“十三五”期间,我国深水油气装备实现国产化,相关技术跃居世界先进水平。中心管汇是深水生产系统中最复杂、最典型的核心设备之一,用于分配、控制、管理石油和天然气的流动。双相不锈钢材料具有出色的耐蚀性和力学性能,在中心管汇上有广泛的应用。 良好的防腐蚀是确保该设备在寿命期内正常服役的关键,管道外涂层在这方面发挥着重要作用,但目前相关研究和关注较少。工程中也存在因双相不锈钢具有优异耐蚀性而忽视其防腐蚀涂装的认识误区。 为此,海洋石油工程股份有限公司的技术人员结合工程应用,通过介绍双相不锈钢表面涂层的重要性,从表面处理、涂装系统、涂层修复等方面提供了实现良好防腐蚀涂装的技术参考。
生产设施及材料介绍 01 水下中心管汇 深水生产系统已成为深水及边际油气田开发的重要模式。中心管汇(Central Manifold)被喻为水下“油气枢纽站”,是设计和制造难度极高的设备,如图1所示。 图1 中心管汇 中心管汇主要分布在海底的井口群之间,承担着将深海油气汇集并输送的重要作用,在南海500级流花、1500级陵水等深水及超深水油气田的开发中,随着关键技术自主创新和核心设备自主研制,中心管汇已实现国产化并成功应用,是目前国产化水平最高的水下关键设备。 02 双相不锈钢 双相不锈钢中铁素体与奥氏体各约占50%,较少相含量最少达到30%。双相不锈钢兼具奥氏体不锈钢和铁素体不锈钢的优点:与铁素体不锈钢相比,双相不锈钢塑性、韧性更高,室温脆性、耐晶间腐蚀性能和焊接性能明显提高;与奥氏体不锈钢相比,双相不锈钢强度高且耐晶间腐蚀、耐氯化物应力腐蚀性能提高。 水下生产设施需具有较长的服役寿命和极高的可靠性,因为它一旦失效可能造成严重的后果且维护费用高昂。双相不锈钢在耐点蚀、耐缝隙腐蚀、耐应力腐蚀方面性能优异,广泛应用于中心管汇主工艺管线、小口径仪表管、阀门等。 流花某气田中心管汇的主工艺管线、管件使用材料为S31803双相不锈钢,管线三维图如图2所示,该中心管汇经过了防腐蚀涂装。 图2 中心管汇的管线三维图 双相不锈钢管线涂层的作用 处于深水的双相不锈钢管线,长期面临海水浸泡、高压、低温、冲击等,腐蚀环境复杂而严苛。双相不锈钢管线处于阴极保护之下,外防腐蚀涂层起到减小阳极消耗,降低氢致应力开裂风险,提高抗腐蚀性的重要作用。 减小阳极消耗 随着水深的增加,海水温度变低、压力增大、pH降低,海水中的碳酸钙低于饱和度,不易形成保护性石灰质沉积垢层。压力增大会增加涂层的吸水率,加速涂层的失效,涂层电阻在较短时间内明显降低。相比于常压海水环境,涂层在深海高压环境中更容易失效。研究表明,在高压(6 MPa)海水中浸泡30天后,常规涂层的阻抗降低1000倍。因此,在深水环境中服役的水下设施需要更大的阴极保护电流,这导致阳极消耗量增加。我国南海某深水气田在开发之初就遇到了管线阳极消耗过快的问题。由于空间和质量的限制,在水下设施中不可能无限增加阳极的数量和质量。 对于双相不锈钢管线来说,采用防腐蚀涂层和阴极保护相互补充方式是较为经济、安全可靠的防腐蚀手段。涂层的致密性和低电导率将大大减小管线对于阴极保护电流的需求,水下设施可被快速极化到最佳保护电位从而得到有效保护,阳极的使用寿命也得到延长。同时涂层有助于实现阴极保护电流的均匀分布,这对于深水中心管汇实现设计寿命有着非常重要的意义。 降低氢致应力开裂风险 应力腐蚀开裂(SCC)是材料在应力和特定介质协同作用下产生的脆性断裂现象。在拉应力作用下,原子氢渗入并扩散到合金晶体结构内部导致合金脆性断裂的失效形式称为氢致应力开裂(HISC)。HISC是一种非延性失效模式,由应力、氢含量和易受影响的钢的微观结构共同作用引起。双相不锈钢对HISC敏感,从环境中吸收一定量的氢和高应力部件微观结构的共同作用可以诱导双相不锈钢发生氢致应力开裂。氢致应力开裂主要可从三个方面控制:材料微观结构、介质中氢的来源、负载评估。 图3为荔湾某深水气田水下双相不锈钢管线服役后发生氢致应力开裂的情况。检测结果表明,回收管道的母材含有较多的氢(质量分数约为0.0172%),焊缝含氢量相对较少(质量分数约0.0084%)。这是因为出现裂纹后氢迅速扩散出金属。 图3 氢致应力开裂 分析发现,虽然焊口组织中铁素体的平均含量符合工程规范要求,但裂纹区域局部铁素体含量非常高。由于氢原子的直径比金属原子小很多,在铁素体中具有很好的渗透扩散性,大量氢原子扩散进入铁素体后产生氢气发生体积膨胀,导致该区域产生开裂。 在海洋环境中,阴极保护电位须严格控制在适当范围。双相不锈钢在海水中暴露于高应力以及保护电位负于-800 mV(相对于Ag/AgCl参比电极)时,容易受到氢致应力开裂的影响。当管线材料中存在结构缺陷、两相组织存在不均匀,服役环境中有丰富的氢源时,双相不锈钢有较高的开裂风险。表面的涂层可以显著降低双相不锈钢对于保护电流的需求从而降低钢材表面氢原子的富集,同时起到屏蔽氢的作用,达到抑制氢致应力开裂的目的。但涂层不是100%的屏障,细小的裂纹或缺陷都可能导致局部产生和吸收氢,因此涂层的质量至关重要。 提高耐腐蚀性能 自然条件下双相不锈钢优良的耐腐蚀性能主要依靠其表面的钝化膜,在海水环境中,双相不锈钢的耐腐蚀性能会减弱。这主要是因为氯离子半径比较小,易于扩散和穿透,吸附在金属表面,与钝化膜发生反应,使钝化膜破坏直到出现微观缺口;缺口处的双相不锈钢失去钝化膜的保护变成阳极区,而钝化膜未被破坏部分双相不锈钢则是阴极区,如此形成了大阴极小阳极模型,使阳极区快速腐蚀形成点蚀坑。水下设施接触的海泥中往往含有细菌等微生物,微生物沉积在双相不锈钢表面形成膜,使不锈钢点蚀敏感性增大。管线外部的保护涂层可以起到隔离氯离子、微生物、污染物等的作用,从而提高管线的耐腐蚀性能。 双相不锈钢管线的防腐蚀涂装 由于材料和服役环境的特殊性与碳钢管线相比,双相不锈钢管线的涂装在涂层选用、检验仪器、施工设备、涂装工艺等方面有更高要求。 01 表面处理 表面处理是涂层优良附着的基础,表面一致有助于涂层的均匀分散。双相不锈钢管线宜采用喷砂处理(除锈等级为Sa2.5级),喷砂处理时必须采用不含氯化物的尖锐的石榴石、氧化铝等非金属磨料以形成锯齿状的轮廓。 经表面处理后,双相不锈钢表面粗糙度的推荐值为50~85 μm。表面粗糙度过大会使波峰处涂料不能完全覆盖金属基材,涂层厚度偏薄,防护性能下降。表面粗糙度过小会使涂层附着力下降,导致涂层提早损坏。 金属基材上的可溶性盐会增加水分子的渗透压导致涂层起泡,表面可溶性盐分控制在20 mg/m2以下(可溶性盐电导率宜控制在170 μS/cm以下)。喷砂处理后双相不锈钢表面附着的灰尘杂质会产生涂层起泡问题,可接受最低除锈等级为Sa2级。 02 涂层系统 涂料性能是长效防腐蚀的关键,阴极保护对涂层有剥离作用,因此在选择防腐蚀涂层时,应考虑涂层的电性能、力学性能、化学性能等。受制造、空间等限制,热固性交联融结环氧等屏蔽性能较佳的涂层在管线上不便实施,因此水下中心汇管常采用液态环氧涂料。 双相不锈钢是一种特殊的合金材料,液态涂料在其表面的浸润性相对较差,必须选择附着力优良的涂层体系。NORSOK M-501标准推荐的涂装系统中,油漆类型为双组分环氧/环氧酚醛,最小干膜厚度为350 μm,最小涂装遍数为2遍,颜色为黄(RAL1004)。 深水防腐蚀涂层系统与深水阴极保护系统必须很好地兼容,这就要求涂层具有良好的耐阴极剥离及耐海水浸泡性能。通过最少4200小时的常温海水浸泡和阴极剥离两项测试,评估涂层的附着力、耐渗透性、致密性、腐蚀蔓延性以及耐电流的剥离性等。如果管线操作温度超过50 ℃,还应在不低于最高服役温度下对涂层再进行阴极剥离测试。 常温管线涂层可采用双组分厚浆型环氧,温度较高时采用环氧酚醛。环氧酚醛有很高的交联密度,自由体积小,温度较高时其高交联的网络使水分子、离子等难以通过,因此耐温性通常优于环氧。 为确保涂层的防腐蚀性能,推荐对深水涂层进行额外的高压浸泡测试,利用电化学、光谱、表面分析等方法检验涂层在高压、低温下的性能及其变化。涂层厚度不应低于350 μm,适当增加厚度可增强涂层对腐蚀介质的屏蔽能力,阻止渗透。图4为水下机器人(ROV)在水下对管线进行操作,深水能见度极低,为便于观察,管线面漆颜色宜采用辨识度较高的黄色RAL1004。 图4 ROV水下操作 03涂层厚度测量 双相不锈钢中的铁素体会产生不均匀的铁磁性,其电磁特性对膜厚测量仪传感器的磁场分布产生影响,从而影响常用磁性或者电涡流探头的灵敏度。在工程中用铁基、非铁基或自动识别底材类型的探头测量膜厚均可能产生偏离。厚度是涂层质量控制的重点,涂层过厚会导致应力集中,涂层过薄会使其屏蔽性能不足。双相不锈钢涂层厚度宜采用超声波厚测量仪器进行检测。超声波脉冲可以准确测量各涂层的厚度,使用前应按涂层厚度范围设置量程以获得准确值。 04游离铁污染控制 阴极保护电流对不锈钢钝化膜的影响较为复杂,极化电位不同可能会导致表面钝化膜变化。钝化膜在双相不锈钢管线整体防腐蚀体系中仍然发挥着重要的防护作用,特别是对于欠保护或电流屏蔽处管线。游离铁会导致双相不锈钢表面污染从而影响钝化膜的形成,如图5所示。双相不锈钢管线的表面处理和喷涂应在独立的车间或专用场地进行,喷砂和作业环境均需与碳钢作隔离处理。 图5 双相不锈钢表面的铁污染 蓝点检测法可用于检验铁污染。检测溶液为1 g K3[Fe(CN)6]加3 mL质量分数为65%~85%的硝酸和100 mL去离子水。滤纸浸渍溶液后贴附于待测双相不锈钢表面或直接将溶液滴涂于双相不锈钢表面,15秒内出现蓝点表明存在游离铁。 05焊缝节点涂层的修复 水下中心管汇双相不锈钢管线常规建造工艺是预涂管线、管件,焊接后再对焊缝进行修补涂装,受空间限制此时往往不再具备喷砂作业条件。用常规钢丝刷或针枪等工具对修复位置打磨只能产生光滑表面,不能形成明显波峰、波谷的锯齿状外形。低表面粗糙度和波浪外形会造成涂层附着力差,影响其抗阴极剥离性能,形成薄弱点。在2012版NORSOK M-501标准中,对于浸没区不锈钢表面粗糙度的要求为50~85 μm,而对于非海洋大气区和2004版浸没区表面粗糙度的要求为25~45 μm。 管线的焊缝是氢致应力开裂最为敏感的部位,焊缝处涂层质量较为重要,提高涂层的附着力可以提高其抗阴极剥离性能。推荐使用立式钢丝刷等工具持续冲刷打磨该区域钢材表面,使该区域钢材表面产生与喷砂类似的清洁度和表面粗糙度,以提高涂层的附着力从而提高其防腐蚀性能和屏蔽作用。在打磨处理前,焊缝表面应处理平整,控制余高3 mm以下,防止应力集中。涂层完全固化后,用湿海绵漏涂点检测仪进行100%针孔检测。
水下油气生产系统是深水油气田开发的重要模式,我国相关装备的研制起步较晚,目前仍存在技术不足等问题,因此向海洋工程制造业深水高端装备进军,开展相关探索和实践具有重要意义。水下中心管汇是深海油气田开发的核心装备之一,管线是该设备正常运行的关键。阴极保护下双相不锈钢管线涂层能起到减小阳极消耗,降低氢致应力开裂风险,提高耐腐蚀性的重要作用。工程设计和制造中应结合双相不锈钢管线的服役特点制定针对性的防腐蚀涂装方案,采用专业仪器设备检测,确保防腐蚀涂层的质量和可靠性。
免责声明:本网站所转载的文字、图片与视频资料版权归原创作者所有,如果涉及侵权,请第一时间联系本网删除。
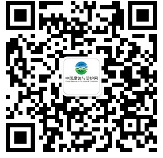
官方微信
《腐蚀与防护网电子期刊》征订启事
- 投稿联系:编辑部
- 电话:010-62316606
- 邮箱:fsfhzy666@163.com
- 腐蚀与防护网官方QQ群:140808414