复合材料应用于汽车行业最早开始于1953年,近年来,复合材料在汽车行业应用中保持着持续增长的发展势头,并且这个趋势还将继续朝着向上方向发展。复合材料的用量之所以会在汽车行业中持续增长,是因为复合材料具备了许多优秀的性能,如:强度高、重量轻、耐腐蚀,并且与铝材和钢材相比,加工成本更低、设计的灵活性更强、更容易成型等等。总之,复合材料是汽车行业替代金属材料的一个很好的可选项。然而,事实上在汽车制造领域,其制作材料并没有完全直接从金属材料转换到复合材料,尤其在大批量生产的汽车方面,复合材料的应用还是很有限的,这是因为有许多和复合材料使用相关的技术问题仍然没有很好地得到解决,其中包括准确的材料定性、生产、油漆、维修、和金属材料的连接以及回收等问题。尽管近年来世界上复合材料的新材料、新工艺和新技术不断涌现,从而在很大程度上使上述问题得到了改善,促进了复合材料在各类汽车中的广泛应用,但也不能否认复合材料在汽车上的广泛应用特别是在中国汽车行业真正广泛应用仍然存在应用技术方面的各类问题,这需要我们去关注,去研究,去探讨,去实践。
本文就汽车复合材料的涂装、连接、维修和回收等四大应用技术问题进行探讨,以期抛砖引玉。
汽车复合材料的涂装
在汽车工业中,汽车车身的外表油漆质量是整车质量最重要的指标之一,因为车身油漆表面不仅起到保护车厢不被腐蚀的作用而且对汽车美化外观有着十分重要的影响。因此,尽管汽车生产主机厂承认复合材料与传统的金属相比具有种种的优点,但是他们对于复合材料经喷涂后的表面是否具有同金属表面一样的质量,仍持保留态度。事实上,复合材料在汽车车身面板方面使用中所遇到的一个最大的挑战就是:复合材料经涂装后产生的瑕疵。
我们以复合材料在汽车车身面板方面使用最多的片状模塑料SMC部件为例,SMC车身部件在涂装后通常会产生很多的表面瑕疵,例如:针眼、气孔、裂纹、气泡等,尤其在车身面板的边缘区域气泡情况较为严重。为了弥补这些缺陷,减少不合格产品率,提高部件的表面质量,国内生产厂家目前是通过大量的涂装后修补手段如破泡、打磨、填腻子、抛光等来加以改进,然后再按通常的涂装工艺进行表面再涂装。这样做的结果虽然减少了不合格品率,但增加了大量的后修补工序和再涂装使生产成本大幅上升,另外也限制了SMC在A级车身面板上的应用。
SMC车身面板在涂装后产生表面油漆瑕疵和起泡的原因绝大部分都归因于基质中的微小孔隙和微裂纹。而这些微小孔隙和微裂纹常常是在生产及搬运过程中不注意人为形成的,例如从部件的模压到脱模到除边的过程,以及从部件的包装到运输的过程,我们经常会发现,在部件的边缘部分会产生许多微裂纹。正是这些看似微不足道的微小孔隙和微裂纹,在油漆喷涂过程中积聚了空气中的水分和油漆中挥发性溶剂,当油漆后的SMC部件通过烘箱高温烘烤时,水分和溶剂膨胀蒸发变成气泡逸出,造成已喷完漆的部件表面起泡或气泡破裂变成气孔、针眼等油漆瑕疵。
就SMC部件在涂装后产生的表面瑕疵,目前国外复合材料行业主要的做法是消除微孔隙和微裂纹,从根夲上杜绝产生油漆表面瑕疵的根源,收到了很好的效果,主要有以下几方面的措施:
1. 生产高强度、高韧性SMC树脂。
近年来,美国AOC公司和Thyssenkrupp Budd 公司联合起来开发了Atryl? TCA一种新的SMC树脂。这种SMC树脂强度高,生产出的部件可减少50%的表面波痕(与传统的SMC表面相比),并增加了69%的韧性(与传统的SMC树脂相比)。由于具有这些性能,可显着地阻止在脱模过程及脱模后微裂纹的产生,这样即使在重要的边缘区域也不会产生微裂纹。
2. 加强模压工艺控制和模具技术进步。
通过改变SMC片材加料方式和片材铺覆位置;增加材料的流动距离;使闭模过程中材料发生均匀位移等措施以达到减少SMC部件孔隙量。具体做法有采用PLC、 NCN控制复合材料压机对不同部件的产品模压工艺进行对应编程模压控制;采用激光定位仪对材料铺覆进行正确定位等。另外对大型或复杂零部件采用真空辅助排气模具,在真空条件下进行模压成型操作,这样就可以显着降低甚至消除SMC多孔性缺陷。
3. 开发新型底漆涂料和新型涂装工艺。
2003年BASF公司针对SMC“油漆气泡”难题,推出DynaSeal? 紫外固化封孔剂,这种技术使得SMC部件在喷漆烘干前,通过紫外引发聚合反应对SMC表面进行封孔,在接下来的喷漆油漆固化中,这层紫外固化的封孔剂层可阻止SMC基体中吸收的挥发物逸出,从而避免了气孔的产生。另外一个方法就是模内涂层(IMC)。SMC在模具内部完全固化了之后,操作人员注入一层液体的涂层材料,然后这层涂层材料在SMC的表面固化并填充满所有的空隙,同时提供一层类似底漆的表面,防止了油漆气泡的产生。|
4. 文明生产,文明搬运。
SMC部件产生微裂纹很大程度上是从脱模到除边的过程,以及从部件的包装到运输的过程中不文明生产和不文明搬运造成的。因此加强文明生产和文明搬运的教育至关重要,国外己普遍实行“产品不着地”的文明生产方式,在汽车复合材料行业大力推广另件专用周转箱(架)物流形式,减少了搬运次数,不让另件有互相碰撞机会,杜绝人为因素造成的微裂纹产生。
以上介绍的国外几种新材料、新工艺、新技术着眼从根源上解决汽车复合材料在涂装方面不尽人意的缺陷,消除限制复合材料大规模应用的障碍,使复合材料车身面板能够达到或超过传统的钢铁材料的油漆的水平,从而使汽车复合材料的应用将日益广泛。
汽车复合材料的连接和固定
随着汽车复合材料的应用日益广泛,汽车复合材料部件之间的组合装配以及复合材料部件与邻近金属零部件的连接固定的问题日益突出,汽车行业传统金属零部件之间的连接方式已不能适应客观需求了,在此情况下,我们有必要对汽车复合材料的连接与固定的连接方式进行新的学习和认识,并进行合理的选择。根据国外成熟的经验,汽车复合材料连接固定的方式主要有三种方式:(1)机械紧固;(2)粘结剂粘接;(3)焊接/熔接。
机械紧固这种连接固定方法使用的是铆钉和螺栓,是最普及也是最容易理解的一种连接方式。对汽车行业来说,机械紧固连接方式有许多不足之处,如:重量增加、应力集中、部件之间的交迭、高公差的要求、电蚀性等。但是,从另一方面说,机械连接不需要对表面进行处理或后续的抛光,这样重复拆卸就很方便(如:检查、维修和回收)。相对而言,对环境的影响也不是很敏感,如温度的影响等。
粘结剂粘接连接固定方法相对于机械紧固连接固定方法具有以下优点:减轻结构重量,外观平整光滑,改善疲劳强度,适应性强,最适合薄壁部件的连接,粘接工艺简单,可缩短生产周期。,但粘结剂粘接连接固定方法也存在一些缺点,如另部件的工作温度范围不高;粘接质量易受不同因素影响,产品性能的分散性较大;没有可靠的检验方法;粘接面的表面处理和粘接工艺过程要求较严;需要专用的加热加压处理粘接工装等。因此,在一些重要的部件和连接位置,往往会采用粘接与某一种机械紧固连接的混合连接固定方法,既充分利用了粘接的优点,又确保了连接部位的足够强度和可靠性。
焊接/熔接连接固定方法主要应用于热塑性汽车复合材料部件,焊接/熔接连接固定方法的主要优点是:良好的机械性能、连接处的耐用性、加工时间短,易于在线检测以及部件表面处理要求低等。可以用于热塑性汽车复合材料的焊接/熔接连接固定方法主要有三种:(1)超声波焊接/熔接、(2)电感应焊接/熔接(3)电阻焊接/熔接。对汽车复合材料进行焊接/熔接有以下不足之处:不易拆卸、需要添加导电性的填料(针对电感应焊接/熔接)、需要使用金属网(针对电阻焊接/熔接)、可允许的碳纤维含量很低(所有三种焊接/熔接工艺)等。
根据上述简单介绍,我们知道汽车复合材料连接固定的方式主要有三种,每一种都有各自的优缺点,适应不同的应用场合。但相对而言,最有发展潜力的汽车复合材料连接工艺是采用粘结剂连接固定方法,随着粘结剂向着功能性不断提高、具有双重效力(既可以粘结热固性复合材料又可以粘结热塑性复合材料)以及绿色环保的方向发展,汽车复合材料粘结剂连接固定方法正日益为汽车工业所重视、接受并盛行起来。限于篇幅,本节汽车复合材料的连接和固定,主要讨论粘结剂粘接连接固定方法。
1.汽车复合材料粘结剂粘接连接固定方法的优点
近年来,由于高性能结构粘结剂的出现,使得采用粘结剂粘接的连接方式不断得到人们的认可。作为一种最有发展潜力的连接固定工艺,它有许多突出的优点:
1) 可以根据具体的设计要求(如:防撞击性能)来决定粘结剂的机械性能;
2) 粘结剂的超抗疲劳和耐腐蚀的优点可以延长产品的使用寿命;
3) 粘结剂具有很好的密封性;
4) 两种材料或结构粘接在一起可以实现比较光滑的表面,具有造型设计上的优势;
5) 通过整个的粘接区域来分散部件所受的负荷,从而避免了局部最大压力的集中;
6) 粘结剂填充空隙的特点可允许部件有一定的公差;
7)可对粘结剂的硬度进行调整,优化整个产品的硬度
2、汽车复合材料常用结构粘结剂的种类
一般来说,汽车复合材料结构粘结剂通常使用环氧树脂、聚氨酯树脂和丙烯酸酯树脂为基础的三大类粘结剂,该三大类粘结剂在使用中也各具特点,应该准对不同的材料和要求进行不同的选择:
环氧基粘结剂:对复合材料、热固性塑料和金属粘接性极好;强度、挠度和弹性都很高;固化过程收缩性最小。分为单、双组份两种。单组份环氧粘接剂要求热固化,应用条件要求很严。
聚氨酯基粘结剂:对绝大部分复合材料和塑料的粘接性极好;对金属的粘接性较好;机械性能从刚性到挠性范围大;持久性好;但加工过程中对潮湿敏感;固化速度的范围较广。
丙烯酸基粘结剂:对复合材料和热固性塑料的粘接性极好;对金属的粘接性好;允许被粘件进行较差的预处理;能达到高强度与高韧性的最佳结合;耐化学性好,有效使用期长;固化速度快;但有恶臭;固化过程中收缩性较高。
3、汽车复合材料粘接前的表面处理
汽车复合材料(尤其是热塑性汽车复合材料)的表面能都相对较低,所以在使用结构粘结剂之前,需要对汽车复合材料表面进行适当的处理,以去除表面的污垢、粉尘、油污、油脂、水分、脱模剂和增塑剂等,同时,提高基材的表面能,使其高于结构粘结剂的表面能量,从而确保结构粘结剂能够充分润湿基材表面,这对于实现坚固可靠且耐久的粘接是至关重要的。下面,将介绍三种常用的表面处理方法。
1) 溶剂擦拭法。
这是最简单的表面处理方式,能够去除粘接表面的蜡质、油污和其他小分子量的污染物。这项技术要求污染物可溶于溶剂,且溶剂本身不含溶解的污染物。为此,对溶剂的选择就显得非常重要。一般,常用的溶剂包括:丙酮、丁酮、甲基异丁基酮、二甲苯、三氯乙烯、乙醇和异丙醇等,在擦拭中应注意使用清洁的无尘擦布或纸巾。但这种表面处理方法的缺点是:溶剂可能会对基材产生不良影响,如热塑性复合材料可能会被溶解,显现出应力裂纹或龟裂;可能会造成交叉污染,如样品与样品之间的污染、重复使用或浸入到溶剂中的擦布的污染等;产生的蒸汽可能会危害工人的健康;不适用于大规模的生产要求(大规模的工业生产可选用蒸汽脱脂和超声波蒸汽脱脂的方法)。
2)打磨法。
打磨可去除表面污染物,并获得高度毛化的表面,从而增加结构粘接剂的粘接接触面,以产生“咬合效应”。常用的打磨方法包括:采用钢丝刷、砂纸或锉削等的手工打磨;采用砂带、砂轮或喷丸/喷砂等的自动打磨;以及相对较快,对操作者依赖性低且重复性和成本效益均较好的机械打磨等。
3)火焰处理法。
火焰处理是利用气体或气体/氧气火焰,对表面进行部分氧化,以产生极性基,从而提高聚合物的表面能。此技术所处理的基材厚度较采用电晕预处理的基材厚度大,尤其适用于不均匀的热塑性复合材料制品。其优点是:气体与氧气的比例、流量、暴露时间和火焰与基材的距离易于调节,已被证实是适用于聚丙烯类复合材料的较有效的方法。
汽车复合材料粘接前的表面处理除了以上介绍三种常用的表面处理方法外,还有一些相对先进和准对特殊粘接要求的复杂的表面处理技术,如等离子体处理 电晕放电处理 化学处理等。但无论采用那种表面处理方法,关键是要求有清洁的粘接表面和确保粘结剂能够充分润湿基材,这是我们应该严格加以关注的。
4、汽车复合材料粘接接头的设计
汽车复合材料粘结剂粘接连接固定方法除了粘结剂的选择与配制以及粘接表面处理是很关键的步骤外,粘接接头的设计好坏同样将直接影响到粘接性能和强度。汽车复合材料粘接接头设计的一般原则是:保证粘接面上应力分布均匀;将应力减少到最小限度,使之纯粹受拉力和剪切力;尽可能扩大粘接面积等。汽车复合材料粘接接头的结构设计形式也是多种多样的,根据被粘物形状可分为平面搭接、角形搭接、T形粘接和管、棒形粘接等形式;根据材料的粘接方式又可分为对接、搭接、插接、对切双搭接等等。从接头形式看,一般认为插接结构比较理想,其次是搭接和斜搭接。但在实际应用中,主要根据被粘接制品的结构和需粘接的部位而具体确定。
汽车复合材料的维修
传统意义上的汽车碰撞维修,只是简单将碰撞受损变形的车身固定后,用加热、机械拉伸的方式进行维修,然后再靠榔头等简单工具调整和修复车身钢板、车门和立柱等的间隙和形状,最后靠腻子、原子灰以及修补漆恢复原貌。对于钢板车身的碰撞维修我们都已驾轻就熟了,但随着汽车复合材料在汽车车身上应用的日益广泛,汽车复合材料车身碰撞受损后的维护修复却开始成为汽车行业新的困惑,汽车复合材料碰撞受损后究竟能不能修复?如果可以的话,怎么进行修复?经过修复后的车身能否恢复到受损前的状态?这些问题的答案是明确的:目前在汽车上所使用的复合材料部件都是可以修补的,而且完全能达到受损前的状态。之所以会得出这样的结论,是因为在过去的若干年中,维修汽车复合材料所用的粘结剂等产品得到了很大的改进,维修的工艺技术也已日臻成熟,从某种程度上讲,汽车复合材料的维修工序要比钢板材料更加简便和易于操作。
汽车复合材料部件是否需要进行修复主要取决于碰撞的程度,汽车复合材料发生碰撞一般会有三种状况:一是轻微的撞击,由于汽车复合材料本身具有良好的抗撞击性能,如能经受普通手推车的撞击而不会产生凹陷,也不会损坏,因此这种状况不需要维修;二是猛烈的撞击,汽车复合材料严重受损,通常建议更换部件而不作维修,因为维修成夲将会大于更换部件的成夲;三是虽经碰撞而受损不严重,在经济上值得维修,这类汽车复合材料是夲节关注的重点。
目前大多数维修部门已经掌握手工铺层玻璃纤维增强塑料的维修技术,而对复合材料在汽车车身面板方面使用最多的片状模塑料SMC部件的维修却缺乏认识,仍采用传统维修手工铺层玻璃纤维增强塑料的方法,结果经常会产生维修失败的情况。这是由于SMC的化学组成成份和手工铺层玻璃纤维增强塑料是不相同的。维修SMC部件通常需要专用SMC材料制成的粘结剂,而SMC维修专用粘结剂的玻纤含量要与被维修SMC部件的玻纤含量基夲一致,这样才能使修补的部分与被修部件保持相对一致的热膨胀或收缩比率,否则的话,维修数周后会出现类似“牛眼”或“晕环”的形状,说明维修工作同样是失败的。另外,无论在维修过程中使用何种材料,都必须按照粘结剂生产商的指导说明正确地去操作,尤其要特别注意维修材料的固化时间。
汽车复合材料的回收
出于经济和环保的原因,在汽车行业中采用回收工艺已经有很长的历史。早期的汽车,如轿车、客车、卡车几乎全都使用了金属,回收的方法主要就是将废旧的金属部件熔化掉,以便于再次利用。
这种回收方法对于金属材料来说是相当理想的,通过熔融处理,金属部件可以成为新的材料。但遗憾的是,汽车复合材料却不能像金属材料这样进行回收,我们经常会被问及:汽车复合材料是否属于可回收的材料?如果属于可回收的材料,怎样才能方便地回收汽车复合材料?正如我们己经知道,汽车复合材料包括热固性汽车复合材料和热塑性汽车复合材料两大类,其中热塑性汽车复合材料可以通过再熔化回收利用已为大家所了解,持有疑问或为汽车行业专家颇感头痛的问题是热固性汽车复合材料能否进行回收和再利用?事实上热固性汽车复合材料同样属于可回收的材料,这在汽车复合材料应用最为发达的美国、欧洲等国家早己有定论,只是热固性汽车复合材料因为具有化学、热力学、机械稳定性较高的特点,一方面使它们成为汽车许多应用领域的首选材料,另一方面也存在着其回收有一定困难的客观事实。热固性汽车复合材料不像传统金属材料和热塑性汽车复合材料那样可以通过简单再熔化方式来回收,它们必须用不同的加工方法处理。
针对热固性汽车复合材料的处理和回收,人们通过不断的探索和实践已研发出多种回收处理技术方案,其中较为行业普遍接受的回收处理方法有下列三种:
1、 热解法。
热解法又称为化学回收处理方法,简单地讲,热解法是在无氧的环境中加热,将有机物质有控制地热分解成可回收的一种或多种物质的方法。热固性汽车复合材料热解处理的一般过程为:先将废旧的热固性汽车复合材料制品切割成50mm×50mm大小的碎块,用水蒸气蒸煮后,置于热解炉中处理。结果显示,热固性汽车复合材料在处理系统中很容易被蒸馏,苯乙烯-聚酯树脂基材料很快被挥发而转变为可燃气体和可燃油,并将有机物质完全从玻璃纤维和CaCO3中分离出来。经热解法处理我们得到了三种可回收的物质,即热解气、热解油及固体副产物。
2、 粉碎法
粉碎法又称为物理回收处理方法,是一种直接利用废旧热固性汽车复合材料而并不改变其化学性质的一种回收方法,也是目前最直接、最有效的方法。热固性汽车复合材料粉碎处理的一般过程为:先将废旧的热固性汽车复合材料切成50mm×20mm大小的碎块,并通过除铁处理,然后用锤磨机对碎块进一步粉碎,粉碎后的粉料通过二级气旋式分离器进行分级分理,粗料重回锤磨机再粉碎,粉料进入振动筛进行分级处理,将各种不同颗粒直径粉料分别贮存于相应的收集箱内,供各种不同应用场合再利用。粉碎法的效果较好,效率较高,实用性也强,可以制成大至9.5mm有用颗粒粗料,也可生产小至200目(60μm)或更细的粉状填料。
3、 焚烧法
焚烧法又称为能量回收法,是一种利用废旧热固性汽车复合材料作燃料进行焚烧,以获取能量的一种回收方法。热固性汽车复合材料焚烧处理的一般过程为:先将废旧的热固性汽车复合材料粉碎为粒径10mm大小的粉末,然后吹入水泥窑炉内,作为燃料燃烧,以能量的方式回收由于焚烧交联的聚酯产生的热能,而经煅烧的灰分能作为水泥原料使用。这种方法的特点是:把废旧热固性汽车复合材料一部分转化成能源,可以减小部分燃料用量,也减少了二氧化碳的排放,另外因窑炉内温度高,产生的有害气体极少,没有有害气体污染空气的问题;再由于经煅烧的灰分与水泥的化学成分相同,完全可以作为水泥原料使用。因此,焚烧法能把废旧热固性汽车复合材料通过焚烧将能源利用和材料回收结合起来一次性全部回收,具有很好的推广价值。
通过上述三种回收处理方法介绍,我们可以更加明确地知道汽车复合材料部件不仅是可以回收的,是一种可回收材料,而且在回收技术没有任何障碍。根据国外回收处理的经验,汽车复合材料存在的最大问题是回收后材料的最终使用以及成本方面的问题,这些问题需要我们今后认真去研究和关注。
结束语
复合材料在汽车中的应用已有五十五年的悠久历史,在世界范围内,复合材料被广泛地应用到汽车的车身内、外饰件以及部分半结构件和结构件,为汽车工业的轻量化做出了巨大的贡献,积累了丰富的设计、制造、应用方面的经验和大量的成功范例,这是汽车复合材料行业的骄傲,也是汽车工业引以为荣的成就。但是,我们应该清醒地认识到:尽管汽车复合材料具有很大的发展潜力,汽车复合材料行业需要展示这些复合材料产品的优点,以及和金属件相比所存在的优势,但这并不意味着复合材料在未来就一定或必然会替代金属材料。
可以预见的是:在近阶段,复合材料应用于汽车部分的数量将不断增加,但正如航空航天业那样,在汽车行业中复合材料同样不会也不可能完全替代金属材料。比较理想的一种情况就是,汽车设计师将同时采用复合材料和金属材料进行设计和生产制造,分别利用其最佳的性能特点,设计制造出真正性价比最佳的新一代汽车。但如果采用这种混合材料汽车的设计制造方法,我们必须要谨慎地考虑复合材料和金属材料的相容性问题,另外一个必要的条件就是需要具备产品设计、模拟和生产方面的软件。希望有一天,汽车工业能像制造波音787飞机一样,50%采用复合材料,这将对世界汽车能源、环保、安全、舒适性产生何等重大的影响啊!我们期待这一天,我们为这一天的早日到来而努力!
更多关于材料方面、材料腐蚀控制、材料科普等方面的国内外最新动态,我们网站会不断更新。希望大家一直关注中国腐蚀与防护网http://www.ecorr.org
责任编辑:庞雪洁
投稿联系:编辑部
电话:010-62313558-806
中国腐蚀与防护网官方 QQ群:140808414
免责声明:本网站所转载的文字、图片与视频资料版权归原创作者所有,如果涉及侵权,请第一时间联系本网删除。
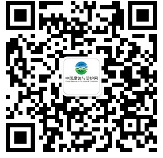
官方微信
《中国腐蚀与防护网电子期刊》征订启事
- 投稿联系:编辑部
- 电话:010-62316606-806
- 邮箱:fsfhzy666@163.com
- 中国腐蚀与防护网官方QQ群:140808414