,5%以下的残留奥氏体对刀具使用没有害处。HSS钢的使用硬度65?66HRC,HSS-E钢的使用硬度66?67HRC,在其他条件都相同的情况下,硬度高者磨损少,刀具的耐用度就高。由此可以判断,会降低硬度的残留奥氏体显然不受欢迎。但刀具的寿命历来不以硬度高低论英雄,过高的硬度导致脆性增大,不仅不会提高寿命,反而会减少寿命。
影响高速钢刀具寿命的因素是多方面的,不能一味地追求高硬度,我们的原则是在满足韧性的前提下力求高硬度。经验表明,回火充分的刀具施以深冷处理,基本上不会增加硬度,更不会提高热硬性,反而会使韧性下降。国内有一些工具厂对部分刀具增加深冷处理,比如剃齿刀、小模数滚刀之类,其目的是消除应力、稳定尺寸,因为两者是要以内径定心的,希望刀具在使用过程中,内孔不发生尺寸变化。还有一些高速钢制高端量具、模具进行深冷处理,目的也是稳定尺寸。
从以上分析不难发现,高速钢经正常的淬火、回火后,组织中有微量的残留奥氏体,对刀具的使用及综合力学性能并无大碍,是否一定要进行深冷处理?这个有争议的问题,有待大量的试验数据及应用实例佐证,但笔者经试验持反对观点。国内数百家工具制造厂无人问津就是一个有力论据。铺天盖地地报道,基本上是大学、研究所的科研成果或实验室的产物,但到面上推广就失败,所谓的回火新工艺,都是昙花一现,在大生产中广泛应用的还是550?570℃×1h×3次的成熟工艺,实践是检验真理的唯一标准,任何新工艺都必须经得起实践生产的考验。全国的工具厂都盼望有指导生产的热处理新工艺涌现,不喜欢“花拳绣腿”式的表演。
高速钢热处理太深奥了,但只要我们认真对待,敢于探索,反复实践,大胆改革创新,就一定能制造出高质量、高寿命的刀具,为振兴机械工业做出热处理人应有的贡献。
免责声明:本网站所转载的文字、图片与视频资料版权归原创作者所有,如果涉及侵权,请第一时间联系本网删除。
相关文章
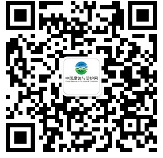
官方微信
《中国腐蚀与防护网电子期刊》征订启事
- 投稿联系:编辑部
- 电话:010-62316606-806
- 邮箱:fsfhzy666@163.com
- 中国腐蚀与防护网官方QQ群:140808414
点击排行
PPT新闻
“海洋金属”——钛合金在舰船的
点击数:7130
腐蚀与“海上丝绸之路”
点击数:5741