球磨机是利用钢球作为研磨介质进行磨矿的设备,其结构简单、性能稳定、破碎比大,可对各种矿石和其他可磨性物料进行干式或湿式粉磨,适应性强,易于实现自动化控制。所以,在选矿、建材、化工、冶金、材料等行业中,球磨机都是最普遍、最通用的粉磨设备。随着企业生产规模的不断扩大和矿石品位的下降,球磨机的生产能力越来越大,并使球磨机越来越大型化。
齿轮轴是传动装置上的关键部件,随着球磨机向大型化发展,齿轮轴的加工工艺也有所改变,采用渗碳钢(渗碳淬火)代替中碳合金钢(调质+齿部位表面淬火)。
某公司齿轮轴材质选用20CrNi2Mo钢,规格为φ579mm×3000mm,模数25,齿数21,左旋7.5°,经锻造、粗车、探伤、调质(650℃回火)、精车、磨前铣齿、齿部渗碳淬火+回火(渗碳层深度2.5~3mm,齿面硬度57~61HRC)、磨齿等工序加工而成,锻造及热处理质量直接影响轴齿轮的使用寿命。
在用户现场使用过程中,齿轮轴断裂时未发现明显异常,只是在运行中电机仍在工作,但齿轮轴已不随着旋转。该齿轮轴使用寿命大概在12个月左右。齿轮轴的结构如图1所示,齿轮轴断裂宏观形态如图2所示。
造成齿轮轴断裂的原因很多,设计、工艺、加工精度、锻造、热处理、安装精度、维护保养等各个环节均可能造成该齿轮轴断裂,由于该断裂齿轮轴为备件,在更换该断轴前的另一根齿轮轴因到使用寿命而失效,说明设计、工艺、加工、安装、维护保养等环节不存在问题。为查找该齿轮轴断裂的主要原因,对其进行了化学成分分析、金相组织观察、断口观察和力学性能测试等。
一、理化检验及分析
断裂齿轴宏观形貌如图2所示,其中图2为现场照片。齿轮轴在轴齿部位断裂,在断口分离前,裂痕呈直线状沿周向分布(见图2a)。裂痕及附近区域无宏观塑性变形,显示脆性断裂特征。断裂齿轴为径向通透型断裂,如图2b所示。对球磨机断裂齿轮轴进行检测,具体检测项目有断口检测、金相组织检测、化学成分检测、力学性能检测。对断轴进行切割取样,取样情况如图3、图4所示。
1.断口检测
(1)断口宏观检测
对应面断口宏观形貌如图5~图7所示。断口平齐,断面可见明显放射状花样。放射状花样的收敛区在偏离圆心的圆形相对平坦区域及略带凹凸位置,该区域距齿顶约250mm,为断裂源区,如图5箭头所示。对应面一侧断口因钻取化学成分分析样品,断裂源区已被破坏(见图6箭头),另一侧除断口表面油污较严重外,断面基本无损伤。在断裂源区取样并清洗后(见图7),肉眼可见断裂源区沿枝晶开裂特征(枝晶间存在明显台阶)及15mm×10mm和10mm×2mm夹杂物缺陷。
(2)断口微观检测
用扫描电镜观察了断裂源区及附近断口微观形貌,如图8、图9所示,断口显示解理及准解理断裂特征。对断裂源区缺陷(见图9)进行了能谱定性及半定量检测,结果缺陷部位含有O、Ca、Si、C、Al、Fe、Mg、Na、K等元素,为夹渣缺陷。
2.金相组织检测
(1)低倍组织检测
在断口附近截取了齿轴径向(距断口轴向距离约20mm)及轴向样品,进行了低倍组织检测,结果如图10~图12所示,图11、图12试样上表面为断口。依据GB/T 1979—2001标准低倍组织评定为一般疏松0.5级,无其他低倍组织缺陷。存在较严重枝晶组织,断裂源区枝晶组织尤为严重,渗碳淬火层及调质处理层清晰可见,调质层距齿顶深度约为110mm。
(2)金相检测
图13为齿轮轴非金属夹杂物检测结果,参照GB/T 10561—2005标准评定为:A类粗系1级,B类粗系1级,C类0级,D类细系2级。图14为齿根部渗碳淬硬层组织,组织为回火马氏体,马氏体级别5级。图15为调质层,调质组织为回火索氏体+铁素体,存在枝晶组织。图16为调质层附近组织,组织为珠光体+铁素体,存在较严重枝晶组织。图17为断裂源区组织,组织为铁素体+珠光体,存在严重枝晶组织,晶粒度≥8级。
(3)化学成分检测
化学成分分析结果如表1所示,参照GB/T 3203—2016标准(渗碳轴承钢),对化学成分的检测值和标准值进行了对比,齿轮轴检测结果基本符合标准规定。
表1 化学成分(质量分数)检测结果 (%)
(4)力学性能检测
在轴心断裂源区附近沿径向截取了力学性能试样,检测结果见表2,参照标准中引用的 GB/T 3203—2016材料牌号(G20CrNi2Mo),强度测量值偏低,这与取样位置有关(标准值为纵向取样,且是经淬火+200℃回火后的值)。表3为渗碳淬硬层硬度梯度检测结果,渗碳淬硬层深度约为3.0mm。表4为距齿根表面调质层硬度梯度检测结果。
表2 力学性能检测结果与参考值对照表
表3 渗碳淬硬层硬度梯度检测结果
表4 距齿根表面调质层硬度梯度检测结果
3.检测结果分析与结论
(1)参照GB/T3203—2016(渗碳轴承钢)标准评定,齿轮轴化学成分基本符合标准相关规定。
(2)在齿轮轴心部断裂源区附近截取了径向试样(拉伸及冲击),检测结果显示,冲击值满足技术条件规定,说明材料具有较好的韧性。强度偏低有两方面原因:一是标准试样为直径25mm的检测值,而该齿轮轴直径为579mm。二是应与横向取样及取样时更靠近轴心部有关(JB/T5000.8—2007标准规定的取样位置为距表面1/3半径处);齿轮轴的齿部渗碳淬火层深度及硬度略低于标准要求。
(3)由齿轮轴表面至心部金相组织检测结果显示,基体组织无异常,齿轮轴枝晶组织较严重,特别是断裂源附近更为严重,说明在锻造过程中枝晶组织未得到有效的改善,在允许的情况下可适当增大锻造比。枝晶组织严重时会不同程度降低材料的力学性能。
(4)齿轮轴显示瞬时(一次性)脆性断裂特征,断裂源区在齿轮轴心部偏离轴心区域。该处存在肉眼可见夹渣物缺陷,且枝晶组织严重,说明该部位是齿轮轴的薄弱区域,易引发应力集中导致的开裂。
(5)齿轮轴是在设备运行过程中断裂,且使用时间约12个月。根据齿轮轴为突发一次性断裂的特点分析,其断裂时应存在两种情况:①断裂源区承受较大应力作用,该应力可排除齿轮轴制造过程中所能残留的组织应力、热应力等应力作用;也可排除使用过程所形成的热应力及齿轮轴旋转所形成的扭转应力作用。由于齿轮轴运行现场无法提供有效的监控记录及相关数据,因此无法更精准的判断轴心应力的来源。②断裂源区相对薄弱。
通过上述分析得出以下结论:齿轮轴心部存在夹渣及枝晶缺陷,在设备运行过程中,当轴心承受较大应力作用时,在薄弱部位引发了瞬时脆性断裂。
4.热加工工艺改进
引起齿轮轴断裂的原因很多,仅从热加工专业着手,通过提高锻件质量、增加锻后正火工序、增加渗碳前预备热处理(粗铣齿后调质)工序、调整渗碳淬火工艺参数等手段,提高热加工工艺效果,保证产品质量。
免责声明:本网站所转载的文字、图片与视频资料版权归原创作者所有,如果涉及侵权,请第一时间联系本网删除。
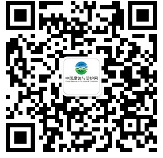
官方微信
《中国腐蚀与防护网电子期刊》征订启事
- 投稿联系:编辑部
- 电话:010-62316606-806
- 邮箱:fsfhzy666@163.com
- 中国腐蚀与防护网官方QQ群:140808414