保温层下腐蚀 (CUI) 是指外部被保温层覆盖的管道或设备,由于水分和腐蚀性物质的进入而发生的腐蚀现象[1]。在石油和天然气行业,CUI是设备设施安全运营主要挑战之一,据估计,CUI监检测和修复占据管道维护成本约40%~60%[2,3]。Geary[4]报道了某炼油厂一起由CUI引发的火灾和爆炸事故,造成设备非计划停工、人员疏散和数百万英镑的经济损失;Morey[5]报道了陶氏公司某化工厂一起由CUI造成一条8inch含有非腐蚀性裂解气体 (40%乙烯) 管道发生灾难性事故。通常CUI是由于保温结构隔水措施失效,保温材料吸收水分并通过毛细现象使金属设备设施表面处于润湿状态引起的。CUI具有隐蔽性、高危害性和普遍性的特点,是石化行业的痛点和难点问题,因此发展CUI监检测技术,了解包覆保温层的设备设施运行状态,对腐蚀管理、控制安全风险具有重大意义。
在不拆除保温层条件下监检测设备设施外腐蚀技术须具备无损伤、快速响应、数据可靠、成本低廉、应用便利等特点,以获取保温层下腐蚀状态,预防发生腐蚀事故。保温层遮挡、干湿交替腐蚀环境限制了传统腐蚀监检测技术的应用。针对CUI发生的不同时期,本文对CUI监检测技术及其研究现状进行了综述。
1 CUI前期监检测技术
保温材料浸水是CUI发生的必要条件,当金属暴露在腐蚀性介质环境时,存在腐蚀风险。CUI前期监检测技术采用直接检测保温材料是否浸水或间接检测保温材料浸水引起的温度分布变化,预测CUI倾向。
1.1 射频识别技术 (RFID)
射频识别技术是一种无线技术,由读取器和标签/应答器组成 (图1)。读取器本身通常由微控制器和射频电路组成,具有接收来自标签的响应信号和历史储存信号和将数据写入内存的功能。标签的硬件包括具有存储器的微芯片,存储器存储标签的唯一识别码。标签的射频部分由连接到电容的卷绕或印刷线圈组成,以形成调谐LC电路。目前RFID标签应用在身份证件和门禁控制、供应链和库存跟踪、汽车收费、防盗、生产控制、资产管理等领域,可工作于各种恶劣环境。RFID技术用于CUI前期监测主要研究方向为具有小尺寸和低成本的有源和无源传感器,商业化湿度测量RFID标签产品已均推出,通用版本的标签可感测的湿度范围为0~100%,读取和灵敏度范围可根据使用场景进行调整。
图1 近场感应耦合原理示意图
Tsai等[6]利用无源RFID传感器 (智能传感技术) 收集现场数据,然后将其集成到建筑信息建模 (BIM) 系统中,设计了一个腐蚀预测框架,包括数据采集模块、腐蚀预测模块和审查模块。现场数据中温度、湿度由RFID定时采集,根据预置腐蚀速率预测算法计算腐蚀速率,根据历史数据综合考虑了预测持续时间、腐蚀速率计算腐蚀的预测深度和安全系数。为便于工程应用,在BIM模型上对腐蚀预测结果进行颜色编码,这有助于现场工作人员直观地理解预测并编制现场CUI检查计划。Ayello等[7]提出了一种与电偶对结合改造的RFID标签,用于保温层湿度监测。将有源RFID标签电源更换为Cu-Mg电偶对,当保温层潮湿时,电偶对形成的原电池在1.6 V的电压下产生约2 A的电流,刚好足以激活RFID标签,当保温层干燥时,RFID信号是不活跃的。
RFID技术也存在局限性,在金属结构中应用缩短了RFID传输距离,有采用固定读取器电路的无人机扫描仪相关研究[8]可以解决此问题。有源传感器采用电池或电偶对供电,使用寿命较短,实际应用中需要配合保温层更换周期更换耗材。标签传感器仅能监测线圈区域范围内数据,而CUI通常发生在保温层隔水措施失效位置,具有随机性,需要根据风险等级布置监测点,达到以点带面的效果。
1.2 红外热成像 (IRT)
浸水后的保温层保温隔热性能下降,造成保温层表面温度异常。IRT技术可以分析保温层表面温度分布,推测保温层浸水情况,预警初期CUI风险,划分CUI高风险区。Cadelano等[9]研究了IRT技术用于管道保温层浸水监测,包括管道温度上升、稳定和冷却对监测效果的影响。研究表明使用IRT技术更易检出管道升温过程中保温层浸水位置;而检测稳定运行管道的保温层浸水位置时,可以用荧光灯或调制灯等外部激励方法提升IRT灵敏度。Amer等[10-12]将人工智能与IRT结合,通过使用人工智能的机器学习应用,最大限度地发挥热像成像的潜力。在机器学习算法的初始阶段,通过提取热异常特征,并将其与设备设施完整性中的腐蚀和不规则性进行关联,来预测腐蚀和退化因素。利用机器学习方法增强红外图像处理技术,从而通过精确定位CUI异常和关注区域,检测极易受腐蚀的位置。机器学习分类器在预测CUI异常方面显示出了出色的效果,从185个实际油田资产中预测的精度在85%~90%。
IRT技术用于CUI监测仅能预警初期CUI风险,需要搭配其他监检测手段评估CUI风险,制定治理措施。该技术监测原理基于保温层表面红外线发射量,保温层表面黑度不均匀或设备设施温度较低时,监测方法失效。
1.3 分布式光纤技术
目前分布式光纤技术用于CUI监测主要有两种形式:分布式光纤测温技术和分布式光纤湿度监测技术。其中分布式光纤测温技术基于光纤拉曼散射原理,监测管道沿线因保温层浸水引起的温度场异常,从而实现管道CUI风险区识别[13];分布式光纤湿度监测技术利用光纤表面吸湿性涂层随环境相对湿度膨胀造成的Rayleigh散射中心离散度变化监测环境湿度变化,间接评估管道CUI风险区[14]。相比于温度监测,湿度监测数据与CUI相关性更强,但精确度也受温度变化影响。
刘洪飞等[13]研究了分布式光纤测温技术在保温层破坏监测应用,当保温层发生破坏时,温度异常变化非常缓慢,且在一段时间后趋于稳定,保温层破坏的范围越大,温度异常的范围也越大。Thomas和Hellevang[14,15]研发了一种用于分布式湿度测量的高响应聚酰亚胺光纤,采用参考光纤的补偿方法,有效地减少了温度变化对测量的影响,并验证了该传感器监测水侵空间分辨率为厘米级,同时也证明了在2 km光纤长度上进行精确水侵测量的可行性。Cho等[16]利用聚乙烯醇、CoCl2涂层和普鲁兰涂层串联在光纤上作为包层,研制了一种基于激光吸收对湿度依赖性的光纤传感器,可用于测量80 ℃时65~95%RH的湿度,温度依赖性小到2.5%RH/10 ℃。
分布式光纤技术已实现商业化,监测范围可达100 km,空间定位精度低至5 cm,温度分辨率0.005 ℃,用于泄漏监测和CUI风险监测,主要限制是只能通过湿度和持续时间推测CUI风险和腐蚀程度,不能直接判断腐蚀类型和腐蚀速率。
1.4 微波技术
管道保温结构通常包括钢质管道、保温材料中间层和和金属皮外层,三者组成同轴导波结构:钢质管道作为内导体、金属皮外层作为外导体、中间保温材料作为介电层,微波在其中通过衰减很小,可以沿管道长度上传播很长距离。当保温层发生部分浸水润湿,该区域波导的阻抗会发生变化,由于干湿保温材料之间的介电常数存在差异,导致入射微波信号部分反射。通过对反射微波信号的行程计时,可以准确地确定水的位置[17],微波信号可以在衰减有限的情况下通过弯管和支架传播,可用于监测炼油厂和其他石化工厂的复杂管道工程。
Jones等[18,19]对在同轴波导中传播的模式结构和色散特性进行了研究,确定了无色散的横向磁电模式 (TEM) 是理想的检测方式,为了获得足够的带宽来实现波导特征的空间分辨率,必须使用高于某些高阶模式的截止点的频率。对于真实的管道几何结构,可以通过实验获得高达39 dB的信噪比。低水平的相干噪声使该技术对波导中的水非常敏感,临界浸水区域检出面积为环状保温层面积的5%。微波技术对于理想化的水含量有很高的灵敏度,而实际情况下保温材料浸水后并非是从干燥到100%水饱和的突然转变,多数情况下会存在一个渐进式的过渡区域,Alleyne等[20]用酚醛泡沫模拟真实保温材料浸水饱和情况,研究对微波灵敏度的影响。结果表明,微波反射的振幅主要与入射信号的波长λ、水饱和保温材料截面积As 和干湿过渡长度?有关。当?大于λ/4时,?的影响增大,在此条件下,反射系数比在相同饱和截面积的情况下观测到的突变反射系数低50%以上。λ/4必须与保温层厚度大致相同,以避免高阶导模的信号污染。因此,在实际测试中,?必须小于保温层厚度,才能避免对微波检测的灵敏度产生不利影响。
综合而言,微波技术所需硬件价格低廉,可永久服役,成本低廉,可覆盖整个管道周长,且已实现商业化应用[21,22]。但局限性也很明显,保温材料润湿不需要达到100%水饱和也能引发管道CUI,而微波技术在这中情况下是无法预警CUI风险的;用于三通、支架等复杂管道结构CUI监测相关研究尚无报道。
2 CUI中后期监检测技术
当金属表面发生CUI,通过监测其电化学或复阻抗特征发生变化,可以预警CUI风险,并采取相应补救措施可以避免设备设施由CUI造成的壁厚缺失。当CUI发生一段时间后,设备设施壁厚发生明显缺失,通过测厚技术可以筛查腐蚀缺陷,采取补救措施可以避免由CUI引起的事故,消除隐患。
2.1 电化学噪声 (EN)
当金属表面发生腐蚀过程时,会在微米尺度上产生不规则随机变化,这些变化体现为电信号波动,EN通过分析电化学电位噪声 (EPN) 或电化学电流噪声 (ECN) 随机波动,获取腐蚀过程信息[23,24]。从EN频谱中提取有用信息的数据处理方法是EN监测有效性的关键因素[25,26]。目前EN数据处理方法包括:时域 (主要指统计方法)、频域 (例如快速傅里叶变换,即FFT) 和时频域 (如小波变换)。其中FFT是EN数据分析最常用的一种方法,FFT主要缺陷在于加窗函数宽度引起的具有固定的分辨率[27],宽窗口提供更好的频率分辨率,但时间分辨率较差。窄窗口的时间分辨率较好,但频率分辨率较差[25]。小波变换更适合处理随机波动的EN数据,将数据转换为一系列不同频率的信号[28]。计算每个信号的能量分布,得到所有信号的能量分布图 (EDP)。腐蚀主导过程对应EDP中最大相对能量位置,该位置随时间的变化可以反映腐蚀过程的演变。
Hou等[28]研究采用ECN表征碳钢在岩棉保温材料下的腐蚀过程,使用递归量化分析提取ECN信号中的特征变量,建立随机森林模型,用于判断腐蚀类型。通过失重法验证腐蚀速率,光学显微镜验证腐蚀类型,证明ECN数据分析结果是可靠的,经过修正后的模型成功地用于预测CUI引起的局部腐蚀速率。Caines[29]研究了一种通过监测EPN预测独立电极腐蚀速率方法,以满足现场应用需求,并实现了应用。探究了处于腐蚀环境的独立电极EPN信号与腐蚀速率、质量损失之间的相关性,表明电极表面生成的腐蚀产物会明显减低EPN信号和腐蚀导致质量损失之间相关性,EPN信号和腐蚀速率相关性主要取决于电极润湿时间,电极润湿时间越长,相关性越好。
EN技术目前在大气腐蚀、应力腐蚀开裂、缓蚀剂现场效果等监测领域取得应用[24-26],作为一种原位无损监测技术,可用于监测局部腐蚀信息,在用于CUI监测实验室研究中有很好的效果。但易发生CUI的环境存在干湿循环、冷热交替、可选择保温材料繁多且随服役时间老化,是非常复杂的腐蚀问题,而EN技术用于CUI监测也存在数据分析复杂问题。此外,EN技术采集信号随机波动数量级很小,现场应用环境恶劣,电磁干扰严重也是限制其推广应用的客观原因。另一方面,EN在CUI监测方面的研究仍然相对较少,其结果的可靠性也尚需进一步验证。阵列电极 (WBE) 是一种电化学方法,可以准确、直观地监测电偶腐蚀和局部腐蚀[30,31],Aung等[32]结合WBE和EN研究监测模拟保温层下腐蚀性介质渗入过程。当腐蚀性介质通过渗透接触WBE表面时,观测到EPN信号大幅跳跃与WBE电流分布图结果具有较好的对应性,WBE电流分布图与实际观测的WBE腐蚀表面具有良好的相关性。
2.2 射频识别技术 (RFID)
RFID技术同样可以用于CUI中后期监测,其主要研究方向为无源传感器,阅读器通过发射电磁波向标签传送足够的能量,支持其完成CUI相关数据采集监测。无源传感器工作不依赖任何耗材,服役期长,维护成本低,非常适合长期CUI监测。
Zhang[33]与研究了采用商用无源13.56 MHz RFID标签进行腐蚀检测和腐蚀阶段分类的方法,采用峰间幅值监测表征低碳钢的一般腐蚀等级。在论文中还研究了RFID监测腐蚀层厚度、电导性和渗透性变化,用于评估钢材所处腐蚀阶段,测得的RFID结果与腐蚀层实际电导率和渗透率变化的相关系数超过90%。Alamin等[34]开发了一种无源低频RFID技术。经试验验证该射频识别系统不仅能够通过标签信号的振幅随着腐蚀程度的增加而增加,区分腐蚀样品和未腐蚀样品,而且能够区分不同表面粗糙度的样品。
RFID用于表面状态监测,阅读器与标签的空间位置会影响到传感器分析结果,很大程度上限制了RFID技术用于CUI中后期监检测的商业化应用。
2.3 电容成像 (CI)
通过带有共面电极的CI传感器在保温层外表面对结构扫描,将电性能分布绘制成图像,根据电性能变化判断是否发生CUI[35]。相比传统脉冲涡流技术,CI对构件表面CUI特征更加敏感,并且不存在最大提离高度限制,更适用于较厚保温层CUI监测[36]。除此之外,CI还可以反映保温层内部的缺陷信息,包括水侵入、空隙和保温材料老化等[35]。目前,CI已用于检查输油管道、复合抽油杆和储罐腐蚀缺陷[37]。
Li等[38]分析测量灵敏度分布的基础上,采用二维反褶积方法来解决了由“模糊效应”导致无法量化表征缺陷尺寸,探讨了CI技术的穿透深度、信号强度和成像分辨率之间的权衡,论证了提取特征真实形状的方法可行性。Yin等[39]提出了一种基于CI技术提离效应的腐蚀深度反演方法,包括建立提离曲线、获得扫描曲线和拟合反演。该方法能够获取缺陷实际深度信息,反演深度的误差率小于10.00%。文献[35]利用CI扫描在不同提升条件下获得的最大变化率 (MVR) 检索绝缘覆盖导体表面特征的尺寸。使用该方法对目标金属表面进行线扫,获取修正后的MVR数据分布,数据处理得到CUI缺陷面积和坑深。
CI技术可以提供更丰富的保温层下信息 (水侵入、空隙和保温材料老化等),而目前在工程应用仅限于缺陷初步筛查,还无法工程应用于量化表征缺陷尺寸。从监测原理而言,该技术更适用于相比传感器尺寸更大的缺陷监测,对于较小的缺陷,需要考虑一个额外的参数,即特征的宽度,在这种情况下,需要两个不同提离高度的测量值信号变化的二维网格数据[39],目前尚无相关研究成果。
2.4 射线成像技术
目前用于CUI检测辐射源主要为γ源,根据胶片或成像板与辐射源的相对位置划分,射线成像技术可以分为直接成像法和后向散射法 (见图2)[40-44]。直接成像法是测量以直线路径穿过物体的入射光束的衰减,入射光束在待测物体中被部分吸收和散射,剩余的透射辐射沿直线到达检测器。衰减量与分布在物体中的各相的原子数以及它们的密度分布有关。当射线在待测物体沿直线传播时,由于康普顿相互作用,部分射线会散射回来,后向散射法是一种利用散射辐射成像技术,辐射在管道输送液体中衰减很少,适用于大型管道成像,且直接成像图像信息是管壁两侧腐蚀信息的加和,数据解读存在困难。综上所述,后向散射法更适合用于CUI检测。
图2 两种成像技术[41]
Sipaun等[40]提出了一种使用伽马射线透射测量和计算机断层扫描 (CT) 来检测和定位管道发生CUI区域的筛选和扫描方法。通过筛选获得沿管道长度的测量值,以缩小管道异常的可疑区域,扫描管段CT图像显示管壁损失。Abdul-Majid等[41-43]建立了一个后向散射成像系统,散射辐射由一个闪烁探测器测量,该探测器使用一个二维机械扫描系统扫描待测物体。用多通道分析仪 (MCA) 显示伽马光谱,并选择能量窗口宽度,以便只测量康普顿单次散射计数,采用用LabVIEW计算机程序构建图像。成功地获得了保温层下物体外表面的缺陷图像,该系统能够检测壁厚超过15 mm的大型管道的壁厚变化。熊亮等[44]开发了一套基于γ射线数字扫描检测技术 (GSDT) 的CUI在线监测系统,用于CUI管道剩余壁厚监测。实验表明,该系统测量误差平均值约0.20 mm,方差0.09 mm,误差范围满足CUI在线监测需求。
射线成像技术具有结果直观可靠的优点,属于一种商业化成熟的无损检测技术。但缺点也很明显,成本昂贵,存在辐射风险,不能用于外部应力腐蚀开裂检测,且监测灵敏度较差,腐蚀缺陷较小时,难以通过该技术预警腐蚀风险。
2.5 超声导波技术
超声导波是常用的管道CUI筛查技术,环状探头由一组交流线圈和强磁性材质薄片组成,将磁化后的薄片 (相当于直流偏磁场) 通过耦合的方式紧贴于管道外表面,探头激发产生的机械弹性波沿着管道双向传播遇到体积截面增加或者减少时,一部分波反射回来,被线圈传感器接收,从而实现对缺陷的检测[45]。商业化超声导波检测设备检测管道温度范围-40~350 ℃,最高检测灵敏度1%壁厚损失。在实际应用中,超声导波检测需拆除部分保温层用于安装探头,恢复保温层可能导致隔水措施失效。焊接钢管的环焊缝也会在反射机械弹性波,掩盖附近缺陷信号,造成漏检,不能用于外部应力腐蚀开裂检测。用于CUI缺陷筛查时,保温层遮盖为环焊缝信号排除造成困难。虽然超声导波用于CUI筛查还存在一些问题,但覆盖范围大,快速高效,仍很受市场认可。超声导波监测技术已在包覆保温层的海上油气平台立管实现商业化应用,覆盖范围和监测效果主要受安装位置影响,在较理想情况下检测范围可达40 m。
2.6 脉冲涡流技术 (PEC)
PEC的工作原理是分析急剧电磁跃迁后导电元件内部的瞬态涡流,每个脉冲分为三个阶段:发射阶段,在此期间探头将磁场注入整个被检查部件;短暂截止阶段,当磁场发射突然停止时,将涡流引入部件;接收阶段,在此期间,磁性传感器测量涡流的衰减。涡流的衰减率与被检查导电部件的厚度直接相关[46]。PEC是一种商业化的检测工具,探头覆盖区平均壁厚检测精度在±10%,可以在不移除管道和储罐上的保温材料的情况下检测腐蚀缺陷[47]。PEC也存在一定局限性:单次检测结果仅能覆盖探头范围,大型结构检测效率低;不能用于外部应力腐蚀开裂检测;保温结构外层金属皮对检测结果影响较大,在弯头虾米腰等金属皮搭接的位置表现不佳。
2.7 示踪剂技术
Lorenz和Sprachmann[48]公开了一种通过检测示踪剂判断是否存在CUI的方法。采集保温材料浸出液分析腐蚀反应的产物或额外加注示踪剂含量变化,当设备设施材质为碳钢时,示踪剂可以包括可包含磷化氢、硫醇、醇、酸、酮、醛或铁氧化过程中释放的任何其他化学成分。额外加注示踪剂可以借助扫描流体起到载体和置换作用,扫描流体通常选择空气、氮气等不参与反应流体。
3 存在的问题与展望
(1) 保温层隔水措施失效发生浸水后,如果金属表面涂层完整或金属表面快速恢复干燥,腐蚀将不会发生。因此CUI前期监检测技术获取的保温层环境信息主要用于推测CUI倾向,以指导及时采取防护措施和检维修作业。
(2) 目前EN和RFID技术是少数在腐蚀发生初期就可以及时预警的CUI中期监检测技术,但尚未实现商业化应用。EN采集信号包含了多个腐蚀过程,对有效信号的提取、不同腐蚀过程信号的区分能力有非常高的要求。RFID用于表面状态监测,阅读器与标签的空间位置会影响到传感器分析结果,实际应用中需额外现场调试。
(3) CUI具有隐蔽性,腐蚀发生一段时间后,金属缺失量达到一定程度才能被后期监检测技术检出,而对设备设施造成的损伤不可逆转。虽然射线成像、超声导波和脉冲涡流技术已实现商业化应用,但不能用于外部应力腐蚀开裂检测且成本昂贵,还不能完全满足需求。
(4) 目前已开展的研究主要集中在CUI的前期和后期监检测技术,中期的相关研究很少;此外,CUI监检测技术还存在数据解读不充分的问题,准确性和精度还有待于进一步提高。
(5) 下一步应从CUI前期的腐蚀倾向、中期的腐蚀发展、后期的腐蚀损伤的全过程,进行CUI监检测技术的研究开发,强化先进技术的应用研究,并结合保温层环境信息和保温类型、管道复杂程度、保温条件等各类关键因素,构建适当的预测模型,不断提高监检测的准确性和精度;同时,根据不同环境下的保温类型、保温结构的特点,综合考虑布设监测传感器网络时监测系统容错性、可拓展性和综合成本,实现CUI的全过程准确监控和工业化应用。
参考文献
1 Cullin M J, Birmingham G, Srinivasan R, et al. Injectable sodium bentonite inhibitors for corrosion under insulation [J]. J. Pipeline Syst. Eng. Pract., 2020, 11: 04020036
2 Burhani N, Muhammad M, Ismail M C. Corrosion under insulation rate prediction model for piping by two stages of artificial neural network [A]. 6th International Conference on Production, Energy and Reliability 2018: World Engineering Science & Technology Congress (ESTCON) [C]. 2018
3 Eltai E O, Musharavati F, Mahdi E S. Severity of corrosion under insulation (CUI) to structures and strategies to detect it [J]. Corros. Rev., 2019, 37: 553
doi: 10.1515/corrrev-2018-0102
4 Geary W. Analysis of a corrosion under insulation failure in a carbon steel refinery hydrocarbon line [J]. Case Stud. Eng. Failure Anal., 2013, 1: 249
5 Morey A. Corrosion under insulation revisited: Aren't we about to finish that project?[J]. Proc. Saf. Prog., 2018, 37(4): 502
doi: 10.1002/prs.12007
6 Tsai Y H, Wang J, Chien W T, et al. A BIM-based approach for predicting corrosion under insulation [J]. Autom. Constr., 2019, 107: 102923
doi: 10.1016/j.autcon.2019.102923
7 Ayello F, Hill D, Marion S, et al. Integrated sensor networks for corrosion under insulation: monitoring, cost reduction, and life extension strategies [A]. Corrosion 2011 [C]. Houston, 2011
8 Deif S, Daneshmand M. Multiresonant chipless RFID array system for coating defect detection and corrosion prediction [J]. IEEE Trans. Ind. Electron., 2020, 67: 8868
9 Cadelano G, Bortolin A, Ferrarini G, et al. Corrosion detection in pipelines using infrared thermography: experiments and data processing methods [J]. J. Nondestr. Eval., 2016, 35: 49
doi: 10.1007/s10921-016-0365-5
10 Amer A, Al-Shehri A, Cunningham V, et al. Artificial intelligence to enhance corrosion under insulation inspection [A]. International Petroleum Exhibition & Conference [C]. Abu Dhabi, 2020
11 Cao Q, Pojtanabuntoeng T, Esmaily M, et al. A Review of Corrosion under Insulation: A Critical Issue in the Oil and Gas Industry[J]. Metals, 2022, 12(4): 561
doi: 10.3390/met12040561
12 Amer A, Al Shehri A, Parrott B, et al. Thermography image processing with neural networks to identify corrosion under insulation (CUI) [P]. U.S. Pat, 10551297B2, 2020
13 Liu H F, Han Y, Feng X, et al. Test on tiny leakage and insulating layer damage monitoring of buried oil pipelines using distributed optical fiber temperature sensor [J]. Oil Gas Storage Trans., 2018, 37: 1114
13 刘洪飞, 韩阳, 冯新 等. 埋地管道微小泄漏与保温层破坏分布式光纤监测试验 [J]. 油气储运, 2018, 37: 1114
14 Thomas P J, Hellevang J O. A distributed fibre optic approach for providing early warning of corrosion under insulation (CUI) [J]. J. Loss Prev. Process Ind., 2020, 64: 104060
doi: 10.1016/j.jlp.2020.104060
15 Thomas P J, Hellevang J O. A high response polyimide fiber optic sensor for distributed humidity measurements [J]. Sens. Actuators, 2018, 270B: 417
16 Cho H, Tamura Y, Matsuo T. Monitoring of corrosion under insulations by acoustic emission and humidity measurement [J]. J. Nondestr. Eval., 2011, 30: 59
doi: 10.1007/s10921-011-0090-z
17 Simonetti F, Nagy P B, Bejjavarapu S M, et al. Long-range microwave detection of wet insulation for CUI mitigation [A]. Corrosion 2015 [C]. Dallas, 2015
18 Jones R E, Simonetti F, Lowe M J S, et al. Use of microwaves for the detection of water as a cause of corrosion under insulation [J]. J. Nondestr. Eval., 2012, 31: 65
doi: 10.1007/s10921-011-0121-9
19 Jones R E, Simonetti F, Lowe M J S, et al. Use of microwaves for the detection of corrosion under insulation: a sensitivity study [J]. AIP Conf. Proc., 2011, 1335: 1714
20 Alleyne D N, Pavlakovic B, Lowe M J S, et al. Rapid, long range inspection of chemical plant pipework using guided waves [J]. AIP Conf. Proc., 2001, 557: 180
21 Mudge P J. Field application of the teletest long-range ultrasonic testing technique [J]. Insight, 2001, 43: 74
22 Guo Q, Wu X Q, Xu S, et al Research status and progress of high temperature and high pressure on-line corrosion monitoring technology [J]. Corros. Sci. Prot. Technol., 2016, 28: 160
22 郭琦, 吴欣强, 徐松 等. 高温高压在线腐蚀监测技术研究现状与进展 [J]. 腐蚀科学与防护技术, 2016, 28: 160
23 Xia D H, Song S Z, Behnamian Y. Detection of corrosion degradation using electrochemical noise (EN): review of signal processing methods for identifying corrosion forms [J]. Corros. Eng., Sci. Technol., 2016, 51: 527
24 Zhang Z, Wu X Q, Tan J B. Review of electrochemical noise technique for in situ monitoring of stress corrosion cracking [J]. J. Chin. Soc. Corros. Prot., 2020, 40: 223
24 张震, 吴欣强, 谭季波. 电化学噪声原位监测应力腐蚀开裂的研究现状与进展 [J]. 中国腐蚀与防护学报, 2020, 40: 223
25 Homborg A M, Tinga T, Van Westing E P M, et al. A critical appraisal of the interpretation of electrochemical noise for corrosion studies [J]. Corrosion, 2014, 70: 971
doi: 10.5006/1277
26 Li H J, Wang Q S, Liao Z H, et al. Electrochemical noise behavior of X70 steel and its weld in Cl--containing high pH solution [J]. J. Chin. Soc. Corros. Prot., 2022, 42: 60
26 李鸿瑾, 王歧山, 廖子涵 等. X70钢及其焊缝在含Cl-高pH值溶液中电化学噪声行为研究 [J]. 中国腐蚀与防护学报, 2022, 42: 60
27 Wei Y J, Xia D H, Song S Z. Detection of SCC of 304 NG stainless steel in an acidic NaCl solution using electrochemical noise based on chaos and wavelet analysis [J]. Russ. J. Electrochem., 2016, 52: 560
doi: 10.1134/S1023193516060124
28 Hou Y, Pojtanabuntoeng T, Iannuzzi M. Use of electrochemical current noise method to monitor carbon steel corrosion under mineral wool insulation [J]. npj Mater. Degrad., 2020, 4: 39
doi: 10.1038/s41529-020-00144-3
29 Caines S. Development of a simplified electrochemical noise method to monitor assets under insulation [D]. St. Johns: Memorial University, 2016
30 Wu Y L, Zhang D P, Cai G Y, et al. Effects of temperature on polarity reversal of under deposit corrosion of mild steel in oilfield produced water [J]. Corros. Eng., Sci. Technol., 2020, 55: 708
31 Shi W, Wang T Z, Dong Z H, et al. Application of wire beam electrode technique to investigate the migrating behavior of corrosion inhibitors in mortar [J]. Constr. Build. Mater., 2017, 134: 167
doi: 10.1016/j.conbuildmat.2016.12.036
32 Aung N N, Wai W K, Tan Y J. A novel electrochemical method for monitoring corrosion under insulation [J]. Anti-Corros. Methods Mater., 2006, 53: 175
doi: 10.1108/00035590610665590
33 Zhang H. Radio frequency non-destructive testing and evaluation of defects under insulation [D]. Newcastle: Newcastle University, 2014
34 Alamin M. Passive low frequencey RFID for detection and monitoring of corrosion under paint and insulation [D]. Newcastle: Newcastle University, 2014
35 Yin X K, Gu Y, Li Z, et al. Retrieving dimensions of surface features on conductors covered by insulation using the maximum Variation Ratio (MVR) in capacitive imaging [J]. NDT & E Int., 2021, 117: 102384
doi: 10.1016/j.ndteint.2020.102384
36 Yin X K, Hutchins D A, Chen G M, et al. Detecting surface features on conducting specimens through an insulation layer using a capacitive imaging technique [J]. NDT & E Int., 2012, 52: 157
doi: 10.1016/j.ndteint.2012.08.004
37 Yin X K, Hutchins D A, Chen G M, et al. Studies of the factors influencing the imaging performance of the capacitive imaging technique [J]. NDT & E Int., 2013, 60: 1
doi: 10.1016/j.ndteint.2013.07.001
38 Li Z, Yin X K, Yan A, et al. Characterizing surface features on conducting specimens through an insulation layer using the capacitive imaging technique [J]. AIP Conf. Proc., 2016, 1706: 090003
39 Yin X K, Li Z, Yuan X A, et al. Corrosion depth inversion method based on the lift-off effect of the capacitive imaging (CI) technique [J]. IEEE Access, 2020, 8: 22770
doi: 10.1109/ACCESS.2020.2970204
40 Sipaun S, Ab Rahman M F, Hasan H, et al. Examination of corrosion under insulation using gamma ray computed tomography [A]. IOP Conference Series: Materials Science and Engineering [C]. Selangor, 2020: 012039
41 Abdul-Majid S, Balamesh A. Imaging corrosion under insulation by gamma ray backscattering method [A]. 18th World Conference on Nondestructive Testing [C]. Durban, 2012: 16
42 Abdul-Majid S, Balamesh A. Single side imaging of corrosion under insulation using single photon gamma backscattering [J]. Res. Nondestr. Eval., 2014, 25: 172
doi: 10.1080/09349847.2013.869376
43 Susiapan Y S L, Rahim R A, Pusppanathan J, et al. Portable gamma-ray tomography instrumentation for investigating corrosion under insulation of pipelines [A]. Proceedings of the 13th WSEAS International Conference on Circuits [C]. Rodos, 2009: 168
44 Xiong L, Sun Y J. Research on monitoring system for corrosion of pipeline under insulation and its application [J]. J. Saf. Sci. Technol., 2019, 15(11): 102
44 熊亮, 孙玉江. 保温层下管道腐蚀监测系统及应用研究 [J]. 中国安全生产科学技术, 2019, 15(11): 102
45 Bray A V, Corley C J, Fischer R B, et al. Development of guided wave ultrasonic techniques for detection of corrosion under insulation in metal pipe [A]. Proceedings of the 1998 ASME Energy Sources Technology Conference [C]. Houston, 1998
46 Cheng W Y. Pulsed eddy current testing of carbon steel pipes' wall-thinning through insulation and cladding [J]. J. Nondestr. Eval., 2012, 31: 215
doi: 10.1007/s10921-012-0137-9
47 Sophian A, Tian G Y, Taylor D, et al. A feature extraction technique based on principal component analysis for pulsed Eddy current NDT [J]. NDT & E Int., 2003, 36: 37
doi: 10.1016/S0963-8695(02)00069-5
48 Lorenz M, Sprachmann G. Method and system for detecting corrosion of an insulated corrosion prone object [P]. U.S. Pat, US-9267874-B2, 2016
免责声明:本网站所转载的文字、图片与视频资料版权归原创作者所有,如果涉及侵权,请第一时间联系本网删除。
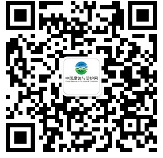
官方微信
《腐蚀与防护网电子期刊》征订启事
- 投稿联系:编辑部
- 电话:010-62316606
- 邮箱:fsfhzy666@163.com
- 腐蚀与防护网官方QQ群:140808414