直升机在海洋环境服役过程中(飞行和露天停放过程),涂层体系不可避免地受到太阳辐射、盐雾腐蚀、海浪冲刷及自身工况等多因素耦合作用,从而引起涂层的新型腐蚀损伤问题。这不仅影响涂层的外观,而且还导致涂层防护体系失效,基体结构腐蚀,甚至引起重大事故。因此,防护体系在海洋大气环境中的防护性能是衡量直升机海洋服役性能的重要指标。40CrNiMoA 结构钢强度高,用于直升机起落架等承力结构,但耐腐蚀性能较差,通常采用涂层体系进行防护。由于对40CrNiMoA 结构钢防护体系在海洋大气环境中多因素耦合作用下的防护性能的研究较少,因此文中针对其在海洋环境中服役的耐腐蚀性能展开相关研究。
针对直升机结构钢40CrNiMoA 的防护体系,利用模拟海洋大气环境加速试验方法,再现其在实际服役过程中出现的损伤形式和特征。通过电化学阻抗(EIS)、微观形貌等方法研究其防护性能变化,为考核海洋大气环境下服役的直升机结构钢涂层体系的耐腐蚀性能提供数据支撑。
1 试验
1.1 试验件试
验件为标准试片,尺寸为100 mm×50 mm×3 mm。
试验件的材料、表面防护体系见表1。
1.2 实验室加速试验
模拟海洋大气环境实验室加速试验方法见表2,其中紫外照射试验采用美国Q-Panel 公司的QUV- SPRAY型紫外老化试验箱进行,盐雾试验采用美国Q-Panel 公司的Q-FOG/CCT1100 型盐雾试验箱进行,周期浸润试验采用丹麦的CCX200 自然环境模拟综合实验箱进行,振动实验在垂直振动台和三综合试验箱中进行。结合相关模拟海洋环境加速试验环境谱以及试验件的工况环境,制定加速试验方法,其中盐雾试验和周期浸润试验所用溶液的pH 均为2.0,以反应结构件实际服役过程中的酸性环境。另外,按照GJB 150.16A 序I 进行振动试验,用来反映工况环境下结构件受到的振动作用。按照表2 所述试验步骤,重复8 次,进行8 个周期试验。
1.3 防护性能评价
目测检查(试验件外观)借用放大镜进行,试验件表面的宏观腐蚀现象采用NiKon D50 数码相机在荧光灯下进行拍照记录。采用VHX-100K 视频显微镜和FEIQUANTA 600 环境扫描电子显微镜,对腐蚀过程中涂层的表面微观形貌进行观察分析。使用Princeton AppliedResearch Model 273A 恒电位仪和Signal Recovery 5210锁相放大器进行电化学阻抗测试,利用三电极体系在3.5%中性氯化钠溶液中完成,铂作为辅助电极,饱和甘汞电极作为参比电极。将带O 型圈的聚氯乙烯管压在试验件表面,使暴露在溶液中的测试面积为1cm2,并保持同一试验件每次测试位置相同。测试区域在溶液中浸泡20 min,待开路电位稳定,测试过程中三电极体系置于法拉第笼中。测试的激励信号为幅值10 mV 的正弦波,频率的扫描范围为0.1 Hz~100 kHz。
2 结果及分析
2.1 宏观形貌
涂层A 的宏观形貌如图1 所示。初始状态时,目测检查涂层A 试验件,表面涂层完整(图1a)。
第2 周期加速试验后,涂层A 表面局部区域出现肉眼可见的不连续鼓泡。在经历每周期的盐雾试验和周期浸润试验后,鼓泡逐渐扩大,并在鼓泡处出现微小裂纹和轻微锈蚀,如图1b、c 所示。产生鼓泡现象的原因可能是涂层与基体界面处存在某种气体,气体膨胀的力超过了涂层与基体的粘结力,导致涂层鼓起。
在该次试验中,推测涂层表面可能存在微小缺陷,在盐雾和周期浸润试验中,涂层暴露在高湿环境或浸入溶液中,水或水气和腐蚀溶液从表面缺陷处渗透进入涂层,在金属基体处积聚,产生相应的渗透压,并发生腐蚀反应,引起体积膨胀,从而导致涂层鼓泡。随着试验周期的增加,鼓泡内压力逐渐增大,在垂直方向上大大超过涂层界面上的粘结力时,将发生涂层表面龟裂,龟裂处基体腐蚀加剧,并沿着裂纹渗出,所以在后期鼓泡处出现锈蚀。为了研究涂层表面是否存在缺陷,后续对涂层微观形貌进行观察。
始时表面平整,无明显缺陷。经过8 个周期加速试验,表面未出现涂层粉化、开裂、起泡、剥落等现象,如图2b 所示。根据宏观形貌变化,可以初步看出,在模拟海洋大气环境中,涂层B 的防护性能优于涂层A。
2.2 微观形貌结果分析
采用视频显微镜和扫描电子显微镜对不同周期加速试验后的微观形貌进行分析。图3 为涂层A 的微观形貌,可以看出涂层A 表面较为疏松,存在微米尺寸孔洞。试验前,在局部位置存在微小的腐蚀锈点,尺寸约为2~5 μm(见图3a)。随着试验周期的增加,发生腐蚀的位置不断增多,产生了较多的红色腐蚀产物(见图3b、c)。这表明由于涂层A 结构较为疏松,局部位置存在孔洞,空气及水分子已通过微孔与结构钢基体接触,并发生化学反应。金属基体与有机涂层界面的主要反应方程式为:
图 4 为涂层B 的微观形貌,涂层B 表面较为致密。经过8 个周期加速试验,表面未发生明显变化,没有锈蚀等现象出现,与前期的宏观形貌结果一致。
2.3 电化学阻抗测试结果
单纯根据形貌变化判断涂层的防护性能往往是不充分的,因此采取电化学阻抗法进一步研究涂层的防护性能。由于电化学阻抗谱的详细解析比较复杂,在工程上应用不便,因此通常采用电化学阻抗谱中低频部分的阻抗模值作为检测涂层防护性能变化的指标。相关研究结果表明,有机涂层低频区的阻抗模值与其防腐蚀性能存在着对应关系,阻抗模值在≥109、108~109、107~108、106~107、≤106 Ω·cm2 范围内时,涂层性能分别为优、良、中、差、很差。当有机涂层的交流阻抗模值低于107 Ω·cm2 时,就表明该有机涂层的防腐蚀能力已经下降,但仍具有一定的防护能力;当有机涂层的交流阻抗达到甚至低于106 Ω·cm2时,表明该有机涂层的防腐蚀能力已经很差,在有机涂层与基体金属界面有可能已经发生了电化学腐蚀反应。由此106 Ω·cm2 可以作为有机涂层是否完全丧失防护能力的临界值。
由图 5a 可见,从试验前到经历了8 周期实验室加速试验过程中,在较宽的低频区域,涂层A 的阻抗模值出现水平段,呈现电阻特征,说明涂层下基体的腐蚀已经发生。从表2 可以看出,试验前涂层A 的特定频率电化学阻抗模值|Z| f=0.1 Hz 的数值较低,为4.3×104 Ω。
表明在电化学阻抗测试过程中,溶液离子通过表面微孔,已与基体接触发生电化学腐蚀反应,导致涂层的特定频率电化学阻抗模值|Z| f=0.1 Hz 很低,说明该有机涂层的防腐蚀能力很差。随着试验周期的增加,电化学阻抗模值略有增加,表明随着试验周期的开展,腐蚀有轻微减缓的趋势。这是因为腐蚀产物覆盖在基体表面,对溶液离子的渗入产生了一定的阻碍作用,降低了腐蚀速率,提高了电化学阻抗模值。
由图 5b 和表2 可见,从试验前到经历了8 周期实验室加速试验过程中,随着频率的变化,涂层B的阻抗模值呈现电容特性,不同周期后阻抗模值变化幅度微小。特殊频率模值阻抗|Z| f=0.1 Hz 的数值一直保持在108~109 之间,处于较高数值,说明涂层防护性能较好,与前期分析结果一致。
结论文中通过模拟海洋环境的实验室加速试验,对比分析了两种涂层的防护性能。
1)涂层A 结构相对疏松,经过8 个周期实验室加速试验后,溶液通过涂层表面孔洞渗入,引起基体腐蚀,导致涂层局部鼓泡。同时,涂层A 的电化学阻抗谱阻抗模值|Z|f=0.1 Hz 也相对较低,说明涂层耐腐蚀性能较差。
2)涂层B 结构相对致密,试验前表面完整,无明显缺陷。经过8 个周期实验室加速试验后,涂层表面未出现涂层粉化、开裂、起泡、剥落等现象。同时,涂层B 的电化学阻抗谱阻抗模值|Z|f=0.1 Hz 也相对较高,说明涂层耐腐蚀性能优异。
3)对于涂层A 试验件,可以尝试改善涂层涂覆工艺,改变涂层结构,降低孔隙率,从而提高其耐腐蚀性能。
免责声明:本网站所转载的文字、图片与视频资料版权归原创作者所有,如果涉及侵权,请第一时间联系本网删除。
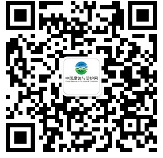
官方微信
《中国腐蚀与防护网电子期刊》征订启事
- 投稿联系:编辑部
- 电话:010-62313558-806
- 邮箱:fsfhzy666@163.com
- 中国腐蚀与防护网官方QQ群:140808414