随着中国制造 2025 和工业 4.0 战略的实施,在我国对新能源汽车产业大力扶持的背景下,新能源汽车的研发与制造已成为推动我国汽车产业升级的一个重要环节。受限于动力电池能量密度的技术瓶颈,纯电动汽车的整备质量比同级别的传统能源车高出13%~20%,车身轻量化是新能源汽车发展的主要趋势,而铝合金材料应用是目前车身轻量化的主要解决方案。
焊接是汽车制造中最重要的制造技术,传统电阻点焊具有设备通用性高、成本较低、质量稳定、工时较短等特点,常规钢车体的主要连接技术是电阻点焊。随着高强度、超高强度钢,铝合金和复合材料的引进,新的连接技术也同时引进,包括激光焊、铆接、胶粘等。文章主要阐述了铝合金电阻点焊的工艺研究和在汽车行业的应用现状。
一、铝合金的焊接性铝合金的焊接性
通常考虑 3个方面:母材、工艺设计和焊接过程。
根据铝合金成型方式的不同,分为变形铝合金(包括冲压板和型材)和铸造铝合金。变形铝合金中,根据强化机制的不同,分为时效硬化铝(例如 6xxx 系和7xxx 系铝合金)和固溶强化铝(例如 5xxx 系铝合金)。不同的强化机制会导致电阻点焊过程中的缺陷倾向和组织形成过程不同。
针对铝合金,不同的热处理工艺对母材的影响很大,常用的热处理工艺包括:
(1)O-退火态:消除加工硬化和内应力,可以稳定外形和尺寸;(2)T 4 -固溶处理(淬火)加自然时效:通过加热保温,使可溶相溶解,然后急冷,获得过饱和固溶体,以提高合金的硬度、强度及抗蚀性。 对 Al- Mg 系合金为最终热处理,对需人工时效的其它合金则是预备热处理;(3)T 5-固溶处理(淬火)加不完全人工时效:用来得到较高的强度和塑性,但抗蚀性会有所下降,尤其是晶间腐蚀会有所增加;(4)T 6-固溶处理(淬火)加完全人工时效:用来获得最高的强度,但塑性和抗蚀性有所降低;(5)T 7 -固溶处理(淬火)加稳定化回火:用来稳定铸件尺寸和组织,提高抗腐蚀(尤其是抗应力腐蚀)能力,并保持较高的力学性能。
此外,焊接工艺设计主要包括:板件搭接形式和工艺尺寸;焊接过程涉及焊接方法、焊接设备、焊前/焊后处理和工艺参数等。
二、铝合金电阻点焊的技术难题
(1) 铝合金的氧化膜
铝合金的熔点为 520~660 ℃,铝合金表面有一层致密的氧化膜,厚度小于 0.01 mm,熔点约 2 000 ℃。电阻点焊过程中,热量输入使熔池温度略高于铝合金熔点,但远远无法达到氧化膜的熔点,因此,氧化物无法熔化。此外,氧化膜具有低导电性和低导热性。因此,电阻点焊如何在焊接开始时保证氧化膜的刺穿和破碎是需要解决的一个重要问题。氧化膜对气体具有吸附作用,容易形成气孔,同时,无法熔化的氧化膜在焊核中容易形成非金属夹杂物。图 1 示出铝合金和无镀层钢板在焊接过程中的电阻变化。
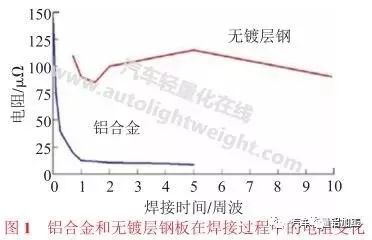
(2)凝固过程中的裂纹
热裂纹
由于部分铝合金的固溶温度区间较大,焊核在熔化、再凝固的过程中,凝固后收缩,在应力影响下,容易在焊核形成热裂纹,根据铝合金成分不同,形成热裂纹的情况如下:
纯铝:无固液两相区,不形成热裂纹;非时效硬化铝(例如 3xxx 和 5xxx),固溶温度区间小于 50 ℃,对于电阻点焊这种熔化焊,热裂纹倾向很小;6xxx 和7xxx 中的 AL- Zn- Mg 系列铝合金,固溶温度区间在50~100 ℃,热裂纹倾向较为敏感,需采用合适的对策保证焊接质量;2xxx和 7xxx中,因为 Cu,Mg,Zn 合金元素的加入,固溶温度区间在 100 ℃以上,热裂纹非常容易形成,应尽量避免熔化焊。
液化裂纹
在时效硬化铝中,还存在一种液化裂纹。当焊核温度达到熔点以上,低熔点共晶相重新溶解到液相中,凝固过程中收缩,同时液态金属无法及时流动到凝固位置,因而形成液化裂纹。液化裂纹的形成主要与高热量输入有关,因此,除了添加低熔点焊丝外,降低能量输入,减少热影响区也是降低液化裂纹的有效手段。
(3)气孔
焊核熔化过程中,液态铝合金吸收大量氢,凝固后,氢的固溶量下降 20%,因此,多余的气体无法排出而形成气孔。
(4)焊接接头的软化问题
对不同合金,常见焊后热处理方法:焊接 Al-Mg- Si 合金(6xxx系铝合金)时,母材采用 T 4 态,焊接后采用时效处理;焊接 AL- Zn- Mg 合金(7xxx 系中无 Cu的铝合金),热影响区由于强化相的固溶而强度下降,焊后可通过约 90 天的自然时效恢复到母材强度。除强度外,热影响区的抗腐蚀能力也是点焊过程中不可忽视的因素。一般来说,时效硬化铝(6xxx系和 7xxx系)抗腐蚀能力较差,非时效硬化铝抗腐蚀能力较强。
三、汽车行业铝合金电阻点焊的研究方向
(1)铝合金点焊需要更高的热输入
由于铝合金的导电和导热性很好,需要比钢大得多的热量输入才能实现焊接。一般来说,铝合金的焊接电流是钢的 2~3 倍,同时为了保证热量的集中快速输入,焊接时间是钢的 1/3。焊接压力相比钢要求更高,因此,焊接钢一般需要 0.2~4 kN 的焊钳压力,最高15 kA 的焊接电流;而焊接铝合金需要 0.2~8 kN 的焊钳压力,最高 40 kA的焊接电流。
(2)电极的延寿
铝点焊过程中,由于大电流、高压力,铝材的粘连和飞溅现象较为严重 ,因此,每个电极帽在焊接约 20 个点后需要进行修磨,需要花费大量时间,降低生产节拍,电极帽的快速磨损导致了生产费用的增加。此外,电极的极性影响焊核质量和电极磨损。焊接过程一开始,势能决定极性,焊核形成偏向于阳极,因此,阳极磨损更为严重。同样厚度的板材,焊核偏向阳极成核;对于不同厚度的板材,可能引起焊核偏移,甚至虚焊。
四、铝合金电阻点焊在汽车行业的研究进展
(1)采用中频直流焊机(MFDC)
应用 MFDC 的最大优势在于焊接不同板厚和材料时,能量供应的灵活切换,在铝点焊时,充分发挥电流传输的高效率和高利用率。
(2)采用交流焊机
采用交流焊机的主要目的有 2 个:一方面,采用直流焊机时,正电极磨损程度明显比阴极严重,采用交流焊机可以均衡并改善正负极磨损情况,间接提高修磨频次,延长电极寿命。另一方面,由于电极极性导致焊核不在板材中间位置,而是向正极侧偏移,导致焊接质量不良,通过采用交流焊机,可以有效避免焊核偏移。
(3)焊钳变压力
法国 ARO 焊钳设备商开发了一套利用电子伺服和压力反馈实现变压力焊接的铝焊钳。针对整个焊接过程初期的预压力、焊接压力、焊核成型的锻压力,可以实现变压力焊接,有效减少因压力不当引起的裂纹和飞溅等焊接缺陷。
五、结语
如何实现铝合金高效、低成本的可靠连接是一个重要的研究方向。相比铆接、胶粘,铝合金电阻点焊具备设备通用率高、成本低廉、轻量化等特点,对其的研究也将持续开展。但铝合金点焊的技术难点主要有:(1)部分铝合金焊接存在软化区,降低焊接强度;(2)铝合金表面有致密氧化膜,难熔、难击穿,且易形成焊接缺陷;(3)铝合金点焊需短时大量热输入,引起电极磨损和粘连。
从目前汽车车身上的铝点焊研究和应用现状来看,未来几年铝点焊的研究重点是铝点焊强度的提升和质量的稳定性,铝点焊大幅产业化应用需进一步降低制造成本。
更多关于材料方面、材料腐蚀控制、材料科普等方面的国内外最新动态,我们网站会不断更新。希望大家一直关注中国腐蚀与防护网http://www.ecorr.org
责任编辑:韩鑫
《中国腐蚀与防护网电子期刊》征订启事
投稿联系:编辑部
电话:010-62313558-806
邮箱:fsfhzy666@163.com
中国腐蚀与防护网官方 QQ群:140808414
免责声明:本网站所转载的文字、图片与视频资料版权归原创作者所有,如果涉及侵权,请第一时间联系本网删除。
相关文章
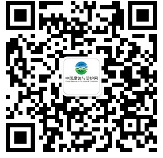
官方微信
《中国腐蚀与防护网电子期刊》征订启事
- 投稿联系:编辑部
- 电话:010-62313558-806
- 邮箱:fsfhzy666@163.com
- 中国腐蚀与防护网官方QQ群:140808414
点击排行
PPT新闻
“海洋金属”——钛合金在舰船的
点击数:5768
腐蚀与“海上丝绸之路”
点击数:4763