高压电力设备由于常年暴晒在户外环境中,因此需要涂装相应的防腐蚀涂料进行保护。涂料大多是有机高分子聚合物,形成涂层后是一种绝缘体材料,在高压强直流电场作用下会产生较强的静电场。静电荷若是在绝缘材料上大量积聚,会导致电力设备无法使用。为此,抗静电涂料应运而生。一般表面电阻率在106~109 Ω·cm-2之间、体积电阻率在105~108 Ω·cm之间的涂料称为抗静电涂料,可快速传导电流,消除静电荷。所以,高压电力设备表面涂层要求不仅具有良好的耐腐蚀性,还必须具有一定的抗静电性。
近年来,防腐蚀涂料的研究十分迅速,在传统的防腐蚀涂料的基础上,研究出了众多性能优异的品种[6]。但目前,最常用仍是富锌涂料,它是以球型锌粉为防锈颜料,环氧树脂为基料,聚酰胺树脂或胺加成物为固化剂,加以适当的混合溶剂配制而成的环氧类防腐蚀涂料,是重防腐涂料中的一种,以其优异的防腐性能得到广泛应用[9],为确保其防腐蚀性能,其中锌粉含量通常要达到85%以上。如此高的锌粉含量也带来一些问题,比如在有其涂层的结构件上进行电焊、切割等热加工作业时会释放出大量的氧化锌物质,容易导致工作人员产生“锌热病”。
含锌粉涂料的防腐蚀机理是阴极保护和屏蔽作用,所以对富锌漆耐蚀性的评价,必须考虑阴极保护性能。评价富锌漆阴极保护性能常用的方法有划痕盐雾实验和电化学阻抗法。有研究表明,环氧富锌底漆中只有25%~30%的锌粉在阴极保护中起作用。因为它的导电性能相对较低,阴极保护作用相对较弱,可接受的氯化物含量较低等,这是它用于腐蚀环境最大的缺点。为了提高其阴极保护作用,不少研究学者采用其他物质代替涂料中的部分锌粉。本文根据电力设备的实际防护要求,通过添加锌粉和不同量的导电云母填料制备抗静电防腐蚀涂料,涂料固化后形成的涂层具有良好的抗静电性,并通过盐雾和电化学实验验证其耐腐蚀性。
1 实验方法
组分A配方采用环氧树脂15%~30%、溶剂5%~10%、分散剂0.3%~1%、防沉剂0.5%~2%、锌粉50%~85%、其他填料3%~5%、导电云母粉0~5%;组分B为环氧固化剂;组分A:组分B (质量比) =13:1。首先将环氧树脂和溶剂混合,在搅拌的条件下加入分散剂和防沉剂,待搅拌均匀依次加入锌粉、填料和导电云母粉,高速搅拌一定时间,并补充挥发损失的溶剂,得到涂料组分A。
实验用规格为150 mm×75 mm的Q235钢为基体,先用丙酮除油,喷砂以清除表面的锈层、氧化皮。喷砂后4 h内采用空气喷涂方式制备涂层,喷涂时,组分A和组分B按比例混合,加稀释剂调到适合的粘度。喷涂后,室温下放置7 d使涂层固化,涂层厚度 (100±10) μm。按导电云母添加量的不同,将涂层命名为CMP0、CMP1、CMP3和CMP5。
按国家标准GB/T 6739-2006测试涂层的铅笔硬度;GB/T 1732-1993测试涂层的耐冲击性;GB 9286-1998测试涂层的附着力;GB/T 1731-1993测试涂层的柔韧性;GB/T 9754-2007测试涂层的光泽;采用美国ACL-800表面电阻测试仪测试涂层表面电阻率和体积电阻率。
按国家标准GB/T 1771-2007色漆和清漆耐中性盐雾的测定进行划痕盐雾实验,采用连续喷雾的方式,实验溶液为5%NaCl (质量分数) 溶液,实验温度为 (35±2) ℃,并沿原样板预制一条划痕。
电化学阻抗谱 (EIS) 测试采用273A电化学阻抗测试系统,在开路电位下进行测量,测量频率范围为105~10-2 Hz,测量信号为幅值10 mV的正弦波,电解池采用三电极测试体系,辅助电极为铂电极,参比电极为饱和甘汞电极 (SCE),涂层/基体试样为工作电极,工作电极的有效面积约为12.56 cm2,腐蚀介质为3.5% (质量分数) NaCl溶液,实验所得到的交流阻抗数据用ZSimpWin阻抗分析软件进行处理与分析。
采用ESEM XL30 FEG环境扫描电镜 (ESEM) 观察涂层的表面形貌,试样表面经过喷金处理,工作电压为10 kV;采用ESEM所携带的附件EDS来分析涂层中元素的种类和含量;采用DMAX/2400X射线衍射仪 (XRD,Rigaku Denki) 分析涂料物相,以CuKα为放射源 (40 kV,100 mA)。
2 结果与讨论
2.1 导电云母的SEM微观形貌和成分分析
图1为导电云母粉的SEM微观形貌和XRD图。可以看出,导电云母粉为大小、形状不规则的鳞片状结构,外观一般呈灰白色或浅灰色粉末,导电云母粉体主要是由云母粉 (KAl3Si3O11) 和人工合成的石英氧化硅 (SiO2) 两种物质组成。
2.2 涂层的常规性能
表1是4种涂层的力学性能,可以看出,4种涂层的铅笔硬度均为2H,柔韧性均为1 mm,耐冲击性均为50 cm。随着导电云母含量的增加,涂层的光泽逐渐降低,柔韧性、耐冲击性都没有明显降低。随着导电云母含量的增大,CMP5试样涂层与基体的附着力变差,原因是片状的导电云母含量为5%时,涂层的流平性受到影响,流平性不好引起涂料与基体不能很好的润湿,导致附着力变差。
2.3 涂层的表面电阻和体积电阻
表2是4种涂层的表面电阻率和体积电阻率,可以看出,4种涂层的表面电阻率都处于106~109 Ω·cm-2之间,体积电阻率都满足105~108 Ω·cm,涂层都属于抗静电涂层范畴。
2.4 涂层的耐盐雾腐蚀性能
图2是4种涂层试样盐雾实验2500 h后的表面形貌照片,从图中可以看出,CMP0、CMP5两种涂层试样划痕边缘都有基体钢的红褐色腐蚀产物,说明未添加导电云母和导电云母含量为5%的涂层划痕处阴极保护消失,CMP0涂层试样未划痕部位,锌粉有腐蚀现象,形成的是白色的腐蚀产物;CMP5涂层试样表面基体被腐蚀,腐蚀面积达50%。CMP1、CMP3试样的涂层表面没有起泡、锈蚀现象,涂层附着较好,划痕处无起泡、无锈蚀现象,说明涂层仍具有保护作用。盐雾实验结果表明,在富锌涂料中添加适量的导电云母可以延长其涂层阴极保护作用。
盐雾实验2500 h后涂层的表面电阻率如图3所示。可以看到,盐雾实验后,涂层表面电阻率和体积电阻率都稍有增大,但都满足抗静电涂层要求,涂层表面有腐蚀产物的形成,致使涂层的抗静电性能有所下降。盐雾实验对涂层的抗静电性能影响不大。
图4是4种涂层盐雾实验后沿划痕处的截面形貌,从图中可以看出,Zn粉在整个涂层中均匀分布,所有涂层内球型的锌粉失去了原来的形貌,球形表面的锌单质优先反应并向球心推进。盐雾实验2500 h后,CMP0试样涂层内靠近表层部分的锌粉已经腐蚀,涂层表面、涂层与基体界面处有腐蚀产物即锈层生成,经EDS分析腐蚀产物中有铁元素,说明基体被腐蚀。CMP5试样涂层内大部分锌粉已经失去了原有的形貌,说明涂层内的锌粉参加了反应。腐蚀产物中也检测到Fe的存在,说明基体也被腐蚀了。CMP1和CMP3两种试样涂层表面、涂层与基体界面处均没有检测到Fe,说明基体没有被腐蚀,这种现象也说明了这两种涂层仍具有良好的阴极保护作用。
2.5 涂层盐水浸泡实验
图5是4种涂层在3.5%盐水浸泡500 h后表面形貌的数码照片。从图中可以看出,未添加导电云母的CMP0试样表面出现白色锈蚀产物,白色锈点部位同时起泡,CMP5试样表面出现较多的白色的锈蚀产物,浸泡边缘出现基体的锈蚀产物,而CMP1和CMP3两种试样表面几乎没有锈点、起泡和基体锈蚀现象,说明这两种涂层具有良好的保护作用,耐腐蚀性能较好,这与盐雾实验结果相吻合的。
2.6 电化学开路电位分析
图6给出了4种涂层在3.5%NaCl溶液中浸泡648 h期间,涂层的腐蚀电位随时间的变化。涂层的开路电位表现了涂层的电化学性质,涂层对基材阴极保护时间的长短可以通过涂层的腐蚀电位低于-860 mV (vs SCE) 的时间来衡量,时间越长,涂层对基材的保护越好。从图中可以看出,CMP0试样涂层在浸泡初期开路电位先从-750 mV下降到-1043 mV,之后上升到-89 mV趋于稳定,阴极保护作用消失;CMP1和CMP3这两种试样涂层开路电位从-650和-850 mV分别下降到-1060 mV和-1030 mV,之后上升到-930和-960 mV趋于稳定;CMP5试样涂层开路电位在浸泡初期从-700 mV左右下降到-1010 mV左右,随后又上升至-650 mV,之后一直大于-860 mV,阴极保护作用消失。CMP5试样涂层在浸泡24 h后,涂层表面就出现黄褐色的锈蚀产物,说明腐蚀介质在浸泡初期很快就进入涂层,到达基材表面,引起了基材的腐蚀。
图7是4种涂层试样随浸泡时间的Bode图。从图中可以看出,这几种涂层试样的电化学行为依然遵循富锌涂层的电化学特征。在浸泡0.5 h时,CMP0、CMP1和CMP3试样涂层的Bode图上阻值|Z |很大,这时由于涂层刚开始浸泡仍是硬而紧密的涂层,涂层中的Zn粉由于树脂的包覆还没有参加阴极保护反应。随着浸泡时间的延长,腐蚀介质的不断渗透,Zn粉被活化开始反应,富锌涂层的阴极保护作用开始,各种涂层的阻值迅速减小。CMP1和CMP3两种试样涂层电阻值下降后维持在104 Ω·cm2左右,涂层Bode图形基本不变。CMP0试样涂层的Bode图在浸泡48 h后,涂层电阻值上升,之后基本维持不变。CMP5试样 (图7d) 刚浸泡0.5 h时,Bode图上显示涂层在低频的阻值在103 Ω·cm2,说明涂层有较多缺陷,腐蚀介质通过缺陷处,很快渗透进入涂层,浸泡5 h时,涂层阻值明显降低,这时涂层中锌粉的阳极反应的腐蚀产物堵塞了涂层表面的空隙,引起涂层阻值在浸泡24 h时提高,在浸泡48 h后,涂层的电阻值迅速减小,说明涂层阴极保护作用此时消失。
2.7 电化学阻抗谱分析
图8是4种涂层在拟合过程中所采用的等效电路,不同含量导电云母改性的抗静电涂层试样的电化学行为依然遵循富锌涂层的电化学特征。图9是4种涂层电阻随浸泡时间变化曲线,由图可知,刚开始浸泡0.5 h时,CMP0、CMP1、CMP3试样涂层的Rc都很高,RCMP0>RCMP1>RCMP3>RCMP5,涂层的电阻反映的是涂层的导电性,电阻越大,导电性越差,这与测得的涂层的表面电阻率值规律相同,此时,遵循图8a R(QR)的等效电路图。随着浸泡时间的延长,涂层的Rc迅速下降。CMP0试样在浸泡24 h后,涂层电阻开始上升,这是涂层中Zn粉开始反应,生成的腐蚀产物堵塞了涂层中的通道,阴极保护作用随着浸泡时间的延长逐渐增强,生成的腐蚀产物屏蔽作用也逐渐增强,96 h后,阴极保护作用达到最大,之后涂层电阻又逐渐减小,说明涂层阴极保护作用减弱,480 h时,涂层屏蔽作用提供涂层的防腐蚀的能力,此时涂层阴极保护作用消失。CMP1、CMP3试样涂层在浸泡期间涂层电阻逐渐减小后维持不变,涂层电阻无明显变大,说明涂层具有一定的阴极保护作用,并一直维持涂层的防腐蚀的能力。CMP5试样涂层浸泡0.5~196 h,涂层电阻呈上升趋势,阴极保护和屏蔽作用在196 h达到最大,之后涂层电阻逐渐降低,屏蔽作用也逐渐减弱,直至基体腐蚀,涂层失效。
2.8 涂层耐腐蚀机理分析
从盐雾实验、浸泡实验和电化学阻抗谱实验总结导电云母添加到有机抗静电涂层中,涂层的阴极保护作用和屏蔽作用为:在富锌涂料中添加导电云母,锌粉的使用量虽然大幅度降低,但涂层中均匀分散的导电云母可在涂料中形成片层和球形锌粉填料复合的导电网状结构,能够更有效地利用锌粉,提高锌粉的阴极保护作用,加强了涂层对基材的保护。将导电云母加入抗静电涂料中并充分分散后,导电云母均匀分布在环氧树脂基体中,可以填充到球状锌粉之间的空隙中。因此,导电云母的加入可以明显提高涂层的致密性和耐水性,有效防止水、氧气等分子渗入到基体表面,降低涂层的鼓泡和腐蚀程度。导电云母的片层结构,使其在涂料中层层叠加,可形成致密的隔绝层。而涂层中均匀分散的导电云母片相互随机堆叠,形成了致密的连续不断的网状片层导电结构,与锌粉搭接形成导电通路,从而活化了涂料中的锌粉,使涂层与钢铁基材形成了电化学回路体系,提高并延长了涂层的阴极保护作用。
根据填料混合填充的聚合物复合材料的导电特性渗流理论,当导电颗粒的体积 (质量) 分数增加到某一临界值时,导电高分子复合材料的电导率突然增加数个数量级,这一临界值对应的填料含量为“渗流阈值”。当导电云母添加量接近3%时,表现为介电常数突然增大,涂层的导电性能增大了两个数量级,导电云母的“渗流阈值”为3%。也就是说,3%的导电云母添加到环氧树脂基体中,在保持环氧树脂本身性能的前提下,大幅提高涂层的导电性能,含3%左右导电云母的涂料可能接近“渗流阈值”,涂层中均匀分散的导电云母片相互随机堆叠,形成致密的连续不断的片层和球形锌粉填料复合的导电网状结构,其介电性能和屏蔽性能最好,相应的防腐性能最佳。而当导电云母添加过量,导电云母会在内部聚集,破坏涂层结构,使其介电性能和屏蔽作用变差,导致涂层的阴极保护防腐性能有所降低。
3 结论
导电云母填料可以替代富锌涂料中的部分锌粉,制备不同含量导电云母的抗静电防腐蚀涂层。随着导电云母添加量的增加,涂层的表面电阻率和体积电阻率降低,抗静电性增加。盐雾实验、浸泡实验和电化学实验结果表明,适量的导电云母片和球形锌粉填料复合形成致密的、连续不断的导电网状结构,可以延长涂层阴极保护时间,提高涂层的耐蚀性,其最佳添加量为3%。盐雾实验对涂层的抗静电性能影响不大。
更多关于材料方面、材料腐蚀控制、材料科普等方面的国内外最新动态,我们网站会不断更新。希望大家一直关注中国腐蚀与防护网http://www.ecorr.org
责任编辑:王元
《中国腐蚀与防护网电子期刊》征订启事
投稿联系:编辑部
电话:010-62313558-806
邮箱:fsfhzy666@163.com
中国腐蚀与防护网官方 QQ群:140808414
免责声明:本网站所转载的文字、图片与视频资料版权归原创作者所有,如果涉及侵权,请第一时间联系本网删除。
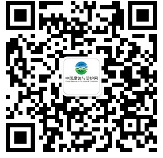
官方微信
《中国腐蚀与防护网电子期刊》征订启事
- 投稿联系:编辑部
- 电话:010-62313558-806
- 邮箱:fsfhzy666@163.com
- 中国腐蚀与防护网官方QQ群:140808414