摘要
对核电站常用不锈钢和镍基合金等结构材料在服役的高温高压水中的应力腐蚀裂纹萌生测试的实验方法、评价指标、影响因素和萌生机理等几个方面进行论述,并指出目前研究的不足和未来研究趋势。
关键词: 核电站 ; 结构材料 ; 高温高压水 ; 应力腐蚀开裂 ; 萌生机理
核用结构材料长期在高温高压水环境中服役,同时还承受由材料自身制造冷加工、工装应力以及高温水热应力等导致的综合应力作用,在环境和力学的交互作用下,具有发生应力腐蚀开裂 (SCC) 的风险。此外堆芯结构材料还具有发生辐照促进应力腐蚀开裂的风险。核电站现场的失效案例表明,核电厂20%~40%的腐蚀失效案例均涉及SCC,在所有腐蚀类型中位列第一[1,2]。据统计,SCC多发生在由镍基合金和不锈钢制造的蒸汽发生器、控制棒驱动机构以及堆内构件等部位[3,4]。SCC可以分为缓慢的裂纹萌生和较快的裂纹扩展两个阶段,裂纹萌生又可以细分为裂纹萌生条件形成的先导阶段 (铅积累、合金元素的贫化等)、裂纹的孕育阶段 (发生晶界蠕变、氧化膜成分改变和晶界扩散等,但是裂纹一般可忽视,不可见) 和裂纹的低速扩展阶段 (裂纹缓慢增长或合并)[5]。实际上,在材料发生失效的总服役寿命中,裂纹萌生时间一般可占到约90%,而裂纹一旦萌生并达到一定的临界长度 (一般在50~500 μm) 后,将以一定的速率稳定扩展,最终将快速失稳扩展导致材料失效,因而裂纹扩展阶段的时间仅约占10%,甚至更低[5]。
目前国内外很多研究机构[6-13]针对核用结构材料的SCC扩展过程已经做了大量的研究,研究表明不锈钢与镍基合金在高温高压水中的SCC裂纹扩展速率一般为10-6~10-9 mm/s。在实验室模拟环境中利用直流电位降 (DCPD) 等技术原位获得载荷条件、温度和水化学等各种因素对裂纹扩展速率的影响规律[9,14,15],就可以借助计算机建模对带裂纹构件的剩余服役寿命进行计算和评价[16]。与裂纹扩展阶段具有稳定和相对较快的裂纹扩展速率相比,裂纹萌生在光滑试样或无明显缺陷的部件表面不易发生,具有试验周期长,萌生位置随机以及不易检测等难点,相对于SCC扩展研究相对较少。
针对核用结构材料的高温高压水SCC行为研究,目前已有研究者进行了综述。例如朱若林等[17]对核电异种金属焊接接头的应力腐蚀裂纹扩展行为、张克乾等[18,19]对核用结构材料SCC裂纹扩展的研究现状进行综述。马成等[20]和焦洋等[21]对核用不锈钢在高温高压水中SCC行为的研究进展进行了综述,其中对SCC萌生行为研究并未进行详细论述。
综上,SCC萌生由于存在不易检测,实验周期长等难点,相比于SCC扩展研究较少。然而材料大部分的服役时间都是处在裂纹萌生阶段,因此裂纹萌生对于评估核电站寿命更具有价值。研究各种因素对SCC萌生的影响,弄清SCC萌生的相关机理,对预防材料失效和核电站的寿命评估与延寿具有重要意义。本文就目前研究中常用的核用不锈钢和镍基合金SCC萌生的常用实验方法、评价指标、影响因素和机理等几个方面的研究进行论述,并指出目前研究的不足和未来研究趋势。
1 裂纹萌生所用的实验方法
核电站的服役寿命大约为40~60 a,在实验室不可能开展如此长时间的同步测试。为了节省成本和时间,实际研究中常采用加速实验。即使是加速实验,在考虑力学和环境的综合作用时,实验周期还是相对比较长。下面介绍几种常用的SCC萌生测试的加速实验方法。
1.1 恒应变实验
恒应变实验是使试样处于特定的几何形状而保持应变不变来评价SCC萌生的方法,比如U弯,反U弯,C环试样等。特点是操作简单,可以同时对多个试样进行实验,定期取出试样观察试样应力腐蚀状态,效率高[22]。但是在高温高压水中随时间的延长会发生应力松弛,偏离原始应力状态[23]。
1.2 恒载荷实验
恒载荷实验在实验过程中使试样保持恒定载荷。有研究[24]表明恒载试验中只有应力等于或高于所测试材料的屈服应力时才可能萌生裂纹,所以恒载试验载荷一般要略高于试样的屈服强度。所用试样一般为棒状试样或钝口紧凑拉伸试样,恒载实验的萌生时间一般通过定期中止实验检测萌生情况来确定,近年来也有很多研究利用DCPD技术检测电位或计算的参比应变值与时间关系曲线的拐点来原位确定裂纹萌生时间[25-29],参比应变表达式为
(1)
式中,Vgauge0和Vref0分别为最初未受力时的标距段和参比段电位,Vgauge和Vref分别为实验过程中实时的标距段和参比段电位。实验过程电流恒定,当试样表面产生裂纹时,标距段横截面减小,电位增大,最终参比应变增大。图1为实际恒载实验过程中检测到轧制退火态600 (600MA) 合金裂纹萌生的实例。如图1a所示,图中拐点位置表明裂纹已经萌生,即裂纹萌生时间为1250 h。图1b和c分别为该试样表面和截面观察到的裂纹。恒载实验更接近核电站中材料的静态应力的实际服役条件,所以该方法有较大的应用前景,但是对于SCC敏感性小的材料实验周期则会非常长[30]。
图1 DCPD检测600MA合金裂纹萌生的实例[26]
1.3 恒定拉伸速率实验 (CERT) 或慢应变速率拉伸试验 (SSRT)
在实验环境下以较缓慢的恒定拉伸速率将试样拉到一定的应变值或持续拉断,然后取出试样进行相关的检测。该方法特点是实验周期比较短,并且可以评价SCC敏感性较低的材料 (如690TT合金等) 的裂纹萌生行为,也是目前文献中比较普遍采用的一种SCC敏感性评价方法,但是结果对拉伸速率的依赖性比较大[31,32],并且会偏离静态应力下服役状态[20]。此外,材料发生塑性变形后表面残余应力很容易被消除[33-35],造成实验结果的误差。
2 SCC萌生的评价指标
2.1 萌生时间
萌生时间占据核电材料寿命的大部分时间,是评价核用材料寿命的重要指标。但是关于萌生时间的定义,还没有统一的说法。研究中通常将裂纹萌生时间定义为从实验开始到直至检测到有效裂纹长度时的累计测试时间[36]。也有专家将萌生时间定义为材料从服役开始到裂纹由缓慢扩展向快速扩展转变时的总时间[37]。而实际实验中,U弯实验时同时对多个平行试样进行实验,定期取出观察,当一半试样萌生裂纹时的时间定义为萌生时间[22]。进行恒载实验时,实验周期长,实样数量较少,但是DCPD技术检测到裂纹萌生信号时,试样表面已经存在了较多数量的裂纹[26],一定程度上也满足统计学规律,结果比较可靠。由此可见,增加检测频率和提高检测设备的分辨率有利于提高萌生时间测试的准确性。
2.2 裂纹大小、数量
裂纹萌生向扩展转变对应一个临界裂纹尺寸,所以材料的裂纹长度尤其是裂纹萌生的临界长度一直是研究中想明确的一个参数,但是影响临界裂纹长度的因素十分复杂。高应力、冷加工以及表面加工硬化层的引入都可能促使裂纹萌生而缩短临界裂纹长度[26,37-39]。而服役环境中的溶解氧、溶解氢和温度也对裂纹萌生有比较明显的影响,但是如何影响临界裂纹长度还不是很明确[25,40-42]。由此而见,萌生过程比较复杂,受各种因素影响,其临界裂纹长度还不能很好的确定,在未来研究中需要进一步明确。
因此实际实验时通常对材料表面萌生的裂纹进行统计来评估SCC萌生。文献中常用裂纹密度[31,43,44]、最大裂纹长度[43]、平均裂纹长度[45]和单位面积的裂纹长度[31,40]等指标来评估SCC萌生。一般用金相显微镜或扫描电子显微镜对试样标距段进行拍照,记录裂纹的数量、长度,统计汇总结果,计算出裂纹密度 (单位面积的裂纹数量或单位面积的裂纹长度)[31,40,44],而实际拍摄所用的倍数要根据实际的裂纹大小进行选择,裂纹较小时需用高倍扫描电镜拍摄[31,40],而裂纹较大时,用金相显微镜拍摄即可[44]。
3 影响SCC萌生的因素
3.1 材料
应力腐蚀是材料、腐蚀环境和力学等因素共同作用的结果,影响因素甚多。材料本身是发生SCC的场所,材料的加工状态、热处理状态都会导致其内部微观结构发生变化,进而会对SCC萌生产生显著的影响。
3.1.1 微观结构对SCC萌生的影响
核用材料部件在制造,安装运行过程中涉及多种不同形式的机械加工,对材料的内部结构和表面状态产生影响。
一般认为材料进行冷加工会促进其SCC的萌生过程。Zhai等[26]和Kuang等[39]在实验中研究表明加工会明显促进600MA (恒载实验) 和690MA合金 (CERT实验) 在高温高压水含氢环境中的SCC裂纹萌生。分析认为,可能是由于冷加工增加了随机大角晶界的数量,能量较高,促使Cr扩散,使裂纹萌生[39]。文献[46]在研究316L不锈钢表明冷加工后滑移线数量明显增加,也促进裂纹萌生。目前主要认为冷加工促使晶界类型转变、滑移线数量增加、应变诱导马氏体转变以及冷加工引入大量空位促使空洞形成都可能会促使SCC萌生[39,46-49]。
材料表面直接与水环境接触,是SCC优先发生的位置。表面车削以及研磨等机加工处理都会在其近表面引入损伤层,两个最重要影响因素就是损伤层的厚度和残余应力[37]。有研究[35,43]认为,在高温高压含氢环境中,316L不锈钢的车削加工表面和690合金的原始表面 (有约10 μm的细晶层) 要比抛光表面更容易萌生裂纹。而研究[26,34]表明,在高温高压含氢环境中,600MA合金 (60#砂纸打磨) 和304L不锈钢 (车削加工) 引入的细晶层表面要比抛光处理的表面试样不易萌生裂纹。加工表面不易萌生可能因为加工引入的细晶层中合金元素快速扩散,促进均匀氧化,避免沿晶界局部氧化的发生,而抛光表面基体晶界直接与水环境接触,会优先发生沿晶氧化促使SCC的发生。一般认为损伤层越厚,越会促进SCC萌生,但是不同材料表面损伤层对SCC萌生产生明显影响的临界厚度还不确定[37]。
表面残余应力对SCC也有很大影响,Zhang等[44]认为在155 ℃的饱和MgCl2溶液中,在不施加外载荷的情况下,当表面残余应力达到190 MPa时就会促进316不锈钢的SCC裂纹萌生。恒载试验表明,当600合金表面引入残余压应力时才会缓解SCC萌生,而引入拉应力则会促进SCC萌生[28,33],所以工程现场会采用对材料进行表面喷丸处理的方式以提高SCC抗性[37]。但是Chang等[34,35]在模拟一回路水环境中对304L不锈钢和316L不锈钢进行SSRT实验,并没有发现表面残余应力与SCC萌生之间的依赖关系,这可能是因为材料一旦发生塑性变形,材料的表面应力就会趋于相似的值[33]。由此可见SSRT试验可能会掩盖残余应力对裂纹萌生的影响。所以材料表面加工硬化层的厚度、残余应力状态和实验方法都有可能影响SCC萌生过程,需要综合考虑。
3.1.2 热处理的影响
对于600合金和690合金通常通过“特殊热处理”(TT) 来提高其SCC抗性[50]。TT处理通常是在700~800 ℃范围内等温处理几至十几小时,控制晶界碳化物的析出,消除或缓解晶界附近的贫Cr区,从而增强SCC抗性[51,52]。但也有研究[53,54]表明,如果690合金在TT处理后再次进行冷加工处理,则会在材料中引入大量空位,空位会在碳化物等高能形核位置聚集形成空洞,此时碳化物反而会促使SCC裂纹萌生。
除了材料在制备过程中必要的热处理,核用结构材料长期在高达340 ℃的高温高压水环境中服役,还会经历低温热老化过程,导致材料微观结构和性能发生变化[55,56]。Tsutsumi等[43]对690TT合金 (420 ℃/60000 h) 在模拟一回路水环境中进行SSRT实验,表明裂纹密度只是稍有增大,热老化对SCC裂纹萌生的影响不明显。Yoo等[57,58]对400 °C热老化0、1142和2284 h的600合金在高温高压水中进行实验,开缺口试样对应萌生时间分别为353.5、316.7和284.5 h,而光滑圆棒试样的萌生时间为560.9、427.9和518.6 h。上述不同形状试样表现出的不同趋势可能与热老化过程中晶界析出相、贫Cr程度以及试验时所受应力状态有关,但具体机理还有待研究。Li等[59]和Lai等[60]对热老化的铸造奥氏体不锈钢在模拟压水堆环境中进行SSRT实验,表明由于组织中的铁素体发生热老化脆化和元素偏析,裂纹会优先在铁素体内部形成。整体上关于热老化处理后的应力腐蚀尤其是SCC萌生测试还较少,有很大的研究前景。
3.2 水化学环境
相比于改善材料本身性能,水化学条件调节范围较宽,操作也相对比较简单,成本也较低,所以通过改善环境因素来降低甚至是抑制材料在服役环境中的SCC萌生过程是一种可行和有效的方法[22,61]。
3.2.1 溶解氢 (DH) 和溶解氧 (DO) 的影响
通常会向一回路溶液中通入一定量的H2来降低与之接触的各种材料的腐蚀电位,从而减缓材料的腐蚀[62,63]。图2a和b分别是DH对600合金裂纹扩展速率和萌生时间的影响总结结果,可以看出在高温高压纯水环境中,在与NiO/Ni相转变线对应的DH浓度附近,600合金具有最大的裂纹扩展速率和最短的裂纹萌生时间,并且进一步增加或降低DH浓度,裂纹扩展速率均随之逐渐减低,而裂纹萌生时间随之增加。裂纹扩展速率关于该DH浓度近似呈对称分布[6],而低浓度DH对萌生时间影响较大,高浓度影响较小,NiO/Ni相转变线两侧萌生时间的变化趋势差异较大[25,41,64]。Kazuya等[43]研究表明,690合金在模拟一回路水环境中SCC萌生时间与NiO/Ni相转变线对应的DH浓度并没有明显的对应关系,但是数据有限并没有得出确定结论。
图2 DH对600合金与82/182合金325 ℃下裂纹扩展速率和600合金在360 ℃下裂纹萌生时间的影响[6,25]
Zhong等[65]在模拟一回路水中对316SS进行SSRT实验,研究了不同DH水平 (5,15,30,50 cm3/kg) 对非敏化316SS SCC萌生的影响,认为随着DH升高,裂纹数量逐渐降低,裂纹不易萌生;但是在DH=15 cm3/kg时,316SS有最大的裂纹扩展速率。而Nakagawa等[66]在模拟沸水堆环境中对316L进行SSRT实验,表明高DH环境中SCC敏感性反而比低DH环境大。Choi等[67]对热轧316L进行裂纹扩展实验,发现氢浓度增加会使扩展速率加快。由上述可知,DH对SCC的影响机理比较复杂,萌生与扩展机理也不尽不同。
与一回路溶液中添加DH相比,DO的添加则会增加腐蚀电位,一般会促使SCC的发生,实际实验中也发现随DO浓度的增加,裂纹扩展速率加快[7,10]。但是Waeng等[42]在模拟一回路水环境中对600合金进行SSRT试验,表明高溶解氧浓度 (~7.8 mg/L) 要比除氧环境的SCC敏感性小,分析认为高氧环境会促使形成更具保护性的氧化膜。目前关于DO对SCC萌生过程影响的研究还很少,还主要集中在SCC的敏感性和裂纹扩展速率的相关研究中。
3.2.2 Cl-,PH,Zn2+等的影响
Cl-对钝化膜具有破坏作用导致钝化膜局部发生破裂,会促进SCC萌生的发生。Matocha等[68]在275 ℃的高压釜中对304不锈钢开展了恒应变的裂纹萌生实验。在DO条件下,表明随着Cl-浓度的升高试样表面出现裂纹并且萌生时间逐渐缩短,说明Cl-浓度的提高确实促进了SCC裂纹的萌生和扩展。在除氧条件下,在不同PH溶液中进行实验,表明酸性溶液中点蚀孔的尺寸和裂纹密度最大,说明酸性也会促使SCC萌生。
而在模拟一回路水环境中添加的Zn离子通常会置换合金表面已经形成的表面膜中的Ni和Fe离子,促使内层形成含Zn和Cr的保护性更好的氧化膜,从而抑制600合金表面SCC裂纹的形成[69,70]。
3.2.3 温度对裂纹萌生的影响
Etien等[41]在模拟一回路水环境中对退火态600合金进行恒载SCC萌生实验,表明在304~367 ℃温度范围内,裂纹萌生时间随着温度的增加逐渐降低,与温度遵循Arrhenius关系,其萌生激活能约为 (103±18) kJ/mol。Moss和Was[40]在亚临界水和超临界水环境中 (320~450 ℃,25 MPa) 对600MA合金以及预变形20%的690MA合金进行了CERT裂纹萌生实验。结果表明单位面积的裂纹长度和温度之间也满足Arrhenius关系,600MA合金裂纹萌生热激活能为 (121±13) kJ/mol,与恒载实验中结果较为相符。另外还发现亚临界水和超临界水中裂纹形貌也基本类似。因而根据激活能和裂纹形貌,可初步推断亚临界水和超临界水中600合金和690合金的裂纹萌生机理是相同的,所以采用高于实际服役环境的温度来进行SCC萌生加速实验也可能是一种有效的方法。
3.3 应力状态
3.3.1 施加应力的影响
Boursier等[24]在模拟一回路水中对600MA合金进行恒载实验,认为只有施加的应力水平等于或高于屈服应力时才会观察到SCC裂纹。所以恒载实验时所选应力一般略高于屈服应力。另外,裂纹萌生向裂纹稳定快速扩展的转变存在一个应力强度因子 (K) 的阈值[5],研究[37]表明600合金缓慢扩展到快速扩展的阈值约为9 MPa 。而后Zhai等[26]对冷加工600合金进行恒载实验时,发现裂纹萌生时对应的K约为10 MPa ,这与9 MPa 比较接近,进一步验证了裂纹萌生向裂纹快速扩展阶段转变时K存在一个阈值。Hong等[37]和Etien等[41]总结到,高温高压水环境中应力水平越高,则SCC萌生时间越短,萌生时间与应力之间的关系近似满足下式:
(2)
式中,SCCItime代表裂纹萌生时间,σ代表施加应力的大小。
3.3.2 应变速率的影响
在进行SSRT实验时,要选择合适的应变速率,过快来不及发生SCC而只发生机械断裂,过慢则实验时间会比较长。
Boursier等[24]对600MA合金分别进行SSRT与恒载荷测试,当SSRT达到既定的恒载荷条件时保持载荷不变,结果表明SSRT测试比恒载荷测试更能促进SCC的萌生。
Kuang等[31]和Zhong等[32]分别对316不锈钢和冷加工的690TT在模拟一回路水环境中进行SSRT实验,表明低应变速率下裂纹密度明显增加,SCC萌生更加容易。Santarini等[45]研究表明随着应变速率的提高,600合金在模拟一回路水环境中的表面平均裂纹长度和最大裂纹长度都增加。Boursier等[21]研究表明,随着应变速率的提高,600MA在模拟一回路水环境中的裂纹扩展速率也提高。Kuang等[31]总结得出,当机械载荷或应变固定时,裂纹萌生主要由腐蚀的时间来控制,而裂纹扩展主要由载荷或应变的大小来控制。
4 SCC萌生的机理
针对SCC扩展已经提出了很多理论,例如滑移-溶解模型[71,72],环境耦合断裂模型[73,74],内氧化模型[75]等。而关于裂纹萌生还没有比较成熟的统一的理论模型。
4.1 内氧化模型
Panter等[76]在模拟一回路水环境的静态釜中对600合金进行恒应变实验。在试样表面下方发现了贫Cr区和晶界氧化物。针对这些发现并结合以前的选择性氧化理论[77]提出了裂纹萌生的内氧化模型,机理如图3所示。可以看出,(1) Cr的选择性氧化,使表面以下贫Cr,并产生空位;(2) O与空位结合,沿晶界扩散;(3) 随扩散沿晶界发生氧化;(4) 随氧化进行,晶界强度弱化;(5) 在应力作用下,易发生沿晶SCC萌生。另外,图6左侧还指出晶界碳化物可以作为O陷阱,阻止O沿晶界向内扩散,这可能就是TT处理增强材料SCC抗性的原因之一。实际上若材料内部存在比较多的孪晶、位错和滑移带时,这些位置也会比较容易氧化,从而倾向于发生穿晶断裂[34]。
图3 内氧化机理示意图[76]
4.2 空洞形成模型
Arioka等[30,49,53,78,79]对冷加工的碳钢、不锈钢、镍基合金等材料在高温高压水中进行了恒载荷萌生实验。结合实验结果,提出了空洞形成模型。如图4a所示,首先 (Stage 1),冷加工引入大量的空位[80],空位在浓度梯度的驱动下从晶粒晶格向晶界扩散。之后 (Stage 2) 晶界处不带电的空位在应力梯度的作用下沿晶界向高应力区扩散。最后 (Stage 3) 空位在高能形核位置 (例如晶界碳化物) 聚集,合并成空洞。空洞的存在使晶界弱化,空洞成为裂纹萌生的前驱体,弱化晶界在应力和水化学条件的共同作用下很容易产生应力腐蚀,萌生裂纹。
图4 空洞形成示意图和690TT合金不同状态空洞形貌图[53,54]
另外,Zhai等[27,54]对冷加工690TT合金在高温高压水中进行萌生实验时,也观察到了空洞现象。如图4b~d所示,展示了不同实验时间的试样空洞情况,表明SCC裂纹是由空洞连接所形成,进一步证实了该模型的合理性。但是就目前来看,只有进行冷加工的材料,才能够观察到明显的空洞,所以该理论的应用范围有一定的局限性。
4.3 动态应变下的690合金的SCC萌生模型
Moss等[23,81]用SSRT实验研究了690合金SCC萌生。他们根据萌生裂纹的结构和成分分析,结合以前针对600合金的选择性氧化的SCC模型和690合金的高Cr含量特性,提出了动态应变条件下的690合金的SCC萌生模型。其机理如图5所示。起初,Cr沿晶界扩散,在晶界上方形成一层致密的Cr2O3氧化膜,而Cr沿晶界扩散会促使形成贫Cr区和造成晶界迁移 (图5a)。Cr2O3膜由于脆性较大,会在动态应变下发生破裂。导致氧会沿晶界扩散而形成晶界氧化物,随着氧化进行,贫Cr区逐渐扩大,晶界强度逐渐降低 (图5b)。当外加应力高于晶界强度时,就会萌生裂纹,而当贫Cr程度达到不能在裂尖形成保护性的氧化膜,则裂纹就会继续扩展 (图5c)。Volpe等[82]在600合金中也观察到了晶界优先氧化和晶界迁移现象。说明晶界氧化和晶界迁移确实会促使镍基合金SCC的萌生。
图5 动态应变下690合金在高温高压水环境SCC萌生机理示意图[81]
实际上述的动态应变下的690合金萌生模型与内氧化模型关系紧密,而实际实验中还有600合金氢气环境中的SCC萌生模型[83,84]、冷变形诱导晶界类型转变[39]、应变诱导马氏体转变[48]以及引入表面细晶层等[34]相关的SCC萌生机理解释。但是整体SCC萌生机理研究不深入,机理适用范围较小,想要与实际的SCC萌生时间等指标建立较好的定量关系还有很大的差距。
5 研究不足与趋势
综上所述,国内外对核用关键结构材料在高温高压水环境中的SCC裂纹萌生行为进行了一系列的研究,也取得了一定的进展。实验方法由定性化逐渐转化为结合DCPD等技术的原位检测。对于冷加工、表面状态、水化学、应力、应变速率等因素对常用核用结构材料的SCC萌生行为的影响进行了初步研究,提出了内氧化、空洞形成等SCC萌生模型。但是研究中仍然存在很多不足:(1) 裂纹萌生时间定义或者由裂纹萌生至稳定快速扩展的临界长度还存在争议,对于萌生时间的测量精确度还有待提高。(2) 如何合适的选择各种实验方法中的载荷、应变以及应变速率还需探索。(3) 裂纹萌生时间快速变化的临界冷加工程度以及临界表面损伤层厚度 (本质上是变形层内微观结构的变化) 还不能很好的确定。(4) DO和DH对核用材料裂纹萌生的影响趋势还不明确。(5) 不同材料的裂纹萌生激活能以及机理不变的温度区间还需进一步确定。(6) 现有的裂纹萌生机理使用范围具有局限性,研究还不够深入。
针对上述研究不足,未来要继续研究各种因素对核用结构材料的SCC萌生的影响,提供更多的基础研究数据探究相应的机理。在实际摸索中不断改进研究方法和选择合适的实验参数,使实验研究更加接近于实际服役状态。而随研究技术和方法的不断进步和成熟,研究也会越来越深入到微纳米尺度[85]。在更微观的层次上探究SCC萌生的转变过程,揭示萌生机理。随着研究的不断深入和数据的不断积累,最终使实验结果从定性化转向定量化,建立有效的萌生时间和裂纹萌生临界长度的评估方法。从而能够比较准确地对核电站的寿命进行评估,也可以从根本上为改善核电材料性能或制定更加规范化的核电运行准则提供理论基础,减缓材料失效和延长核电站的寿命。
参考文献
1 Berg H P. Corrosion mechanisms and their consequences for nuclear power plants with light water reactors [J]. Reliab. Risk Anal.: Theory Appl., 2009, 2: 57
2 Liu X, Zhao J C, Wang G G, et al. Failure analysis of pipelines and welding joints in nuclear power plant [J]. Failure Anal. Prev., 2013, 8: 300
2 刘肖, 赵建仓, 王淦刚 等. 核电厂管道及焊接接头失效案例综述 [J]. 失效分析与预防, 2013, 8: 300
3 Was G S, Ashida Y, Andresen P L. Irradiation-assisted stress corrosion cracking [J]. Corros. Rev., 2011, 29: 7
4 Sun H T, Ling L G, Lv Y H, et al. Stress corrosion problems and safety management of equipment and materials in domestic pressurized water reactor nuclear power plants [J]. Corros. Sci. Prot. Technol., 2016, 28: 283
4 孙海涛, 凌礼恭, 吕云鹤 等. 国内压水堆核电站设备材料应力腐蚀问题及安全管理 [J]. 腐蚀科学与防护技术, 2016, 28: 283
5 Hojná A. Environmentally assisted cracking initiation in high-tem-perature water [J]. Metals, 2021, 11: 199
doi: 10.3390/met11020199
6 Andresen P L, Hickling J, Ahluwalia A, et al. Effects of hydrogen on stress corrosion crack growth rate of nickel alloys in high-temperature water [J]. Corrosion, 2008, 64: 707
doi: 10.5006/1.3278508
7 Andresen P L. Stress corrosion cracking of current structural materials in commercial nuclear power plants [J]. Corrosion, 2013, 69: 1024
doi: 10.5006/0801
8 Amzallag C, Vaillant F. Stress corrosion crack propagation rates in reactor vessel head penetrations in alloy 600 [A]. BruemmerS, FordP, WasG. Ninth International Symposium on Environmental Degradation of Materials in Nuclear Power Systems—Water Reactors [M]. The Minerals, Metals and Materials Society, Newport Beach, 1999: 235
9 Zhu R L, Wang J Q, Zhang L T, et al. Stress corrosion cracking of 316L HAZ for 316L stainless steel/Inconel 52M dissimilar metal weld joint in simulated primary water [J]. Corros. Sci., 2016, 112: 373
doi: 10.1016/j.corsci.2016.07.031
10 Zhang L T, Wang J Q. Effect of dissolved oxygen content on stress corrosion cracking of a cold worked 316L stainless steel in simulated pressurized water reactor primary water environment [J]. J. Nucl. Mater., 2014, 446: 15
doi: 10.1016/j.jnucmat.2013.11.027
11 Chen K, Wang J M, Du D H, et al. dK/da effects on the SCC growth rates of nickel base alloys in high-temperature water [J]. J. Nucl. Mater., 2018, 503: 13
doi: 10.1016/j.jnucmat.2018.02.032
12 Du D H, Wang J M, Chen K, et al. Environmentally assisted cracking of forged 316LN stainless steel and its weld in high temperature water [J]. Corros. Sci., 2019, 147: 69
doi: 10.1016/j.corsci.2018.10.032
13 Chen K, Wang J M, Shen Z, et al. Effect of intergranular carbides on the cracking behavior of cold worked alloy 690 in subcritical and supercritical water [J]. Corros. Sci., 2020, 164: 108313
doi: 10.1016/j.corsci.2019.108313
14 Zhang L T, Wang J Q. Stress corrosion crack propagation behavior of domestic forged nuclear grade 316L stainless steel in high temperature and high pressure water [J]. Acta Metall. Sin., 2013, 49: 911
doi: 10.3724/SP.J.1037.2013.00171
14 张利涛, 王俭秋. 国产锻造态核级管材316L不锈钢在高温高压水中的应力腐蚀裂纹扩展行为 [J]. 金属学报, 2013, 49: 911
doi: 10.3724/SP.J.1037.2013.00171
15 Zhu R L, Wang J Q, Zhang Z M, et al. Stress corrosion cracking of fusion boundary for 316L/52M dissimilar metal weld joints in borated and lithiated high temperature water [J]. Corros. Sci., 2017, 120: 219
doi: 10.1016/j.corsci.2017.01.024
16 Guo S, Han E-H, Wang H T, et al. Life prediction for stress corrosion behavior of 316L stainless steel elbow of nuclear power plant [J]. Acta Metall. Sin., 2017, 53: 455
16 郭舒, 韩恩厚, 王海涛 等. 核电站316L不锈钢弯头应力腐蚀行为的寿命预测 [J]. 金属学报, 2017, 53: 455
17 Zhu R L, Zhang Z M, Wang J Q, et al. Review on SCC crack growth behavior of dissimilar metal welds for nuclear power reactors [J]. J. Chin. Soc. Corros. Prot., 2015, 35: 189
17 朱若林, 张志明, 王俭秋 等. 核电异种金属焊接接头的应力腐蚀裂纹扩展行为研究进展 [J]. 中国腐蚀与防护学报, 2015, 35: 189
18 Zhang K Q, Hu S L, Tang Z M, et al. Review on stress corrosion crack propagation behavior of cold worked nuclear structural materials in high temperature and high pressure water [J]. J. Chin. Soc. Corros. Prot., 2018, 38: 517
18 张克乾, 胡石林, 唐占梅 等. 冷加工核电结构材料在高温高压水中应力腐蚀裂纹扩展行为的研究进展 [J]. 中国腐蚀与防护学报, 2018, 38: 517
19 Zhang K Q, Tang Z M, Hu S L, et al. The research status of SCC crack propagation in structural materials of nuclear reactors [J]. Corros. Prot., 2019, 40: 157
19 张克乾, 唐占梅, 胡石林 等. 核电用结构材料SCC裂纹扩展的研究现状 [J]. 腐蚀与防护, 2019, 40: 157
20 Ma C, Peng Q J, Han E-H, et al. Review of stress corrosion cracking of structural materials in nuclear power plants [J]. J. Chin. Soc. Corros. Prot., 2014, 34: 37
20 马成, 彭群家, 韩恩厚 等. 核电结构材料应力腐蚀开裂的研究现状与进展 [J]. 中国腐蚀与防护学报, 2014, 34: 37
21 Jiao Y, Zhang S H, Tan Y. Research progress on stress corrosion cracking of stainless steel for nuclear power plant in high-temperature and high-pressure water [J]. J. Chin. Soc. Corros. Prot., 2021, 41: 417
21 焦洋, 张胜寒, 檀玉. 核电站用不锈钢在高温高压水中应力腐蚀开裂行为的研究进展 [J]. 中国腐蚀与防护学报, 2021, 41: 417
22 Dozaki K, Akutagawa D, Nagata N, et al. Effects of dissolved hydrogen content in PWR primary water on PWSCC initiation property [J]. E-J. Adv. Maint., 2010, 2: 65
23 Moss T, Kuang W J, Was G S. Stress corrosion crack initiation in Alloy 690 in high temperature water [J]. Curr. Opin. Solid State Mater. Sci., 2018, 22: 16
doi: 10.1016/j.cossms.2018.02.001
24 Boursier J M, Desjardins D, Vaillant F. The influence of the strain-rate on the stress corrosion cracking of alloy 600 in high temperature primary water [J]. Corros. Sci., 1995, 37: 493
doi: 10.1016/0010-938X(94)00158-3
25 Richey E, Morton D, Schurman M. SCC initiation testing of nickel-based alloys using in-situ monitored uniaxial tensile specimens [A]. AllenT R, KingP J, NelsonL. Proceedings of the 12th International Conference on Environmental Degradation of Materials in Nuclear Power Systems-Water Reactors [M]. The Minerals, Metals & Materials Society, 2005: 947
26 Zhai Z Q, Toloczko M B, Olszta M J, et al. Stress corrosion crack initiation of alloy 600 in PWR primary water [J]. Corros. Sci., 2017, 123: 76
doi: 10.1016/j.corsci.2017.04.013
27 Toloczko M, Zhai Z Q, Bruemmer S. SCC initiation behavior of alloy 182 in PWR primary water [A]. JacksonJH, ParaventiD, WrightM. Proceedings of the 18th International Conference on Environmental Degradation of Materials in Nuclear Power Systems-Water Reactors [M]. Cham: Springer, 2019: 137
28 Pemberton S R, Chatterton M A, Griffiths A S, et al. The effect of surface condition on primary water stress corrosion cracking initiation of alloy 600 [A]. JacksonJ H, ParaventiD, WrightM. Proceedings of the 18th International Conference on Environmental Degradation of Materials in Nuclear Power Systems-Water Reactors [M]. Cham, 2019: 203
29 Wu W B. Study of stress corrosion cracking initiation and propagation behavior of two typical nuclear key metal materials [D]. Hefei: University of Science and Technology of China, 2019
29 吴文博. 两种典型核电关键金属材料应力腐蚀裂纹萌生与扩展行为研究 [D]. 合肥: 中国科学技术大学, 2019
30 Arioka K, Staehle R W, Yamada T, et al. Degradation of alloy 690 after relatively short times [J]. Corrosion, 2016, 72: 1252
doi: 10.5006/2107
31 Kuang W J, Was G S. The effects of grain boundary carbide density and strain rate on the stress corrosion cracking behavior of cold rolled Alloy 690 [J]. Corros. Sci., 2015, 97: 107
doi: 10.1016/j.corsci.2015.04.020
32 Zhong X Y, Bali S C, Shoji T. Accelerated test for evaluation of intergranular stress corrosion cracking initiation characteristics of non-sensitized 316 austenitic stainless steel in simulated pressure water reactor environment [J]. Corros. Sci., 2017, 115: 106
doi: 10.1016/j.corsci.2016.11.019
33 Hong S L. Influence of surface condition on primary water stress corrosion cracking initiation of alloy 600 [J]. Corrosion, 2001, 57: 323
doi: 10.5006/1.3290356
34 Chang L T, Volpe L, Wang Y L, et al. Effect of machining on stress corrosion crack initiation in warm-forged type 304L stainless steel in high temperature water [J]. Acta Mater., 2019, 165: 203
doi: 10.1016/j.actamat.2018.11.046
35 Chang L T, Burke M G, Scenini F. Stress corrosion crack initiation in machined type 316L austenitic stainless steel in simulated pressurized water reactor primary water [J]. Corros. Sci., 2018, 138: 54
doi: 10.1016/j.corsci.2018.04.003
36 Wang S, Shoji T, Kawaguchi N. Initiation of environmentally assisted cracking in high-temperature water [J]. Corrosion, 2005, 61: 137
doi: 10.5006/1.3278168
37 Hong S L, Amzallag C, Gelpi A. Modelling of stress corrosion crack initiation on alloy 600 in primary water of PWRs [A]. BruemmerS, FordP, WasG. Proceedings of the Ninth International Symposium on Environmental Degradation of Materials in Nuclear Power Systems-Water Reactors [M]. The Minerals, Metals and Materials Society, Newport Beach, 1999: 115
38 Rebak R B, Smialowska Z S. Influence of stress intensity and loading mode on intergranular stress corrosion cracking of alloy 600 in primary waters of pressurized water reactors [J]. Corrosion, 1994, 50: 378
doi: 10.5006/1.3294347
39 Kuang W J, Was G S, Miller C, et al. The effect of cold rolling on grain boundary structure and stress corrosion cracking susceptibility of twins in alloy 690 in simulated PWR primary water environment [J]. Corros. Sci., 2018, 130: 126
doi: 10.1016/j.corsci.2017.11.002
40 Moss T, Was G S. Accelerated stress corrosion crack initiation of alloys 600 and 690 in hydrogenated supercritical water [J]. Metall. Mater. Trans., 2017, 48A: 1613
41 Etien R A, Richey E, Morton D S, et al. SCC initiation testing of alloy 600 in high temperature water [A]. BusbyJ T, IlevbareG, AndresenP L. Proceedings of the 15th International Conference on Environmental Degradation of Materials in Nuclear Power Systems-Water Reactors [M]. Cham: Springer, 2011: 2407
42 Maeng W Y, Choi M S, Kim U C. Effect of dissolved oxygen on PWSCC susceptibility of Alloy 600 in high temperature water [J]. J. Mater. Sci., 2004, 39: 655
doi: 10.1023/B:JMSC.0000011524.41986.4c
43 Tsutsumi K, Couvant T. Evaluation of the susceptibility to SCC initiation of alloy 690 in simulated PWR primary water [A]. BusbyJ T, IlevbareG, AndresenP L. Proceedings of the 15th International Conference on Environmental Degradation of Materials in Nuclear Power Systems-Water Reactors [M]. Cham: Springer, 2011: 41
44 Zhang W Q, Fang K W, Hu Y J, et al. Effect of machining-induced surface residual stress on initiation of stress corrosion cracking in 316 austenitic stainless steel [J]. Corros. Sci., 2016, 108: 173
doi: 10.1016/j.corsci.2016.03.008
45 Santarini G. Comprehensive interpretation of CERTs: a method for the characterization and the prediction of IGSCC [J]. Corrosion, 1989, 45: 369
doi: 10.5006/1.3582031
46 Isselin J, Kai A, Sakaguchi K, et al. Assessment of the effects of cold work on crack initiation in a light water environment using the small-punch test [J]. Metall. Mater. Trans., 2008, 39A: 1099
47 Zhang K Q, Tang Z M, Hu S L, et al. Effect of cold work and slow strain rate on 321SS stress corrosion cracking in abnormal conditions of simulated PWR primary environment [J]. Nucl. Mater. Energy, 2019, 20: 100697
48 Kuniya J, Masaoka I, Sasaki R. Effect of cold work on the stress corrosion cracking of nonsensitized AISI 304 stainless steel in high-temperature oxygenated water [J]. Corrosion, 1988, 44: 21
doi: 10.5006/1.3582020
49 Arioka K, Miyamoto T, Yamada T, et al. Role of cavity formation in crack initiation of cold-worked carbon steel in high-temperature water [J]. Corrosion, 2013, 69: 487
doi: 10.5006/0821
50 Zhang H B, Li S J, Hu Y H, et al. Research status of Inconel 690 alloy in steam generator heat transfer tubes abroad [J]. Spec. Steel Technol., 2003, 8(4): 2
50 张红斌, 李守军, 胡尧和 等. 国外关于蒸汽发生器传热管用Inconel 690合金研究现状 [J]. 特钢技术, 2003, 8(4): 2
51 Yang Y Z, Cai Z G, Wang Y D, et al. Effects of thermal treatment on microstructure and properties of 690 alloy heat transfer tubes [J]. Hot Work. Technol., 2017, 46(22): 209
51 杨义忠, 蔡志刚, 王永东 等. TT处理对690合金传热管显微组织和性能的影响 [J]. 热加工工艺, 2017, 46(22): 209
52 Zhang Y Y. Effects of deformation and hot treatment on microstructure and mechanical properties of 690 alloy [D]. Dalian: Dalian University of Technology, 2017
52 张雨樾. 变形和热处理对690合金微观组织与力学性能的影响 [D]. 大连: 大连理工大学, 2017
53 Arioka K. 2014 W. R. Whitney Award Lecture: change in bonding strength at grain boundaries before long-term SCC initiation [J]. Corrosion, 2015, 71: 403
doi: 10.5006/1573
54 Zhai Z Q, Toloczko M, Kruska K, et al. Grain boundary damage evolution and SCC initiation of cold-worked alloy 690 in simulated PWR primary water [A]. JacksonJH, ParaventiD, WrightM. Proceedings of the 18th International Conference on Environmental Degradation of Materials in Nuclear Power Systems-Water Reactors [M]. Cham: Springer, 2019: 457
55 Yu W W, Meng X M, Jiang J W, et al. Investigation on sensitive to thermal aging for key materials used in primary circuit of nuclear power plants [J]. Nucl. Power Eng. Technol., 2014, 27(3): 22
55 余伟炜, 蒙新明, 姜家旺 等. 核电站一回路关键设备材料热老化敏感性分析 [J]. 核电工程与技术, 2014, 27(3): 22
56 Lin X D, Peng Q J, Han E-H, et al. Review of thermal aging of nuclear grade stainless steels [J]. J. Chin. Soc. Corros. Prot., 2017, 37: 81
56 林晓冬, 彭群家, 韩恩厚 等. 核级不锈钢的热老化研究进展 [J]. 中国腐蚀与防护学报, 2017, 37: 81
57 Yoo S C, Choi K J, Kim T, et al. Microstructural evolution and stress-corrosion-cracking behavior of thermally aged Ni-Cr-Fe alloy [J]. Corros. Sci., 2016, 111: 39
doi: 10.1016/j.corsci.2016.04.051
58 Yoo S C, Choi K J, Kim T, et al. Effects of thermal aging and stress triaxiality on PWSCC initiation susceptibility of nickel-based Alloy 600 [J]. J. Mater. Sci. Technol., 2016, 30: 4403
59 Li S L, Wang Y L, Wang H, et al. Effects of long-term thermal aging on the stress corrosion cracking behavior of cast austenitic stainless steels in simulated PWR primary water [J]. J. Nucl. Mater., 2016, 469: 262
doi: 10.1016/j.jnucmat.2015.11.043
60 Lai C L, Lu W F, Huang J Y. Effect of δ-ferrite content on the stress corrosion cracking behavior of cast austenitic stainless steel in high-temperature water environment [J]. Corrosion, 2014, 70: 591
doi: 10.5006/1155
61 Kim H S, Hong J D, Lee J, et al. Effects of hydrogen on the PWSCC initiation behaviours of alloy 182 weld in PWR environments [J]. Corros. Sci. Technol., 2015, 14: 113
doi: 10.14773/cst.2015.14.3.113
62 Li Y C, Zhu Z P, Yang D W, et al. Hydrochemical Control Conditions in Nuclear Power Plants [M]. Beijing: Chemical Industry Press, 2008
62 李宇春, 朱志平, 杨道武 等. 核电站水化学控制工况 [M]. 北京: 化学工业出版社, 2008
63 Kim Y J, Andresen P L, Moran E, et al. Modification of surface property for controlling the type 304 stainless steel electrochemical corrosion potential in 288℃ water [J]. Corrosion, 2005, 61: 648
doi: 10.5006/1.3278200
64 Soustelle C, Foucault M, Framatome P C, et al. PWSCC of alloy 600: a parametric study of surface film effects [A]. BruemmerS, FordP, WasG. Proceedings of the Ninth International Symposium on Environmental Degradation of Materials in Nuclear Power Systems-Water Reactors [M]. The Minerals, Metals and Materials Society, Newport Beach, 1999: 105
65 Zhong X Y, Bali S C, Shoji T. Effects of dissolved hydrogen and surface condition on the intergranular stress corrosion cracking initiation and short crack growth behavior of non-sensitized 316 stainless steel in simulated PWR primary water [J]. Corros. Sci., 2017, 118: 143
doi: 10.1016/j.corsci.2017.02.003
66 Nakagawa K, Nono M, Kimura A. Effect of dissolved hydrogen on the SCC susceptibility of SUS316L stainless steel [J]. Mater. Sci. Forum, 2010, 654-656: 2887
doi: 10.4028/www.scientific.net/MSF.654-656.2887
67 Choi K J, Yoo S C, Kim T, et al. Effects of dissolved hydrogen on crack growth rate of warm-rolled 316L austenitic stainless steel in primary water condition [A]. Proceedings of the ASME 2015 Pressure Vessels and Piping Conference [C]. Boston, 2015: 1
68 Matocha K, Wozniak J. Stress corrosion cracking initiation in austenitic stainless steel in high temperature water [A]. BruemmerS, FordP, WasG. Proceedings of the Ninth International Symposium on Environmental Degradation of Materials in Nuclear Power Systems-Water Reactors [M]. The Minerals, Metals and Materials Society, Newport Beach, 1999: 383
69 Kawamura H, Hirano H, Shirai S, et al. Inhibitory effect of zinc addition to high-temperature hydrogenated water on mill-annealed and prefilmed alloy 600 [J]. Corrosion, 2000, 56: 623
doi: 10.5006/1.3280565
70 Febrianto, Sriyono, Widodo S, et al. The effect of zinc injection on the increasing of Inconel 600 TT corrosion resistances [J]. J. Phys.: Conf. Ser., 2018, 962: 012049
71 Ford F P. Quantitative prediction of environmentally assisted cracking [J]. Corrosion, 1996, 52: 375
doi: 10.5006/1.3292125
72 Andresen P L. Emerging issues and fundamental processes in environmental cracking in hot water [J]. Corrosion, 2008, 64: 439
doi: 10.5006/1.3278483
73 Macdonald D D, Lu P C, Urquidi-Macdonald M, et al. Theoretical estimation of crack growth rates in type 304 stainless steel in boiling-water reactor coolant environments [J]. Corrosion, 1996, 52: 768
doi: 10.5006/1.3292070
74 MacDonald D D, Urquidi-MacDonald M. A coupled environment model for stress corrosion cracking in sensitized type 304 stainless steel in LWR environments [J]. Corros. Sci., 1991, 32: 51
doi: 10.1016/0010-938X(91)90063-U
75 Peng Q J, Hou J, Takeda Y, et al. Effect of chemical composition on grain boundary microchemistry and stress corrosion cracking in Alloy 182 [J]. Corros. Sci., 2013, 67: 91
doi: 10.1016/j.corsci.2012.10.012
76 Panter J, Viguier B, Cloué J M, et al. Influence of oxide films on primary water stress corrosion cracking initiation of alloy 600 [J]. J. Nucl. Mater., 2006, 348: 213
doi: 10.1016/j.jnucmat.2005.10.002
77 Scott P M. An overview of internal oxidation as a possible explanation of intergranular stress corrosion cracking of alloy 600 in PWRS [A]. BruemmerS, FordP, WasG. Proceedings of the Ninth International Symposium on Environmental Degradation of Materials in Nuclear Power Systems-Water Reactors [M]. The Minerals, Metals and Materials Society, Newport Beach, 1999: 3
78 Arioka K, Miyamoto T, Yamad T, et al. Role of cavity formation on crack growth of cold-worked carbon steel, TT 690 and MA 600 in high temperature water [A]. BusbyJ T, IlevbareG, AndresenP L. Proceedings of the 15th International Conference on Environmental Degradation of Materials in Nuclear Power Systems-Water Reactors [M]. Cham: Springer, 2011: 55
79 Arioka K, Miyamoto T, Yamada T, et al. Formation of cavities prior to crack initiation and growth on cold-worked carbon steel in high-temperature water [J]. Corrosion, 2010, 66: 015008
80 Van Bueren H G. Theory of the formation of lattice defects during plastic strain [J]. Acta Metall., 1955, 3: 519
doi: 10.1016/0001-6160(55)90109-7
81 Kuang W J, Was G S. A high-resolution characterization of the initiation of stress corrosion crack in Alloy 690 in simulated pressurized water reactor primary water [J]. Corros. Sci., 2020, 163: 108243
doi: 10.1016/j.corsci.2019.108243
82 Volpe L, Burke M G, Scenini F. Correlation between grain boundary migration and stress corrosion cracking of alloy 600 in hydrogenated steam [J]. Acta Metall., 2020, 186: 454
83 Terachi T, Totsuka N, Yamada T, et al. Influence of dissolved hydrogen on structure of oxide film on alloy 600 formed in primary water of pressurized water reactors [J]. J. Nucl. Sci. Technol., 2003, 40: 509
doi: 10.1080/18811248.2003.9715385
84 Ferguson J B, Lopez H F. Oxidation products of INCONEL alloys 600 and 690 in pressurized water reactor environments and their role in intergranular stress corrosion cracking [J]. Metall. Mater. Trans., 2006, 37A: 2471
85 Han E-H. Research trends on micro and nano-scale materials degradation in nuclear power plant [J]. Acta Metall. Sin., 2011, 47: 769
85 韩恩厚. 核电站关键材料在微纳米尺度上的环境损伤行为研究—进展与趋势 [J]. 金属学报, 2011, 47: 769
免责声明:本网站所转载的文字、图片与视频资料版权归原创作者所有,如果涉及侵权,请第一时间联系本网删除。
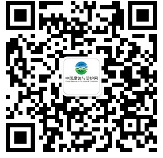
官方微信
《腐蚀与防护网电子期刊》征订启事
- 投稿联系:编辑部
- 电话:010-62316606-806
- 邮箱:fsfhzy666@163.com
- 腐蚀与防护网官方QQ群:140808414