科技决定未来,科技创造未来,新一轮防腐蚀技术革命正在兴起,为石油行业的发展保驾护航。
“西气东输”管道的安全措施
西起新疆的轮南,经甘肃、宁夏进入陕西,在陕西的靖边与长庆气田连接,再穿越黄河经山西、河南、安徽、江苏、浙江,东抵上海,把塔里木盆地储量丰富的天然气源源不断地输送到我国经济最发达的东单沿海地区,直径过一米的输气管道约 4000 公里,管道建设投资 435 亿元,覆盖东部 8500万户居民生活用气。
那么粗大的钢管,经过那么多不同的侵蚀性土壤,4000公里输气,能安全吗?万一出现管道腐蚀、点蚀或应力腐蚀开裂,引发了天然气泄漏,爆发熊熊大火,还得了吗?那么,怎样才能做到万无一失,保证 50 年的安全输送呢?
作为五大运输手段之一的管道运输,我国的管道建设专家,在全国各地尤其是大城市星落棋布的管网建设中街垒了一整套的科学技术能力,他们为“西气东输”管道所设计的技术方案:“阴极保护 + 涂层”的双重保护措施,即全线设置 19 个阴极保护电源供应和检测站。在专家评审会上,一致认为采用这种技术方案,可保“西气东输”工程万无一失。
碳纤维抽油杆解决 抽油机井举升问题
胜利油田东辛采油厂与新大公司联合研发的碳纤维连续杆及配套技术,收到节能、深抽、延缓钢制抽油杆腐蚀疲劳的效果。
由于油藏特性和开发时间的延长, 抽油杆腐蚀疲劳断裂、深抽投资增加和能耗高成为抽油机井普遍存在的三大举升问题。 就拿深层抽油来说, 东辛厂有122口油井泵深超过2200米,其中相当一部分井动液面测不出,如果继续加深泵挂,不仅增加能耗,而且必须更换大一型号的抽油机。再加上传统的钢制抽油杆自重大,深抽后会增加杆断风险,直接影响单井效益。
碳纤维是一种纤维状的碳材料,不仅具有优异的耐腐蚀性,而且强度高、重量轻。经过反复试验,他们从抽油机井的深抽提液入手,分析如何减少抽油机的悬点载荷,联合研发了碳纤维连续杆,提高单井产量,减少杆断倒井现象。
他们还优化碳纤维连续杆的配套方式,减少腐蚀杆断现象。在普通井中采用“上部碳纤维连续杆、下部钢制抽油杆”模式;对腐蚀重的井,下部的钢制抽油杆采用防腐抽油杆,收到全井抽油杆的防腐效果。
超声波在线测厚油气管线安全运行
安庆石化炼油一部定期联系公司特种设备检验站人员,利用超声波在线测厚先进技术,定点检测 20 条油气管线,并根据测厚数据技术分析,及时更换、整改腐蚀减薄严重的问题油气管线。
生物防腐技术 助力效益开发
为缓减油井腐蚀,江苏油田石油工程技术研究院油田化学研究室自 2011 年起开展油井生物防腐技术研究,利用油井内有益菌的生长竞争优势抑制有害菌的繁殖。截至目前,他们共开展试验 53 井次,试验油井累计减少作业 45 井次,减少作业费 872 万元。科研人员在马五站污水膜处理间开展污水生物防腐评价试验,利用生物防腐技术解决管网腐蚀严重的问题。
首创高硫超稠油安全密闭集输
西北塔河油田超稠油储量达 7.5 亿吨,稠油产量占原油产量的 45%。由于超稠油油品性质极差,腐蚀介质含量极高,加之油田地理环境特殊,对超稠油集输处理与防腐技术提出严峻挑战。
西北油田工程院首创了高硫超稠油智能化安全密闭集输和火车安全运输工艺、负压气提脱硫与稳定一体化工艺、超稠油集输设备和管道腐蚀防治技术,形成了超稠油地面集输处理与腐蚀防治关键技术系列,发挥了地面生产设施最大潜能,建立了“两超两高”油藏开发地面配套示范区。该项目累计获得授权专利 13 项,年可处理稠油 320 万吨。
稠油处理及防腐技术解决腐蚀难题
西北油田“超稠油集输处理与腐蚀防治关键技术研究及工业化应用”通过专家组鉴定。该项目针对塔河油田高硫化氢、高矿化度超稠油集输与腐蚀防治技术难题,研发形成超稠油集中掺稀降黏、安全密闭集输、负压气提法脱硫、稠油高效破乳及脱水集成工艺,建立管线点蚀评价及锌铝共渗处理等稠油集输系统腐蚀防护技术体系。项目成果已应用于 783口单井、23 座接转站、4 座联合站及 1426 千米管线,年处理稠油 320 万吨,集输系统腐蚀穿孔数两年降低 30%。
高桥石化加氢空冷器关键技术国内领先
由高桥石化与 SEI( 中国石化工程建设有限公司 )、浙江理工大学共同负责的总部科研项目“基于流动腐蚀预测的加氢空冷器关键技术研究”——加氢空冷器关键技术国内领先。
加氢装置的反应馏出物空冷器系统处于高压、临氢、多相变、高流速工况中,存在流动腐蚀问题,尤其受当前劣质原料油加工的影响,REAC 系统极易出现严重腐蚀,引起穿孔泄漏、爆管事故,由此导致的非计划停工已成为制约炼油工业良性发展的重大瓶颈。
“基于流动腐蚀预测的加氢空冷器关键技术研究”项目于 2012 年在集团公司科技部立项,构建了加氢装置 REAC 系统失效预测控制体系;研制开发了基于流动腐蚀预测及风险防控于一体的 REAC 智能系统与专用碳钢管束;通过实效控制参数建模、自主编程,研发基于流动腐蚀动态预测监管的加氢 REAC 实时专家诊断监管系统。
项目成果在高桥石化的加氢裂化装置进行了工业应用,结果表明,该技术为碳钢高压空冷器提供了有效的动态监测和腐蚀防控,可在拥有高压碳钢空冷器的中国石化其他单位推广应用。
钛合金油管首次在超深高含硫气井应用
随着元坝 205-2 井完井封隔器顺利坐封,标志着由西南油气分公司联合天津钢铁集团共同研制的钛合金油管在元坝205-2 井顺利完成首次入井。
该井完井投产管柱采取钛合金油管,取代常用的镍基合金油管。该油管在超深高含硫气井首次入井使用,并进行了氦气螺纹泄漏检测,未发现泄漏。钛合金油管具有重量轻、抗腐蚀和耐磨性能优异的优点。 科研人员历经3年的技术攻关,反复试制,抗腐蚀性能、机械性能、整管性能和螺纹密封性能等均能满足元坝气井使用要求。
小处入手降成本
“有了这个‘澡堂’,我们只要把滤芯放进去,半个小时就清洗干净。不仅每年可节省 10 万元的费用,而且还可以在清洗滤芯时回收原油。 ” 西北油田油气运销部结合生产实际,从小处入手降本增效,收到较好效果。
雅克拉末站有输油泵 11 台,其进口段的过滤器专门过滤原油杂质。长时间使用,滤芯表面会黏附油垢等杂质,如果不及时清洗,会严重堵塞过滤器,影响正常生产。对此,该站组织技术人员通过技术攻关,为过滤器设计了“澡堂”,将滤芯放入密闭的装置中,接入高压水蒸气冲洗滤芯的油污杂质。油水混合物通过管道进入回收单元,沉降后油水分离,污油得到回收。
风向带是观测风向的装置,更是天然气场站的必备装置。其材料为棉布,使用时间长了会老化、破裂,经常需要更换。为了减少更换风向标的安全风险,输气队组织安全人员讨论研究,借鉴国旗的升降办法安装了滑轮,使原来换风向带由 4人改为 1 人,时间从两小时缩短至 10 分钟。自从加装静态混合器以后,塔库首站外输原油品质得到改善,加注比例也从1.51‰下降至 0.9‰,每月可节约成本十几万元。
新技术可提高管道安全性
管道运输石油有较高风险,尤其是在水下的管道。不过,一家公司采用了一种新技术,称其能使运输过程更安全。挪威科技工业研究院正致力于完成对 SmartPipe 系统的测试,即使用传感器和无线系统可将管道状态数据传送给监控方。SmartPipe 项目负责人欧雷·奥斯汀·克努森 2003 年起一直致力于攻克管道安全难题。
克努森认为,通过更频繁的监测可减少泄漏事故的发生。 目前,管道公司通常使用一些传感器来监测管道的健康状况,同时采用“清管”手段进行清理,即将一种工具插入管道内测量管壁的厚度和发现薄弱点。该方法费用较高,且每隔几年做一次。也就是说,如果一次检查后管道便开始腐蚀,至少要几年后才会被发现。
克努森称,有了 SmartPipe 系统,运营商在了解管道实际情况的基础上更容易控制,因为掌握实时信息可防止泄漏,任何腐蚀过程都可在早期被发现及纠正。
SmartPipe 系统是为海底管道而造,不过克努森表示,该系统也可用于陆地管道。相比于海底管道,陆地管道的外部腐蚀问题带来的风险更多。因而,应用于陆地管道的 SmartPipe系统需加装一个测量外部腐蚀的传感器。
免责声明:本网站所转载的文字、图片与视频资料版权归原创作者所有,如果涉及侵权,请第一时间联系本网删除。
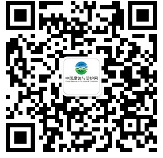
官方微信
《中国腐蚀与防护网电子期刊》征订启事
- 投稿联系:编辑部
- 电话:010-62316606-806
- 邮箱:fsfhzy666@163.com
- 中国腐蚀与防护网官方QQ群:140808414