油管是油气从井底到地面的生产管线[1],油管腐蚀会引起严重的经济损失,同时也存在重大安全隐患,甚至会危及人身安全[2-7]。塔河油田具有“高CO2、高H2S、高Cl-、低pH值”的“三高一低”特点[8-10],酸化压裂是提高其产量的重要手段。随着开发进程的不断深入,酸化压裂等作业的影响,以及综合含水的不断上升,油管腐蚀问题日益凸显,频繁的腐蚀穿孔严重制约了油气田高效开发、安全生产[11-13]。因此,研究油管腐蚀穿孔失效原因、提出防护建议[14],对提高油井管柱安全及经济效益具有重大意义。
1 井况分析
塔河油田某井2009年酸压完井,初期油井自喷生产,后由于日产能低,进行注水替油。2013年至2018年,共实施单元注水7轮次,此间累计产油2151 t,累计产水8533 t,平均含水率为79.8%。
2018年4月修井起出油管,发现多根油管腐蚀严重,部分油管已发生腐蚀穿孔甚至断脱,如图 1所示。油管内外壁存在较多腐蚀坑槽及表面缺陷,且多处发生由内而外的腐蚀穿孔,内壁腐蚀坑深约0.1~4.2 mm。失效油管材质为P110S,入井服役1849天;井底温度约135 ℃,地温梯度1.8 ℃/100 m;该井自喷初期油压27.5 MPa,井底压力约为85 MPa;H2S体积分数约为1.60%,井底分压约1.3 MPa;CO2体积分数为5.93%,井底分压约5.0 MPa,是CO2/H2S共存的复杂腐蚀环境。
2 理化检验及结果
2.1 化学成分分析
依据GB/T 22368-2008《低合金钢多元素含量的测定辉光放电原子发射光谱法(常规法)》、GB/T 20123-2006《钢铁总碳硫含量的测定高频感应炉燃烧后红外吸收法(常规方法)》在油管管体采集金属粉末,对金属中的C、P、S、Cr等元素进行检测,结果见表 1。表 1表明,该失效油管化学成分及含量符合标准ISO 11960-2011《Petroleum and natural gas industries-Steel pipes for use as casing or tubing for wells》中P110S钢化学成分的规定。
表 1 失效油管化学组成检测结果
Table 1 Test results of chemical composition of failed tubing
2.2 金相组织分析
在油管基体切取试样,试样长15 mm、宽10 mm,试样厚度取油管壁厚,参照GB/T 10561-2005《钢中非金属夹杂物含量的测定标准评级图显微检验法》、GB/T 13298-2015《金属显微组织检验方法》和GB/T 6394-2017《金属平均晶粒度测定方法》对油管纵向和横向进行非金属夹杂物检测与评级、金相组织分析、晶粒度评级,结果见表 2。表 2表明:油管金相组织为回火索氏体,组织均匀且正常、晶粒细小,晶粒度为9.5级;纵向截面和横向截面的非金属夹杂物都为球状氧化物类夹杂,夹杂物尺寸正常,其等级为D0.5细。油管金相组织满足标准要求,结果如图 2所示。
表 2 金相组织测试结果
Table 2 Metallographic structure test results
2.3 硬度分析
参照GB/T 230.1-2018《金属材料洛氏硬度试验第一部分:试验方法》在失效管段上取环形试样,采用洛氏硬度计按照四个象限,内中外的方法在环形试样截面上进行环向硬度测试。测试结果表明,失效管件的硬度平均值为28.5 HRC,低于30 HRC,符合标准ISO 15156-2015《Petroleum and natural gas industries-Materials for use in H2S-containing environments in oil and gas production》规定。
2.4 冲击性能分析
基于失效件腐蚀情况,参照GB/T 229-2007《金属材料夏比摆锤冲击试验方法》,在金属管段上取样,加工成小尺寸冲击试样(55 mm×10 mm×5 mm),采用ZBC2302-D型示波冲击试验机对其进行冲击韧性试验。从实验结果(见表 3)可知,满足标准ISO 11960-2011要求。根据示波冲击试验机录取的实验数据,绘制冲击力、能量与位移的关系曲线(见图 3)。
表 3 失效油管冲击性能测试结果
Table 3 Test results of impact performance of failed tubing
2.5 拉伸性能分析
在失效油管上参照ISO 11960-2011选取拉伸试样(由于油管内壁有诸多深浅不一的腐蚀坑,选取拉伸试样时应尽量避开),将其加工为标准板状拉伸试样,试样厚度为油管壁厚。依据GB/T 228-2010《金属材料室内拉伸试验方法》,利用MTS拉伸实验机进行力学性能测试,结果见表 4。由表 4可知,失效管件的抗拉强度、屈服强度均符合标准ISO 11960-2011中关于P110S钢级管材力学性能的规定。但由于内壁腐蚀坑较多,在取拉伸试样时无法完全避免腐蚀坑取完整试样,这导致拉伸试样断后延伸率测试值较标准值略低。
表 4 失效油管拉伸性能检测结果
Table 4 Test results of tensile properties of failed tubing
2.6 腐蚀形貌分析
油管管体存在多处刺漏,刺漏处附近可见较浅坑槽,如图 4(a)所示,但刺漏处壁厚无明显腐蚀趋势特征。从图 4(a)中红框所示位置切开,观察到内壁腐蚀较外壁更严重,且壁厚由内向外减薄,如图 4(b)所示,可以判断油管发生由内向外的腐蚀穿孔。用扫描电子显微镜(SEM)对管柱内壁的腐蚀微观形貌进行了观察,见图 5。由图 5可知,在高倍放大下可观察到规则立方状腐蚀产物晶体,为CO2腐蚀产物FeCO3晶体[15],同时可见少量H2S腐蚀球状晶体,腐蚀产物处元素主要由C、O、Na、Ca、S、Fe组成,推断该腐蚀存在H2S与CO2共同腐蚀,以CO2腐蚀为主。
将图 4(b)中A-A剖面加工成20×壁厚的截面试样,用环氧树脂进行封样,使用扫描电子显微镜观察失效油管截面(A-A剖面)腐蚀情况,结果见图 6。图 6中a区域为环氧树脂,b区域为腐蚀产物膜,c区域为油管基体。该油管腐蚀明显,腐蚀膜厚度约为120 μm,从b区域可以观察到FeCO3晶体形貌;在腐蚀膜位置C、O含量较高,进一步论证了该膜为CO2腐蚀产物膜,且油管腐蚀以CO2腐蚀为主。
利用X射线衍射仪对内壁附着物进行取样分析,结果见图 7。由图 7可知,内壁腐蚀产物主要为FeS、FeCO3、FeO(OH)、Fe8O8(OH)8Cl1.35。综上可知,内壁腐蚀是由于油管中存在强腐蚀性介质CO2、H2S,从而导致油管内壁发生腐蚀。
3 腐蚀原因分析
依据相关标准对该井P110S油管失效管段进行检测分析的结果表明,油管的化学成分、金相组织、硬度、力学性能等都满足标准对管材材质的要求。失效油管宏观形貌、微观形貌表明油管以内腐蚀为主,外壁存在少量较浅腐蚀坑。内壁腐蚀主要表现为点蚀及穿孔。油管内壁SEM图像表明内壁腐蚀产物主要为FeCO3晶体,EDS能谱表明腐蚀产物中主要含有C、O、S、Fe等元素,结合XRD腐蚀产物分析,确定内壁主要腐蚀产物为FeS、FeCO3、FeO(OH)、Fe8O8(OH)8Cl1.35。FeO(OH)、Fe8O8(OH)8Cl1.35的形成是由于油管从井底到地面后暴露于空气中,腐蚀产物发生进一步氧化。FeS为H2S腐蚀的代表性腐蚀产物,FeCO3为CO2腐蚀的重要腐蚀产物[15]。因此可以判断,该井油管点蚀(穿孔)是H2S、CO2、Cl-共同作用的结果。
该井为高H2S、高CO2、高Cl-的间歇生产油井,在点蚀坑初期形成过程中,主要发生酸性工况下的析氢腐蚀,Fe2+与CO32-、S2-结合形成FeCO3、FeS。CO2溶于水生成碳酸,水释放出H+,H+夺取电子还原,促进阳极铁溶解,Fe与CO32-、HCO3-反应,在油管内壁形成FeCO3膜。FeCO3膜对基体有一定的保护作用,但与裸露的基体会形成腐蚀原电池,导致点蚀的发生[3, 16-20]。
H2S在水溶液中具有较大的溶解度,在水中电离出HS-和S2-,带有较强的腐蚀性。S2-不仅是阴极去极化剂,也是阳极去极化剂,S2-与FeCO3膜反应,生成FexSy,附着在油管内壁的FexSy对基体有一定的保护作用。但附近裸露的基体作为阳极,FeS可参与阴极反应,形成腐蚀原电池,进一步加剧局部腐蚀。
点蚀形成后,在其纵向发展的过程中,Cl-起着催化作用,加速了金属基体的溶解[1]。Cl-虽然不参与金属的阳极反应过程,但它会阻碍金属表面钝化膜(保护膜)的形成,这是导致金属点蚀的重要原因。此外, Cl-会破坏具有保护性的腐蚀产物膜,在界面富集,增加溶液的导电性,并使H+活性增强,加速点蚀坑的纵向发展。在点蚀坑纵向发展过程中,随着腐蚀坑深的增加,坑的直径减小,就更易形成大阴极/小阳极,进一步提高腐蚀前沿的腐蚀速率,最终导致腐蚀穿孔。因此,针对此类高含H2S、CO2和H2O的油井需添加缓蚀剂或采用涂层、镀层、衬里油管,提高油管服役寿命。
4 结论
(1) 入井P110S油管的理化性能、抗拉强度、屈服强度、冲击功满足ISO 11960-2011标准的规范要求。该井平均含水率为78.9%,CO2分压为5.0 MPa,H2S分压为1.3 MPa,高含CO2、H2S、H2O的腐蚀环境是引起油管失效的原因。
(2) 该井油管发生由内向外的腐蚀穿孔,内壁腐蚀产物主要是FeCO3,含有少量的FeS。表明在CO2- H2S- Cl--H2O共存的体系中,油管以CO2腐蚀为主,H2S腐蚀为辅,同时高含量的Cl-加速了局部腐蚀。
(3) 针对此类高含H2S、CO2和H2O的油井,建议继续使用P110S抗硫钢,并采用定期投注缓蚀剂等方法,延长油管服役寿命。
[1] 钟彬, 陈义庆, 孟凡磊, 等. N80油管穿孔失效原因分析[J]. 腐蚀与防护, 2018, 39(8): 647-650.
[2] ZHU S D, WEI J F, BAI Z Q, et al. Failure analysis of P110 tubing string in the ultra-deep oil well[J]. Engineering Failure Analysis, 2011, 18(3): 950-962. DOI:10.1016/j.engfailanal.2010.11.013
[3] 郭玉洁, 张子如, 孙海礁, 等. H2S/CO2环境中某油井管腐蚀失效的分析与讨论[J]. 材料保护, 2018, 51(6): 120-123.
[4] 吴贵阳, 余华利, 闫静, 等. 井下油管腐蚀失效分析[J]. 石油与天然气化工, 2016, 45(2): 50-54.
[5] 付安庆, 耿丽媛, 李广, 等. 西部油田某井油管腐蚀失效分析[J]. 腐蚀与防护, 2013, 34(7): 645-648.
[6] LAUMB J D, GLAZEWSKI K A, HAMLING J A, et al. Wellbore corrosion and failure assessment for CO2 EOR and storage: two case studies in the Weyburn field[J]. International Journal of Greenhouse Gas Control, 2016, 54: 479-489. DOI:10.1016/j.ijggc.2016.08.031
[7] 裘智超, 熊春明, 常泽亮, 等. CO2和H2S共存环境下井筒腐蚀主控因素及防腐对策——以塔里木盆地塔中Ⅰ气田为例[J]. 石油勘探与开发, 2012, 39(2): 238-242.
[8] 叶帆, 杨伟. H2S-CO2-Cl-共存体系下的腐蚀状况[J]. 石油化工腐蚀与防护, 2009, 26(6): 44-46. DOI:10.3969/j.issn.1007-015X.2009.06.013
[9] 战征, 蔡奇峰, 汤晟, 等. 塔河油田腐蚀原因分析与防护对策[J]. 腐蚀科学与防护技术, 2008, 20(2): 152-154. DOI:10.3969/j.issn.1002-6495.2008.02.018
[10] 汤晟, 蔡奇峰, 何小龙. 塔河油田集输管线绝缘法兰附近内腐蚀穿孔因素分析[J]. 石油与天然气化工, 2008, 37(2): 156-159.DOI:10.3969/j.issn.1007-3426.2008.02.018
[11] 张抗, 王大锐, HUFFB G. 塔里木盆地塔河油田奥陶系油气藏储集层特征(英文)[J]. 石油勘探与开发, 2004, 31(1): 123-126. DOI:10.3321/j.issn:1000-0747.2004.01.039
[12] 吕拴录, 骆发前, 相建民, 等. API油管腐蚀失效原因分析[J]. 腐蚀科学与防护技术, 2008, 20(5): 388-390. DOI:10.3969/j.issn.1002-6495.2008.05.022
[13] ZHANG Z, ZHENG Y S, LI J, et al. Stress corrosion crack evaluation of super 13Cr tubing in high-temperature and high-pressure gas wells[J]. Engineering Failure Analysis, 2019, 95: 263-272. DOI:10.1016/j.engfailanal.2018.09.030
[14] ZENG D Z, ZHANG N Y, WANG F, et al. Corrosion assessment of different production casings and material selection in sour gas wells[C]//Proceedings of SPE/IATMI Asia Pacific Oil & Gas Conference and Exhibition. Nusa Dua, Bali, Indonesia: Society of Petroleum Engineers, 2015.
[15] 何智勇, 谷坛, 杨仲熙, 等. 西北某酸性油田腐蚀及防护措施分析[J]. 石油与天然气化工, 2008, 37(3): 240-242.DOI:10.3969/j.issn.1007-3426.2008.03.018
[16] ZHANG N Y, ZENG D Z, ZHANG Z, et al. Effect of flow velocity on pipeline steel corrosion behaviour in H2S/CO2 environment with sulphur deposition[J]. Corrosion Engineering, Science and Technology, 2018, 53(5): 370-377. DOI:10.1080/1478422X.2018.1476818
[17] 曾德智, 董宝军, 石善志, 等. 高温蒸汽环境中CO2分压对3Cr钢腐蚀的影响[J]. 钢铁研究学报, 2018, 30(7): 548-554.
[18] 陈长风, 路民旭, 赵国仙, 等. N80油管钢CO2腐蚀点蚀行为[J]. 中国腐蚀与防护学报, 2003, 23(1): 21-25. DOI:10.3969/j.issn.1005-4537.2003.01.005
[19] 李建平, 赵国仙, 郝士明, 等. 常用油管钢的CO2局部腐蚀速率[J]. 东北大学学报(自然科学版), 2004, 25(11): 1069-1071. DOI:10.3321/j.issn:1005-3026.2004.11.014
[20] 马德胜, 王伯军, 吴淑红. 油气生产过程中CO2腐蚀预测研究[J]. 西南石油大学学报(自然科学版), 2010, 32(3): 137-140. DOI:10.3863/j.issn.1674-5086.2010.03.026
免责声明:本网站所转载的文字、图片与视频资料版权归原创作者所有,如果涉及侵权,请第一时间联系本网删除。
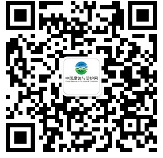
官方微信
《中国腐蚀与防护网电子期刊》征订启事
- 投稿联系:编辑部
- 电话:010-62313558-806
- 邮箱:fsfhzy666@163.com
- 中国腐蚀与防护网官方QQ群:140808414