热喷涂可磨耗封严涂层(简称封严涂层)被广泛应用在航空发动机的风扇、压气机和涡轮等部位。在发动机运行过程中,叶片尖端对封严涂层产生刮削作用,从而减小发动机径向气流间隙,减少发动机内部气体泄漏,获得最大压差,显著提高航空发动机效率并降低油耗。数据显示,航空发动机的涡轮叶尖间隙与叶片长度比每增加1%,发动机整体效率下降1.5%,油耗上升3% ;压气机径向间隙每增加0.076mm,发动机的单位油耗量增加1%。
航空发动机用可磨耗封严涂层在实际工作中与叶片、篦齿等零件刮磨,通过牺牲自身达到气路封严,保护叶片。可磨耗封严涂层由起支撑作用的金属相、润滑作用的非金属相和降低涂层硬度的孔隙组成;通常采用等离子喷涂或火焰喷涂工艺方法制备,为底层/ 面层双层结构,保证涂层结合力的同时又起到封严作用。可磨耗封严涂层的工作环境及服役特点决定了其具有质软、多孔、多相、多层等组织结构特点。
随着海上和沿海地带空军防务力量的增加,越来越多的可磨耗封严涂层需在空气湿度大、盐碱重的恶劣环境中服役,然而到目前为止,航空发动机可磨耗封严涂层的研究仍主要集中在耐冲蚀性、可磨耗性等服役性能的提高,在涂层设计方面缺乏耐蚀性的考虑,导致现役的封严涂层存在较大的海洋环境腐蚀隐患。虽然对发动机结构件腐蚀性能的研究已经有所报道,但目前针对可磨耗封严涂层腐蚀问题的研究报道还很少,尚未检索到国外相关资料。
封严涂层腐蚀研究现状
由于国外对航空发动机涂层腐蚀问题的研究保密,对于不同状态下封严涂层的腐蚀行为研究尚无文献报道。目前可查到资料仅为CFM56-7 型发动机封严涂层腐蚀失效破坏实例(图1)。这台装配于波音737 的CFM56-7 发动机一级压气机的Al 基封严涂层内部结构因腐蚀而完全破坏,涂层分层,并发生整体开裂、剥离,失去封严效果。
封严涂层的腐蚀失效形式对发动机的安全服役存在着严重的安全隐患。首先是难以发现,腐蚀通常发生在涂层内部,常规检测、观察不易发现。其次危害严重,腐蚀破坏涂层在发动机运行过程中一旦脱落,将被高速气流吸入发动机内部,严重时可能毁坏发动机内部零件,造成安全事故。
热喷涂涂层腐蚀机理
1 涂层在海洋环境中的腐蚀规律
航空发动机在飞行和停放过程中会遇到各种不同的环境,根据结构腐蚀调查,发动机在不同环境中的腐蚀特点不尽相同,但主要发生在海洋大气区内,可以得到如下规律:
(1)沿海地区的腐蚀比内地严重,离海岸越近越严重;
(2)大气污染严重地区的腐蚀比其他地区严重;
(3)南方沿海的腐蚀比其他沿海地区严重;
(4)在多雨水、多盐雾或空气湿度大、温度高的地区腐蚀比较严重;
(5)服役日历年限长的腐蚀比服役时间短的严重;
(6)连续长时间停放的腐蚀比经常使用和维护的严重。
在实验室研究阶段得出,常温水溶液环境下,部分封严涂层的腐蚀速率随环境氯离子浓度增加而增加,随温度的升高而加快,如Al-BN涂层;在中高温且潮湿环境下,涂层中金属相抗氧化能力弱是引发涂层腐蚀的主要因素,石墨相的存在是加速封严涂层金属基腐蚀速率的又一因素,如CuAl-NiC、NiCrAl-NiC涂层。
2 涂层在海洋环境中的腐蚀分类及腐蚀机理
按腐蚀发生的发动机服役状态分类,可分为飞行环境和停放环境。据统计,航空发动机服役寿命的90%为停放状态,发动机在加工、装配、运输、运行、存放和修理过程中的任何一个环节都可能发生腐蚀,尤其是在靠近沿海地区的存储及服役环境下,腐蚀问题将更为严重。
2.1 停放期间涂层腐蚀
发动机在停放时, 从封严涂层失效机理可主要分为闭塞区腐蚀和电偶腐蚀。
(1)闭塞区腐蚀
可磨耗封严涂层具有连续的多孔结构,在腐蚀性环境中,腐蚀介质能够通过孔隙向涂层内部渗透,其腐蚀机理与缝隙腐蚀以及点蚀相似。它们的共同特点是在缝隙、蚀孔内部存在“闭塞电池”。由于闭塞的几何条件,缝隙、孔内外存在对流和扩散障碍,随着腐蚀的进行闭塞区内溶液会发生贫氧、酸化、Cl- 富集等变化,腐蚀条件恶化。闭塞区内外电化学条件的差异产生自催化加速腐蚀效应。
(2)电偶腐蚀
封严涂层体系一般由可磨耗表层、连接层、基体3 部分构成,由于不同层的材料不同、结构不同、开路电位不同,因此在不同层之间、同层的不同材料之间形成电位差,满足电偶腐蚀产生的热力学因素;封严涂层因其服役性能要求具有多孔,在不同层之间由于孔隙存在可以形成导通的回路,在高电位区域与低电位区域之间形成畅通的电子通道和离子通道,满足电偶腐蚀产生的动力学因素;当热力学和动力学条件同时满足时,即可发生电偶腐蚀。
以航空发动机压气机用Al-BN封严涂层为例,在含氯介质中,涂层会发生Al-BN 表层、NiAl 连接层和不锈钢基体3 部分的电偶腐蚀。在3 部分的腐蚀电偶中,Al-BN 为阳极,优先腐蚀。通常发生电偶腐蚀的涂层,会引起表层或连接层甚至基体的破坏,从而导致整个系统涂层的破坏以及结合强度的降低。
在停放期间,海洋环境中的真菌和霉菌沉积在金属表面,加速了金属的腐蚀。另外,航空发动机在停放时将受到废气和尾气中的硫化物、氮氧化物与海洋盐雾组合成的pH 值为2.4~4.0 的酸性潮湿层腐蚀,再形成酸性液膜,加速了涂层的失效。
2.2 发动机运行时腐蚀机理
航空发动机在服役状态下,通常面临中温盐和水蒸汽综合作用腐蚀,即在航空发动机运行时,外部气体被压入发动机中,随着压气机级数的升高,气压和气体温度随之升高,在压气机区域温度可达300~700℃。当发动机在海洋环境下服役运转时,大气中的盐分将随气体被吸入发动机中,沉积在压气机叶片和机匣内表面,形成沉积盐膜。在压气机区域温度下,沉积盐以固态形式存在,一旦气氛中含有水蒸汽,涂覆于压气机部位的封严涂层将遭受中温固态盐膜和水蒸汽协同作用下的腐蚀,造成封严涂层严重的腐蚀失效。
未来发展展望
1 设计新型抗腐蚀涂层材料体系
热喷涂封严涂层中使用的复合粉体材料根据使用部位的不同而多种多样,表1 列出航空发动机上常见的可磨耗封严涂层。
随着我国航空发动机服役环境和区域范围的增加,对热喷涂可磨耗封严涂层的抗海洋腐蚀能力提出了明确要求,现有涂层材料体系已经不能满足实际使用,发展新型的抗海洋腐蚀涂层材料迫在眉睫。基于电化学腐蚀的特点,选择电极电位比部件基体材料低的的元素形成涂层,充当电化学腐蚀电池中的阳极,先失去电子不断被腐蚀,而电位较高的基体材料成为阴极,不断得到电子而受到保护。由于石墨具有较高的自腐蚀电位,会引起封严涂层内部金属相与非金属相间的电偶腐蚀,导致涂层的结合强度急剧下降;六方氮化硼具有极小的导电性,可以有效抑制涂层内不同相组成间发生的电偶腐蚀,因此中科院过程工程研究所采用六方BN替代石墨作为润滑相材料,开发新型耐腐蚀涂层粉末。
2 优化涂层结构
目前,常见封严涂层体系为基体→粘接层(底层)→功能层(面层),现阶段航空发动机粘接层通常采用镍铝或镍铝钨,面层根据涂层服役工况进行选择。当前航空发动机用封严涂层在选材时通常仅考虑涂层的使役性能,对涂层的耐腐蚀性能并未纳入其中。基体与粘接层、粘接层与功能层之间的电势对涂层的腐蚀速率有很大影响,优化涂层基体/ 粘接层/ 功能层3 者之间的电化学性能匹配,对热喷涂封严涂层的耐腐蚀性能具有重要的意义。有研究表明,将Ni5Al 粘接层替换为Ni20Al 粘结层,可以降低涂层体系电偶腐蚀过程中的电偶电位,从而抑制铝基封严涂层的自发点蚀行为,降低涂层体系腐蚀速率。
3 建立热喷涂涂层腐蚀性能测试方法
丰富封严涂层性能检测手段,完善封严涂层性能评价体系和选材体系,建立封严涂层模拟实际工况试验装置,是满足热喷涂工艺以及稳定批量供应和高质量批量生产的必要条件。目前,金属材料耐腐蚀性测试可依据ASTM G76 标准进行,而涂层的腐蚀性能测试标准及主要性能指标尚未颁布。因涂层的多孔、多相、多层结构,在腐蚀过程中呈现出多元性、复杂性等特点,不能与金属材料测试标准混用,需编制涂层专用腐蚀测试标准。目前,航空行业部分研究院所及制造单位正在累积相应数据,为编制涂层腐蚀性能测试标准进行技术储备。
结束语
随着我国航空事业的飞速发展,尤其对舰载飞机、沿海飞机等需求激增,航空发动机零部件的海洋环境腐蚀损伤及其防护研究已成为热点。需要涂层体系设计、涂层材料开发和工艺研制等领域的技术人员携手攻关,通过大量严苛的试验测试,完成耐海洋腐蚀热喷涂可磨耗封严涂层的开发。同时,对航空发动机封严涂层在海洋环境中腐蚀失效机理研究、服役寿命预测等方面均需加大科研力度,以便为设计部门提供可靠的数据支持及解决方案。另外,相关科研单位应着手准备建立涂层在海洋环境中腐蚀测试方法,完善封严涂层的海洋腐蚀性能测试技术,确保航空发动机封严涂层在海洋环境中服役寿。
更多关于材料方面、材料腐蚀控制、材料科普等等方面的国内外最新动态,我们网站会不断更新。希望大家一直关注中国腐蚀与防护网http://www.ecorr.org
责任编辑:刘洋
《中国腐蚀与防护网电子期刊》征订启事
投稿联系:编辑部
电话:010-62313558-806
邮箱:ecorr_org@163.com
中国腐蚀与防护网官方 QQ群:140808414
免责声明:本网站所转载的文字、图片与视频资料版权归原创作者所有,如果涉及侵权,请第一时间联系本网删除。
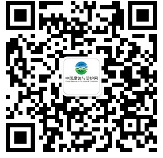
官方微信
《中国腐蚀与防护网电子期刊》征订启事
- 投稿联系:编辑部
- 电话:010-62316606-806
- 邮箱:fsfhzy666@163.com
- 中国腐蚀与防护网官方QQ群:140808414