有色金属
压力容器常用有色金属有:铜及其合金、铝及其合金、铅及铅合金、镍和镍合金、钛和钛合金、锆及锆合金等。
01 铜及其合金
① 纯铜
在无氧条件下,铜在许多非氧化性酸中都是比较耐腐蚀的。耐稀H2SO4、H2SO3、稀的和中等浓度的HCl、HAc、HF及其它非氧化性酸等介质的腐蚀,对淡水、大气、碱类溶液的耐蚀能力很好。不耐各种浓度的HNO3、NH3和铵盐溶液。但铜最有价值的性能是在低温下保持较高的塑性及冲击韧性,是制造深冷设备的良好材料。
② 黄铜
铜与锌的合金称黄铜,最简单的黄铜是铜-锌二元合金,称为简单黄铜或普通黄铜。黄铜中Zn含量对力学性能影响较大,Zn的含量增加,其强度升高,塑性降低。工业应用的黄铜含Zn小于45%(mass),含锌量再高合金变脆。
黄铜的耐蚀性能与纯铜相似,在大气中耐腐蚀性优于纯铜,常用的黄铜牌号有H80、H68、H62等。H80在大气、淡水及海水中有较高耐腐蚀性。
为了改善黄铜的某种性能,在二元黄铜的基础上加入其它合金元素的黄铜称为特殊黄铜。常用的合金元素有Si、Al、Sn、Pb、Mn、Fe和Ni等。
锡黄铜HSn70-l又称海军黄铜,含有1%(mass)的Sn,能提高在海水中的耐蚀性。
③ 白铜
铜与镍的合金,呈银白色,镍含量低于50%(mass)的铜镍合金称为简单(普通)白铜,加入Mn、Fe、Zn或Al等元素的白铜称为复杂(特殊)白铜。纯铜加Ni能显著提高强度、耐蚀性、电阻和热电性。工业用白铜根据性能特点和用途不同分为结构用白铜和电工用白铜两种,分别满足各种耐蚀和特殊的电、热性能。白铜多经压力加工成白铜材,是铜合金中抗冲刷腐蚀、应力腐蚀性最好的,多用于循环水、海水换热器管束和管板覆盖层。
④ 青铜
青铜是历史上应用最早的一种合金,原指铜锡合金,因颜色呈青灰色,故称青铜。为了改善合金的工艺性能和力学性能,大部分青铜内还加入其它合金元素,如Pb、Zn、P等。无锡青铜主要有铝青铜、铍青铜、锰青铜、硅青铜等。此外还有成份较为复杂的三元或四元青铜,现在除黄铜和白铜(铜镍合金)以外的铜合金均称为青铜。
锡青铜有较高的力学性能、耐蚀性、减摩性和铸造性能,对过热和气体的敏感性小,焊接性能好,无铁磁性,收缩系数小。锡青铜在大气、海水、淡水和蒸汽中的抗蚀性都比黄铜高。锡青铜用来铸造耐腐蚀和耐磨零件,如泵壳、阀门、轴承、蜗轮、齿轮、旋塞等。典型牌号 ZQSn10-1,有高强度和硬度,能承受冲击载荷,耐磨性很好,具有优良的铸造性,比纯铜耐腐蚀。
02 铝及其合金
铝是一种轻金属,密度小,铝的标准电极电位为-1.67V,化学活性很高,应该易于遭受腐蚀,但在许多介质中由于它的表面易于生成一层致密的、自愈性好、有保护性的氧化物膜,因此有很好的耐蚀性,在大气中优于黄铜及碳钢。
铝合金具有较好的强度,比强度远高于钢。具有良好的抗腐蚀性能和较好的塑性,适合于各种压力加工,因此得到广泛的运用。由于熔焊的铝材在低温(-196℃)下冲击韧性不下降,适合做低温设备。
铝合金按加工方法可分为变形铝合金和铸造铝合金。变形铝合金又分为不可热处理强化型铝合金和可热处理强化型铝合金。不可热处理强化型不能通过热处理来提高力学性能,只能通过冷加工变形来实现强化,它主要包括高纯铝、工业高纯铝、工业纯铝以及防锈铝等。可热处理强化型铝合金可以通过淬火和时效等热处理工艺提高力学性能,它可分为硬铝、锻铝、超硬铝和特殊铝合金等。
有些铝及铝合金可以采用热处理获得良好的力学性能,物理性能和抗腐蚀性能。设备或构件应避免与其他金属直接接触,并不能在含有重金属离子的介质中使用,一般的铝合金也不抗氯化物腐蚀,抗垢下腐蚀性能差。Hg对铝镁合金有严重的腐蚀作用。因为Al是两性金属,故一般只能在近中性(pH 4.5-8.5)的介质中使用,但在氨水中因为络离子的产生而耐蚀。在氧化性酸中极易钝化,所以可耐各种浓度的HNO3,在弱有机酸(如HAc)、弱无机酸(如H2CO3)、尿素等介质中耐蚀性优良。
压力加工产品曾分为防锈(LF)、硬质(LY)、锻造(LD)、超硬(LC)、包覆(LB)、特殊(LT)及钎焊(LQ)等7类。常用铝合金材料的状态为退火(M)、硬化(Y)、热轧(R)3种。高强度铝合金指其抗拉强度大于480MPa的铝合金,主要是压力加工铝合金中硬铝合金类、超硬铝合金类和铸造合金类。牌号有硬铝:Al-Cu-Mg的合金,如LY1L-1L-2;防锈铝:Al-Mg的合金,LF21;铸铝:Al-Si的合金,ZL107。
耐蚀铝合金主要有Al-Mg、Al-Mn、Al-Mn-Mg和Al-Mg-Si 4个系列。铝中加入Mg、Zn、Mn、Ai、Cu等元素后,铝合金的电极电位也随之变化。对每一种元素,当它完全溶于固溶体中时,元素含量的变化对铝的电极电位影响明显,进一步添加形成第二相的同种元素,仅使电极电位稍有变化。铝合金的耐蚀性与合金中相的电极电位关系很大,当基体为阴极,第二相为阳极时,合金具有较高的耐蚀性;如基体为阳极,第二相为阴极,则第二相的电极电位越高,数量越多,合金的耐蚀性越差。Si与Al的电位虽然相差较大,但在复相合金中耐蚀性仍然很好,这是因为在氧化性介质中合金表面有保护性氧化膜(Al2O3 + SiO2)生成。
① 铝及铝合金的主要腐蚀类型
a.点蚀
点蚀是铝合金最常见的腐蚀形态,在近中性的大气、水等介质中都会发生。
引起铝合金点蚀需要3个条件:
一是水中含有能导致钝化膜破坏的离子,如Cl-;
二是含有能抑制全面腐蚀的离子,如SO42-;
三是含有能促进阴极反应的氧化剂,因为铝合金在中性环境中的点蚀是阴极控制的过程;
b.晶间腐蚀
Al-Zn-Mg 和Mg质量分数大于3%的Al-Mg合金,常因热处理不当引起晶间腐蚀。Al-Cu和Al-Cu-Mg合金热处理时在晶界上连续析出富Cu的CuAl2相时,则临近CuAl2相的晶界固溶体中贫Cu,晶界贫Cu区成为阳极而发生腐蚀;
c.应力腐蚀
对于纯铝和低强度铝合金,一般不产生应力腐蚀。铝合金常在海洋环境、不含Cl-的高温水中产生应力腐蚀开裂,其破裂的特征是晶间型开裂,说明铝合金的应力腐蚀与晶间腐蚀有关。当晶界为阳极时,因选择性腐蚀导致晶界优先溶解。铝合金中含有足够量的可溶性合金元素(主要为Cu、Mg、Si和Zn)时,对应力腐蚀敏感性显著提高。容易产生应力腐蚀的主要是高强度铝合金,如Al-Cu、Al-Cu-Mg、Mg质量分数大于5%的Al-Mg合金、Al-Zn-Mg-Cu等合金;
d.电偶腐蚀
铝及铝合金自然腐蚀电位低,当与其他金属接触时,在腐蚀环境中成为阳极而被腐蚀。当其与电位更正的金属接触时,本身会发生孔蚀。因此,铝及铝合金在使用上须避免与其他金属接触,如无法避免时,应在设计上应尽可能增加铝合金的暴露面积,减少铝合金的腐蚀电流密度;
e.剥落腐蚀(剥蚀、鳞状腐蚀)
剥落腐蚀是变形铝合金的一种特殊腐蚀形态,与合金的显微组织有关,表现为铝合金从表层一层一层地剥离下来。腐蚀过程是有选择地沿着与表面平行的次表面开始,未腐蚀金属薄层在腐蚀层之间剥裂分层。剥蚀通常仅发生在有明显的定向伸长组织的产品中,最多的是Al-Cu-Mg系合金,在Al-Mg系、Al-Mg-Si系和Al-Zn-Mg系中也有发生,但在Al-Si系中尚未发现。在挤压材表层之下发生,而挤压材已经再结晶的表层不发生。
提高铝合金耐蚀性的主要措施是增厚表面氧化膜,方法有化学氧化法和电化学阳极氧化法。
② 铝及铝合金牌号
按GB/T 16474变形铝及铝合金牌号表示方法,铝及铝合金分为9个系列,GB/T 3190[3]变形铝及铝合金化学成分给出了新旧牌号对照表和化学成分。
a.工业纯铝
按GB/T 1196[4]重熔用铝锭(MOD ISO 115-2003), 重熔用铝锭按化学成分分为8个牌号,分别是Al99.90、Al99.85、Al99.70、Al99.60、Al99.50、Al99.00、Al99.7E和Al99.6E(注:Al之后的数字为铝含量);
工业高纯铝的代号为LG×(铝、工业用,Al含量大于99.85%)和L×(Al含量99.7-98.3%)。
工业高纯铝用于抗氧化性酸腐蚀和大气腐蚀,用于制作反应器、热交换器、深冷设备、塔器等;
b.防锈铝
由铝锰系或铝镁组成的铝合金,强度比纯铝高,用于中等强度的零件、管道、换热管、低压容器等;
c.铸造铝合金
铸造铝合金(ZL)按化学成分可分为铝硅合金,铝铜合金,铝镁合金和铝锌合金,代号编码分别为100、200、300、400。铝的铸造性、流动性好,铸造时收缩率和裂纹敏感性性小,广泛用来铸造形状复杂的耐蚀零件,如管件、泵、阀门、汽缸、活塞等。
Al-Si系,俗称“硅铝明”,典型牌号ZAlSi7Mg,合金号为ZL101;
Al-Cu系,应用最早,热强性高,300℃,耐腐蚀性较差。典型牌号ZAlCu5Mn,合金号为ZL201;
Al-Mg系,室温力学性能高,耐腐蚀性能好,但热强性低。铸造性能差,典型牌号ZAlMg10,合金号为ZL301;
Al-Zn系,Zn在Al中溶解度大,再加入硅及少量镁、铬等元素,具有良好的综合性能,典型牌号ZAlZn11Si17,合金号为ZL401。
03 铅及其合金
铅合金是以铅为基加入其他元素组成的合金。按照性能和用途,铅合金可分为耐蚀合金、电池合金、焊料合金、印刷合金、轴承合金和模具合金等。铅合金硬度低、强度小,不宜单独作为设备材料,只适于做设备的衬里。在硫酸(80%的热硫酸及92%的冷硫酸)中铅具有很高的耐蚀性。
铅合金表面在腐蚀过程中产生氧化物、硫化物或其他复盐化合物覆膜,有阻止氧化、硫化、溶解或挥发等作用,所以在空气、硫酸、淡水和海水中都有很好的耐蚀性。铅合金如含有不固溶于铅或形成第二相的Bi、Mg、Zn等杂质,则耐蚀性会降低,加入Te、Se可消除杂质Bi对耐蚀性的有害影响。在含Bi的铅合金中加入Sb和Te,可细化晶粒组织,增加强度,抑制Bi的有害作用,改善耐蚀性。
铅与锑合金称为硬铅,硬度、强度都比纯铅高,铅锑合金加入少量的Cu、As、Ag、Ca、Te等,可增加强度,在硫酸中的稳定性也比纯铅好。从综合性能考虑,铅合金用于制作化工设备、管道等耐蚀构件时,以含Sb 6%(mass)左右为宜;用于制作连接构件时,以含Sb 8%~10%为宜。
硬铅的主要牌号为 PbSb4、 PbSb6、 PbSb8和 PbSb10。
铅和硬铅在与硫酸接触的介质中可用来做设备衬里、加料管等。
04 镍和镍合金
纯镍或低合金镍对各种还原性化学物质有一定抗力,特别是耐苛性碱腐蚀性能优异。与镍基合金相比,纯镍有更高的导电和导热性能。退火镍具有低的硬度以及良好的延展性和韧性。镍的加工硬化相对较低,但它可以通过冷作达到中等强度水平并保持其延展性。这些特性加上其良好的焊接性能使得该金属容易加工成型。
按 GB/T 25951.1镍及镍合金 术语和定义 第1部分:材料,镍合金为除Ni + Co外,至少一种合金元素质量分数大于0.3%,合金元素总质量分数超过1%。按 GB/T 5235加工镍及镍合金 化学成分和产品形状,纯镍分为N2~N9和DN 9个牌号。
镍和镍合金对稀非氧化性无机酸,如HCl、H2SO4、H3PO4,在低温至中温环境中有良好的耐腐蚀性。因为镍的析氢过电位高, 对一般的非氧化性酸来说, 析氢反应困难, 需要供给氧气才能使腐蚀较快发生。因此, 镍在含氧化性组分如Fe3+、Cu2+、HON3、O2和其他氧化剂等物质的酸性介质中, 能被快速腐蚀。镍对氯化物晶间型应力腐蚀有较好的抵抗力,但在强应力情况下,在有氧溶液中对碱性开裂很敏感。镍对大部分天然淡水和快速流动海水都有较高的抗腐蚀能力。但在滞流状态或有裂缝的情况下,可能会发生严重腐蚀。镍不会被无水氨水或很稀的氨水腐蚀,但高浓度氨水中因为有可溶性的络合物(Ni-NH4 )产生,会导致快速腐蚀,
Nickle 200、Nickle 201和 INCOLOY alloy 25-6Mo是被ASME 锅炉和压力容器代码Section VIII, Division 1 批准的结构材料。Nickle 200批准的使用温度可以达到600℉ (315℃),Nickle 201批准的服役温度可达到1250℉ (677℃)。
① Nickle 200
Nickle 200(UNS N02200/W.Nr. 2.4060 和2.4066)是商业纯镍(99.6%),特别适用于食品、人造纤维以及苛性碱等需要保证产品纯净的设备。在含气量不是很高的情况下,Nickle 200 对抗有机酸的腐蚀非常优异。Nickle 200 通常被限制在低于315℃下使用,高温下Nickle 200 产品会发生石墨化,这会使材料的力学性能严重下降。
Nickle 200 虽然大多数使用是在还原环境中,但它也在可以形成钝化膜的氧化条件下使用,Nickle 200 对苛性碱的优异抗腐蚀能力就是基于这一种保护。
通常Nickle 200 在室内气氛中保持光亮状态,在海洋和乡村环境中的腐蚀速率均非常低。在室外,由于形成了很薄的保护膜(通常是硫酸盐),其腐蚀速率也很低。腐蚀速率随气氛中SO2含量(如在工业大气中)的增加而增加。
Nickle 200 对蒸馏水和天然水的耐蚀能力非常优异。在蒸馏水中腐蚀速率小于0.01mpy (0.3μm·a-1),在民用热水温度200℉(95℃)下通常小于0.02mpy (0.5μm·a-1)。
Nickle 200 能有效的耐含H2S或CO2的水溶液腐蚀,被用于油井中抵抗硫化氢和盐水腐蚀。Nickle 200在淡水和盐水中的腐蚀疲劳极限非常接近。在流动的海水(即使流速非常高)非常耐蚀,但在停滞或流速非常低的海水中在有机物的污垢或其它沉积下可能出现非常严重的局部腐蚀。
在水蒸气含有一定比例的CO2和空气的系统中,腐蚀速度开始时非常高,但在环境有利于形成保护膜时,随时间推移腐蚀速度会降低。但铁的腐蚀产物等杂质会干扰这种保护膜的形成。为防止腐蚀,在这类系统中应该带有供水消气泡装置或除去不凝气的设备。
在室温的非充气溶液H2SO4环境中,Nickle 200 有一定的耐蚀性,充气和提高温度均能增加腐蚀速率,氧化性盐的存在也会加速腐蚀。
在HCl中,Nickle 200 可以在充气或不充气的室温浓度不超过30%的盐酸中使用,在质量分数低于0.5%的情况下,材料可以满足温度直到300-400℉ (150-205℃)的使用。同样提高温度和充气将加速腐蚀。
在HF中,Nickle 200 对无水HF即使在较高温度下也有优异的耐蚀性。但在水溶液中,其应用通常限制在温度低于180℉ (80℃)以下。即使在室温下,质量分数为60-65%的商用等级酸也可以对Nickle 200造成严重的腐蚀。
在H3PO4中,Nickle 200在环境温度下的各种浓度的纯的不通气H3PO4中的腐蚀速率均比较低。但由于商用磷酸通常含有能加速腐蚀的氟化物和Fe3+杂质,不能达到合理的服役寿命,Nickle 200 的使用有限。
在HNO3中,Nickle 200 仅在室温质量分数不高于0.5%的HNO3中使用。
Nickle 200的突出的耐蚀性能是它耐苛性钠和其它碱类(Nickle 200不会被质量分数小于1%的氨水腐蚀,更高的浓度会引起快速侵蚀)的腐蚀。在苛性钠中Nickle 200对所有浓度和温度包括熔融状态都有出色的耐蚀性。质量分数低于50%时,即使在沸腾状态,腐蚀速率也可以忽略。随浓度和温度升高,腐蚀速率升高非常缓慢,其突出的耐蚀性能的主要贡献来自于溶液中暴露时形成的黑色氧化镍膜。但由于腐蚀性氯酸盐的存在能明显提高腐蚀速率;硫化物也有增加苛性钠对Nickle 200腐蚀性的倾向,可以增加足量的过氧化钠来使硫化物氧化成硫酸盐来抵消这种腐蚀。在氧化性的碱性氯化物中长期使用Nickle 200 的最大的安全极限为氯含量为500mg·L-1。对断续使用并在中间有漂洗清洁操作的情况含量可达到3g·L-1,在漂白工艺中,用0.5mL·L-1硅酸钠(密度1.4)作为腐蚀缓蚀剂是有效的。
该金属在所有非氧化性卤化物盐中均不会遭受应力腐蚀开裂。
氧化性的酸性氯化物如Fe3+、Cu2+和Hg对Nickle 200 有强烈的腐蚀作用,对硫磺、Pb、Sn、Zn和Bi等低熔点金属的晶间侵蚀非常敏感。
虽然氟和氯强氧化剂会与金属反应,但在特定条件下Nickle 200 可以成功的在这种条件下应用,也抵抗Br2蒸气的腐蚀。在室温下Nickle 200 形成保护性氟化物膜可以满足处理在低温下处理氟。在较高温度下,201比200 更好。
Nickle 200在实际使用时在加热前应该特别小心除去所有的润滑剂、标记、车间灰尘等。由于存在危险的晶间氧化,应避免在高温氧化性气氛中加热。
② Nickle 201
Nickle 201(UNS N02201/W. Nr.2.4061 和2.4068)是Nickle 200 的低碳版本。典型应用为碱蒸发器、电镀棒和电子部件。由于Nickle 201的硬度较低,而且加工硬化速率也较低,因此特别适合做旋压和冷成型。相较Nickle 200 而言,Nickle 201 更适合在温度高于600℉(315℃)的场合使用。
Nickle 201具有Nickle 200的优异的抗腐蚀性能。由于它是一种低碳材料(C质量分数最高0.02%),Nickle 201在长期处于600℉-1400℉(315℃-760℃)、而且没有与含碳材料接触的情况下不会出现由于晶间碳或石墨的析出而发生的脆化。
在温度高于600℉(315℃)的情况下,该材料会发生硫化物引起的晶间脆化。Nickle 201 被大量用来处理苛性钠,仅在苛性钠质量分数高于75%并接近沸点的情况下腐蚀速率才开始超过1mpy(0.025mm·a-1)。
在某些存在硫酸盐的高温碱的应用领域,由于合金INCONEL 600 更高的抗硫脆能力而取代Nickle 201。
05 钛及钛合金
钛金属已成为化工装备中主要的耐蚀材料之一,经过多年的推广,钛及其合金已作为一种优异的耐腐蚀结构材料在化工生产中得到了广泛应用,特别是用钛代替不锈钢、镍基合金和其它稀有金属作为耐腐蚀材料,在延长设备使用寿命、降低能耗、降低成本、防止产品或环境污染、提高装置的运行周期等方面都有十分重要的意义。许多氯碱厂使用的钛制湿氯气冷却器使用寿命超过20年,目前钛设备的应用已从最初的“纯碱与烧碱工业”扩展到氯酸盐、氯化铵、有机合成、染料、无机盐、农药、合成纤维、化肥、采油和天然气、石油炼化和精细化工、煤化工等行业,设备种类已从小型、单一化发展到大型、多样化。目前,国产化工钛设备中,钛换热器占57%,钛阳极占20%,钛容器占16%,其它占7%。
按GB/T 3620.1标准,根据纯度的不同,工业纯钛共分9个牌号,TA1类型的有3个,TA2-TA4每个类型的各有2个。从TA1-TA4每个牌号都有一个后缀带ELI的牌号,ELI为英文低间隙元素的缩写,即高纯度的意思。钛合金中Fe元素是作为杂质存在的,而不是作为合金元素特意加入的。由于Fe、C、N、H、O在α-Ti中是以间隙元素存在,它们的含量对工业纯钛的耐腐蚀性能以及力学性能产生很大影响,C、N、O固溶于钛中可以使钛的晶格产生很大的畸变,使钛被强烈的强化和脆化。带ELI的牌号这5个元素含量的最高值均低于不带ELI的牌号。这个标准主要是参照ISO外科植入物和ASTM B265、B338、B348、B381、B861、B862和B863这7个标准[19-25],并与ISO和ASTM标准相对应,例如TA1、TA2、TA3 和TA4分别对应Gr1、Gr2、Gr3和Gr4。随着牌号的数字增加,这5个杂质元素的含量也在增加,也就意味着强度增加,塑性逐步下降。
工业纯钛主要应用于化工行业的反应釜、压力容器、换热元件等,应用最广泛的是TA1,其次是TA2。
钛合金的分类法有多种,按钛合金在室温下3种基体组织分为以下3类:α合金、(α+β)合金和β合金,我国分别以TA、TC、TB表示。比较常见的还有以退火后的金相组织形态进行分类:
① 退火后基本组织是α相的,称为α型钛合金。不能进行热处理强化,室温强度不高。TA7是比较典型的α合金组织;
② 退火后基本组织是α+β,但是以α相为主的,称为近α型合金。TA15完全退火后的组织,α含量能占到接近70%左右;
③ 退火后基本相α+β,两个相相近,称为α+β型合金。TC4完全退火后的典型两相组织为α+β各相都接近50%的形态;
④ 退火后基本上是β相,但还有一定的α相的,称为近β型合金。TB3的金相组织,α相的含量较少;
⑤ 退火后基本全是β相的,称为β型合金。未热处理即具有较高的强度,淬火、时效后合金得到进一步强化,室温强度可达1372~1666 MPa,但热稳定性较差,不宜在高温下使用。如Ti-40(Ti-25V-15Cr)阻燃钛合金。
TA合金(α-型钛合金),含有Al、Sn和(或) Pb的钛合金为α-Ti合金。其中纯钛的牌号有TA1、TA2、TA3,1、2、3为工业纯钛的编号顺序,编号越大则添加元素含量越多,其强度也就相应提高。工业纯钛主要应用于化工、造船等工业部门在350℃以下使用。
TA4(Ti3Al)、TA5(Ti4Al0.005B)、TA6(Ti5Al) 和TA7(Ti5Al2.5Sn),这类钛合金组织稳定、耐热性高、焊接性优良,适宜于在高温和低温下使用,是压力容器常用的钛合金材料。其缺点是可锻性差,不能通过热处理强化。
TB合金(β-型钛合金)。TB1(Ti3Al8Mo11Cr)、Ti13V11Cr3Al、Ti8Mo8V2Fe3Al、Ti3Al8V6Cr 4Mo4Zr以及Ti11.5Mo6Zr4.5Sn等,这类钛合金强度较高、冲压性能较好、抗脆断性能好、易于焊接,还可以通过热处理进一步强化。其缺点是热稳定较差,不宜于高温下工作。主要用于宇航工业。
TC合金(α+β型钛合金),牌号TC1-TC10,这类钛合金塑性好,容易锻造和冲压成形,可时效强化,退火后有良好的低温性能、热稳定性能及焊接性能。主要用于制造火箭发动机外壳、舰艇耐压壳体等。
钛的化学活性大,标准电极电位-1.63V,在介质中的热力学腐蚀倾向大,可与大气中O2、N2、H2、CO、CO2、H2O(气)、NH3等产生强烈的化学反应。但因钛的致钝电位亦低,故钛极易钝化。常温下钛表面极易形成由氧化物和氮化物组成的钝化膜,它在大气及许多腐蚀性介质中非常稳定,具有很好的抗蚀性。含C量大于0.2%(mass)时,会在钛合金中形成硬质TiC;温度较高时,与N作用也会形成TiN硬质表层;在600℃以上时,钛吸收氧形成硬度很高的硬化层;氢含量上升,也会形成脆化层。吸收气体而产生的硬脆表层深度可达0.1~0.15 mm,硬化程度为20%~30%。钛的化学亲和性也大,易与摩擦表面产生粘附现象。
钛是具有强烈钝化倾向的金属,在空气或含氧的介质中,介质温度在315℃以下,钛表面能生成一层致密的、附着力强、极稳定和自愈能力强的氧化膜,保护了钛基体不被腐蚀。这也使钛及其合金在氧化性、中性和弱还原性等介质中是耐腐蚀的,而在强还原性介质中不耐蚀。
钛合金在潮湿的大气和海水介质中抗蚀性远优于不锈钢,对点蚀、全面腐蚀、应力腐蚀的抵抗力特别强,对碱、氯化物、氯的有机物、HNO3、稀H2SO4等有优良的抗腐蚀能力,是海洋工程理想的材料。但钛在还原性酸(较浓H2SO4、HCl、H3PO4)、HF、Cl2、热强碱、某些热浓有机酸、沸腾浓AlCl3溶液等中不稳定,会发生强烈腐蚀。另外,钛合金有热盐应力腐蚀倾向。钛在550℃以下能与氧形成致密的氧化膜,具有良好的保护作用。在538℃以下,钛的氧化符合抛物线规律。但在800℃以上,氧化膜会分解,氧原子以氧化膜为转换层进入金属晶格,此时氧化膜已失去保护作用,使钛很快氧化。
为增强钛的氧化膜保护作用,可以通过表面氧化、电镀、等离子喷涂、离子氮化、离子注入和激光处理等表面处理技术,获得所希望的耐腐蚀效果。针对在H2SO4、HCl、甲胺溶液、高温湿Cl2和高温氯化物等生产中对金属材料的需要,开发出钛-钼、钛-钯、钛-钼-镍等一系列耐蚀钛合金。钛铸件使用了Ti-32Mo合金,对常发生缝隙腐蚀或点蚀的环境使用了钛-0.3钼-0.8镍合金或钛设备的局部使用了Ti-0.2Pd合金,均获得了很好的使用效果。
钝态下,钛及钛合金的自然腐蚀电位比碳钢正,在电偶腐蚀中钛常为阴极,易产生阴极析氢导至钛的氢脆。但钛与不锈钢的自然腐蚀电位相差不大(低于50mV),一般不考虑钛与不锈钢的电偶腐蚀问题。钛容器中可用不锈钢内件,不锈钢容器中也可用钛内件。
钛及钛合金不考虑晶间腐蚀问题。只在很少几种介质中可能产生应力腐蚀,如发烟硝酸及含有盐酸的甲醇、乙醇。其他介质条件一般不考虑应力腐蚀问题。当用于制作可能产生缝隙腐蚀的构件时,可采用抗缝隙腐蚀性能更好的TA9和TA10耐蚀低合金钛。当盐水温度超过74℃时,TA10比工业纯钛具有更好的耐蚀性。
钛的液相线和固相线间的温度区域窄,焊接熔池凝固时,溶解在钛液中的气体析出不畅,易形成气孔和局部疏松,成为钛焊缝在强腐蚀介质中易遭坑蚀的原因。
钛容器制造过程中钛表面易遭铁污染,与腐蚀介质接触时会造成电偶腐蚀,易导致钛阴极析氢与钛氢脆。因此钛容器最好在制造后进行化学钝化或阳极化处理,以消除铁污染。钛表面的铁污染可用蓝点试验检验。经验表明,一般情况下钛表面的铁污染量不会很大,即使未清除,在与腐蚀介质接触的初期,铁会很快被腐蚀消失,析氢量有限,所造成的氢脆现象不会很严重。因此不能说,未消除铁污染的钛容器就一定不能用。
在碳钢件上不能堆焊钛,只能采用钛钢复合板。因此,钛容器常用钛衬里和钛钢复合板,钛的对接焊容易将钢溶入钛焊缝中使焊缝脆化,因此常用钛盖板搭接焊的接头形式。
钛容器允许介质有较高的流速。在海水中,钛允许海水最高流速20m?s-1。
钛容器主要采用工业纯钛,其耐蚀性比一般的钛合金好(除耐蚀钛合金外)。工业纯钛杂质含量低的牌号耐蚀性稍好,但差别不大,耐蚀性不作为选用工业纯钛牌号的主要依据(主要依据力学性能与成形性能)。可用来制造各种化工设备如热交换器、泵、反应器、加热器、储存容器等。例如在化肥工业中,目前国外已使用钛材来制造尿素生产中的合成塔、反应器、搅拌器、换热器、分离器和压缩机等设备。因在HCl,NH4Cl,NH4HS中的耐蚀性好,多年来钛及钛合金已成功地用于炼油常减压蒸馏装置冷凝器管组,其寿命远高于碳钢或其他耐蚀合金。
随着科技的发展,冶炼技术的不断改进,钛的年产量逐渐提高,金属钛的许多优良性能将会得到越来越广泛的应用,钛大有可能成为继铜、铁、铝之后的第四代金属,成为未来的钢铁。因此,有人把钛誉为21世纪的金属。
06 锆及锆合金
锆及锆合金在酸、碱等介质中具有良好的耐蚀性,同时具有突出的核性能和优良的力学性能,是工业上常用的金属之一。
金属锆制品分为两大类,一种为核级锆,利用锆的热中子俘获截面小,有突出的核性能,所以,作为核动力反应堆的燃料包覆材料和其他结构材料,最初是用于核动力舰船,后来则大量用于原子能发电站。另一种利用锆及其合金具有优异耐蚀性,对很多腐蚀介质有很强的抗力,同时又具有良好的力学和传热性能,以及显著的成本优势,作为工业级锆(或化工锆、火器锆),主要用于制作军工、航空航天、石油化工、电子等领域优异的耐蚀结构材料,主要应用包括压力容器、热交换器、管道、槽、轴、搅拌器及其它机械设备以及阀、泵、喷雾器、托盘、除雾器和塔衬料等。美国在非核领域用锆方面已相当广泛,例如已制成直径达6m的锆制反应塔、100马力大型锆制离子泵、直径达3m的管式换热器等,近年来非核用锆更有扩大的趋势。目前,从锆材的生产到设备的设计、制造和检验技术也已日渐成熟,为锆容器的广泛应用提供了基础。随着国内化工行业的发展,许多强腐蚀的设备越来越多地采用锆材,大大提高设备寿命及可靠性,取得很好的经济效益。
我国已能生产核用和非核用的锆材,锆及锆合金国家标准为GB/T 26314锆及锆合金牌号和化学成分、GB/T 8767锆及锆合金铸锭、GB/T 8769锆及锆合金棒材和丝材、GB/T 21183锆及锆合金板、带、箔材。标准参考了美国ASTM B551锆和锆合金带材、薄板和中厚板、ASTM B352核工业用锆和锆合金薄板、带材和中厚板材 的内容,结合国内实际生产情况制定。标准规定了一般工业和核工业用锆及锆合金铸锭及其加工产品的牌号、化学成分及化学成分分析和分析报告等,适用于一般工业和核工业用锆及锆合金铸锭及其加工产品。非核用锆牌号主要有R60702、R60703、R60704、R60705、R60706等。
Zr与Ti同属第IV族副族,和Ti一样,室温时为六方密排的晶格结构,造成锆和钛显示出强烈的各向异性。在稀有金属中都为活性、高熔点稀有金属,具有许多相同的物理和化学性能。但Zr的化学活性更高,更易钝化,因此,Zr在多数介质中的耐蚀性比Ti更好,接近Nb和Ta。
锆的标准电极电位为-1.53V,易于氧化,在表面生产致密钝化膜,使锆在大多数有机或无机酸、强碱、酸碱循环、熔盐、高温水、液态金属等中具有良好的耐蚀性。如在沸点以下温度的浓HCl中耐蚀性优异,但在149℃以上有氢脆的危险;可用于质量分数小于70%,250℃以下的HNO3。用于H2O2中既不会被腐蚀,也不会产生能分解过氧化氢的催化剂。在HF、H2SO4(浓)、H3PO4(浓)、王水、Br2(水)、HBr、H2SiF6、次氯酸盐、HBF中不耐蚀;在氧化性氯化物中不耐蚀,可能产生点蚀,但在还原性氯化物中耐蚀。
锆主要靠本身的钝化性能耐蚀,并不靠加入合金元素来提高耐蚀性。纯锆耐蚀性比锆合金稍好。锆在空气中,425℃会严重起皮,540℃生产白色氧化锆,700℃以上吸氧变脆,在空气中进行预氧化处理可以提高耐蚀性,如纯锆在700℃保温2h,锆合金在550℃保温4h或600℃保温2h。
在400℃以上与N2反应,800℃左右反应剧烈。300℃以上吸氢,产生氢脆,可通过1000℃真空退火消氢。
温度和pH值对锆在相容媒介里的防腐能力只有微弱的影响,锆在水中长期使用的温度局限为350℃。
锆应用于尿素合成塔,200℃下,腐蚀速率比钛低一个数量级。用于230℃的尿素合成塔,尿素合成的转化率可达80%-90%。
锆在氟化物除外的卤化物里,对缝隙腐蚀有免疫能力。
锆的电偶腐蚀,和大多数金属偶合时,锆通常作为阴极;不应和惰性材料偶合,如石墨或铂,会增加锆的腐蚀率。
锆在纯水和蒸汽、非氧化性氯溶液、NaOH、H2S中有抗应力腐蚀的能力,在氧化性氯化物溶液、浓甲醇、含酸甲醇、I2蒸汽、含盐酸乙醇、HNO3(浓)、质量分数64%-69%H2SO4等中可能产生应力腐蚀开裂。
锆、钛和铌对微生物腐蚀有免疫力,这是由于它们对硫化物的亲合力低,又有氧化膜的防护。
锆焊接接头在冷却中由β锆转变为α锆的过程中,锆中含有的Fe会富集在β晶界和α片间。含量可达平均值的20倍,从而降低焊接接头的耐蚀性。经700℃-800℃的均匀化处理,可有效地改善焊接接头的耐蚀性。
应力大于240MPa时,锆合金会出现延迟氢化物裂纹,在锆705材料焊接后14d内要做应力释放处理,减低发生延迟氢化物裂纹的可能性。锆和锆合金的热处理规范为:消除应力退火,500℃-600℃,0.5h/25.4mm;减少应力加厚氧化膜,500℃-600℃,4-6h;完全退火,625℃-788℃,0.5-4h,恢复力学和耐蚀性能。
07 钽及钽合金
钽有很高的化学稳定性,优于钛、镍基合金及不锈钢,近似于铂和玻璃。钽在150℃以下抗化学腐蚀及大气腐蚀的能力很强,可耐沸腾温度下任何浓度的HCl和HNO3、200℃以下的酸性和碱性介质,耐室温至150℃的发烟硝酸和发烟硫酸所组成的混合酸。除浓碱、KI、F-、发烟和高温浓H2SO4和浓H3PO4外,钽对其他的酸都是稳定的。
钽在质量分数75%以下H2SO4中耐蚀性能优良,可使用于任何温度,对不充气的浓H2SO4可用于170℃,充气的浓H2SO4可用于260℃,超过此温度腐蚀增大。钽材对H3PO4的耐蚀性能良好,但酸中如含有微量的F-(质量分数>4×10-6)时,则腐蚀率加大。
钽材在碱中通常不耐蚀,会变脆,在高温、高浓度下腐蚀更快。
钽能与高温气体(惰性气体除外)反应,O2、N2、H2等可渗入内部使之变脆,如与初生态H接触,也会吸氢变脆。因此,钽材设备不可与较活性金属(如Fe、Al、Zn)等接触,因为易构成钽-铁(Al、Zn)原电池,腐蚀反应产生的氢将破坏钽阴极,使设备失效。如用氢超电压极小的一小块铂(面积大约为钽的万分之一)与钽连接,那么所有的氢将在铂上放出,可以避免氢对钽的破坏。
钽的腐蚀是均匀的全面腐蚀,对切口不敏感,不发生腐蚀疲劳和腐蚀破裂等局部类型的腐蚀。利用钽的这一特性,可以做包覆和衬里材料。
我国钽及钽合金标准有GB/T 3629钽及钽合金板材、带材和箔材,GB/T 14841钽及钽合金棒材。钽材耐蚀性能优异,但价格昂贵,为了降低成本,钽层的厚度希望尽可能的薄。因为钽材和钢材的熔点相差悬殊(钽材的熔点为2996℃,钢材的熔点为1400℃),且Fe与Ta在高温下会形成Fe2Ta脆性金属间化合物,如果措施不当,容易导致焊缝开裂,所以薄层钽钢复合板或衬里的焊接非常困难。
08 铌和铌合金
铌是优质耐酸碱和液态金属腐蚀的材料,在许多腐蚀环境中都有极佳的抗腐蚀能力,可应用于盛HCl的容器中。铌对一些含氟化物溶液也有抗腐蚀作用,在活性金属中这是独一无二的。在化学工业中可用于制作反应容器、换热器、蒸煮器、加热器、冷却器、各种器皿器件、热电偶、安全膜和管线等。
在室温H2SO4溶液中,铌一般对低浓度H2SO4有较好的防腐能力,但在高浓度下会引起脆化。当H2SO4质量分数高于40%时,随着温度升高,铌将迅速被侵蚀。在硫酸中含有Fe3+、Cu2+可以明显改善铌的耐蚀性能。
在HNO3环境具有很强的抗腐蚀能力,对任何浓度的HNO3都具有抗蚀能力,并不产生应力腐蚀开裂。
在H3PO4溶液中表现出极佳的抗蚀能力,加入大量钽的铌-钽合金显著地改善了铌在热H3PO4溶液中的抗蚀性。
在许多有机酸有很强的抗蚀性,对醋酸、柠檬酸、甲醛、甲酸、乳酸、酒石酸、三氯甲酸等有机酸,铌有较好的抗腐蚀性。
除了那些水解形成碱性溶液的盐以外,铌在盐溶液具有极佳的耐蚀性。即使有氧化剂存在,铌对铬盐的溶液也具有抗蚀性。
免责声明:本网站所转载的文字、图片与视频资料版权归原创作者所有,如果涉及侵权,请第一时间联系本网删除。
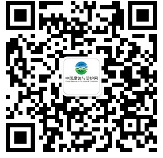
官方微信
《中国腐蚀与防护网电子期刊》征订启事
- 投稿联系:编辑部
- 电话:010-62316606-806
- 邮箱:fsfhzy666@163.com
- 中国腐蚀与防护网官方QQ群:140808414