1 前 言
近几年,随着油气长输管道的发展,现在全国在用长输管道约15 万公里[1],燃气泄漏引发的事故越来越多,为了保障长输管道的安全可靠运行,须对其进行定期检验。而在影响长输管道安全运行各因素中腐蚀是其第一要素,对天然气长输管道的内腐蚀检测方法常用的有管道内腐蚀内检测,但由于内腐蚀内检测费用较高,且对管道的设计和安装有一定的要求,全国大概只有70% 的管线可以实施管道在线内检测,剩下的管道只有通过管道内腐蚀外检测技术来发现内腐蚀缺陷[2]。本文研究的内腐蚀外检测技术在国内外实际检验中开展比较少,相应的标准和文献也较少[3],但现在很多企业迫切希望能够开展该项检验技术,防止管道因内腐蚀产生安全隐患。本文详细介绍了管道内腐蚀外检测的原理和在实际检验中的应用。
2 管道内腐蚀外检测原理
管道内腐蚀外检测技术原理是通过流动力学模型计算结果来识别管道中潜在积水或者杂质的位置,预测各检测区段可能发生内腐蚀的位置,然后通过对这些位置进行开挖检测,在管道外部通过超声波测厚仪等仪器来发现管道内腐蚀位置及判断其严重程度。内腐蚀外检测技术主要包括了检测区域的划分、临界倾角的计算、管道实际倾角计算以及内腐蚀位置识别和开挖验证等工作,其中管道的临界角和实际倾角的计算是该项技术的难点。首先管道临界倾角的计算可采用流动力学模型来计算,对于输气管道可用式(1)来计算临界倾角
其次在现场可利用管道探管仪对管道走向、位置与地形的信息采集如图1,可确定管道各分段各的水平间距ΔL,各分段高程之间的高程差ΔH,通过式(2)能够精确的计算出管道的实际倾角。
图1 探测管道埋深和收集高程值
在临界倾角和实际倾角计算出来后,当实际倾角θa> 临界倾角θc 时如图2 所示,管道顺气流开始上波段易积液而产生内腐蚀,可对这些易积液的位置进行开挖验证,从而发现管道内腐蚀的位置以及腐蚀程度。
图2 倾角比较图
3 管道内腐蚀外检测技术在检验中的应用
某燃气公司位于分输站与门站之间的长输管道长约2 公里,因建设初期未设置收发球系统,导致无法做管道内检测,因此对其进行管道内腐蚀外检测。其规格为DN406*7.9mm,设计压力7.5Mpa,运行时最低操作压力4.0Mpa,平均温度16℃,最大流量418kNm³/h,管道东西敷设,气体只能单一方向输送,管道沿途为山地丘陵地表环境。
(1)管道临界倾角的计算
根据式(1)计算临界倾角,参数选择最低操作压力P=4.0Mpa,介质操作温度T=16℃,最大流量Q=418kNm³/h,液体密度ρ1=1g/cm³、气体分子量M= 取甲烷分子量16g/mol、重力加速度g=9.81m/s²,理想标准气体常数R=8.314Pa.m³/(K.mol),气体压缩因子Z=0.83。
(2)现场数据采集与管道的分段
在实际检验中可以通过管道定位仪和GPS 仪器收集管道沿线的实际埋深和实测高程[4],在收集资料中需顺着气流方向进行如图3 所示,同时根据管道沿线的敷设环境对管道进行分段,一般按150-200 米的距离进行分段计算实际倾角。由于管道每一处的埋深不一致,在全线管道数据采集完成后需对实测高程值进行修正,实际高程= 实测高程- 管道埋深如图4 所示。
图3 管道GPS 采集数据
图4 实测高程与实际高程图
(3)实际倾角的计算
通过对管道数据的采集获得各分段的管道敷设水平长度ΔL、实际高程ΔH 后,可通过式(2)计算出各分段的实际倾角θa,以下为实际倾角和临界倾角和实际高程的比较图:
(4)易发生内腐蚀开挖点的选择和验证
根据图5 分析可知,顺气流方向有1~3# 点的实际倾角大于临界倾角,此外根据地势选择4# 穿越铁路段进行开挖验证,下游方向选择最大倾角6# 开挖验证,每一处开挖点开挖范围约3m*2m,如图6 所示对开挖处的管道进行超声波检测,发现管道内腐蚀的位置和判断其腐蚀严重程度,验证结果如表1。
表1 开挖验证结果
从以上开挖检测数据可以看出利用管道内腐蚀外检测技术对管道内腐蚀缺陷的检出率非常高,也易判断管道内腐蚀严重程度。由于输气管道的管道内腐蚀主要是由积液或者杂散堆积造成的,腐蚀位置主要发生在管道底部,腐蚀形态为局部点腐,腐蚀速度相对较慢。
图5 实际倾角与临界倾角比较
图6 1# 开挖点现场照片
4 结束语
综上所述,通过长输管道内腐蚀外检测技术在实际检验中的应用,可知该项技术能在不能实施管道内检验的管道发现内腐蚀缺陷,且内腐蚀缺陷检出率和缺陷准确度都比较高。根据实际检验中的经验可知易发生内腐蚀位置的开挖点选择还应遵循几个原则:首先管道实际倾角大于临界倾角顺气流上坡方向点必选,该处发生内腐蚀几率最大;其次应考虑穿越铁路、地铁、河流等且实际倾角较大的管道,该处发生内腐蚀几率较大,且发生管道失效后果较大;再则管道上游部分的内腐蚀可能性大于管道下游部分。长输管道内腐蚀外检测技术作为一项可操作性强、可靠高的检测方法,值得大家推广。
参考文献
[1] 高叶雄. 我国油气长输管道技术现状及差距探究[J]. 化工管理,2016,(23).182-182.
[2] 杨涛,仇攀,陈少松,等. 天然气管道内检测金属损失缺陷数据分析及验证评价[J]. 天然气技术与经济.2020,(2).52~5.
[3] 王亮,胡月,漆勇. 天然气长输管道外腐蚀检测技术研究[J].能源研究与管理.2017,(3).12-13,22.
[4] 苏建国,龙媛媛,高峰,等. 油田埋地管道管体腐蚀不开挖检测技术现状与应用[J].中国特种设备安全,2008,024(10).42-43,70.
免责声明:本网站所转载的文字、图片与视频资料版权归原创作者所有,如果涉及侵权,请第一时间联系本网删除。
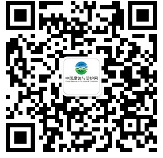
官方微信
《腐蚀与防护网电子期刊》征订启事
- 投稿联系:编辑部
- 电话:010-62316606-806
- 邮箱:fsfhzy666@163.com
- 腐蚀与防护网官方QQ群:140808414