硬质合金强度是表征产品韧性、抗冲击能力的关键指标之一。在断续切削、不均匀切削(包括带黑皮加工)等金属切削加工领域,刀具断裂或崩碎是最主要的失效方式,因此对硬质合金基体强度提出了极高要求。
在现代切削加工中,涂层技术的引入使刀具的耐高温、耐磨、耐腐蚀等性能都得到了很大提升,达到了高速加工的要求。但由于涂层刀具在高速加工中的耐冲击能力不理想,国内大部分工况恶劣的粗加工领域还在使用切削效率非常低的非涂层刀具。经过分析和研究认为,涂层过程中硬质合金基体长时间处于500℃-1100℃,对基体的强度会产生不利影响,使涂层刀具的耐冲击性能下降。
试验方案与试验结果
试验选用6种K系列涂层硬质合金基体牌号,基体WC粒度分别为0.4μm、0.6μm、0.8μm、1.5μm、3.0μm和4.0μm,其主要成分为WC+Co,含有微量添加剂。每个牌号选用同一批原料,分别压制5.25mm×6.5mm×20mm的强度试样条30根,同炉同舟皿一次烧结出来。取10根磨制试样进行强度检测,取未磨毛坯试样条10根进行CVD涂层、10根进行PVD涂层。对涂层后的试样条分别进行磨样,并检测硬质合金基体的强度,从而研究涂层后各种粒度的硬质合金基体强度的变化。
图1为不同粒度基体在涂层前后强度的变化情况。除去试验中磨样、人为操作等偶然因素外,由图1可知,强度变化趋势明显,同一种基体牌号烧结后强度>PVD涂层后强度>CVD涂层后强度。
(a)0.4μm
(b)0.6μm
(c)0.8μm
(d)1.5μm
(e)3μm
(f)4μm
图1 不同粒度的基体强度变化
图2是试样条在烧结态、PVD涂层态和CVD涂层态的平均强度变化趋势。由图2可知,试样经过PVD和CVD涂层后强度呈下降趋势,且CVD涂层比PVD涂层降低得更多。
图2 不同晶粒度的基体涂层前后的平均抗弯强度变化
图3是PVD涂层态和CVD涂层态试样条相比烧结态试样条的强度下降幅度对比。由图可知:WC粒度0.4μm的牌号,PVD涂层态强度下降约11.6%,CVD涂层态强度下降16.3%;其它硬质合金基体牌号PVD涂层态强度下降在6%-8%之间,CVD涂层态强度下降了10%-12%。随着粒度的加粗,PVD涂层后的强度降低幅度先减少后又增加,CVD涂层后的强度降低幅度则随着晶粒度的加粗而降低。
图3 不同晶粒度基体涂层后的强度下降幅度对比
通过以上试验发现,经过PVD涂层和CVD涂层后,同一种硬质合金基体牌号的涂层刀具强度比非涂层刀具降低约10%。在设计涂层刀具基体牌号时要充分考虑这一强度降幅,才能保证刀具在实际切削过程中的抗冲击性达到基体设计的要求。
小结
在高速、高效加工中,不仅要求刀具具有耐高温、高耐磨和抗冲击等性能,还要求获得最佳的表面加工质量,刀具涂层工艺是满足当前金属切削加工需求的基本途径之一。本文的研究结果揭示了涂层对硬质合金刀具基体强度的影响规律,对设计硬质合金涂层刀具基体材质、探索涂层温度下硬质合金基体材质变化都有一定帮助。
免责声明:本网站所转载的文字、图片与视频资料版权归原创作者所有,如果涉及侵权,请第一时间联系本网删除。
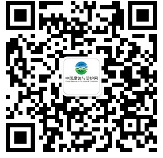
官方微信
《中国腐蚀与防护网电子期刊》征订启事
- 投稿联系:编辑部
- 电话:010-62313558-806
- 邮箱:fsfhzy666@163.com
- 中国腐蚀与防护网官方QQ群:140808414