随着国家“南海海洋纵深开发”战略规划实施,国家海洋战略使命由近海扩展到远海及大洋,由我国自主研制的高技术装备已陆续列装南海,进入大批量服役阶段。海洋钻井平台、海上风电/核电、舰船和港口机械等国防与海工装备的机械运动系统部件直接暴露服役于海洋大气氛围中,受海洋气氛的化学/电化学引起的腐蚀以及力学因素引起的摩擦磨损交互作用,急剧加速了金属材料的损伤失效。 热带海洋气氛摩擦腐蚀挑战 ▷ 我国四大海域环境条件 我国大陆边缘的渤海(内海)、黄海、东海和南海互相连成一片,其海洋大气具有动态性和地域性等特点,受地球经纬度和海岸地理条件影响,温度、湿度、辐照度、氯离子浓度和盐度等主要环境因子及其耦合作用对材料服役行为的影响差异很大。 渤海(盘锦-唐山-天津-东营)为近封闭的内海,常年平均气温10.7 ℃,夏季水温24~25 ℃,冬季水温0 ℃左右,普遍有结冰现象,河口及滩涂区多堆积冰(高度可达2~3米),冰期1~3个月不等。3月初融冰时还常有大量流冰发生,流速为50 cm/s左右。渤海海水盐度仅为3‰,海面风浪较小。 整体来说,渤海区域舰船及武器装备面临的腐蚀工况较弱(低温、低湿、低盐、低紫外和弱台风),但在严酷的冬季,海洋工程装备外暴露部件及其防护涂层是否能经受高低温交变及极限低温冰冻(-20 ℃),钻井平台结构物及船用钢表面能否耐冰层冲击/刮擦,是渤海区域海洋环境适应性的关键难点。 黄海海域(青岛-日照-连云港-盐城)温度季节变化较为明显,1月最低(-2~6 ℃),8月最高(25~27 ℃)。其水温年变化小于渤海(15~24 ℃),海水盐度也比较低(32‰),且流入黄海的各河携带泥沙过多。黄海易受台风侵袭,水中含氧量为四大海域最高(达5.9 ml/L)。通过分析以上数据,黄海腐蚀工况较渤海苛刻,主要是温度、盐度及水含氧量有所提高,风力增强且伴随泥沙冲刷。 此海域服役的海洋装备需选用具有一定防腐蚀效果的表面防护手段,比如海洋钻井平台生活舱室常出现结露/凝水情况而引起金属腐蚀与电气绝缘降低,需采用有机涂层等具有绝缘耐蚀的防护手段;钻井平台的桩腿、海管和动力定位系统还应具备一定抗颗粒物冲刷性能,需考虑并选用“底+中+面漆”3层体系防护技术。 东海(舟山-宁波-福州-厦门)是中国、日本和韩国等国的海洋战略要地,属于亚热带和温带气候,有较高水温(年平均水温20~24 ℃)和较大的盐度(34‰左右),水中氧含量也较高(5.2~5.6 ml/L),且海中浮游生物的生长茂盛。 相比渤海与黄海海域,东海海域腐蚀条件明显增强(中温、中湿、中盐、较强紫外和较强台风),海洋装备部件需根据自身不同服役工况,针对性选择适宜的防腐蚀方案,比如海洋钻井平台结构件(静止暴露)受盐雾腐蚀、紫外照射和台风/海浪水雾冲刷等影响,其使用寿命大大降低;而升降滑轨、传动齿轮和桩腿/导管接头中的连接螺栓及系泊链(运动暴露)则同时面临磨损与腐蚀的双重考验,须重点研究其磨损腐蚀失效行为机理,并用耐磨防腐涂层材料进行表面防护。 南海海域(广东-湛江-三亚-西/南沙群岛)接近赤道,接受太阳辐射的热量较多,南海的年日照辐射总量接近7000 MJ/m2,约是其它海域的1.5~1.7倍;年平均温度高达27.5 ℃,约是其它海域的1.7~2.7倍;一年中气温大于30 ℃的天数高达160天,约是其它海域的3.0~25.5倍;年平均降雨量约是其它海域的1.3~2.4倍。南海是我国最深、最大的半封闭海,相比渤海、黄海及东海具有更为复杂多变的热带海洋性气候特点,湿度常年高达90% RH,海水盐度高达35‰,其气氛环境具有更高的饱和蒸气压及盐雾浓度(>300 mg/m2d)。在亚热带气候的万宁试验点暴露试验结果表明,传统Q235和Q345碳钢由于高氯离子含量致使锈层结构疏松;海洋平台高湿高盐的盐雾气氛对航空钢表面电镀Cd层穿透性更强,腐蚀更加严重。 南海诸岛在夏秋两季还常受强台风影响,台风狂虐,裹挟暴雨,掀起巨浪,给海工装备的承力结构物、连接紧固件/焊缝和运动滑轨/齿轮传动部件的使用可靠性带来极大挑战。针对南海高温、高湿、高盐及高紫外辐照的热带海洋区域,伴随海浪飞溅、泥沙冲刷及强台风冲击等极端苛刻工况,南海海洋装备需经历比其他海域更为复杂和严酷的贮存、运输和服役环境,南海工程性防护材料的性能数据及规律仍极度匮乏,其热带海洋环境适应性考核体系亟待建立。 ▷ 海洋装备面临严峻摩擦腐蚀挑战 然而,在南海海域服役的海洋装备外暴露关键摩擦副零部件受海洋盐雾气氛的化学/电化学引起的腐蚀以及力学因素引起的摩擦磨损交互作用,将急剧加速其损伤失效。目前的海洋工程用材料(如耐候钢、铜合金、铝合金和钛合金等)还不能完全满足海洋装备外暴露传动系统/部件在热带海洋气氛下高可靠性和长寿命运行的要求。 传统3层防护的防腐涂层技术(涂层厚度>400 μm)与表面处理技术(氧化、磷化、镀铬、镀锌、镀镍、镀镉及盐浴氮化等)可一定程度上提升工程金属材料的耐蚀性及服役寿命,但仍难以满足海洋高技术装备高冲击和高承载运动/传动系统的实际工程需求。 目前,涉及摩擦磨损与腐蚀交互作用的海洋装备部件失效难题亟待解决,比如,内陆用高技术装备于南海海域首次试用,仅静置72小时后,其焊缝和螺栓紧固件等部位(传统防腐漆防护)即出现锈蚀现象,运动传动系统的滑轨、弹簧及键/销等关键运动部件于200小时后出现润滑油降解及基材腐蚀磨损现象。海上航行体的制动轮机、活塞杆、支撑接头以及轴承/轴套在其运行过程中同时经历干湿交替与摩擦磨损作用,大型海工装备的高冲击滑轨和高承载齿轮/齿条则长期受到高冲击载荷、应力腐蚀以及摩擦磨损的叠加作用。 海上风电机组从发电机到齿轮箱以及变桨距机构整个传动链都安装了运行状态的远程在线监测系统,涉及复杂的滑轨及齿轮等传动设计,现采用的传统油脂润滑方案在海洋盐雾氯离子和高温水汽作用下极易发生油脂降解而引起传动部件的摩擦-腐蚀损伤甚至失效,极大威胁着风机电阻的传感监测安全。 海上钻井平台轻量化高技术装备常采用铝-碳钢异类金属耦合的承力底座设计,在冲击和振动作用下会发生摩擦和磨损,且未采用任何防腐处理的底盘基座会因发生电偶腐蚀而加速裂纹产生与扩散,甚至导致基座开裂而损坏。尤其在高温高湿高盐的热带海洋盐雾气氛条件下,各影响因子间的耦合加速失效作用更加猛烈。 针对与热带海洋气氛直接接触的机械开放运动系统/部件,其摩擦磨损问题主要通过自润滑涂层技术解决,腐蚀问题也主要通过绝缘耐蚀涂层材料技术解决。 但是,由于摩擦磨损产生的新的表面活性高,会加快腐蚀速率,如加速氯离子渗透并与亚表面甚至深层材料发生化学反应,而腐蚀产生的孔洞或异质相晶界弱化材料力学性能,加快磨损速率。 因而,热带海洋气氛下的开放运动系统/部件的磨损与腐蚀是耦合损伤(图1),需要发展兼具有自润滑与防腐功能的涂层材料与技术,同时解决摩擦磨损和腐蚀问题。 图1 (a)海上钻井平台、(b)海上风电、(c)舰船和(d)水陆两栖飞机等热带海洋工程装备图片以及(e)面临的摩擦腐蚀挑战 自润滑涂层技术的海洋应用 自润滑(亦称为固体润滑)涂层技术具有优异的减摩耐磨性能,是解决机械传动系统/部件摩擦、磨损、烧蚀及疲劳失效等难题的有效途径之一。 目前基础研究与应用方面较成熟的自润滑技术包括润滑脂、硬质碳基薄膜、陶瓷涂层、轻合金微弧氧化涂层、MoS2基粘结涂层和功能一体化高分子涂层等,主要针对航空航天、核电及军工高技术装备的传动系统关键部件的润滑性能提升与可靠性保障。 随着海洋科技的迅猛发展以及海洋工况的复杂、多变,传统单一组分的润滑薄膜材料面临严峻挑战,学者们针对自润滑技术的海洋应用开展了大量的研究工作。 ▷ 硬质自润滑薄膜技术研究进展 张俊彦等研发的类富勒烯结构DLC涂层表现出超长寿命(>1.8×105 循环)和超低磨损率(2.2×10-8 mm3·N-1·m-1),然而高度sp3杂化的DLC涂层的摩擦系数和粘附性能受到环境条件影响显著。研究表明,DLC涂层在水中的磨损随着氢浓度的增加而增加,通过Si掺杂构筑多层结构DLC薄膜可在一定程度上降低磨损率。 对于潮湿大气环境,张广安等通过第一性原理计算和模型拟合来研究水蒸汽压力下摩擦过程时,滑动界面吸附的水分子变化,揭示了DLC涂层摩擦系数随水蒸汽压力变化的内在机制,建立了摩擦系数与气体压力关系的数学模型,该模型的建立为DLC涂层于海洋盐雾气氛环境的摩擦预测提供了良好的基础。 针对海洋海水腐蚀磨损工况,薛群基等研究了316L钢基WC/Ni60涂层、F690钢基TiSiN-Cu纳米复合涂层以及304钢基(Cu,Ce)/Ti-DLC膜等硬质自润滑薄膜在人工海水中的摩擦磨损行为及电化学腐蚀参数。以上研究表明,通过构筑力学传递合理的多层结构,可有效延长硬质自润滑薄膜在海水环境下的耐磨寿命,但该类涂层应用于工程环境时,一旦被碰伤或穿透,其组分-组分之间以及涂层-基材之间的电极电位差可能会诱导电偶腐蚀,引起界面失效。 针对海洋盐雾腐蚀磨损工况,研究学者通过对比304不锈钢、GCr15和9Cr18三种基底表面上Ti掺杂含氢DLC薄膜在盐雾试验后的摩擦学性能,发现后两种基底薄膜的摩擦寿命降低约50%。利用Pb/Ti金属复合相对MoS2氧化的抑制作用,构筑MoS2/Pb-Ti纳米多层薄膜可有效提升MoS2基自润滑薄膜的热带海洋环境适应性,其于南海岛屿暴露6个月后仍然保持较低的摩擦系数与一定耐磨寿命。 以上研究表明,设计力学传递合理、界面匹配、结构致密且化学性能稳定(抗氧化)的自润滑硬质薄膜是保障其海洋环境适应性(耐盐雾、耐海水性能)和突破海洋工程应用极限的关键之一。前人通过模拟自润滑技术的不同应用工况(摩擦速度、承载应力和摩擦方式等),研究了DLC薄膜和陶瓷涂层等自润滑硬质薄膜材料在潮湿大气、盐雾、盐水或其他腐蚀介质中的摩擦磨损行为,以及腐蚀介质环境对其转移膜形成的影响机制。 但对于该类薄膜材料在单一电化学腐蚀(化学场)下的组织结构演变规律及静态失效机制鲜少报道,作者认为,研究揭示薄膜材料在单一热场和化学场下的组织结构演变机理,或许有助于理解其在磨损腐蚀工况(热-力-化场耦合作用)下的动态损伤失效机理并提出有效的防护设计原理。 近年来我国大力发展海洋经济,轻量化的海洋装备制造业蓬勃发展,但新型高强度轻合金在海洋盐雾气氛的静态腐蚀工况下易发生点蚀和晶间腐蚀,导致合金材料的力学性能快速劣化。研究报道了TC4钛合金在海水动态磨损腐蚀条件(力-化学场)下的总腐蚀磨损量明显大于其在阴极保护条件(力场)下的纯磨损量(占总腐蚀磨损量的65.9%~89.8%),量化地证明了海洋腐蚀介质磨损-腐蚀工况下轻合金的“化学-力场”耦合损伤效应。 因此,针对轻合金传动/运动关键部件表面,发展自润滑耐磨防腐功能一体化的动态防护涂层技术是近年来的研究热点之一。阳极氧化与微弧氧化(MAO)是提高铝、镁和钛等轻合金表面硬度及耐蚀性的常用技术手段,微弧氧化还因具有表面零增量(向内生长)的技术优势被广泛采用。 虽然阳极氧化与MAO涂层材料通常钝化且化学性能稳定,相比于前述碳基薄膜的环境敏感性有一定优势,但在其加温电解制备过程中常常会产生气体而生成多孔层结构,这极不利于阻挡腐蚀介质的渗透,容易在涂层-基材界面处发生腐蚀,进而导致动载下的结合失效问题。赵文杰等发现具有纳米管结构的TC4阳极膜由于其较高的比表面积和较大的毛细作用力而显示出较差的防腐性能。 研究表明,不管是DLC薄膜、MoS2基硬质薄膜、陶瓷涂层或是轻合金微弧氧化膜,在其加温溅射、热喷涂、离子镀及电解沉积等制备过程中常常产生孔隙等缺陷结构,当这些自润滑硬质薄膜应用于高温高湿高盐的海洋盐雾气氛环境时,腐蚀介质一方面穿过表面微孔及涂层内部孔隙缺陷到达基体发生腐蚀;另一方面在裂缝和蚀孔内部形成“闭塞电池”,在闭塞区内发生贫氧、酸化和氯离子富集,在闭塞区外由于电化学条件的差异产生自催化加速腐蚀效应。 综上所述,仅靠单一的硬质薄膜技术尚难以独立、有效地满足高温高湿高盐的热带海洋盐雾气氛下装备关键运动部件(齿轮、轴、导轨等)的动态摩擦-磨损-腐蚀长寿命及高可靠性保障。为了弥补上述不足,前人对DLC薄膜、MoS2基硬质薄膜、CrN涂层以及MAO涂层等自润滑硬质薄膜开展了改性填充和掺杂封孔等复合增强研究,通过构筑多相或多层致密结构,优化力学承载性,提升涂层在空气、盐雾和盐水环境下的摩擦磨损服役长效性。 薛群基等通过Zr掺杂方法有效改善了MoS2涂层在高湿环境下的化学稳定性与减磨耐磨性。张广安等在MoS2薄膜基础上引入Ti和Pb元素,设计构筑复合及多层结构,通过调控制备工艺提高了薄膜的致密性以及抗氧化性,在交变湿度环境下表现出良好的摩擦磨损性能。 王鹏等制备出具有纳米级周期性自组装多层结构的Mo-S-C-N复合薄膜,使薄膜表面硬度提升了近3倍(9.76 GPa),空气条件下显示出较低的磨损率。以上研究工作对于未来将二硫化钼基硬质薄膜技术拓展应用至海上运输和发射航天器关键部件等工程领域具有重要意义。 李焰等则提出了插入夹层的设计思路,利用多层结构构筑复杂的穿透路径及提升涂层力学强度,有效延长了盐雾条件下NiCr-Cr3C2金属-陶瓷复合涂层以及海水条件下TiSiN/Ag纳米多层涂层的耐磨寿命。 陈俊锋等和尹登峰等通过在MAO涂层表面原位合成MgFe-LDH纳米片(层状双金属氢氧化物)或利用CeO2颗粒促进镁合金MAO层的自密封行为来优化MAO涂层的致密结构。 尽管以上硬质复合涂层的设计策略可一定程度抵抗腐蚀介质在涂层内部渗透,提升涂层抗腐蚀能力,但由于此类硬质复合涂层中存在多种硬-硬界面,遇冲击载时容易产生裂纹甚至脱落,或许可以通过在其表面复合制备可与之键合匹配的软质自润滑涂层吸收冲击能,同时降低硬质涂层于干摩擦工况下普遍偏高的摩擦系数(μ>0.1),提升硬质自润滑涂层的抗冲击和减摩耐磨能力。 ▷ 软质自润滑高分子涂层研究进展 罗荘竹等针对南海装备所面临的“摩擦-磨损-腐蚀”共性工程技术难题,结合前期在工程防结冰PTFE/PPS高分子合金涂层的设计构筑及应用性能研究的积累,选用综合性能良好的改性聚氨酯树脂粘结剂、含氟聚合物填料和混合有机溶剂,采用传统的常温喷涂工艺,利用两种聚合物组分之间交联缠结,一步成膜制备出化学稳定且结构致密的软质耐磨防腐高分子涂层材料,如图2(a)所示。其涂层厚度为(30±5) μm,仅为传统3层防护体系(>300 μm)的1/10,在载荷为11 MPa、转速为1.05 m/s、温度为25 ℃、湿度为60%~70% RH的干摩擦测试条件下,涂层稳定摩擦系数为0.06~0.08,耐磨行程约0.6 km/μm,是传统聚氨酯型防腐涂层的100倍,而摩擦面温升仅约45~60 ℃,随温度升高,摩擦系数不断降低,可低至0.03~0.04,如图2(b)所示。 图3 (a1, a2)高分子合金涂层微观表征分析、(b1, b2)涠洲岛热带海洋暴露试验及(c1~c4)高分子合金涂层性能测试结果照片 相比中性盐雾加速腐蚀试验,热带海洋大气暴露试验为海洋盐雾气雾、紫外光、氧和热等多因素耦合的试验方法,虽然其试验周期长,但可更合理、科学地评价/考核耐蚀涂层的实际防护寿命。通过将中性盐雾加速腐蚀试验、热带海洋暴露试验和涂层表面微观分析手段有机结合,根据涂层在中性盐雾/海洋气氛中暴露前后表面组成(C1s谱峰相对强度)衰减变化量推算得知,1200小时中性盐雾试验相当于2.5年实际热带海洋暴露防护寿命,初步建立了实验室中性盐雾与实际热带海洋暴露的对应关系规律。 海洋装备表面防护材料的长效性一般要求10~30年,为了适应南海高温、高湿的盐雾环境,该类具有低膜厚(30~60 μm)特点的动态耐磨防腐软质高分子涂层体系的耐盐雾性能还应提升至6000小时以上。 此种低膜厚且热带海洋长效稳定的自润滑高分子涂层技术突破了传统“底-中-面”高膜厚三层防护体系的技术瓶颈,实现自润滑技术与静态防腐技术协同融合,可能是解决热带海洋盐雾气氛“高承载-低中速”工况下的磨损-腐蚀耦合损伤的有效手段之一。但由于高分子材料自身的力学强度有限,导致软质高分子涂层的剪切强度及耐磨寿命难以满足“重载-高速”摩擦工况的要求,需要发展与其匹配性良好的复合增强涂层技术来弥补。 ▷ 硬-软梯度自润滑防腐涂层研究进展 对比结果如图4所示,在长时间腐蚀化学场作用下,45#钢基材锈蚀严重,出现碎屑状剥落,由于贯穿空隙及晶间裂纹影响,45#钢表面的DLC薄膜能够保持完整但出现腐蚀斑点,局部发生脱落,DLC薄膜-高分子合金涂层未发生明显的腐蚀现象,对45#钢基材表现出较好的腐蚀防护效果。 海洋环境摩擦-腐蚀模拟评价 ▷ 液体介质环境磨蚀研究方法 ▷ 中性盐雾与海洋大气暴露试验方法 以上研究表明,“静态腐蚀+动态磨损”2步法的测试结果可一定程度地反映腐蚀工况对涂层材料减摩耐磨性能的弱化作用,但该分步测试评价方法仍无法模拟真实的海洋盐雾气氛所特有的磨损-腐蚀耦合效应。因此,为了揭示自润滑涂层在热-力-化学耦合作用下的动态失效本质(图5),亟需建立实际热带海洋盐雾气氛下涂层摩擦、磨损、腐蚀及电化学腐蚀行为的动态实时监测测试手段/方法。 ▷ 热带海洋气氛摩擦磨损实海在线监测新方法 图6 热带海洋气氛摩擦磨损实海在线监测装置设计 ▷ 实际热带海洋装备考核试验验证(国防装备和海洋平台等工程应用示范) 研究团队已联合了攀钢集团、中远海运、中海油和珠海云洲智能科技有限公司等10余家装备制造企业共同攻关/提升其海洋装备产品的海洋环境适应性及运行可靠性(图7),定型产品有10余种,已在珠海东澳岛、海南陵水和广西涠洲岛建设的由南海临海至南海深远海的“多海域热带海洋环境盐雾腐蚀暴露试验基站”开展固体润滑材料和自润滑耐磨防腐防护等新型功能材料的热带海洋环境适应性考核及南海海洋工程应用示范验证。 结论与展望 随着我国“南海海洋纵深开发”战略规划及相关海洋利益的拓展,国家海洋战略使命也由内陆及近海扩展到远海及大洋。高盐、高湿的热带海洋区域,伴随海浪飞溅、盐雾气氛腐蚀、强风干湿对流及太阳光老化等复杂工程环境作用,我国海洋工程高技术装备滑轨/导轨、轴/轴承和齿轮/链轮传动系统等关键部件的减摩耐磨及防腐防护需求不断提升。现有润滑技术及静态防腐技术远远不能满足装备运动传动系统/部件在热带海洋高精度、高可靠和长寿命运行的要求。 目前,如何解决热带海洋气氛中特有的磨损与腐蚀耦合动态损伤是现有海洋工程设备与运动部件所面临的重大科学问题与技术难题。 ▷ 硬软复合自润滑防腐材料-构筑原理创新 图8 碳基薄膜-硅碳氧纳米薄膜-高分子合金涂层构筑示意图 其中,硬质碳基薄膜的作用是提高金属基底的表面硬度和承载能力,介于无机和有机特性的硅碳氧纳米薄膜的作用是通过与碳基薄膜针孔边缘的悬键和高分子合金层的化学键合,实现两个界面的高结合力,同时阻断氯离子向碳基薄膜的穿透,软质高分子合金的作用是吸收部件启动时的冲击能量,降低摩擦疲劳损伤,同时,抑制氯离子吸附和渗透。 在腐蚀摩擦过程中,软质高分子合金的疏水特性抑制氯离子吸附和渗透,弹性结构吸收启动冲击能量,降低摩擦疲劳损伤,从而抑制腐蚀并降低磨损。 在服役过程中,即便高分子合金层被磨损消耗,硅碳氧封孔防腐层表面因摩擦产生的官能团(如-OH)和氯离子反应并阻断后续氯离子吸附穿透,由于硅碳氧嵌入碳基薄膜针孔并化学键合,与硬质碳基薄膜成为一体继续起到耐磨防腐作用。 对于运动非精密部件(齿轮、导轨、弹簧及紧固件等)采用软质自润滑防腐涂层,对于运动精密部件(滑轨/导轨、轴/轴承及齿轮/链轮等)选用“硬质薄膜+软质涂层”的复合匹配材料技术工艺,旨在提升海洋装备部件,尤其是热带海洋装备运动传动部件的长寿命及高可靠性。 ▷ 热带海洋气氛多场耦合摩擦磨损实海在线监测新方法建立 ▷ 海工装备全海域自润滑耐磨防腐防护材料技术体系建立 针对全海域复杂环境,开展海(H)、陆(L)、空(K)全口径海工装备自润滑耐磨防腐防护材料的全链条研发与工程化具有重大科学价值及经济社会效益。构建海工装备全海域(近海、深远海)“立体摩擦-腐蚀防护网格”与维护保障材料体系数据库(图9),开展H、L、K全海域典型海工装备自润滑耐磨防腐防护材料的工程示范及海试考核。 图9 海工装备全海域动态腐蚀防护与维护保障材料体系数据库示意图 建立相关数据库及技术工艺规范/标准,全面保障海工装备核心系统的海洋环境适应性,为提升我国“南海纵深开发”海洋工程装备的运行可靠性与防护/维保技术革新奠定理论基础及技术支持。 来源信息 作者:罗一旻,杨军华,李霞,谭生,王伟,罗荘竹,张广安,张俊彦 工作单位:中山大学材料学院,南京电子技术研究所,中国科学院兰州化学物理研究所固体润滑国家重点实验室 来源:摩擦学学报、中国腐蚀与防护网
免责声明:本网站所转载的文字、图片与视频资料版权归原创作者所有,如果涉及侵权,请第一时间联系本网删除。
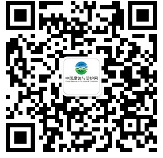
官方微信
《腐蚀与防护网电子期刊》征订启事
- 投稿联系:编辑部
- 电话:010-62316606
- 邮箱:fsfhzy666@163.com
- 腐蚀与防护网官方QQ群:140808414