定向凝固高温合金是航空发动机涡轮叶片上使用最多的材料之一,其与等轴晶铸造高温合金相比,具有更好的持久性能、抗蠕变性能和抗热疲劳性能等,但其在高温条件下单独使用容易出现氧化及热腐蚀现象。解决这一问题的有效手段是在材料表面施加高温防护涂层,保护基体材料不受腐蚀性元素侵蚀。传统高温防护涂层通常可分为:简单铝化物涂层、改性铝化物涂层、MCrAlY包覆涂层和热障涂层。铝化物涂层是工业上应用最早且应用范围最广的高温防护涂层。
简单铝化物涂层具有较好的抗高温氧化性能,但其存在脆性大,易开裂剥落,涂层退化速率快等缺点。改性铝化物涂层通过在简单铝化物涂层中添加Cr、Pt、Si、Co 或稀土元素Hf、Y等有益元素,有效地降低了氧化速率,并提高了氧化膜与涂层之间的结合力,故具有更好的抗高温氧化性能和抗热腐蚀性能。其中,Pt 改性铝化物涂层因其具有很好的抗高温氧化性能,在工业上获得非常广泛的应用。
近年来,为进一步提高Pt 改性铝化物涂层的性能,研究者尝试在Pt 改性铝化物涂层中添加其他有益元素,利用两种元素的协同效应达到增强涂层使役寿命的目的。Yang 等在Pt 改性铝化物涂层中添加Hf 元素,发现Hf 阻碍β-(Ni,Pt)Al→γ '-Ni3Al 相转变,同时增强了氧化膜抗剥落能力,提高了涂层的抗高温氧化性能。Song 等制备了Pt/Ru 共改性铝化物涂层,研究结果表明:Ru 提高了Pt 改性铝化物涂层的抗剥落能力,增强了涂层的抗循环氧化能力。Zhou等研究发现:Pt/Dy 共改性铝化物涂层比单一的Pt 改性铝化物涂层或Dy改性铝化物涂层具有更低的氧化速率和更好的抗氧化膜剥落能力。
研究发现在简单铝化物涂层中添加稀土元素Zr可以促进α-Al2O3 的形成,抑制有益元素Al 的外扩散,同时消除氧化膜/涂层界面孔洞的形成,增强膜基结合力,降低氧化膜内应力和蠕变速率,提高铝化物涂层的抗高温氧化性能。但关于Pt/Zr 共改性铝化物涂层的研究报道还比较少。为此,文中采用电镀Pt 和化学气相沉积Zr-Al 共渗的方法制备了Pt/Zr 共改性铝化物涂层,并对涂层进行了抗高温氧化性能测试,分析了涂层氧化前后的组织结构形貌。
1 实验方法
实验选用定向凝固镍基高温合金材料,其化学成分(质量分数,%) 为:Co 7.5,Cr 7.0,Mo 1.5,W5.0,Al 6.2,Ta 6.5 ,Re 3.0,Hf 0.15,Ni 为余量。样片尺寸为Φ 30 mm×2 mm,将其边角倒磨成圆角后,依次采用150#、400#和800#砂纸研磨。随后采用喷砂机进行喷砂处理,进一步去除样片表面杂质,同时提高样片表面粗糙度,以增强电镀层与基体之间的结合力。将样片在丙酮、酒精、蒸馏水中依次超声清洗20 min后烘干,并放入Pt电镀液中,沉积一层2~4 μm厚的电镀Pt 涂层。将样品在1080 ℃温度下真空退火2 h,使电镀Pt 涂层与基体发生扩散,提高结合力,同时可除去Pt 涂层中残留的氢气。将Al 源,Zr 源,活性剂NH4F 和惰性填充剂Al2O3充分混合,并放入高温扩散炉中托盘上。用铁丝将样片悬挂在托盘上方。关闭炉门,打开机械泵,待炉内真空低于10 Pa时,使炉内温度升高至1080 ℃,保温4 h 后获得Pt/Zr共改性铝化物涂层(PtAlZr 涂层)。Pt 改性铝化物涂层(PtAl 涂层) 制备工艺除了渗剂中不含Zr 源,其他与PtAlZr涂层工艺相同。
采用高温马弗炉(KXF1400-IV) 对两种涂层进行1000 ℃恒温氧化实验,氧化环境为静态空气。为获得涂层在氧化过程中包含剥落氧化皮在内的增重,将样品放入已烧至恒重的氧化铝坩埚中。随后将装有试样的坩埚放入已达到实验温度的马弗炉中,每隔一段时间取出坩埚,在空气中冷却至室温后,同时称量坩埚和样品的总重量。称重后再将装有样品的坩埚放入马弗炉中继续实验。为提高测量的精确性,每种涂层采用3 个平行试样。称量过程中,每个试样测量至少5 次,增重结果取平均值。本次实验使用天平的感量为1×10-4 g。
采用日本理学D/max-RA 转靶式X 光衍射仪(XRD,PANalytical X'Pert PRO) 分析涂层氧化后的相结构和氧化产物。分别采用钨灯丝扫描电镜(SEM,ZEISS EVO MA 25/LS 25,) 和场发射扫描电镜(SEM,FEI Inspect F) 分析涂层的表面组织形貌和截面组织形貌,并利用电镜附带能谱仪(EDS) 对涂层进行元素成分分析。
2 结果与讨论
2.1 氧化前的组织结构
图1 为PtAl 和PtAlZr 涂层氧化前的XRD 图谱。可以看出:两种涂层的主要相均为(Ni,Pt)Al,同时含有少量的PtAl2相。另外,PtAlZr 涂层中探测到微弱的PtZr 相的衍射峰。图2 为PtAl 和PtAlZr 涂层的截面形貌图。两种涂层均为双层结构,外层呈灰色,主要为(Ni,Pt)Al 相,并未观察到明显的PtAl2和PtZr 相,这是因为涂层中PtAl2 和PtZr 相含量较少;内层为互扩散区,含有大量的重金属元素析出相(呈亮白色)。PtAl 和PtZrAl 涂层外层元素成分(原子分数,%) 分别为:Al 46.16,Cr 1.89,Co 4.5,Ni43.5,Pt 3.9 和Al 44.8,Cr 5.0,Co 5.1,Ni 41.1,Zr 0.4,Pt 3.6。
2.2 氧化动力学曲线
图3 为PtAl 和PtZrAl 涂层在1000 ℃ 下氧化300 h 的氧化动力学曲线,从图中可以看出:前80 h两种涂层氧化增重急剧增加,这主要因为涂层表面元素与空气中氧发生氧化反应形成保护性的氧化铝膜。随后增重进入稳定期,涂层增重缓慢。这是由于氧化膜阻碍了空气中的氧向涂层内扩散,降低了涂层的氧化速率。PtAl 和PtAlZr 涂层的最大氧化增重分别为1.30 和1.22 mg/cm2。
2.3 氧化后组织形貌
图4 为PtAl 和PtAlZr 涂层氧化300 h 后的XRD图谱。从图中可以看出:两种涂层氧化300 h 后,涂层的主要相依然为NiAl 相,并未检测到贫Al 的γ-Ni/γ '-Ni3Al 相,这可能是因为涂层中仅有极少量的Ni-Al 相转化为γ-Ni/γ '-Ni3Al 相。另外,涂层中出现了α-Al2O3相的衍射峰,并没有发现其他氧化物,说明涂层表面发生了Al的选择性氧化。
图5 和6 分别为PtAl 和PtAlZr 涂层在1000 ℃下氧化300 h 后的表面宏观形貌和微观形貌图。从图5 中可以看出:两种涂层氧化300 h 后表面形成了灰色的氧化膜,宏观上氧化膜致密、完整,没有出现明显的剥落和裂纹。在低倍的微观形貌图(图6a 和c)中也可以看到:PtAl 和PtAlZr 涂层表面氧化膜颗粒细小、均匀、致密。采用EDS 分析了涂层表面的元素成分如图7 所示。可以看到:两种涂层氧化后表面主要元素为Al 和O,仅含有极少量的Ni、Cr、W元素,证实涂层表面生成了完整的Al2O3膜。在更高倍数形貌图(图6b 和d) 中可以看到PtAl 涂层表面有裂纹产生,而PtAlZr 涂层表面未有裂纹生成。PtAl 涂层表面的裂纹会破坏氧化膜的完整性,为外界O元素提供扩散通道,加速涂层中有益元素Al 的消耗。
图8 为PtAl 和PtAlZr 涂层在1000 ℃ 下氧化300 h 后的截面形貌图。两种涂层表面均有一层连续、致密的氧化铝膜生成。但在PtAlZr 涂层中,氧化膜下方有黑色的条状物生成,这些氧化物为富Zr 的氧化物。有研究表明:Zr 在高温下向涂层/氧化物界面扩散形成条状氧化物,可以起到钉扎氧化膜的作用,提高氧化膜与涂层之间的结合力。氧化膜下方涂层外层中浅灰色的区域为γ '-Ni3Al 相,深灰色的为β-NiAl 相。在高温环境下外层中的Al 向外扩散形成氧化铝膜,消耗涂层中的Al 元素,使涂层外层发生β-NiAl→γ-Ni/γ '-Ni3Al 相转变。对比图8a 和b可以看出:PtAl 涂层外层中γ ‘相多于PtAlZr 涂层中的γ ’相,说明氧化过程中PtAl 涂层中消耗了更多的Al 元素。另外,在化学浓度梯度作用下,涂层中的Al 元素会向基体内部扩散,而基体中的合金元素也会向涂层内扩散,使涂层内层同样发生β-NiAl→γ-Ni/γ '-Ni3Al 相转变,并在涂层内层下方形成二次反应区。二次反应区的形成消耗了涂层中的有益元素Al,同时也可能影响基体材料的机械性能,因而在涂层与基体之间添加扩散阻挡层,降低基体与涂层之间的互扩散是改善高温防护涂层性能的有效途径之一。
3 结论
(1) Pt/Zr 共改性铝化物涂层外层主要相为β -(Ni,Pt)Al,同时含有少量的PtAl2和PtZr 相;内层含有大量的重金属元素析出相。
(2) 在1000 ℃下氧化300 h 后,Pt 改性铝化物涂层和Pt/Zr 共改性铝化物涂层中仍有大量的富Al 的β-NiAl 相存在,表现出很好的抗高温氧化性能。
(3) Pt/Zr 共改性铝化物涂层比Pt 改性铝化物涂层具有更低的氧化速率,同时具有更致密的氧化铝膜,这是因为在保护性的氧化铝膜下方形成了条状的富Zr氧化物,起到钉扎作用。
免责声明:本网站所转载的文字、图片与视频资料版权归原创作者所有,如果涉及侵权,请第一时间联系本网删除。
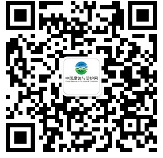
官方微信
《中国腐蚀与防护网电子期刊》征订启事
- 投稿联系:编辑部
- 电话:010-62313558-806
- 邮箱:fsfhzy666@163.com
- 中国腐蚀与防护网官方QQ群:140808414