▏节选自《中国材料科学2035发展战略》
第三篇 无机非金属材料学科
第十章 新型无机非金属材料
第七节 高性能结构材料
一、发展现状
高性能结构材料,包括C/C复合材料、超高温陶瓷、陶瓷基复合材料、超硬材料、陶瓷涂层等,是航空、航天等领域极端环境应用不可或缺的战略性材料。以下将详细梳理各方向发展现状。
(一) C/C复合材料
自问世以来,C/C复合材料因具有优异的高温性能,被欧美视为最具前景的高性能结构材料,其制备技术至今仍被发达国家严密封锁。我国经40余年自主发展,已形成较完善的C/C复合材料研发与产业化力量。近年来,国内C/C复合材料的发展为先进空天飞行器、大功率核反应堆、光伏发电等研制与市场扩容提供了重要保障,在国防与民用领域发挥了不可或缺的作用,其重要性表现在以下几个方面。
(1) C/C复合材料具有轻质、耐高温、抗烧蚀等特性,可极大提升固体火箭发动机比冲、增加火箭射程、提高打击精度,是最理想的固体火箭发动机喉衬、扩张段材料。近年来,国内自主发展了超高压/等静压浸渍碳化、热梯度化学气相渗透(chemical vapor infiltration,CVI)、压差化学气相渗透、醇烃混合裂解化学气相渗透及组合式致密化工艺等,推动了其在国防领域的规模化应用。同时,C/C复合材料成本的降低有力推动了光伏多晶硅制造热场系统等民用市场的发展,贡献了超过100亿元/年的市场容量。
(2) 长时抗氧化/烧蚀C/C复合材料是高推重比航空发动机、高超声速热防护系统研制的重要候选材料。国内创新发展了双温区化学气相沉积、超声速等离子喷涂、高温原位反应等多种长寿命抗氧化方法,形成了多相镶嵌、纳米线增韧、多层交替、梯度复合等超高温陶瓷抗氧化涂层体系。研制的抗氧化涂层在1500~1600℃静态空气下抗氧化寿命达到1000小时;在1600℃燃气风洞冲刷环境下抗氧化寿命超过300小时。研制的长寿命抗氧化C/C复合材料已在新型航空发动机中心锥、冲压发动机热防护衬板、唇口前缘试验件等多个国防重点项目中验证应用。
(3) 热解碳织构可控沉积是制备高性能C/C复合材料的前提,也是研制航空制动系统和高效散热部件的关键。我国自主提出了引入氧原子消除微晶缺陷、诱导高织构热解碳形成的思路,发明了烃醇微氧化组织优化技术,突破了传统烃类沉积难以实现热解碳织构精细调控的难题,为提高国产C/C复合材料摩擦磨损和力学性能、提升国际竞争力提供了重要思路。
当前C/C复合材料研究主要存在以下不足之处。
(1) 制备周期长、热解碳沉积控制难,导致不同批次材料的性能波动较大,难以建立性能预测模型。
(2) 极端环境下C/C复合材料服役过程的物理化学转变机制不明确,在热-力-氧耦合环境下的失效机理尚未探明。
(3) 材料服役环境考核平台缺乏,标准不统一,难以满足服役环境的极端性和复杂性测试要求。
(二) 超高温陶瓷
超高温陶瓷背后所蕴含的重大科学问题已经成为制约下一代高推重比航空发动机和空天飞行器热防护部件、先进核能系统研发的关键技术难题。一旦实现超高温陶瓷在战略装备中的工程化应用,将会显著提升现有材料科学技术水平及航空航天装备能力。以二硼化锆(ZrB2)、二硼化铪(HfB2)、碳化锆(ZrC)和碳化铪(HfC)等为代表的超高温陶瓷由于具有极高的熔点和优异的耐冲刷抗氧化烧蚀性能,能够在2000℃以上的强氧化高气流环境中长时间使用,并维持非烧蚀和结构完整,是高超声速飞行器鼻锥/前缘/翼舵、超燃冲压发动机燃烧室、发动机喷管喉衬等关键结构的重要或首要候选材料。此外,超高温陶瓷在第四代核反应堆中也有广泛的应用前景,如惰性基体燃料、燃料包壳、热交换器、聚变堆第一壁材料等。
我国制备的超高温陶瓷在室温/高温力学性能、抗氧化烧蚀性能等方面已经达到或超过国际上最新公开报道的数据,并通过了大量地面模拟环境考核试验和飞行演示验证试验。与此同时,计算材料学在超高温陶瓷领域发展迅速,研究者采用第一性原理计算、分子动力学、蒙特卡罗模拟、相场理论、机器学习、有限元模拟等多尺度手段预测了多种超高温陶瓷的基本性质、热力学稳定性、稳定晶体结构、弹性常数,以及高温应力下的变形、断裂等力-热响应机制。
当前超高温陶瓷研究主要存在以下不足之处。
(1) 超高温陶瓷潜在的工作条件是强热流、高应力、剧烈氧化烧蚀等极端苛刻环境多场耦合的复杂工况,然而目前材料的测试环境与真实情况有较大差距,难以精准指导材料设计,如何快速、低成本获得真实或近真实环境下材料关键数据是亟须解决的问题。
(2) 超高温陶瓷研究人员与机构比较分散,试验数据缺乏系统性整合,计算材料学与材料高通量制备相结合的研究模式开展时间较短,尚未形成具有指导意义的超高温陶瓷基因组技术体系。
(三) 陶瓷基复合材料
根据基体差异,陶瓷基复合材料大致可以分为SiC陶瓷基复合材料(C/SiC、SiC/SiC)、超高温陶瓷基复合材料(C/HfC、C/ZrC-ZrB2等)及氧化物陶瓷基复合材料(Al2O3/Al2O3、Al2O3/Al2O3-SiO2等)。不同基体的陶瓷基复合材料特性不同,适用于不同的服役环境。与美国、日本等发达国家相比,我国陶瓷基复合材料的研究和应用起步较晚,具有巨大的发展潜力。
(1) SiC陶瓷基复合材料:SiC陶瓷基复合材料是目前应用最广泛的陶瓷基复合材料。近年来,我国在C/SiC的研发和应用方面取得重大进展,C/SiC空间发动机喷管、高分辨率空间相机支撑结构、制动片等已成功应用于空间和交通运输等高科技领域。SiC/SiC作为新一代航空发动机热端结构和先进核能包壳管的重要候选材料,是未来一段时间陶瓷基复合材料的主要发展方向。
(2) 超高温陶瓷基复合材料:超高温陶瓷基复合材料是继C/SiC后高温结构材料领域的另一个研究热点,研究主要集中在组元设计、制备工艺及抗氧化烧蚀性能和机理等方面。我国属于最早开展超高温陶瓷基复合材料研究的国家之一,目前在超高温陶瓷基复合材料及构件关键制造技术与环境模拟技术方面已形成特色,并在一些国家重大工程中获得应用。
(3) 氧化物陶瓷基复合材料:受航空发动机热端部件应用需求牵引,以多孔莫来石为基体的氧化物陶瓷基复合材料日益受到重视,成为相关领域的重点发展方向。我国氧化物陶瓷基复合材料发展总体落后,目前处于材料发展的起步阶段,以基础研究为主,尚未形成自有的材料设计与制备技术体系,离应用仍有很大距离。
我国陶瓷基复合材料发展主要存在以下几个问题。
(1) 缺乏深入的基础理论研究,对关键技术涉及的基础科学问题理解不深,影响材料/构件的研发和应用。
(2) 高性能陶瓷纤维制备技术落后,高端纤维严重依赖进口,受制于人。
(四) 超硬材料
金刚石和立方氮化硼(cubic BN,cBN)是两种典型的超硬材料。天然金刚石是在6000多年前的古印度发现的,直到20世纪50年代,美国科学家才利用高温高压技术在实验室相继合成了人造金刚石和cBN。随后含黏结剂的聚晶金刚石和cBN、无黏结剂的纳米晶金刚石和cBN逐步被开发出来,并实现了工业化生产,推动了现代加工业的技术进步。我国金刚石和cBN的研发工作起步于20世纪60年代,生产的金刚石和cBN单晶颗粒占到全球市场的90%以上,现已成为超硬材料生产大国。然而与发达国家相比,我国在高性能超硬材料制品与工具的研发方面尚存在较大差距。近年来,我国自主研发了纳米孪晶结构金刚石和cBN,大幅提升了两种超硬材料的综合性能,为发展具有中国标签的高性能超硬材料提供了重要的历史机遇。此外,我国学者最新研发的非晶碳、非晶/金刚石自生复合材料、石墨—金刚石的杂交碳、类石墨—类金刚石结构的杂交BN等新型超硬材料具有半导体超硬、导电超硬/超强、极硬极韧等多种功能组合,将极大地拓展超硬材料的应用领域(图1)。
图1 超硬材料发展现状与方向
当前超硬材料研究还存在以下几个问题。
(1) 超硬材料中显微组织结构的精细调控及新型显微组织结构的设计和实现途径一直以来都是研究难点。
(2) 结构基元种类、分布、尺寸、含量及基元间的关联对材料性能的影响还不够清楚。
(3) 大尺寸无黏结剂超硬块材制备的科学原理和技术还需要完善和提升。
(五) 陶瓷涂层
为发展下一代大推力和高推重比航空发动机及高效率燃气轮机,需要进一步提升涡轮/透平入口温度,这给热端部件的承温能力及服役可靠性带来巨大挑战。一方面,在高温合金叶片表面涂敷耐高温陶瓷TBC可以显著提升服役温度与服役寿命。另一方面,SiC/SiC在航空发动机燃气环境中受到水氧腐蚀和低熔点氧化物腐蚀等侵伤造成性能迅速退化,必须在其表面涂敷EBC才能满足实际服役的苛刻要求。国际上已经发展了多代次的TBC及EBC材料,目前商用的陶瓷涂层可将稳定服役温度保持到1300℃。美国、德国、日本、韩国、中国的多个研究机构致力于发展TBC及EBC的新材料体系设计和先进制备技术,高效推动了陶瓷涂层在航空发动机及燃气轮机热端部件的实际应用。
近年来,国内多家科研单位开展了TBC及EBC的理论基础和应用基础研究,在涂层材料关键结构性能数据积累及耐水氧和CaO-MgO-Al2O3-SiO2(CMAS)腐蚀机制理解方面取得了一些成果。但综合分析,陶瓷涂层仍存在以下几个问题。
(1) 等离子喷涂用高质量粉体原料仍受国际技术禁运供应限制,迫切需要解决国产化问题。
(2) 涂层的制备技术和结构设计以跟踪国外报道为主,自主知识产权的创新能力较薄弱。
(3) 涂层在(近)服役环境中的评价测试和寿命预测方法尚需大量测试数据积累,陶瓷涂层产业尚属于初始研发阶段,离大规模产业化仍有距离。
(六) 高熵陶瓷
高熵陶瓷作为陶瓷界的新星,具有巨大的组分空间、独特的熵效应及性能可调控等优点,有望填补传统陶瓷发展的某些性能不足。自2015年“氧化物高熵陶瓷”概念被首次提出后,高熵陶瓷的研究受到国内外研究人员的广泛关注。目前,高熵陶瓷家族不断发展壮大,已由各种结构的氧化物高熵陶瓷发展到硼化物、碳化物、氮化物、硅化物等非氧化物高熵陶瓷体系,甚至扩展到多元阴离子高熵陶瓷体系等。然而,目前高熵陶瓷的研究尚处于起步阶段,大量的研究工作聚焦于概念推广、单相材料形成能力、制备方法、粉体原料合成及基本性能等方面。与传统陶瓷相比,高熵陶瓷表现出优异的力、热、电、磁、抗腐蚀、抗辐照性能等,在极端环境下展示出诱人的应用前景。
高熵陶瓷的成分复杂且研究体系庞大,这给研究带来了巨大的挑战。当前高熵陶瓷研究主要存在以下不足。
(1) 高熵陶瓷的性能挖掘不够充分。
(2) 高熵陶瓷的成分设计理论尚未建立,单相形成能力的判据尚未完善,成分和结构协同设计与调控研究尚需开展。
(3) 先进的计算、制备和表征方法与技术缺失,难以建立高熵陶瓷的组分—微结构—性能关联,高品质高熵陶瓷粉体原料的合成及高性能高熵陶瓷的开发尚未实现。
(七) 结构功能一体化陶瓷的增材制造
实际服役环境通常需求复杂异形陶瓷构件,这给其制造带来极大困难与挑战。传统的烧结—后加工、近净尺寸成形—烧结等技术已难以满足复杂异形陶瓷构件的高效率、高精度、低成本制造需求。增材制造技术的出现为复杂异形陶瓷构件的制造与应用提供了崭新的技术途径。同时,实际工程应用中结构材料正向结构功能一体化方向发展。结构陶瓷具有强度等结构承载性能的同时,还期待兼具轻量化、防热、隔热、抗冲击、电磁吸波、阻尼、零膨胀等一种或几种功能属性。因此,发展结构功能一体化陶瓷的增材制造技术,对于拓展结构陶瓷科学前沿、推进实际应用,具有重要科学意义与工程价值。
当前结构功能一体化陶瓷的增材制造研究主要存在以下不足。
(1) 传统结构陶瓷的设计方法已不适用,结构功能一体化陶瓷的增材制造面临复杂多物理场耦合环境,相应设计理论与方法不具备。
(2) 大尺寸复杂异形陶瓷增材制造工艺急需发展,形状/性能协同制造技术尚未建立,形状/ 性能协同机理尚未揭示。
(3) 增材制造的结构功能一体化陶瓷服役环境多物理场耦合复杂,表征评价方法缺乏,耦合机制与失效机理尚不明确。
二、发展态势
目前,高性能结构材料呈现如下发展态势。
新一代空天飞行器与核能装备急需超高温、低烧蚀/零烧蚀、长寿命抗氧化、高导热C/C复合材料。光伏电池、大飞机、高铁的快速发展对低成本、摩擦磨损性能优异的C/C复合材料提出规模化制备需求。强化C/C复合材料设计与制备技术上的源头创新,突破微结构的稳定化精细控制,实现结构多元化、功能复合化、产品多样化,是推动该方向快速发展的关键。
随着航空航天和先进核能系统对超高温陶瓷的需求日益迫切,未来将聚焦材料高通量制备与多尺度模拟相结合的研究模式,推动材料强韧化—抗氧化烧蚀—防/隔热承载一体化协同发展,逐步实现超高温陶瓷在宽温域(1800~3000℃)、长时间粒子冲刷、强氧化烧蚀等极端苛刻环境中的工程化应用。
随着航空航天和先进核能技术的发展,材料所处的服役环境越来越苛刻,对更长寿命、耐更高温度和结构功能一体化陶瓷基复合材料提出了新的需求。当前,陶瓷基复合材料发展的关键是高性能陶瓷纤维的开发和陶瓷基复合材料制备与应用所涉及基础科学问题的突破。
未来,超硬材料的基础理论将更加完善,其综合性能得到不断优化和提升,并涌现出系列具有优异光、电学性能的新型超硬材料。大尺寸高性能超硬材料的产业化将带来现代加工业、高压科学研究等领域的重大变革。
陶瓷涂层研制方兴未艾,需要建立陶瓷涂层材料及陶瓷涂层体系的关键力、热和腐蚀性能数据库,据此开展陶瓷涂层体系和结构的高通量设计与多层次构筑技术,指导其与基体构件的匹配性设计,开展服役性能评价、失效机理及精确寿命预测等研究。
目前,高熵陶瓷的研究处于起步阶段,未来将以国家重大需求为导向,聚焦高熵陶瓷的理论和基础研究,主要包括高熵陶瓷材料设计理论和单相形成能力判据的建立、新制备方法和技术的突破、高性能高熵陶瓷体系的开发及相关机制的揭示等方面,进而逐步推进高熵陶瓷的应用。
高超声速飞行器蒙皮、翼舵、端头等热端部件亟须发展使用兼具轻量化、承载等结构性能与防热、隔热、电磁吸波等多功能属性的结构功能一体化陶瓷;武器装备爆炸冲击防护结构亟须发展使用兼具轻量化等结构性能与抗冲击、隐身等多功能属性的结构功能一体化陶瓷。突破结构功能一体化陶瓷设计理论、增材制造工艺与表征评价方法,实现高性能结构材料的结构功能一体化,是推动该方向快速发展的关键。
三、发展思路与发展方向
高性能结构材料应重点发展以下方向。
(一) C/C复合材料
高强、高导热等特种碳纤维的低成本制备与异形预制体编织成形技术;基于可控多尺度强韧结构的高性能薄壁、尖锐C/C复合材料研究;超高温陶瓷与基体碳前驱体转化的普适性机理与协同作用机制研究;碳基体微结构宽域稳定控制与精细调控机理研究;基于多组元陶瓷相或难熔金属相基体改性与表面涂层一体化的长寿命抗氧化/烧蚀研究;大尺寸异形构件的整体成形与变形控制研究;基于微纳功能基元的C/C复合材料多功能一体化研究(图2)。
图2 C/C 复合材料发展态势与主要方向
(二) 超高温陶瓷
系统性开展超高温陶瓷筛选、组分设计优化与性能预测工作,发展宽温域超高温陶瓷的制备与结构控制技术,开发高强韧—抗氧化烧蚀—防/ 隔热承载等结构功能一体化新型超高温陶瓷,建立超高温陶瓷基因工程;开展服役环境或近服役环境下超高温陶瓷的失效损伤机制研究,聚焦大尺寸复杂形状陶瓷精密部件的高效制备技术,逐步实现超高温陶瓷技术从基础研究阶段到工程化应用阶段的过渡。
(三) 陶瓷基复合材料
关键原材料(特别是高性能SiC纤维和Al2O3纤维)批量化、稳定生产技术能力;航空发动机用SiC/SiC热端结构材料、先进核能用SiC/SiC包壳材料和极端服役环境用超高温陶瓷基复合材料及构件的低成本、规模化制造技术。
(四) 超硬材料
通过超硬材料显微组织结构的调控,发展纳米晶、纳米孪晶、非晶和自生复合等系列新型和高性能超硬材料;通过合成工艺优化,发展厘米级无黏结剂超硬块材的制备技术,催生高性能超硬材料新兴产业;通过激光成形和热化学抛光技术,发展原创的先进工具及变革性加工技术,实现其在功能晶体、有色金属、高硬度陶瓷等切削加工中的应用;研发新型超硬材料对顶砧,突破静高压研究的技术瓶颈,将人类在高压下探索新材料、新现象、新效应和新反应的压力条件推至500吉帕以上。
(五) 陶瓷涂层
复杂成分与多相涂层的成分及多层次结构高通量设计;热障/环境障一体化构筑设计;电磁波和红外发射调制功能设计;涂层结构与性能的多尺度模拟技术和寿命预测方法;陶瓷涂层模拟力、热、化耦合服役环境性能测试平台;陶瓷涂层数据库和材料信息学优化设计方法。
(六) 高熵陶瓷
高熵陶瓷的设计依据或理论判据研究;高纯、超细、成分均匀等高品质粉体的开发与低成本制备技术;高性能高熵陶瓷的成分和结构设计与调控及性能提升机理研究;基于高熵陶瓷概念拓展的高熵陶瓷涂层、高熵陶瓷纤维、高熵陶瓷基复合材料等新型高熵陶瓷研究;基于成分与结构基元的高熵陶瓷多功能一体化研究。
(七) 基于增材制造的结构功能一体化陶瓷
基于增材制造的结构功能一体化设计理论研究;适用于增材制造的专用结构陶瓷原料制备方法研究;陶瓷高效精密智能化增材制造装备研发;大尺寸复杂异形陶瓷形状/性能协同增材制造工艺研究;增材制造陶瓷的致密化与强韧化机理研究;结构功能一体化陶瓷多物理场耦合机制与表征评价方法研究。
四、至2035年预期的重大突破与挑战
到2035年,高性能结构材料有望在以下几个方面获得突破。
(1) 重点突破1700℃以上长寿命抗氧化与2000~2300℃长时抗烧蚀C/C复合材料制备技术,满足航空航天、核能等领域国家重大工程对关键热结构材料的需求,同时发展高导热、稳态摩擦磨损等高品质C/C复合材料低成本制备技术,满足光伏电池、高铁等民品市场应用。
(2) 发展超高温陶瓷多尺度、多维度、原位强韧化—宽温域下结构功能一体化的协同设计依据与调控机制,突破极端温度、极端气氛、极端速度/载荷、极端辐照、特种腐蚀环境等多物理场交叉耦合条件下材料优化设计、组织性能调控、使役性能协同与损伤机理研究,颠覆现有超高温陶瓷合成制备技术和极端环境服役极限。
(3) 突破关键原材料(高性能SiC纤维和Al2O3纤维)、陶瓷基复合材料及其构件制备核心技术瓶颈,研制满足航空发动机、先进核能和新型飞行器等领域应用需求的关键陶瓷基复合材料及构件。
(4) 突破已建立的超硬材料力学传统理论,发现逼近材料性能上限的变革性技术原理和途径,不断刷新共价材料硬度、韧性的纪录,同时发展导电超强、半导体超硬等新型超硬材料,极大地推动材料科学、高压物理学、地球科学、压缩科学及行星科学等学科领域的发展和进步。
(5) 突破陶瓷涂层的高通量设计和多层次构筑制备核心技术,满足新一代航空发动机、燃气轮机中多类热端部件的高温防护需求。
(6) 突破高强韧、耐蚀、抗辐照的高熵陶瓷关键科学问题,研制满足航空航天、核能等领域国家重大工程需求的关键高性能结构材料与装备,发展用于微电子、生物医学等结构功能一体化的高熵陶瓷及低成本和复杂构件制备方法。
(7) 突破基于增材制造的结构功能一体化陶瓷设计原理与方法,满足航空航天、兵器等领域重大工程对结构功能一体化陶瓷的需求。
免责声明:本网站所转载的文字、图片与视频资料版权归原创作者所有,如果涉及侵权,请第一时间联系本网删除。
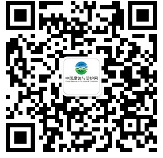
官方微信
《腐蚀与防护网电子期刊》征订启事
- 投稿联系:编辑部
- 电话:010-62316606
- 邮箱:fsfhzy666@163.com
- 腐蚀与防护网官方QQ群:140808414