高强度铝合金由于密度小、强度高、韧性和耐蚀性良好、可加工性及焊接性优良等综合性能,在航空航天、机械和汽车制造业等领域得到了广泛应用。多数高强度铝合金材料需要通过热处理获得高强度与高韧性以满足使用需求,而在热处理强化过程中,快速的淬火冷却使得材料内部形成巨大温差,冷却结束后在构件内部形成较大的残余应力,在加工、储存及长时间使用过程中会发生残余应力的释放与松弛,从而带来零件的精度超差或尺寸不稳定等问题。目前降低与消除残余应力的方法主要有:时效处理、振动时效、深冷处理、机械拉伸(压缩)法等。
深冷处理过程也被称上坡淬火或反淬火,按工艺可划分为深冷急热法与冷热循环法,可广泛用于铝合金构件残余应力的减小与控制。本文对国内外铝合金深冷处理的研究与应用进行总结分析,讨论了不同类型铝合金工件深冷处理的工艺选择和适用场合。
1.残余应力的产生
工件在没有外力的作用下内部存有的保持工件自身平衡的应力被称为残余应力。一般来讲,铝合金在淬火过程中不发生组织转变,所以其构件残余应力主要来自于淬火冷却过程的热应力,应力的演变过程如图1所示。
热应力是由于材料不同部位存在温度差别而导致热胀和(或)冷缩的不一致所引起的应力。对于2D内外两层简化模型,在淬火冷却开始前(见图1a),在长时间高温条件下,材料内部温度均匀,不存在热应力;在淬火冷却初期(见图1b),铝合金工件进入淬火冷却介质后,由于金属表面与淬火冷却介质温差很大,散热很快,使得表层温度下降很快,而内部依靠热传导方式散热,温度下降较慢,在表层与心部形成巨大温度差。在热胀冷缩的作用下,工件因温度下降而体积收缩,表面温度下降较多因而体积收缩较多,心部温度下降较少因而体积收缩较少。因内外收缩量不同,相互发生作用力,此时表面因受到心部抵制收缩力而长大,所以此时外部受拉应力,心部受压应力。在应力的作用下,心部金属由于温度较高、屈服强度较低,发生塑性变形,从而释放一部分应力。
淬火冷却第二阶段(见图1c),由于金属表层温度已经较低,与淬火冷却介质热交换较少,所以此时表层温度下降速度放慢。而里层金属与表层温差较大,里层金属温度下降速度较表层快,使得表层收缩得少,心部收缩得多,内外层相互涨缩的牵制力减小,使得内应力减少,出现表层温度低于心部,但内应力为零的情况。
随着工件继续冷却(见图1d),当金属内部的温度也降至较低温度时,构件整体的抗变形能力提升,心部金属温度下降且产生相比表层金属更大的收缩,而该收缩受到表层金属的牵制,且整体无法产生塑性变形,内应力不会消减,此应力留在工件内部,最终造成工件表层受压应力,心部受拉应力的残余应力状态。
图1 2D简化模型淬火过程应力演变示意
2.残余应力对构件的影响
残余应力的存在严重影响工件的加工精度与尺寸稳定性。
以2D简化模型为例,淬火冷却完成后,沿着中心线的残余应力分布如图2a所示,在中心区域为拉应力,外部为压应力。当沿着中间线进行加工时,表层金属被切除,这时原始的应力平衡受到破坏,在残余应力的作用下加工面发生微小凹陷,同时部分应力被释放,剩余的残余应力重新分配并创造了新的平衡(见图2b),加工面的凹陷宏观表现为尺寸精度的降低。
(a)残余应力分布示意 (b)残余应力重新分配示意
图2 残余应力对加工精度的影响
同时残余应力的变化是导致构件尺寸不稳定的重要原因。尺寸稳定性表示材料在热处理与加工完毕后,在工作环境条件下,不受外力作用或在低于其弹性极限的应力作用下抵抗永久变形的能力。构件在储存及长时间使用过程中会发生残余应力松弛,使构件的尺寸形状发生微小变化,从而导致尺寸不稳定,而构件形变量的大小取决于残余应力值的大小。
3.铝合金深冷处理技术的提出与发展
使用深冷处理进行铝合金残余应力的控制与消除可追溯到20世纪30年代,在早期使用中,通常将工件埋在干冰中,之后快速浸入100℃开水,由于当时缺乏系统、基础的研究未能广泛应用。直到20世纪50年代末,美国铝业公司对铝合金深冷处理技术开展了深入研究,应用了液氮与蒸汽分别作为冷却与升温介质并进行了公开报道,深冷处理技术开始广泛应用于航空航天,国防和高精度成像系统中关键部件的残余应力消除。同时,深冷处理技术经常用于具有关键公差的铝合金部件的生产过程,比如光学试验台等在高精度环境中工作的组件。在Bodycote热处理威斯敏斯特加州工厂,采用液氮和沸水对多种锻铝进行残余应力的消除,该过程作为商业与军用、航空等产品的一个特殊的工艺过程。2013年发布了铝合金产品的深冷处理标准AMS2767《uphill quenching of aluminum alloyproduct》。
国内有关铝合金深冷处理的研究工作开始于20 世纪90 年代末期,开展了很多工艺性研究,已经取得了比较重要的研究成果,并在铝合金工件残余应力消除与尺寸稳定化控制方面开展了应用,同时对铝合金深冷处理的微观机理也进行了一定的研究。
4.铝合金深冷处理技术研究进展
从温度变化与宏观应力的变化趋势来看,由于深冷处理过程中构件的状态是从低温快速升至高温,与淬火过程相反,也被称为反淬火,能够产生与淬火相反的热应力,所以理论上能够创建一个新的应力状态或分布,从而实现残余应力的控制与消除。低温与高温之间温度差越大,升温速度越快,得到的反淬火应力越大,残余应力消除的效果越明显。因此,为了得到更大的温差,目前深冷处理均采用液氮作为冷却介质,而在升温介质、温度与使用环节方面存在一定差异。
在深冷处理环节方面主要分为以下两种类型(见图3):I在淬火后立刻进行深冷处理(见图3a),处理次数1次或多次,之后进行时效强化;II在时效强化后进行深冷处理(见图3b),处理次数1次或多次。
(a)淬火后深冷处理 (b)时效后深冷处理
图3 深冷处理使用环节示意
国内外不同研究中所采用的升温介质或设备差异较大,所得到的残余应力消除效果也存在较大差异,如附表所示。其中采用高压热气流进行快速整体升温时残余应力的消除率可达86%,但该方法需要设计制造专用供气装置与气流喷射工装(见图4),且对于存在封闭内腔等结构产品并不适用。比较容易实现且投入较少的方式为采用开水和空气炉进行加热,残余应力的消除率分别可达29%、40.7%;而采用高温有机介质,相关研究表明其残余应力的消除率可达58%,在实际使用过程中,为保证工件表面清洁,需增加清洗工序。
(a)
(b)
图4 采用高压热气流与液氮进行深冷处理的设备与工装
不同深冷处理方式对不同材料残余应力消除文献数据统计
对于深冷处理消除淬火残余应力的效果,相关研究指出:针对本身残余应力较低的工件,如采用热水或有机淬火液进行淬火的产品,深冷处理的效果会不太明显。另外,也有研究结果表明,在时效强化后进行深冷处理(使用环节II),虽然残余应力消除率不高,但对于尺寸稳定性依然有明显的积极作用,可以在加工过程中进行,用来保证产品尺寸精度。
5.深冷处理工艺的缺点与不足
(1)价格相对昂贵与传统的机械变形消除应力的方法相比,深冷处理过程价格相对昂贵,冷却过程需要消耗大量的液氮,同时升温过程需要专用设备、工装与介质。
(2)产品对象受限 与其他消除残余应力的方法一样,深冷处理的应用同样受限于产品对象的尺寸结构等因素。比如为达到最佳应力消除效果,需设计制造专用高压热气流装置,但对于一些结构复杂、尺寸较大的产品很难实现。
(3)应力消除效果受限前文提到为达到消除残余应力的最佳效果,应在工件固溶后尽快进行深冷处理。而实际生产过程中,为了保证工件的尺寸精度,往往需要在固溶后进行人工或机械矫正、尺寸测量等工序,对于深冷处理的效果存在一定影响。
6.结语
国内外铝合金深冷处理技术研究结果表明:
(1)深冷处理能够有效减少铝合金构件内部的残余应力,提高尺寸稳定性。
(2)在铝合金构件完成固溶处理后尽快进行液氮深冷处理,之后快速转移至高温热气流设备中进行上坡淬火,在此条件下残余应力消除率最高,采用热水或循环空气电炉进行加热效果次之。
(3)多次冷热循环处理的效果普遍优于单次上坡淬火处理,一般推荐的次数为2~3次。
免责声明:本网站所转载的文字、图片与视频资料版权归原创作者所有,如果涉及侵权,请第一时间联系本网删除。
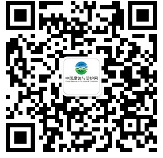
官方微信
《中国腐蚀与防护网电子期刊》征订启事
- 投稿联系:编辑部
- 电话:010-62316606-806
- 邮箱:fsfhzy666@163.com
- 中国腐蚀与防护网官方QQ群:140808414