复合材料具有轻质、高比强度、高比刚度及1有效实现结构减重,提高飞行性能、安全性和可靠性,并有可能使得复合材料结构全寿命成本低于传统的金属结构,同时复合材料的广泛应用还可进一步推进隐身和智能直升机结构设计技术的发展。因此,近几十年来,几乎直升机的所有结构都开展了复合材料的应用研究,并大部分得到了应用推广。
直升机复合材料应用特点
直升机与固定翼飞机相比,最显著的不同是有一、两个或更多的旋翼,利用旋翼旋转所提供及传动系统所传递的升力、前进力和操纵力,直升机能有效的完成垂直起落、空中悬停和前飞、侧飞、回转飞行及贴地飞行,以及当发动机停车时可自转下滑安全着陆。旋翼及传统系统作为直升机所独有的两大动部件,因其动力响应产生高周疲劳( HCF )环境;同时直升机因地空地循环所诱发也存在低周疲劳( LCF )环境;对于部分利用悬停效应承担搜索救援及外载运输等起重任务的直升机,其附加疲劳环境为重复周期疲劳( RCF );选用具备优良抗疲劳特性的复合材料将是直升机追求高减重效益的最有效途径。
直升机与固定翼飞机相比,其飞行高度一般在6 000 m以下,甚至在超低空15~30 m之间,飞行速度约在300 km/h,是一种中低空、低速飞行器。与高空高速固定翼飞机所不同,其主要应用环境为湿/热、干/寒、沙尘/雨淋、海水等恶劣环境条件,为满足在上述不同区域、不同气候条件下的苛刻使用要求,具备优良的耐候性、耐蚀性的复合材料将是直升机环境适应性设计的必然选择。
因直升机与固定翼飞机上述不同的飞行原理和使用环境,使直升机结构设计要求,除一般航空器设计的刚度、强度、质量、空气动力、工艺性和使用维护性外,还有其特殊要求。例如旋翼系统对气动弹性、疲劳寿命、振动、可靠性等设计要求尤为关注;突出的振动问题使直升机结构设计在很大程度上是结构动力学设计问题,直升机结构设计中必须设法降低强迫振动的振幅和避免出现动稳定性问题;军用直升机还应满足防弹、耐坠性等要求。
直升机结构通常分为以旋翼系统为代表的动部件结构和机体结构两大类。这两类结构设计有明显的不同,旋翼系统动部件更加突出直升机专有技术。旋翼系统动部件设计以疲劳强度和调频设计为主,率先选用复合材料正是看中复合材料优异的疲劳和刚度可剪裁特性,树脂基复合材料模压成型有利于旋翼桨叶采用先进翼型、沿翼展多翼型先进气动布局和采用绕衬套缠绕接头等,球柔性旋翼连接件采用的铝基复合材料具有高的比刚度、比强度、低密度和韧性好等优异的力学性能,尤其具有极好的抗疲劳特性。与钛合金结构件相比质量分数减轻30%,与铝合金结构件相比寿命提高50% 。复合材料在旋翼桨毂上的应用不仅使桨毂明显减重,更重要的是研制出了星型柔性桨毂、纤维/弹性轴承桨毂、无轴承桨毂等新型桨毂。
直升机机体结构采用复合材料,一方面着眼于结构减重,另一方面着眼于改进和创新结构设计及制造工艺,如涵道大垂尾结构、驾驶舱管梁骨架结构、耐坠吸能结构和大型整体壁板、夹层结构尾梁等。
与固定翼飞机相比,直升机在复合材料应用技术特点上有一定区别,主要表现在:
1结构形式不同。直升机与固定翼飞机有显著区别,旋翼是直升机特有的结构,旋翼系统及传动系统不仅动部件多,受力方式也不同;机身存在较多薄壁复杂曲面,大量采用蜂窝夹层结构。
2材料体系不同。直升机采用环氧树脂预浸料,增强材料以织物为主,包括碳纤维/玻璃纤维/芳纶等织物,而固定翼飞机主要采用双马树脂碳纤维单向带预浸料;直升机旋翼连接件基于疲劳及减重的考虑,采用了铝基复合材料。
3性能要求不同。由于结构形式和使用环境的区别,直升机复合材料在材料选用和环境适应性要求上与固定飞机存在差异,使得固定翼飞机所获取的设计性能数据不能直接应用到直升机上;且对于旋翼系统等直升机特有的动部件,还要求复合材料具有优异的高周疲劳特性。国内直升机复合材料应用情况1960年代,国内即开展了碳纤维复合材料研究,直9型机就大量采用了环氧基碳纤维、高强玻璃纤维及芳纶的复合材料,主要用于主桨叶、涵道大垂尾、平尾、侧端板、座舱罩等结构部件。
1990年代,国内在开展直升机研制初期即开始确定大量采用先进复合材料的技术方案,主要涉及到了各个型号旋翼系统的动部件(桨叶、桨毂、主减机箱),机身结构的座舱骨架、尾梁、垂尾、平尾等主受力结构。
进入21世纪后,碳纤维及高强玻璃纤维环氧基复合材料等此类战略性材料基本已实现国内自我保障,解决了关键材料受制于人的困境,并掌握了包括复合材料研制、结构设计、制造、检测、试验、数据分析以及项目管理在内的系统的工程化验证技术和管理方法,实现了碳纤维等关键材料的工程化生产和大批量供应。通过建立国产复合材料标准体系,对直升机复合材料从原材料控制到结构设计、工艺制造、无损检测以及试验验证等各方面进行了统一规范,直接推动了国产复合材料在国内直升机上的大面积应用。
目前,国内在研和在役直升机均大量采用复合材料,主要应用部位有旋翼桨叶中的大梁、蒙皮、垫布、后缘条等,机体结构中的机身下构件蒙皮、座舱、动力舱整流罩、短翼、尾梁蒙皮、壁板、尾斜梁、尾段整流罩、仪表板、遮光罩等。其中,桨毂部分零件采用了金属基复合材料,武装直升机座舱采用了陶瓷复合防弹装甲。
国内直升机复合材料应用存在的问题
直升机上推广使用复合材料是一项能大幅度改善性能、降低生产成本、缩短生产周期和收益颇丰的适用技术。从设计的角度来考虑,目前主要要研究复合材料结构的力学问题,其中包括复合材料结构耐久性、抗坠毁性、定寿方法、接触应力、弹击损伤等;复合材料机身结构设计问题,包括设计准则、铺层设计、破坏形式、损伤容限试验、防断裂方法、连接方法、疲劳强度、修补方法、工艺成型及质量控制等;复合材料旋翼结构设计研究,包括设计准则、选材、旋翼桨叶及桨毂结构型式及剖面形状、桨叶及桨毂铺层构造及刚度设计、测试及工艺等。
由于复合材料具有各向异性和性能可设计性的特点,设计人员以根据直升机结构的特点选用适当的组分材料和调整增强材料的方向使设计的直升机结构性能大幅得到改善,同时实现降低结构质量、减少生产成本、缩短生产周期的目的。
从国内直升机复合材料的应用与发展现状来看,制约复合材料在国内直升机上的应用也在性能、重量和价格这3 个方面。
性能方面
目前国内先进直升机树脂基复合材料用量很大,但由于其耐温性能、湿/热性能和断裂韧性等几个关键指标的限制,影响了其在某些特殊工况要求部位的推广应用。
新一代损伤容限型、高抗疲劳性能的铝基复合材料在应用上获得了很好的减重效果,并有利于降低制造和维护成本。目前国内外正在进行这些铝基复合材料的扩大应用和材料改进研究工作。
陶瓷复合防弹装甲已在国内军用直升机上成熟应用,但陶瓷材料脆性大,弹击后容易破碎,抗多发弹能力较差。针对未来武装直升机高生存力的要求,对开发出防护性和韧性好的陶瓷复合材料提出了需求。
质量方面
直升机大量应用薄壁结构,其复合材料面板厚度为0.3~1.0 mm,而目前直升机上普遍应用的织物预浸料单层厚度约为0.2~0.3 mm,复合材料的方向可设计性和厚度可设计性受到限制,明显牺牲结构质量,制约了复合材料在直升机结构上的减重优势。
价格方面
直升机复合材料成本主要包含原材料成本、制造成本和使用维护成本,制造成本大约占复合材料制件总成本的80%。热压罐法成型是目前国内直升机复合材料制件最主要的成型工艺方法,但其设备成本高,生产周期长,能源消耗大,故其生产成本高。为降低制造成本,国外已在开发低成本成型方法和先进的自动化工艺与设备,提升复合材料整体化、模块化设计和制造水平上开展了大量的研究工作,在这些方面国内还有较大差距。
直升机复合材料发展趋势
未来复合材料在直升机发展中的地位将更加重要,直升机在继续选用成熟应用的复合材料的同时,应考虑开发性能更优异、且更适合直升机设计与制造要求的先进复合材料,采用更多先进的制造工艺和技术,扩大复合材料在直升机上的使用范围。未来直升机复合材料总体发展方向是高性能化、结构-功能一体化、设计-制造一体化、智能化及低成本化协调发展,其发展趋势展望如下:
1 高性能化
原材料技术是先进复合材料应用的基础与前提,直升机复合材料的高性能化发展是未来的趋势之一。树脂基复合材料将在发展高强高模增强纤维的同时,提升树脂基体的韧性、湿热性能及环境适应性能力;金属基复合材料着重于提升损伤容限及抗疲劳性能;陶瓷复合防弹装甲材料应在提升综合防护性能的同时进一步减轻质量。
2 结构-功能一体化
直升机的服役环境对防雷击性能提出了要求,同时军用直升机由于战场特殊环境,还应具有隐身(视觉、红外、雷达和声学)、防弹、电磁屏蔽、耐坠性等功能。未来先进直升机复合材料应至少具备两种或更多功能,有效实现复合材料结构承载-功能(隐身、防弹、防雷击、电磁屏蔽、耐坠性等)一体化发展将是一大趋势。
3 设计-制造一体化
发展以DFM(Design for Manufacture)为核心的设计-制造一体化技术,其实质是随计算机和制造技术的进步,采用全新的设计理念和手段,发展数字化、自动化的设计技术,将设计和制造进一步融为一体,从而加快产品研发进度,提高质量。实现直升机复合材料制造过程数字化与飞机结构设计数字化趋向相适应,减少试验次数,缩短研制周期,节约研发资金,降低废品率及提高生产效率。
4 智能化
智能化是直升机复合材料结构设计亟需关注的研究方向。开发直升机复合材料自感知、自诊断、自修复和自适应智能化技术,可以实现直升机复合材料结构噪声抑制、振动控制、主动变形和性能监测与损伤自修复。
5 低成本化
直升机复合材料全寿命周期的低成本化是未来的发展趋势,包括材料低成本化、设计低成本化、制造低成本化和维护低成本化4 个方面。核心是发展低成本制造技术,其主要有:发展以自动铺带(ATL)和纤维自动铺放(AFP)为核心的自动化制造技术;发展以共固化/共胶接为核心的大面积整体成型技术;发展以树脂传递模塑成型技术为核心的低成本制造技术;发展非热压罐成型技术等。
结束语
随着近几十年的不断发展,复合材料在直升机上的应用已发展到主承力结构并实现大范围成熟应用,也推动了直升机技术的进步。国内直升机复合材料通过国内直升机型号需求的牵引和推动,目前已经基本实现国产化,形成了我国直升机复合材料研发及生产体系,技术水平在不断提高,并有了较全面的发展和广泛的应用,但是与国外发达国家相比,在材料、设计、工艺等方面仍有差距。未来国内直升机技术发展将追求高效能、长寿命、高可靠和低成本,对其材料与结构的综合要求越来越高,对高性能复合材料、先进设计技术和制造工艺需求迫切。为此,国内今后应在解决目前发展中存在的复合材料性能稳定性问题的同时,大力发展高性能复合材料、结构功一体化复合材料和智能复合材料;重视发展自动化制造、大面积整体成型和低成本制造技术,提升复合材料工艺制造水平,降低制造成本;还应重点关注复合材料整体化和模块化设计技术,发展复合材料设计-制造一体化技术,进一步提升复合材料的应用技术水平。
更多关于材料方面、材料腐蚀控制、材料科普等方面的国内外最新动态,我们网站会不断更新。希望大家一直关注中国腐蚀与防护网http://www.ecorr.org
免责声明:本网站所转载的文字、图片与视频资料版权归原创作者所有,如果涉及侵权,请第一时间联系本网删除。
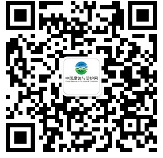
官方微信
《中国腐蚀与防护网电子期刊》征订启事
- 投稿联系:编辑部
- 电话:010-62316606-806
- 邮箱:fsfhzy666@163.com
- 中国腐蚀与防护网官方QQ群:140808414