目前我国各大钢铁企业的煤气管道一般采用钢管和铸铁管,由于煤气的成分复杂多样,内含多种杂质,再加上设计、施工等方面的诸多不合理因素,煤气管道内壁很容易被腐蚀。另由于煤气具有易燃、易爆、剧毒等方面的有害特性,被腐蚀的煤气管道可能带来的危害性很大。腐蚀严重时会导致管道穿孔、开裂而使煤气泄漏,造成火灾、爆炸以及人身中毒、伤亡等恶性事故,因此研究煤气管道内壁的腐蚀及防护具有十分重要的意义。
一、煤气的组成
1.煤气的主要成分
各种煤气成分如表1所示,其中焦炉煤气的可燃成分种类较多,除H2和CH4外,还有少量的CO和CmHn,热值较其他两种煤气也大很多,而高炉煤气和转炉煤气的主要可燃成分均为CO,转炉煤气中CO含量较高,因此其毒性在三种煤气中也最大。
2.煤气的主要杂质
煤气除上述主要成分外,还含有多种杂质,各种杂质的存在也是煤气管道腐蚀的最主要原因。焦炉煤气中杂质种类最多,一般含有焦油、灰尘、萘、氨、硫化氢、苯类、氰化氢等,其中硫化氢对管道的腐蚀危害最大,各大钢铁企业的焦化厂虽然设有多种脱硫设备,但由于技术手段的限制,煤气中硫化氢的含量仍然相对较高,较好的企业能够达到200 mg/m3的水平,普通的企业仅为400~1000mg/m3,甚至更高。
高炉煤气中的杂质主要为灰尘,还有少量的氯化物和硫酸盐、碳酸盐。近年来随着高炉煤气干法除尘设施的推广和应用,与传统的湿法除尘方式相比,不但用水量大大降低,高炉煤气中的含尘量得到了有效地控制,一般能够达到10~20mg/m3的水平。但高炉煤气干法除尘带来了新的腐蚀问题,煤气中氯化物在干法除尘中不能被去除,大量存在于高炉煤气中,一般能达到3000~5000mg/m3,若不及时处理,一旦氯化物融于凝结水中,不仅腐蚀碳钢材料的煤气管道,还能腐蚀普通不锈钢材料的波纹管补偿器,危害很大。转炉煤气中的主要杂质也为灰尘,还含有少量的硫酸盐、碳酸盐,对煤气管道的腐蚀主要表现为灰尘对管道内壁的冲刷,硫酸盐和碳酸盐为一般酸性腐蚀。
二、腐蚀分析
通过比较三种煤气的主要杂质成分,结合腐蚀机理,可以将煤气管道的腐蚀分为以下几种。
1.酸性化学腐蚀
煤气管道的酸性化学腐蚀是指煤气管道的内表面与酸性气体或电解质溶液接触发生化学作用而引起的腐蚀。煤气中的酸性物质在遇到冷凝水时溶解于水中发生电离,电离出H+,从而使冷凝水呈酸性[2]。其中焦炉煤气主要是硫化氢融于水后产生H+,而高炉和转炉煤气主要是氯化物、硫酸盐等强酸弱碱性的盐融于水后产生H+,H+的活泼性比铁强,发生下述化学反应,造成管道腐蚀:2H++Fe 2Fe++ H2。煤气管道在发生化学腐蚀后,破坏了管道表面的原有保护膜,杂质渗入铁晶体内部,从而形成原电池,进而发生电化学腐蚀。
2.电化学腐蚀
金属电化学腐蚀是由于金属与其他杂质之间存在电位差,在有电解质溶液的情况下形成原电池而发生的金属腐蚀,煤气管道材质一般是碳钢,碳钢主要是由铁素体和渗碳体两种组织构成的机械混合物[3]。管道接触同一电解质溶液--冷凝水,由于金属本身存在着电化学的不均匀性,即在金属表面或内部的不同区域具有不同的电极电位,它们与铁元素组成许多对电极,当杂质电极电位高于铁的电极电位时就会发生腐蚀反应。其主要过程可简单表示为:在阳极区,铁溶解变成铁离子进入电解质溶液(凝结水)中并产生电子,而在阴极区,阳极区产生的电子被电解质溶液(凝结水)中能吸收电子的物质(离子或分子)所接受。当阳极反应与阴极反应等速进行时,腐蚀电流就不断从阴极区流经电解质溶液(凝结水)进入阳极区,在阳极区产生Fe(OH)2。
因有少量的氧存在,Fe(OH)2会继续反应,生成Fe(OH)3。由于氢氧化铁在水中的溶解度低于氢氧化亚铁,在管道上沉淀析出,开始时是非晶态,并在管壁表面形成多孔的结合较差的腐蚀产物。该腐蚀产物对管壁并无保护作用,相反起着传递铁离子和氧的作用,使腐蚀继续蔓延,腐蚀产物与氢氰酸发生络合生成六氰合铁,进一步加速了管壁的腐蚀[4]。
3.磨损与应力腐蚀
煤气中一般含有一定浓度的灰尘和其他固体杂质,灰尘等杂质随煤气在管道内部流动时,将会对煤气管道内壁形成冲刷和磨损,固体杂质含量越大,煤气流动速度越快,对管道的冲刷和磨损越严重。 管道在焊接制作和安装过程中产生的残余内应力,或者是管道在使用过程中所承受的各种应力,使金属晶格歪扭,从而降低了应力部分的金属电极电位,使它变成腐蚀电池阳极,形成裂纹。
三、应对措施 根据引起煤气管道腐蚀的原因,可采取以下措施进行预防和应对:
(1)防止煤气管道内壁腐蚀的根本措施是将煤气净化,增加脱硫、喷碱、脱水等设施对煤气进行处理,使煤气中的各种杂质成分如灰尘、硫化氢、氨、氯化物、硫酸盐、氧和其他腐蚀性物质的含量达到允许值以下。 针对经干法除尘后的高炉煤气冷凝水中氯离子含量较高的问题,新设计的高炉煤气管道中会增设喷碱液(氢氧化钠溶液或氨水)及脱水塔等设施,将高炉煤气中的含氯离子较多的酸性水溶液中和后脱除,能够有效地防止管道内壁酸性化学腐蚀。如新建设投产的首钢京唐钢铁公司,在高炉煤气管道的低压段设有喷碱脱水塔,喷碱脱水前高炉煤气冷凝水的PH值约2.5~4.5,氯离子含量约2000~3000mg/L,喷碱脱水后高炉煤气的PH值约6~9,氯离子含量约300mg/L。通过一年的运行效果看,喷碱前未做好内防腐的高炉煤气管道腐蚀严重,仅运行四个月就出现了漏气现象,而喷碱后的高炉煤气管道未出现过漏气。
(2)工艺设计时选择合适的煤气流速、温度、管道坡度等,同时在运行过程中加强对煤气管道进行排水或保证连续排水,以减少煤气输送过程中杂质的沉积和水蒸汽的冷凝。 目前绝大多数煤气管道均设有能够实现连续排水功能的设施,通过使用排水器或加强人工定期排水,不仅使煤气中的冷凝水及时排出,也使煤气中的杂质,如焦油、萘、灰尘等随冷凝水一同排出,最大限度地减少了腐蚀媒介的存在,有效地保护了煤气管道的内壁。
(3)根据煤气中主要腐蚀性杂质的成分及含量,在煤气管道内壁涂敷合适的防腐层,以隔绝铁基体与腐蚀介质的接触。 对煤气管道内壁涂敷防腐层已经成为钢铁企业有效防止管道腐蚀的普遍做好,尤其是对于高炉煤气管道,内防腐涂层对管道的运行寿命至关重要。目前钢铁企业都根据高炉矿料的成分采用了有针对性的防腐方案,但一般均为除锈+底漆+防腐涂层+面漆的方案,并且根据需要改变防腐涂层的材料和厚度。一种比较流行的方案为:管道内壁除锈达到Sa2.5级后,涂乙烯基树脂用底漆1道,干膜厚度100 μm,乙烯基树脂玻璃鳞片胶泥2道,干膜厚度1000 μm,(管道下部1/3部分加厚至1060 μm),涂乙烯基树脂用面漆1道,干膜厚度100 μm。
(4)在管道制作中,对焊接后变形或加工后的物件进行消除内应力的处理,防止应力腐蚀,最有效的方法是进行热处理。
(5)对于已经投入运行的煤气管道,应加强对煤气管道壁厚的监测,定期进行壁厚测量,对于因煤气腐蚀而造成的管道泄漏,应及早发现,及时处理,并可采取带压堵漏[5]的方法进行补救,主要施工工艺为: 表面除污除锈→漏点止漏→加固增强→外部防腐
责任编辑:曾祥伟
《中国腐蚀与防护网电子期刊》征订启事
投稿联系:编辑部
电话:010-82387968
邮箱:ecorr_org@163.com
中国腐蚀与防护网官方 QQ群:140808414
注:本稿为中国腐蚀与防护网版权所有,未经允许, 严禁用于商业用途。转载时请务必以超链接形式标明文章原始出处和作者信息及本版权声明。
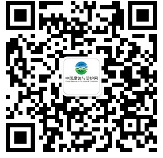
官方微信
《中国腐蚀与防护网电子期刊》征订启事
- 投稿联系:编辑部
- 电话:010-62313558-806
- 邮箱:fsfhzy666@163.com
- 中国腐蚀与防护网官方QQ群:140808414