镍基复合粉末具有良好的工艺成型性、耐蚀耐磨和耐高温性,得到了广泛的应用。镍基复合粉末的成分、含量以及涂层成型方法皆影响涂层的组织结构和形貌,从而影响涂层的耐腐蚀、耐高温、耐摩擦等性能。
真空熔覆技术是将涂覆在零件表面的镍基合金粉末进行高温烧制,使涂覆层与基体间产生分子间结合或化学结合,从而提高零部件的物理、化学性能从而提高零部件的使用寿命。真空熔覆技术有工艺简单、涂层表面光滑致密、与基体发生高强度冶金结合和涂层厚度可控等优点。Gao等用真空烧结技术制备了性能优良的合金,发现烧结温度和时间对合金孔隙度、显微组织和力学性能有很大的影响;当温度低于粘结相熔点时出现固态烧结,表面和体积的扩散引起的收缩使试件致密化;液相出现后WC颗粒在液相中重新排列、溶解和沉淀,进一步消除了合金的孔隙,促进合金的致密化;随着Fe/Ni比率的增大晶体结构也发生变化,从fcc γ-(Fe、Ni)到bcc α-(Fe、Ni),WC颗粒逐渐减小,分布更加均匀。Elkhoshkhany等的研究发现,随着WC含量的提高Ni涂层中Ni晶粒的尺寸减小、复合材料的硬度提高;而钴的加入改善了涂层的表面形貌,因此涂层硬度的提高比纯镍基合金更显着。Babu等用爆炸喷涂技术制备了致密的WC-(W,Cr)2C-Ni和WC-12Co涂层,发现WC-(W,Cr)2C-Ni涂层主要由WC相、第二硬质相(W,Cr)2C、W和Ni-Cr相组成,其耐磨性、硬度以及耐腐蚀性都有明显的提高。Ghasali等[以镍和钼为粘结剂制备了两种不同类型的WC/基陶瓷,在WC/Mo金属陶瓷烧结过程中形成了Mo2C化合物,而WC/Ni 金属陶瓷烧结中只有WC/Ni的结晶相;镍粘结剂的良好润湿性使WC/Ni型金属陶瓷的抗弯强度和断裂韧性均比WC/Mo的高,中间相Mo2C的形成使WC/Mo金属陶瓷具有比WC/Ni金属陶瓷更高的硬度。
对于涂层的结构设计和性能,真空熔覆过程有决定性的作用。结构决定性能,对熔覆层形成过程的分析可为制备结构更优、性能更好的涂层奠定理论基础。本文用真空熔覆技术制备镍基复合涂层,根据在涂层形成过程中中间阶段取样的形貌和成分研究熔覆层的形成机制。
1 实验方法
采用真空熔覆工艺在尺寸为50 mm×50 mm×10 mm的45钢基体上制备Ni基复合涂层,复合涂层的设计构成主要有20%WC粉末和余量Ni基合金粉末。镍基合金粉末的化学成分列于表1,粉末的外观形貌在图1中给出。镍基合金颗粒直径为48~106 μm,硬质颗粒WC的粒径为5~10 μm,具有不规则的几何形状,高硬度和高熔点,为了提高涂层的硬度以及耐磨性。
制备试样时,先用砂轮将基体45钢表面的氧化层除去,然后用砂纸将其打磨至平整光亮,再用丙酮和无水乙醇清洗除去油污,最后烘干备用;将镍基合金粉末与自制粘结剂混合均匀后涂覆在基体表面即为过渡层,厚度为0.5~2 mm,而后将混合均匀的复合粉末用粘结剂混合后涂覆在过渡层的表面,厚度为2~4 mm;先用吹风机将涂有预制层的试样吹5~10 min,然后在无强光(如阳光)直射的条件下自然阴干2 h,再在马弗炉中烘干(100℃,2 h),最后将其放入ZT-18-22型真空碳管炉烧结。碳管炉的真空度为6.67×10-2 Pa,升温至1060℃并保温10 min,然后随炉冷却到150℃出炉空冷至室温,即可得到镍基复合涂层。实验中进行中间阶段取样:升温至1020℃并保温10 min,随炉冷却后取样分析。
线切割纵向切取大小为10 mm×10 mm的试样,磨样、抛样和腐蚀后进行组织观察与成分分析。使用Quanta 450-FEG型扫描电子显微镜(SEM)观察熔覆层的微观组织形貌,使用附带的EDAX能谱仪(EDS)分析各组织元素及其含量。用D/max-2400型X射线衍射仪(XRD)分析熔覆层的物相组成。用EPMA 1600电子显微探针分析仪(EPMA)分析熔覆层截面元素分布。
2 结果与讨论
2.1 熔覆层的微观组织
由图2a可见,Ni+20%WC真空熔覆涂层的横截面主要分为复合层(CZ),过渡层(TZ),扩散熔合区(FZ)以及扩散影响区(DZ)。复合层的厚度为4 mm,呈黑白色;过渡层的厚度为1 mm,呈黑灰色;扩散影响区的厚度约为250 μm。复合层与过渡层的组织致密均匀,组织中有在试样制备过程中残留的硬质颗粒和微孔。在过渡层的结合界面与45钢基体间有一条较为光亮的条带(图2a中方框A),将其放大后可见这一亮带的宽度约为20 μm。在此区域做EDS线扫描,显示为从过渡层到45钢基体,Ni元素含量先增加后降低,Cr元素含量降低,Fe元素含量增加,如图2b所示。由此可见,在此区域因元素扩散而形成了良好的冶金结合,即为扩散熔合区FZ。在过渡层靠近扩散熔合区的C区域内可见一些粗大的针棒状相,EDS分析显示主要为碳元素和铬元素。由于碳元素和铬元素的亲和力较大,容易形成Cr7C3 、Cr23C6,可阻止碳元素和铬元素的扩散[14]。因此,熔合区的C、Cr等元素极少,基本上没有硬质相。由图2c可见,EDS分析点16、点17颜色较深的相主要为碳元素和铬元素,即铬的碳化物,而点18颜色较浅的相为(Ni,Cr)固溶体相并夹杂着少量的Fe、Si等元素。图2d所示为复合层组织,可见白色颗粒和白色絮状物弥散分布在镍基固溶体上,WC颗粒分解形成了富W的复相碳化物。例如:M7C3(M=W、Cr)为复杂六方点阵结构,M23C6(M=W、Cr、Ni)为复杂立方点阵结构。
由图3可见,Ni+20%WC熔覆层的主要相为γ-Ni固溶体,Cr7C3、Ni2.9Cr0.7Fe0.36、Cr23C6、Ni3Fe、Ni3Si、Ni3B、W2C、C等。在烧结过程中低熔点共晶组元Si快速扩散与镍元素形成Ni3Si相,少量的铁、硼元素与镍元素形成的Ni3Fe、Ni3B相弥散分布与共晶组织中;在结晶过程中从晶界析出的Cr7C3、Cr23C6硬质相分布在γ-Ni固溶体中;Fe与Ni、Cr原子反应生成中间化合物Ni2.9Cr0.7Fe0.36;持续高温使WC分解即2WC=W2C+C,形成了W2C和C。
2.2 熔覆层的形成机理
图4给出了真空熔覆中间阶段1020℃取样的预制层与基体结合处预制层侧结合面的原始形貌。由图4a可见,在涂层与基体结合面上呈现出大小不同的颗粒,颗粒之间已经程度不同的熔合,局部颗粒间存在孔隙。其原因是,Ni基粘结相并没有完全熔合并充分填充颗粒间的孔隙,多数颗粒表面较为粗糙。将其进一步放大(图4b)可见少量表面光滑的圆形颗粒(如图中箭头所示),与图1a中的颗粒相同,说明此为未熔颗粒,而表面粗糙颗粒为熔融颗粒(如图中方框内所示),且其表面部分包裹着针棒状相。EDS分析结果表明,粗糙颗粒主要是Ni、Cr、C元素组成,针棒状相则主要由Cr、C元素组成,为铬的碳化物,熔融的镍基合金填充至颗粒之间的孔隙。图4c给出了凹陷部位的形貌,可见在Ni基固溶体上分布着部分分解的块状WC颗粒和新生成的针棒状相。在熔融过程中靠近结合界面的WC颗粒通过空隙下沉到过渡层,而过渡层的Ni基合金颗粒此刻并不能完全熔融,使块状WC颗粒和新生成的针棒状相直接裸露出来。 EDS分析点A结果列于表2,可见这些针棒状相主要为C和Cr的化合物Cr7C3、Cr23C6。图中较小的方框区域为熔融的镍基合金区域。
图5给出了真空熔覆中间阶段1020℃取样的基体与预制层结合处基体侧结合面的原始形貌。由图5a可见,在基体侧的结合面上呈现出大小不同的颗粒以及其间填充着Ni基固溶体,颗粒间不同程度的融合。其放大图为图5b,可见在Ni基固溶体上分布着一些针棒状相、表面粗糙的颗粒以及表面较为光滑的颗粒;方框A显示的大量针棒状相。EDS分析结果表明,这些针棒状相是C和Cr的化合物Cr7C3、Cr23C6;箭头所指的颗粒表面较为光滑。这与图1a中的颗粒相同,说明此为未熔颗粒;方框B所示的表面粗糙的颗粒,其进一步放大图为图5c,可见颗粒表面包裹着大量针棒状相,说明颗粒融解并在其表面生成新相。
图5与图4相对应,说明在结合面上颗粒间发生了不同程度的融合,部分颗粒间熔合形成烧结颈,使彼此连接在一起,随着烧结颈的逐渐增大,使颗粒间结合越牢固;部分颗粒未熔合而单独存在,结果是颗粒间的结合不牢固,使涂层从基体上剥落。
图6给出了在真空熔覆中间阶段1020℃取样的预制层表面组织形貌。图6a表明,此时熔覆层表面已经熔融且组织致密,在箭头所示Ni基固溶体相上分布着形状不同的未完全分解的WC颗粒。WC部分分解并在其表面及周围形成新的絮状碳化物,如图中方框所示。絮状物和未完全分解的WC在Ni基固溶体上呈网状分布。从图6b可见,这些颗粒较大的絮状物呈菱形、矩形,分布在部分分解的WC颗粒周围。从图6c可清晰看到这些絮状碳化物的形状,其间填充有镍基固溶体。图7所示给出了该区域的EDS元素扫描结果。可见这些白色絮状颗粒主要为W、Cr、Si和C形成的复相化合物,絮状颗粒以外主要以Ni为主,辅以少量Si与Cr。由此可知,WC颗粒区域发生了WC的部分溶解和富W复相碳化物的析出。
图8给出了剥落涂层的侧面形貌。图8a是整个涂层的侧面形貌,A侧为靠近表面区,B侧为靠近与基体结合面区,可见整个熔覆层靠近表面的区域较为致密,中部区域至基体结合面区域有孔洞。图8b为A侧区域的放大形貌,可见较多光滑的相(如点C)。对其进行EDS分析结果表明,这个相主要由Ni基固溶体以及少量钨和铬的碳化物组成。图8c结合界面区域的放大形貌,融合较好的光滑相较少,箭头所示区域有较多的原始未完全熔化的镍基合金颗粒。由此可知,熔覆层的形成先从表面开始熔融,然后逐渐向内部进行。
图9给出了剥落涂层截面的组织形貌。从图9a可见,熔覆层靠近表面的区域较为致密,靠近结合面的区域组织较为疏松,中间区域最为疏松,孔隙较多。图9b给出了截面组织。EDS分析结果表明,深灰色区域由Ni基固溶体、灰白色区域WC(如箭头所示)以及分布在WC颗粒周围及表面的絮状富W复相碳化物组成,黑色区域为孔隙。从图9c可见,这些絮状富W复相碳化物呈矩形或菱形等形状。
由镍基复合涂层形成过程的中间阶段1020℃取样分析可知,其熔融、熔合、孔隙填充等自预制层的表面开始,其形成过程示意图如图10所示。图10a给出了制备后烘干的预制层,图10b给出了在真空碳管炉中熔覆层熔覆前期升温至接近镍基合金颗粒熔点前即900℃时的情况。此时复合层的最外层和涂层侧面的Ni基合金颗粒发生表面微熔形成微烧结颈,涂层的内部尚未熔化。随着温度的升高微熔加剧,从涂层表面Ni基合金颗粒相互接触位置的微烧结颈逐渐长大,孔隙体积逐渐减小。温度进一步升高到镍基合金的熔点1020℃时(图10c),过渡层镍基合金颗粒处于熔融状态,而复合层中的镍基合金颗粒只有部分熔融。由于加入高熔点的WC(2776±10℃),只有部分WC边角发生分解2WC=W2C+C,此时Ni、Cr、Fe等元素向WC周围扩散,与分解的WC形成一些富W的复相碳化物;随着烧结颈的长大颗粒间孔隙越来越小,颗粒之间变得紧实,涂层稍有下沉,熔融的镍基合金颗粒之间出现扩散。随着温度的升高扩散逐渐加剧,熔融的镍基合金溶液与部分分解的WC颗粒在WC颗粒周围形成絮状的富W含Cr复相碳化物,其间充满镍基固溶体;在此温度下镍基合金液的粘度较大,随着熔融的镍基合金溶液不断填充孔隙,其间的WC等硬质颗粒在局部区域发生微移而调整其位置;熔融的镍基合金熔液与基体之间也发生扩散。较高的浓度差使过渡层中的Cr和Ni元素在扩散驱动力的作用下向基体方向扩散,基体中的Fe元素向过渡层方向扩散,在过渡层和基体间形成一个新区 [18,19,20];由于C与Cr的亲和力较大,容易形成Cr7C3、Cr23C6,阻止了C元素和Cr元素的扩散。因此,在扩散熔合区靠近过渡层的一侧主要为Ni基固溶体,靠近基体一侧主要为Fe基固溶体,而在过渡层和扩散熔合区的边缘上聚集一些粗大的针棒状相Cr7C3 、Cr23C6。过渡层中的B和Si在γ-Ni固溶体中溶解度很小,这些元素趋向于晶界和枝晶间区域,Si元素快速扩散与Ni元素结合形成Ni3Si弥散分布在共晶组织中,B元素主要存在于晶界。B元素的存在可抑制M23C6碳化物在晶界上的早期偏聚。随着温度的升高更深层颗粒间烧结颈不断形成以及之前形成的烧结颈不断长大,到如图10d所示的保温阶段(1060℃,保温10 min),过渡层与基体之间充分扩散形成了如图2所示的大约20 μm的扩散熔合区,即镍基固溶体与铁基固溶体交互存在并在该区梯度分布,并在基体上形成了一个250 μm左右的扩散影响区,主要由珠光体组成;聚集在过渡层和扩散熔合区边缘的粗大针棒状相Cr7C3和Cr23C6越来越多。在该阶段复合层中的Ni基合金也处于完全的熔融状态,熔融态的Ni基合金外缘填充到相邻颗粒的间隙中。Ni基合金的熔化提供了足够的液相,使全部WC颗粒完全润湿。被润湿的WC颗粒由于高熔点在粘度较大的镍基合金液中近似悬浮,颗粒间因液相的存在产生毛细管力以及自身的粘性流动,使得颗粒发生移动并重新调整分布位置,直到实现紧密的排列 ;这一过程使整个涂层有一下沉,涂层更加致密而具有更高的力学性能。在保温条件下硬质相颗粒WC的溶解加剧,在液相中较小的颗粒过饱和溶解度较大,使小颗粒优先溶解和大颗粒的边角区域溶解。颗粒表面曲率较大的棱角处的溶解比较明显,使得小颗粒较为圆整,大颗粒棱角趋于圆滑。大颗粒饱和溶解度较低,使液相中部分饱和原子Ni、Cr等在其表面析出,即在WC大颗粒表面及周围形成大量絮状富W的复相碳化物。溶解和新相形成析出同时进行,小颗粒溶解和大颗粒长大使颗粒表面趋于圆滑,颗粒之间相互靠拢收缩。镍基合金液相使颗粒间完全填充,形成了区域内的固相骨架,最终形成致密均匀、结合牢固的复合涂层。
3 结论
(1)使用真空熔覆技术在45钢表面制备的Ni+WC复合涂层,与基体冶金熔合、组织致密均匀,缺陷较少。熔覆层由复合层、过渡层、扩散熔合区、扩散影响区组成,WC和分解生成的富W复相碳化物包围在Ni颗粒周围,其主要组成相有γ-Ni固溶体、Cr7C3、Ni2.9Cr0.7Fe0.36、Cr23C6、Ni3Fe、Ni3Si、Ni3B、W2C及C等。
(2)在真空熔覆过程中熔融从表面开始,随着温度的升高微熔加剧;温度升高到1020℃时过渡层熔化,过渡层与基体之间元素扩散形成一个新区,而复合层只有部分熔融;温度升高到1060℃保温10 min后元素大量扩散形成一个大约20 μm厚的扩散熔合区。这时复合层完全熔融,硬质颗粒重排且部分溶解并析出富W复相碳化物,最后形成由WC和包围在Ni颗粒周围的富W复相碳化物组成的复合涂层。
免责声明:本网站所转载的文字、图片与视频资料版权归原创作者所有,如果涉及侵权,请第一时间联系本网删除。
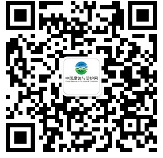
官方微信
《中国腐蚀与防护网电子期刊》征订启事
- 投稿联系:编辑部
- 电话:010-62313558-806
- 邮箱:fsfhzy666@163.com
- 中国腐蚀与防护网官方QQ群:140808414