一. 基本概念
1. 腐蚀的定义:
腐蚀是材料与环境反应而引起的破坏或变质。更广泛地讲是指除了单纯机械破坏以外的材料的一切破坏。
按照此定义包括橡胶老化、金属的高温氧化、塑料发胀或开裂、 木头腐烂、花岗岩风蚀、水泥剥离脱落等现象均属于腐蚀。在石化领域,腐蚀更多地集中于金属设备和管道。
2. 腐蚀的分类
腐蚀的分类方法很多,简介如下:
2.1 按照腐蚀破坏过程分类
可分为化学腐蚀(例如:金属的高温氧化、塑料和橡胶在阳光下的老化开裂)和电化学腐蚀(包括换热器腐蚀穿孔、埋地管道腐蚀泄漏等)两种。
2.2 按照腐蚀环境分类
可分为化学介质腐蚀、大气腐蚀、土壤腐蚀、海水腐蚀等。
2.3 按照腐蚀的破坏形态分类
可分为均匀腐蚀和局部腐蚀两大类。
其中局部腐蚀又分为以下10个类别:
① 小孔腐蚀(又称点腐蚀);
② 斑点腐蚀;
③ 电偶腐蚀;
④ 应力腐蚀;
⑤ 晶间腐蚀;
⑥ 选择性腐蚀;
⑦ 氢脆;
⑧ 磨损腐蚀;
⑨ 细菌腐蚀;
⑩ 其他局部腐蚀(包括:缝隙腐蚀、垢下腐蚀、浓差腐蚀、丝状腐蚀等)。
二. 防腐蚀的基本方法
根据腐蚀的定义和机理,防腐蚀的方法也应从材料和环境两方面着手。主要包括三个方面的手段:
① 合理地选材(包括复合材料)及结构设计;
② 改变环境(腐蚀介质的控制和处理,也称工艺防腐措施);
③ 电化学保护。
1. 合理选材及结构设计
合理选材及结构设计是腐蚀控制最重要的方法。
选材必须与实际环境和工作条件相结合来考虑,并不是耐腐蚀性最好的材料就是最佳选择。最优秀的选材是根据材料和腐蚀介质之间的最佳耐蚀性和最低费用以及安全性能进行的合理组合。例如:不锈钢-硝酸,碳钢-浓硫酸,蒙乃尔-氢氟酸,铅-稀硫酸、硬橡胶-盐酸等均是最佳组合。有时选材不当往往会造成灾难性的后果。例如:在卤素离子、连多硫酸等腐蚀介质存在的情况下选择通常条件下耐蚀性能不错的奥氏体不锈钢极有可能发生点蚀或应力腐蚀,造成设备突然穿孔或破裂。
另一种经济有效的选材方法是选择复合结构的材料。例如:钢制设备表面的防腐层(包括防腐涂料、电镀层、化学镀层、渗铝层、渗锌层、金属喷涂、复合钢板、橡胶衬里、玻璃钢衬里等)均有较好的应用效果。
合理的结构设计也十分重要。例如设计时要考虑易于清洗排放不留死区,易腐蚀的部件应易于更换或材质升级,要避免应力集中、直接冲刷、局部温度不均匀、局部气化、异种金属连接等。
2. 改变环境(腐蚀介质的控制和处理,也称工艺防腐蚀措施)
改变环境常用的方法包括:
① 降低温度;
② 降低流速;
③ 去 除腐蚀介质或氧化剂(包括电脱盐、脱酸、加入中和剂);
④ 改变介质浓度(包括高硫高酸值原油的掺炼);
⑤ 使用缓蚀剂(包括水处理药剂、工艺缓蚀剂等)。
3. 电化学保护
电化学保护是利用外部电流(包括外加电流和牺牲阳极)控制被保护设备的腐蚀电位处于非极化区而得到保护。在海港设施、埋地管道、石油储罐内防腐等方面使用效果显著。
三. 石化企业常见腐蚀现象及应对措施
1. 化工大气腐蚀
由于石化企业自身有大量的腐蚀性气体排放,装置区的腐蚀一般相对较重。
对于化工大气腐蚀一般采用镀锌金属构件(包括镀锌铁皮、镀锌电缆槽盒、镀锌灯杆等)或者涂料防腐的方法进行防护。常用的涂料包括环氧树脂类、醇酸树脂类、氯磺化聚乙烯、氯化橡胶、过氯乙烯、聚氨酯类、氟碳涂料、富锌涂料、含铝粉涂料等。涂料的品种选用应根据环境条件、施工条件、耐久性、价格等因素综合考虑。
2. 土壤腐蚀
土壤腐蚀因地质条件不同和区域不同以及杂散电流的干扰腐蚀率可能相差数十倍。一般有效的防护方法是覆盖层防腐(包括传统的石油沥青、环氧煤沥青、煤焦油磁漆涂料玻璃钢结构防腐层以及近年开发的热融结环氧粉末、聚乙烯胶带、三层聚乙烯、硬质聚氨酯泡沫塑料防腐等结构)。各种防腐结构性能对比详见附表。
对关键长输管道也可采用阴极保护技术。阴极保护技术进行专门讲座。
3. HCl-H2S-H2O体系腐蚀
这种腐蚀主要是由于原油中所含的盐分(CaCl2、MgCL2)水解形成盐酸并原油中的含硫物质分解产物H2S一同形成酸性腐蚀环境。主要发生在常压塔顶及挥发线、空冷器、塔顶冷却器等部位,是一种典型的液相部位均匀腐蚀。
通常的防腐措施包括工艺防腐措施“一脱三注”(电脱盐、塔顶挥发线注水、注氨、注缓蚀剂),以及换热器进行涂料防腐等。有时也采用复合衬里不锈钢(碳钢+0Cr13)。电脱盐效果好坏是决定防腐效果的最关键因素。一般要求二级电脱盐后的含盐量低于2.5mg/L。
4. 湿硫化氢腐蚀
在二次加工装置及储运系统中,由于原油中的硫化物分解产生大量的H2S,在有水存在的情况下在常温条件下易造成设备材料发生氢鼓包和硫化氢应利腐蚀开裂。易发生部位是催化装置的吸收稳定系统和液化气储罐。尤其是高强钢材料在此种环境下更易出现开裂问题。
通常的防护措施包括:
① 控制硫化氢浓度低于50ppm;
② 控制PH值大于7;
③ 去除水分;
④ 提高温度至65℃以上;
⑤ 控制介质中的Cl-、CO32-、CN-等有害离子浓度;
⑥ 消除材料的残余应力,包括避免冷加工、控制焊接残余应力等;
⑦ 控制金属材料成分和硬度,包括选择低含硫量的钢材、焊后热处理保证硬度低于HB200。
5. HCN-H2S-H2O腐蚀体系
这种腐蚀主要发生在催化装置反应系统,原料中的硫化物和含氮物质发生分解反应生成HCN和H2S,造成钢材发生均匀腐蚀、氢鼓包以及硫化物应力腐蚀开裂。这种腐蚀的特点是在材料表面会出现普鲁士蓝(亚铁氰化铁)。
通常的防护措施包括:采用水洗降低浓度以及使用铬钼钢、铁素体不锈钢等。要严格限制使用奥氏体不锈钢。
6. 高温硫腐蚀和环烷酸腐蚀
主要发生在加工高硫原油的焦化、减压、催化裂化装置的加热炉、分馏塔底部、转油线、换热器等部位。腐蚀介质是单质硫、硫化氢、硫醇、环烷酸等。在380℃时腐蚀速度最快。
控制措施主要是提高材质等级,选用铬钼钢、奥氏体不锈钢等。另外降低介质流速也十分有效。
7. 硫酸露点腐蚀
硫酸露点腐蚀主要发生在使用含硫燃料的加热炉、锅炉的尾部烟道低温部位。它是由于含硫燃料燃烧后最终形成的亚硫酸和硫酸在温度降低是发生的液相酸腐蚀,这是一种十分强烈的腐蚀,不仅对炉管、预热器、热管、管板、保温钉等金属结构件腐蚀,而且对耐火浇注料、纤维类也产生强烈腐蚀,是一种破坏性十分强烈的腐蚀方式。
控制方法最根本的是对燃料进行脱硫,确保燃料中硫含量不超标,最终控制烟气中硫含量不超标。其次提高排烟温度,使炉管或炉壁的壁温高于烟气露点温度。但是这样会牺牲一定的热效率。其三是选用耐硫酸露点腐蚀的钢种,包括ND钢等。
8. 连多硫酸腐蚀
连多硫酸(H2SxO6)是在停工期间设备表面附着的FeS与水和氧气反应生成的,它是奥氏体不锈钢发生应力腐蚀的敏感介质。最易发生在加工含硫原油的奥氏体不锈钢上,经常发生在加氢精制、加氢裂化、催化重整等装置的不锈钢设备和炉管上。这种腐蚀主要发生在设备停工检修期间。腐蚀开裂的特点是沿晶间开裂,最易发生在焊缝附近或者经过敏化温度停留过的情况下。控制方法是按照美国工程师协会(NACE)颁布的RP0170—97《奥氏体不锈钢和其他奥氏体合金炼油设备在停工期间产生连多硫酸应力腐蚀的防护》在停工中进行氮气吹扫干燥和碱洗,同时不锈钢一定要选用含稳定化元素Ti、Nb或者超低碳类别的奥氏体不锈钢。
9. 循环水腐蚀
循环水系统的腐蚀是一个涉及面很广的问题。影响循环水腐蚀的最主要因素是水质。含盐量高、硬度高、富氧、微生物含量高等因素均会增加腐蚀性。控制循环水系统设备管线的腐蚀主要从水质控制和设备管道防腐两方面入手。
水质控制主要包括通过加入各类化学试剂和必要的排污来控制循环水的硬度、温度、PH值、微生物等指标,使腐蚀控制在允许的范围内。实践证明,水质控制的好坏不同,腐蚀速率可相差百倍以上。
设备防腐方面的措施包括使用耐腐蚀的材料、利用防腐涂料、镀层进行隔离,利用牺牲阳极进行电化学保护。
四. 石化企业相关的防腐标准
1. 石油化工设备和管道涂料防腐蚀技术规范 SH 3022
2. 工业设备、管道防腐蚀工程施工及验收规范 HGJ 229
3. 埋地钢质管道聚乙烯胶粘带防腐层施工及验收规范 SY 4014
4. 埋地钢质管道环氧煤沥青防腐层施工及验收规范 SY/T 0447
5. 埋地钢制管道聚乙烯防腐层技术标准 SYT 0413
6. 钢制储罐液体环氧涂料内防腐层技术标准 SYT 0319
7. 钢制储罐氯磺化聚乙烯外防腐层技术标准 SYT 0320
8. 埋地钢质管道煤焦油瓷漆外防腐层技术标准 SYT 0379
9. 钢质石油储罐防腐蚀工程技术规范 GB 50393
免责声明:本网站所转载的文字、图片与视频资料版权归原创作者所有,如果涉及侵权,请第一时间联系本网删除。
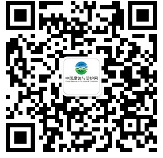
官方微信
《中国腐蚀与防护网电子期刊》征订启事
- 投稿联系:编辑部
- 电话:010-62316606-806
- 邮箱:fsfhzy666@163.com
- 中国腐蚀与防护网官方QQ群:140808414