汽车蓄电池电缆端子由黄铜冲压成型,通过螺栓拧紧并固定在蓄电池电极上,主要起到紧固的作用。某汽车蓄电池电缆端子现场装配后出现多起开裂故障,该蓄电池电缆端子的材料为H65黄铜,硬度状态等级为Y2,成型工艺为:多道冲压→整形→去毛刺→电镀→装配。抽取同批次库存端子进行检验,发现部分端子也存在裂纹。
为了查明该汽车蓄电池的H65黄铜电缆端子出现开裂的原因,笔者对其进行了检验和分析。
理化检验
宏观观查
图1 蓄电池电缆端子的宏观形貌
宏观观查发现,出现开裂的端子形状类似“卡箍”,裂纹出现在折弯区域,部分裂纹较长,长度达到2~3mm;部分裂纹较细小,长度不到0.5mm,如图1所示。
化学成分分析
对端子开裂部位取样,采用Bruker Q4/UV型直读光谱仪进行化学成分分析,结果如表1所示。
表1 蓄电池电缆端子的化学成分质量分数 %
可见端子的化学成分符合GB/T 5231—2012?加工铜及铜合金牌号和化学成分?对H65黄铜成分的要求。
断口分析
图2 端子断口的宏观形貌
将端子沿着裂纹人工打开,使用VHX-200E型体视显微镜观察断口形貌,如图2所示。
可见断口颜色发暗,断面平齐且附近无明显的塑性变形,断口表面有腐蚀产物覆盖。采用EVO MA25型扫描电镜(SEM)观察断口形貌。
图3 端子断口不同部位的SEM形貌
由图3可见,断口呈沿晶开裂特征并伴随二次裂纹,断口附近表面区域有腐蚀产物堆积,断口内部晶面有颗粒状物质覆盖。
使用扫描电镜附带的能谱仪(EDS)分别对断口附近表面腐蚀产物和内部晶面颗粒状物质进行微区成分分析。
表2 端子断口不同物质的能谱分析结果质量分数 %
由表2可见,断口附近表面腐蚀产物中含有较多的锡元素,内部晶面也含有锡元素,这说明在进行镀锡工艺前,端子已产生裂纹。由锡元素含量可推测裂纹为由表及里扩展。在裂纹附近,除了锡元素以及基体材料中的铜、锌元素外,还含有较多的氧元素,未检测到其他腐蚀性元素如氯、硫等,这说明端子断面的腐蚀产物主要为氧化物。
金相检验
在端子的开裂部位取样,试样经镶嵌、打磨、抛光,使用三氯化铁盐酸水溶液(FeCl3,HCl,H2O的体积比为1∶3∶12)浸蚀后,采用Axio Imager.A2m型光学显微镜观察显微组织。
图4 端子开裂部位不同位置的显微组织
由图4可见,端子开裂部位组织中裂纹沿着晶界呈树枝状扩展,裂纹形态与应力腐蚀裂纹的相似。由图4a)可见,端子开裂部位的边缘组织中存在变形的α相和β相,组织内部分布着大量的黑色滑移线,因此判断边缘区域由于组织变形存在较高的残余应力。由图4b)和图4c)可见,端子开裂区域与未开裂区域的心部显微组织无明显差异,均为等轴α+β相,且无明显的冶金缺陷。
硬度测试
在端子基体取样,采用ZHVU-AH型维氏硬度计进行硬度测试,得到端子硬度测试结果为85,86,86HV,符合JIS H3100—2006?铜及铜合金薄板、板材和带材?对H65黄铜的硬度要求(85~145HV)。
盐雾模拟试验
为查明端子冲压成型后残余应力对其性能的影响,同时为了加快试验速率,取同批次库存正常端子共计5个,在ZYQ-16型中性盐雾箱(注入质量分数为5%的NaCl溶液)中进行不同时长(24,48,96h)的盐雾模拟试验。试验后在端子冲压折弯部位取样,试样经镶嵌、打磨、抛光,使用三氯化铁盐酸水溶液(FeCl3,HCl和H2O的体积比为1∶3∶12)浸蚀后,采用Axio Imager.A2m型光学显微镜观察显微组织。
图5 经过48h盐雾模拟试验后正常端子的显微组织
试验结果表明,经过24h盐雾模拟试验后,端子的冲压折弯部位均未发现明显裂纹;经过48h盐雾模拟试验后,部分端子的冲压折弯部位存在应力腐蚀裂纹,裂纹长度约为0.55mm,且表面存在脱锌现象,如图5所示;经过96h盐雾模拟试验后,部分端子肉眼可观察到宏观裂纹。这说明在现有冲压工艺条件下,端子对应力腐蚀开裂的敏感性较高,在遇到腐蚀介质时,时间越长发生应力腐蚀开裂的概率越大。
分析与讨论
由上述理化检验结果可知,端子的化学成分、硬度及显微组织均未有异常,这说明端子出现裂纹与上述因素无关。由断口分析结果可知,端子断口处的近表面及内部均含有一定量的锡元素,这说明端子在进行镀锡工艺前已有裂纹。断口颜色发暗,无明显的塑性变形,断口呈现沿晶开裂形貌且伴随二次裂纹,这与应力腐蚀断口的特征较相似。由金相检验结果可知,端子断口附近区域的裂纹起源于端子表面,且呈树枝状向内部扩展,裂纹走向符合应力腐蚀裂纹走势。从裂纹萌生位置和裂纹走向来看,裂纹主要分布在端子冲压折弯部位,且从折弯处向端子内部扩展,这是由于冲压折弯部位为端子变形量较大处,冲压成型后该处存在较大的残余拉应力。由盐雾模拟试验结果可知,经过48,96h盐雾试验后,在端子的冲压折弯部位有裂纹萌生,这表明端子在残余应力下,遇到Cl-,OH-等腐蚀介质一段时间后会产生应力腐蚀裂纹。
应力腐蚀开裂是金属构件在静应力和特定腐蚀环境共同作用下所形成的脆性开裂,其成形的必要条件包括一定的拉应力和腐蚀环境。黄铜冷加工后往往存在一定的残余拉应力或者外加拉应力,且处于易引起锌选择性溶解的腐蚀介质中,黄铜处于有氨、氧、水、二氧化硫的环境中,再加上黄铜易于脱锌,因而易于发生应力腐蚀开裂。
通过调查出现裂纹端子的工艺流程卡,发现生产过程中无退火工序,且表面镀锌工序采用的是委托外厂电镀。端子的生产日期为2018年5月,电镀时间为同年7月,端子放置时间为2个月,而此期间正是南方梅雨季节,气温较高且气候潮湿。端子成型后应力未能得到释放,在残余应力和H2O,O2,CO2等腐蚀介质的共同作用下发生了应力腐蚀开裂。
结论及建议
汽车蓄电池电缆端子冲压成型后残余应力未得到有效释放,且端子在存储期间接触到H2O,O2,CO2等腐蚀介质,导致其发生了应力腐蚀开裂。建议对于冷加工件增加退火工艺,同时避免冲压件在存储期间接触到腐蚀介质,以降低发生应力腐蚀开裂的概率。
免责声明:本网站所转载的文字、图片与视频资料版权归原创作者所有,如果涉及侵权,请第一时间联系本网删除。
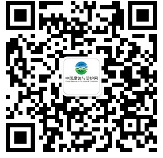
官方微信
《中国腐蚀与防护网电子期刊》征订启事
- 投稿联系:编辑部
- 电话:010-62316606-806
- 邮箱:fsfhzy666@163.com
- 中国腐蚀与防护网官方QQ群:140808414