当前,由于环保和节能的需要,汽车轻量化已经成为汽车工业发展的趋势与潮流。此外,近年来由于国家政策大力扶持以及基础设施的不断完善,新能源汽车驶入快速发展轨道。但相对于传统燃油汽车,新能源汽车在绝对销量和市场占有率方面仍处于劣势。其原因在于新能源汽车的两个短板:相对高昂的价格及续航里程不足。在目前电池能量密度无法实现大突破的背景下,轻量化作为提升新能源汽车续航能力的重要手段成为了新能源汽车发展趋势之一。
轻质材料的应用是目前实现汽车轻量化的主要措施,但单一材料不能满足汽车各项性能要求,特别是在减重与安全性存在一定矛盾的情况下。铝和镁合金等轻质金属材料虽然有良好的减重效果,但制造和维修成本较高,且在强度要求高的车身区域不能满足碰撞时的安全性能要求,而高强度钢对保证驾驶室的安全有显著效果。充分利用高强钢和轻金属各自性能优势的“多材料混用”概念应运而生。如今,这一理念已广泛被车企接受,如奥迪A8系列抛弃质量更小的全铝车身而改用多材料混合车身,这一转变表明多材料混用是汽车技术发展的必然趋势。
虽然多材料混用实现了汽车轻量化,但同时使汽车更易发生电化学腐蚀,尤其是电偶腐蚀。电偶腐蚀是由于相接触的异种材料之间存在着电位差,在一定的条件下,电位较低的材料加速腐蚀的现象。此外,电偶腐蚀还会进一步诱发点蚀、缝隙腐蚀,当与外力协同作用时又容易造成磨损腐蚀和应力腐蚀等更危险的腐蚀破坏,从而导致零件或构件的寿命降低,影响汽车长期行驶的安全性。
目前,较为常见的异种金属连接有钢-铝、钢-镁、铝-镁等,大量研究表明这些金属的偶接都会加速阳极金属的腐蚀。因此,揭示典型汽车结构材料偶接件的腐蚀机制,确定影响腐蚀速率的关键因素,从而提出有效的腐蚀防护措施及优化连接设计,对轻量化车辆安全稳定行驶具有重要的指导意义。
典型车用钢及铝合金的耐蚀性
1 普通碳钢
普通碳钢耐蚀性较差,在城市、沿海和工业大气等汽车典型服役环境中的腐蚀等级仅为C5,难以满足车辆长期服役的要求。但其成本较低,在汽车轻量化进程中很难完全被淘汰。碳钢的大气腐蚀常表现为整体腐蚀,短时间内表面就能形成较厚的腐蚀产物层。普遍认为在腐蚀初期,碳钢的腐蚀速率非常大,随着时间的延长,腐蚀速率逐渐减慢并趋于一个比较稳定的值,这与锈层结构和成分有明显关系。
为了改善碳钢的耐蚀性,在碳钢基础上添加少量多元合金元素形成耐候钢。合金元素的作用特点是暴露时间越长,耐蚀效果越明显,耐候钢的腐蚀速率越低。此外,为了延长钢材服役寿命,常对汽车用钢进行镀层处理,如镀锌、镀锌铝等。其中,镀锌层对钢基体保护体现在锌对钢基体的阴极保护作用以及锌生成的各种腐蚀产物对腐蚀的抑制作用,但在实际使用中,需要根据使用环境调整镀层厚度。
2 高强钢
早在1995年,“超轻碳钢车身”的概念就已被提出,采用高强钢可使车身质量减少25%。以轻量化为目标的“多材料混用”理念,使高强钢的应用更具针对性,主要运用在具有高碰撞性能、强度和刚度要求的结构件上,例如立柱、门槛、加强板、梁架等,同时在汽车底盘上也有使用。
高强钢可分为传统高强钢和先进高强钢,先进高强钢不仅力学性能更优,在耐蚀性方面也有一定的提升。但不是所有的高强钢都具有较好的耐蚀性,耐蚀性与高强钢的组织结构有关。
腐蚀产物对进一步腐蚀有重要影响。研究显示,高强钢和普通碳钢的腐蚀产物基本一致,主要有Fe3O4、α-FeOOH和γ-FeOOH。锈层通常为双层结构。外层由γ-FeOOH、α-FeOOH、Fe3O4组成,随着腐蚀时间的延长,腐蚀产物由针状向棉球状转变,由于结构疏松对腐蚀基本不起抑制作用。内层腐蚀产物以Fe3O4为主,结构较为致密,但存在较多的裂纹,对基体的保护有限。
高强钢具有很高的氢脆敏感性。在钢铁冶炼、酸洗、电镀以及服役过程中,氢原子有可能渗入材料基体,在材料-氢-应力三者相互作用下,导致钢发生氢脆。研究发现,钢的氢脆敏感性随着钢强度的提高而增大,因为强度提升可显著降低钢发生氢致延迟断裂的临界氢浓度;当钢的抗拉强度超过1000 MPa后,氢脆几乎不可避免。氢在不同组织中表现出不同的扩散行为,因此显微组织对钢的氢脆有重要影响。热处理、应力应变、冷加工和材料缺陷都对高强钢的氢脆敏感性有不同程度的影响,在材料的冶炼和加工过程中需要额外注意。鉴于氢脆危害巨大,高强钢在汽车上的应用需要考虑氢脆问题。
3 铝合金
相对于高强度钢,铝合金减重效果更为明显,典型的铝合金零件一次减重可达30%~40%,对制动系统和悬架等零件可进一步减重50%。汽车用铝合金有铸件、锻件、挤压件和板材,主要是2xxx系、5xxx系和6xxx系铝合金。A356和ZL101是国内汽车铝制零部件的主要材料,广泛用于轮毂、控制臂、副车架和发动机等铸件;铝合金板件主要应用于发动机罩盖(外板6016,内板5082)、顶盖、翼子板、车门、行李箱盖等覆盖件和车厢底板结构件等。
铝合金在自然状态下存在一层稳定的氧化膜,一定程度上阻碍了腐蚀的发生,但在氧化膜缺陷处(活性较高部位),遭到侵蚀性离子的侵蚀,这些脆弱的区域会首先发生点蚀,点蚀坑的直径和深度取决于合金成分、局部pH和电解质成分。
点蚀过程通常分为两个阶段:第一阶段,点蚀开始,涉及氯离子对氧化物层的吸附和侵蚀,在此阶段,若氧化层重新钝化,点蚀过程不会进入第二阶段;第二阶段,凹坑生长,其特征在于铝或合金元素强烈溶解和腐蚀产物沉淀。
合金化是改善铝材性能的主要途径。合金元素与铝基体结合形成不同类型的金属间化合物,而这些金属间化合物的电化学性质与铝基体不同,易与铝基体形成电偶从而加速局部腐蚀。从电化学角度,常见的金属间化合物包括阳极相如MgZn2、Mg2Si,阴极相如Al2Cu、Al3Fe、Al7Cu2Fe ,以及发生元素选择性溶解后阴阳极性发生反转的Al2CuMg等。以上阴极、阳极都是相对于铝基体而言。
铝合金腐蚀是从点蚀开始的,而第二相的腐蚀往往是点蚀的起点。铝合金中两种合金相诱发点蚀过程如图1所示。阴极相往往是铝合金腐蚀的先行地带,而后逐渐扩展至晶界处,若晶界存在连续的阳极相,则会因阳极相的溶解发生晶间腐蚀。因此,若能从材料本质研究铝合金第二相的腐蚀规律并提出针对第二相腐蚀的有效防护手段,就能从根本上缓解铝合金的腐蚀,进而缓解铝合金与其他材料的电偶腐蚀。
图1 铝合金中两种合金相诱发亚稳点蚀示意
5xxx系铝合金的主要合金元素是镁,其强度随镁含量增加而提高,但电位较基体负的β相不断析出且沿晶界分布,它会先于基体发生腐蚀,最终导致铝合金在晶界处产生点蚀和晶间腐蚀。对于5xxxx系铝合金来说,强度的提升通常会造成耐蚀性下降,研究表明,在Al-Mg合金中加入锌、铜或适量稀土元素对改善合金耐蚀性能有显著效果。
6xxx系铝合金作为可热处理强化的变形铝合金,主要添加的合金元素为镁和硅。6xxx系铝合金通常具有较高的晶间腐蚀(IGC)敏感性。通过添加微量的合金元素或稀土元素也能提高6xxx系铝合金的耐蚀性。
钢-铝合金电偶腐蚀
1 钢-铝合金的电偶腐蚀行为
碳钢与铝合金在海水中的电偶序较为接近,其自腐蚀电位(相对于饱和甘汞电极,SCE)分别为-600 mV和-750 mV左右。铝合金的电位负于钢,当铝合金与钢接触时会发生电偶腐蚀。电偶腐蚀不仅极大增加铝合金的腐蚀速率,而且可能改变其腐蚀机理,腐蚀机理也与不同种类的钢-铝组合有一定关系。但目前从材料本质上揭示钢-铝合金电偶腐蚀机理的研究较少,特别是在车用钢-铝合金材料方面。
影响电偶腐蚀的因素主要为几何因素及环境因素。CUI等研究了多种因素对5050铝合金-45钢电偶腐蚀的影响。结果表明:pH在4~7变化时对电偶电流影响不大,pH的影响体现在强酸或强碱性环境中,这体现了铝合金两性金属的特点;拉应力能显著增加电偶腐蚀效应,并且呈现着正相关关系;铝合金对Cl-含量具有强敏感性,在不含Cl-的蒸馏水中能在较短时间里发生极性反转,由于不存在Cl-的侵蚀作用,铝合金表面易形成完整的氧化膜。在研究温度对2024铝合金-低碳钢电偶腐蚀行为影响时,DONATUS等同样发现,当温度大于35 ℃时会发生极性反转的现象。温度对极性反转的影响是由于温度的升高加快了氧的扩散速率,有利于形成完整的氧化膜。可见铝合金表面氧化膜的完整性对钢-铝电偶腐蚀的极性变化有重要影响。
在实际工程中,由于环境难以可控,几何因素对电偶腐蚀的影响得到了更多关注。MANSFELD研究了氧扩散速度控制情况下面积变化对电偶腐蚀的影响。在忽略阴、阳极扩散电流密度差异情况下,得出阳极腐蚀电流密度(Jag)与氧的扩散电流密度(JLO2)及阴阳极面积比(Ac/Aa)满足正比关系,如下式所示:
苏方腾推导出了阳极和阴极金属均受氧扩散控制时偶对的电偶腐蚀速率方程如下:
式中:Jacorr和Jccorr分别为阳极、阴极金属自腐蚀电流密度;Eacorr和Eccorr分别为阳极金属和阴极金属的自腐蚀电位;βaa和βca分别为阳极极化曲线和阴极极化曲线的Tafel斜率。
从上述两个公式可以看出,在材料表面状态不变,忽略局部腐蚀现象的情况下,阴阳极面积比越大,阳极腐蚀速率越大。PRAYITNO等和姚希等分别采用浸泡试验和电化学试验研究了阴阳极面积比、偶间距对钢-铝电偶腐蚀的影响,并证实随着阴阳极面积比的增大和偶间距的减小,腐蚀速率增大的普遍规律。但ARYA等研究发现,虽然电偶腐蚀速率随着阴阳极面积比增大而增大,但腐蚀电流密度的增长速率却随着阴阳极面积比的增大而降低。所以综合考虑,腐蚀速率存在一个极大值。黄桂桥等的研究证实这一观点。当偶对的电位差较小时,在阴阳极面积比不大的情况下,阳极的腐蚀速率就能达到极限值;而偶对的电位差较大时,在阴阳极面积比很大的情况下,阳极的腐蚀速率才能达到极限值。影响腐蚀速率的离子扩散距离均受阴阳极面积比和偶接件间距的控制,这两种影响因素可联合影响电偶腐蚀。
数值模拟在金属材料的腐蚀防护尤其是电偶腐蚀预测中发挥着巨大作用。SONG等通过理论推导提出了电偶腐蚀过程中电偶电流和电位分布的一维数学模型。STENTA等也从一维角度提出了电偶腐蚀损伤演化的方法。在中性NaCl电解液中,通过有限元方法模拟得到锌-钢和镁-钢的腐蚀行为与试验测试结果具有高度的一致性。近年来,薄液膜下腐蚀问题也受到研究人员的关注。RUIZ-GARCIA等提出了一种薄电解质膜下钢-铝电偶腐蚀的数值模型,并用该模型对腐蚀过程中动态变化的腐蚀产物(OH-、Al3+等)含量进行了预测,预测结果与试验结果获得较好的一致性。有研究者利用Nernst-Planck线性方程,采用边界元法模拟研究了液膜厚度及Cl-含量对薄电解质膜下铸造铝合金与黄铜电偶腐蚀的影响,结果表明:Cl-含量和液膜厚度的增加均会加剧电偶腐蚀,液膜厚度的影响更大。
2 镀层钢-铝合金的电偶腐蚀行为
镀锌层对钢基材有着屏蔽和阴极保护双重作用,能有效延长钢材的使用寿命。但是镀锌钢与铝合金偶接后的使用寿命尚不明确。汽车零件的镀层在实际服役过程中可能发生破损,破损处露出的小面积基体会因为大阴极小阳极效应而加剧镀层与基体之间的电偶腐蚀,加速镀层的破坏。
ZHANG等采用边界元法模拟研究了薄液膜下的电偶腐蚀。结果发现,腐蚀速率与涂层损坏面积密切相关,损伤面积越小,涂层损伤区域的腐蚀速率越大。近年来,车企逐渐使用镀锌镍或涂覆锌铝钢,其与铝合金偶接后的电偶腐蚀特征及腐蚀机理尚不明确。
机械连接的钢-铝合金连接接头和搭接处是电偶腐蚀最为严重的部位。MANDEL等通过动电位极化测试研究了镀锌钢铆钉与两种车用铝合金板材铆接后的电偶腐蚀行为。结果发现:腐蚀初期锌层作为阳极保护了碳钢基体,但随着锌层的溶解,极性发生反转,碳钢作为阴极,铝合金作为阳极发生腐蚀;研究样品的铝钢面积比较大,属于大阳极小阴极,电偶电流较小,铝表面发生严重的晶间腐蚀,大量腐蚀产物富集,这是铝合金自身溶解导致的。
连接方式对接头的耐蚀性也有不小的影响。DU等研究了车用镀锌钢与铝合金两种接头(TOX和SPR接头)的腐蚀特性。由于镀锌层的电位更负,铝合金和受拉应力状态的镀锌层形成大阴极/小阳极状态并发生严重的电偶腐蚀,同时铝合金上出现点蚀和腐蚀裂纹,且受应力部位的腐蚀更为严重。对比发现,TOX接头的耐腐蚀性能要低于SPR接头,这与铆接后板材变形处的应力状态有关。接头处多材料偶接组合情况复杂,使研究也变得复杂。PALANI等和HAKANSSON等也进行了类似的试验。他们发现,随着腐蚀时间的延长,出现多种腐蚀类型,包括电偶腐蚀、点蚀和缝隙腐蚀。研究发现,在某些腐蚀体系中缝隙腐蚀比电偶腐蚀和自腐蚀更为严重。
3 电偶腐蚀研究的关键技术
腐蚀是一个随时间动态演化的过程,随着电偶腐蚀的发展,腐蚀产物积累,合金表面状态以及溶液环境发生相应变化,从而影响电偶腐蚀速率,也有可能改变腐蚀机理。因此,在电偶腐蚀研究中,需要对两电极的耦合电位、电偶电流等参数进行实时监测。
电化学噪声(EN)是指电化学动力系统演化过程中,其电学状态参量(电极电位、外测电流密度等)的随机非平衡波动现象。电化学噪声技术是目前应用最为普遍的电偶腐蚀电位及电流实时监测技术。零电阻电流计(ZRA)即用于电偶腐蚀过程中电化学噪声信号的测量。电化学噪声结合电化学阻抗谱(EIS)可得到电极反应界面特征的动态演化。两种方法均体现了电极表面平均的腐蚀特征,无法给出局部最大腐蚀电流数据及其位置信息。对腐蚀过程中电偶电流分布情况及腐蚀后合金形貌、成分及溶液环境的演化进行定性分析,从而判断腐蚀类型的演化,可更为准确地量化腐蚀速率。SONG对一维电偶腐蚀系统的模拟研究结果表明,电偶腐蚀电流与电位空间分布不均匀,在两电极接触位置阴/阳极电流密度均达到最大值,距离连接处越远,腐蚀电流越小。在SONG等的相关研究中,也出现了这一现象。另外,研究发现电偶对的距离即电极之间的间距是影响电偶腐蚀速率的重要因素之一,电极之间的间距越大,电偶作用影响越弱。
近年来,能获取局部电偶腐蚀信息的微区电化学测量技术在电偶腐蚀机理研究中得到了广泛的应用,如用于测量电偶腐蚀电流空间分布的扫描振动参比电极(SVET),测量气相环境中表面电位分布的扫描Kelvin探针(SKP),测量局部阻抗分布的局部电化学阻抗(LEIS)等。此外,还有一些扫描微电极也可以获取局部电偶腐蚀信息,如微离子选择电极(SIET),它可原位监测活性离子如H+或侵蚀性离子如Cl-的空间分布情况。
SHI等将SVET与SIET技术结合,测量了Al2Cu-Al及Al3Fe-Al电偶对阴/阳极电流及pH的空间分布。IKEUBA等采用了SVET/SIET技术监测了Al/MgZn2电偶腐蚀电流、局部pH及Cl-浓度的分布,并采用扫描电镜及X射线光电子能谱分析了腐蚀产物,证明了酸碱度的变化会引起两电极极性反转现象,并从微观上实时监测腐蚀发生的位置。对于两性金属铝,可通过pH随腐蚀演化的变化有效判断其反应机理。结合扫描电子显微镜(SEM)、透射电子显微镜(TEM)以及X射线光电子能谱(XPS)等设备对腐蚀表面形貌成分以及组织结构进行分析,可为电偶腐蚀机理分析提供更为充分的证据。目前关于钢-铝偶接后腐蚀速率变化规律的研究较少,缺乏试验数据积累,因此无法建立可靠的腐蚀演化预测模型。
随着车用高强钢在汽车行业中的广泛使用,关于不同的高强钢-铝合金机械连接后的电偶腐蚀行为也逐渐成为研究热点。从材料本质来说,合金化处理后的高强钢必然存在微观腐蚀行为的差异。而铝合金作为两性金属,局部的酸化或者碱化都会诱发铝合金的溶解。这种局部pH的变化会显著影响微区电偶腐蚀行为。由于显微组织的尺度较小,微区测量技术对于高强钢-铝合金电偶腐蚀机理的研究更为重要。
汽车电偶腐蚀的防护措施
设计制造中采取的防护措施
选用耐蚀性强的材料可从根本上提高结构的耐腐蚀性能,必要时可对材料进行表面处理进一步提高其耐腐蚀性能,如镀层、涂层处理,铝合金阳极氧化、化学转化膜处理。根据电偶腐蚀机理,应尽量选用电位相近的连接材料以减小电偶腐蚀倾向;应极力避免大阴极小阳极的结构,避免过小的零件为阳极;将偶接材料进行绝缘,或将两种材料完全覆盖以隔绝腐蚀环境。
在车身结构设计时也要考虑后续防腐蚀工艺的适应性,避免不利于涂装的尖角结构。
1、工艺孔
在满足车身强度和刚度的前提下,内腔尽量增加电泳工艺孔以提高漆膜厚度,结合电泳生产线和车身空腔结构,合理设计和布置放气孔,避免出现气室和产生电泳盲区。
2、空 腔
车身空腔对增加汽车强度和减少汽车质量都非常重要,但空腔的防腐蚀较为困难,因此可以通过合理布局空腔位置以提高电泳和注蜡等防腐蚀工艺的可实施性,优化结构,采用空腔注蜡以及强耐蚀性材料等提高空腔防腐蚀性能。
此外,车辆结构设计时应避免腐蚀诱导区的形成。若钢-铝接触面较大时,应采用线接触代替平面接触,中间填充密封胶,这样既消除了腐蚀诱导区,又消除了因接触面积大造成的缝隙。对于外露板件的折边设计,折边方向应与雨水侵入方向一致,下端不应有沟槽,以避免泥水滞留而引发腐蚀。对于水容易流入汇集的区域如车门板件总成、底板,需合理开设排水孔。
不同工艺异种接头处的防护处理
异种件的接头部位往往是电偶腐蚀的敏感位置。在设计时应尽量减少异种接头的数量,可将多个零件设计成一个整体。由于连接处紧固件(铆钉、螺钉等)属于小部件,其材料活性对腐蚀有较大影响,原则上选用的紧固件材料活性需低于大接触面金属的活性,紧固件表面处理也是十分必要,目前最为常用的工艺是达克罗工艺,也可在结构设计时设计预防电偶腐蚀的紧固件。
铆接工艺是钢-铝连接的主要方法之一,在长期使用过程中接头的腐蚀是影响连接强度,导致失效的重要原因。CALABRESE等将自冲铆接头电偶腐蚀降解区进行划分,如图2所示。
图2 自冲铆接头电偶腐蚀导致的临界降解区域
由图2可见,在GC2处镀锌铆钉头与周围钢板形成偶接,前期电偶效应加速锌层腐蚀溶解,但锌层溶解后,由于铆钉和钢属于同类材质,电偶效应大幅减低,在长期服役中对接头的失效影响不大;而GC1和GC3处由于存在缝隙导致电解液侵入,在电偶腐蚀和缝隙腐蚀双重作用下加速了接头的腐蚀失效。所以铆钉连接钢-铝部件时,为了减轻电偶腐蚀应采用带镀层铆钉,若从铝一侧连接,最好选择铝合金铆钉。钢和铝硬度相差较大,当采用铆钉工艺时,应避免超过三层板的连接。因为当铆接力不足时,板与板之间会留有较大缝隙,造成电解液的侵入加剧腐蚀。胶铆复合连接能够在加强连接强度的基础上,避免搭接区域钢、铝的直接接触,既有效防止了电偶腐蚀又阻止缝隙腐蚀的发生。
采用螺栓连接时,需要加非金属绝缘衬垫阻隔异种金属的直接接触,或者用胶隔绝。混合车身上大量的机械连接接头往往是电偶腐蚀的重灾区,机械连接接头的密封处理能减缓接头处的腐蚀。异种材料搭接边缘通常是电偶腐蚀的先行地带,采用密封胶密封可有效抑制腐蚀的发生,为了保证密封质量应严格控制搭接的缝隙尺寸。
车辆不同部位的防腐蚀工艺
车辆的表面涂装是最为有效也是最为成熟的防护方法,不仅对车身电偶腐蚀有显著防护效果,同时也能阻止其他腐蚀形式。车辆不同部位有不同的防腐蚀要求,需要采用先进完善的工艺。
对外观等防护要求高的部件,通常采用底漆+中间漆+面漆的涂层结构。阴极电泳底漆不仅防腐蚀能力强,而且可实现自动化生产,涂装质量稳定,在提高复杂结构零件的防护方面具有不可替代的作用,已经成为整车防腐蚀必不可少的工序。
对于底盘、轮罩等易受沙石飞溅冲击的区域,应该喷涂PVC抗石击涂料,提升车身底部的耐蚀性。
在车门内板、发动机罩和行李箱盖等覆盖件的锐边使用折边胶,既能增加翻边的强度,又能防止水分和道路泥土渗入引起腐蚀。
在缝隙表面、无法封闭的空腔、发动机舱和车门铰链处可采用防锈蜡以提高这些部位的防腐蚀能力。
结束语
随着轻量化进程中多材料混合车身的不断发展,汽车的电偶腐蚀问题必然会成为影响汽车服役寿命的重要因素。铝合金作为轻量化车辆的主要金属材料,其自身腐蚀问题的研究已较为成熟,但是与钢偶接后的电偶腐蚀问题研究尚有不足,尤其是随着新型高强钢的开发应用,从材料本质即微观结构上对钢-铝电偶腐蚀机理的研究较少。
此外,当钢经过涂镀处理后,与铝合金的接触腐蚀随时间的动态演化行为尚不明确,进一步完善不同表面处理的钢-铝偶接后的腐蚀行为和机理是目前需要关注的问题。
钢-铝机械连接处往往是腐蚀的重灾区,在发生电偶腐蚀的同时还伴随着自腐蚀和缝隙腐蚀,接头处多材料偶合也使相关研究变得更为复杂。为保障结构设计可靠性,开展多金属复杂偶合体系腐蚀行为的研究至关重要。
针对汽车电偶腐蚀,目前的防护手段主要为涂装防护以及异种材料之间的有效隔离,但防护效果缺乏数据积累及行业标准。异种材料的连接有多种工艺,在腐蚀防护时需要考虑各自工艺的特点。
值得注意的是,电偶腐蚀的防护应与整车的防腐蚀相结合,采用先进完善的防腐蚀工艺,从而显著延长汽车的服役寿命。
免责声明:本网站所转载的文字、图片与视频资料版权归原创作者所有,如果涉及侵权,请第一时间联系本网删除。
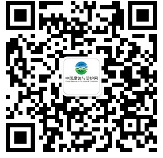
官方微信
《腐蚀与防护网电子期刊》征订启事
- 投稿联系:编辑部
- 电话:010-62316606-806
- 邮箱:fsfhzy666@163.com
- 腐蚀与防护网官方QQ群:140808414