1.情况介绍
该拉簧直径为8mm,材质为65Mn,硬度要求HRC45~50,拉簧表面镀铬处理;在服役时发生断裂,拉簧外观及断裂位置见图1,断裂发生在拉簧尾勾与工作圈过渡位置。现将分析结果介绍如下:
图1 拉簧外观及断裂位置
2.理化分析
2.1断口分析
拉簧的断口宏观形貌见图2,从断口形貌分析,拉簧断口呈金属疲劳断裂特征,断口底部为断裂起始段(疲劳源),向上可见因交变应力作用产生的海滩纹(疲劳扩展区)约占整个断面的1/5,海滩纹以上区域呈现快速断裂粗瓷状断口(快速断裂区)。
图2 断口宏观形貌
2.2金相检验
2.2.1非金属夹杂物检验
在拉簧断口附近取样进行金相分析,根据GB/T10561-2005评定其非金属夹杂物,级别为:A1.0、B0.5、C0.5、D0.5,见图3。
图3 100X 拉簧非金属夹杂物微观形貌
2.2.2微观组织检验
拉簧边缘组织见图4,无脱碳现象;拉簧金相组织见图5,金相组织为屈氏体+珠光体+部分未溶铁素体。
图4 100X 拉簧边缘组织形貌
图5 500X 拉簧金相组织
2.3硬度试验
在拉簧断裂位置附近取样,依据GB230.1-2009标准进行洛氏硬度试验,试验结果见表1。硬度值检测结果低于技术要求规定值下限。
表1 拉簧硬度检测结果 HRC
2.4化学成分分析
在拉簧断裂位置附近取样,进行化学成分分析,分析结果见表2,其化学成分符合GB/T1222-2007中65Mn的技术要求。
表2 拉簧的化学成分(质量分数) wt%
3.结论
(1)拉簧表面无氧化脱碳,非金属夹杂物洁净度良好;
(2)拉簧的化学成分符合GB/T1222-2007中65Mn的技术要求;
(3)拉簧的硬度值低于技术要求规定值下限;
(4)拉簧的金相组织为屈氏体+珠光体+部分未溶铁素体;
(5)拉簧的断裂形式为疲劳断裂。热处理工艺不当导致拉簧的硬度低于规定值下限值,拉簧刚度减小,导致拉簧的实际使用寿命低于设计寿命,拉簧发生早期疲劳断裂。
免责声明:本网站所转载的文字、图片与视频资料版权归原创作者所有,如果涉及侵权,请第一时间联系本网删除。
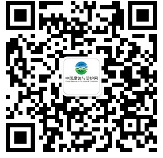
官方微信
《中国腐蚀与防护网电子期刊》征订启事
- 投稿联系:编辑部
- 电话:010-62316606-806
- 邮箱:fsfhzy666@163.com
- 中国腐蚀与防护网官方QQ群:140808414