导读:沉淀相可以有效阻碍位错滑动,显著提高金属材料的强度。特别是峰时效条件下的致密纳米级析出物可获得有利的析出物尺寸,以实现显著强化,然而,这通常会导致延性降低的合金出现局部化渐进应力和过早失效。本文展示了具有中高层错能(SFE)的高熵合金(HEA)系统中的“峰时效态的异常延性效应”。与欠时效HEA相比,具有相对较大析出物的峰值时效HEA在强度和拉伸塑性方面均表现出显著的增加,这与传统观点不同。通过激活微带触发独特的多阶段应变硬化机制,实现了塑性对析出物尺寸的异常依赖性,这些发现为先进结构应用的超强韧性金属材料的创新设计提供了新的见解。
长期以来,对于制造和承重应用中的结构材料而言,获得坚固而有韧性的金属材料一直是一个巨大的挑战。基本上,这两种相互排斥的力学性质与位错活动密切相关。一方面,提高强度需要尽可能多的障碍物来阻止位错的运动。另一方面,合金的拉伸延展性本质上取决于位错活动在空间分布、增殖和传播方面的控制程度。
在材料中引入分散的纳米沉淀是最有效的强化方法之一。该策略已被广泛应用于实现各种金属材料(如马氏体时效钢和镍基高温合金等)的吉帕斯卡强度。通常,通过峰时效可实现最大强度,指时效材料在特定温度下达到其最大硬度值,然而,这总是以拉伸延展性为代价。沉淀硬化材料的这种强度-韧性权衡可能源于沉淀和基体之间的变形不相容性。在机械应变过程中,在相界附近通常会出现明显的位错堆积,这会导致较大的局部应力集中,加速微裂纹和过早塑性失稳的发生。值得注意的是,沉淀硬化合金的室温延展性通常由局部应力集中程度决定,局部应力集中程度随沉淀的增长而明显增加。因此,可以预期,析出物越小,延展性越好。在以前的许多研究中,可以通过实验发现这种沉淀尺寸相关的延展性。例如,Peng等人报告,峰值时效(800 °C下24 h)L12强化Ni28Co28Fe21Cr15Al4Ti4HEA的最大屈服强度为855 MPa,但与未时效样品(800 °C下4h)相比,其塑性损失约为13%,析出物相对较少。
有趣的是,在峰时效强化L12HEA中,存在反常的沉淀尺寸依赖延展性。(FeCoNi)85.9Al8Ti6B0.1(at.%)HEA,具有中高层错能(SFE,53 mJ/m2)。值得注意的是,当在740 °C下时效时,精心制作的合金达到1433±35 MPa的更高强度,与通过较小沉淀强化的欠时效合金相比,塑性甚至提高了约43±1%。峰时效纳米沉淀物对多组分HEA系统延展性的这种有趣影响挑战了传统智慧,促使我们解读这种异常现象的微观结构起源。因此,在这项工作中,试图建立加工硬化能力(延展性)和纳米沉淀微观结构特征的内在联系,包括沉淀体积分数和尺寸。
哈尔滨工业大学赵怡潞、香港城市大学刘锦川院士和杨涛等人提出并证明,中等至高SFE和相对较大纳米沉淀的高体积分数的微妙组合将通过触发明显的交叉滑移事件促进微带的形成,从而导致可持续的应变硬化,从而同时增加强度和延展性。这些发现可以为先进结构材料的未来设计提供一个范例,将强度-延性协同作用推进到一个无法进入的领域。相关研究成果以题“Anomalousprecipitate-size-dependent ductility in multicomponent high-entropy alloys with densenanoscale precipitates”发表在金属顶刊Acta Materialia上。
链接:https://doi.org/10.1016/j.actamat.2021.117480
与UA合金相比,PA合金中较高的位错存储率导致过早结晶HDDW的形成,从而导致更高水平的背应力硬化和应变硬化率(图2中的第一阶段)。后来,为了进一步适应塑性应变,多滑移系统中的微滑移成为主要的塑性变形模式。这是通过对析出物硬化HEA的析出物尺寸、体积分数和SFE的精细调节实现的。具体而言,加载时的动态活性微带可同时作为强化的位错障碍,也是应力分散的起源,导致平衡力学性能的可持续应变硬化。
摘要图
图1 (FeCoNi)85.9Al8Ti6B0.1HEA的显微硬度随时效时间的在740 °C下时效的变化。
图2 (FeCoNi)85.9Al8Ti6B0.1HEA的力学性能和应变硬化行为具有不同时效过程的。(A) UA和PA HEA的工程应力-应变曲线。PA合金的强度和延展性同时增加,插入的低倍断裂表面未显示宏观颈缩。(B)应变硬化率曲线显示了PA合金独特的多阶段加工硬化行为。
图3 显示UA和PA合金韧性韧窝的高放大断口。
图4 UA和PA合金的初始微观结构。(A)和(B)UA和PA合金的反极图(IPF)图,分别显示所有合金完全再结晶,没有优先织构。(C)和(D)两种合金晶界附近的近景。在PA合金(D)中观察到少量晶界L21颗粒,如插图所示的选区衍射图证实了这一点。
图5 UA和PA合金的微观结构和化学分布。(A)(B)暗场TEM图像显示,在FCC基体中均匀分布着具有不同沉淀尺寸的L12纳米沉淀的高密度。(C)和(D)UA和PA合金的统计沉淀直径直方图。(E) APT针的3D重建,其中只有Ti原子显示为蓝色,沉淀的轮廓用8 at.%突出显示钛等值面。(F)通过相界的典型化学剖面定量显示了PA合金中单个元素的分配行为。
对于小颗粒,在剪切过程中,前导位错和尾随位错可能位于分离的颗粒中,这被称为弱对耦合情况。相比之下,当粒子变大时,成对位错将在单个粒子内移动,从而导致塑性变形期间的强对耦合行为。
图6 UA和PA合金拉伸变形时位错亚结构的演化。
(A)(B)UA和PA合金在约5%真实应变下的变形微观结构.(C)和(D)在约18%的真实应变下。(E) PA合金变形过程中激活的多个微带约32%塑性真实应变。(F)示意图显示了在相同应变水平下变形的UA和PA合金中位错累积的情况
图7 PA合金在约18%真实应变下形成微带结构。(A)变形PA合金的IPF图。(B)样本的均为局部取向差(KAM)映射。(C)位错子结构沿(B)中白色箭头的错向轮廓。
图8 在约18%的真实塑性应变下,PA合金中微带边界附近的变形诱导相变。
(A)(C)高分辨率TEM图像和每个相的相关活衍射点,显示了微带边界附近高应力集中导致的BCC相的存在。(B)(D)变形PA合金中FCC型和BCC相之间观察到的两种取向关系示意图。
图9 UA和PA合金的应力分配行为。
(A) UA和PA合金的加载-卸载-再加载(LUR)试验。(B) LUR试验中磁滞回线的放大图。(C)有效应力和背应力随真实应变的变化而变化。(D)有效应力和背应力之间的差异,表明PA合金中的变形行为更协调。
微带的动态形成将增强微带壁和相邻微带内部之间的塑性变形兼容性,进而有助于抑制塑性不稳定性(即早期局部颈缩)使PA合金具有更大的拉伸延展性。
图10 PA合金中应变硬化行为和相关微观结构演变的示意图。结果表明,沉淀硬化HEA中微带的动态细化是独特的多阶段应变硬化行为的关键,这是通过巧妙地调节沉淀尺寸、体积分数以及材料的SFE实现的。(图中蓝色条带为平面滑动痕迹,绿色条带为微条带)
基于上述讨论,可以得出结论,在变形机制从弱对耦合转变为强对耦合的范围内,大量纳米沉淀物的粒径在该范围内,中高SFE在激活多重微裂纹和相关的高强度延性方面起着关键作用。
在这项工作中,发现在具有中高SFE的峰值高熵合金中存在异常的沉淀尺寸相关塑性。研究结果表明,析出相的尺寸、体积分数以及SFE对微裂纹的激活和有趣的多阶段应变硬化行为都至关重要,这是克服强度-塑性冲突和塑性失稳的关键。具体而言,相对较大的纳米沉淀的高体积分数有助于位错在初级滑移系统中累积,这与中高SFE效应同时发生,使明显的交叉滑移,促进变形过程中微带的形成。由此产生的微带及其随后的细化导致动态应力分散和应变硬化,从而同时提高强度和延展性。这项工作为设计具有巨大应用潜力的高性能纳米沉淀强化材料提供了一种新颖可行的方法。
免责声明:本网站所转载的文字、图片与视频资料版权归原创作者所有,如果涉及侵权,请第一时间联系本网删除。
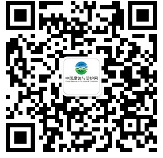
官方微信
《中国腐蚀与防护网电子期刊》征订启事
- 投稿联系:编辑部
- 电话:010-62316606-806
- 邮箱:fsfhzy666@163.com
- 中国腐蚀与防护网官方QQ群:140808414