1 腐蚀的危害
腐蚀是设备与构件的重要破坏形式之一,它与断裂、磨损一起构成了材料在使用过程中的三大重要破坏形式,常导致设备早期失效或意外事故,造成巨大损失。
腐蚀永远都是“正在进行时”,在热力学上,除了极少数贵金属(Au、Pt等)外,一般材料发生腐蚀都是一个自发过程。承压设备很少是由于单纯机械因素(如拉、压、冲击、疲劳、断裂和磨损等)或其他物理因素(如热能、光能等)引起破坏的。腐蚀的危害主要有4个方面:
① 经济和人员损失
凡是使用材料的地方,都存在不同形式和不同程度的腐蚀问题,每年腐蚀所造成的经济损失已超过火灾、水灾、地震和车祸损失的总和。经济损失包括直接损失和间接损失,直接损失指增加腐蚀裕度或耐蚀合金造成材料费用增加、采用防护技术的费用和发生腐蚀破坏以后的维修、更换费用和劳务费用等。每年由于腐蚀而报废的金属设备和材料相当于金属年产量的10%~40%,其中2/3可再生,而1/3的金属材料被腐蚀流失无法回收。间接损失指设备发生腐蚀破坏造成停工、停产;跑、冒、滴、漏造成物料流失;腐蚀使产品污染,质量下降,设备效率降低;因腐蚀产物沉积引起的热传递效率降低,或是因腐蚀产物阻塞而产生额外的压力降,造成装置能耗和水耗增加等。由于腐蚀意外事故而引起的停工、停产所造成的间接经济损失,可能超过直接经济损失的若干倍。
由于历史原因,我国在20世纪60~70年代制造的承压设备缺乏质量控制,形成严重的先天不足,有的存在着大量的超标缺陷,有的结构不合理,有的用材不当。在80年代初期,形成了压力容器爆炸事故的高峰期。据1987年的不完全统计,我国此前10年间发生的压力容器爆炸事故2254起,停产事故23起,因事故丧生1200人,直接经济损失4~5亿元,间接经济损失80~100亿元,万台压力容器年均爆炸事故率是世界发达国家的10倍以上。中国石化集团公司和中国石油天然气总公司先后4次对石化企业的压力容器和管道进行了调查,中石化所属企业1989年因腐蚀造成的经济损失估计约20亿左右。1990年至1995年35个石化企业容器失效原因,腐蚀失效占80%;Ⅱ、Ⅲ类压力容器报废原因中,腐蚀原因占65%;在炼油、化工等企业,腐蚀原因造成的非计划停车占40%以上,为非计划停车的主要因素。20世纪80年代和90年代我国压力容器失效原因见图1-1、1-2[1],1990年以前的压力容器,资料不全和材质不明占48.29%,设计和制造遗留的先天缺陷(包括结构不合理,错边量及棱角度超标,焊缝存在超标缺陷)占30.41%,使用中产生的缺陷占12.96%,因此压力容器失效主要是因设计和制造缺陷引起的。而90年代后,随着压力容器的管理制度的健全和设计、制造水平的提高,压力容器的使用寿命延长,操作条件越来越苛刻,暴露出的腐蚀的问题也越来越多,因此,腐蚀引起的问题明显增多,腐蚀导致的压力容器失效案例也越来越多。
近年来,由于设计人员和用户缺少丰富经验的腐蚀控制工程师,造成承压设备的设计和制造存在不满足腐蚀控制要求的情况,用户的管理和操作者对腐蚀控制的认识不足,也导致了较多的承压设备腐蚀失效案例。所以,承压设备的腐蚀已成为影响其工业装置长周期运行的主要因素和主要失效模式,对安全生产构成很大威胁。
图1-1 中国压力容器失效原因示意图
承压设备事故往往具有突发性、灾难性,引起爆炸、火灾、中毒和环境污染等,造成灾难性的恶果,不但造成重大经济和环境损失,还常常使人民生命财产受到重大损失。如应力腐蚀等往往造成压力容器的突发爆炸事故,造成重大人员和财产损失。2005年3月21日21时20分左右,平阴鲁西化工第三化肥厂有限公司发生尿素合成塔爆炸事故,共造成4人死亡,32人受伤,直接经济损失约780万元,其主要原因是尿塔发生了严重的应力腐蚀开裂。1979年12月18日14点7分,长春市煤气公司液化气站的102号400m3液化石油气球罐发生破裂,直接经济损失约627万元,死36人,重伤50人。
② 对安全和环境造成危害
腐蚀破裂造成“跑、冒、滴、漏”,既浪费资源、能源和污染环境,又是发生火灾爆炸事故的重要原因之一。材料在腐蚀介质作用下,因腐蚀导致壁厚减薄、开裂及材料组织结构改变使材料力学性能降低,造成设备因承载能力不足而发生的断裂,从而引发安全事故。世界范围内1960年至1990年30年石化行业发生的100起损失最大的事故主要引发原因统计分析结果显示,由于设备腐蚀和疲劳原因导致的失效占41%,排在首位,图1-2。国外因设备腐蚀造成的生产事故约占全部事故的50%以上。
图1-2 1960年至1990年30年石化行业发生的100起损失最大的事故主要引发原因
压力容器盛装的介质,常有不同程度的毒性和易燃易爆性,它们的泄漏都会带来严重的后果。而且有些环境污染还具有长效性,如核电站泄漏的铯、锶、钚等放射物元素对环境造成的污染,它们的半衰期分别为3万年、2.9万年和2.4万年,这意味着在长达几万年里,这些化学物质才能衰减至以前浓度的一半。某炼油厂因事故泄漏的原油渗入地下,20多年后污染了城市自来水。
材料与环境之间的相互作用,不仅局限于环境对材料的腐蚀作用,材料腐蚀对环境所造成的影响也不容忽视。腐蚀对环境的污染包括两个方面,一是因采取腐蚀控制措施而使用的涂层、化学药剂、牺牲阳极和其他材料等对环境产生的影响,二是因腐蚀泄漏增加了工业废水、废渣的排放置和处理难度,增多了直接进入大气、土壤、江河湖海中的有害物质,增加了能源消耗,造成了自然环境的污染,破坏了生态平衡,危害了人民健康,妨碍了国民经济的可持续发展。腐蚀引起的环境污染问题日益引起人们的关注,西方国家在1990年前已经开始关注材料腐蚀产物对环境(土壤和水系)的污染作用,并进行了系统的观测和研究,取得了大量的数据和研究成果,这些成果不仅对学科建设的发展起到了极大的促进作用,而且也成为他们制定社会发展政策的基础和依据。
③ 阻碍新技术发展
腐蚀引发的事故直接影响科学技术和生产的发展。一项新技术、新工艺、新产品的实现过程中,往往会遇到腐蚀问题,只有解决了这些棘手的腐蚀问题,这些新技术、新工艺、新产品才得以发展。比如,美国曾用30年时间研究熔盐原子能反应堆(1947-1976),但由于裂变产物对材料的腐蚀难以解决而放弃;不锈钢的发明和应用,促进了硝酸和合成氨工业的发展;高强度耐蚀合金的出现,使压力容器设备大型化成为可能;抗湿硫化氢腐蚀材料和焊接技术的研发,促进了含硫油气田的开发和高硫原油炼制技术的发展;美国的阿波罗登月飞船贮存N2O4的高压容器曾发生应力腐蚀破裂,经分析研究,加入质量分数为0.6%的NO之后才得以解决,美国著名腐蚀学家方坦纳(Fontana)认为,如果找不到这个解决办法.登月计划会推迟若干年。
未来的高新技术发展过程中,还会不断遇到各种新的腐蚀问题,而且是越来越难以解决的问题,比如化学、能源等领域的压力容器都有向高温、高压方向发展的趋势,这样可获得更高的生产率,更快的生产速度和更低的生产成本,但高温高压却会造成更加苛刻的腐蚀环境。随着全球原油和天然气的不断开发,原油品质逐渐劣化,含S量越来越高,由此引发的湿硫化氢应力腐蚀问题越来越严重,在很多关键的承压设备上,腐蚀问题一直没有得到有效的控制,这也严重地制约了原油和天然气产业链的安全生产和经济效益。
④ 促进自然资源的消耗
腐蚀对自然资源是极大的浪费,同时还浪费了大量的人力和能源,增加了碳排放。以金属材料为例,每年约30%的钢铁产品因腐蚀而报废,其中的1/3变成铁锈而损耗,同时,防腐蚀施工、维护还消耗了大量的人力资源。上世纪80年代,国内年产30万吨合成氨的中型化肥厂,每年因腐蚀报废的钢铁达1350-2100t,平均每吨氨耗钢4.5~7kg;我国每年因腐蚀、结垢报废的换热器达万台左右,仅钢材就消耗5万吨以上。我国资源利用率较低,要使我国经济快速增长,需尽快改变目前“高投入、高能耗、高排放、低效率”的粗放型增长方式,这就迫切需要政府各部门、各企业和全民都来关注腐蚀问题,才能实现开源节流,促进我国经济的可持续发展。
2 腐蚀控制的意义
以上可以看出,腐蚀与防护技术已成为社会发展中保证安全生产、提高经济效益、节能减排中不可或缺的重要组成部分。
腐蚀控制的意义在于:保障安全、保护环境、节约资源、改善环境、创造财富。安全生产、节能减排和经济因素是当前腐蚀与防护领域中许多研究工作的原动力。
鉴于腐蚀问题的严重性,国内外对防腐蚀工作都很重视,采取各种措施来减轻腐蚀的危害。为了保证油气管道的长期安全运行,各国政府和企业都制定有防腐法规,作为设计、施工、管理必需遵循的准则。
腐蚀控制的目标是使设备、结构或零部件的腐蚀速度保持在一个可接受的水平。实践表明,若充分利用现有的防腐蚀技术,广泛开展防腐蚀教育,实施严格的科学管理,因腐蚀而造成的经济损失中有30%~40%是可以避免的。所以说,腐蚀与控制研究具有很大的现实意义和经济意义。
绝大多数材料的破坏都与其周围环境的腐蚀因素有关,腐蚀控制的方法很多,在腐蚀控制上并没有所谓的“标准答案”,腐蚀环境对腐蚀机理和腐蚀控制的要求影响很大,不同行业和产品质量对腐蚀控制的要求也不相同,因此,对于腐蚀控制技术的制定,必须明确应用的具体条件,必须在生产安全、社会关注和经济上都进行评估才能获得最佳的结果,具体的腐蚀控制方案应运用腐蚀经济学方法进行评价确定。
中国工业防腐蚀技术协会从1985年成立就提出了“全面腐蚀控制(Total Corrosion Control,TCC)”的理论,全面腐蚀控制的核心是将防腐蚀技术和科学管理密切结合起来以达到最大限度的控制腐蚀,保证设备或装置的长周期连续安全运转。即必须从设计、制造、储运安装、运行操作、维修5个方面进行腐蚀控制,而且要和教育、科研、管理、经济评价4个环节紧密结合,从而达到对各种腐蚀的全面控制,才能把防腐蚀工作从消极的、治表的、被动的局面转变为的积极的治本主动的局面。
全面腐蚀控制是一项系统工程,压力容器的腐蚀虽然大多发生在设备的使用阶段,但是其产生的原因却孕育于各个阶段之中,而解决的措施也可以在各个阶段实现。对于一台设备或一套装置的腐蚀,不能只注意某种材料与环境作用产生的后果,要把装置的腐蚀作为一个整体加以考虑。作为防腐蚀工程技术人员,除掌握先进实用的防腐蚀理论与技术外,还需要宣传腐蚀的危害性,普及防腐蚀基础知识,引起有关部门乃至全社会的重视,同心协力控制腐蚀,使腐蚀损失降到最低程度。比如,对于湿H2S环境下的设备安全,用户管理不到位是导致设备早期失效的重要因素。相关的腐蚀控制和容器设计标准已经赋予用户更多的责任,用户应确定操作条件并指定使用何种材料、应确保所用材料能满足使用环境的要求、负责操作现场安装和设备的运行。而生产商仅负责满足金属材料学要求。
2009年世界腐蚀组织(World Corrosion Organization, WCO)在世界范围内确立每年的4月24日作为“世界腐蚀日(Worldwide Corrosion Day)”,在腐蚀和防护的研究中,致力于知识的发展和传播。其宗旨是唤醒政府、工业界以及我们每个人认识到腐蚀的存在,认识到每年由于腐蚀引起的经济损失在各国的GDP中平均超过3%;同时向人们指出控制和减缓腐蚀的方法。
正确的腐蚀控制,是延长设备的使用寿命,避免事故发生的重要保证。腐蚀控制通常有2种措施,一是补救性控制,即腐蚀发生后再消除;二是预防性控制,即事先采取防护措施,避免或减缓腐蚀,尽量减少可能引起的损害。预防性措施包括选材、结构设计、制造和热处理工艺、具体的防腐技术等。后者属于设计职责,如果在压力容器的设计阶段就充分考虑了腐蚀控制方案,就可以避免或减缓腐蚀的发生,节省大量的检维修费用。
当然,对于一个设计工程师来说,并不要求其同时又是腐蚀工程师,但如果其对腐蚀知识不了解,也绝不可能成为一个合格的设计者。以往的设计者对材料的力学性能十分熟悉,但对材料的耐蚀性能缺乏了解或综合分析能力,只能按照手册的相近条件选材,往往导致设备的早期腐蚀失效。所以,压力容器设计者了解一些基本的腐蚀和腐蚀控制基本知识是十分必要的。
腐蚀控制要从源头抓起,应以预防为主,避免短期行为,提倡“在使用寿命期内总费用的技术/经济综合分析”的概念,需要认真总结腐蚀控制工作的经验,结合国情吸收国外先进的防护技术和管理经验,促进腐蚀控制新技术在我国承压设备设计、制造和使用中的推广应用。不同行业,应根据自身的情况制订腐蚀控制的标准与规范,使防护工作有章可循,有法可依。全面宣传和推广寿命期内总费用全分析(Lifetime Cycle Cost)方法、以风险分析为基础的检测(Risk based inspection)、防护系统工程学等近代理念和方法来管理腐蚀,推广综合防护措施。企业或工程的腐蚀控制工作,要有专门的队伍从事该项工作。在设计、制造、施工安装、操作运行的全过程都要加强腐蚀控制管理,使压力容器的腐蚀处于可接受、风险可控的状态,使我国腐蚀控制水平尽早进入世界先进行列。
免责声明:本网站所转载的文字、图片与视频资料版权归原创作者所有,如果涉及侵权,请第一时间联系本网删除。
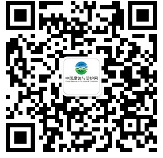
官方微信
《中国腐蚀与防护网电子期刊》征订启事
- 投稿联系:编辑部
- 电话:010-62316606-806
- 邮箱:fsfhzy666@163.com
- 中国腐蚀与防护网官方QQ群:140808414