图1 喷丸处理对FGH96合金表面硬化层残余压应力分布的影响[30]
1.2 高温合金喷丸处理后的表面硬化层组织
喷丸处理过程中,高温合金表面产生了理想残余压应力的同时,显微组织亦发生了显著变化。Zhao等[33]对GH4169合金喷丸强化的研究发现,经过喷丸强化后合金表面形成厚度约96 μm的硬化层,而且表面形成平均尺寸约为9 nm的等轴纳米晶(图2[33])。在一定深度范围内还形成高密度形变孪晶,进一步细化了硬化层合金的显微组织,提高了合金的高温疲劳抗力。在IN718合金的研究[34]中发现,超声喷丸处理也可获得厚度约为90 μm、平均晶粒尺寸约为12 nm的表面纳米晶层,有效地提高了合金的高温疲劳抗力。喷丸处理中,高温合金表面产生显著塑性变形,必然引起位错密度增加,并在晶界处形成大量的位错塞积与缠结,这是喷丸处理获得表面硬化层的根本原因。
图2 GH4169合金喷丸处理获得的表面硬化层截面梯度分布的纳米晶和形变孪晶层[33]
同时发现,喷丸处理硬化层的硬化程度呈梯度分布、总深度有限。Dong等[35]对Udimet 720Li合金喷丸硬化层的研究发现,喷丸后合金表面显微硬度由440 HV增至590 HV,但在距离表面50 μm处即开始迅速下降。在铸造高温合金的喷丸处理研究中也发现类似规律,喷丸处理后的K4169[32]、K403[36]铸造合金表面形成深度为100~140 μm的表面硬化层,表层均具有较好的硬化效果。
1.3 高温合金喷丸处理后的表面粗糙度
虽然喷丸处理可在高温合金表面形成具有显著残余压应力的硬化层,但其对构件机械加工表面粗糙度的影响规律并不一致,改善作用有限[30,32,36]。大部分关于高温合金表面喷丸处理的研究[13,36]均表明,表面粗糙度随喷丸强度的升高而增大。图3[13]为GH4169合金经不同强度喷丸处理后的表面形貌。可见,随喷丸强度的增加,材料表面粗糙度明显增大。而Wang等[30]的研究表明,喷丸处理后,FGH96合金表面的车削加工痕迹可完全(或大部分)被弹丸冲击弹坑所覆盖,但喷丸后表面粗糙度却有明显升高之趋势。Shen等[36]对K403铸造高温合金进行超声喷丸处理,发现超声喷丸对合金的表面粗糙度无明显影响。
图3 喷丸处理前后GH4169合金的表面形貌[13]
1.4 高温合金表面喷丸强化的抗疲劳作用及影响因素
高温、循环载荷作用下,高温合金喷丸硬化层内的高密度缺陷和亚稳微结构,可阻碍位错运动,提高微观塑性变形抗力,增加裂纹萌生阻力,进而提高喷丸处理合金的疲劳裂纹萌生临界应力值和疲劳强度[33]。Dong等[35]的研究表明,由于喷丸处理形成的硬化层残余压应力和高密度位错缠结,表面裂纹萌生抗力增加,喷丸后合金的疲劳裂纹萌生位置从表层转移到内部(图4[35])。而在其他条件相同的情况下,疲劳裂纹由内部萌生所需的能量远高于由表面萌生的能量,因此可显著提高材料的疲劳寿命[37,38]。
图4 喷丸处理对Udimet 720Li合金相同载荷幅条件下疲劳裂纹萌生位置的影响[35]
亦有研究表明,高温合金喷丸处理的抗疲劳强化作用与应力状态、应力幅值均有关。Dong等[35]对Udimet 720Li合金的研究发现,与未喷丸合金相比,喷丸处理后合金的缺口低周疲劳寿命显著提高,其在1390和1070 MPa应力幅下的增幅分别为2.05倍和6.07倍。由此可见,喷丸处理在低应力水平下对提高疲劳寿命的作用更加显著。此外,应力状态还影响喷丸硬化层的残余应力松弛程度。高玉魁等[31]对FGH97合金喷丸前后的不同应力状态疲劳寿命进行对比,发现在630 MPa的低应力状态下,喷丸硬化层的残余压应力可有效延缓表面裂纹萌生,提高合金的疲劳寿命。而在740 MPa高应力状态下硬化层的残余压应力作用减弱,抗疲劳作用并不明显。Luo和Bowen[38]对Udimet 720Li合金的研究也证实了600℃高温条件下,在较低的应力幅范围内,喷丸处理可提高合金的疲劳寿命;而当处于高应力幅时,喷丸处理反而降低了合金的疲劳寿命。
同时应注意到,高温合金喷丸处理的抗疲劳作用亦与喷丸强度有关。过高的喷丸强度反而会降低抗疲劳的功效[28]。主要是由于过高强度的喷丸处理,会在材料内局部引入残余拉应力,明显降低合金的疲劳抗力。Qin等[13]对GH4169合金进行不同强度的喷丸处理,发现局部的残余应力状态波动,增大了裂纹尖端附近的应力场起伏,导致裂纹扩展速率增加,降低了喷丸处理合金的疲劳抗力(图5[13])。
图5 不同强度的表面喷丸处理对GH4169合金疲劳应力幅-循环周次(S-N)曲线的影响[13]
综上,高温合金喷丸处理表面硬化层的残余压应力、强化效果和表面粗糙度,均随喷丸强度的提高而增加。其中残余压应力与表面强化可显著改善合金疲劳性能,而表面粗糙度多不利于高温合金疲劳寿命。Wu等[39]和Klotz等[34]对Inconel 718合金的研究也表明,喷丸处理后,表面残余压应力与表面粗糙度2者对抗疲劳的作用不同。在低周疲劳条件下,表面粗糙度为影响疲劳寿命的主要因素;而高周疲劳条件下,残余压应力的分布状态则为提高疲劳寿命的主要影响因素。
2 高温合金的表面机械挤压强化
高温合金的表面强化还包括复杂结构部位的机械挤压强化[40~42]。机械挤压强化方式根据强化部位形状、工艺要求不同,一般包括孔挤压强化和表面机械滚压强化。由于涡轮转子热端部件的连接孔处应力集中明显,孔周围易产生严重的疲劳损伤,对转动部件孔周围通常进行孔挤压强化。而对于平面或相对平缓曲面,多采取表面机械滚压方式进行强化处理。机械挤压处理可有效改善高温合金的表面状态,机械挤压硬化层内的残余压应力增加、组织细化和均匀化、高密度位错缠结和表面粗糙度的降低,可显著提高合金的高温强度和疲劳强度极限。
2.1 高温合金机械挤压表面粗糙度
王欣等[42]的研究表明,孔挤压处理可显著改善GH4169转动部件孔内铰削刀痕引起的粗糙度突变,挤压后孔壁达到镜面,表面粗糙度Ra由1.083 μm降至0.237 μm。罗学昆等[43]对不同过盈量孔挤压处理的IN718合金研究结果显示,孔挤压显著改善了孔壁表面完整性。低过盈量挤压的孔壁表面粗糙度Ra由原始的0.855 μm降至0.306 μm;高过盈量试样的粗糙度Ra降至0.296 μm。可见,与喷丸处理对表面粗糙度影响不同,挤压处理普遍降低高温合金的孔壁表面粗糙度,有利于降低孔壁的表面微观应力集中效应,从而使高温合金构件获得理想的表面强化效果[43,44]。
2.2 高温合金机械挤压硬化层组织及硬度
Yin等[45]对Inconel 690合金表面的超声滚压处理研究表明,经表面超声滚压后,表层塑性变形引起位错密度增加,产生加工硬化效应,硬化层硬度提高幅度达到44.45%。孙智妍等[46]研究发现,电脉冲的辅助可显著增加GH4169合金表面超声滚压硬化层深度与强化效果。而且,电脉冲辅助超声滚压(电脉冲/超声滚压耦合场强化)能够突破传统超声滚压处理的变形临界极限,获得更细的晶粒、更深的硬化层。
2.3 高温合金机械挤压硬化层的残余压应力
机械挤压强化可在高温合金表面获得比喷丸处理更显著的残余压应力层。Yin等[45]研究了表面超声滚压处理Inconel 690合金硬化层的残余压应力分布,发现经超声滚压处理后表面形成明显的残余压应力层,压应力提高幅度达到33.5%,层深约达400 μm。对孔挤压处理IN718合金的研究[43]也表明,挤压强化后甚至可在孔壁形成超过3000 μm的残余压应力层(图6[43]),这对于合金的表面强化和抗疲劳作用无疑具有积极的作用。
图6 不同孔挤压处理的IN718合金孔壁硬化层的残余压应力分布[43]
3 激光冲击处理高温合金表面强化
激光表面冲击强化,是利用高能激光诱导的冲击波在金属表面引入高速塑性变形的强化技术,可广泛应用于高温合金、高强钢、钛合金和铝合金等关键构件的抗疲劳制造[15,16]。与传统表面强化处理方式相比,LSP处理更适合型面复杂结构、大型构件的在线处理[12]。LSP处理能够在金属表层引入可观的残余压应力和塑性变形,诱导高密度位错、孪晶等,显著改变表面微结构[17,47],获得显著的硬化层,成为目前最有效的高强金属材料表面抗疲劳制造技术。
3.1 高温合金LSP处理的表面粗糙度
Tan等[48]对抛光的FGH96合金LSP处理的研究表明,表面激光冲击波作用后,合金抛光划痕减少,表面粗糙度略有增大,但增加幅度甚微(图7[48])。与传统的喷丸、机械挤压强化不同,由于LSP处理过程中,高能冲击波与合金表面为非直接接触,可显著减缓表面强烈塑性变形引起的粗糙度增大。
图7 FGH96高温合金经不同表面处理后的表面形貌[48]
3.2 高温合金LSP处理的硬化层组织及硬度
Rozmus-Górnikowska等[49]对Inconel 625合金LSP处理的研究发现,LSP处理后合金表面形成较大塑性变形,产生高密度位错和密集分布的滑移带,表面形成呈梯度分布的冲击硬化层。Cao等[50]关于GH4586合金LSP处理的研究表明,LSP表面硬化层的位错密度显著增加,形成高密度缠结位错、位错壁和位错胞结构,LSP处理后合金的疲劳寿命增加了近1倍。而且,LSP硬化层表面的平均晶粒尺寸降低约43.6%,同时发现基体中形变孪晶数量亦明显增多,使GH4586合金LSP硬化层表面获得了明显的协同强化作用,硬度提高幅度达到27.4%。值得关注的是,经LSP处理的GH4586合金表层γ?相中也观察到大量的层错以及高密度位错,这在传统机械作用表面处理的高温合金硬化层中未见报道。LSP处理后,GH4586合金硬化层中不同尺度、高密度微结构的形成与细化,有效抑制了疲劳裂纹的萌生和扩展,显著提高了合金的疲劳抗力。Luo等[51]对K417合金进行LSP处理的研究发现,激光冲击引入剧烈塑性变形,在合金表面产生更高密度的位错缠结,硬化层表面形成纳米晶,使表层硬度明显增加。此外,LSP处理后进行900℃、10 h的保温,K417合金硬化层中高密度位错、晶粒细化等微结构特征并未见显著变化,强化效果表现出了较好的高温稳定性,这主要与LSP硬化层的高密度位错与纳米晶复合结构有关。
研究者们[12,13,19]对如何在高温合金表面获得高温稳定的抗疲劳硬化层进行了大量的研究,发现引入温度场的温度辅助耦合激光冲击强化技术(warm laser shocking processing,WLSP),可获得高温强化增幅更显著的抗疲劳硬化层。本课题组[19,52]对比研究了LSP和WLSP处理IN718合金的表面硬化层微结构特征,发现WLSP作用下能够在高温合金表面获得强化相/高密度位错复合微结构(图8[52])。而且,值得关注的是,IN718合金WLSP硬化层中的γ′′相内部观察到高密度层错及纳米尺寸孪晶(图8b[52]中蓝色箭头所示)。硬化层中有序强化相内部纳米尺度微结构的形成和细化,显著提高了硬化层的强化效果和高温稳定性。
图8 IN718合金LSP、温度辅助耦合激光冲击强化技术(WLSP)硬化层中的γ″相及位错形态[52]
3.3 高温合金LSP处理的硬化层残余应力状态
与传统的常规喷丸、机械挤压处理相比,LSP硬化层最大残余压应力影响深度超过了3倍,约达700 μm[48]。因此,LSP处理更深的残余压应力层可更加显著地阻碍疲劳裂纹的萌生和扩展,更有效地提高合金的疲劳强度极限、延长疲劳寿命。Pan等[53]关于带孔的ЭΠ741ΠН合金LSP处理的研究表明,LSP处理可在孔附近圆环区域引入深度约为750 μm、最大残余压应力超过650 MPa的残余压应力场。研究认为,高于传统机械表面强化处理硬化层的残余压应力场,与表层微结构的显著细化协同作用提高了合金LSP硬化层的疲劳极限。
LSP处理GH4586合金表面沿单冲击点直径方向分布的残余应力研究[50]显示,最大残余应力位于距激光光斑中心约1 mm半径的位置(图9[50]),而且沿深度方向呈降低趋势。光斑中心附近的残余压应力相对有所降低,这种现象被称为“残余应力孔”,其主要取决于激光冲击波在合金表面的作用特征。
图9 单激光脉冲LSP处理后GH4586合金残余压应力的分布[50]
本课题组[19,50]对LSP和WLSP处理IN718合金的硬化层残余应力进行了对比研究,发现WLSP硬化层中形成的纳米尺度的强化相/高密度位错复合微结构,在合金表层产生了更高的残余压应力。因此,IN718合金的WLSP硬化层表现出更明显的高温强化和抗疲劳作用。而且,即使在高温长期时效条件下合金表面硬化层残余压应力有所松弛,相比于LSP硬化层,WLSP硬化层的残余压应力仅小幅降低,具有更好的高温稳定性,在高温强化、抗疲劳方面均更突显优势。
4 高温合金的表面冲击强化微观机制
4.1 喷丸及机械冲击表面硬化机理
高温合金表面喷丸、机械挤压处理硬化层的形成,主要是表面机械冲击过程中基体剧烈塑性变形的结果[32~34,54~59],塑性变形程度及影响层深度与弹丸、机械冲击的能量输入直接相关。孔挤压强化IN718合金孔内壁表面160 μm深度范围内可观察到明显的旋转塑性变形,越靠近内壁表面,变形程度越大[60]。RR1000合金经过喷丸处理后,表面硬化层剧烈塑性变形的晶粒比例明显增加,形成大量亚结构[61]。FGH96合金[30]、FGH97合金[28]经喷丸处理后,硬化层小角晶界比例显著增加。随表面喷丸或机械冲击能量输入的增加,高温合金硬化层表面发生了明显的晶粒细化。对K417合金的喷丸硬化层进行后处理,亦可形成较大深度范围的细晶硬化层,有效抑制表面疲劳裂纹的萌生[62]。
表面机械变形层中变形孪晶的产生与高温合金的层错能有关,层错能越低位错的交滑移受到的阻碍程度越大,变形机制越趋向于孪生[45]。Zhao等[33]研究GH4169合金的超声喷丸硬化层发现,表面剧烈塑性变形产生的位错密度足够高时,位错湮灭、重组现象显著,形成位错胞。随超声喷丸应变量和应变速率进一步增加,形变孪生机制被激发,基体中形成高密度形变孪晶。而且,表面硬化层形成的形变孪晶,与高密度缺陷、纳米晶等微结构特征相比,在高温下稳定性更高,具有提高高温合金表面硬化层高温稳定性之功效。
4.2 LSP和WLSP处理表面强化机理
与传统表面喷丸、机械冲击/挤压强化处理不同,LSP处理是源于高能量密度(109 W/cm2量级)、短脉冲宽度(10~30 ns量级)的强激光诱发等离子体与合金表面的剧烈相互作用。因此,LSP处理可获得比传统表面喷丸、机械冲击/挤压强化更加显著的表层强化程度和层深度[50~53,61~65]。
LSP处理后高温合金表层中结构细化,晶界和孪晶界数量增多。Cao等[50]研究了GH4586合金LSP处理后硬化层微结构发现,LSP处理使合金表层晶粒明显细化、孪晶数量增加,同时LSP硬化层的晶界比例明显提高(图10[50])。在K417合金的LSP硬化层中,观察到在强激光冲击作用下表层产生了高密度缺陷和晶粒尺寸为20~200 nm的纳米晶。同时发现,纳米晶在垂直激光冲击波方向被明显拉长,随着离表面深度的增加,激光冲击压力减弱,不足以形成纳米晶,微结构特征以高密度位错缠结为主。
图10 LSP处理对GH4586合金表面晶粒尺寸及孪晶数量的影响[50]
调整LSP处理参数可在高温合金表面硬化层形成不同的组织结构。Yu等[64]对GH4169合金利用高能LSP、低能LSP和飞秒LSP处理调控硬化层微结构,发现飞秒LSP硬化层深度基本小于100 μm,而低能LSP处理后,合金硬化层深度增加,表面可诱导形成高密度亚结构。但由于能量输入较低,低能LSP处理仅在距表面约100 μm范围内形成了致密的亚结构,在100 μm以下的区域,主要以位错的增殖或缠结为主,而未发现致密亚结构层。当提高输入能量时,高能LSP处理的剧烈变形影响层深可达几百微米甚至几毫米,层深1400~1600 μm时,仍可观察到致密亚结构。
LSP处理除诱发高温合金表面塑性变形层中更高的基体位错密度,明显降低晶粒尺寸,进而形成纳米晶外,更重要的是能够诱导合金中共格有序强化相的微结构改变。Geng等[65]研究某镍基单晶高温合金LSP硬化层发现,LSP处理后合金中产生了高密度的复杂位错结构,且分布不均匀,大量位错在γ基体以及γ/γ′界面形成位错缠结和复杂位错网络。同时,γ相中高密度塞积的位错切入γ'相形成滑移带,在γ′相内部还出现了短位错线和位错环(图11[65]),形成硬化层中包含有序强化相的高密度位错复合结构。
图11 LSP处理对某镍基单晶高温合金表面硬化层基体位错密度及γ′相内部微结构的影响[65]
Cao等[50]研究GH4586合金LSP硬化层微结构发现,LSP处理后合金中γ′相周围形成大量的位错缠结,γ′相结构、形态和尺寸并未发生显著变化。而γ′相内部产生了高密度的层错(图10[50])。可见,与常规喷丸、表面机械冲击/挤压处理对比,LSP处理的优势在于,可以在较低的应变量下产生更高密度的位错缠结和强化相内部的特殊亚结构。
近年来,WLSP技术越来越受到高温合金、超高强钢表面强化领域的关注。由于在强激光脉冲冲击过程中,辅助温度场耦合更易于在含有沉淀强化相的高强结构材料表面诱导形成特殊微结构。本课题组[19]对IN718合金LSP和WLSP硬化层微结构的对比研究发现,2种处理后IN718合金均形成了明显的表面硬化层,与未处理状态相比,LSP和WLSP处理后合金表面硬度分别提高了14.562%和22.689%,WLSP处理获得了硬度更高、更深的表面硬化层(图12[19])。
图12 LSP和WLSP处理对IN718合金表面硬度分布的影响[19]
在WLSP处理IN718合金表面硬化层中,观察到γ″相/高密度位错复合微结构。这种特殊微结构尺寸较均匀,以γ″相为内核,弥散状分布在γ基体上(图13[19])。结合此位置γ″相暗场像可发现:在γ″相上存在大量的纳米尺寸微孪晶,微孪晶的孪晶界面方向基本平行,且与γ″相的长轴方向具有较明显的取向关系。微孪晶主要分布在γ/γ″相界面附近,孪晶一侧贯穿γ″相,另一侧终止于γ″相旁的γ基体中的高密度位错缠结区(图13c[19]中蓝色箭头所示)。形成了WLSP处理的IN718合金中“内含微孪晶的γ″相/高密度位错复合体”这一特殊结构。
图13 WLSP处理后IN718合金表面硬化层γ″相/高密度位错复合体形态及强冲击作用下γ″相中出现的微孪晶[19]
深入研究WLSP处理IN718合金硬化层的这种特殊微结构发现,WLSP处理后γ″相周围形成了高密度的原子尺度微区压向相对应变集中,同时γ″相内部形成了微区应变[52] (图14[52])。而且,层错、微孪晶处微区应变明显加剧。在微孪晶贯穿γ″/γ相界面并延伸至γ基体的位置,界面两侧垂直延伸方向均发生拉向/压向微区应变的起伏(图14b和c[52])。同时,在γ″/γ相界面的γ相一侧,微区应变的集中也较明显。γ″相内部可见层错、微孪晶的交错,而且层错、微孪晶中的微区压向应变明显高于其他位置(图14e和f [52])。
图14 经WLSP处理后IN718合金表面硬化层中γ″/γ界面细节的HRTEM像[52]
WLSP处理IN718合金硬化层中这种特殊结构贯穿γ″/γ相界面,其改变了γ″/γ相界面形态,使得γ″相内部及其周围应变分布的复杂程度提高。这种特殊结构势必阻碍高温服役下位错反应和位错回复。同时,高温下这些高密度位错包裹、内含微孪晶的γ″相,其长大以及γ″→δ相转变的复杂程度均将加剧。
综上,高温合金表面LSP和WLSP硬化层的强化本质,除剧烈塑性变形在基体中引入的高密度缺陷及亚结构和大量形变孪晶外,还包括在γ'、γ″主要相内部诱导形成大量层错、微孪晶等特殊微结构。与传统喷丸处理和表面机械冲击/挤压强化相比,LSP和WLSP处理合金表面硬化增量更显著、硬化层更深,并且形成了稳定强化相/高密度位错复合结构和剧烈塑性变形亚结构,有利于提高高温合金的表面强化和抗疲劳能力。那么,如能利用耦合场在硬化层引入更多微纳尺度“异质结构(heterostructure)”[66~68]、“化学界面工程(chemical boundary engineering)”[69,70]等强化因素,有望在高温合金表面处理过程中收获更显著的强韧化效果。
5 高温合金表面强化的高温稳定性
5.1 硬化层高密度亚结构的演化与位错反应
高温合金表面形成的显著硬化层和残余压应力,均与基体中高密度位错及亚结构的形成和分布密不可分[71~80]。但在高温下,空位、位错等缺陷均会发生回复和强烈的相互作用,服役温度越高缺陷演化越剧烈,导致残余压应力不同程度的松弛甚至消失。
王欣等[42]对比研究了孔挤压GH4169合金在400和600℃条件下抗疲劳强化的高温稳定性。发现,即使孔挤压合金获得了明显的强化;但高温下,位错运动激活能降低、位错运动能力增加,残余压应力易发生应力松弛,硬化层的疲劳抗力降低;当温度提高到600℃时,基体高密度位错的强化作用下降更加明显。
激光冲击高温合金硬化层中基体的高密度位错及亚结构的强化贡献占比亦不容忽视。在本课题组[52]关于IN718合金表面LSP和WLSP硬化层高温稳定性的研究中发现,650℃长期时效后,LSP硬化层中基体位错密度显著降低,缺陷回复明显,导致硬化层表面硬度和硬化层深度均下降较为明显(图15[52])。
图15 650℃时效200 h对LSP和WLSP处理IN718合金表面硬化层硬度分布的影响[52]
基体中高密度位错缺陷在高温下的快速演化,在经表面机械冲击/挤压、LSP和WLSP硬化层中普遍发生。机械冲击/挤压处理的高温合金硬化层,由于表面强化的主要微结构为高密度缺陷,高温下这些缺陷的减少,导致硬化层稳定性降低、强化作用退减。
5.2 高温下硬化层细晶组织及形变孪晶的演化
超细晶(纳米晶)层并非高温合金表面硬化层的普遍性微结构特征,多出现在高能机械冲击/挤压叠加硬化层和LSP硬化层表面,其分布深度也仅约100 μm。高温时效中,表面晶粒长大迅速,硬化层稳定性降低。而高温合金表面硬化层的形变孪晶比纳米晶更为常见,且生成深度达200~500 μm,是高能机械冲击/挤压处理高温合金硬化层的典型微结构特征。Zhao等[33]研究GH4169合金超声喷丸硬化层形变孪晶高温稳定性发现,350℃保温后硬化层形变孪晶无明显改变;当温度升高至650℃时,孪晶间距明显加宽,导致硬化层的硬度降低。
5.3 冲击诱导强化相内部微结构的高温稳定性
研究[65,81~93]发现,与机械冲击/挤压硬化层相比,LSP和WLSP处理硬化层在高温长期时效后的抵抗疲劳裂纹萌生、扩展方面更具优势。Buchanan等[82]对比研究了IN100合金的喷丸处理、LSP处理硬化层的高温应力松弛,发现650℃、100 h时效后,喷丸硬化层最大残余压应力下降约800 MPa,而LSP处理的仅下降200 MPa (图16[82])。可见,LSP处理除使表面强化幅度和硬化层深度明显增加外,硬化层高温服役的稳定性也更佳。Lu等[83]研究GH4169合金WLSP硬化层的高温长期时效组织、性能稳定性发现,WLSP硬化层的残余应力降低幅度明显小于LSP硬化层。而且,600℃的时效未观察到表面残余压应力的显著改变。但当时效温度升高至650℃时,LSP硬化层的残余压应力几乎完全释放,而WLSP处理的残余压应力仅降低约8%。当时效温度增加到700℃时,WLSP硬化层的残余应力在时效100 h后仍可保持在原来的50%左右,表现出极高的高温稳定性。
图16 喷丸处理与LSP处理后IN100合金表面硬化层在650℃、100 h时效后的残余应力分布对比[82]
本课题组[81]对长期时效后LSP和WLSP处理IN718合金的硬化层硬度进行了系统对比,发现600和650℃时效200 h后,LSP和WLSP硬化层硬度、深度均有所降低。但经过650℃及以下温度长期时效后,WLSP处理的IN718合金表面硬化层硬度、深度的降低幅度均小于LSP处理(图17[81])。尤其是,WLSP处理合金经650℃、200 h长期时效后表面硬度增量的下降幅度仅为40.79%,而相同时效条件下LSP处理合金表面硬度增量的下降幅度达71.69%。680℃、200 h时效后,LSP处理合金的表面硬化现象几乎完全消失,而此时WLSP处理合金表面硬度仍保持一定的增量。研究[81]还发现,表面硬化层的强化增量主要来源于LSP和WLSP处理后合金中的高密度位错增殖和塞积(图18[81])。尤其对于WLSP硬化层而言,更显著的强化作用主要来源于硬化层γ″相/高密度位错复合微结构。同样,WLSP硬化层的强化现象在600℃以上长期时效后仍得以保持,也主要取决于WLSP处理诱发的高密度位错和特殊亚结构。
图17 不同温度长期时效后IN718合金LSP和WLSP硬化层硬度分布及硬化层深度变化[81]
图18 长期时效对LSP和WLSP处理的IN718合金表面硬化层强化机制贡献增量的影响[81]
本课题组[54]在研究长期时效后LSP和WLSP处理IN718合金表面硬化层的几何必需位错(geometrically necessary dislocation,GND)演化行为发现,WLSP硬化层的GND密度明显高于LSP处理,升高幅度约为248.71% (图19[52])。硬化层中GND密度的增加,除形成各向同性强化外,更重要的是可产生更加显著、稳定的背应力强化。经长期时效处理后,LSP硬化层中的GND密度明显降低,而WLSP硬化层的GND密度虽有降低,但降幅很小。而且长期时效后,LSP处理合金GND密度统计分布的相对频率峰位,向低位错密度方向发生了明显的移动,同时相对频率峰值也呈现出明显的上升趋势。但WLSP硬化层在长期时效后GND密度统计分布相对频率的峰值、峰位、峰宽无明显变化。这进一步说明,WLSP处理不仅仅使IN718合金获得了更高的GND密度,而且GND密度的集中程度和分布位置变化并不明显,WLSP处理合金均表现出了比LSP处理合金更显著的高温长期服役稳定性。
图19 650℃长期时效后LSP和WLSP处理IN718合金表面硬化层的几何必需位错(GND)密度分布图及正态分布统计图[52]
综上,LSP和WLSP处理高温合金硬化层微结构方面的深入研究[94~96]发现,弥散分布的γ'、γ″相在剧烈塑性变形时形成的特殊微结构,是LSP和WLSP硬化层区别于传统机械冲击/挤压强化,获得优异、稳定强化效果的关键。而WLSP处理更突显的高温强化作用和高温稳定性,不仅与特殊微结构、高的缺陷密度有关,更应与“内含层错、纳米尺寸微孪晶的有序强化相/高密度位错复合体”这种复杂微结构自身的高温稳定性直接相关[52,81]。在高温合金表面硬化层中诱导和调控高密度特殊微结构的形成和分布状态,将是获得合金稳定高温抗疲劳强化的核心。
6 总结与展望
本文基于先进涡轮动力系统用镍基高温合金的典型表面强化技术,以及强化作用高温稳定性的研究和应用分析,就镍基高温合金表面冲击强化总结与展望如下。
(1) 高温合金的表面机械喷丸、挤压/滚压强化处理,均可产生明显残余压应力和硬化层,有效阻碍裂纹在表面萌生,从而提高高温合金的疲劳抗力。但应用中需注意控制喷丸处理造成的表面粗糙度增大、挤压/滚压处理的残余压应力梯度调控以及表面机械强化超过500℃后的强化作用衰减。
(2) LSP和WLSP处理等表面高能冲击强化技术具有不受构件规格、形状限制的独特优势,同时其强化增幅及层深均优于机械表面强化处理,由此经其处理的高温合金显示出更高的疲劳抗力。WLSP处理在高温合金表面硬化层中形成的“有序强化相/高密度位错复合特殊微结构”,进一步提升了表面强化的作用效果。
(3) 硬化层微结构的高温、长时稳定性,是高温合金表面强化技术飞跃发展与深入应用的关键。高温合金表面剧烈塑性变形产生的基体微结构中,高密度缺陷的高温演化与回复显著,不具备高温稳定能力。表面细晶(纳米晶)层较浅,高温下长大倾向明显,稳定性亦不足。而形变孪生可在600℃以下保持一定的高温稳定性。耦合场高能强冲击(LSP和WLSP等)处理在获得上述基体微结构的同时,诱导γ′、γ″相内部形成内含大量层错、微孪晶的“强化相/高密度位错复合特殊微结构”,是使硬化层兼具强化作用、高温稳定性与长时稳定性的关键特殊微结构。
(4) WLSP处理在高温合金表面冲击强化作用高温稳定性方面所凸显的优势,启发人们应关注硬化层不同尺度关键微结构的综合调控。如能利用高能冲击耦合场将诸如“异质结构”、“化学界面工程”等微纳尺度强韧化理念引入高温合金的表面微结构精准设计,在硬化层精准诱导“有序强化相/高密度位错特殊微结构”的梯度分布,构筑具有更高高温强度与高温稳定性的表面硬化层,将有望开辟高温合金表面强化相关研究的新方向。
参考文献
1 Ren X P, Liu Z Q. Microstructure refinement and work hardening in a machined surface layer induced by turning Inconel 718 super alloy [J]. Int. J. Miner., Metall. Mater., 2018, 25: 937
doi: 10.1007/s12613-018-1643-2
2 Stinville J C, Callahan P G, Charpagne M A, et al. Direct measurements of slip irreversibility in a nickel-based superalloy using high resolution digital image correlation [J]. Acta Mater., 2020, 186: 172
doi: 10.1016/j.actamat.2019.12.009
3 Pradhan D, Mahobia G S, Chattopadhyay K, et al. Effect of surface roughness on corrosion behavior of the superalloy IN718 in simulated marine environment [J]. J. Alloys Compd., 2018, 740: 250
doi: 10.1016/j.jallcom.2018.01.042
4 Pradhan D, Mahobia G S, Chattopadhyay K, et al. Effect of pre hot corrosion on high cycle fatigue behavior of the superalloy IN718 at 600oC [J]. Int. J. Fatigue, 2018, 114: 120
doi: 10.1016/j.ijfatigue.2018.05.021
5 Telesman J, Gabb T P, Kantzos P T, et al. Effect of broaching machining parameters, residual stresses and cold work on fatigue life of Ni-based turbine disk P/M alloy at 650oC [J]. Int. J. Fatigue, 2021, 150: 106328
doi: 10.1016/j.ijfatigue.2021.106328
6 Zangeneh S, Lashgari H R, Asnavandi M. The effect of long-term service exposure on the stability of carbides in Co-Cr-Ni-W (X-45) superalloy [J]. Eng. Failure Anal., 2018, 84: 276
doi: 10.1016/j.engfailanal.2017.11.018
7 Zhang P Y, Zhou X, Wang X D, et al. Study on the microstructural degradation and rejuvenation heat treatment of directionally solidified turbine blades [J]. J. Alloys Compd., 2020, 829: 154474
doi: 10.1016/j.jallcom.2020.154474
8 Vikram R J, Singh A, Suwas S, et al. Effect of heat treatment on the modification of microstructure of selective laser melted (SLM) IN718 and its consequences on mechanical behavior [J]. J. Mater. Res., 2020, 35: 1949
doi: 10.1557/jmr.2020.129
9 Deng H Z, Wang L, Liu Y, et al. The evolution law of δ phase of IN718 superalloy in temperature/stress coupled field [J]. Mater. Charact., 2022, 184: 111684
doi: 10.1016/j.matchar.2021.111684
10 An J L, Wang L, Liu Y, et al. The role of δ phase for fatigue crack propagation behavior in a Ni base superalloy at room temperature [J]. Mater. Sci. Eng., 2017, A684: 312
11 Tomevenya K M, Liu S J. Probabilistic fatigue-creep life reliability assessment of aircraft turbine disk [J]. J. Mech. Sci. Technol., 2018, 32: 5127
doi: 10.1007/s12206-018-1010-2
12 Maleki E, Unal O, Guagliano M, et al. The effects of shot peening, laser shock peening and ultrasonic nanocrystal surface modification on the fatigue strength of Inconel 718 [J]. Mater. Sci. Eng., 2021, A810: 141029
13 Qin Z, Li B, Chen R, et al. Effect of shot peening on high cycle and very high cycle fatigue properties of Ni-based superalloys [J]. Int. J. Fatigue, 2023, 168: 107429
doi: 10.1016/j.ijfatigue.2022.107429
14 Yang J, Liu D X, Fan K F, et al. Designing a gradient structure in a Ni-based superalloy to improve fretting fatigue resistance at elevated temperatures through an ultrasonic surface rolling process [J]. Int. J. Fatigue, 2023, 168: 107397
doi: 10.1016/j.ijfatigue.2022.107397
15 Wu J J, Huang Z, Qiao H C, et al. Prediction about residual stress and microhardness of material subjected to multiple overlap laser shock processing using artificial neural network [J]. J. Cent. South Univ., 2022, 29: 3346
doi: 10.1007/s11771-022-5158-7
16 Gu H Q, Yan P, Jiao L, et al. Effect of laser shock peening on boring hole surface integrity and conformal contact fretting fatigue life of Ti-6Al-4V alloy [J]. Int. J. Fatigue, 2023, 166: 107241
doi: 10.1016/j.ijfatigue.2022.107241
17 Zhang H P, Cai Z Y, Chi J X, et al. Microstructural evolution, mechanical behaviors and strengthening mechanism of 300 M steel subjected to multi-pass laser shock peening [J]. Opt. Lasers Technol., 2022, 148: 107726
doi: 10.1016/j.optlastec.2021.107726
18 Wang C Y, Luo Y K, Wang J, et al. Carbide-facilitated nanocrystallization of martensitic laths and carbide deformation in AISI 420 stainless steel during laser shock peening [J]. Int. J. Plast., 2022, 150: 103191
doi: 10.1016/j.ijplas.2021.103191
19 Liu Y, Wang L, Yang K Y, et al. Effects of thermally assisted warm laser shock processing on the microstructure and fatigue property of IN718 superalloy [J]. Acta Metall. Sin. (Engl. Lett.), 2021, 34: 1645
doi: 10.1007/s40195-021-01340-z
20 Lin C H, Wu H B, Li Z G, et al. Evaluation of oblique laser shock peening effect of FGH95 superalloy turbine disk material [J]. Mater. Today Commun., 2022, 31: 103534
21 Geng Y X, Mo Y, Zheng H Z, et al. Effect of laser shock peening on the hot corrosion behavior of Ni-based single-crystal superalloy at 750oC [J]. Corros. Sci., 2021, 185: 109419
doi: 10.1016/j.corsci.2021.109419
22 Qiao Y, Guo P Q, Chen H T, et al. Roughness prediction model of face milling surface for nickel-based superalloy FGH97 [J]. IOP Conf. Ser.: Mater. Sci. Eng., 2019, 562: 012154
23 Jiang R, Song Y D, Reed P A. Fatigue crack growth mechanisms in powder metallurgy Ni-based superalloys—A review [J]. Int. J. Fatigue, 2020, 141: 105887
doi: 10.1016/j.ijfatigue.2020.105887
24 Xu C, Yao Z H, Dong J X, et al. Mechanism of high-temperature oxidation effects in fatigue crack propagation and fracture mode for FGH97 superalloy [J]. Rare Met., 2019, 38: 642
doi: 10.1007/s12598-018-1123-x
25 Zhang X S, Ma Y E, Yang M, et al. A comprehensive review of fatigue behavior of laser shock peened metallic materials [J]. Theor. Appl. Mech., 2022, 122: 103642
26 Child D J, West J D, Thomson R C. Assessment of surface hardening effects from shot peening on a Ni-based alloy using electron backscatter diffraction techniques [J]. Acta Mater., 2011, 59: 4825
doi: 10.1016/j.actamat.2011.04.025
27 Zhong L Q, Liang Y L, Hu H. Study on plastic deformation characteristics of shot peening of Ni-based superalloy GH4079 [J]. IOP Conf. Ser.: Mater. Sci. Eng., 2017, 230: 012041
28 Zhong L Q, Liang Y L, Yan Z, et al. Effect of shot peening on high cycle fatigue limit of FGH4097 P/M superalloys at room temperature [J]. Rare Met. Mater. Eng., 2018, 47: 2198
28 钟丽琼, 梁益龙, 严 振 等. 喷丸强化对FGH4097粉末高温合金室温高周疲劳极限的影响 [J]. 稀有金属材料与工程, 2018, 47: 2198
29 Kumar D, Idapalapati S, Wang W, et al. Microstructure-mechanical property correlation in shot peened and vibro-peened Ni-based superalloy [J]. J. Mater. Process. Technol., 2019, 267: 215
doi: 10.1016/j.jmatprotec.2018.12.007
30 Wang X, Xu C L, Wang X F, et al. Turning/shot peening of nickel-based powder metallurgy superalloy: Effect on surface integrity and high-temperature low-cycle fatigue properties [J]. Int. J. Fatigue, 2023, 166: 107291
doi: 10.1016/j.ijfatigue.2022.107291
31 Gao Y K, Zhong Z, Lei L M. Influence of laser peening and shot peening on fatigue properties of FGH97 superalloy [J]. Rare Met. Mater. Eng., 2016, 45: 1230
31 高玉魁, 仲 政, 雷力明. 激光冲击强化和喷丸强化对FGH97高温合金疲劳性能的影响 [J]. 稀有金属材料与工程, 2016, 45: 1230
32 Luo X K, Zhang W C, Wu B, et al. Effect of combination of laser shock peening and shot peening on surface integrity and fatigue property of K4169 casting alloy [J]. Aeron. Manuf. Technol., 2022, 65(11): 57
32 罗学昆, 张文灿, 吴 波 等. 激光冲击/喷丸复合强化对K4169铸造合金的表面完整性和疲劳性能的影响 [J]. 航空制造技术, 2022, 65(11): 57
33 Zhao X H, Zhou H Y, Liu Y. Effect of shot peening on the fatigue properties of nickel-based superalloy GH4169 at high temperature [J]. Results Phys., 2018, 11: 452
doi: 10.1016/j.rinp.2018.09.047
34 Klotz T, Delbergue D, Bocher P, et al. Surface characteristics and fatigue behavior of shot peened Inconel 718 [J]. Int. J. Fatigue, 2018, 110: 10
doi: 10.1016/j.ijfatigue.2018.01.005
35 Dong C L, Yang S K, Peng Z C. Effect of shot peening on notched fatigue performance of powder metallurgy Udimet 720Li superalloy [J]. Intermetallics, 2021, 135: 107226
doi: 10.1016/j.intermet.2021.107226
36 Shen X J, Wang C, Sun D, et al. Comparison research on mechanical properties of high temperature alloy after laser peened and ultrasonically peened [J]. Appl. Mech. Mater., 2014, 670-671: 46
doi: 10.4028/www.scientific.net/AMM.670-671
37 Chen Y X, Wang J C, Gao Y K, et al. Effect of shot peening on fatigue performance of Ti2AlNb intermetallic alloy [J]. Int. J. Fatigue, 2019, 127: 53
doi: 10.1016/j.ijfatigue.2019.05.034
38 Luo J, Bowen P. Effects of temperature and shot peening on S-N behavior of a PM Ni-base superalloy UDIMET 720 [J]. Metall. Mater. Trans., 2004, 35A: 1007
39 Wu D X, Yao C F, Zhang D H. Surface characterization and fatigue evaluation in GH4169 superalloy: comparing results after finish turning; shot peening and surface polishing treatments [J]. Int. J. Fatigue, 2018, 113: 222
doi: 10.1016/j.ijfatigue.2018.04.009
40 Sun Z Y, Ye Y D, Xu J B, et al. Effect of electropulsing on surface mechanical behavior and microstructural evolution of Inconel 718 during ultrasonic surface rolling process [J]. J. Mater. Eng. Perform., 2019, 28: 6789
doi: 10.1007/s11665-019-04443-y
41 Jiang H, Li L H, Dong J X, et al. Microstructure-based hot extrusion process control principles for nickel-base superalloy pipes [J]. Prog. Nat. Sci.: Mater. Int., 2018, 28: 391
doi: 10.1016/j.pnsc.2018.04.009
42 Wang X, Hu R G, Hu B, et al. Effect of hole-expansion on high-temperature fatigue property of GH4169 superalloy hole structure [J]. J. Aerosp. Power, 2017, 32: 89
42 王 欣, 胡仁高, 胡 博 等. 孔挤压对于高温合金GH4169孔结构高温疲劳性能的影响 [J]. 航空动力学报, 2017, 32: 89
43 Luo X K, Wang X, Hu R G, et al. Effects of hole cold expansion on fatigue property of Inconel 718 superalloy [J]. China Surf. Eng., 2016, 29(3): 116
43 罗学昆, 王 欣, 胡仁高 等. 孔挤压强化对Inconel 718高温合金疲劳性能的影响 [J]. 中国表面工程, 2016, 29(3): 116
44 Yang J, Liu D X, Zhang X H, et al. The effect of ultrasonic surface rolling process on the fretting fatigue property of GH4169 superalloy [J]. Int. J. Fatigue, 2020, 133: 105373
doi: 10.1016/j.ijfatigue.2019.105373
45 Yin M G, Cai Z B, Zhang Z X, et al. Effect of ultrasonic surface rolling process on impact-sliding wear behavior of the 690 alloy [J]. Tribol. Int., 2020, 147: 105600
doi: 10.1016/j.triboint.2019.02.008
46 Sun Z Y, Zhang Y F, Zhao X J, et al. Effect of electropulsing on the surface mechanical behavior of GH4169 during ultrasonic surface rolling process [J]. Ordnance Mater. Sci. Eng., 2021, 44(3): 33
46 孙智妍, 张雲飞, 赵秀娟 等. 电脉冲对GH4169超声滚压表面性能的影响 [J]. 兵器材料科学与工程, 2021, 44(3): 33
47 Ermakova A, Braithwaite J, Razavi J, et al. The influence of laser shock peening on corrosion-fatigue behaviour of wire arc additively manufactured components [J]. Surf. Coat. Technol., 2023, 456: 129262
doi: 10.1016/j.surfcoat.2023.129262
48 Tan Q, Yan Z R, Huang H, et al. Surface integrity and oxidation of a powder metallurgy Ni-based superalloy treated by laser shock peening [J]. JOM, 2020, 72: 1803
doi: 10.1007/s11837-020-04054-2
49 Rozmus-Górnikowska M, Kusiński J, Cieniek ?. Effect of laser shock peening on the microstructure and properties of the inconel 625 surface layer [J]. J. Mater. Eng. Perform., 2020, 29: 1544
doi: 10.1007/s11665-020-04667-3
50 Cao J D, Zhang J S, Hua Y Q, et al. Low-cycle fatigue behavior of Ni-based superalloy GH586 with laser shock processing [J]. J. Wuhan Univ. Technol.—Mater. Sci. Ed., 2017, 32: 1186
51 Luo S H, Nie X F, Zhou L C, et al. Thermal stability of surface nanostructure produced by laser shock peening in a Ni-based superalloy [J]. Surf. Coat. Technol., 2017, 311: 337
doi: 10.1016/j.surfcoat.2017.01.031
52 Liu Y, Wang L, Yang K Y, et al. Characteristics of microstructure evolution of surface treated IN718 superalloy by warm laser shock peening during long-term aging at high temperatures [J]. Mater. Charact., 2022, 193: 112261
doi: 10.1016/j.matchar.2022.112261
53 Pan X L, Guo S Q, Tian Z, et al. Fatigue performance improvement of laser shock peened hole on powder metallurgy Ni-based superalloy labyrinth disc [J]. Surf. Coat. Technol., 2021, 409: 126829
doi: 10.1016/j.surfcoat.2021.126829
54 Mythreyi O V, Nagesha B K, Jayaganthan R. Microstructural evolution & corrosion behavior of laser-powder-bed-fused Inconel 718 subjected to surface and heat treatments [J]. J. Mater. Res. Technol., 2022, 19: 3201
doi: 10.1016/j.jmrt.2022.05.123
55 Orozco-Caballero A, Jackson T, da Fonseca J Q. High-resolution digital image correlation study of the strain localization during loading of a shot-peened RR1000 nickel-based superalloy [J]. Acta Mater., 2021, 220: 117306
doi: 10.1016/j.actamat.2021.117306
56 Moran?ais A, Fèvre M, Fran?ois M, et al. Residual stress determination in a shot-peened nickel-based single-crystal superalloy using X-ray diffraction [J]. J. Appl. Crystallogr., 2015, 48: 1761
doi: 10.1107/S1600576715017689
57 Goulmy J P, Kanoute P, Rouhaud E, et al. A calibration procedure for the assessment of work hardening Part II: Application to shot peened IN718 parts [J]. Mater. Charact., 2021, 175: 111068
doi: 10.1016/j.matchar.2021.111068
58 Salvati E, Lunt A J G, Heason C P, et al. An analysis of fatigue failure mechanisms in an additively manufactured and shot peened IN 718 nickel superalloy [J]. Mater. Des., 2020, 191: 108605
doi: 10.1016/j.matdes.2020.108605
59 Gibson G J, Perkins K M, Gray S, et al. Influence of shot peening on high-temperature corrosion and corrosion-fatigue of nickel based superalloy 720Li [J]. Mater. High Temp., 2016, 33: 225
doi: 10.1080/09603409.2016.1161945
60 Song D Y, Luo Z P, Yang Y R, et al. Microstructure of the hole expansion strengthened layer of high temperature alloy GH169 [J]. Acta Aeronaut. Astronaut. Sin., 1996, 17(1): 123
60 宋德玉, 罗治平, 杨玉荣 等. GH169高温合金孔挤压强化层的微观结构 [J]. 航空学报, 1996, 17(1): 123
61 Messé O M D M, Stekovic S, Hardy M C, et al. Characterization of plastic deformation induced by shot-peening in a Ni-base superalloy [J]. JOM, 2014, 66: 2502
doi: 10.1007/s11837-014-1184-8
62 Wang D L, Li J B, Jin T, et al. Fatigue-life improvement of K417 alloy by shot peening and recrystallization [J]. Rare Met. Mater. Eng., 2006, 35: 1294
62 王东林, 李家宝, 金 涛 等. 利用喷丸再结晶方法提高K417合金的疲劳寿命 [J]. 稀有金属材料与工程, 2006, 35: 1294
63 Ren X D. Laser Impact Peening of High Temperature Service Materials [M]. Beijing: Science Press, 2014: 11
63 任旭东. 高温服役材料激光冲击强化技术 [M]. 北京: 科学出版社, 2014: 11
64 Yu Y Q, Gong J N, Fang X Y, et al. Comparison of surface integrity of GH4169 superalloy after high-energy, low-energy, and femtosecond laser shock peening [J]. Vacuum, 2023, 208: 111740
doi: 10.1016/j.vacuum.2022.111740
65 Geng Y X, Dong X, Wang K D, et al. Evolutions of microstructure, phase, microhardness, and residual stress of multiple laser shock peened Ni-based single crystal superalloy after short-term thermal exposure [J]. Opt. Lasers Technol., 2020, 123: 105917
doi: 10.1016/j.optlastec.2019.105917
66 Wang Y F, Zhu Y T, Wu X L, et al. Inter-zone constraint modifies the stress-strain response of the constituent layer in gradient structure [J]. Sci. China Mater., 2021, 64: 3114
doi: 10.1007/s40843-021-1702-2
67 Gao B, Lai Q Q, Cao Y, et al. Ultrastrong low-carbon nanosteel produced by heterostructure and interstitial mediated warm rolling [J]. Sci. Adv., 2020, 6: eaba8169
doi: 10.1126/sciadv.aba8169
68 Sun G S, Liu J Z, Zhu Y T. Heterostructure alleviates Lüders deformation of ultrafine-grained stainless steels [J]. Mater. Sci. Eng., 2022, A848: 143393
69 Ding R, Yao Y J, Sun B H, et al. Chemical boundary engineering: A new route toward lean, ultrastrong yet ductile steels [J]. Sci. Adv., 2020, 6: eaay1430
doi: 10.1126/sciadv.aay1430
70 Ding R, Yang Z G, van der Zwaag S, et al. How chemical boundary engineering can produce cheap, ultra-strong steels [J]. Proc. Inst. Civil Eng.—Civil Eng., 2020, 173: 102
71 Altinkurt G, Fèvre M, Geandier G, et al. Local strain redistribution in a coarse-grained nickel-based superalloy subjected to shot-peening, fatigue or thermal exposure investigated using synchrotron X-ray Laue microdiffraction [J]. J. Mater. Sci., 2018, 53: 8567
doi: 10.1007/s10853-018-2144-4
72 Salvati E, Lunt A J G, Ying S, et al. Eigenstrain reconstruction of residual strains in an additively manufactured and shot peened nickel superalloy compressor blade [J]. Comput. Methods Appl. Mech. Eng., 2017, 320: 335
doi: 10.1016/j.cma.2017.03.005
73 Buchanan D J, John R. Residual stress redistribution in shot peened samples subject to mechanical loading [J]. Mater. Sci. Eng., 2014, A615: 70
74 Zhu L H, Fan X L, Xiao L, et al. Influence of shot peening on the microstructure and high-temperature tensile properties of a powder metallurgy Ni-based superalloy [J]. J. Mater. Sci., 2023, 58: 2838
doi: 10.1007/s10853-023-08182-3
75 Yang J, Liu D X, Ren Z C, et al. Grain growth and fatigue behaviors of GH4169 superalloy subjected to excessive ultrasonic surface rolling process [J]. Mater. Sci. Eng., 2022, A839: 142875
76 Lesyk D A, Dzhemelinskyi V V, Martinez S, et al. Surface shot peening post-processing of Inconel 718 alloy parts printed by laser powder bed fusion additive manufacturing [J]. J. Mater. Eng. Perform., 2021, 30: 6982
doi: 10.1007/s11665-021-06103-6
77 Li L, Liu D J. Complete dissolution of gamma prime via severe plastic deformation in a precipitation-hardened nickel-base superalloy [J]. Mater. Lett., 2021, 284: 128607
doi: 10.1016/j.matlet.2020.128607
78 Colliander M H, Sundell G, Thuvander M. Complete precipitate dissolution during adiabatic shear localisation in a Ni-based superalloy [J]. Philos. Mag. Lett., 2020, 100: 561
doi: 10.1080/09500839.2020.1820595
79 Liao Z R, Polyakov M, Diaz O G, et al. Grain refinement mechanism of nickel-based superalloy by severe plastic deformation—Mechanical machining case [J]. Acta Mater., 2019, 180: 2
doi: 10.1016/j.actamat.2019.08.059
80 Takizawa Y, Sumikawa K, Watanabe K, et al. Incremental feeding high-pressure sliding for grain refinement of large-scale sheets: Application to Inconel 718 [J]. Metall. Mater. Trans., 2018, 49A: 1830
81 Liu Y, Wang L, Yang K Y, et al. Mechanism for superior fatigue performance of warm laser shock peened IN718 superalloy after high-temperature ageing [J]. J. Alloys Compd., 2022, 923: 166340
doi: 10.1016/j.jallcom.2022.166340
82 Buchanan D J, Shepard M J, John R. Retained residual stress profiles in a laser shock‐peened and shot‐peened nickel base superalloy subject to thermal exposure [J]. Int. J. Struct. Integr., 2011, 2: 34
doi: 10.1108/17579861111108590
83 Lu Y, Yang Y L, Zhao J B, et al. Impact on mechanical properties and microstructural response of nickel-based superalloy GH4169 subjected to warm laser shock peening [J]. Materials, 2020, 13: 5172
doi: 10.3390/ma13225172
84 Lu G X, Jin T, Zhou Y Z, et al. Research progress of applications of laser shock processing on superalloys [J]. Chin. J. Nonferrous Met., 2018, 28: 1755
doi: 10.1016/S1003-6326(18)64819-8
84 卢国鑫, 金 涛, 周亦胄 等. 激光冲击强化在高温合金材料应用上的研究进展 [J]. 中国有色金属学报, 2018, 28: 1755
85 Chin K S, Idapalapati S, Ardi D T. Thermal stress relaxation in shot peened and laser peened nickel-based superalloy [J]. J. Mater. Sci. Technol., 2020, 59: 100
doi: 10.1016/j.jmst.2020.03.059
86 Zhou Z, Gill A S, Telang A, et al. Experimental and finite element simulation study of thermal relaxation of residual stresses in laser shock peened IN718 SPF superalloy [J]. Exp. Mech., 2014, 54: 1597
doi: 10.1007/s11340-014-9940-9
87 Gill A, Telang A, Mannava S R, et al. Comparison of mechanisms of advanced mechanical surface treatments in nickel-based superalloy [J]. Mater. Sci. Eng., 2013, A576: 346
88 Gill A S, ZhouZ., Lienert U, et al. High spatial resolution, high energy synchrotron X-ray diffraction characterization of residual strains and stresses in laser shock peened Inconel 718SPF alloy [J]. J. Appl. Phys., 2012, 111: 084904
89 Wang H M, Sun X J, Li X X. Laser shock processing of an austenitic stainless steel and a nickel-base superalloy [J]. J. Mater. Sci. Technol., 2003, 19: 402
90 Zhu H Y, Qu X M, Cao J, et al. Study on stress relaxation characteristics of FGH95 powder superalloy treated by laser shock peening [J]. Mater. Res. Express, 2022, 9: 106502
doi: 10.1088/2053-1591/ac95f9
91 Zhou G N, Zhang Y B, Pantleon W, et al. Quantification of room temperature strengthening of laser shock peened Ni-based superalloy using synchrotron microdiffraction [J]. Mater. Des., 2022, 221: 110948
doi: 10.1016/j.matdes.2022.110948
92 Lu Y, Zhao J B, Qiao H C, et al. A study on the surface morphology evolution of the GH4619 using warm laser shock peening [J]. AIP Adv., 2019, 9: 085030
93 Xiang S, Liu X T, Xu R, et al. Ultrahigh strength in lightweight steel via avalanche multiplication of intermetallic phases and dislocation [J]. Acta Mater., 2023, 242: 118436
doi: 10.1016/j.actamat.2022.118436
94 Lin C H, Tang Y, Yu L W, et al. Oblique laser shock peening effect of the FGH95 superalloy with a PCA and comprehensive index [J]. Appl. Opt., 2022, 61: 2690
doi: 10.1364/AO.450877 pmid: 35471349
95 Gill A S, Telang A, Ye C, et al. Localized plastic deformation and hardening in laser shock peened Inconel alloy 718SPF [J]. Mater. Charact., 2018, 142: 15
doi: 10.1016/j.matchar.2018.05.010
96 Luo S H, He W F, Zhou L C, et al. Aluminizing mechanism on a nickel-based alloy with surface nanostructure produced by laser shock peening and its effect on fatigue strength [J]. Surf. Coat. Technol., 2018, 342: 29
doi: 10.1016/j.surfcoat.2018.02.083
免责声明:本网站所转载的文字、图片与视频资料版权归原创作者所有,如果涉及侵权,请第一时间联系本网删除。
-
标签: 镍基高温合金, 表面强化处理, 抗疲劳制造, 硬化层, 组织和性能高温稳定性
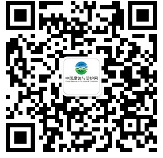
官方微信
《腐蚀与防护网电子期刊》征订启事
- 投稿联系:编辑部
- 电话:010-62316606
- 邮箱:fsfhzy666@163.com
- 腐蚀与防护网官方QQ群:140808414