冷换设备是炼化企业使用量最大的一类设备,其腐蚀泄漏问题是困扰炼油装置长周期安全运行的一个主要隐患。基于某炼化企业冷换设备在1个运行周期及大检修期间的腐蚀案例,分别从腐蚀类型、腐蚀部位、腐蚀成因等方面对其腐蚀情况进行统计分析,深入研究了冷换设备的腐蚀成因及主要影响因素,提出了从选材、制造、运行控制、循环水管理等方面对冷换设备的防腐进行优化的措施,为炼化企业冷换设备的腐蚀防护工作提供了有益的借鉴。
近年来,随着原油的劣质化日益加重,原油中所含的硫、酸、氯等腐蚀性杂质含量不断提高,使设备腐蚀问题成为困扰炼油装置长周期安全运行的一个主要隐患。冷换设备是炼油装置中应用最广泛的设备,投资占总体工艺设备投资的1/3以上,同时也是服役环境最恶劣的设备之一,经常因腐蚀、制造等因素发生泄漏,尤其是腐蚀泄漏问题,一直困扰着设备的管理工作,严重影响产品质量,甚至导致装置非计划停工及重大安全事故。
1 典型冷换设备的腐蚀统计分析
国内沿海某炼化企业1200万t/a原油加工能力,涉及常减压、催化裂化、加氢裂化、加氢精制、延迟焦化、硫磺回收等11套炼油装置,共有冷换设备457台。2014年装置停工大检修期间,针对401台冷换设备进行开盖检查,发现存在腐蚀问题的冷换设备共计73台,约占18.2%。通过对腐蚀失效的73台冷换设备进行统计分析发现,其腐蚀失效涉及的因素不仅与服役环境有关,还与设备材质、制造缺陷等密切相关。按照冷换设备失效类型进行统计分类(见图1),可分为均匀减薄、局部腐蚀、开裂、焊接缺陷和机械变形5种。其中与腐蚀相关的减薄、局部/坑蚀和开裂问题最多,约占失效案例的92%,与制造相关的约占8%。
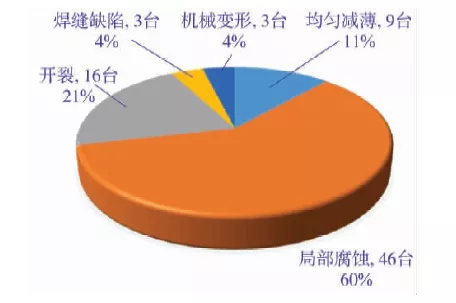
图1 冷换设备失效类型统计
注:同1台换热器可能同时发生1种或几种腐蚀类型,下同。
按照冷换设备出现腐蚀的部位进行统计分析,结果如图2所示。冷换设备的腐蚀主要发生在管束、管箱、管板、换热管管口、入口接管和壳体等部位,分别占腐蚀案例的25%、23%、31%、12%、5%和4%。其中发生在管束、管箱、管板上的最为突出,合计约占腐蚀案例的79%;易导致冷换设备腐蚀泄漏的部位出现在管束和换热管管口的案例,合计约占腐蚀案例的1/3。
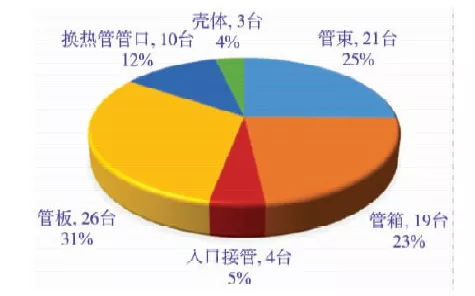
图2 腐蚀部位统计
根据冷换设备发生腐蚀失效的成因进行初步归纳分析,主要分为工艺介质腐蚀、循环水腐蚀、焊接及施工质量问题和选材等级低等4大类,如图3所示。其中由工艺介质导致的腐蚀失效问题最多,约占总腐蚀案例的45%;其次是因循环水腐蚀导致的失效,约占40%;焊接及施工质量问题约占10%;选材等级低问题约占5%。
2 冷换设备的腐蚀成因分析
工艺介质腐蚀
工艺介质,主要是指油品、油气等工艺物流。由于油品发生高温分解、加氢、裂解等反应,因此工艺介质中除了含有石油产品外,还含有硫、硫化氢、氯化氢、氨氮等腐蚀性物质。这些腐蚀性物质会对冷换设备产生HCl-H2S-H2O腐蚀、高温硫腐蚀、高温环烷酸腐蚀、氯化铵结垢及垢下腐蚀等。腐蚀形态主要表现为均匀腐蚀、点蚀、应力腐蚀、冲刷腐蚀、开裂等,详见图1的统计。原油-常顶油气换热器(E101/E201/E301/E401)为并列的4台换热器,2009年4月投用。该换热器管程介质为常顶油气,操作温度(进出口温度)118~93℃,管束材质为TA1,管板材质为16MnⅣ+TA1;壳程介质为原油,操作温度(进出口温度)40~60℃,筒体和封头材质为16MnR(自GB713—2008标准起牌号更新为Q345R,下同)。
检修期间发现,管箱内壁污垢、锈蚀较重,隔板及基体布满蚀坑,隔板中部存在明显的冲刷腐蚀减薄现象。从测厚情况看,E201管箱隔板冲蚀部位区域测厚值为10.14~10.37mm,其余部位为15.45~15.51mm;E301管箱隔板冲蚀部位区
域测厚值为9.51~10.02mm,其余部位为15.32~15.57mm;E401管箱隔板冲蚀部位区域测厚值为6.92~7.12mm,其余部位为13.95~15.51mm。管/箱出入口接管(光谱材质检测为317L)表面存在裂纹(见图4)。
为分析腐蚀原因,与现场工作人员进行交流发现,因油品性质变轻,2011年对常减压装置进行了扩容原油适应性改造。改造后,常压塔顶(简称常顶)负荷高于设计值,具体为:设计流量102t/h,实际流量126t/h;设计流速22m/s,计算最大塔顶流速达到27m/s。高流速的常顶油气加上腐蚀介质会对管箱造成严重的冲刷腐蚀,且高流速、高剪切力会破坏已经形成的缓释剂保护膜,使金属裸露,加速腐蚀。另外,此部位的常顶注水点设置在E101/E201/E301/E401管箱入口法兰上部管线,而缓蚀剂与中和剂注入点在常顶,注水后时间太短,中和剂不能充分与生成的盐酸反应;而且通过模拟,最优操作时,注水后液态水也只有5%,量明显不足。这就导致了HCl-H2S-H2O腐蚀环境的形成,进而造成奥氏体不锈钢的应力腐蚀开裂。
循环水介质腐蚀
随着节能环保要求的提高,循环水浓缩倍数不断提高,回用污水后水质状况日益变差,导致装置循环水侧的腐蚀和结垢问题日益突出。循环水的水质状况对水冷器的腐蚀影响较大,主要因为循环水中杂质含量较多,同时存在大量粘泥,容易在金属表面结垢,产生垢下腐蚀,造成管子出现蚀坑、穿孔。另外,如果循环水中存在一定量的氯离子,则会造成不锈钢管束点蚀,甚至引起奥氏体不锈钢管束开裂。根据图3的腐蚀成因统计分析可见,循环水造成的冷换设备腐蚀占总体的40%。

图4 换热器E101/E201/E301/E401腐蚀宏观形貌
催化分馏塔顶油气冷凝器E203ABCD管程为循环水。因循环水中微生物控制不力,导致细菌大量繁殖,形成粘泥,吸附水中灰分,附着在设备壁上,产生粘泥下腐蚀和结垢腐蚀,同时,又因换热器结构不合理,在管子与管板的连接处产生了较大的附加应力,从而造成4台换热器的管板腐蚀严重且存在开裂现象(见图5和图6)。
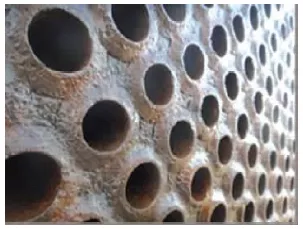
图5 E203D管板腐蚀开裂形貌

图6 E203A管板坑蚀及焊缝开裂形貌
脱硫联合装置循环碱液冷却器E505A,管程为循环水,管束多处出现腐蚀穿孔,穿孔处位于壳程进料口一侧、导流筒和管板之间。对管束进行测厚,结果显示,穿孔处附近厚度为1.5mm,未穿孔处为2.3mm。内窥镜观察发现,其管束内壁有片层状垢物(见图7)。
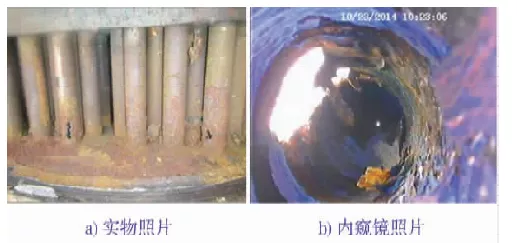
图7 循环碱液冷却器E505A管束穿孔
加氢低分气冷却器E102,管程为循环水,管箱和管板表面结硬质黄褐色垢物,垢下为红棕色铁锈,环焊缝点蚀坑深度达0.5mm(见图8)。
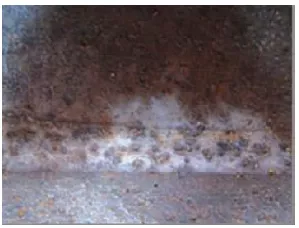
图8 加氢低分气冷却器E-102管板点蚀形貌
脱硫联合装置再生塔顶冷凝器E302AB,操作介质为循环水/贫液,管束材质为00Cr17Ni14Mo2,筒体和封头材质为16MnR+316L。检修发现,管箱内结黄褐色硬质垢,垢下点蚀坑深度达0.2~0.4mm(见图9)
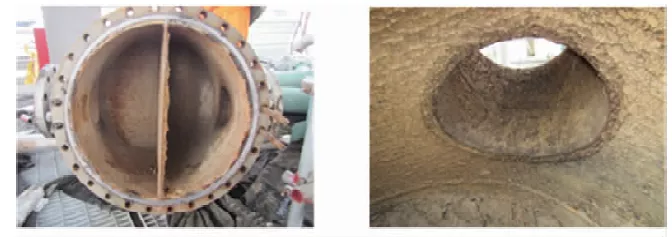
图9 E302AB管箱腐蚀形貌
制造/设计缺陷
根据图3的统计,因焊接、施工质量、设计缺陷(包括选材等级低)造成的换热器腐蚀大概占15%。换热器在制造、安装或运输过程中,因制造和施工质量的低劣或不稳定,以及运输过程中的不文明操作,造成焊接质量不合格,涂层存在针孔、漏涂、磨损,设备出现凹坑、局部擦伤、挤压等,这些缺陷可导致腐蚀的加剧,容易导致泄漏发生。在此次检维修的过程中,发现发生在焊缝处的腐蚀较多,比如多处出现换热管管口、管板焊缝开裂,同时还发现管箱密封面处焊缝缺陷(见图10~图13)。
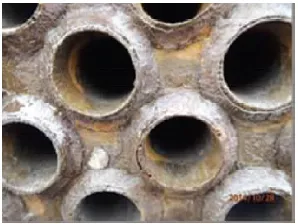
图10 原油-减一中油换热器E204A管头焊缝腐蚀
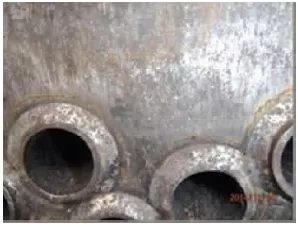
图11 原油-常顶循换热器E302管板热影响区裂纹
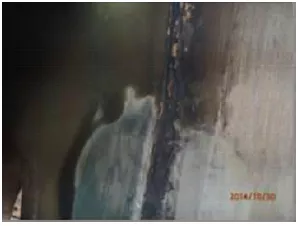
图12 脱盐油-减二中E406A换热器管箱密封面处焊缝缺陷
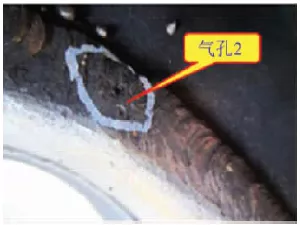
图13 顶循环油-热水换热器E204D管箱焊缝缺陷
另外,换热器的寿命与选材相关性很大。换热器的选材原则上既要满足工艺过程的要求,又要满足强度要求和制造工艺要求,所以要根据不同介质和工艺,选择合适的金属材料。此次检修过程中,发现4台换热器因选材等级偏低造成了严重腐蚀。
3 冷换设备的防护措施
材料/制造
设备的制造和选材是设备设计的关键和基础,将直接影响设备的使用寿命、安全性以及成本。所以一定要严把冷换设备的制造质量,并保证焊接、施工质量。施工过程中,应文明操作,避免挤压、擦伤等。采用耐蚀涂层时,确保涂层质量没有缺陷,并注意开、停工过程的蒸汽吹扫,防止涂料失效。
针对高温部位,要防止高温硫、高温环烷酸、高温氢/硫化氢等的腐蚀。碳钢及合金钢在高温硫、高温环烷酸及高温氢/硫化氢等环境中的腐蚀速率可参考API RP581—2016《基于风险的检验技术》,API RP939-C-2009《避免炼油厂硫腐蚀失效导则》中的Modified McConomy Curves 、Couper-Gorman H2/H2S Curves ;针对低温部位,要避免碳钢在湿硫化氢环境中的损伤。关于冷换设备的选材可参照SH/T3219-2012《高酸原油加工装置设备和管道设计选材导则》、SH/T3096—2012《高硫原油加工装置设备和管道设计选材导则》的有关规定,以炼油装置正常操作条件下原油的硫含量和酸值为依据,充分考虑最苛刻条件下可能出现的最大硫含量与最高酸值来确定最适用的材料,力求做到所选用的材料经济、可靠和耐用。
运行控制
根据国内外炼油企业的生产经验,对于低温服役环境,工艺防腐是关键,尤其是常减压装置,如果工艺防腐做得不好,即使材质等级很高(如上述案例中常顶换热器使用钛材),也避免不了腐蚀。所以针对炼油装置冷换设备低温处,要参照执行中国石化《炼油工艺防腐蚀管理规定》实施细则的相关要求加强工艺防腐措施。例如,对常减压蒸馏装置,控制处理量和原油质量在设计范围内。加强常减压装置的“一脱三注”系统操作管理,控制脱后含盐≤3mg/L、脱后含水≤0.3%、污水含油≤200mg/L。控制塔顶冷凝水pH 值为5.5~7.5(注有机胺时)、7.0-9.0(注氨水时)、6.5~8.0(有机胺+氨水);铁离子含量≤3mg/L。控制塔顶内部操作温度高于水露点温度14℃以上、塔顶回流返塔温度高于90℃等。针对高温部位,以设备材质为基础,对新建或在役炼油装置制定有针对性的最低设防值,并按要求严格执行。运行期间要加强工艺介质化验分析,禁止超出设计/设防值,同时应对腐蚀严重部位强化监检测措施并提出材质升级方案。
水冷器防护措施
循环水管理:根据中国石化《炼油工艺防腐蚀管理规定》实施细则管理规定:
1)循环冷却水管程流速不宜小于1。0m/s,当循环冷却水壳程流速小于0。3m/s时,应采取防腐涂层、反向冲洗等措施。循环冷却水水冷器出口温度推荐不超过50℃。采用超声波流量计对水冷器水侧进行流速抽查,防止偏流或流速过低。对于结垢倾向严重的水冷器,可以加设反冲洗设施或采用超声波除垢等技术。
2)循环冷却水水质应符合GB50050-2017循环冷却水水质的控制指标要求。使用再生水作为补充水应符合Q/SH0628.2-2014《水务管理技术要求第2 部分:循环水》的要求。
3)缓蚀阻垢剂应针对水质和工况选择高效、低毒、化学稳定性和复配性能好的环境友好型药剂。当采用含锌盐药剂配方时,循环冷却水中锌盐含量应小于2mg/L(以锌离子计);循环冷却水系统中有铜合金换热设备时,水处理药剂配方应有铜缓蚀剂。
4)循环冷却水微生物控制宜以氧化型杀菌剂为主,非氧化型杀菌剂为辅。当氧化型杀菌剂连续投加时,应控制余氯量为0.1~0.5mg/L;冲击投加时,宜每天投加2~3次,每次投加时间宜控制水中余氯0.5~1mg/L,保持2~3h。非氧化型杀菌剂宜选择多种交替使用。
5)循环冷却水浓缩倍数应按照有关要求进行控制,当出现超标时,可采取增大排污量的方式来调整;循环冷却水出换热器的温度控制推荐不超过50℃;各装置应根据实际情况建立腐蚀监检测系统和腐蚀管理系统,保证生产的安全运行。
水冷器管束防腐
1)升级材质
严格控制水冷器管束材料的加工、热处理工艺,使用更合适的材料,可以有效缓解循环水结垢、垢下腐蚀等。目前,大多数炼厂水冷器管束材质以碳钢为主,对腐蚀严重部位可升级材质以提高水冷器的使用寿命。炼化装置中应用较多的高等级水冷器管束材质有08Cr2A1Mo、092A1MoRe、022Cr19Ni10、022Cr17Ni12Mo,双相钢、钛材等。奥氏体不锈钢具有良好的耐蚀性,并且结垢不易附着管壁表面,使用效果较好,但在使用过程中要严格控制循环水以及工艺介质氯离子的含量。进行材质升级时,应从介质控制、防腐涂料、阴极保护、经济效益等方面综合考虑。
2)防腐涂料
水冷器管束涂料防腐已广泛应用于炼油装置的冷换设备。采用耐腐蚀涂料解决碳钢换热器管束的腐蚀与结垢问题,可取得较好的效果。通过使用性价比较高的防腐涂料,可有效延长水冷器的使用寿命,节约钢材,增加经济效益。
3)牺牲阳极用牺牲阳极法对管板和管束进行保护,是防止水冷器在循环水中腐蚀的重要手段之一。该措施不但可延长碳钢材料水冷器使用寿命,而且可达到提高防腐效果与降低成本的双重效果。一般常用的牺牲阳极材料有铝、镁、锌3种,分别适用于不同的腐蚀介质。炼厂水冷器的保护宜选择使用镁合金牺牲阳极。在使用镁阳极块的时候,要做好牺牲阳极规格的选取、保护面积的计算及安装位置的确定工作
免责声明:本网站所转载的文字、图片与视频资料版权归原创作者所有,如果涉及侵权,请第一时间联系本网删除。
相关文章
无相关信息
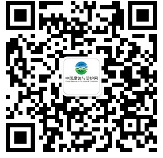
官方微信
《中国腐蚀与防护网电子期刊》征订启事
- 投稿联系:编辑部
- 电话:010-62316606-806
- 邮箱:fsfhzy666@163.com
- 中国腐蚀与防护网官方QQ群:140808414
点击排行
PPT新闻
“海洋金属”——钛合金在舰船的
点击数:7130
腐蚀与“海上丝绸之路”
点击数:5741