近日,上海交通大学材料科学与工程学院王浩伟教授团队在增材制造复合材料疲劳与缺陷容限评价方面在International Journal of Fatigue期刊发表题为“Fatigue performance of laser powder bed fusion manufactured TiB2 / AlSi10Mg composite: Experimental investigation and fracture mechanics-based life prediction model for defect tolerance analysis (Int. J. Fatigue 2024, 180:108100)”学术论文。
该论文对比分析了激光粉末床熔融增材制造(LPBF)的纳米陶瓷颗粒增强的AlSi10Mg复合材料疲劳性能,根据断后分析结果提出了基于断裂力学的寿命预测方法,并结合CT扫描结果建立增材制造缺陷容限相关评价准则。
论文链接: https://www.sciencedirect.com/science/article/abs/pii/S0142112323006011
相比传统材料,增材制造(Additive Manufacturing)材料中的缺陷呈现出数量多、空间分布广、尺寸范围大的特点。现有研究表明即使通过工艺优化及后处理也无法做到完全消除。
快速制造拥有复杂几何特征的结构是增材制造技术的独特优势,但由于缺陷的存在且缺乏相关定量化的疲劳强度评定,一定程度上制约了增材制造技术在承受循环载荷零部件上的工程应用。为此通过断裂力学理论建立缺陷容限的设计评价准则,以回答增材制造过程中的缺陷在特定使用条件下是否可被“容忍”。
图1 论文图文摘要
上海交通大学材料科学与工程学院王浩伟教授团队的研究表明:
(1) PBF增材制造制备的TiB2/AlSi10Mg复材的疲劳性能在R=0.1室温条件下,其疲劳性能明显优于其他LPBF-AlSi10Mg合金以及SiC或WC/AlSi10Mg复材, 与文献报道的LPBF-AlSi10Mg合金相比,TiB2/AlSi10Mg复材的疲劳极限存在约50%的提升。
(2)提出了一种基于断裂力学的寿命预测方法,通过输入缺陷尺寸位置以及外加载荷等信息,可快速预测其疲劳寿命,精度可达。但绝大部分预测结果属于适度保守,具有一定工程意义。
(3)通过将达到疲劳极限的样品进行CT分析,进一步检验了寿命预测模型的准确性。同时结果表面内部缺陷的等效直径即使达到85μm也不引起破坏。而近表面缺陷等效直径仅为18~25μm也已经发生了微小裂纹扩展,但该裂纹并未在达到目标循环数之前引起全局失效,故这类缺陷是可以被“容忍”的。最后针对试样截面及载荷,提出依据空间的寿命分布图。
图2 3D渲染后的#1-F-28(, N cycle)的大缺陷:(a)大缺陷的位置; (b)(c)大缺陷的具体信息
图3 3D渲染后的#1-F-28(, N cycle)的缺陷:(a)(b)(d)(e)亚表面缺陷; (c)亚表面缺陷位置(为提升分辨率采取了局部放大)
免责声明:本网站所转载的文字、图片与视频资料版权归原创作者所有,如果涉及侵权,请第一时间联系本网删除。
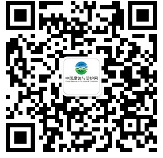
官方微信
《腐蚀与防护网电子期刊》征订启事
- 投稿联系:编辑部
- 电话:010-62316606
- 邮箱:fsfhzy666@163.com
- 腐蚀与防护网官方QQ群:140808414