应力腐蚀开裂(SCC)是材料在拉应力和腐蚀环境共同作用下发生的低应力脆性开裂,自1965年美国首次记录长输埋地管道发生SCC以来,加拿大、欧洲、俄罗斯、伊朗、巴西、阿根廷和巴基斯坦等国也相继发生了数百起由SCC导致的管道失效事故。SCC是近几十年来导致管道失效事故的重要原因之一,它已经成为威胁埋地管道安全运行的重要因素,是管道特别是老旧管道完整性管理的重点关注问题。
大量SCC现场调查分析结果表明,SCC通常发生在防腐蚀涂层破损和阴极保护失效的管体位置,在管体上通常表现为垂直于主应力方向的多条平行裂纹。按照其发生的环境和开裂路径,SCC可分为两种类型:高pH SCC和近中性pH SCC。
2001-2002年间,中国石油集团公司组织开展的SCC调查结果表明,四川油气管网、陕京管道和涩宁兰管道暂未发现SCC,但管道服役环境存在发生SCC的风险。近十几年来的大量室内试验研究结果表明,国内埋地长输管道具有发生SCC的可能性,然而国内埋地管道SCC事故鲜有报道。
SCC的孕育、萌生和前期扩展需要较长的时间,其风险随着管道运行年限的增加而增加,一般认为服役超过10年的非环氧类防腐蚀层管道具有发生SCC的风险,管道运行20年左右进入SCC高发期。国内长输管道经过近20年的快速建设和发展,在役管道里程接近14万公里,与SCC相关的管道防腐蚀层类型、管线运行参数、管道防腐蚀和检测管理方法都有了显著的变化、提高或改进。
但目前尚缺乏与长输埋地管道SCC风险状况相关的调查数据或资料,本工作在分析SCC相关历史调查和案例的基础上,结合近年来开展的埋地长输管道SCC现状调查结果(补口位置现场开挖检测,管道外腐蚀调查和环焊缝开挖检测结果),分析目前国内埋地长输管道发生SCC的原因,并探讨其未来的SCC风险和防控方法,为国内埋地长输管道的SCC防控管理提供参考和借鉴。
埋地管道SCC历史调查及案例分析
在国外相继发生多起由SCC导致的埋地管道开裂事故,加拿大能源管道协会(CEPA)于1996年首次颁布了SCC管理推荐做法的背景下,2001年中国石油集团公司组织了由中国石油大学、四川石油勘探设计研究院和石油管材所等多家单位参与的长输埋地管道SCC调查和敏感性试验评价。
该项目主要调查了19世纪60年代至90年代建设投产并采用石油沥青防腐蚀层的2600多公里的四川油气管网,分析了近40年来管道失效事故案例,结果没有发现由SCC导致的事故。历年来开展的169处现外腐蚀调查和21处SCC开挖检测结果表明,部分管道存在沥青防腐蚀层老化破损和腐蚀情况,但均未检测到SCC裂纹。调查期间发现有一起裂纹开裂事故,管道开裂处存在机械损伤和腐蚀产物,开裂原因可能是机械损伤导致管道在服役早期形成的近中性pH SCC。然而,四川油气管网、陕京一线、西气东输和涩宁兰管道的室内SCC敏感性试验研究结果表明,在国内中西部土壤环境中服役的管道具有发生SCC的可能性。
2011年运行9年的山东某天然气管道发生爆裂事故,事故原因为:爆裂起源于管道外表面机械划伤位置萌生的裂纹,机械划伤使涂层破损,阴保失效导致划伤底部发生腐蚀,划伤造成的局部应力集中和腐蚀过程共同作用导致SCC裂纹的萌生,管道运行过程中裂纹不断扩展最终导致了管道爆裂,裂纹的扩展路径为沿晶开裂+穿晶开裂的混合型开裂方式,氢对裂纹的扩展也起到了一定的作用,该管道SCC的萌生主要是由于机械损伤引起,为管道服役初期发生SCC的情况。
2016年某储气库管道经过11年服役后,在弯头位置发生开裂失效,开裂源于管道外表面形成的裂纹。失效原因分析结果表明:该管道弯管材料的硬度和强度参数不合格,热煨弯管工艺控制不当导致弯管表面组织变为硬度大且脆性敏感的马氏体和魏氏体;在管道埋设位置,地下水丰富,土壤电阻率低,环境腐蚀性强,服役过程中,弯管外部的热收缩带涂层破损剥离,管体表面与外部腐蚀环境接触;弯管位置的阴极保护电位在析氢电位以下,导致部分氢析出进入材料内部,在外部应力和氢的协同作用下,脆性相马氏体组织发生氢致开裂,形成初期裂纹;服役过程中储气库管道压力波动和温度变化产生低周疲劳导致裂纹不断扩展,最终管体因疲劳而开裂失效。材料不合格导致氢致开裂是该管道产生裂纹的初始原因,因此该管道的SCC并不是典型的一般意义上的埋地管道近中性pH或者高pH SCC。
上述SCC历史调查和仅有的两个埋地管道SCC案例分析结果表明,国内埋地长输管道发生SCC的案例很少,发生SCC的原因与管体机械损伤和材料质量有关,且都发生在管道服役初期,与典型的埋地管道SCC存在明显差别。目前,未发现国内埋地管道发生由典型的SCC导致的开裂事故。
埋地管道SCC现状调查
自2002年SCC调查以后,经过近20年的发展,国内长输埋地管道里程数量、运行工况和日常管理维护方式都发生了巨大变化,长输油气管道总里程超过14万公里,大口径、高钢级和高压力的天然气管道投运越来越多,在役管道外防腐蚀层90%以上为三层聚乙烯(3PE),定期开展的管道内外检测成为管道完整性管理的重要依据。
部分管道的运行年限超过20年,进入了埋地管道SCC的高发时期。为明确在役管道SCC风险现状,依据埋地管道SCC发生特点和直接评价标准,一方面选择了不同服役时间的管道SCC高风险位置进行现场开挖,开展裂纹检测和应力腐蚀相关参数的测试,明确所选择管段的SCC风险,另一方面整理分析近年来的外腐蚀调查和环焊缝排查工作的调查结果,分析外腐蚀位置和管道补口位置的SCC风险。
01 埋地管道补口位置现场开挖检测
本次开挖检测包括位于榆林和泰安的天然气管道和呼和浩特的原油管道,所开挖调查管道的服役时间分别为22年、8年和7年。共调查了8处位置。其中,6处管道的防腐蚀层为3PE防腐蚀层,补口采用热收缩带补口;1处管道的防腐蚀层为含聚氨酯泡沫的防腐蚀保温层;1处站内管道的防腐蚀层为聚丙烯冷缠带+环氧底漆。所开挖调查管道的基本信息如下:
A管道服役时间为22年,2018年内检测结果表明,补口位置发生了腐蚀,而2012年内检测结果表明补口位置没有明显腐蚀迹象。这说明随着服役时间的延长,该管段补口位置的腐蚀风险升高。补口位置通常会出现阴保屏蔽,所以该位置发生SCC的概率增大,且该管道服役时间超过了20年,达到了SCC的高发年限。因此,选择了5处典型的补口腐蚀位置进行开挖检测。其中,距离上游压气站20km内4处、存在交流干扰位置1处。
在B管道上选择了容易产生额外应力的石方区补口位置。
在C管道上选择了距离压缩机较近的管道出站焊缝位置,该处运行压力较大、温度高、壁厚变化容易导致应力集中。
在D管道上选择了发生阴极保护屏蔽、导致管道发生微生物腐蚀的补口位置。
考虑到腐蚀检测的需要、操作方便性和可视化效果,采用DPT-5型探伤渗透剂检测裂纹位置,并采集了部分腐蚀样品进行了物相分析。
A管道:补口位置的典型防腐蚀层和补口腐蚀形貌如图1a所示,腐蚀以均匀腐蚀为主,腐蚀产物为棕褐色铁锈,主要成分为Fe3O4和α-FeOOH,与大气腐蚀产物类似,表明补口位置的腐蚀主要是由埋设位置沙土中的湿气进入补口导致。打磨除锈后的裂纹渗透检测结果如图2a所示,仅在个别位置有很小的点蚀坑,点蚀深度在0.2mm左右,没有发现裂纹类缺陷。
B管道:补口位置典型防腐蚀层和腐蚀形貌如图1b所示,腐蚀产物为黄褐色浮锈,管道没有发生明显的点蚀。腐蚀产物的主要成分为α-FeOOH,部分为SiO2杂质,这表明该位置的腐蚀也主要是湿气进入补口导致的。打磨除锈后的裂纹渗透检测结果如图2b所示,没有发现点蚀或者裂纹类缺陷。
C管道:焊缝位置防腐蚀层形貌和腐蚀形貌如图1c所示,在聚丙烯冷缠带防腐蚀层底部存在翘边和脆化的现象,但内部红色底漆基本良好,没有明显的腐蚀迹象。打磨后的裂纹渗透检测结果如图2c所示,没有发现点蚀或者裂纹类缺陷。
D管道:补口位置的腐蚀形貌如图1d所示,腐蚀产物为灰黑色黏稠物质,管道存在明显的点蚀,且点蚀坑深度较大,达管道壁厚的70%。腐蚀产物的主要成分为FeCO3和FeS,是典型的厌氧环境硫酸盐还原菌腐蚀产物,同时腐蚀产物中还含有部分β-FeOOH,该物质主要在富含氯离子的环境中产生。这表明该环境中的氯离子加速了细菌腐蚀。打磨除锈后的裂纹渗透检测结果如图2d所示,除了较大的点蚀坑外,补口局部位置还存在深度1mm左右的点蚀坑,没有发现明显的裂纹类缺陷。
(a) A管道 (b) B管道
(c) C管道 (d) D管道
图1 不同调查点管道的防腐蚀层和腐蚀形貌
(a) A管道 (b) B管道
(c) C管道 (d) D管道
图2 不同调查点管道裂纹的渗透检测结果
上述现场调查结果表明,所调查管线的补口位置均未发生SCC现象。
02 管道外腐蚀开挖调查结果
收集分析了2015-2020期间开展的总共98处管道外腐蚀调查结果。现场调查检测均未发现管道表面有裂纹类缺陷,具体调查信息和结果如表1所示。其中管道防腐蚀层主要为3PE,防腐蚀层类型中的其他是指聚丙烯冷缠带或沥青。调查结果表明,在发生外腐蚀的管道中,阴保屏蔽或者保护不足的有62处,存在机械损伤的有33处,发生明显点蚀的有43处。阴保不足或屏蔽导致管道发生腐蚀是管道发生SCC的必要条件,机械损伤导致的应力集中可明显增大管道发生SCC的风险。而调查结果表明,在上述易发生SCC的管道位置均未发现SCC现象,这表明目前国内埋地长输管道SCC的风险较低。
表1 2015-2020管道外腐蚀调查结果
03 环焊缝排查检测结果
针对事故风险高的环焊缝补口位置,中石油自2018年起开展了环焊缝排查工作,将需要排查的环焊缝定位、开挖、去除补口防腐蚀层并打磨后,采用超声相控阵、超声衍射时差法、磁粉、渗透和X射线等无损检测技术,对焊缝位置的缺陷进行详细的检测,并对检测出的缺陷定性、定量、分级和评价。
目前,总共已完成3万多处环焊缝开挖检测工作,截至2019年底共发现了180多处裂纹类缺陷,但通过渗透或者磁粉检测发现的表面开口裂纹仅3处,且都是单一裂纹。其中,两处焊缝表面裂纹沿管道轴向扩展,焊缝位置没有腐蚀迹象:裂纹1位于管道的1点钟位置,长度7mm,裂纹2位于11点半位置,长度8 mm,裂纹形貌如图3所示。
(a) 裂纹1
(b) 裂纹2
图3 焊缝表面裂纹
由于焊缝表面没有腐蚀迹象,所以这两处裂纹主要由焊接和应力集中导致。另一处存在表面裂纹的补口位置有浮锈,射线检测时发现了3mm左右的裂纹,去除浮锈后再次进行渗透检测时,裂纹消失,这表明该处裂纹很浅。该处补口位置土壤较为干燥,补口热收缩套黏结力合格(大于80N/cm),腐蚀产物仅为一层浮锈,不存在明显的点蚀,发生腐蚀的风险低。且该位置管线运行压力为6.7MPa,壁厚17.5mm,管径1016mm,管道环向受力仅为194MPa,为管道屈服强度(485MPa)的40%,受力较低,因此该位置出现SCC的风险较低,该裂纹由焊接导致的可能性较大。
以上分析表明,环焊缝排查发现的裂纹多数为内部裂纹而非表面开口裂纹,仅有3处表面开口裂纹,其中两处裂纹位置不存在腐蚀,1处裂纹位置发生腐蚀和SCC的可能性很小,因此可判定这3处裂纹不是SCC导致的裂纹。环焊缝排查结果表明,现阶段国内管道补口位置发生SCC的风险较低。
原因分析
上述国内管道SCC相关调查结果表明,目前国内尚未发现典型的管道高pH或者近中性pH的SCC,SCC风险较低。国内外大量的现场调查和试验研究数据表明,管道SCC只有在应力、环境和材质3个因素的协同作用下才会发生,风险随着管道运行年限延长而增加,且SCC只可能在因涂层破损而发生腐蚀的位置发生。目前,国内管SCC风险较低的原因主要有以下几点:
01 国内在役管道外腐蚀风险低
通常采用防腐蚀涂层加阴极保护的方式抑制土壤对埋地长输管道的腐蚀,目前在使用的管道外防腐蚀层有沥青、煤焦油瓷漆、聚乙烯缠带、三层聚乙烯(3PE)和熔结环氧粉末(FBE)等。其中,3PE防腐蚀层由于其优良的绝缘性、耐腐蚀、抗渗透和耐破坏性能,自20世纪90年代引入国内后,在陕京管道、西气东输和中俄东线等重大管道工程中得到了广泛应用,成为国内长输埋地管道应用最多的外防腐蚀层,3PE防腐蚀层管道占长输埋地管道总里程的90%以上。同时,还有少部分管道采用了FBE防腐蚀层,其他类型防腐蚀层管道基本停用。FBE防腐蚀层与阴极保护兼容性很好,不会发生SCC,而3PE防腐蚀层管道存在由阴保屏蔽导致近中性pH SCC的风险。然而近年来的腐蚀调查结果表明,即便3PE防腐蚀层出现剥离,管体上暂未出现由大面积剥离失效导致的阴极保护屏蔽的情况。国内3PE防腐蚀层管道发生SCC的主要为补口、划伤、硌伤等容易产生阴保屏蔽、阴保不足或杂散电流干扰的位置。目前我国针对外腐蚀开展的外检测和针对管体缺陷开展的内检测频率较高,一般3~5年开展一次外检测和内检测,且每次检测后都制定了针对防腐蚀层和外腐蚀的开挖修复计划,并开展了专项的阴极保护问题或杂散电流干扰的治理工作,使得管道发生外腐蚀的风险明显降低,从而降低了SCC发生的风险。
02 管道服役时间较短
SCC的发生需要较长的裂纹萌生和孕育时间,国外统计资料表明,对于沥青、缠带和煤焦油瓷漆类等现场涂覆施工的管道,通常在管道运行20年左右进入SCC高发期。一方面,相对于其他防腐蚀层,3PE防腐蚀层的抗老化能力强,SCC裂纹的萌生和扩展需要的时间更长。另一方面,目前国内管道服役时间大多不满20年,大部分管道未进入SCC高发期。
03 管道运行压力相对较低
国外SCC案例分析表明,应力腐蚀通常发生在运行压力大于管线钢屈服强度60%的管段。国内大部分管道的设计压力管线钢屈服强度的60%~70%,但实际运行压力一般低于设计压力,主要输气管道运行压力如表2所示。可见,只有陕京一线和西一线的实际服役压力大于管线钢屈服强度的60%,此外国产管线钢的屈服强度一般高于标准要求,如X80管线钢屈服强度的实测值通常偏高,高于标准要求的555MPa,因此管道实际运行压力高于管材屈服强度60%以上的情况较少,管线钢不具有发生SCC所需的应力条件。
表2 国内主要输气管道运行压力
虽然目前国内3PE防腐蚀层管道发生SCC的风险较低,然而防腐蚀层的涂覆质量差别较大及施工过程中可能遭受的外力破坏等都可能使3PE防腐蚀层存在局部破损和较为严重的涂层剥离情况,另外其绝缘电阻高,容易屏蔽阴极保护电流,导致剥离涂层下管道发生腐蚀。此外,3PE防腐蚀层管道补口位置大多采用液态环氧加热收缩带的结构,投产后这种结构补口发生失效的比例较大,补口位置容易发生阴极保护屏蔽导致管道腐蚀。
调查结果表明,大量补口存在腐蚀迹象。室内试验结果表明,在阴保屏蔽的自腐蚀条件下,管线钢存在发生近中性pH SCC的可能性。随着服役年限的增加,3PE防腐蚀层管道存在较高的SCC风险。
结合国内管道服役现状,建议现阶段采取以下措施降低3PE防腐蚀层管道发生SCC的风险:
(1)继续加强外腐蚀控制,通过定期开展外检测和内检测,修复破损涂层,防止出现3PE防腐蚀层发生大面积剥离腐蚀的情况;
(2)根据埋设土壤环境,对在役的X70和X80钢级管道设定合适的阴极保护电位范围,避免发生析氢;
(3)在日常外腐蚀开挖检测工作中,重点关注防腐蚀补口、划伤、硌伤、凹陷、环境干湿交替和石方区等SCC高风险位置,并开展裂纹检测工作;
(4)对运行20年以上的管线开展SCC直接评价,建立SCC位置识别模型,积累SCC高风险位置识别经验;
(5)管道运行和启停输过程中,尽量减少压力波动范围、升降压速度和次数。
结束语
国内现有SCC案例分析和管道补口、环焊缝和外腐蚀开挖调查结果分析表明,国内尚未发现典型的埋地管道SCC案例,已发生的管道SCC主要与材料制造缺陷、焊接缺陷和机械损伤有关。目前,国内3PE防腐蚀层埋地管道外腐蚀控制较好,服役时间较短和服役压力较低,因此管道发生SCC的风险较低。但国内3PE防腐蚀层管道存在较多的剥离和补口失效问题,易产生阴极保护屏蔽导致管道腐蚀,随着服役时间的延长,管道存在发生近中性pH SCC的风险。建议通过加强外腐蚀控制,防止高强钢阴极析氢导致的氢脆,减少运行压力波动,开展针对性SCC调查和直接评价工作,降低SCC风险,保障管道的安全运行。
免责声明:本网站所转载的文字、图片与视频资料版权归原创作者所有,如果涉及侵权,请第一时间联系本网删除。
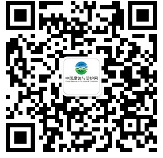
官方微信
《腐蚀与防护网电子期刊》征订启事
- 投稿联系:编辑部
- 电话:010-62316606-806
- 邮箱:fsfhzy666@163.com
- 腐蚀与防护网官方QQ群:140808414