以热塑性树脂为基体,以纤维为增强体而制成的复合材料——纤维增强热塑性树脂基复合材料(FRTP)是近年来发展迅速的一类纤维增强复合材料。与以往传统的纤维增强热固性树脂复合材料(FRP)相比,FRTP具有很多优点:
① 密度小,强度高。钢材的密度为7.88 g/cm3,FRP的密度为1.7~2.0 g/cm3,FRTP的密度为1.1~1.6 g/ cm3,仅为钢材的16%~20%,比热固性玻璃纤维复合材料(GFRP)的密度还要小。因此,他能够以较小的单位质量获得更高的力学性能。
②韧性比较高。以环氧树脂和PA为例,环氧树脂的断裂后伸长率<10%,而PA的断裂后伸长率则可达60%。
③热塑性树脂成型过程中无需化学反应,因此成型周期短。
④可重复利用。热塑性树脂可反复加热冷却成型,废料可回收利用,达到节能环保的目的。
⑤选用PPS、PEEK等耐热工程塑料作复合材料的基体,可以使得复合材料在更高的温度下使用。
基于上述优势,FRTP越来越受到人们的重视,在航空、体育、汽车等领域的应用日渐增长。
碳纤维(Carbon fiber,CF)是由有机纤维在惰性气氛中经高温碳化而成的纤维状聚合物碳。CF具有很高的抗拉强度,其抗拉强度是钢材的2 倍和铝6 倍,模量是钢材的7 倍和铝的8 倍。与热塑性树脂复合后,更能进一步提高热塑性树脂的性能,扩大应用范围。以PPS为例,CF增强PPS复合材料已用在空客A340和A380飞机机翼的主椽上。美国新泽西Summit的高尔夫球杆制造商Phoenixx golf公司选用CF增强线型PPS来制造高尔夫球杆。
碳纤维增强聚酰胺树脂(PA)
PA是具有许多重复的酰胺基的线型热塑性树脂的总称,俗称尼龙,商品有PA6、PA1010等。PA6本身就是性能优异的工程塑料,但吸湿性大,制品尺寸稳定性差,强度和硬度也不如金属。

碳纤维增强PA粒料
用CF增强改性后,大大提高了PA的力学性能,改性后即可作为结构材料承受载荷,又可作为功能材料发挥作用。孙伟等用双螺杆反应挤出制备了CF/PA6复合材料(CFRPA6),并考察了CF表面处理方法、CF的质量分数和初始CF长度 对CFRPA6性能的影响。指出经过表面处理的CF增强效果较未经表面处理的明显变好,用液相氧化+ 硅烷偶联剂复合处理法比气相氧化和液相氧化的表面处理法要好;CF质量分数9%时,CFRPA6的力学性能最好;CF长度10 mm比5 mm更有利于增强复合材料的各项力学性能,而且并不影响挤出和 CF在CFRPA6中的分散效果。
葛世荣等采用溶剂湿法超声法将空气氧化处理的CF与PA1010混合,而后使用微型注塑机注塑成型。研究发现CF表面氧化处理提高了CF 与PA1010的粘结力;随着CF体积分数的增加,CFRPA1010的抗拉伸强度和洛氏硬度先增加后下降,当CF体积分数为20%和30%时,CFRPA1010 的抗拉伸强度和洛氏硬度分别达到了最大值;CFRPA1010的摩擦系数随着CF体积分数的增加而降低,当CF体积分数达到20%时,摩擦系数稳定在0.24左右。
碳纤维增强聚醚砜树脂(PES)
PES是英国ICI公司在1972年开发的一种综合性能优异的热塑性高分子材料,是目前得到应用的为数不多的特种工程塑料之一。由于它具有优良的自润滑性,加之电绝缘性及阻尼性好,并且可以采用挤出和注塑成型,因而特别适合用于制作干滑动元件,用CF作填料的CFRPES摩擦系数低且耐磨性好。
赵伟岩等采用模压工艺制备CFRPES,并考察CF体积分数及长度对CFRPES/ 固体润滑剂/PTFE(聚四氟乙烯)复合材料摩擦性能的影响。研究发现随着CF体积分数的增加,复合材料的硬度增加;抗冲击强度随CF体积分数增加,先增加后下降,在10%~20%之间达到最高;随着CF体积分数的增加,材料储能模量增加,而损耗角正切逐渐减小,并在CF体积分数达到20%以后渐趋平缓;对于长度为40 ?m及100 ?m的CF,100 ?m的CF增强效果更佳。
郑亮等采用溶液浸渍法制备连续CF增强PES、PPESK、PPBES(共聚型二氮杂萘酮联苯结构聚醚砜)、PEI(聚醚酰亚胺)预浸料,而后将预浸料热压成型制备CF/PPESK、CF/PPBES、CF/PPESK/PES、CF/PPESK/PEI复合材料。研究发现用溶液浸渍法制备的复合材料纤维在树脂基体中分布均匀,纤维与树脂的粘结性能良好;聚合物溶液的粘度越低,浸渍效果越好;所制备的各种树脂基复合材料力学性能随CF体积分数的增加,都呈现先增大后减小的趋势。
碳纤维增强聚碳酸酯(PC)
PC是一种应用广泛的工程塑料,把CF与PC复合后,可进一步提高PC的各种性能,扩展它的应用领域。

碳纤维增强PC笔记本外壳
李春华等用双螺杆挤出法制备CFRPC,并研究了纤维表面处理、纤维长度、纤维体积分数及挤出成型工艺对复合材料性能的影响。研究发现,用液相氧化+硅烷偶联剂复合处理法比气相氧化和液相氧化的表面处理法要好;CF 体积分数增加后,复合材料的力学性能得到显着提高,热变形温度也得到了明显提高;当CF体积分数为13%时,抗屈服强度比纯PC提高了32%,弹性模量提高了近1 倍,热变形温度提高了43 ℃;CF长度10 mm比5 mm更有利于增强复合材料的各项力学性能。
碳纤维增强聚苯硫醚(PPS)
PPS是一种半结晶热塑性树脂,具有卓越的力学性能、耐化学侵蚀性、阻燃性等。张随山等用悬浮熔融法制备CFRPPS预浸带,采用模压工艺制备了CFRPPS。制备的复合材料有很好的力学性能及优良的耐溶剂性,PPS与CF之间的粘结性能优良,证明用悬浮熔融法制备连续CF增强PPS 预浸料是可行的。
邱军等用冷压烧结制备了CFRPPS。研究发现CF(布)的体积分数对复合材料的力学性能影响很大,随着CF(布)体积分数增加,复合材料的力学性能提高。当CF(布)体积分数超过50%时,力学性能开始下降;经CF 表面处理的CF/PPS复合材料的抗拉伸性能和抗冲击性能都得到了显着的提高,且经过丙酮浸泡处理的CF(布)比经过高温处理的CF(布)增强效 果要好。
碳纤维增强聚醚砜酮 (PPESK)
PPESK是一种新型的耐高温聚合物,具有较高的力学性能和良好的耐热性、绝缘性以及耐化学腐蚀性,而且熔解性能好,可用作高性能复合材料的基体。
彭静等将CF等离子接枝处理后与PPESK及固体润滑剂溶液共混干燥后,采用热压成型工艺制作CF/PPESK/固体润滑剂复合材料,考察CF质量分数对复合材料耐磨性能的影响。研究发现少量CF(质量分数5%) 的加入就可以显着提高复合材料的耐磨性能,可降低摩擦系数和提高自润滑效果;当CF质量分数超过5%以后,复合材料的比磨损率变化不大。超过10%后比摩损率稍有增加,但摩擦系数有所减小。
碳纤维增强聚醚醚酮(PEEK)
PEEK是新一代耐高温热塑性树脂,其CFRTP已经用于机身、卫星部件和其他空间结构,PEEK的CFRTP可在250 ℃条件下连续使用。

碳纤维增强PEEK板材针对PEEK熔融粘度大,难于浸渍的特点,隋月梅设计了PEEK/DPS(二苯砜)混合体系冻胶浸渍工艺,在PEEK中加入一定比例的DPS形成固体混合物,再将PEEK/DPS混合物以熔融浸渍的方法浸渍CF,完全浸渍后,去除多余的溶剂,形成CF/PEEK预浸料。考察了纤维张力对熔融浸渍效果及复合材料力学性能的影响,研究发现一定的纤维张力有利于纤维的分散,张力过大时,纤维易集束,不利于浸渍;纤维张力的大小对其复合材料的抗拉伸强度和抗拉伸模量有较大的影响。
碳纤维增强热塑性聚酰亚胺(PI)
PI具有突出的热稳定性,良好的抗冲击、抗辐射和耐溶剂性能,在高温、高低压和高速等极端环境下具有优异的耐摩擦磨损性能,用CF增强后,可进一步提高性能,扩大应用范围。
碳纤维增强PI耐高温复合材料李健将CF表面处理后,采用热压成型工艺制备CF/ PI复合材料。考察了CF质量分数及RES表面改性(稀土溶液处理CF)、空气氧化改性处理对CFRPI力学性能的影响。研究发现,RES表面改性方法优于空气氧化处理方法。当稀土溶液中稀土质量分数为0.3%时,所制得的CFRPI具有最优的力学性能。随着CF体积分数的增加,CFRPI的摩擦学性能得到提高。当CF体积分数为20%时,CFRPI的摩擦系数和磨损量最小。
结 束 语
⑴ 与CFRP相比,选择合适的热塑性树脂基体,可以使CFRTP有更好的耐腐蚀、耐温等性能。CFRTP成型周期短,制品可回收循环利用,但须解决热塑性树脂浸渍问题。
⑵ 对于CF短纤维,可以采取双螺杆挤出的方法制备CFRTP预浸料,而后注塑成型,也可直接将CF与树脂混合后热压成型;对于连续CF,可以采用熔融浸渍或溶液浸渍的方法制备预浸料,而后热压成型。
⑶ 采用不同的CF表面处理方法,均可以提高CF与基体的粘结力,从而提高CFRTP的力学性能,合适的处理方法可使树脂的抗拉伸强度提高40%。
⑷ CFRTP的性能随CF体积或质量分数的提高而提高,力学、耐温、耐磨等性能均有所提高。当CF体积分数为10%~20%时,CFRTP的各项性能最好,热变形温度最高可提高将近50 ℃,常温下的摩擦系数可降低50%左右。但当CF体积分数增大到一定值时,由于树脂基体体积分数的减少,CF与树脂基体的粘结性能降低,从而导致CFRTP各项性能的降低;CF的长度对CFRTP的性能也有所影响。长度稍长的CF增强效果更佳(最长可至10 mm),采用合适的工艺参数则不会影响CF在CFRTP中的分散效果。
免责声明:本网站所转载的文字、图片与视频资料版权归原创作者所有,如果涉及侵权,请第一时间联系本网删除。
-
标签: 碳纤维, 热塑性树脂基复合材料, 现状
相关文章
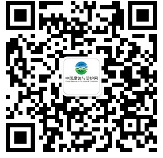
官方微信
《中国腐蚀与防护网电子期刊》征订启事
- 投稿联系:编辑部
- 电话:010-62313558-806
- 邮箱:fsfhzy666@163.com
- 中国腐蚀与防护网官方QQ群:140808414
点击排行
PPT新闻
“海洋金属”——钛合金在舰船的
点击数:5768
腐蚀与“海上丝绸之路”
点击数:4763