世界腐蚀日(WorldwideCorrosion Day)“由世界腐蚀组织(WCO)确立。世界腐蚀组织是于 2006 年在纽约注册成立的非营利学术组织。是一个代表地方及其国家的科学家、工程师和其它团体的世界性组织。在腐蚀和防护的研究中,致力于知识的发展和传播。
2009年经过WCO各成员的讨论并一致通过了在世界范围内确立每年的4月24日作为”世界腐蚀日(WorldwideCorrosion Day)“,其宗旨是唤醒政府、工业界以及我们每个人认识到腐蚀的存在,认识到每年由于腐蚀引起的经济损失在各国的 GDP 中平均超过 3%;同时向人们指出控制和减缓腐蚀的方法。
值此”2019.4.24“世界腐蚀日来临之际,中国腐蚀与防护学会本届世界腐蚀日专题活动是以科普角度与公众聊聊腐蚀的兄弟——疲劳那些事儿。
腐蚀与疲劳的”兄弟情“腐 蚀 与 疲 劳均为材料构件失效的主要形式,在多种情况下,二者相辅相成,相互促进,共同对材料发起攻击,俨然一对团结互助的”好兄弟“。 这对”好兄弟“一起出现时就是腐蚀疲劳,腐蚀疲劳是指材料在交变载荷和腐蚀介质的协同、交互作用下发生的一种破坏形式,广泛存在于航空、船舶以及石油等领域,腐蚀疲劳破坏是工程上面临的严重问题,现已成为工业领域急需解决的课题。但本次世界腐蚀日,我们先不说兄弟俩的事儿,而是聊聊腐蚀的弟弟——金属疲劳那些事儿。
金属为什么会疲劳?
生活经验告诉我们,要想徒手拉断铁丝是非常困难的,但如果反复折几下却很容易折断。这表明,即使反复变化的外力远小于能将金属直接拉断的恒力,也会使它的机械性能逐渐变弱并最终损毁。
金属的这种现象和人在长期工作下的疲劳非常像,科学家们便形象地称其为”金属疲劳“。
不少小伙伴都会疑惑:人累了会疲劳,怎么坚硬的金属也会疲劳呢?正所谓”黄金无足色,白璧有微瑕“,我们目前所用的金属并非是完美的,在加工或使用的过程中,金属总会存在一些缺陷,比如内部有杂质或孔洞、表面有划痕。这些缺陷往往只有微米量级,很难通过肉眼观察,如果给金属施加一个不变的拉力,它们并不容易产生裂缝。可如果外力是反复变化的,一会儿是拉力一会儿是压力,一部分能量就会转换成热,积累在金属内部,一旦超过某个限度,金属就很容易在缺陷处发生原子间的化学键断裂,导致结构开裂。
显微镜观测到的金属缺陷及起始于该缺陷的金属疲劳开裂过程
什么会是疲劳?
疲劳是指在低于材料极限强度(ultimate strength)的应力(stress)长期反复作用下,导致结构终于破坏的一种现象。由于总是发生在结构应力远低于设计容许最大应力的情况下,因此,常能躲过一般人的注意而不被发觉,这也是疲劳最危险的地方。
材料在承受反复应力的作用过程中,每一次的应力作用称为一个应力周期(cycle),此周期内的材料受力状态,由原本的无应力先到达最大正应力(拉伸应力),然后到达最大负应力(压缩应力),最后回到无应力状态。在此受力过程中,每一个应力周期所经历的时间长短(即:频率)与疲劳关系甚微,应力周期的振幅及累积次数才是决定疲劳破坏发生的时机;另外,压缩应力不会造成疲劳破坏,拉伸应力才是疲劳破坏的主因。
材料承受反复应力的作用过程
疲劳破坏大致分为两类:低周期疲劳(low cycle fatigue)及高周期疲劳(highcycle fatigue)。一般而言,发生疲劳破坏时的应力周期次数少于十万次者,称为低周期疲劳;高于此次数者,称为高周期疲劳。低周期疲劳的作用应力较大,经常伴随着结构的永久塑性变形(plasticdeformation);高周期疲劳的作用应力较小,结构变形通常维持在弹性(elastic)范围内,所以不致有永久变形。
材料疲劳破坏的进程分为三阶段:
裂纹初始(crack initiation)、裂纹成长(crack growth)、强制破坏(rupture)。
材料表面瑕疵或是几何形状不连续处,材料晶格(lattice)在外力作用下沿结晶面(crystallography plane)相互滑移(slip),形成不可逆的差排(dislocation)移动,在张力及压力交替作用下,于材料表面形成外凸(extrusion)及内凹(intrusion),造成初始裂纹。这些初始裂纹在多次应力周期的拉伸应力连续拉扯下逐渐成长,并使材料承载面积缩减,降低材料的承载能力。当裂纹成长到临界长度(critical length)时,材料净承载面积下的应力已超过材料的极限强度,此时的材料强制破坏也就无法避免了。
疲劳破坏特点
突然性:断裂时并无明显的宏观塑性变形,断裂前没有明显的预兆,而是突然地破坏;
低应力:疲劳破坏在循环应力的最大值,远低于材料的抗拉强度或屈服强度的情况下就可以发生;
重复载荷:疲劳破坏是多次重复载荷作用下产生的破坏,它是较长期的交变应力作用的结果,疲劳破坏往往要经历一定时间,与静载下的一次破坏不同;
缺陷敏感:疲劳对缺陷(例如缺口、裂纹及组织缺陷)十分敏感,由于疲劳破坏是从局部开始的,所以它对缺陷具有高度的选择性;
疲劳断口:疲劳破坏能清楚地显示出裂纹的发生、扩展和最后断裂三个组成部份。
图4 疲劳破坏典型断口图
影响疲劳强度的主要因素
影响疲劳强度的因素比较多,以下几类因素在航空发动机设计、制造中需要重点予以考虑。
应力集中:疲劳源总是出现在应力集中的地方,必须注意构件的细节设计以避免严重的应力集中,比如加大剖面突变处的圆角半径;
表面状态:疲劳裂纹常常从表面开始,所以表面状态对疲劳强度会有显着的影响,表面加工越粗糙,疲劳强度降低、越严重;
温度:一般随着温度的升高,疲劳强度会降低。
疲劳的危害
虽然很多人都没听过金属疲劳的事儿,但它却广泛潜伏在人们的日常生活中,常常引发出人意料的严重事故。据估计,约 90% 的机械事故都和金属疲劳有关。2007 年,美国空军的一架 F-15战斗机在模拟空战时,战机机头与机身分离,飞行员弹射出舱,这次事故造成美军F-15 战机大面积停飞,调查结果显示,事故起因于飞机上的一根金属纵梁发生了疲劳。无独有偶,2002 年,一架由我国台湾飞往香港的波音 747 客机在澎湖附近海域解体坠毁,造成包括机组成员在内共225 人不幸罹难。事后调查认为,飞机上一块修补过的蒙皮发生了严重的金属疲劳开裂,造成机尾脱落,最终导致飞机因舱体失压而解体。 除了飞行事故,轮船、列车、桥梁、汽车等也常因金属疲劳招致灾难:二战期间,美国的 5000 艘货船发生了近 1000 次金属疲劳事故,200 多艘货船彻底歇菜;1998 年,德国一列高速行驶的动车因车轮轮箍的疲劳断裂而脱轨,造成 100 余人死亡。
飞机疲劳事故详解
(一)航空史上最著名的军用飞机疲劳破坏事件,应该是1969年美国空军的F-111空中解体。F-111 结构中有个特殊的可变后掠机翼设计,这是因为固定式机翼在特定的飞行速度、高度、大气温度、大气密度、引擎推力下,有最佳的性能表现,一旦其中某个因素改变,性能就会降低。而可变后掠机翼则完全无此缺点,它就像是设计各种不同的机翼,来配合飞行中不同的飞行情况,例如:起降时把机翼完全向外伸展,增加机翼的升力,缩短起降距离;亚音速巡航时则把机翼部分后掠,减少机翼的阻力;超音速贴地飞行时则将机翼全角度后掠。
F-111 于 1967 年出厂,当年 10 月,第一个 F-111 联队在内华达州内里斯(Nellis)空军基地正式成立,8 个月之后的 1968 年 3 月 17 日,6 架 F-111 被派驻泰国执行越南战场上的轰炸任务,经过几个架次的熟悉环境飞行后,F-111立即开始执行任务,但 3 月 28 日一架飞机未返航,两天后另一架飞机也未见踪影,第三架飞机失踪则是发生在 4 月27 日。由于每一架飞机的飞行计划都是由飞行组员自行拟定,且飞行途中需保持无线电静默,因此无从知道到底发生了什么事。1969 年 12 月 22 日,编号第 94 号的 F-111 在基地上空进行武器抛投(Weapons Delivery)训练飞行时坠毁,当时飞机是低空飞越一仿真目标后,以 3.5g(±0.5g)拉起时,左翼掉落,飞机坠毁,两名飞行员当场丧生,飞机残骸中连接机身和左机翼的枢纽接头(Wing Pivot Fitting)从中间断裂成内、外两半,内半块遗留于机身上,外半块则与机翼相连。检查残骸的结果,发现枢纽接头下缘有个制造过程遗留的半椭圆形疲劳初始裂纹瑕疵,宽约一英吋,深度几乎穿透厚度,因此初始裂纹经过短时间后,就成长到使接头强制破坏的临界长度。
(二)2007 年 11 月 2 日 上 午, 一 架 隶属于美国密苏里州空中国民兵(AirNational Guard)的 F-15C,在执行训练任务时突然空中解体,就是上述顾虑的最佳例证。失事当时,这架编号 80-0034 的 F-15C 正执行基本战斗机机动(Basic Fighter Maneuvers)演练,与僚机进行一对一的空中攻击及防御动作训练。在进行第二次的接战练习时,失事机以 450 节的空速快速右转,机体承受负载约为7.8G,此时机体开始剧烈抖动,飞行员立即将飞机改为平飞状态,机体承受负载迅速降到 1.5G,数秒钟后,前机身于座舱罩后面位置处断裂并与机体完全脱离,机体空中解体为两截,所幸飞行员跳伞后平安获救。
F-15C 80-0034空中解体示意图
失事后的调查报告显示︰失事发生原因为机身斜站位(Canted FuselageStation)CFS337 处 的 右 侧 上 纵 梁 断裂,失事机上纵梁残骸经金相分析(Metallurgical Analysis)后,发现破断面处的厚度仅有 0.039 英吋(不到一毫米)到 0.073 英吋,完全不符合蓝图规定的 0.090 到 0.110 英吋厚度,且上纵梁表面粗度(surface roughness)也较蓝图规定粗糙。过薄的破断面直接造成上纵梁局部应力大幅升高,在反复的飞行负载作用下,上纵梁很容易由粗糙面产生多处的疲劳初始裂纹,继而在后续的飞行负载中持续成长,最后导致上纵梁完全断裂。
问题就出在这根纵梁上
对其他F-15检查后也发现了裂纹
这架 F-15C 于 1982 年开始服役,失事时飞行时数接近5,900小时。F-15C原始设计规范为”安全寿命“(SafeLife),服役寿限为 4,000 飞行小时,在美国空军颁布”容许损伤“(DamageTolerance)设计规范后,重新依据此规范进行分析,服役寿限延长到 8,000 飞行小时,并以 16,000 飞行小时的全机疲劳试验来加以验证。由于分析数据显示上纵梁的裂纹成长寿命高达 31,000飞行小时,依据设计规范其定期检查时距为 15,500 飞行小时,远超过飞机的服役寿限,且上纵梁在全机疲劳试验过程中也未发现有任何损伤,所以虽属攸关飞行安全的主要结构件,但在服役期间内并不需要进行定期检查。
疲劳对策难道我们就对邪恶的金属疲劳束手无策了吗?非也。
我们了解疲劳相关的内容,最终目的是要预防或者减少航空发动机等机械构件发生疲劳失效的情况,进行长寿命设计。如下这些措施常用于提高结构的疲劳强度:
结构优化设计结构设计中尽量避免产生应力集中,对过渡圆角、螺栓孔等容易产生应力集中的部位进行优化,疲劳往往出现在这些应力集中部位。
严格控制温度疲劳强度一般随着温度的升高急剧下降,不能为了性能达标而一味地提高温度。
采用强化措施采用各种表面强化处理、孔挤压强化等。
提高零件加工质量裂纹往往出现在材料缺陷或者加工缺陷位置,必须加强零部件加工制造工艺,严格控制关键位置的加工精度和加工质量,减少疲劳源,防止超差等质量问题引起的疲劳失效。
在飞机制造领域,增强”金属免疫力“是对抗金属疲劳的有效方法。一方面,在钢铁和有色金属中,加进微乎其微的稀土元素,可以大大提高金属的抗疲劳属性,延长使用寿命;另一方面,减少金属材料中的杂质也能增强”金属免疫力“,延长金属使用寿命。杂质对疲劳性能和应力腐蚀性能影响很大,例如,对于超高强度钢的金属性能,国际上是通过控制硫和磷的杂质含量来保证的。在技术标准中,对于每一种杂质的最高含量,以及所有杂质含量之和都有明确的要求。在金属构件上尽量避免生锈,用辅助工艺提高表面光洁度,以及对产生震动的机械采取防震措施,都能有效防止金属疲劳。
在必要的时候,对金属内部结构进行检测,也是预防金属疲劳的常用方法。
经过科学家们的不懈努力,如今已有多种方法可以检测金属的疲劳,超声波、红外线、γ 射线等都能对金属进行体检。日本的科学家还发明了一种掺入钛酸铅粉末的特殊涂料,在敲击金属时,金属表面的涂料薄膜中会有电流通过,且电流的大小和金属的疲劳程度有关,通过测量这股电流,便可知道金属究竟有多”累“。
结束语
中国工程院赵振业院士呼吁,加速抗疲劳制造研究发展,建立抗疲劳制造、极限寿命设计、极限性能材料新三位一体技术体系是机械制造升级转型的当务之急,是提升国民经济发展的根本道路,是实现机械制造强国的根本道路。强硬如金属尚且如此,虽然算不上什么新知,但也从某一种角度提醒着我们:革命尚未成功,我辈仍须强韧性、减疲劳,来日方长。
免责声明:本网站所转载的文字、图片与视频资料版权归原创作者所有,如果涉及侵权,请第一时间联系本网删除。
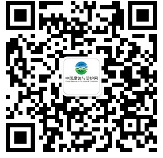
官方微信
《腐蚀与防护网电子期刊》征订启事
- 投稿联系:编辑部
- 电话:010-62316606-806
- 邮箱:fsfhzy666@163.com
- 腐蚀与防护网官方QQ群:140808414