镍基高温合金凭借其耐高温、耐腐蚀、耐复杂应力等性能,在制作涡轮发动机工作叶片、导向叶片、飞机发动机以及工业用燃气轮机等高温零部件方面具有广泛的适用性,也因此被称作“发动机的心脏”。但当这些零部件在高温、复杂应力,特别 是在海水中等复杂环境下工作时, 容易产生裂纹、磨损、断裂和腐蚀等,致使零部件大量报废。采用增材再制造技术对废旧零部件“再制造”,可使其价值得到最大程度的发挥,获得巨大的经济收益 。
增材再制造技术就是利用增材制造技术对废旧 零部件进行再制造修复:
首先,利用数字加工的一些原理扫描出零部件的3维数字模型;
然后,对数字模型进行后处理,得出缺损部分的3维数字模型;
最后,通过一层一层向上叠加的方式直接快速加工 出缺损部分。
其建立在数控CAD/CAE/CAM 、焊接、新材料等已有的成熟技术基础之上,核心理念是“逐层叠加、分层成形”。自20世纪开始,美国就在B-52轰炸机和M1坦克等军用装备上进行了增材再 制造, 并将武器系统的更新换代和再制造技术列为国防科技重点研究领域。国内也成功地将增材 再制造技术应用在各种军用装备上,产生了巨大的 经济效益 。由于增材再制造技术本身还不够成熟,目前研 究尚处于初级阶段,因此存在许多亟待解决的问题。为此,对基于焊接的增材再制造技术研究现状进行简要介绍,通过对比不同焊接工艺,提出未来发展的研究热点。
1、焊接工艺
钨极氩弧焊
钨极氩弧焊(GasTungstenArcWelding, GTAW)是以钨棒作为电弧一极的气体保护电弧焊。其应用非常灵活,尤其是与激光熔覆相比,可以更容易地处理铜、铝、镁等有色金属的增材再制造。此外,其弧长及电弧稳定性好,焊接电流下限不受焊丝 熔滴过渡等因素制约,最低焊接电流可用到2A。但它自身仍有一些不足:一方面,钨极的承载能力有 限,过大电流容易使钨极烧损,从而限制了熔深;另 一方面,随着电流的增大,钨极电弧的发散变得严重,使得熔池成形之后塌陷,严重影响成形质量。
影响GTAW工艺的因素主要有焊接电流、钨极直径、弧长、电弧电压及焊速等。其中:焊接电流是决定GTAW焊缝成形的关键参数,当其他条件不变时,焊接电流的增加可导致电弧压力、热输入及弧柱直径增加,使焊缝熔深、熔宽增大;弧长范围通常为0.5~3.0mm,当成形件变形小时,弧长取下限,否则取上限;焊接速度是调节GTAW热输入和焊道形状的重要参数,焊接电流确定后,焊速有相对应的取值范围,超过该范围上限,易出现裂纹、咬边等缺陷。
等离子弧焊
以等离子弧为焊接热源的增材再制造方法称为等离子增材再制造(PlasmaAdditiveRemanufactu-ring,PAR)。其中,等离子弧是一种压缩的钨极氩弧,钨极氩弧最高温度为10000~24000K,能量密 度小于104W/cm2 ,而等离子弧的温度高达24000 ~50000K,能量密度可达106~108W/cm2。依靠喷嘴的机械压缩作用,同时伴随着最小电压原理 产生的热压缩以及弧柱本身的电磁压缩,使等离子 弧的能量密度远远超过钨极氩弧,甚至能够达到激光的能量密度 ,图1为二者电弧形态的对比,自由电弧的扩散角约为45°,等离子弧则仅有5°。
与采用激光焊接电源相比,PAR具有绝对的成本优势。据资料显示:常见激光焊接电源一般价格在50万美元左右,而等离子弧焊接电源价格则只有7000美元,不足激光焊接电源价格的2%。与GTAW相比,PAR的工艺调节较为繁琐,主要包括喷嘴结构、电极内缩量、离子气流量、焊接电流、焊接速度和喷嘴高度。其中:喷嘴结构和电极内缩量是其他工艺参数选择的前提,通常根据材料种类和成形条件来确定;离子气流量决定了等离子弧的穿透力,离子气流量越大,电弧穿透能力越强。
激光熔覆成形
以激光为热源的增材再制造成形技术通常被称为激光熔覆成形(LaserDepositionForming,LDF),是目前发展最为广泛的增材制造技术之一。控制LDF成形质量的因素主要有激光功率、扫描速度、粉末粒度、送粉量和载气流量等。与GTAW和PAR相 比, LDF成形过程需要考虑粉末对激光的吸收率。当送粉量一定时,可通过调节激光功率和扫描速度来获得所需的激光能量。LDF的显著特点是能量密度高、电弧热量集中、焊接热影响区小、温度梯度大、 成形效率高,但焊后有很高的残余应力,因此多 采用脉冲方式调节激光的热输入。目前的研究结果表明:采用脉冲激光熔覆成形可获得稍低的热 输入量,能对焊接成形有更好的控制。
相反, GTAW和PAR在提供高热输入量的同时,会增大焊后热影 响区,恶化成形后工件组织性能。采用脉冲工艺,则可利用脉冲峰值电流熔化基材、基值电流维弧,通 过峰值电流与基值电流的交替变化可有效地分散焊接过程的热积累,从而减小焊接热影响区。 Balachandar等研究表明:利用合适的脉冲工艺参数,可以有效地减少GTAW的焊接热影响区,从而在提高焊接接头力学性能的同时,也提高并稳定了焊接接头硬度值, 甚至力学性能优于焊接热处理后的力学性能。Chen等采用脉冲工艺对比分析了小孔PAR和GTAW,结果发现:脉冲等离子弧焊可有效地减小焊接热影响区宽度,且使熔合区的金属组织更为致密。
为了对比在不同焊接工艺下快 速成形的综合有效性, Martina等利用直接成形的宽度、层间高度等参数进行建模,结果表明:PAR 比GTAW和LDF直接成形都具有显著优势。不同 焊接工艺成形性对比如图2所示。总之,基于不同焊接工艺的增材再制造技术各有特点:GTAW效率高、设备成本低,但其输入热量大、零件成形精度不高;脉冲LDF热输入量小、焊接热影响区小,且成形效果优良,但其设备价格昂贵;PAR技术在设备成本上相较于LDF具有显著优势,其沉积效率约为98%,最大沉积率可达到1.8kg/h,成形零件的有效宽度和沉积率高于GTAW和LDF。
2、组织与性能
基于焊接的增材再制造成形技术是一个受多参 数影响的复杂焊接过程:热源能量输入、 CAD模型扫描数据、焊接路径规划,都会对微观组织的形态、 晶粒生长方式、晶界夹杂以及偏析等产生影响,进而影响镍基高温合金的整体性能。国内外学者对此作了大量深入的比较研究。
成形件组织特征
何绍华利用Inconel718合金通过LDF得到了成形件,对其沉积态组织进行深入分析得出:熔覆层组织是由具有方向性生长的柱状枝晶组成,生长 方向为由基体向外,并且在枝晶间有Mo、Nb等元素的偏析及少量碳化物生成,这对基体的拉伸强度产 生不良影响,试验测得沉积态试样室温情况下的拉伸强度不足变形合金的50%;而经过热处理工艺后,晶粒被细化,消除了部分枝晶偏析,较好地提高了试件的屈服强度和抗拉强度。这与美国Dinda等的研究结果相似,后者发现沉积态柱状晶能够定向生长,为沿着沉积轨迹高度向上。不同的熔池 冷却速率是导致成形件从下到上组织不均匀的原 因,如图3所示。同时,Dinda等研究发现:在热处理时,在1200℃的温度下柱状枝晶能够转变成等轴晶,且在700℃下γ‘和γ″相的析出使试样的显微硬度增高。
图3 镍基高温合金激光快速成形沉积态组织特性
徐富家采用PAR成形了Inconel625薄壁零件,如图4所示,结果表明从底部到顶部组织呈现不 同的形态特点:
1)底部组织呈现细小的胞状晶,没有发达的二次枝晶;
2)中部组织为明显的胞状枝晶形态, 并且枝晶间距增大;
3)在试样上部出现了较为发达的二次横枝,枝晶间距明显增大;
4)在试样顶部则出现了由柱状晶向等轴晶转变的过渡区。
文献作者研究发现:在增材再制造过程中,温度梯度增加、冷却速度增大、热输入量减小都可以使组织形核率增大,从而使晶粒变得十分细小,也使整体组织更为细密,试验测得这种情况下成形件的拉伸力学性能有所提升。上述研究结果表明:冷却速率和热输入量的变化是沉积态组织柱状枝晶形成的原因,且大多都是定性的描述,对枝晶的大小、分布及间距与冷却速率和热输入的定量关系研究较少。
工艺参数对组织性能的影响
扫描路径
乌日开西·艾依提采用PAR技术研究了不 同扫描路径对成形件力学性能的影响, 结果发现:沿扫描路径平行方向的试件抗拉强度高于其他方向,且塑性最优,这表明成形件在宏观上具有各向异性。席明哲等采用多向组合方式(不同方向交替熔 覆)得出的试样则表现出各向同性,试件的抗拉强度优于焊丝, 而前者塑性低于焊丝。Liu等根据不同沉积路径的变化对Inconel718合金LDF组 织及性能进行了系统研究,结果发现:单一沉积路径和变化沉积路径得到的试样抗拉强度相当,但是前者的延伸率明显低于后者。在特定路径条件下,增材再制造所得的成形件在性能上呈现出各向异性,因此垂直于成形方向上增材部分与基体结合处的力学性能研究就显得尤为重要,但目前国内在此方面的研究较少。
热输入
费群星等研究了LDF不同工艺参数对试件 组织和性能的影响,结果发现:
1)沿沉积方向的重熔区截面呈片状,多为柱状晶,且晶粒向上呈放射状生长;
2)当加大激光功率、增加热输入量时,可观察到晶粒的跨层生长现象,重熔区厚度显著增大;
3)过高的功率会使热积累加大,从而使试样产生织构,柱状晶外侧界面容易产生热裂纹。
Ganesh等 在 研究工艺参数对成形性能影响时发现:工艺参数可影响沉积效率,促使组织形态发生明显变化,形成柱状枝晶和胞状晶的混合形态。徐富家等研究峰值电流、脉冲频率、焊接速度和送丝速度对PAR成形件组织性能影响时发现:低峰值电流和高焊接速度可获得细小致密的枝晶组织,析出的Laves相和金属碳化物呈弥散分布特征;增大脉冲频率或降 低送丝速度会使组织粗大,Laves相和金属碳化物增多, 且呈连续分布特征。上述研究结果反映了增材再制造过程中循环热输入产生的热积累效应对成形件组织与性能的影响 规律,但是均采用定性描述,缺乏对热积累效应的定 量研究。
冷却速度
由于GTAW热输入量较小、能量密度较低,因此成形件受热过程中冷却速度低于PAR、LDF。王威等系统研究了不同冷却速度对Inconel718合 金碳化物、Laves相析出规律的影响,如图5所示。上述结果表明:
1)冷却速度较低时,碳化物呈 链状分布在枝晶间,呈大块状相连;
2)随着冷却速度的加快, 碳化物逐渐向小块状转变,尺寸也随之减小;
3)聚集状态类似于碳化物,而随着冷却速度的加快,呈弥散分布且尺寸逐渐减小 。
Yin等提 出碳化物的析出量和析出形态均会对合金的力学性 能产生重要影响,弥散分布且尺寸较小的碳化物形貌更优。当Laves相尺寸每减小1μm时,室温断面收缩率就可提高2.5% 。目前还无相关报道证明 完全消除Laves相是可行的,因此探讨工艺参数对Laves相尺寸数量的定量影响关系具有重要意义。
3、发展与展望
针对增材再制造技术工艺及组织性能的特点, 未来研究热点将集中在以下方面:
1)提高成形件精度,减小热影响区。引入脉冲 工艺,通过调控峰值电流、基值电流、脉冲频率、占空 比等工艺参数,准确控制增材再制造热输入量及冷却速率,从而较好地控制熔池尺寸, 提高成形精度。
2)优化成形件组织。
一是研究枝晶的大小、分布及间距与冷却速率和热输入的定量关系;
二是研究垂直于成形方向上增材部分与基体结合处的力学性能,避免各向异性带来的不利影响;
三是研究再制造过程中循环热输入产生的热积累效应对成形件组 织与性能的影响规律,降低有害Laves相的析出,从而提高成形件的力学性能。
更多关于材料方面、材料腐蚀控制、材料科普等方面的国内外最新动态,我们网站会不断更新。希望大家一直关注中国腐蚀与防护网http://www.ecorr.org
责任编辑:庞雪洁
投稿联系:编辑部
电话:010-62313558-806
中国腐蚀与防护网官方 QQ群:140808414
免责声明:本网站所转载的文字、图片与视频资料版权归原创作者所有,如果涉及侵权,请第一时间联系本网删除。
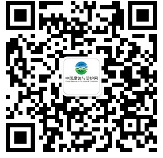
官方微信
《中国腐蚀与防护网电子期刊》征订启事
- 投稿联系:编辑部
- 电话:010-62316606-806
- 邮箱:fsfhzy666@163.com
- 中国腐蚀与防护网官方QQ群:140808414