0 前言
随着航空工业对涡轮发动机的推力、推重比及燃油效率的要求越来越高,发动机的进口温度和燃气压力逐渐增大,发动机的压气机及涡轮叶片部分服役环境更加恶劣,特别是叶尖部分。在这种恶劣环境下,要求所使用的叶片金属材料( 镍基、钴基高温合金,单晶高温合金,钛合金等) 既要有优异的高温力学性能( 蠕变性能、持久性能、疲劳性能、韧塑性能等) ,又要具备良好的抗热腐蚀、抗氧化、抗磨损等性能,然而这两者难以兼顾。为了提高发动机叶片的高温性能,科研工作者一方面致力于提高高温合金的耐热性能,如目前已研制出的第四代镍基单晶高温合金承温能力已达1180 ℃; 同时采用先进的气膜冷却技术,如叶片冷却气膜设计及制造工艺的改进,能使叶片表面温度降低300~500 ℃。据报道,目前已发展到第五代高温合金,每代高温合金的提升温度为30 ℃,提温速度缓慢,显然不能解决这2 个问题。因此,在另一方面,科研工作者致力于研究高温合金的防护涂层。
近年来,国内外对叶片防护涂层进行了深入研究,独特设计理念的新型叶片高温防护涂层的报道越来越多,但是对于叶尖部分的防护涂层报道较少。涂覆在叶片叶尖表面的封严涂层材料,特别是应用于800 ℃以上高温段的叶片,承受的工作应力和温度较高,同时应力和温度的变化也比较频繁和剧烈,还存在腐蚀和磨损问题,对磨的氧化锆基、MCrAlY 基可磨耗封严涂层较低温段可磨耗封严涂层硬度相对较高、润滑性相对较差。叶片叶尖的服役环境较叶身要恶劣得多,对材料的综合使用性能要求也要高得多,叶尖涂层还需做进一步的深入研究。本文分析了叶片叶尖损伤的原因,在此基础上总结了航空发动机叶片叶尖高温防护涂层的性能要求。对国内外多种设计理念的叶尖防护涂层进行了阐述,综述了叶尖涂层最新研究进展,提出了目前叶片高温防护涂层存在的问题并展望了其发展趋势。
1 叶尖失效方式及性能要求
1.1 失效分析
1.1.1 裂纹及磨损
叶尖部分的磨损及裂纹是其常见的失效形式之一,如图1 和图2 分别是某型发动机叶尖裂纹显微形貌和磨损形貌。柴志刚等对某涡轮发动机I级涡轮叶片叶尖涂层剥落进行了失效分析。经宏观显微镜和电子显微镜观察后,发现有2 片叶片叶尖排气边涂层剥落,剥落厚度最高达1 mm。叶盆侧涂层基本剥落,断口整齐,残留少量涂层且边缘粗糙。有的叶尖涂层虽然未剥落,但是涂层局部区域鼓起,有裂纹产生。初步分析,涂层剥落主要由烧蚀引起,叶片工作时的超温现象导致了叶尖处基体γ‘相粗化。根本原因是发动机在大修试车过程中T3 温度超温。此外,叶片叶尖会与机匣发生瞬时摩擦,导致涂层的磨损。史文军等分析某机型低压压气机叶尖摩擦故障时发现,零件制造、发动机工作及环境因数的影响会导致机匣产生局部变形,引起叶片和机匣之间的间距减小,导致机匣和叶尖发生瞬时摩擦使叶尖受损。
1.1.2 热腐蚀和氧化
热腐蚀和氧化也是叶尖受损的重要原因。徐建等发现叶尖表层材料的腐蚀和氧化会导致叶尖裂纹的形成。在分析某型航空发动机高压涡轮工作叶片叶尖裂纹产生原因时,指出叶尖裂纹的形成与扩展是环境因素和热应力复合作用的结果,先产生腐蚀后形成裂纹: 首先涂层表面发生衰变并形成局部腐蚀坑,在热循环过程中起缺口效应,形成微裂纹; 裂纹出现后,氧化物和碳化物等腐蚀产物在微裂纹内部形成并如“钉子”一样深入到金属内部,形成“钉扎效应”;在循环应变下对裂纹尖端处造成附加应力,使裂纹进一步扩展。这一热腐蚀过程使裂纹面氧化增宽并且材料晶界腐蚀为分叉裂纹提供核心,并在热应力作用下扩展。
1.1.3 扩散退化
扩散会引起涂层的退化,特别是对于高温下工作的叶尖涂层,涂层和涂层之间、涂层和基体之间会发生扩散,最终导致涂层失效。以航空发动机叶片热障涂层为例,如图3 为1 种热障涂层及其在1 100 ℃高温下经100 h 氧化后的截面形貌。金属粘结层表面有1 层热氧化生长层( TGO) 产生,并且金属粘结层和基体金属之间的互扩散导致基体内部形成了二次析出相( SRZ) 。
1.2 叶尖防护涂层性能要求
叶尖涂层主要有2 个作用: ( 1) 作为封严涂层,减少叶片和机匣之间的间隙,提高气密性,从而保证发动机的效率; ( 2) 保护叶片基材。根据对发动机叶片叶尖失效原因的分析,对叶尖涂层提出以下性能要求。
1.2.1 优良的抗热腐蚀和抗高温氧化性
航空发动机涡轮叶片和压气机叶片通常使用力学性能优良的高温合金,如镍基高温合金、钴基高温合金等。虽然叶片基材在高温高压下具有优良的力学性能,但是易于受到高温气体的氧化作用和严重的热腐蚀。一旦高温合金暴露于此种恶劣的环境下,叶片极易受损失效。因此,在高温环境下,要求叶尖表面能形成完整而致密的保护膜,使高温合金基体免受高温氧化和腐蚀。
1.2.2 界面稳定性
( 1) 在高温下,薄膜和基体的力学性能以及界面状态都会发生一定的变化,其匹配性必须得到充分考虑。
涂层的组织结构稳定,使用过程中不易发生相变退化,并且在与基体的界面处不形成有害相( TCP 相) 。
( 2) 高温防护涂层与基材之间的互扩散可导致涂层退化以及基材中脆性相的产生,从而造成涂层/合金体系高温抗氧化性能和力学性能的下降。将传统的高温防护涂层如Pt 改性铝化物涂层或MCrAlY 包覆涂层应用于镍基单晶高温合金上时,涂层和基体发生了互扩散,在基体/涂层界面生成了二次析出相( SRZ) 有害层。所以防护涂层应具有扩散阻挡性能。
1.2.3 高温耐磨性
封严涂层技术是提升发动机性能的重要气路封严技术之一。为了保证涡轮效率,需要减小叶尖和机匣之间的间隙,一般在机匣内表面和叶尖部分都制备了封严涂层。由于飞行中瞬态载荷或机动过载等原因,通常会引起涡轮叶尖径向间隙骤然缩小,叶尖与机匣接触,发生干涉磨擦。为了防止涂层磨损失效而导致间隙增大,甚至暴露叶片基材,涂层需要有优良的高温耐磨性能。
1.2.4 抗热震性
涂层与金属基材的热膨胀量不匹配,受热时涂层内将产生内应力,当涂层所经受的循环应力幅高于涂层的疲劳强度极限时,涂层内将产生裂纹。涂层热震失效的本质为循环应力作用下的疲劳失效,其失效过程包括裂纹形成、扩展及最终剥落3 个阶段。发动机叶片工作情况是一个高温低温反复循环的过程,为防止涂层和金属基材线膨胀系数之间的差异,导致在温度剧变时涂层剥离和破坏,要求叶片涂层尤其是叶尖部分需要具备优良的抗热震性能。
2 单层涂层
直接应用于叶尖的单层结构高温防护涂层比较少见,复合涂层及层状结构涂层应用较多。单层涂层在某一性能上特点突出,但综合性能有所欠缺,研究此类涂层对复合涂层及多层涂层的研究具有参考意义,可做为复合及多层涂层的一部分。
2.1 铝化物涂层
早在1911 年,有研究者提出了采用粉末包埋法( pack cementation) 制备铝化物涂层———渗铝涂层。作为第一代高温防护涂层,渗铝涂层具有良好的抗氧化性能,以镍基高温合金为例,发挥其性能作用的是β -NiAl 化合物相。涂层的制备方法还包括热浸渗铝( hotdipcoating) 、料浆渗铝( slury coating) 、化学气相沉积( CVD) 渗铝等。从20 世纪50 年代开始,渗铝涂层被大量应用于镍基和钴基高温合金涡轮叶片及导向叶片,有效提高了叶片的抗氧化性能。
传统的热扩散铝化物涂层制备技术( 如粉末包埋、料浆扩散法和化学气相沉积等) 存在涂层有害元素掺杂和有毒气体释放等问题。沈明礼等研发出颠覆传统的“绿色”渗铝技术,获得了亚微米级超细晶β -NiAl 渗层,其抗高温氧化性和抗热腐蚀性能超越了传统的渗铝工艺所制得的涂层,并且作为保护涂层可应用于航空发动机叶片。
渗铝涂层抗氧化性能好,可应用于发动机叶片叶身,但是不能满足叶尖部分的使用要求,并且涂层还存在一些缺点,王俊一发现,此类涂层脆性大,易开裂和剥落; 涂层/基体易发生互扩散,涂层性能退化速度快; 富镍的NiAl 相易发生马氏体相变; 不耐硫化和热腐蚀等。
2.2 改性铝化物涂层
为改善单渗铝涂层的性能,张忠礼通过多元共渗,制得了改性的铝化物涂层,即在单渗铝的基础上,在铝化物涂层中加入铬、硅、铂及稀土元素等,达到改善其性能的目的。
Cr 元素的加入可以明显提高涂层的抗热腐蚀性能,减缓涂层和基材之间的互扩散,避免涂层的退化,同时能促进Al 的选择性氧化形成Al2 O3膜。王占考等利用化学气相沉积( CVD) 法在单晶高温合金基体上制备了铬改性铝化物涂层。铬改性涂层在1 000℃下高温氧化200 h 内涂层保持良好的表面形貌,但在300 h 后出现脱落。
涂层中加入适量的Si 比加入Cr 有更好的抗高温氧化性能,能减缓涂层和基材之间互扩散引起的的退化,并且对其抗热腐蚀性能提高也有一定作用。刘磊等利用CVD 在Inconel 718 镍基高温合金表面制备了120 μm 厚的Si 改性铝化物涂层。进行1 100 ℃高温氧化试验后发现,所获得的Si 改性铝化物涂层在氧化增量阶段比单一铝化物涂层增量小,说明Si 的加入改变了试样表面的氧化机制,有效促进了表面Al2O3氧化膜的形成,同时抑制了Fe、Cr 等合金元素的氧化。
Pt 的加入可以提高α -Al2O3膜的抗剥落和自愈能力,增加铝化物涂层的组织稳定性,降低涂层与基体之间的互扩散[25]。戴建伟等[26] 采用化学气相沉积( CVD) 方法在单晶高温合金基体上制备了铂改性铝化物涂层,研究了其高温氧化行为,并与单一渗铝涂层进行了对比。结果发现Pt 元素的加入既可减缓β→γ’的相变速率,又可有效阻挡基体中难熔金属元素的外扩散行为,保证了高质量α -Al2O3保护膜的生成。
利用稀土的活性元素效应可以改善涂层的抗氧化性、抗硫化性和热疲劳性能。刘得波等研究了稀土La 对渗铝涂层的表面改性和作用机理。分析发现,La元素的加入可以促进渗铝过程,并且能细化渗层的组织,提高表面质量。在高温氧化过程中,渗铝涂层表面形成了致密的氧化膜,氧化增重速率降低,涂层的抗高温氧化性能提高。Zhang 等利用传统的粉末包埋法,将Y2O3 /CeO2部分代替Al2O3,在镍基表面制备了改性铝化物涂层。在1 000 ℃的循环氧化下,Y2O3对θ -Al2O3的生长起抑制作用,CeO2对θ -Al2 O3相向α -Al2O3相的转化起促进作用,最终的效果都是提高了涂层的抗氧化性能。
改性铝化物掺杂了不同的元素,其性能具有一定的差异,主要是为了提高抗高温氧化性能和抗热腐蚀性能,虽然涂层的耐磨等性能有所欠缺,但是可作为金属粘结层应用于叶尖双层结构耐磨涂层。
2.3 MCrAlY 包覆涂层
MCrAlY 包覆涂层最早于20 世纪60~70 年代发展起来的,如今已经发展成一系列涂层体系,其中M 为Fe,Co,Ni 或者它们的组合。其中Al 是用来形成保护性的氧化膜,Cr 可以改善涂层的抗热腐蚀性能,同时也能促进Al2 O3的形成,钇元素可以提高涂层的黏附性。此外,涂层中还可以加入Hf、Si、Ta、Re、Zr、Nb 等元素对涂层进行改性,以满足特定的性能要求。包覆涂层与扩散涂层的区别是涂层只和基材相互结合,基材不参与涂层的形成,因此,涂层的成分具有更多的选择性。MCrAlY 是一种比较理想的涂层,同时具有抗高温氧化和抗热腐蚀性能,还有很好的韧性和抗疲劳强度,因此,可以应用于叶尖防护涂层,如早期普惠公司JT9D-70 发动机的第1、2 级叶片采用了等离子技术在叶片上涂覆了MCrAlY 涂层。
Hu 等运用激光熔覆的方式将改性MCrAlY 沉积到某种涡轮叶片叶尖端面,使沉积厚度高于预定尺寸,然后进行叶尖加工至精确尺寸。改性的MCrAlY 涂层与高温合金基体之间形成了冶金结合,结合强度高并且抗高温氧化性能和抗热腐蚀性能得到了提高。
2.4 高温微晶涂层
王福会等 研制出了一种全新的高温防护涂层———微晶涂层。大多数高温防护涂层的特点是涂层与基体合金的组成材料不同,高温环境下,涂层和基体间界面发生扩散,易产生对抗氧化性能和材料力学性能有害的脆性相,还可能改变涂层的成分,引起涂层的性能的退化。而微晶涂层的成分与基体合金完全相同,因此可以避免此类现象。
侯少军利用多靶磁控溅射法在镍基单晶高温合金表面制备了β -NiAl 微晶涂层,晶粒的大小为300 nm~1 μm。在经过1 100 ℃下恒温氧化和循环氧化的测试后,与传统的电弧离子镀NiCrAlY 涂层做了对比,发现微晶涂层表面只生成单一的α -Al2O3氧化膜且氧化膜连续、生长缓慢、黏附性好,涂层具有很强的自愈能力,经200 h 循环氧化涂层表面没有明显脱落,而NiCrAlY涂层在循环氧化的过程中出现了脱落,并且微晶涂层中涂层/基体界面下方没有观察到明显的SRZ 或TCP 相形成,说明微晶涂层具有良好的抗高温氧化性能。另外,Shin 等在镍基单晶高温合金表面利用脉冲激光制备了镍基高温合金薄膜,随着脉冲能量和基体温度的上升,薄膜内出现了明显的强化多晶结构并且薄膜表面平整。
2.5 陶瓷涂层
陶瓷涂层耐热性好,不易发生腐蚀氧化、硬度高且表面致密。应用于发动机叶片叶尖的陶瓷涂层能提供优异的高温防护性能。Bintz 等在叶尖金属表面镀覆了一层陶瓷薄膜( 包括TiN、TiAlN、Al2O3、BN、SiCN、TiCN、TiO) 。此涂层可以避免对于不同基材的叶片采用不同的陶瓷涂层,如铝合金叶片。氧化铝涂层更适合Ti 合金叶片,可以使用氧化钛或者氮化钛涂层。涂层可以采用物理气相沉积或者料浆法制备,制得的涂层对叶片基体起到了很好的保护作用。
3 复合涂层
包括金属与陶瓷颗粒的复合涂层,层状复合涂层及层状与颗粒的复合涂层。一般单一结构涂层对叶尖某一性能具有提升作用,但对于叶尖高温防护而言远远不够,相比单一结构,复合涂层在提升叶尖综合防护性能方面具有更大的优势。
3.1 金属/陶瓷颗粒复合涂层
叶尖涂层不仅需要足够高的抗高温氧化性及抗热腐蚀性能,还需要很高的耐磨性能。复合涂层一般由耐磨微粒材料和抗氧化的合金基质材料组成。耐磨微粒通常为硬质陶瓷颗粒,如碳化钨、氧化铝、氧化锆、氧化铬、立方氮化硼、碳化硅等碳化物或氧化物陶瓷材料,或者金刚石等硬度较大的材料。这些微粒通常为纳米级或者微米级,或者两者混在一起使用。复合涂层中的硬质颗粒可以通过细晶强化、弥散强化、位错强化等作用来实现复合涂层的结构强化; 在叶尖与机匣封严涂层的对磨过程中,硬质颗粒可对涂层起到一定支撑作用,并且可利用突出于涂层表面的颗粒的超强硬度和不规则边角对机匣封严涂层起到刮削作用,能清除磨削,减缓粘性磨损; 硬质颗粒在摩擦过程中还可以抵抗塑性变形、阻碍磨料运动及终止磨痕扩展等作用。关于耐磨粒子的嵌入涂层的方式目前有2 种思路,( 1) 颗粒在涂层内部,主要发挥其支撑和强化涂层的作用,使涂层的硬度和耐磨性得到提高,另一种是颗粒子露出涂层表面,这样的好处是露出硬质颗粒顶部可以切入机匣封严涂层,不仅能使涂层耐磨性能提高,也能进一步减小叶尖机匣之间的间隙,Allen提出了在叶尖表面制备具有切削功能的涂层,该涂层表面排列无数“金字塔”状的耐磨尖端,在叶片工作时,能切入机匣涂层,减小间隙提高效率。
应用于叶尖的复合涂层要同时兼顾高温耐磨、抗高温氧化与抗热腐蚀等性能。所以,研究者提出利用耐磨陶瓷颗粒与MCrAlY 包覆涂层进行复合,这样制得的涂层不仅能保留包覆涂层的高温性能,而且能提高其耐磨性能。胡泽祥等利用激光熔覆技术在纯钛表面制备了NiCoCrAlY/HfB2复合镀层,所制得涂层的平均显微硬度约为850 HV2 N,涂层与基体呈冶金结合,涂层具有较好的高温耐磨性能。同样,Guo 等利用激光熔覆技术在纯钛表面制备了NiCoCrAlY/ZrB2复合涂层,研究发现相对于单一的NiCoCrAlY 涂层,NiCo-CrAlY/ZrB2复合涂层具有更好的微观硬度和高温耐磨性能。
目前,国外关于单层复合涂层应用于叶尖部分已有相关报道。Liu 等利用冷喷涂的方式,将耐磨粒子( 如CBN) 直接喷涂到叶尖金属涂层表面,形成复合涂层,方法: ( 1) 将叶片喷涂完后安装在叶盘上,( 2) 将叶片表面遮挡,直接进行冷喷涂。
3.2 层状复合
双层涂层既可以是2 层金属涂层,也可以是由陶瓷层和金属粘结层组成的热障涂层。Hu 等报道了一种可应用于叶尖的涂层,该涂层是由MCrAlY 和改性MCrAlY 组成的双层涂层,具有良好的抗热腐蚀性能和高温氧化性能,而且具有很高的耐久性,涂层与基体结合牢固。目前广泛采用的是热障涂层,其中陶瓷涂层起隔热作用,同时兼具一定的耐磨性能,陶瓷涂层和基体金属之间为改性渗铝涂层或MCrAlY 粘结层,起着改善基体和陶瓷层物理相容性和抗氧化腐蚀的作用,双层结构制备工艺简单、隔热性能强,也可应用于整体叶片。
3.3 层状与颗粒复合涂层
在层状结构的涂层中混入陶瓷颗粒,可以有效增强涂层的耐磨性能,减小叶尖和机匣的间距。混合耐磨颗粒部分露出陶瓷外表面,有部分颗粒穿插于陶瓷层和金属粘结层( 图4 为一种叶尖涂层的结构示意图) 。这样设计的目的不仅能提高的涂层的耐磨性能,同时,露出陶瓷表面的硬质颗粒尖端可以切入机匣封严涂层表面,形成特定的运行轨迹,减小叶尖和机匣之间的间隙,从而提高了发动机效率和输出功率。复合双层涂层目前面临的问题是: 硬质颗粒的选材问题,需要足够高的硬度,与外沿涂层具有良好的相容性并且在高温下不发生氧化; 外沿涂层需要足够的耐高温耐腐蚀性能,可以选用渗铝涂层或者陶瓷涂层等,和硬质颗粒相容,结合牢固; 粘结层需要很好的耐高温性,重要的是要与基体和外沿涂层结合牢固,保证涂层的稳定性。
Schell 等提出在陶瓷涂层和金属粘结层组成的热障涂层中嵌入SiC 颗粒,并且颗粒贯穿陶瓷涂层和金属粘结层,部分颗粒露出陶瓷涂层外表面。金属粘结层采用MCrAl 或NiCrCoAl 合金涂层,在保证热障涂层原有高温性能的条件下,使涂层的耐磨性能得到了进一步提高。但需要考虑的问题是陶瓷涂层与硬质颗粒的相容性问题,颗粒和陶瓷涂层的选材显得尤为重要。
除了最外层使用陶瓷涂层,使用金属涂层的报道也很多。为了保证硬质颗粒不脱落,具有足够的使用寿命,Wilson 等提出了一种复合涂层的制备方法。
以SiC 为耐磨颗粒,外层使用具有自修复性能的MCrAlX( 其中M 指的是Ni、CO 或Fe,X 指的是Y、Zr或Hf) 涂层,涂层与SiC 相容性良好,保证了SiC 的耐久性硬质颗粒除了SiC,还有硬度更高的氮化硼。Laul等制备了一种复合双层涂层,涂层包括CBN 硬质颗粒,金属粘结层CoNiCrAlY 以及最外层的经扩散处理( 渗铝) 的NiCoCrAlHf 涂层。CBN 镶嵌于外层,在粘结层以上,经扩散处理的外层表面形成了渗铝涂层,提高抗氧化性能的同时,也保证了CBN 的牢固结合。这种结构的涂层既保证了耐磨性能,也保证了涂层的抗氧化和腐蚀性能。而且,金属粘结层和外层都可以掺杂其他元素进行改性,进一步提升性能。
4 存在的问题和发展趋势
国外关于航空发动机叶尖涂层的研究起步较早,我国起步较晚,技术落后于美国等航空工业发达的国家。航空发动机叶片工作环境恶劣,尤其是叶片的叶尖部分,叶片的使用寿命往往与叶尖相关。就目前而言,叶尖防护涂层的研究比较少,相关涂层技术具有很大的潜力和良好的发展前景。和多数防护涂层一样,叶尖涂层仍然有许多问题需要解决,如涂层的结构设计、涂层的综合高温性能、涂层与基体的结合强度、涂层的制备工艺以及如何应用于叶尖等。因此,在前面对国内外相关涂层的研究进展的综述基础上,对应用于叶尖的防护涂层进行以下几点展望。
4.1 叶尖涂层的成分与结构优化
单层涂层的综合性能有所欠缺,其中铝化物涂层及微晶涂层可以达到很高的抗氧化和热腐蚀性能,但是耐磨性能有所欠缺,应用于叶尖受到限制。对于陶瓷涂层,单独使用的情况下,虽然其隔热效果好、硬度高,但是其与叶片的物理相容性很差、热导率较低。
MCrAlY 涂层虽然也有直接应用于叶片及叶尖的报道,但是随着发动机温度的提升,性能达不到要求。单层复合涂层相对其他涂层综合性能有所提升,所以应用于叶尖部分仍有很大的发展潜力,但有许多问题有待优化,如利用复合电镀制备高温耐磨复合镀层,需要考虑的问题有涂层基质金属的选择以及耐磨粒子的选择、电镀的方式以及镀液的分散等。
双层涂层的设计优于单层涂层,双层涂层将2 种不同性能的涂层结合起来,如热障涂层,包括陶瓷涂层和MCrAlY 涂层。但是涂层之间的结合强度、涂层之间的扩散、涂层之间的适配型以及加入耐磨颗粒后带来的问题都影响着涂层的性能和使用,为了避免这些问题,涂层结构更加多元也更加复杂。所以,今后发展多层涂层以及梯度涂层具有良好的前景,但是多层及梯度涂层制备工艺复杂,实际应用较为困难,因此,多层及梯度涂层的优化问题需要进一步研究。
双层涂层在服役中可能会出现涂层内热应力不匹配,涂层和基体、涂层和涂层之间发生互扩散,导致涂层的退化等问题,因此有研究人员提出发展多层结构和梯度结构系统。多层结构每层涂层性能不同,一方面延缓涂层的扩散,另一方面缓和涂层之间的热应力,增强涂层的稳定性。梯度涂层的基本思想是将2 种或2 种以上不同材料制备成梯度分布的复合材料,使得材料具备非梯度结构达不到的功能,但是多层体系涂层的热化学行为复杂,涂层的制备工艺繁琐,许多技术问题尚未得到解决,限制了其实际应用。多层结构和梯度结构涂层的综合性能很强,适用于性能要求极高的叶尖涂层,如果能解决技术上的难题,将会有良好的应用前景。
4.2 叶尖涂层的制备工艺
开发国内关于叶尖涂层制备工艺的研究报道较少,我国多项技术还处于起步阶段和实践证明阶段,在叶尖涂层的制备工艺研究方面与美国等发达国家相比存在巨大差距。叶尖表面复杂,尺寸精度要求高,涂层的实际工程应用也将是一个巨大的问题。叶尖涂层的结构朝着多层化发展,涂层的制备工艺不仅仅是单工艺的应用,而是多工艺的结合。工艺研究及工艺优化对涂层制备成本和制备效率具有重要意义。国外已经具备比较成熟的技术,因此不断引进和吸收国外先进技术,将实验室研究和工程化应用相结合是一个努力方向。
4.3 叶尖涂层失效及修复研究
叶尖防护涂层在高温工作环境下失效是一个非常复杂的过程,其失效受多种因素影响。叶尖的工作环境较整体叶面恶劣,因此叶尖是发动机叶片最易受损的部位。目前国内对叶尖受损机理的研究较少,对于受损叶片的分析和修理也是基于一个具体案例,如果能建立一个更加系统化、规范化的分析机制,对叶尖的损伤原因进行分类归纳,对以后损伤叶尖的分析及修复提供一个更加标准的参考依据,对于提高效率和节约成本具有显着意义。
更多关于材料方面、材料腐蚀控制、材料科普等方面的国内外最新动态,我们网站会不断更新。希望大家一直关注中国腐蚀与防护网http://www.ecorr.org
责任编辑:王元
《中国腐蚀与防护网电子期刊》征订启事
投稿联系:编辑部
电话:010-62313558-806
邮箱:fsfhzy666@163.com
中国腐蚀与防护网官方 QQ群:140808414
免责声明:本网站所转载的文字、图片与视频资料版权归原创作者所有,如果涉及侵权,请第一时间联系本网删除。
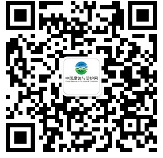
官方微信
《中国腐蚀与防护网电子期刊》征订启事
- 投稿联系:编辑部
- 电话:010-62313558-806
- 邮箱:fsfhzy666@163.com
- 中国腐蚀与防护网官方QQ群:140808414