复合层能够有效提高零部件的表面质量、降低维护成本并延长使用寿命,因此广泛用于石油化工、工程机械、航海等领域零部件的表面性能改善等。
碳化钨材料具有良好的热稳定性、化学稳定性、抗氧化性,还具有熔点高、硬度大,耐磨性好的特点,因此常用作表面涂层。然而,纯碳化钨的润湿性较差,不能直接用于涂层制备,因此常将Co、Ni等金属作为黏结金属与纯碳化钨粉末混合,制造硬质合金和耐磨涂层。
超声速火焰喷涂
超声速火焰喷涂技术又称高速氧燃料火焰(HVOF)(喷涂)技术,是一种基于高速度粒子获得涂层的技术。利用特制的燃烧室或特殊的喷嘴,喷射引燃燃气或液体燃料形成高速、高压、高温的燃烧焰流,金属粉末经惰性气体送入焰流中加热,熔融的金属粉末加速撞击基体表面并快速凝固,连续沉积从而形成涂层。
01 工艺参数对涂层性能的影响
姚舜晖采用HVOF技术制备了碳化钨(WC,质量分数为20%)增强镍基合金涂层,研究表明WC颗粒的几何形状对于涂层耐磨性影响较大,对于圆形WC颗粒来说,在一定粒径范围内,其耐磨增强效果与颗粒直径正相关。
赵文胜分析了粉末粒径和喷涂道次对涂层耐磨性和耐蚀性的影响,结果表明所得涂层的孔隙率均小于1.5%,显微硬度为1000 HV,粉末粒径越小,涂层的孔隙率越低,且粉末粒径为5~15 μm,喷涂8道次条件下所得涂层在3.5%氯化钠溶液中的耐蚀性较好。
王大锋等研究了纳米结构、亚微米结构和常规结构的WC-10Co-4Cr涂层,发现涂层的脱碳率和孔隙率呈现先增大后减小的趋势,纳米结构涂层的显微硬度最高,亚微米结构涂层的显微硬度最低。
赵立英等研究表明,在HVOF喷涂过程中添加丙烷,可有效降低涂层的氧化和脱碳问题,涂层硬度和附着力随丙烷流量提高呈现出先升高后降低的趋势、而涂层孔隙率则先降低后升高。
张磊等的研究结果表明:涂层的孔隙率随送粉速率和喷涂距离的增大先降低后升高,随喷涂角度和丙烷流量的升高而降低;涂层显微硬度随喷涂角度的增大而升高,随丙烷流量、喷涂距离和送粉速率的增大先升高后降低。
刘杰等分析了煤油流量对于WC-12Co/NiCrBSi复合涂层的影响,结果表明随着煤油流量提高,涂层硬度提高,涂层孔隙率和耐磨性先降低后升高,涂层孔隙率最低为0.11%,硬度为927 HV。
韩旭等研究发现,粒子速度、温度和直径不沿火焰中心线对称,并且粒径越小,速度越高。
SONESTEDT等研究发现随着粉末粒径的增大和火焰功率的减小,涂层中Ti2AlC的含量增加,但涂层厚度减小,黏结性降低。
CABRAL-MIRAMONTES等研究发现涂层厚度随着喷射距离的增加而减小,火焰中粒子的温度随着喷射距离增加而升高,最佳喷射距离为229~254 mm。
MENDEZ-MEDRANO等分析了火焰类型(还原性、中性和氧化性)和喷枪喷嘴出口区域对于涂层组织、晶体结构的影响后发现,WC颗粒在喷涂过程中发生了相当程度的脱碳和溶解,相变程度取决于火焰化学成分,涂层的微观结构主要受喷嘴的影响。
JONDA等分析了基于HVOF制备的AZ31基体上WC-Co-Cr涂层的相组成、残余应力,结果表明相组织的峰值与WC有关,残余应力为压应力。
02 涂层的耐磨耐蚀性
代雪婷等采用HVOF技术在AF1410钢表面制备了厚200~220 μm的WC-10Co-4Cr涂层,并与电镀硬Cr涂层进行对比,结果表明WC-10Co-4Cr涂层的摩擦因数低于后者,磨损质量和磨损深度也远低于后者,但是二者的耐蚀性无明显区别。
刘福朋采用HVOF技术在304不锈钢基体上制备了WC-Co和NiCr-Cr3C2合金涂层,其硬度为1100~1400 HV,硬质相和黏结相相互错落分布,WC-Co在H2SO4中的腐蚀速率与H2SO4温度和浓度呈现正相关规律。
刘建武等采用HVOF技术制备了WC-10Co4Cr涂层,其硬度为1315 HV,孔隙率为0.33%,与传统镀铬层相比,硬度和耐磨性分别提高了约2倍和3.6倍。此外,WC-10Co4Cr涂层结构致密、结合强度高,具有良好的抗盐雾腐蚀性能。
黄博等研究发现WC-10Co-4Cr涂层的硬度随喷涂距离增大而提高,但是涂层孔隙率随喷涂距离增大而降低,涂层硬度最高为1100~1400 HV,此时涂层孔隙率小于1%,且在盐溶液中,涂层的耐磨性比304不锈钢高2个数量级。
范俊等研究发现WC-Co-Ni涂层中的WC相较多,力学性能较均衡,抗电化学腐蚀性能较好。
KOMAROV等讨论了不同粒径碳化钨粉末和颗粒组合对涂层疏水性的影响。结果表明粗粉和超细碳化钨颗粒组合可用于制备高疏水性硬质涂层,通过化学改性可使涂层进一步变为超疏水性硬质涂层。
JIN等分析了表面载荷对于HVOF技术制备的WC-12Co涂层耐磨性的影响。结果表明Fe和W在涂层与基体界面处的相互扩散使涂层具有良好的附着力,摩擦因数随着表面载荷增加而增大。
ASL等研究发现,采用HVOF技术所得WC-17Co涂层结构致密,厚度为500 μm,但后续进行真空热处理易导致涂层附着失效。
等离子喷涂
等离子喷涂(PS)是一种以直流驱动的等离子弧为热源的热喷涂技术。
01 工艺参数对涂层性能的影响
宋超群等研究发现当喷涂功率过低时,WC颗粒融化程度低;而当喷涂功率过大时,WC又会出现脱碳现象,最佳喷涂功率为65 kW,此时涂层孔隙率最低(0.87%)。
李万青等研究发现采用PS技术所得纳米结构涂层的致密性和结合强度高于微米涂层,前者孔隙率仅为0.56%,两者硬度相差不大。
黎红英等对比分析了大气等离子喷涂(APS)和HVOF技术的工艺参数对WC-Ni涂层性能的影响。结果表明较大功率下,APS所得涂层致密,但脱碳程度大;当喷涂距离较小时,HVOF技术所得涂层致密,脱碳程度小。
AFZAL等研究发现,在一定范围内,较远喷涂距离条件所得涂层的孔隙率较低,厚度较小,界面良好。
鲍君峰等研究发现0.8 μm粒径条件下,WC-17Co涂层的力学性能最好,随着WC粒径增大,涂层孔隙率增大,结合强度和硬度降低,磨损量增大。
富伟等研究发现,在适当的喷涂距离下,涂层脱碳程度和致密度随喷涂功率上升而上升。
安连彤等分析发现,提高电弧电压有利于粉末的融化,提高涂层耐磨性和硬度,但电压过高会反而使Wc-Co涂层质量劣化。
伏利等利用高焓等离子喷涂法所得WC-10Co-4Cr涂层的孔隙率为0.77%,硬度达到1210 HV,耐磨性为0Cr13Ni4Mo钢基体的143倍,适当提高粒子速率和温度可提高涂层结合强度。
KUZMIN等基于超音速空气等离子喷涂喷枪,制作了孔隙率小于0.4%的WC-10Co-4Cr涂层,其硬度也比HVOF所得涂层更高。
ANWAR等采用氮气包裹CO2激光对WC-12Co涂层进行表面处理后发现,表面涂层的附着力和基体硬度显著提高,且表面无缺陷。
02 涂层的耐磨耐蚀性
梁存光等的研究表明喷涂距离太近,WC涂层的脱碳行为严重,耐磨性较差,而喷涂距离过远,涂层结合强度低,抗冲蚀及磨蚀能力差。
徐一等分析了基于超音速等离子喷涂的WC-10Co4Cr涂层在不同条件下的耐磨行为,结果表明涂层中存在未融化颗粒,涂层硬度达到1408.2 HV,干燥条件下涂层磨损以磨料磨损为主,湿润条件下以黏着磨损为主,后者磨损率远低于前者。
袁晓静等研究发现采用PS所得纳米结构WC-10Co4Cr涂层在高低温下的摩擦因数和磨损率优于微米结构涂层,可有效提高1Cr18Ni9Ti钢在3.5% NaCl溶液中的腐蚀电位。
JIANG等对比分析了基于APS和HVOF技术制备的Al2O3-40TiO2和WC-10Co-4Cr两种涂层在NaCl溶液中的耐蚀性,结果表明短期内WC-10Co-4C涂层的耐蚀性更好,但是Al2O3-40TiO2涂层的长期耐蚀性更好。
HOU等研究了喷涂功率对WC-(W,Cr)2C-Ni涂层性能的影响,结果表明中等喷涂功率下所得涂层的断裂韧性最高,界面结合力最强,耐磨性最好。
等离子熔覆
等离子熔覆技术的原理在于将等离子弧热源作用在预制的熔覆层粉末或者同步送粉,使熔融的粉末与部分熔化的基体呈现冶金结合。
01 工艺参数对熔覆层的影响
卢金斌等利用等离子熔覆技术在Q235碳钢表面制备了含50% Ni-WC的Fe-Cr-B-Si合金涂层,其显微硬度为560~820 HV。
屈平等采用等离子熔覆技术在Q235碳钢表面制备了Ti(C,N)-WC涂层,结果表明在一定范围内,涂层硬度和耐磨耐蚀性随碳化钨含量提高而提高,并且当碳化钨质量分数为12%时,涂层的耐磨耐蚀性最优。
王笑生采用等离子熔覆技术在Q235钢板上制备了镍基碳化钨熔覆层,并分析了铸造和单晶碳化钨含量对镍基合金防护性能的影响。结果表明在Ni25合金熔覆层中加入60%铸造碳化钨,涂层耐磨性最佳,单晶碳化钨熔覆层的耐磨性较低。
PENG等研究发现随着WC含量的增加,FeCoCrNi高熵合金/碳化钨复合涂层的组织变得更加复杂,当WC质量分数为60%时,涂层具有最佳的耐磨性,硬度为690 HV。
02 熔覆层的耐磨耐蚀性
XIE等研究表明,三种镍基WC涂层表面无裂纹且孔隙率极低(<1%)。等离子熔覆层的维氏显微硬度随熔覆WC量的增加而增加。熔覆层的显微硬度和电化学行为与镀镍WC粉的含量有关,熔覆层的腐蚀可能是熔覆层中相间的微镀锌腐蚀。
胡明强采用等离子熔覆技术在高锰钢表面制备碳化钨-镍基合金复合涂层,结果表明熔覆涂层厚度可达1~2 mm,且涂层质量好,表面无缺陷,涂层表面硬度最高为621.77 HV。
吴磊等利用等离子熔覆技术制备了涂层,研究碳化钨含量对于镍基碳化钨涂层组织性能的影响,结果表明涂层表面无气孔缺陷,在一定范围内,涂层耐磨性和硬度随碳化钨含量显著提高,当碳化钨质量分数为50%时,涂层硬度和耐磨性最好,硬度达到1024 HV。
XIE等研究发现在室温下,涂层的耐磨性随着WC含量的增加而逐渐提高,硬度最高达到954.64 HV,随着温度的升高,涂层的耐磨性下降,碳化钨/钴基涂层的磨损机制为氧化磨损。
激光熔覆
激光熔覆(LC)是将高功率密度激光束辐照到基材表面,使基材与熔覆层材料迅速熔化凝固,获得与基材冶金结合的涂层。
01 工艺参数对熔覆层的影响
张煜等对比分析了超高速和低速激光熔覆技术对涂层的影响,结果表明采用超高速激光熔覆技术,可以在保证冶金结合的同时,大大抑制基体元素对涂层稀释,同时抑制涂层中WC颗粒热损伤和空隙的形成,降低残余应力,避免裂纹产生。
邱焕霞等通过数值模拟方法发现预热可明显降低激光熔覆层的温度梯度和冷却速度,抑制表面裂纹生成,且最优预热温度为200 ℃。
刘泽研究了不同尺度WC对Ni基熔覆层微观结构的影响,结果表明在微米尺度涂层的界面结合力和晶粒尺寸随热处理温度的提高而升高,但是硬度和耐蚀性则随热处理温度的提高而下降;亚微米结构涂层的摩擦因数和磨损率随热处理温度的升高呈现出先降低后增加的现象;微纳米结构涂层的冲蚀磨损速率分别为微米和亚微米结构涂层的1/24、1/6。
朱继祥研究发现,当WC质量分数为20%~50%时,WC铁基涂层的硬度值随WC含量的上升而提高,且当WC质量分数为30%时,涂层的耐磨性最优。采用数值模拟方法研究发现熔覆层与基材结合处存在较大残余拉应力,易产生纵向裂纹。
樊帅奇等讨论了Ni60+30% WC涂层和Ni60+30% Ni涂层中WC初始形态对涂层性能的影响。结果显示前者内部存在少量孔洞和微裂纹,后者组织均匀致密,无气孔和裂纹。
ZHOU等研究发现激光熔覆涂层的裂纹主要源于熔覆层和基体的界面,提高激光熔覆速率可以降低复合涂层的孔隙率,此外,提高基体预热温度可大大降低涂层出现裂纹可能性。
ERFANMANESH等对比分析了镀镍WC-12Co粉末和商用WC-12Co粉末对激光熔覆层性能的影响,结果发现前者能显著降低复合涂层的孔隙率,获得高质量的复合涂层。
BARTKOWSKI等分析了工艺参数对于Fe/WC金属基复合涂层性能的影响,结果表明复合层厚度随着激光功率和进粉速度提升而增厚,当送料速度为12.50 g/min时,复合涂层的显微硬度达到1400 HV,涂层的耐蚀性随着涂层中WC含量的增大而增强。
02 熔覆层的耐磨耐蚀性
李礼等在Cr12MoV钢表面激光熔覆Ni60A-35% WC涂层,研究显示涂层与基体间无裂纹和气孔缺陷,硬度为基体的1.7倍。涂层的磨损机理为疲劳磨损和磨粒磨损,而基体则为黏着磨损和磨粒磨损。
肖奇等研究发现在一定范围内,WC可细化Ni60A-WC涂层晶粒,Ni60A-WC 涂层在不同pH环境中的耐蚀性与WC加入量呈负相关,复合涂层在中性、碱性和酸性腐蚀环境中的耐蚀性依次递减。
杨行等分析了WC含量对于WC-Cr覆层耐磨性影响,结果表明25WC-1.5C覆层的显微硬度达到666.3 HV,磨损率仅为基体的30%。
何波等研究发现碳化钨/钴基合金复合涂层的显微硬度和耐磨性比Co基合金涂层明显提高,且磨损质量损失量仅为后者的48%。
真空熔覆
真空熔覆技术是将具有需某种特殊性能的金属粉末涂敷在预处理后的零件表面,在一定真空度下,经一段时间高温烧制后,涂覆层与基体间产生分子间结合或化学结合,进而提高零件的使用性能和寿命的技术。
01 参数对熔覆层的影响
路王珂等分析了WC含量、熔覆温度对镍基真空熔覆层的影响。结果表明随着WC质量分数从20%增大到40%,熔覆层的耐磨性提高,但是结合力出现先增后降趋势,当WC质量分数为40%时,WC颗粒之间或者周围出现大量孔洞。熔覆层厚度随熔覆温度升高而增厚,但若温度过高,WC颗粒会分解严重,熔覆层耐磨性下降,最优熔覆温度为1225 ℃。
马世博等研究发现,当WC质量分数小于60%时,涂层缺陷较少,耐磨性、显微硬度均随WC含量上升而增强;但当WC质量分数超过60%,涂层出现气孔和未浸润缺陷,结合力下降。
何力分析指出WC-10Ni/NiCrBSi涂层中WC的适宜加入量为30%~45%,此时涂层与基体达到冶金结合,当WC含量过少时涂层表面成型较差,当过多时涂层与基体润湿反应较差,无法形成有效冶金结合。
苏科勇等研究发现能与正火态45钢基体形成有效冶金结合的WC质量分数为10%~40%,随着WC含量提高,WC颗粒周围孔洞增多,涂层耐蚀性降低,最佳WC质量分数为30%。
姚永强等分析了真空和基体预热温度对于WC-Ni基涂层性能的影响,结果表明基体预热和真空环境中涂层显微硬度低于大气环境中氮气吹扫和不预热的涂层,但是前者的稳定摩擦因素仅为0.5,且耐磨性更高。
YANG等研究发现基于真空熔覆技术制备的Ni/WC复合涂层由复合层、过渡层、熔合层和扩散影响层组成,复合层的显微硬度为基体的6倍、整个复合材料熔覆层的形成主要取决于烧结颈的形成和长大、WC颗粒的浸润以及其随温度和保温时间的增加而完全融合。
TAO等研究表明,原位合成的WC增强相在复合层中的分布比外部添加的WC相更加均匀,并且后者易发生断裂和WC颗粒脱落。
02 熔覆层的耐磨耐蚀性
黄新波等研究发现当添加15% WC时涂层的耐蚀性最佳,在10%盐酸溶液中,涂层耐蚀性为45钢基体的10倍,腐蚀出现在基体和涂层界面处。
周新星研究发现熔覆层硬度随WC含量提高而提高,少量WC可以增强涂层的耐蚀性,但WC量过大会导致位错和点阵畸变,降低涂层耐蚀性。
张喜冬研究表明当熔覆温度为1225 ℃,WC质量分数为30%时,熔覆层的耐磨性和耐蚀性分别为基体45钢的6倍和10倍。
ZHANG等在制备真空熔覆WC/NiCrBSi层的过程中发现,原位合成WC增强相和外部添加WC增强相涂层的耐蚀性都高于316L不锈钢基材,但是前者WC颗粒与基体紧密结合,其锚定作用可防止微裂纹的形核和扩展,故前者的耐蚀性、抗空化能力更强。
HAN等分析了熔覆温度和WC含量对于NiFeCrBSi/WC熔覆层硬度和耐磨性的影响,表明熔覆温度越高,WC溶解越严重,当熔覆温度为1225 ℃时,涂层的耐磨性随WC含量的增加先增大后减小,当熔覆层WC质量分数为30%时,其耐磨性较好。
结束语
超声速火焰具有较低的温度和高速的焰流优点,所制备的WC涂层具有硬度高、孔隙率低、氧化物、脱碳少和耐磨性好等特点,因此可用于快速制备大面积且厚度可控的梯度耐磨涂层。但是由于设备运行成本高且粉末价格较高,因此WC涂层的制备成本较高,且涂层容易存在夹杂和副产物。
等离子喷涂由于喷涂温度较高,涂层具备结合强度高、工作环境适应性强优点,且在制备过程中辅助惰性气体保护,因此粉末不易被氧化,但是涂层制备成本比较高,设备比较复杂。基于等离子喷涂技术制备的金属涂层与基体的结合属于机械结合范畴,涂层中的硬质颗粒很容易脱落。
激光熔覆技术具备速度快、热影响区域小、工件形变小、熔覆层稀释率小等特点,因此环保、高效、灵活,自动化程度高,但是由于其能量集中、能量大,因此涂层中会存在较大的残余应力,且容易产生裂纹和气孔缺陷。
等离子熔覆技术的熔化速度快,涂层和基体结合力强,硬度均匀,孔隙率低,不容易产生质量缺陷,且涂层中的氧化物与杂质相对较少,因此涂层更厚、耐磨性和耐蚀性也更高,但存在涂层质量控制比较困难,涂层精度难以精准控制、实际性能难以满足预期目标等缺点。
如何进一步优化工艺参数,提高涂层的致密度、强化涂层与基体的结合力,是不同WC涂层制备技术后续发展的重点。当前涂层耐磨性和耐腐蚀性的研究主要针对单一因素,比如干摩擦或者湿摩擦,或者单一腐蚀环境。但在涂层实际服役过程中,可能是腐蚀、磨损和疲劳等多因素协同作用,因此有必要对复杂服役环境中涂层的性能开展深入研究。
免责声明:本网站所转载的文字、图片与视频资料版权归原创作者所有,如果涉及侵权,请第一时间联系本网删除。
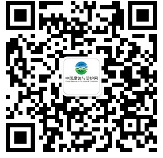
官方微信
《腐蚀与防护网电子期刊》征订启事
- 投稿联系:编辑部
- 电话:010-62316606
- 邮箱:fsfhzy666@163.com
- 腐蚀与防护网官方QQ群:140808414