随着人类工业化进程不断发展,煤炭、油气等化石能源大规模使用,全球气候变暖加剧,严重危及人类生存。温室气体大量排放是气候变暖的主要因素,其中尤以CO2增长最快。为积极应对气候变暖,国际能源署呼吁各国进行碳减排行动,各国积极响应并相继发布碳中和计划。2020年中国宣布“双碳”战略,力争于2030年前实现碳达峰、2060年前实现碳中和。在此背景下,以氢能为代表的能源转型技术、以新型储能为代表的新能源利用技术、以CO2捕集与利用为代表的碳减排技术等一系列示范工程相继落地。
钢管作为物料、能源输送的重要载体,是“双碳”战略相关新兴产业发展的基础物资保障,同时新兴产业的发展亦对钢管的功能和性能提出了新的需求,尤其是钢管的安全性和经济性直接关乎“双碳”战略相关的技术研发和项目建设。
《钢管》中的这篇文章以“双碳”战略中的碳捕获、利用与封存技术(Carbon Capture, Utilization and Storage,CCUS)和氢能及压缩空气储能三个重要领域发展中的用管需求为契入点,综述CO2输送管道、氢气输送管道以及压缩空气储能用注采管的应用现状、研究进展和需求,并对未来进行展望,以期为“双碳”战略下新能源用钢管的发展提供参考。
1 CCUS用CO2输送管
CCUS是将生产过程中排放的CO2进行二次利用或封存,CCUS技术在将CO2转化为具有经济效益资源的同时还利于环保,是目前唯一能够大量减少工业流程温室气体排放的手段,在应对全球气候变化中起到关键作用,受到世界各国的高度重视。
在CCUS中管道输送是连接CO2捕集端和封存/利用端不可或缺的环节。目前在CO2输送方式上,主要有罐车运输、船舶运输和管道运输,其中管道运输是CO2长距离输送最具性价比的方式,其成本约为罐车运输成本的35%,可以有效降低CCUS项目的运营成本。
管道输送CO2常采用密相或超临界态输送,这是因为密相(-56 ℃温度T为31.1 ℃,压强P为7.38 MPa)和超临界态的CO2具有低黏度、高密度特点,在管道输送过程中摩阻小、耗能少,能够实现更高的经济性和大规模输量。
01 国内外CO2输送管道建设现状
国外尤以北美地区在CCUS技术应用及CO2管网建设上经验最为丰富,世界第一条CO2输送管线在19世纪70年代于美国德克萨斯州投产,截至目前全球CO2管道里程约9000公里,其中北美地区CO2管道占比近85%,欧盟、日本、加拿大、挪威和土耳其等地区也有部分管道,根据国际能源署预测,至2050年全球CO2输送管道建设总长度将达到20万公里。
二氧化碳捕集、运输与地质封存技术委员会(CCS)对全球CO2输送管道进行了统计,如表1所示,并根据管道输送里程、设计输量等方面将其规模划分为三级,目前全球已建成的CO2输送管道约一半为超临界/密相输送,单条管道输送量最高可达28 Mt/a。
表1 全球CO2输送管道基本情况统计
国内CO2管道输送技术起步较晚,此前国内投运的CCUS项目整体规模较小,运输方式仍以低温储罐公路运输为主,近些年国内若干CO2管道输送项目逐渐建成投产,其大多为短距离、小规模输送,国内已建成CO2输送管道基本情况统计见表2。2023年“齐鲁石化-胜利油田百万吨级CCUS示范项目CO2输送管线”全线贯通,该管道全长109公里,设计压力12 MPa,采用高压常温密相输送,设计年输送量170万吨/年,该项目标志着我国第一条长距离、大规模CO2输送管线正式建成投产。
表2 国内已建成CO2输送管道基本情况统计
02 CCUS管道输送CO2技术研究进展
Part.01 输送管道失效风险控制
腐蚀是CO2输送管道主要的失效原因,常规含水环境中的CO2腐蚀是因CO2溶于水后电离产生H+,H+再与金属之间发生氧化还原反应;而在CCUS管道输送CO2中,密相或超临界态CO2具有更高的压缩性、扩散性和溶解度以及更低的黏度,且CCUS气源不可避免地混有水分、杂质气体等因素,因此CCUS中的CO2腐蚀更为复杂,输送管道的腐蚀速率在一些特定工况中甚至高达10 mm/a。
此外,管道输送密相或超临界态CO2的运行压力大都在9~20 MPa,一旦管道发生泄漏,压力会迅速释放,由于CO2气体具有强的节流膨胀效应,会导致泄漏点附近的温度急剧降低,使管道易发生低温脆裂。输送管道发生泄漏的瞬间会在泄漏点处产生向管道两端传播的减压波,相较于天然气的减压波曲线而言,CO2减压波曲线存在高压平台,更接近于管材的裂纹扩展曲线,因此管道裂纹扩展过程中更难以实现韧性止裂。
超临界/密相下的CO2腐蚀受到介质成分、运行工况等多方面因素的影响,国内外进行了大量的研究。
含水率
水在金属腐蚀中起着至关重要的作用,研究表明在绝对干燥或含水量低于临界含水量的超临界CO2气体输送中,金属管道不会发生腐蚀;然而,在CCUS实际运行中,CO2气体不可能完全干燥,当其中的含水量接近或大于临界含水量,则会引发较高速率的腐蚀。
高怡萱等统计了文献报道中X65钢在不同含水量的超临界CO2环境中的腐蚀速率,结果如图1所示,可以看出随着含水量的升高,X65钢在超临界CO2环境中的腐蚀速率逐渐增大。
图1 X65钢在不同含水量的超临界CO2环境中的腐蚀速率
Hua等对X65碳钢在50 ℃、8 MPa输送压力时不同含水量下的超临界CO2腐蚀进行了研究,得到在CO2饱和的水相、水饱和的CO2相及不饱和水的CO2相三种工况下X65钢的腐蚀速率分别为10.0 mm/a、1.4 mm/a、0.2 mm/a,而在含水量低于1600 μL/L的不饱和水的CO2相条件下未发生明显的腐蚀,说明含水量是影响CCUS中CO2输送管线腐蚀的关键因素。
杂质气体
CCUS输送的超临界CO2中可能含有多种杂质气体,主要有O2、SO2、H2S等。O2在超临界CO2腐蚀过程中会将CO2腐蚀产物FeCO3转变为Fe2O3。但是,目前对于超临界CO2环境中O2含量对管道腐蚀速率的影响研究结果存在一些差异。
Hua等研究了不同O2含量对X65钢在超临界CO2环境中腐蚀速率的影响,如图2所示,可见随着O2含量的增加,X65钢的平均腐蚀速率呈现下降趋势,然而其局部腐蚀速率却显著增大。
图2 O2含量对X65钢在超临界CO2环境中腐蚀速率的影响
Sun等的研究结果也显示当超临界CO2中的O2含量从0升高至0.1%时,X65钢的腐蚀速率从0.015 mm/a增大至0.034 mm/a。
然而Wang等的研究结果显示,随着超临界CO2中的O2含量升高,碳钢的腐蚀速率呈现先增大后减小变化趋势,如图3所示。
图3 超临界CO2环境中O2含量对管线钢腐蚀速率的影响
(Sat.指CO2中的H2O达到饱和)
超临界CO2中的杂质气体SO2对管道腐蚀的影响主要在于其与水和O2发生耦合作用,促进了酸性介质形成,使体系pH降低,加速管道腐蚀。
高怡萱等统计了杂质气体SO2对超临界CO2输送管线腐蚀的影响的部分研究结果,具体见表3。对比SO2和O2单独存在时的管道材料平均腐蚀速率结果可以看出,SO2对管线钢的腐蚀的影响要高于O2;并且当SO2与O2同时存在时,管线钢的腐蚀速率高于其任一单个杂质气体下的腐蚀速率。
表3 杂质气体SO2对超临界CO2输送管线腐蚀影响的研究结果统计
注:①指气体体积百分比;②指摩尔百分比。
杂质气体H2S也会加速超临界CO2输送管线的腐蚀,Wei 等研究结果表明在含饱和水的超临界CO2中添加0.005% H2S会导致其对X65管线钢的平均腐蚀速率和局部腐蚀速率分别提高40%和65%。
Sun等研究了H2S与O2共同存在时X65管线钢在含饱和水的超临界CO2中的腐蚀行为,结果表明含杂质气体0.1% H2S+0.1% O2时X65钢的腐蚀速率较仅含0.1% O2杂质气体时高6.5倍。
目前通过研究H2S对超临界CO2腐蚀的影响机理,认为H2S会提高管壁对水的吸附能力,增加管壁凝集水的含量,加速表面薄液膜形成,从而导致腐蚀加速。
综上所述,在超临界CO2腐蚀环境中,对管道内腐蚀影响较大的杂质主要有H2O、O2、SO2、H2S,因此控制CCUS中CO2输送管线腐蚀的关键在于控制超临界态CO2中的杂质气体含量。
严永博等统计了目前部分CCUS项目中CO2输送管道的杂质控制标准(按摩尔百分比计),其中H2O 0.063%、O2 0.007%、SOx 0.01%、H2S 0.9%。
温度和压力
在CCUS超临界态CO2输送过程中须对温度、压力进行严格控制。在低温高压工况下CO2易转变为固态导致管线堵塞;在密相或超临界态时,CO2的输送温度、压力也会影响管线腐蚀。
Hua等对比了管线钢在压力为8 MPa时的密相(35 ℃)和超临界态(50 ℃)CO2中的腐蚀行为,研究结果显示在密相CO2中管线钢发生了明显的腐蚀,而在超临界态中并未观察到腐蚀现象。
Wei等研究了X70钢在80 ℃的气相(1 MPa)和超临界态(9.5 MPa)CO2中的腐蚀行为,研究结果显示X70钢在超临界CO2中的平均腐蚀速率高于气相CO2。作者认为其原因是试样在气相CO2中时表面会快速形成致密的FeCO3腐蚀产物层,减缓基体腐蚀;而在超临界态CO2中,试样表面则优先生成非晶态腐蚀产物层,然后再逐渐转变为致密的FeCO3腐蚀产物层。
温度和压力除直接对CO2腐蚀产生影响外,还会改变杂质气体对输送管线腐蚀的影响,其作用机理更为复杂。
Part.02 输送管道应用技术
CO2输送管道主要采用高频电阻焊管(HFW),在北美地区CO2输送管道中HFW焊管占比达74%,钢级通常为X65~X80,如图4和表4所示。HFW焊管相较于其他ERW类焊管具有焊接速度快、热影响区小、使用范围广、尺寸规格宽等优点,自20世纪70年代以来,HFW技术广泛应用于输送管道建设。
图4 北美地区超临界CO2输送管道用管类型
表4 北美地区部分超临界CO2输送管道设计参数及用管情况
注:1 in=25.4 mm,1 mile=1.609344 km。
尽管HFW焊管已成为CO2输送管道的主要选材,但其仍存在失效风险。2010—2011年,Denbury公司HFW CO2输送管道发生两次泄漏事故,调查结果认为管道泄漏是由焊缝处的“灰斑”缺陷导致。
“灰斑”是高频电阻焊缝特有的缺陷,是因冷焊或过烧导致焊缝中的氧化物不能充分挤出而形成,其特征是在拉伸试样或冲击试样的焊缝宏观断口处出现无金属光泽的灰色区域。
英国焊接研究所对HFW焊管的质量进行过深入研究,提出消除焊缝“灰斑”缺陷的4 个关键因素:
① 采用优质(洁净)带钢;
② 焊接过程中需施加足够挤压力,以确保清除熔合线上的所有异物;
③ 焊缝区域需充分正火;
④ 对焊缝区域进行充分的无损检测,确保检测出所有缺陷。
由于超临界态CO2的节流膨胀效应和减压波特性,韧性控制是防止输送管道破裂失效以及止裂性能的重要指标。然而,目前对于CCUS中CO2输送管道的韧性控制并无统一标准。
2015年投产的Shell Quest CCS Pipeline项目中使用HFW焊管作为CO2输送管道,管径168.3~323.9 mm,设计压力14.79 MPa,其对材质的夏比V型冲击韧性(-45 ℃)要求为:管体平均值≥60 J,单个值≥52 J。
2020年投产的加拿大ACTL项目中CO2输送用HFW焊管设计压力为17.926 MPa,其要求Φ457 mm以下规格管体的夏比V型冲击韧性单个值≥27 J,Φ457 mm及以上规格管体的夏比V型冲击韧性单个值≥40 J。
全尺寸爆破试验是研究管道断裂控制最为直接有效的方法,国外针对CO2输送管道进行了多轮次试验,殷布泽等对国内外CO2输送管道全尺寸爆破试验进行了详细的统计分析,但是作者认为针对管道断裂过程中的裂纹扩展规律、裂纹断裂形态规律、韧-脆转变温度规律的研究仍比较缺乏。
2023年5月,我国开展了国内首次CO2管道全尺寸爆破试验,管道为X65钢级Φ323.9 mm规格HFW焊管,试验压力12 MPa,得出了试验条件下管道破裂过程中的压力变化和裂纹长度等一系列重要参数。该试验为我国掌握百万吨级CO2输送管材研制、管道设计及建设技术提供了重要的数据支撑,标志着我国在CCUS技术研究领域取得了重要的突破性进展。
03 CO2输送用管需求分析
针对CCUS中超临界/密相CO2输送用管,应重点考虑管材在耐蚀性能和防止低温脆断以及开裂后的韧性止裂要求。如前所述,尽管近些年对于超临界/密相CO2腐蚀开展了广泛而深入的研究,但对于含水率、气体杂质、温度、压力等多因素耦合作用下的超临界/密相CO2腐蚀机理仍不甚清晰,需更进一步的研究以支撑管道选材。
对于低温脆断时的启裂预防和韧性止裂技术研究,应当进行更多的全尺寸爆破试验,探索各种管材在超临界/密相CO2输送工况中的适用边界,建立涵盖运行工况与材料性能需求的数据库,为CO2输送用管标准的制定提供数据和理论基础。
2 氢气输送用管
氢能的产业化发展是我国“双碳”战略的主要着力点之一,《氢能产业发展中长期规划(2021—2035年)》中明确表明,到2025年我国可再生能源制氢量达到10~20万吨/年,实现二氧化碳减排100~200万吨/年,到2035年形成氢能产业体系,构建涵盖交通、储能、工业等领域的多元氢能应用生态。在氢能大规模应用的背景下,氢能输送作为连接上下游的通道,是氢能产业发展中的关键环节。
按照输送介质相态可将运氢方式分为气态、液态和固态3种,氢气输送方式对比见表5,目前气态储运氢应用最为广泛。气态储运氢可采用储气瓶、长管拖车和管道等方式,然而储气瓶和长管拖车运输能力有限、成本高,难以支撑氢能大规模应用需求,因此发展管道输氢是必然选择。
表5 氢气输送方式对比
01 国内外输氢管道建设现状
根据氢气纯度可将管道输氢分为纯氢输送和掺氢输送。纯氢输送一般通过新建或改造现有管道来输送高纯度氢气直接用于生产生活;掺氢输送则是利用现有的天然气管道,向天然气中掺入一定比例氢气输送,掺氢天然气既可以作为燃料直接使用,也可在末端通过纯化分离出高纯度氢气供使用。
Part.01 纯氢输送
国外输氢管道建设早、里程长,最早的长距离纯氢输送管道于1938年在德国鲁尔建成,其总里程达208 km,输送压力2.5 MPa,管材为Φ168~273 mm SAE 1016材质。目前全球纯氢输送管道总里程达4500 km,主要集中在北美和欧洲地区,约占90%以上。
表6列出了国外部分纯氢输送管道运行情况,已建输氢管道用材质普遍为低钢级的碳钢和低合金钢焊管或无缝管,超短距离输送压力最高达14 MPa,长距离输送压力普遍在10 MPa以下,大部分集中在3~5 MPa。
表6 国外部分纯氢输送管道运行情况
国内纯氢输送管道建设起步较晚,2020年以前建成的管道主要以短距离、小规模输送为主,大多服务于炼化企业,见表7。自2021年始,国内长距离、大规模输氢管道建设逐渐启动,2021年河北定州—高碑店氢气管道工程建设启动,管道总里程达164.7 km,年最大输送量为10万吨,这是全球第一条为输送燃料电池所需的氢气而建设的管线;2023年“西氢东送”输氢管道示范工程被纳入《石油天然气“全国一张网”建设实施方案》,该条管道的起点位于内蒙古自治区的乌兰察布市,终点则是位于北京市的燕山石化公司,全长400多公里,年输氢量达10万吨,并预留50万吨/年的远期提升潜力,是我国第一条跨省区、大规模、长距离的纯氢输送管道。
表7 国内部分纯氢输送管道
Part.02 掺氢输送
掺氢输送因其利用现有管道,具有启动成本低的优势,在国内外均有发展。根据国际能源署统计,目前全球约有40个天然气管道掺氢项目,国外主要有法国GRHYD、英国Hydeploy、荷兰VG2等,我国已建成的管道掺氢项目有朝阳天然气掺氢示范工程(2019年建成)、陕宁一线掺氢示范项目(2021年建成)、张家口掺氢管道示范项目(2023年建成)等。
管道掺氢输送中掺氢比例是衡量输氢能力的重要指标。表8统计了各国部分管道掺氢输送项目中的掺氢比例,欧洲稳定运行的管道掺氢输送项目中掺氢比例可达20%,国内已建成项目的掺氢比例普遍在10%以下,更高掺氢比例管道输送正在试验中,2023年397公里长的宁夏宁东天然气掺氢管道示范平台试验将掺氢比例逐步提高至24%,并维持100天运行,管道整体运行安全稳定。
表8 各国管道掺氢输送项目中的掺氢比例(部分)
02 氢气管道输送技术研究进展
Part.01 管道失效风险控制
输氢管道失效风险主要来源于氢气引起的金属管道氢脆,主要表现为管道在涉氢环境中会发生力学性能降低以及延迟开裂,国内外对于氢脆机理开展了大量研究,目前主要有氢压理论、氢致局部塑性变形理论、氢致弱键理论等。
氢脆导致管道失效是环境、材料和应力共同作用的结果。影响氢脆的环境因素有温度、氢气分压等,通常随着氢气分压升高,材料的氢脆敏感性增大;温度对氢脆敏感性的影响较为复杂,在较低温度下,氢进入材料的扩散速率慢,而在较高温度下,虽然氢的扩散速率加快,但同时也难以在材料局部富集,因此氢脆具有温度敏感区间。
影响氢脆的应力因素有外部载荷、内应力以及应力变化等,其对氢脆的影响主要是在材料局部产生高的应力集中,氢原子在应力集中处聚集并与材料发生相互作用,降低材料的力学性能,最终导致材料失效。影响氢脆的材料因素有合金成分、晶体结构、组织、晶粒尺寸等,对于输氢管道而言,通过对管材的合理设计来提高其抗氢脆性能是有效的方法。
合金成分
目前国内对于长距离输氢管道选材无专用标准,一般参考储氢容器选材,常用的输氢管道材质有4130X、30CrMo、4140和2.25Cr1Mo(V)。许多研究表明C、Mn、P、S元素对低合金钢的氢脆敏感性影响显著。C含量过高时会导致钢材在热轧状态下产生大量对氢脆敏感的马氏体组织,国内的储氢容器用钢中控制C含量≤0.35%,欧洲工业气体协会控制C含量≤0.37%;Mn元素易与P、S 形成夹杂物,同时还易在钢管内壁形成带状偏析,这些缺陷降低了管材在临氢环境中的临界应力强度因子,增大了管材的氢脆敏感性,因此需对其进行严格控制。
近些年对于微合金化制备高强度抗氢钢研究较多,其机理是在钢中添加一定量的V、Ti、Nb形成高度弥散分布的微细碳化物。这些碳化物的存在一方面能够起到析出强化作用,提高钢材的强度;另一方面可以作为氢陷阱,将扩散进入钢材内部的氢原子捕获固定,使其难以与位错、晶界等缺陷相互作用,提高钢材的抗氢脆性能。
组织结构
金属材料的微观组织是影响管线钢氢脆敏感性的重要因素,一般认为其相组成按照氢脆敏感性由低到高依次为:铁素体<珠光体(或珠光体+铁素体)<贝氏体<低碳马氏体<马氏体和贝氏体混合<孪晶马氏体。
对于管线钢而言,未经回火的原始马氏体、低温回火马氏体和回火屈氏体具有高的氢脆敏感性,在热处理时应避免此类组织,而经高温回火得到的回火索氏体和等温淬火得到的下贝氏体的氢脆敏感性低,可作为输氢管材的最终组织。
此外,热处理后得到的残余奥氏体作为软相组织能够减缓材料内部的应力集中,阻止氢致裂纹扩展,因此可以适当采用淬火配分工艺得到一定量的残余奥氏体,提高管材的抗氢致开裂性能。
夹杂物
夹杂物与基体界面极易成为氢原子在钢中的聚集位点,成为氢致裂纹起源。钢中夹杂物可按形态和大小分为A、B、C、D和DS五类,其中呈球状的A类(硫化物类)夹杂物对钢材的氢脆敏感性影响小于其余四类,炼钢时应采取适当的脱氧工艺和精炼工艺去除钢中的Al2O3和SiO2夹杂物,还可以在钢的冶炼过程中喷吹适量的Si-Ca以抑制硫化物的生长,改善其形状和分布,对于长条状的MnS夹杂可采用稀土改性,进一步提高钢材的抗氢脆性能。
宏观缺陷
输氢管道在生产制造和管道建设过程中不可避免地会在管道表面产生一些压痕、划伤等宏观缺陷,缺陷的存在将导致局部应力集中,从而影响管道的抗氢脆性能。
Holbrook等研究了缺口对压力容器用钢在高压氢气环境中力学性能的影响,如表9所示,带缺口试样的抗拉强度和断面收缩率相较于光滑试样发生了大幅度降低,这一结果表明表面宏观缺陷或将严重恶化输氢管道的抗氢脆性能。
表9 缺口对压力容器用钢在高压氢气环境中力学性能的影响
Part.02 输送管道应用技术
表10列出了目前输氢管道的常用材质牌号(钢级)及其强度要求,可以看出相关标准推荐的均为低钢级碳钢管,这是因为钢材强度低有利于提高抗氢脆性能。
表10 输氢管道常用材质牌号(钢级)及其强度要求
注:① 要求屈强比≤0.93。
美国机械工程师协会统计了Air Products公司137条输氢管道的运营情况,如图5所示,其中90%的管道为X52钢级及以下的HFW焊管,管道公称外径50.8~457.2 mm,管道运行压力85%集中在4.5~10 MPa,最高运行压力达到15 MPa。
图5 Air Products公司137条输氢管道统计
迄今国外关于氢气输送管道相关标准有欧洲标准CGA G-5.6—2005《Hydrogen Pipeline Systems》、美国标准ASME B 31.12—2019《Hydrogen Piping and Pipelines》和亚洲标准AIG A 033/14—2014《Hydrogen Pipeline Systems》,国内暂无氢气输送管道专用标准。上述标准对管道的材质性能、运行压力、建设安全性等方面作出相关建议和要求,输氢管道常用材质牌号(钢级)及其强度要求如表11所示。
表11 输氢管道常用材质牌号(钢级)及其强度要求
注:①P为设计压力,MPa;S为材料屈服强度,MPa;δ为管道壁厚,mm;dN为管道外径,mm;F为设计系数;fE为焊缝系数;fT为温度折减系数;Hf为材料性能系数。
由于长时间以来氢能市场规模较小、输氢压力低,氢气输送管材多以X52及以下钢级为主,管型主要为HFW焊管和无缝管,2020年以来氢能市场发展迅速,尤其国内输氢管道工程规划和建设里程大幅增长,对于使用高钢级管材实现大输量、高压力氢气输送的需求日益突出。
03 氢气输送用管需求分析
由于氢气具有的高危险性,现有的氢气输送用管相关标准中对于管道选材、设计及建设等方面均较为保守,管材钢级处于较低水平,X60及以上钢级应用较少,这制约了高压氢气输送的发展;因此,对高钢级管材在临氢环境中的适用性应进行系统评估。
在掺氢输送方面,国内掺氢比例普遍低于国外,提高掺氢比例对于管道安全性的影响程度也亟需研究。
在管线钢抗氢脆性能室内研究方面,常用的模拟氢环境方式有高压氢气环境和电化学阴极充氢,然而这两种方法的结果重现性较差,甚至相互矛盾,如何设计试验使室内研究条件更贴合实际工况仍需探索。
3 盐穴压缩空气储能注采用管
在“双碳”战略背景下,能源结构调整与优化是实现绿色可持续发展的主要抓手,大力发展“绿电”是政策和市场的双重要求。国内“绿电”的主要来源以水力、风力以及太阳能为主,然而电量输出不稳定且并网难等问题限制了“绿电”进一步的发展。针对这一问题,运用储能技术对电网削峰填谷成为发展“绿电”的基础技术支撑。目前储能技术主要有抽水蓄能、压缩空气储能、电池储能等,相较于其他储能方式,压缩空气储能因其储能成本低、功率大、环境影响小、运行稳定等优点,近两年迎来大规模商业化建设。
压缩空气储能是指利用风、光等波动性电力以及在电网负荷低谷期的剩余电力将空气压缩至储气容器中形成高压气体,待到用电高峰时再将高压气体释放并通过透平发电,从而提升电网调节能力和新能源消纳能力的技术。压缩空气储能的储气方式主要有盐穴、人造硐室、地面储气罐、废弃矿洞等,表12列出了国内外部分压缩空气储能项目建设情况,其中盐穴压缩空气储能因其建设成本低、周期短、资源丰富等优势,近年来在国内发展迅速。
表12 国内外部分压缩空气储能项目的建设情况
01 盐穴压缩空气储能用注采管失效风险分析
在盐穴压缩空气储能的储穴建设初期,需要对盐穴进行注水溶腔和注气排卤,在该过程中注采水含有高浓度卤化物以及氧气,井筒管柱会面临严峻的盐水腐蚀和氧腐蚀,易造成管体减薄以及腐蚀穿孔。
在运行阶段,周期性注采高达十几兆帕的压缩空气,井筒管柱面临潮湿、含盐、高压空气环境中的腐蚀以及高速气流冲蚀;此外,周期性的注采空气对管柱,尤其是螺纹接头的抗疲劳性能也提出更高要求。除上述风险外,井筒管柱还面临盐岩层蠕变、注采压力波动大、地下水侵蚀等复杂环境因素导致的失效风险。
Part.01 腐蚀失效
盐穴压缩空气储能注采用管服役环境中氧气分压高、含盐量大、湿度高、气体流速高,服役温度在30~90 ℃不等,此类腐蚀工况与油田注空气驱油时管柱所面临的工况具有一定的相似性,参考以往对油田注空气驱管柱腐蚀情况研究结果,认为盐穴压缩空气储能注采用管易发生腐蚀失效。然而,由于盐穴压缩空气储能在国内近些年才开始建设,对于如何进行室内腐蚀模拟试验来支撑管柱选材尚无标准参考,研究人员在腐蚀试验研究方法和研究结果上差异较大。
表13为盐穴压缩空气储能工况和注空气驱油工况管柱腐蚀研究结果统计,可以看出研究结果大都认为随着工况环境中的温度、氧分压、矿化度升高,碳钢管柱的腐蚀速率整体上呈现上升趋势,然而碳钢在模拟压缩空气储能和注空气驱油两种工况中的腐蚀速率研究结果差异极大,在模拟压缩空气储能工况中的腐蚀速率在1 mm/a以下,而在模拟注空气驱油工况中的腐蚀速率达15 mm/a以上。
表13 盐穴压缩空气储能工况和注空气驱油工况管柱腐蚀研究结果统计(部分)
笔者认为造成这一显著差异的原因与二者试验过程中釜内是否有液相介质有关,在两例盐穴压缩空气储能工况下的管柱腐蚀情况研究中釜内均无液相介质,其中一例虽然在试样表面喷洒饱和食盐水模拟管壁盐沉积,但由于水量少,在随后的试验过程中釜内环境湿度应仍处于较低水平;而在实际工况中,盐穴底部往往存在难以排尽的卤水,这导致注采管长时间处于饱和湿度的压缩空气环境中,易在管壁形成薄液膜,从而发生电化学腐蚀。
笔者采用动态腐蚀高压釜研究了碳钢(N80)、不锈钢(超级13Cr、2507)、镍基合金(2532、2250)在模拟盐穴压缩空气储能工况中的腐蚀情况,试验条件及步骤如下:
(a) 使用丙酮、乙醇依次清洁待测腐蚀挂片表面,测量计算腐蚀挂片表面积并称重;
(b) 每组腐蚀挂片共6个平行样,分两层安装在盘状聚四氟夹具上,每层同材质有3个平行试样;
(c) 配制1 L的230 g/L NaCl溶液,并将溶液倒入容积为3 L的动态腐蚀高压釜中,釜腔规格为Φ140 mm×195 mm,此时液面距釜腔顶部和底部分别约为130 mm和65 mm;
(d) 调整两个聚四氟夹具位置,使其在高压釜密闭后各有一个夹具分别处于气相和液相环境中,如图6所示;
图6 腐蚀试样安装方法示意
1.转轴 2.釜腔 3.聚四氟夹具 4.液相 5.腐蚀挂片 6.气相
(e) 为模拟气相环境中管材表面盐沉积,在高压釜密闭前,将气相环境中的试样在230 g/L NaCl溶液浸润1 min,而后合上釜盖,设置温度为70℃、转速为1.5 m/s;
(f) 待温度达到设定值后,向釜内充入12 MPa压缩空气,而后开启旋转电机,计时;
(g) 168 h后试验停止,取出试样;
(h) 去除试样表面腐蚀产物,采用失重法计算腐蚀速率。
不同材质试样在气相和液相环境中的平均腐蚀速率和宏观腐蚀形貌如图7和图8所示。可以看出N80碳钢试样在气相和液相环境中发生了显著的均匀腐蚀减薄,平均腐蚀速率分别约为2.0 mm/a和2.6 mm/a;超级13Cr不锈钢试样在气相和液相环境中的平均腐蚀速率分别约为0.25 mm/a和1.0 mm/a,与N80碳钢不同的是,超级13Cr不锈钢的腐蚀以点蚀为主,特别是在液相环境中,试样表面的最大点蚀速率可高达50 mm/a;2507双相不锈钢试样在气相和液相环境中腐蚀轻微,主要是在挂片孔洞与聚四氟夹具接触位置处发生了缝隙腐蚀,平均腐蚀速率分别为0.015 mm/a和0.065 mm/a;2532和2250镍基合金的平均腐蚀速率极低,试样表面基本未发生明显腐蚀。
图7 不同材质在气相和液相中的平均腐蚀速率
图8 不同材质在气相和液相中的宏观腐蚀形貌
Part.02 断裂、变形失效
盐穴压缩空气储能井深大都在500~3000 m,尽管相较于油气开发井其井深较浅,但井筒管柱通常须穿越较厚的盐膏层,盐膏层具有蠕变特性,易导致井壁失稳,最终致使井下管柱发生严重变形,甚至断裂。
在造腔阶段,盐穴腔体失稳以及夹层的垮塌会砸坏或挤毁溶腔管柱,另外下落的夹层不溶物会挤压溶腔内管,可能使其弯曲变形。
在注采运行阶段,水锤效应及周期性注采导致的振动,也可能使管柱发生弯曲以及引起螺纹接头损坏和柱体疲劳开裂。
02 盐穴压缩空气储能用管需求分析
盐穴压缩空气储能井下环境具有高含氧、高含盐、高湿度特征,注采管柱腐蚀失效风险高,同时盐膏层蠕动以及周期性注采对管柱的抗挤毁、气密封、抗疲劳等性能提出更高要求。
然而,由于盐穴压缩空气储能发展时间较短,目前对于注采管在井下的真实运行工况认识不全面,例如管材表面是否有水、盐等腐蚀性物质沉积,周期性注采对于管材表面腐蚀性物质沉积是否有影响,进而影响管材腐蚀行为,如何设计腐蚀模拟试验进行选材研究等一系列问题,制约着盐穴压缩空气储能注采管更加安全、经济应用。因此,明晰管柱实际运行工况,对于盐穴压缩空气储能注采管的相关研究至关重要。
4 思考与建议
“双碳”战略下新能源及相关产业的发展给钢管带来新的机遇和挑战,CO2输送、氢气输送以及压缩空气储能等新的应用需求给钢管带来更加广阔的市场,然而目前钢管在新场景中应用的基础理论研究、关键技术开发和标准体系建设等方面均滞后于产业发展,使得钢管应用的安全性、经济性和规范性难以保障。
在基础理论研究方面应聚焦于新场景下钢管潜在的失效机理研究,并基于此开发高性能用管。例如,超临界CO2输送中的多因素耦合腐蚀机理、管道断裂理论,氢气输送中的管道氢脆机理,盐穴压缩空气储能中注采管在高含氧、高含盐、高湿度环境中的腐蚀机理等,继而在失效机理研究的基础上开展钢管合金成分、组织、力学性能等对失效的影响研究,以开发适用于新场景中的高性能、经济性钢管产品。
在关键技术开发方面应聚焦于钢管的应用技术开发和适用边界研究。推进HFW焊管在CO2输送和氢气输送中的应用,开发盐穴压缩空气储能用注采管腐蚀控制技术、大直径注采管螺纹连接技术,探索各种材质、钢级管材在不同服役工况下的适用边界,建立全面的选材数据库。
在标准体系建设方面应聚焦于新能源用管的特殊需求,建立包括CO2输送用钢管、纯氢及掺氢输送用钢管、盐穴压缩空气储能用套管等在内的新能源用管标准技术规范体系,同时应将阶段性研究成果始终与标准紧密结合,持续推进标准的更新升级,实现以标准促发展,推动我国新能源行业发展。
免责声明:本网站所转载的文字、图片与视频资料版权归原创作者所有,如果涉及侵权,请第一时间联系本网删除。
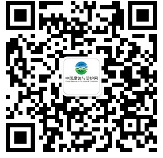
官方微信
《腐蚀与防护网电子期刊》征订启事
- 投稿联系:编辑部
- 电话:010-62316606
- 邮箱:fsfhzy666@163.com
- 腐蚀与防护网官方QQ群:140808414