2 铜镍合金耐蚀性的影响因素
图 4 影响铜镍合金耐蚀性的合金元素种类及作用
Fig.4 Types and effects of alloying elements that affect the corrosion resistance of copper-nickel alloys
2.2 温度对铜镍合金耐蚀性的影响
温度对 Cu-Ni 合金耐蚀性能的影响包括对腐蚀反应的动力学参数、氧的扩散系数等方面,温度的升高 可以使腐蚀反应的动力学参数和氧的扩散系数增加,但是氧的溶解量会降低[28]。温度也影响了合金表面钝 化膜的变化[29]。关于温度对 Cu-Ni 合金耐腐蚀性能的影响还没有形成统一的认识,结论各有差异[30-31]。ASTM 腐蚀研究数据显示[32]:当 90Cu-10Ni 在 18 ℃和 28 ℃之间的浸泡时,比在该温度范围以下和以上浸泡时表现出更好的耐腐蚀性。Wan 等[33]研究了铜在高温下的腐蚀,结果表明初期腐蚀速率与暴露时间呈线性关系, 随后呈指数关系,而且温度升高会成倍地加速铜的腐蚀。腐蚀产物分析表明,铜在高温下的腐蚀产物为 Cu2O 和 CuO,其中内层是 Cu2O,外层由 CuO 和 Cu2O 组成。Cai 等[34]的研究表明前期温度的升高会导致 扩散速率的加快,铜镍合金腐蚀速率会升高;但是后期合金的腐蚀速率会随着海中溶解氧的溢 出而降低。
2.3 pH 值对铜镍合金耐蚀性的影响
pH 值也是铜镍合金耐蚀性的重要影响因素之一。Al-Thubaiti 等[35]为了研究 pH 值对铜镍合金腐蚀的影 响,在室温大气条件下加盐酸进行了腐蚀试验。实验是在对大气开放的容器中进行的,氧的含量较高。结果 表明在温度相同的条件下,pH 值越小,极化电阻越小,其对应的腐蚀电流越大,合金越容易受到腐蚀。罗 宗强等[36]研究了 Cu-17Ni-3Al-X(X=Cr、Si、Ti、Mn、Zr;总含量≤4%)合金在 pH 值变化的 3.5% NaCl 溶 液中的腐蚀行为,结果表明随着 pH 值的增加,合金的平均腐蚀速率迅速降低,当 pH 值=3 时,合金的平 均腐蚀速率为 0.147 mm/a;当 pH 值=6 时,合金平均腐蚀速率下降到 0.039 mm/a;当溶液的 pH 值=12 时, 合金的平均腐蚀速率约为 0.005 mm/a,说明合金在酸性溶液中相对于中性和碱性溶液更易受到腐蚀。原因 是当溶液为强酸性时,铜合金表面不容易形成致密的保护膜;且溶液 pH 不同时,电化学反应过程中阴极的 还原反应也有所差异。Chen 等[37]研究了 Cu-Cr-Zr 合金在 0.6 mol/L NaCl 溶液和不同 pH 的纯水溶液条件下 的耐蚀性,结果显示氯离子的加入降低了合金的耐蚀性;Cu-Cr-Zr 合金在碱性溶液中的耐蚀性优于在酸性 溶液中,在强酸溶液中发生均匀腐蚀,而在碱性溶液中发生局部腐蚀。Bai 等[38]研究了氯化物存在下产酸杂 色曲霉对铜的腐蚀的影响。结果表明:在 0.01% NaCl 溶液中,真菌会分泌多种有机酸,如乙酸和乳酸,会 使得溶液的 pH 从 7.01 降到 5.26,这些有机酸扩大了铜的腐蚀面积,促进了大气腐蚀。在腐蚀产物中发现 有羧酸铜的存在,随着腐蚀产物的积累,空气中的 CO2 和 O2 在铜表面扩散,Cl-的扩散受到了抑制。综上, pH 值的差异引起的合金耐蚀性的不同主要是由于不同的 pH 值条件下,电化学反应中吸氧腐蚀的阴极还原 反应不同[39],其次 pH 值的不同也会导致合金表面腐蚀产物的不同,这也是影响合金腐蚀速率的重要因素。
2.4 硫离子对铜镍合金耐蚀性的影响
硫酸盐细菌还原、工业废弃物的排放、腐烂的动植物等最终都会以硫化物的形式进入到海水中。现有研 究证实天然海水或人造海水中硫化物的存在会加速铜镍合金的腐蚀[40-41]。如郑强等[42]研究了硫酸盐还原菌 (SRB)生物膜下 BFe30-1-1 合金的腐蚀行为。结果表明 SRB 的存在使电极自腐蚀电位负移,合金腐蚀速 率显著增加;极化电阻在细菌生长后期显著降低,在 SRB 的作用下合金发生了严重的点蚀。Rahmouni 等[43] 研究了 3% NaCl 中添加硫化物对铜合金腐蚀的影响。EIS 测量结果显示,随着硫化物浓度增加,电化学阻抗 谱半径逐渐减小,合金腐蚀倾向增加。有学者认为铜的钝化膜结构和性能很大程度取决于硫化物的浓度。
Kong 等[44]研究了硫化物浓度对铜在含厌氧氯化物溶液中腐蚀的影响。结果显示:在含硫化物溶液中生成的 腐蚀产物包含 Cu2S、CuS。铜的耐蚀性随硫化物浓度增加而降低,保护膜的生长和溶解速率更高。Gao 等[45] 研究了 C71500 合金在高浓度硫化物污染的海水中的腐蚀行为。结果表明合金浸泡初期腐蚀速率较高,表现 出均匀腐蚀,腐蚀产物主要由 Cu2S、CuS、Cu2O 等组成,随着浸泡时间的延长,Cu2S 的含量逐渐增加,S 2- 的加入导致了 Fe 和 Ni 的溶解,Cu2O 膜的形成受到了阻碍,促进了腐蚀过程。Chen 等[46]发现铜在含硫化 物环境中腐蚀很快,当硫化物浓度足够大时,被硫化物沉积的表面区域和多孔沉积物的区域之间可以形成 微电偶腐蚀,这样会导致多孔膜的局部腐蚀。
3 提高铜镍合金耐蚀性的方法
研究表明铜镍合金在海水中有良好的耐蚀性与铜镍合金表面形成的腐蚀产物有关,在相同的腐蚀介质 条件下,合金抵御冲刷腐蚀的能力主要取决于自身的力学性能和表面的钝化膜结构。为了提高铜镍合金耐 腐蚀的能力,现有途径主要包括合金化法、牺牲阳极的阴极保护法、缓蚀剂的应用、防腐涂料、超疏水膜技 术、自组装单分子膜技术等。
3.1 合金化法
合金化法是提高铜镍合金耐蚀性的最基础、简单有效的方法之一。Yang 等[47]研究了 Cu-7Ni-3Al-1Fe1Mn 合金在 3.5% NaCl 溶液中的腐蚀行为。微观分析结果表明浸泡在 3.5%NaCl 溶液中形成的主要腐蚀产物 是Cu2(OH)3Cl和Cu2O。其中Cu2(OH)3Cl存在于合金表面,Cu2O主要集中在合金基体表面内侧附近。Zubeir[48] 研究发现,当 Fe 的含量大于 2%时,90Cu-10Ni 换热器在海水中的腐蚀速率会变大。过控制 Fe/Mn 比例找 到提高 B10 耐腐蚀性能的最佳合金配比,发现当 Fe/Mn=3:2 时,合金的耐腐蚀性能最好。Zhu 等[49]研究了 不同铁含量对 70/30 铜镍合金腐蚀性能的影响。结果显示,当 Fe 的含量为 1.0%时,合金的耐蚀性最好。他认为铁元素能够提高合金耐腐蚀能力是因为在合金的腐蚀过程中一部分铁会取代 Cu2O 薄膜中的阳离子空穴,空穴数量减少,薄膜电阻增加,除此之外一部分铁还会以 γ-FeOOH 的形式在腐蚀产物膜中积累和富集, 该物质具有较高的电阻率。Shao 等[50]研究了 Fe/Mn 含量对 90/10 铜镍合金腐蚀性能的影响。他认为当 Fe/Mn 含量为 1.69/0.69 时,此时 90/10 铜镍合金具有良好的耐蚀性。Zhu 等[51]研究了不同 Mn 含量对 90/10 铜镍合 金耐腐蚀性的影响。结果表明在铜镍合金中添加适量的 Mn 元素可以提高合金的耐蚀性。他认为 Mn 的加入 促进了 Ni 对阳离子空位的填充,生成了更多的 NiO,进一步增强了腐蚀产物膜的稳定性。童庆坤等[5]研究 了微量 Zr、Ti、B 对 B30 合金铸态组织和性能的影响,结果表明:三种元素均有晶粒细化和强化作用,其 中微量 B 对合金晶粒细化的效果强于微量 Zr 元素;而 Ti 的添加主要是提高了合金的硬度。微量元素的加 入使得合金的铸锭组织枝晶偏析逐渐减弱,力学性能提高间接提高合金的耐蚀性。Taher 等[52]认为,从相图 考虑,Cu-Ni 合金中加入的 Fe 的最大含量为 1.5%,若 Fe 的含量过多时会在晶界处形成第二相,腐蚀速率 加快;经人工盐溶液浸泡的 Cu-Ni-Fe 合金,其表面形成的钝化膜包括内层和外层,内层钝化膜为多孔结构 且膜层较厚,与基体结合力较好,加入 Fe 会使外层孔隙消失,钝化膜中生成的 Fe2O3 提高了钝化膜的耐蚀 性,也增加了钝化膜外层的密度。Rosalbino 等[53]研究了 Cu91.6-Nd8.4 和 Cu90.5-Er9.5 合金在碱性溶液中的 腐蚀性能,结果发现:与纯铜相比,Cu-RE(RE=Nd、Er)合金的耐蚀性更好。Li 等[54]采用活化反应烧结技 术制备多孔 Ni-Cr-Mo-Cu 合金,通过 SEM、XPS 等技术表征结果表明,随着 Cr 元素的增加,合金的防腐能 力也逐渐增强。稀土元素因其独特的物理化学特性,可以吸收杂质气体,净化基体,近年来受到广泛关注。Burleigh 等[55]发现铜镍铸件中加入铁元素可以提高合金的耐蚀性,但是在海水中铁的析出物会通过电偶腐 蚀导致晶界腐蚀,而通过冲击试验表明,2%的铟可以提高合金的耐蚀性也不会发生晶界腐蚀。Lin 等[56]发 现在铝黄铜中加入稀土 Ce 和 La 可以使合金表面的腐蚀产物膜层更加致密,合金的点蚀程度 显著降低。谢蔚等[57]发现纯铜在 NaCl 溶液中浸泡后生成了 Cu2O 和 Cu2(OH)3Cl 等腐蚀产物,纯铜中加 入稀土 La 以后会生成网格状的 CuLa 中间相,其具有较大的体积分数,在合金表面形成阻挡层,提高纯铜 的耐腐蚀性能。宋春梅等[4]研究了稀土钇对 B10 合金耐蚀性的影响。结果表明:添加稀土 Y 的 B10 合金能 够细化二次枝晶的间距,优化了合金晶界结构,抑制了沿晶腐蚀的现象,从而提高了 B10 合金的耐蚀性。冷翔等[58]研究了稀土 La 对 B10 合金耐蚀性的影响,结果表明 La 能够提高 B10 合金表面腐蚀产物膜与基体 的稳定性,减少腐蚀产物中的裂纹。郝齐齐[59]利用热-力模拟技术对 BFe10-1.5-1 合金的热变形行为进行研 究,结果表明当 Ce 含量为 0.014 wt.%时,可以有效细化合金的树枝晶,合金中的稀土 Ce 以团状颗粒、椭 球相形式存在。陈少华等[60]研究了稀土元素 Ce 对 Cu-10Ni-7Si-5Mn 合金组织和耐蚀性的影响。结果表明:CuCe 相与基体呈现半共格界面,起到细化合金组织作用。稀土 Ce 以其氧化物 Ce2O3 和 CeO2 的形式存在于 腐蚀产物中,通过提高腐蚀产物膜层的阻抗值,促使开路电位向正移动来提高合金的耐腐蚀性能。Zhang 等 [61]研究了稀土元素 Nd 对 Cu-13.0Al-4.0Ni 高温形状记忆合金组织、力学性能的影响。结果表明 Cu-13.0Al4.0Ni 合金中添加 Nd 可以细化晶粒,晶粒尺寸从毫米级减小到几百微米级,晶粒细化改善了合金的力学性 能。Dalvand 等[62]研究了合金元素 Ti 和混合稀土 Ce、La 对 Cu-Ni-Al 系合金的组织的影响,结果表明稀土 作为二次细化剂的加入能促进晶粒尺寸缩小,使晶粒尺寸分布更加均匀。Leng 等[63]研究了稀土 La 对 Cu-Ni 合金在 0.1 mol/L NaOH 溶液中钝化膜性能的影响。结果表明 Cu-Ni 合金表面都会形成高缺陷 p 型半导体(即 Cu2O),同时 La 的加入可以提高合金的耐蚀性。主要原因是在 Cu2O 中增加高价态阳离子,将增加钝化膜层 的电阻,导致铜合金的耐蚀性增加。Zhang 等[64]认为在 Cu-Ni 合金中加入适量的 Y 可以细化铸态组织的二 次枝晶间距,通过浸泡实验可知合金的耐蚀性随着 Y 含量的增加先升高后降低,当 Y 含量为 0.021%时,合 金的耐蚀性最好。
3.2 牺牲阳极的阴极保护法
牺牲阳极的阴极保护法是防止管路材料腐蚀的传统方法。朱伟明等[65]参考了国外设计的铁合金牺牲阳 极的方法,根据国标进行了材料的溶解形貌、自腐蚀电位、电流效率和阳极溶解性能的评价,开发了适用于 国内 B10 管材的铁合金牺牲阳极材料。材料的选择原则是(1)电位足够负,但要避免阴极区产生析氢反应;(2)阳极的极化率要小。因此常选择锌-铅-镉合金和铁合金作为牺牲阳极[66]。马启国等[67]采用了恒电流法 测试了纯铁牺牲阳极性能,并通过电偶腐蚀试验进一步分析了纯铁进行阴极保护的可行性。结果表明:纯铁 的自腐蚀电位低于 B10 和 B30 铜镍合金,作为阳极材料很好地抑制了铜合金的腐蚀,有良好的保护作用, 该方法利用了原电池的原理。选择还原性强的金属充当保护剂,其作为负极发生氧化反应而被消耗,B10 合 金作为正极免于腐蚀。
3.3 缓蚀剂
缓蚀剂有着生产简单、见效快等特点,使用缓蚀剂是减缓铜合金腐蚀的另外一种措施,它主要抑制了阳 极或者阴极的腐蚀速率[68]。近年来学者对缓蚀剂在铜镍合金方面的应用做了大量的研究[69-76]。如图 3 所示, 缓蚀剂根据化学组成可以分为有机缓蚀剂和无机缓蚀剂;根据控制电化学腐蚀部位可分为阳极型、阴极型 和混合型缓蚀剂;根据形成的保护膜类型分为氧化膜型、沉淀膜型、吸附膜型缓蚀剂。在不同的腐蚀介质中 应用不同类型的腐蚀剂,在淡水或海水中,因其 pH 呈中性或者弱碱性常使用有机类缓蚀剂。在中性腐蚀介 质中应用最多的为苯并三氮唑(BTA)和它的衍生物类,缓蚀效率达到了 90%以上,但使用成本高、毒性重。王琳等[77]为了研究苯并三唑对碳钢/铜合金电偶腐蚀行为的影响,通过观察电极分布、电流密度分布和电化 学阻抗谱得出了在铜合金和碳钢的电偶腐蚀过程中,BTA 的加入仅仅对铜合金的腐蚀起到了良好的抑制作 用,对碳钢的耐蚀抑制效果不明显;在铜合金表面形成的 Cu-BTA 分子膜更加稳定且缓蚀效果良好。关于缓 蚀剂的耐蚀机理学者提出了不同的理论,其中吸附膜机理最成熟[78]。有机类缓蚀剂含有的极性基团或者含 有不饱和有机物上的 Π 键与 Cu 原子上的空轨道形成配位键,在铜合金表面形成具有疏水性的吸附膜,可以 阻止腐蚀介质与合金的进一步接触,提高了铜合金的耐蚀性。
图 5 缓蚀剂分类
Fig.5 Classification of corrosion inhibitors
3.4 防腐涂料
使用防腐涂料是减缓铜合金腐蚀简单有效的保护方式之一。但是,涂料附着力不够,在海水的浸泡下涂 层容易出现大面积的脱落,因此需要提高涂层与基体的附着力改善涂料的防腐能力。白雪等[79]通过基体树 脂、固化剂等配方试验,筛选出对铜合金表面具有良好耐腐蚀效果的配方,经过各种性能测试,该涂料可以 作为铜合金管路防腐涂料。潘鑫宇等[80]利用聚多巴胺(PDA)辅助共沉积法制备了高性能防腐涂层,并借助 缓蚀剂进一步强化涂层的耐蚀性。Jena 等[81]提出了一种新型的三元复合涂层,由氧化石墨烯-壳聚糖-银组成,该复合涂层具有很强的防腐性和抗菌性能,成本廉价也可工业规模化生产,在海洋环境中具有广阔的应用前景。Gao 等[82]采用激光选区熔化法在 90/10 铜镍合金表面制备了不同 Ti 含量的 Al-Ti-Ni 复合涂层,电化学实验结果显示带有涂层的铜镍合金比裸铜镍合金在 3.5% NaCl 溶液中有更强的耐腐蚀性,当 Ti 含量为 30%时,合金表面形成的钝化膜最致密,稳定性最强。石墨烯具有显著的惰性和不渗透性,石墨烯涂层对镍 和铜具有良好的耐腐蚀性。对含石墨烯涂层的耐腐蚀性的早期研究通常是在氯化物的环境中进行的。Raman 等[83]研究了石墨烯涂层在酸和碱等侵蚀性更大的环境中的耐腐蚀性,结果表明多层石墨烯的稳定性基本不 受腐蚀环境的影响。Vinodhini 等[84]合成反应制得反应性 SiC 纳米颗粒,并通过 FE-SEM(场发射扫描电子 显微镜)、AFM(原子力显微镜)、FTIR(傅里叶红外变换)和 TGA(光谱和热重分析)等技术,对天然 海水中的 Cu-Ni 合金上形成的新型纳米复合涂层进行了研究,结果表明反应性 SiC 纳米颗粒均匀地分散在 材料导报, 2024, 38(18): 23020095 DOI: 10.11896/cldb.23020095 http://www.mater-rep.com 11 / 18 合金表面和涂层界面,阻碍了侵蚀离子的传递从而提高了合金的耐蚀性。现在对于防腐涂料的要求需要环 保无毒,逐渐向高固体分(指固体含量的体积分数在 65%-80%之间)、无溶剂和使用寿命长的方向发展。除此之外,如何提高涂层的附着力和致密性也是现在研究者们关注的焦点[85]。
3.5 超疏水膜技术
超疏水膜技术是指利用水热法、刻蚀法、电化学沉积法等在低表面能的材料表面构建纳米粗糙结构[86- 87]。该薄膜可以在微纳米凹凸中产生一层空气膜,避免腐蚀介质与金属基体直接接触,达到了防腐的目的。熊静文等[88]采用高速电火花切割技术构造出表面粗糙结构,进一步降低材料表面能,在铜基体表面制备超 疏水膜,在 3.5% NaCl 溶液中对试样表面进行极化测试时,带有超疏水膜的试样表现出良好的耐蚀性。Mohamed 等[89]发现通过 Ni 和 Ni-石墨烯复合材料恒电位沉积,用硬脂酸处理后制备的超疏水膜具有微纳米 结构,有较高的化学稳定性和机械耐磨性,带有超疏水膜的铜基材在 0.5 mol/L NaCl 中具有强的耐蚀性。表 1 列举了多种制备超疏水表面的方法并介绍了其优缺点。
表 1 制备超疏水膜表面的方法及特点[86]
免责声明:本网站所转载的文字、图片与视频资料版权归原创作者所有,如果涉及侵权,请第一时间联系本网删除。
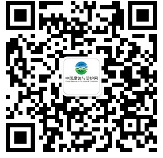
官方微信
《腐蚀与防护网电子期刊》征订启事
- 投稿联系:编辑部
- 电话:010-62316606
- 邮箱:fsfhzy666@163.com
- 腐蚀与防护网官方QQ群:140808414