摘要
利用高温高压反应釜,采用失重、电化学实验和慢应变拉伸方法,结合X射线衍射 (XRD) 、扫描电子显微镜 (SEM) 和能量散射X射线谱 (EDS) 等手段研究了0~3 MPa静水压力对X70钢在模拟海洋环境中的腐蚀行为的影响。结果表明:静水压力在0~2 MPa范围内,X70钢的腐蚀形态表现为局部腐蚀,腐蚀产物主要成分为FeOOH。静水压力为3 MPa时,腐蚀形态倾向于均匀腐蚀,腐蚀产物除FeOOH外,还出现少量的Fe3O4。随着静水压力的增加,X70钢的腐蚀速率先增加后减小,在2 MPa时达到最大。静水压力在0~2 MPa范围内,X70钢SCC敏感性随着压力增加而增加;继续增加到3 MPa时,SCC敏感性有降低的趋势。X70钢在模拟海洋环境溶液中应力腐蚀开裂敏感性取决于金属表面点蚀的状况,而不一定正相关于静水压力。随静水压力的增加,X70钢表面的阳极溶解被促进,同时也促进更多的氢原子进入钢中,其应力腐蚀开裂机制是由阳极溶解和氢致开裂共同控制的混合机制。
关键词: X70钢 ; 海洋环境 ; 静水压力 ; 电化学行为 ; 应力腐蚀开裂
随着能源需求的激增和陆地资源日趋枯竭,海洋油气开发已经成为国家战略项目。海底油气管线是海洋油气集输的关键设备之一,其可靠性和完整性关系海洋石油工程的安全运行和生态环境的质量[1]。X70钢是一种低合金钢,由于其强度高,韧性好,从而成为石油和天然气经济、安全、不间断长距离输送的重要材料之一[2,3]。然而,海底油气输送服役期长,检测和维护难度高[4],一旦防护层失效或破损,金属基体将长期暴露在海水环境当中,极易引发泄漏和开裂而导致灾难性后果[5],严重威胁海底管线的安全性和可靠性。2010年墨西哥湾和2011年渤海湾的漏油事件造成的海洋危机已经给人们敲响了警钟。
海洋环境具有多元性、复杂性和可变性。海水的静水压力、含氧量、温度、光照、pH、含盐量、海水流速和海洋生物污损等均会影响海底管道的完整性[6]。其中,静水压力随水深的变化最为明显,压力对材料性能的影响也最为突出[7]。为研究静水压力对材料腐蚀行为的影响,各国学者针对不同材料开展了现场和实验室的相关研究。Bhosle等[8]在阿拉伯海3个测试站点以不同深度 (0~100 m) 对低碳钢进行了现场投样实验。结果表明,在海洋环境下,低碳钢的腐蚀速率随海水深度增加而减小,且腐蚀程度与海水温度、溶解氧呈正相关,与腐蚀产物中的有机碳和水溶性碳水化合物呈逆相关。Fozan等[9]在实验室采用浸泡试验,研究了海水水位对不同合金 (G1010碳钢、1020碳钢、304不锈钢、316L不锈钢和铜镍等) 腐蚀行为的影响。研究[9]表明,碳钢的腐蚀速率在海水、部分浸没以及完全浸没3个海水区均最高。铜镍合金625在所有3个位置的腐蚀速率最低,并且在部分浸没区观察到所有研究合金最严重腐蚀情况;随着铜镍合金中镍含量的增加,材料抗腐蚀能力增强。Beccaria等[10-14]研究了静水压力对纯镍、不锈钢和铝合金腐蚀行为的影响。结果表明:增加静水压力会增加纯镍在0.58 mol/L的NaCl溶液中的腐蚀速率和点蚀敏感性,但会降低纯镍在海水中的腐蚀速度和点蚀敏感性。这是由于在这两种溶液中形成的镍的腐蚀产物膜具有本质的区别,在0.58 mol/L NaCl溶液中形成了镍的氧化物和氢氧化物,而在海水中形成了镍的氧化物、氢氧化物和Ni-Mg碳酸盐。当静水压力增加时,镍的氧化物会转变成可溶的氯氧化物从而促进点蚀的形成,而腐蚀产物膜中的Ni-Mg碳酸盐会增加膜的覆盖能力和抗点蚀能力。杨延格等[15,16]采用扫描电镜 (SEM) 和有限元分析 (FEA) 研究了Ni-Cr-Mo-V高强度钢在不同静水压力下的腐蚀行为。结果表明,Ni-Cr-Mo-V高强度钢的腐蚀坑源于钢中的夹杂物 (Al2O3和MnS),随着静水压力的增加,平行于钢表面的凹坑扩展速率增大,相邻凹坑合并速率加快,高静水压力下腐蚀是电化学腐蚀与弹性应力相互作用的结果。刘斌等[17]研究了静水压力对Ni表面钝化膜生长和点蚀行为的影响,表明在高静水压力作用下,Ni表面形成钝化膜的能力变弱,而点蚀敏感性提高。Yang等[18]研究了静水压力对两种低合金钢腐蚀行为的影响,表明深海静水压力加速了低合金钢的阳极溶解速率。Sun等[19]研究了静水压力对低合金钢在模拟海洋环境的腐蚀影响。结果表明,在整个浸泡过程中,在浸泡初始阶段 (前5 d),3.5 MPa静水压力时的腐蚀速率明显高于0.1 MPa时的,随后两种压力之间无明显差异;15 d后,3.5 MPa时的腐蚀速率仅略高于0.1 MPa时的腐蚀速率,这可能与高压下Cl-吸附的增强有关。Sun等[20]还表明Al-Zn-In-Mg-Ti合金在深海中的腐蚀速度加快,这主要是由于阴极过程的加速;Al-Zn-In-Mg-Ti合金牺牲阳极在深海中的效率急剧下降,这与重量损失和放电容量的增加有关。当在深海中对同一受保护钢进行阴极保护时,至少需要22%以上的Al-Zn-In-Mg-Ti牺牲阳极才能达到与浅海中相同的设计使用寿命。
尽管上述工作涉及了钝性材料、活性溶解材料以及牺牲阳极材料深海腐蚀行为的研究内容[23]。但是,研究静水压力对材料应力腐蚀行为的鲜有报道,尚不能满足对深海环境材料应力腐蚀规律和电化学反应机制的探索。研究[22,23]表明,高强钢在深海环境中应力腐蚀开裂 (SCC) 敏感性较高;静水压力的增加提高了Cl-活性以及Cl-渗透到钝化膜、氧化物,导致坑起始点的形成,金属的SCC敏感性增加。然而受制于高压环境下电化学及应力腐蚀实验设备,相关研究还鲜有报道。2018年我国南海气田海域完成195 km的海底管线铺设,是我国迄今为止自主铺设的最长海底管线,作业水深3000 m[24]。因此研究静水压力对海洋油气管道腐蚀性行为的影响机理具有重要的理论及实际意义。
1 实验方法
实验材料为X70钢,其化学成分 (质量分数,%) 为:C 0.045,Si 0.26,Mn 1.48,S 0.001,P 0.017,Cr 0.031,Ni 0.16,Mo 0.23,Nb 0.033,Cu 0.21,Fe余量。X70钢金相组织如图1所示,由针状铁素体和珠光体组成。线切割电化学实验试样尺寸为Φ3 mm×10 mm;浸泡实验试样尺寸为10 mm×50 mm×3 mm;慢应变速率拉伸实验 (SSRT) 试样尺寸如图2所示。实验前将试样编号并将试样测试区域表面用水砂纸从80#打磨至2000#,然后用丙酮去掉表面的油污,用去离子水清洗后吹风机吹干待用。
图1 X70钢的显微组织图
图2 慢应变速率拉伸实验试样示意图
用NaCl分析纯和去离子水配置浓度为3.5% (质量分数) 的NaCl模拟海水溶液,实验前向腐蚀介质通入高纯N2除氧至溶液中含氧量为2 mg/L。浸泡实验在高温高压磁力反应釜内进行,高压釜内共放入4个平行试件,实验时间为7 d (168 h)。实验中静水压力分别为0、1、2和3 MPa,温度为室温。实验结束后取出试样,其中3个试样清除腐蚀产物后进行失重测量,剩余1个用SU-8010型扫描电子显微镜 (SEM) 进行腐蚀形貌观察,并对对腐蚀产物进行X射线衍射 (XRD,D8 Advance) 和能量散射X射线谱 (EDS) 分析。失重测试采用BSA224S电子天平对腐蚀前后的试样进行测量,3个试样测量得出的数据取平均值,再利用如下公式计算不同条件下的腐蚀速率:
式中,Va为平均腐蚀速率 (mm/a),ΔW为质量损失 (g),S为试样的腐蚀面积 (cm2),t为腐蚀时间 (h)。
电化学测试在动态电化学腐蚀实验釜中进行。采用三电极体系,工作电极为X70钢,辅助电极为Pt电极,参比电极是外置Ag/AgCl电极。实验的静水压力与浸泡实验相同,温度为室温。测试在CHI660C电化学工作站上完成。动电位极化扫描范围为-1.0~0.5 V,扫描速率为0.667 mV/s。电化学阻抗谱 (EIS) 测量频率范围为105~10-1 Hz,交流激励信号为10 mV,测试结果采用ZSimpWin软件进行拟合。本文实验所有电位均相对于参比电极电位 (SCE)。
慢应变速率拉伸实验 (SSRT) 在YYF-50慢应变速率应力腐蚀试验机上进行,拉伸试样取中间段15 mm进行标记,记录拉伸区域的长、宽和厚度。将拉伸试样放在容器中,使试样表面状态达到稳定后,在相应的压力 (0~3 MPa) 和环境 (3.5%NaCl溶液) 下先快速拉伸到300 N,其后以10-6 mm/s的拉伸速率对其进行拉伸。测量试样断口的截面面积和试样的延伸量,计算试样的断面收缩率和延伸率。断口用除锈液超声清洗,酒精擦拭、吹干,对断口及侧面形貌用 (FESEM) 场发射电子扫描显微镜进行观察。
材料的应力腐蚀敏感性指标用断面收缩率ψ、延伸率δ和断裂时间t来衡量:
其中,A0和A分别为试样原始横截面积和断后横截面积 (mm2),L0和L分别为试样原始长度和断后长度 (mm)。
2 结果与讨论
2.1 失重实验
采用失重法得到X70钢在不同静水压力下的腐蚀失重速率计算结果如图3所示。可以看出,随着静水压力增大,X70钢腐蚀速率先增大后减小,2 MPa时腐蚀速率最大。在0,1和3 MPa时,X70钢的腐蚀速率分别为0.02,0.03和0.07 mm/a;而在2 MPa时,X70钢的腐蚀速率则达到0.11 mm/a。
图3 X70钢在不同静水压力条件下的腐蚀速率
2.2 不同压力条件下的腐蚀形貌特征
2.2.1 宏观腐蚀形貌及XRD结果
图4为X70钢在不同静水压力条件下浸泡168 h后的宏观腐蚀形貌。可以看出,在0 MPa时局部区域未腐蚀,而1,2和3 MPa压力下试样均发生了腐蚀,且随压力增加,试样表面颜色加深。
图4 X70钢在不同静水压力条件下的腐蚀形貌
为了确定腐蚀产物的具体成分,对腐蚀产物进行了XRD分析,结果见图5。可以看出,在4个静水压力条件下,腐蚀产物均主要为FeOOH,其中3 MPa时有少量的Fe3O4。
图5 X70钢在不同静水压力条件下腐蚀168 h后的XRD谱
2.2.2 SEM及EDS结果
图6为X70钢在不同静水压力条件下浸泡168 h后带有腐蚀产物的SEM和EDS结果。由图6a可见,0 MPa时试样表面生成的腐蚀产物呈片状,较为致密;1 MPa时 (图6b),试样表面有腐蚀产物覆盖,但在膜层上有颗粒状产物堆积;2 MPa时 (图6c),腐蚀产物明显增厚,且呈条状,在整个表面均匀覆盖;3 MPa时 (图6d),腐蚀产物相较于2 MPa要少,且试样表面有明显的颗粒状产物。EDS结果表明,腐蚀产物膜主要为Fe的氧化物和氯化物,3 MPa时颗粒状腐蚀产物中Cl含量显著增加。图7为X70钢在不同静水压力下去除腐蚀产物后的SEM图。可以看出,X70钢在模拟海洋溶液中发生了腐蚀并伴随有点蚀。0~2 MPa时 (图7a~c),随静水压力增加,表面腐蚀程度增加,点蚀坑尺寸增加;3 MPa时 (图7d),点蚀坑较2 MPa明显减小,表明随静水压力增加,X70钢表面腐蚀形貌由点蚀趋向于均匀腐蚀。Yang等[16]认为这是由于静水压力提高了亚稳态点蚀的起始速率,降低了亚稳态点蚀的生长概率,导致了高静水压力下的金属的耐蚀性更均匀。
图6 X70钢在不同压力下腐蚀168 h后的SEM形貌和EDS谱
图7 X70钢在不同静水压力下去除腐蚀产物后的SEM形貌
在3.5%NaCl溶液中,X70钢在腐蚀开始阶段,Fe不断发生阳极溶解,反应界面附近Fe2+浓度较高,因此,在较短的时间内会在电极表面形成一层较薄的Fe(OH)2腐蚀产物膜:
但Fe(OH)2膜是一种疏松且多孔的腐蚀产物层,容易在空隙内形成局部活化点,且溶液中存在的Cl-更容易通过这些孔隙富集到阳极活化点附近,导致膜内局部Cl-浓缩,使该处腐蚀产物膜的动态平衡受到破坏[25],电极腐蚀速率增大,从而形成点蚀。Fe(OH)2膜不稳定,有O2存在时,Fe(OH)2能被氧化成为Fe(OH)3,进而转变成更稳定的腐蚀产物FeOOH:
另外,在3 MPa压力条件下试样的XRD还测出有Fe3O4,这是因为溶液中多余的Fe2+与FeOOH反应在试样表面生成Fe3O4:
2.3 电化学实验
2.3.1 动电位极化曲线
X70钢在不同静水压力条件下的极化曲线分别见图8。从图中可以看出,各条件下极化曲线差别不大,这说明高静水压力并没有改变材料的腐蚀历程;在0~3 MPa范围内,静水压力对腐蚀速率影响不显著。自腐蚀电位Ecorr随静水压力增加先降低后增加,表明腐蚀的热力学倾向先增加后减小。不同静水压力下的极化曲线均表现为活化溶解,表明海洋环境中X70钢的阳极溶解过程比较容易进行。1 MPa时,阳极极化曲线在最右,即阳极电流最大,但其阴极极化曲线在最左,对应的阴极电流最小;2 MPa时,阳极电流最小,阴极电流最大。结合SEM结果,此时X70钢表面腐蚀产物最厚,一定程度上抑制了阳极过程。采用Tafel外推法,对极化曲线进行拟合,结果见表1。可以看出,当静水压力从0增加至2 MPa时,腐蚀电流密度Icorr逐渐增加,此时阳极极化曲线斜率ba达到最大,阴极极化曲线斜率bc最小,表明阴极析氢反应变得更容易,反应由阳极过程控制,这与失重实验结果一致。当静水压力为3 MPa时,Icorr逐渐降低,ba逐渐减小,表明阳极过程开始变得容易进行,而bc则变化不大,表明进一步增加静水压力对阴极过程影响不大。此时ba等于bc,电化学过程表现为典型的混合控制。
图8 X70钢在不同静水压力下的极化曲线图
表1 X70钢在不同静水压力下的极化曲线拟合结果
2.3.2 电化学阻抗谱分析
X70钢在不同静水压力条件下的EIS结果如图9所示。从Nyquist图 (图9a) 可以看出,不同静水压力下的X70钢电化学阻抗图均出现感抗弧。中频感抗弧与中间产物的溶解吸收有关,而低频容抗弧与试样表面有腐蚀产物膜覆盖区的活化溶解有关[26],样品表面溶解产生点蚀,导致腐蚀产物在点蚀坑内富集。容抗弧半径大小一般与金属的耐蚀性能有关,容抗弧半径越大表明金属在该腐蚀体系下具有更好的耐蚀性。可以看出,随静水压力增加,容抗弧半径现增加后降低,在2 MPa时容抗弧半径最小,3 MPa时的容抗弧半径最大。在相位角图 (图9b) 中,0和1 MPa时观察到两个时间常数,但在2和3 MPa时出现了3个时间常数。2 MPa时相位角峰值向低频移动表明加速了阳极过程[27],各条件下相位角峰值均较小,远低于90°,表明X70钢表面的形成表面膜完整性较差。在|Z|-f图 (图9c) 中,在低频区,阻抗值|Z|随着静水压力的增大先减小后增加,说明静水压力从0 MPa增大到2 MPa,电化学过程被静水压力加速。继续增大静水压力至3 MPa,在低频区阻抗|Z|随着静水压力的增加而增加,表明电化学过程受到抑制。
图9 X70钢在不同静水压力下的EIS图
采用图10所示的等效电路对实验结果进行拟合,结果见表2。其中,Rs是溶液电阻,Qf和Rf分别是与腐蚀产物膜有关的电容和电阻,Qdl是工作电极与电解质之间电容 (双电层电容),Rct表示电荷转移电阻,L表示中间产物吸收形成的电感,RL是电感电阻。从表2结果可见,表面膜电阻Rf在2 MPa时最小,表明腐蚀产物膜不具有保护性;此时Rct也达到最小值,即电化学反应最容易进行。增加压力至3 MPa时,膜电阻Rf和Rct均增大,表明3 MPa下材料表面形成的腐蚀产物膜有更高的保护作用[25],从而降低了材料的腐蚀速度。
图10 X70钢在不同静水压力条件下的EIS等效电路图
表2 X70钢在不同静水压力条件下的电化学阻抗拟合结果
2.4 SSRT实验
图11是X70钢在不同静水压力下的应力-应变曲线。试样在弹性形变阶段应力应变是呈正比的线性阶段,在实验设定条件下曲线没有明显区别。X70钢的抗拉强度在0和1 MPa时没有区别,随着静水压力进一步增加,抗拉强度增加。X70钢的应变量随着压力的增大呈先下降后上升的趋势,在0 MPa下延伸率最大,在2 MPa下延伸率最低。
图11 X70钢在不同静水压力下的SSRT曲线图
图12是X70钢在不同静水压力下的延伸率δ和断面收缩率ψ图。在0 MPa时,X70试样δ和ψ最大,随静水压力增加,δ和ψ降低,并在2 MPa条件下达到最小值,之后,进一步增加静水压力,δ和ψ降低开始增加,这表明X70钢在2 MPa条件下模拟海洋环境中的SCC敏感性最强。
图12 X70钢在不同静水压力下的伸长率 (δ%) 与断面收缩率 (ψ%) 图
X70钢不同静水压力条件下的断口形貌SEM图见图13。可以看出,在0 MPa条件下,断口截面以韧窝为主 (图13a),有一些小的孔洞存在,无解理开裂迹象,属于典型的韧性断裂;当在1 MPa条件下,主断口形貌主要以浅韧窝为主 (图13b),断口较0 MPa时平整;当在2 MPa条件下,虽有韧窝 (图13c),但断口呈平面状,基本没有起伏;当在3 MPa条件下,断口虽较为平整 (图13d),但韧窝数量和深度增加。
图13 X70钢在不同静水压力下的断口形貌
为了更进一步探究不同静水压力对X70钢应力腐蚀开裂的影响,对X70钢在不同静水压力条件下试样侧断口进行了SEM分析,结果如图14。可以看出,在不同静水压力条件下,侧断口均存在不同程度的二次裂纹,裂纹密度或尺寸均随着压力的增加呈先增加后减小趋势。当试样在0 MPa条件下时 (图14a),裂纹内部有腐蚀痕迹,表明裂纹起源于点蚀;1 MPa时 (图14b),试样表面腐蚀较轻微,但二次裂纹破坏程度有增加,且裂纹同样起源于点蚀坑;2 MPa条件下 (图14c),裂纹长度增长并且宽度扩大,试样表面及裂纹内部出现严重的点蚀,说明压力的增加促进了裂纹的生长;当试样在3 MPa条件下时 (图14d),二次裂纹变得细长,比2 MPa条件下的裂纹小很多。这表明静水压力的增大,在一定范围内会促进X70钢的SCC过程,继续增大压力却会抑制X70钢的SCC过程。
图14 X70钢在不同静水压力下的侧断口形貌
大量研究[28-32]表明,点蚀一般是SCC的萌生处。当载荷作用于点蚀坑处时,坑内的应力将发生变化,点蚀坑的尺寸大小影响坑内的应力集中水平[33]。图7的SEM结果与图11的应力-应变曲线结果表明,X70钢在不同静水压力下的点蚀坑的尺寸与SCC敏感性呈正相关。随着点蚀坑的尺寸增加,点蚀坑内的应力集中更加明显,当应力集中达到一定程度时,点蚀坑内将出现塑性变形。此时金属的阳极溶解动力学方程可以表达如下[34]:
其中,Ip是阳极溶解电流密度,Ia是试样在无应力条件下的阳极溶解电流密度,Δ是塑性变形率,Vm是金属的摩尔体积,Δσ是加载应力的变化,σappl是施加的应力,σsc是点蚀引起的应力集中,σH为静水压力。点蚀内的应力σ由以上三项构成,当点蚀坑内的应力集中σsc达到足够大是,此处的应力σ将达到发生SCC的临界值。此外,图14结果表明,在载荷作用下,点蚀沿垂直于应力加载方向传播,并随时间增加形成裂纹。即SCC的敏感性正相关于点蚀坑尺寸。然而,当静水压力由2 MPa增加至3 MPa时,点蚀坑尺寸减小,金属表面由局部腐蚀发展到均匀腐蚀,这在一定程度上缓解了点蚀坑内的应力集中,SCC敏感性降低。因此SCC敏感性不一定正相关于静水压力,这取决于金属表面点蚀的状况。然而,继续增加静水压力,当σH增加至σsc可以忽略时,SCC敏感性将随静水压力增加而增加。
此外,阴极析氢反应产生的氢原子部分进入钢中,另一部分以氢分子形式进入到溶液中[35]。文献[36,37]表明,静水压力增加将促进氢在金属表面的吸附,进而导致更多的氢原子进入金属机体,高静水压力下金属内的氢浓度远高于常压下的氢浓度。H进入基体后,将在缺陷处富集,如点蚀和裂纹尖端。因此,点蚀坑处的氢含量要高于基体内的平均氢含量,导致断口表面出现出准解理特征。结合本实验结果,X70钢在3.5%NaCl溶液中,随静水压力增加,X70钢表面的阳极溶解被促进,同时也促进更多的氢原子进入钢中,导致SCC敏感性增加,其开裂机制是由阳极溶解和氢致开裂共同控制的混合机制。
3 结论
(1) 在3.5%NaCl溶液中,静水压力为0~2 MPa时,X70钢的腐蚀速率随着静水压力的增大而增大,X70钢的腐蚀产物主要为FeOOH;继续增加静水压力至3 MPa时,X70钢表面因生成具有保护性的Fe3O4,腐蚀速率降低。
(2) 当静水压力为0~2 MPa时,X70钢腐蚀形态表现为局部腐蚀形态;当静水压力为3 MPa时,腐蚀形态表现为全面腐蚀形态。
(3) 当静水压力为0~2 MPa时,X70钢SCC敏感性随着压力增加而增加;继续增加到3 MPa时,SCC敏感性有降低的趋势。SCC敏感性不一定正相关于静水压力,而取决于金属表面点蚀的状况。
(4) 在3.5%NaCl溶液中,随静水压力增加,X70钢表面的阳极溶解被促进,同时也促进更多的氢原子进入钢中,其开裂机制是由阳极溶解和氢致开裂共同控制的混合机制。
参考文献
1 Liu Z Y, Wan H X, Li C, et al. Comparative study on corrosion of X65 pipeline steel welded joint in simulated shallow and deep sea environment [J]. J. Chin. Soc Corros. Prot., 2014, 34: 321
1 刘智勇, 万红霞, 李禅等. X65钢焊接接头在模拟浅表海水和深海环境中的腐蚀行为对比 [J]. 中国腐蚀与防护学报, 2014, 34: 321
2 Wang G F, Chen X, Gao F J, et al. Corrosion mechanism of X70 pipeline steel in different Cl- concentration [J]. Hot Work. Technol., 2015, 44(22): 34
2 王冠夫, 陈旭, 高凤姣等. X70管线钢在不同浓度Cl-溶液中腐蚀机理研究 [J]. 热加工工艺, 2015, 44(22): 34
3 Li H L. Developing pulse and prospect of oil and gas transmission pipe [J]. Welded Pipe Tube, 2004, 27(6): 1
3 李鹤林. 油气输送钢管的发展动向与展望 [J]. 焊管, 2004, 27(6): 1
4 Chen G M. Inspection and repair optimization of offshore structure for cracks [J]. J. Univ. Petroleum, China, 2000, 24(5): 73
4 陈国明. 海洋结构裂纹检测与维修优化 [J]. 中国石油大学学报 (自然科学版), 2000, 24(5): 73
5 Hou J, Guo W M, Deng C L. Influences of deep sea environmental factors on corrosion behavior of carbon steel [J]. Equip. Environ. Eng., 2008, 5(6): 82
5 侯健, 郭为民, 邓春龙. 深海环境因素对碳钢腐蚀行为的影响 [J]. 装备环境工程, 2008, 5(6): 82
6 Cao P, Zhou T T, Bai X Q, et al. Research progress on corrosion and protection in deep-sea environment [J]. J. Chin. Soc. Corros. Prot., 2015, 35: 12
6 曹攀, 周婷婷, 白秀琴等. 深海环境中的材料腐蚀与防护研究进展 [J]. 中国腐蚀与防护学报, 2015, 35: 12
7 Yang Z X, Kan B, Li J X, et al. Hydrostatic pressure effects on corrosion behavior of X70 pipeline steel in a simulated deep-sea environment [J]. J. Electroanal. Chem., 2018, 822: 123
8 Bhosle N B, Wagh A B. The effect of organic matter associated with the corrosion products on the corrosion of mild steel in the Arabian Sea [J]. Corros. Sci., 1992, 33: 647
9 Al-Fozan S A, Malik A U. Effect of seawater level on corrosion behavior of different alloys [J]. Desalination, 2008, 228: 61
10 Beccaria A M, Poggi G, Arfelli M, et al. The effect of salt concentration on nickel corrosion behaviour in slightly alkaline solutions at different hydrostatic pressures [J]. Corros. Sci., 1993, 34: 989
11 Beccaria A M, Poggi G, Castello G. influence of passive film composition and sea water pressure on resistance to localised corrosion of some stainless steels in sea water [J]. Br. Corros. J., 1995, 30: 283
12 Hamdy A S, Beccaria A M, Temtchenko T. Corrosion protection of AA6061 T6 by fluoropolymer coatings in NaCl solution [J]. Surf. Coat. Technol., 2002, 155: 176
13 Beccaria A M, Poggi G. Influence of hydrostatic pressure on pitting of aluminium in sea water [J]. Br. Corros. J., 1985, 20: 183
14 Beccaria A M, Fiordiponti P, Mattogno G. The effect of hydrostatic pressure on the corrosion of nickel in slightly alkaline solutions containing Cl- ions [J]. Corros. Sci., 1989, 29: 403
15 Yang Y G, Zhang T, Shao Y W, et al. Effect of hydrostatic pressure on the Corrosion behaviour of Ni-Cr-Mo-V high strength steel [J]. Corros. Sci., 2010, 52: 2697
16 Yang Y G, Zhang T, Shao Y W, et al. New understanding of the effect of hydrostatic pressure on the corrosion of Ni-Cr-Mo-V high strength steel [J]. Corros. Sci., 2013, 73: 250
17 Liu B, Zhang J, Zhang T, et al. Influence of deep-sea environment on corrosion behavior of pure nickel-Ⅱ-stochastic analysis approaches to pitting of pure nickel under hydrostatic pressure [J]. Corros. Sci. Prot. Technol., 2010, 22: 85
17 刘斌, 张杰, 张涛等. 深海环境对纯镍腐蚀行为的影响Ⅱ-利用随机分析方法研究纯镍在静水压力下的点蚀行为 [J]. 腐蚀科学与防护技术, 2010, 22: 85
18 Yang Z X, Kan B, Li J X, et al. Pitting initiation and propagation of X70 pipeline steel exposed to chloride-containing environments [J]. Materials, 2017, 10: 1076
19 Sun H J, Liu L, Li Y, et al. Effect of hydrostatic pressure on the corrosion behavior of a low alloy steel [J]. J. Electrochem. Soc., 2013, 160: C89
20 Sun H J, Liu L, Li Y, et al. The performance of Al-Zn-In-Mg-Ti sacrificial anode in simulated deep water environment [J]. Corros. Sci., 2013, 77: 77
21 Ding K K, Fan L, Guo W M, et al. Deep sea corrosion behavior of typical metal materials and research hotspot discussion [J]. Equip. Environ. Eng., 2019, 16(1): 117
21 丁康康, 范林, 郭为民等. 典型金属材料深海腐蚀行为规律与研究热点探讨 [J]. 装备环境工程, 2019, 16(1): 117
22 Du C W, Li X G, Liu Z Y, et al. Stress corrosion cracking susceptibility of X70 steel in simulation deep sea environment [A]. Conference Record of 2014 Marine Materials Corrosion and Protection Conference [C]. Beijing, 2014
22 杜翠薇, 李晓刚, 刘智勇等. X70钢在模拟深海环境中的应力腐蚀开裂敏感性研究 [A]. 海洋材料腐蚀与防护大会 [C]. 北京, 2014
23 Zhang T, Yang Y G, Shao Y W, et al. A stochastic analysis of the effect of hydrostatic pressure on the pit corrosion of Fe–20Cr alloy [J]. Electrochim. Acta, 2009, 54: 3915
24 Luo Y Y. CNOOC: completed the independent laying of the longest submarine pipeline in China [J]. Petrol. Knowl, 2018, (2): 22
24 骆秧秧. 中国海油: 完成我国最长海底管线自主铺设 [J]. 石油知识, 2018, (2): 22
25 Sun H J, Liu L, Li Y, et al. Corrosion behavior of a high strength low alloy steel under hydrostatic pressure in deep ocean [A]. Conference Record of the 6th China Corrosion Conference Yinchuan [C]. Yinchuan, 2011
25 孙海静, 刘莉, 李瑛等. 低合金高强度钢在深海静水压力环境中腐蚀行为的研究 [A]. 第六届全国腐蚀大会论文集 [C]. 银川, 2011
26 Li J, Chen X, Li B W, et al. Effect of CO2 partial pressure on corrosion of 20 steel in oil-gas gathering and transporting [J]. J. Mater. Sci. Eng., 2018, 36: 589
26 李建, 陈旭, 李博文等. 20钢在集输系统中不同CO2分压下的腐蚀行为 [J]. 材料科学与工程学报, 2018, 36: 589
27 Liu Z Y, Jia J H, Du C W. Corrosion behavior of X80 and X52 steels in simulated seawater environments [J]. J. Chin. Soc. Corros. Prot., 2014, 34: 327
27 刘智勇, 贾静焕, 杜翠薇. X80和X52管线钢在模拟海水环境中的腐蚀行为与规律 [J]. 中国腐蚀与防护学报, 2014, 34: 327
28 Yao X F, Xie F Q, Wu X Q, et al. Effects of Cl- concentration on stress corrosion cracking behaviors of super 13Cr tubing steels [J]. Mater. Rev., 2012, 26(18): 28
28 姚小飞, 谢发勤, 吴向清等. Cl-浓度对超级13Cr油管钢应力腐蚀开裂行为的影响 [J]. 材料导报, 2012, 26(18): 28
29 Song B Q, Chen X, Ma G Y, et al. Effect of SRB on SCC behaviour of X70 pipeline steel and its weld joint in near-neutral pH solution [J]. Trans. Mater. Heat Treat., 2016, 37(4): 122
29 宋博强, 陈旭, 马贵阳等. SRB对X70钢及其焊缝在近中性pH溶液中SCC行为的影响 [J]. 材料热处理学报, 2016, 37(4): 122
30 Chen X, Wu M, He C, et al. Effect of applied potential on SCC of X80 pipeline steel and its weld joint in Ku'erle soil simulated solution [J]. Acta Metall. Sin., 2010, 46: 951
30 陈旭, 吴明, 何川等. 外加电位对X80钢及其焊缝在库尔勒土壤模拟溶液中SCC行为的影响 [J]. 金属学报, 2010, 46: 951
31 Rhouma A B, Sidhom H, Braham C, et al. Effects of surface preparation on pitting resistance, residual stress, and stress corrosion cracking in austenitic stainless steels [J]. J. Mater. Eng. Perform., 2001, 10: 507
32 Zhu M, Du C W, Li X G, et al. Effect of AC on stress corrosion cracking behavior and mechanism of X80 pipeline steel in carbonate/bicarbonate solution [J]. Corros. Sci., 2014, 87: 224
33 Wang H T, Han E-H. Simulation of metastable corrosion pit development under mechanical stress [J]. Electrochim. Acta, 2013, 90: 128
34 Yang Z X. Study of corrosion and stress corrosion cracking of X70 pipeline steel in simulated deep-sea environment [D]. Beijing: University of Beijing Science and Technology China, 2017
34 杨子旋. X70钢在模拟深海环境中腐蚀及应力腐蚀行为研究[D]. 北京: 北京科技大学, 2017
35 Moayed M H, Newman R C. The relationship between pit chemistry and pit geometry near the critical pitting temperature [J]. J. Electrochem. Soc., 2006, 153: B330
36 Yang Z X, Kan B, Li J X, et al. A statistical study on the effect of hydrostatic pressure on metastable pitting corrosion of X70 pipeline steel [J]. Materials, 2017, 10: 1307
37 Xiong X L, Tao X, Zhou Q J, et al. Hydrostatic pressure effects on hydrogen permeation in A514 steel during galvanostatic hydrogen charging [J]. Corros. Sci., 2016, 112: 86
免责声明:本网站所转载的文字、图片与视频资料版权归原创作者所有,如果涉及侵权,请第一时间联系本网删除。
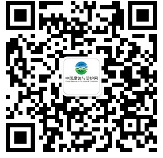
官方微信
《中国腐蚀与防护网电子期刊》征订启事
- 投稿联系:编辑部
- 电话:010-62316606-806
- 邮箱:fsfhzy666@163.com
- 中国腐蚀与防护网官方QQ群:140808414