由于高性能复合材料包含于整个复合材料之中,且高性能是相对而言的,因此叙述国内外发展概况宜论述整个复合材料为好。复合材料根据基体种类可分为树脂基复合材料、金属基复合材料、陶瓷基复合材料、水泥基复合材料等。
(一)树脂基复合材料国内外发展概况
树脂基复合材料是最先开发和产业化推广的,因此应用面最广、产业化程度最高。根据基体的受热行为可分为热塑性复合材料和热固性复合材料。
1.热固性树脂基复合材料
热固性树脂基复合材料是指以热固性树脂如不饱和聚酯树脂、环氧树脂、酚醛树脂、乙烯基酯树脂等为基体,以玻璃纤维、碳纤维、芳纶纤维、超高分子量聚乙烯纤维等为增强材料制成的复合材料。
树脂基复合材料自1932年在美国诞生之后,至今已有近70年的发展历史。1940~1945年期间美国首次用玻璃纤维增强聚酯树脂、以手糊工艺制造军用雷达罩和飞机油箱,为树脂基复合材料在军事工业中的应用开辟了途。1944年美国空军第一次用树脂基复合材料夹层结构制造飞机机身、机翼;1946年纤维缠绕成型在美国获得专利;1950年真空袋和压力袋成型工艺研究成功并试制成功直升飞机的螺旋桨;1949年玻璃纤维预混料研制成功,利用传统的对模法压制出表面光洁的树脂基复合材料零件;20世纪60年代美国用纤维缠绕工艺研制成功“北极星A”导弹发动机壳体。为了提高手糊成型工艺的生产率,在此期间喷射成型工艺得到了发展和应用,使生产效率提高了2-4倍。1961年德国研制成功片状模塑料(SMC),使模压成型工艺达到新水平(中压、中温、大台面制品);1963年树脂基复合材料板材开始工业化生产,美、法、日等国先后建起了高产量、大宽幅连续生产线,并研制成功透明复合材料及其夹层结构板材;1965年美国和日本用SMC压制汽车部件、浴盆、船上构件等;拉挤成型工艺始于20世纪50年代,60年代中期实现了连续化生产,除棒材外还生产细管、方形、工字形、槽形等型材,到了70年代,拉挤技术有了重大突破,目前美国生产拉挤成型机组最先进,其制品断面达76×20cm2,并设计有环向缠绕机构;进入70年代,树脂反应注射成型(RRIM)研究成功,改善了手糊工艺,使产品两面光洁,已用于生产卫生洁具、汽车零件等。70年代初热塑性复合材料得到发展,其生产工艺主要是注射成型和挤出成型,只用于生产短纤维增强塑料。1972年美国PPG公司研制成功玻璃纤维毡增强热塑性片状模塑料(GMT),1975年投入生产,其最大特点是成型周期短,废料可回收利用。80年代法国研究成功湿法生产热塑性片状模塑料(GMT)并成功地用于汽车制造工业。离心浇铸成型工艺于20世纪60年代始于瑞士,80年代得到发展,英国用此法生产10m。长复合材料电线杆,而用离心法生产大口径压力管道用于城市给水工程,技术经济效果十分显著。到目前为止,树脂基复合材料的生产工艺已有近20种之多,而且新的生产工艺还在不断的出现。
关于树脂基复合材料的开发应用,各国的发展途径有所不同。美国首先在军工方面应用,二次大战后逐渐转为民用为主。西欧各国则直接从发展民用开始(如波形板、防腐材料、卫生洁具等)兼顾军工。就全世界而言,目前已形成了从原材料、成型工艺、机械设备、产品种类及性能检验等较完整的工业体系,与其它工业相比,发展速度很快。
当今复合材料的树脂基体仍以热固性树脂为主。根据2000年的统计,全世界树脂基复合材料制品种类超过40000种,总产量达600万吨,其中高性能树脂基复合材料产量超过300万吨,高性能热塑性复合材料产量为120多万吨。
树脂基复合材料的应用领域十分广阔,表1为美国、西欧、日本等几个主要国家的树脂基复合材料在汽车、建筑和造船等工业中用量比例。
我国树脂基复合材料始于1958年,当年以手糊工艺研制了树脂基复合材料渔船,以层压和卷制工艺研制成功树脂基复合材料板、管和火箭筒等。1961年研制成耐烧蚀端头。1962年引进不饱和聚酯树脂和蜂窝成型机及喷射成型机,开发了飞机螺旋桨和风机叶片。1962年研究成功缠绕工艺并生产一批氧气瓶等压力容器。1970年用手糊夹层结构板制造了直径44米的大型树脂基复合材料雷达罩。1971年以前我国的树脂基复合材料工业主要是军工产品,70年代后开始转向民用。1987年起各地大量引进国外先进技术如池窑拉丝、短切毡、表面毡生产线及各种牌号的聚酯树脂(美、德、荷、英、意、日)和环氧树脂(日、德)等生产技术;在成型工艺方面,引进了缠绕管、罐生产线、拉挤工艺生产线、SMC生产线、连续制板机组、树脂传递模塑(RTM)成型机、喷射成型技术、树脂注射成型技术及渔竿生产线等,形成了从研究、设计、生产及原材料配套的完整的工业体系,截止2000年底,我国树脂基复合材料生产企业达3000多家,已有51家通过ISO9000质量体系认证,产品品种3000多种,总产量达73万吨/年,居世界第二位。产品主要用于建筑、防腐、轻工、交通运输、造船等工业领域。近年来碳纤维片材补强建筑结构、拉挤复合材料门窗、SMC或BMC模压电表箱、RTM制品等兴起。
在建筑方面,树脂基复合材料已广泛应用于内外墙板、透明瓦、冷却塔、空调罩、风机、玻璃钢水箱、卫生洁具、净化槽等。
在石油化工方面,主要用于管道及贮罐。其中玻璃钢管道有定长管、离心浇铸管及连续管道。按压力等级分为中低压管道和高压管道。我国“八五”、“九五”期间引进管罐生产线40条,现场缠绕大型贮罐最大直径12米,贮罐最大容积1万立方米。国内研制与生产的玻璃钢管罐生产设备部分技术指标已超过国外同类设备的技术水平。
在交通运输方面,为了使交通工具轻型化、节约耗油量、提高使用寿命和安全系数,目前在交通工具上已经大量使用复合材料。汽车上主要有车身、引擎盖、保险杠等配件;火车上有车厢板、门窗、座椅等;在船艇方面主要有气垫船、救生艇、侦察艇、渔船等,目前我国制造的玻璃钢渔船最长达33米。在机械及电器领域如屋顶风机、轴流风机、电缆桥架、绝缘棒、集成电路板等产品都具有相当的规模。
在航空航天及军事领域,如轻型飞机、尾翼、卫星天线、火箭喷管、防弹板、防弹衣、鱼雷等都取得了重大突破,为我国的国防事业作出了重大贡献。
高性能热固性树脂基复合材料所采用的基体主要有环氧树脂、酚醛树脂、乙烯基酯树脂等。
(1)环氧树脂
环氧树脂的特点是具有优良的化学稳定性、电绝缘性、耐腐蚀性。良好的粘接性能和较高的机械强度,广泛应用于化工、轻工、机械、电子、水利、交通、汽车、家电和宇航等各个领域。
1993年世界环氧树脂生产能力为130万吨,1996年递增到143万吨,1997年为148万吨,1999年150万吨,预计2003年可达到160万吨左右。
我国是从1975年开始研究环氧树脂。据不完全统计,目前我国环氧树脂生产企业约有170多家,总生产能力为15万多吨,设备利用率为50%左右。
(2)酚醛树脂
酚醛树脂具有耐热性、耐磨擦性、机械强度高、电绝缘性优异、低发烟性和耐酸性优异等特点,因而在复合材料产业的各个领域得到广泛应用。近年来在某些高新技术如电子行业、汽车行业、航空航天等领域得到了应用。
1997年全球酚醛树脂的产量为300万吨,其中美国为164万吨。我国的产量为18万吨,进口4万吨。酚醛树脂的应用包括汽车刹车片、酚醛电容包封料、深层过滤材料、航空航天等行业。
(3)乙烯基酯树脂
乙烯基酯树脂是20世纪60年代发展起来的一类新型热固性树脂,其特点是耐腐蚀性好、耐溶剂性好、机械强度高、延伸率大、与金属、塑料、混凝土等材料的粘结性能好、耐疲劳性能好、电性能佳、耐热老化、固化收缩率低、可常温固化也可加热固化。
南京金陵帝斯曼树脂有限公司引进荷兰的先进技术生产的Atlac系列强耐腐蚀性乙烯基酯树脂,已广泛用于贮罐、容器、管道等,有的品种还能用于防水和热压成型。南京费隆复合材料有限公司、上海新华树脂厂、南通明佳聚合物有限公司等厂家也生产乙烯基酯树脂。
2.热塑性树脂基复合材料
热塑性树脂基复合材料是20世纪80年代发展起来的,由于可以回收利用,所以在复合材料总量中的比例呈逐年增长趋势。主要品种有长纤维增强粒料(LFP)、连续纤维增强预浸带(MITT)和纤维热塑性片树(GMT)。根据使用要求不同,树脂基体主要有PP、PE、PA、PBT、PEI、PC、PEI、PES、PEEK、PI、PAI等热塑性工程塑料,纤维种类包括玻璃纤维、碳纤维、芳纶纤维和硼纤维等一切可能的纤维品种。
欧美发达国家热塑性树脂基复合材料占树脂基复合材料总量的3O%以上。2000年酉欧热固性树脂基复合材料产量为106万吨,热塑性复合材料为54万吨,占树脂基复合材料总量的34%。
高性能热塑性树脂基复合材料以注射件居多,基体以PP、PA为主。产品有管件(弯头、三通、法兰)、阀门、叶轮、轴承、电器及汽车零件、挤出成型的管道、GMT(热塑性片状模塑料)模压制品如吉普车座椅支架、汽车踏板、座椅等。玻璃纤维增强聚丙烯在汽车中的应用包括通风和供暖系统、空气过滤器外壳、变速箱盖、座椅架、挡泥板垫片、传动皮带保护罩等。
滑石粉填充的PP具有高刚性、高强度、极好的耐热老化性能及耐寒性。滑石粉增强PP在车内装饰方面有着重要的应用,如用作通风系统零部件。仪表盘和自动刹车控制杠等。汽车装磺类零部件多用于普通PP和添加滑石粉等无机填充材料的复合聚丙烯。美国HPM公司用20%滑石粉填充PP制成168m2、重5kg的蜂窝状结构的吸音天花板和轿车的摇窗升降器卷绳筒外壳。
云母复合材料具有高刚性、高热变形温度、低收缩率、低挠曲事、尺寸稳定以及与金属相比的低密度、低价格等特点,利用云母/pp复合材料可制作汽车仪表盘、前灯保护圈、挡板罩、车门护栏、热闹外壳、电机风扇、百叶窗等部件,利用该材料的阻尼性可制作音响零件,利用其屏蔽性可制作蓄电池箱等。
目前丰田汽车工业公司与三菱化学公司共同开发成功的PP/EPR/滑石粉纳米复合材料制造汽车的前、后保险杠,已于1991年实现了商用化,由此丰田汽车上的保险杠厚度可以由4mm减少到3mm,质量约减轻1/3。丰田公司在1994年又开发出用于汽车内装饰的TSOP-2、TSOP-3等纳米复合材料。
对于热塑性复合材料如PA、PP等一般基体,由于其耐热性差一直未能得到普及应用。近年来,一方面通过对现有热塑性树脂的改性,另一方面开发高性能热塑性树脂如PPO、PEEK、PEI、PPS、PSF等,使得热塑性复合材料的应用越来越多。
我国的热塑性树脂基复合材料开始于20世纪80年代末期,近十年来取得了快速发展(见表3),2000年产量达到12万吨,约占树脂基夏合材料总产量的17%,与发达国家尚有差距。所用的基体材料仍以PP、PA为主,增强材料以玻璃纤维为主,少量为碳纤维,在热塑性复合材料方面未能有重大突破。我国纳米科技为聚合物改性及应用提供了良好的机遇,如纳米改性PA等,但目前仍存在复合体系单一,工业化程度不高,大多数只处于实验室研究阶段,没有完全推广实用,聚合物纳米复合材料所具备的特性和潜能,在今后很长一段时间内都要靠纳米科技开创先河和提高。
树脂基复合材料采用的增强材料主要有玻璃纤维、碳纤维、芳纶纤维、超高分子量聚乙烯纤维等。
(1)玻璃纤维
目前用于高性能复合材料的玻璃纤维主要有高强度玻璃纤维、石英玻璃纤维和高硅氧玻璃纤维等。
20世纪50年代末美国首先研究开发成功了高强度玻璃纤维(S-994),迄今为止,世界上仅有美、法、日、俄、加及我国六个国家能生产高强度玻璃纤维。由于高强度玻璃纤维性能价格比较优,以年增长率10%以上的速度发展。1991年西方各国的总产量已达到480吨,目前估计已在5000吨以上。高强度玻璃纤维复合材料不仅应用在军用方面,近年来民用产品也有广泛应用,如防弹头盔、防弹服、直升飞机机翼、预警机雷达罩、各种高压压力容器、民用飞机直板、体育用品、各类耐高温制品以及近期报道的性能优异的轮胎帘子线等。
石英玻璃纤维及高硅氧玻璃纤维属于耐高温的玻璃纤维,是比较理想的耐热防火材料,用其增强酚醛树脂可制成各种结构的耐高温、耐烧蚀的复合材料部件,大量应用于火箭、导弹的防热材料。
迄今为止,我国已经实用化的高性能树脂基复合材料用的碳纤维、芳纶纤维、高强度玻璃纤维三大增强纤维中,只有高强度玻璃纤维已达到国际先进水平,且拥有自主知识产权,形成了小规模的产业,现阶段年产可达500吨。
(2)碳纤维
碳纤维具有强度高、模量高、耐高温、导电等一系列性能,首先在航空航天领域得到广泛应用,近年来在运动器具和体育用品方面也广泛采用。据预测碳纤维复合材料在近年内还将扩大开辟新的应用领域,土木建筑、交通运输、汽车、能源等领域将会大规模采用工业级碳纤维。1997~2000年间,宇航用碳纤维的年增长率估计为31%,而工业用碳纤维的年增长率估计会达到130%。
我国的碳纤维总体水平还比较低,相当于国外七十年代中、末期水平,与国外差距达20年左右。国产碳纤维的主要问题是性能不太稳定且离散系数大、无高性能碳纤维、品种单一、规格不全、连续长度不够、未经表面处理、价格偏高等。
(3)芳纶纤维
1972年美国杜邦公司研究开发成功的全对位芳香族聚酰胺名为Kevlar的商品正式用于高性能夏合材料。1972年的产量仅为45吨,到1977年就增加到4200吨,1982年上升到21000吨,年增长速度为20%。20世纪80年代以来,荷兰、日本、前苏联也先后开展了芳纶纤维的研制开发工作。荷兰AKZO公司的子公司恩卡公司的“Twaron”系列纤维在1986年的年生产能力为1000~2000吨,预计2000年能达到15000吨的能力。日本帝人公司及俄罗斯的芳纶纤维已投入市场,年增长速度也达到20%左右。
芳纶纤维比强度、比模量较高,因此被广泛应用于航空航天领域的高性能复合材料零部件(如火箭发动机壳体、飞机发动机舱、整流罩、方向舵等)、舰船(如航空母舰、核潜艇、游艇、救生艇等)、汽车(如轮胎帘子线、高压软管、摩擦材料、高压气瓶等)以及耐热运输带、体育运动器材等。
(4)超高分子量聚乙烯纤维
目前市场上出售产品主要有美国Ailled公司的Spectra900和1000、DSM(荷)-Toyoba(日)联合生产的DyneemaSK60以及Mitsui(日)公司的TekmilonI等。超高分子量聚乙烯纤维的比强度在各种纤维中位居第一,尤其是它的抗化学试剂侵蚀和抗老化性能优良。它还具有优良的高频声纳透过性和耐海水腐蚀性,许多国家已用它来制造舰艇的高频声纳导流罩,大大提高了舰艇的探雷、扫雷能力。在海上油田应用的高性能轻质复合
材料方面都显示出极大的优越性,除在军事应用领域发挥举足轻重的作用外,在汽车制造、船舶制造、医疗器械、体育运动器材等领域也有广阔的应用前景。该纤维一经问世就引起了世界发达国家的极大兴趣和重视,美国1989年增长率为26%,远远高于其他高性能纤维。芳纶纤维、高分子量聚乙烯纤维在国内迄今均未实现商品化。尽管在1972年我国就开始研究芳纶纤维,1981年2月与1985年底分别对芳纶工、芳纶Ⅱ进行了技术鉴定,其高纯度料块在南通合成树脂厂试制、由上海合成纤维研究所拉制成纤维,由于单丝直径均匀性、集束性方面均存在一些问题,到20世纪90年代初的产量也仅为几吨,与国外的差距很大。
21世纪高性能树脂基复合材料技术是赋予复合材料自修复性、自分解性、自诊断性、自制功能等为一体的智能化材料。以开发高刚度、高强度。高湿热环境下使用的复合材料为重点,构筑材料、成型加工、设计、检查一体化的材料系统。组织系统上将是联盟(如美国汽车联盟)和集团化。这将更充分的利用各方面的资源(技术资源、物质资源),紧密联系各方面的优势,以推动复合材料工业的进一步发展。
(二)金属基复合材料
金属基复合材料主要是随航空航天工业上高强度、低密度的要求而出现的,因此被广泛研究和应用的金属基复合材料是以Al、Mg等轻金属为基体的复合材料。20世纪60年代,以鹤和硼纤维连续增强的金属基复合材料如雨后春笋般发展起来。由于连续纤维增强复合材料价格昂贵和生产制造工艺复杂,70年代该材料的研究有所滑坡。随着涡轮发动机中高温部件对于耐高温材料的不断需求,又触发了对金属基复合材料特别是钛基材料研究的复苏。
非连续增强复合材料在80年代得到迅速发展,研究重点集中在以碳化硅或氧化铝粒子、短纤维增强铝基复合材料。这类材料无论基体和增强体承受载荷的比例都介于弥散强化和连续纤维强化这两种极端情况之间,它具有优良的横向性能、低消耗和优良的可加工性,与未强化合金相比,性能也有大幅度地提高。所有这些因素使这类材料已成为在许多应用领域里最具商业吸引力的材料。
金属基复合材料在航空和宇航方面的应用主要包括代替轻但有毒的铍。例如,在美国的三叉戟导弹中用SiCp/Al复合材料取代了铍,碳化硅颗粒/铝基复合材料还在飞机的电子设备中取代碳/环氧。在非航空和宇航方面的应用,短纤维增强金属基复合材料在汽车领域的应用得到普遍关注。例如局部增强内燃机活塞,其顶部是由氧化铝短纤维或氧化铝和二氧化硅短纤维混杂增强铝基复合材料构成。常规的内燃机活塞用Al-Si铸造合金制造,有些则采用在第一道环槽镶嵌高镍铸铁环。
金属基复合材料在国外已经实现了商品化,而在我国仅有少量批量生产,以汽车零件、机械零件为主,主要是耐磨复合材料如颗粒增强铝基、锌基复合材料、短纤维增强铝基或锌墓复合材料等,年产量仅5000吨左右,与国外差距较大。南京宝色钛业有限公司,用不同有色金属以爆炸焊接复合及爆炸一轧制复合方法生产复合材料制品,是我国生产复合材料制品主要厂家之一,目前市场占有率在40%以上。
(三)陶瓷基复合材料
陶瓷基复合材料(CMC)包括颗粒、晶须、短或连续纤维增强复合材料。陶瓷基复合材料的潜在应用须域广泛,包括宇航、国防、能源、汽车工业、环保、生物、化学工业等,在未来的国际竞争中将起关键的作用。
陶瓷基复合材料的开发一直吸引着技术发达国家投入巨资进行研究。目前,对陶瓷基复合材料的研究,美国和西欧各国侧重于航空和军事应用,日本则力求把它应用在工业上。1987年美国能源部开始实施对陶瓷基复合材料的研究开发计划,国防部和宇航局(NASA)等单位也投入大量人力和经费,仅1992年美国投入陶瓷基复合材料应用研究的经费就高达3500万美元。近年来美国国防部一直把这项技术列入重点投资项目,在迪拉瓦等一些高等学校和杜邦等一批大公司中集中力量研究三维编织增强陶瓷的热结构件。据悉,SiCf/SiC已得到比较成功的应用,NASA开展的陶瓷燃气轮发动机(AGT)研究课题,研制的转子、叶片、燃烧室涡形管等件已通过热试验;法国SEP公司用陶瓷基复合材料制成的SCD-SEP火箭试验发动机已经通过点火试车,由于使用了陶瓷基复合材料使结构减轻了50%。
国内从20世纪90年代初开始进行纤维增强玻璃基复合材料的研究,包括C纤维增强微晶玻璃Cf/LAS、碳化硅纤维增强微晶玻璃SiCf/LAS、SiCf/LCAS,研究内容包括工艺、组成、显微结构、界面结构、力学性能和热处理等方面,开展研究的单位有中科院上海硅酸盐研究所、西安交大、华东理工大学、中国建筑材料科学研究院等,目前尚未有批量生产的报道。
(四)水泥基复合材料
水泥基复合材料包括颗粒型复合材料(如混凝土)和纤维增强水泥基复合材料(如纤维混凝土)。1980年高性能纤维增强水泥基复合材料诞生。混凝土基体的组成不断优化,已由普通水泥基向环保水泥基聚合物(Geopolymer)、聚合物水泥基发展,MDF水泥基、DSP水泥基材料属超高性能水泥基材料,在此基础上又出现了性能与工艺优化的RPC水泥基;增强水泥基的纤维品种也越来越多。金属纤维(主要是钢纤维)已有各种尺度与各种形状(平直型、端勾形、波浪形、质铃形、哑铃形)的钢纤维;无机纤维有天然有机纤维(木纤维、竹纤维、剑麻纤等)以及不同尺度与不同性质的混杂纤维。20世纪90年代又发展了新型高性能FRP筋材。基体性能的优化和纤维品种的增多大大促进了水泥基复合材料的发展,应用领域也越来越宽。以钢纤维增强水泥基复合材料为例,普通钢纤维混凝土(SFRC)已是水泥基复合材料中研究最多、应用最广的一种,它广泛用干各种重大和重要工程中,高性能纤维增强水泥基复合材料中,典型的有渍浆结维混凝土(SIFCON)、渍浆网片混凝土(SIMCON),它们的力学行为均按数量级增长,在军事工程上发挥了特殊的优势。特别是继MDF和DSP材料之后,又出现了活性粉末混凝土RPC材料。国际上的RPC材料有两大系列,一是RPC200,二是RPC800,RPC800的性能已能与金属材料媲美,与高分子材料抗衡了,但其生产工艺复杂,能耗高,难以向工程化和产业化转换,相比之下RPC200则显示出更美好的发展前景。加拿大Sherbrooke采用RPC200建造了世界上第一座RPC步行桥(WalkBridge),该桥不仅强度高、耐久性好,而且水泥用量降低40%,结构自重减少1/2~2/3,且制备工艺简单,有自流平特征,能耗下降,这一超高性能水泥基复合材料己引起世界各国的高度重视,且不断在工程中拓宽应用。RPC材料虽出现在SIFCON和SIM-CON之后,但其发展速度却有过之而无不及。
用RPC材料来增强水泥基解决混凝土早期收缩是一项关键技术,可国内生产的纤维质量与水平至今不能过关,尤其是在搅拌过程中纤维能否在水泥基体中均匀分散的关键技术至今没有解决,现在国内生产现状与美国纤维有很大差距,所以美国杜拉公司也看准了中国的大市场,积极在工程中推广他们的产品,所以增强材料不过关,就是水泥基体优化了,性能价格比仍然难以提高。因此水泥基复合材料的发展没有配套技术,产品质量不赶超世界先进水平,不形成大规模生产,则不可能满足工程上的需求。
更多关于材料方面、材料腐蚀控制、材料科普等等方面的国内外最新动态,我们网站会不断更新。希望大家一直关注中国腐蚀与防护网http://www.ecorr.org
责任编辑:王元
《中国腐蚀与防护网电子期刊》征订启事
投稿联系:编辑部
电话:010-62313558-806
邮箱:ecorr_org@163.com
中国腐蚀与防护网官方 QQ群:140808414
免责声明:本网站所转载的文字、图片与视频资料版权归原创作者所有,如果涉及侵权,请第一时间联系本网删除。
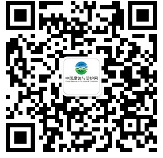
官方微信
《中国腐蚀与防护网电子期刊》征订启事
- 投稿联系:编辑部
- 电话:010-62316606-806
- 邮箱:fsfhzy666@163.com
- 中国腐蚀与防护网官方QQ群:140808414