摘要
综述了Cu-Ni合金海水管系冲刷腐蚀的研究方法、腐蚀机理以及近年来冲刷腐蚀表征的新方法,主要分析了合金成分、微观组织结构、温度、pH值、含砂量、硫化物、流速和冲击角等因素对冲刷腐蚀的影响规律,并对Cu-Ni合金海水冲刷腐蚀的研究趋势进行展望。
关键词: Cu-Ni合金 ; 冲刷腐蚀 ; 实验研究 ; 数值模拟 ; 影响因素
1 前言
我国是一个人口众多,资源相对紧缺的国家,但却拥有丰富的海洋资源。开发海洋资源,发展沿海经济,对我国经济建设和社会发展都具有重大的战略意义。而海洋资源的开发和利用离不开海上基础设施的建设,目前海上基础设施采用的绝大多数材料为金属材料。早期的海水管道系统多用碳钢、铸铁建造,虽然初始投入成本低,但因这些材料的耐海水腐蚀性能差,抗海生物污损能力低,不仅浪费大量的人力物力,缩短工程寿命,而且还常常酿成重大事故[1]。Cu-Ni合金因其耐流动海水腐蚀性能比较好,在船舶与海洋工程海水管路系统中的应用范围逐渐扩大,如海水淡化处理管道、冷凝器管、海电厂的热交换器等。据统计,Cu-Ni合金在商船和军船的用量占船总重比例的2%~3%[2]。
但是Cu-Ni合金在海水环境服役过程中同样会发生腐蚀问题,甚至造成严重的泄事故,如船舶海水管系,以往船舶海水管路选用TUP紫铜管,其腐蚀是常见问题;船用冷凝器管采用B30铜镍合金,在东海海域含砂量很高的海水环境中使用存在严重腐蚀[3,4]。近些年海水管系多采用耐蚀性能更好的B10铜镍合金,能够较好地满足船舶与海洋工程中高盐、高压、高速环境下的使用要求,但仍存在一定的冲刷腐蚀现象。海水管路的频繁腐蚀穿孔,严重影响设备的正常使用,减少了船舶在航率,造成事故隐患[5]。由于材料在海水中的冲刷腐蚀涉及因素错综复杂,如流体的流速[6-9]、含沙量[6-8,10]、沙粒尺寸[7,8]、冲击角[11-14]、pH值[14]、温度[8,9,15]以及材料的组成[10,13]、微观结构[16-18]、热处理方法[19]等,Cu-Ni合金在海水中的腐蚀规律并不完全清楚[3,5],因此掌握Cu-Ni合金的冲刷腐蚀机理,找到有针对性的切实可行的防护措施和方法,对发展海上运输、港口码头和海上石油钻井平台的建设有十分重要的意义。本文综述了近年来国内外海洋腐蚀与防护工作人员在Cu-Ni合金海水冲刷腐蚀方面的研究工作和成果,并对其进行展望。
2 Cu-Ni合金海水冲刷腐蚀研究方法
2.1 实验研究法
实验研究法的共同点是通过将材料置于特定的试验装置中,利用相应的技术手段让介质和试样之间产生一种相对运动[20,21],通过失重和电化学测量等技术手段,研究Cu-Ni合金的冲刷腐蚀过程。目前,开展冲刷腐蚀较常用的试验装置有3类:旋转试验装置、喷射冲刷试验装置和管流试验装置,不同的试验装置各有优缺点和适用范围[22,23]。旋转试验装置因为装置结构简单、价格低廉、所需溶液少、周期短等优点,国内外很多都采用旋转试验装置;但其对电机平稳性和转轴垂直度要求很高,旋转引起的涡流影响大,实验工况和管道实际工况差距较大[22,24]。喷射式试验装置适合于高流速下的冲刷腐蚀研究[25],但不能很好地模拟管道实际工况条件,实验结果往往比实际情况更严重[26]。管流式试验装置能很好模拟实际管道工况条件,可精确控制流速,有良好的流体力学模型,实验结果有很强的实用价值,但由于装置建设费用和操作费用高[27]、占据空间较大等缺点,限制了其使用。
在冲刷腐蚀过程、结果的采集与记录方面常采用失重法和电化学测量法。失重法操作简单、直接、容易实现,在冲刷腐蚀研究中应用最广,但其实验周期较长[28]。电化学测试法包括极化曲线、电化学阻抗和电化学噪声等测量方法。电化学方法不仅可用于定量测定冲刷腐蚀速率的大小,还可以用于深入研究冲刷腐蚀的机理,实验周期短[22],但用于冲刷腐蚀的三电极体系难以构造且测量结果容易受到人为及环境因素的干扰。
冲刷腐蚀样品的形貌、微观组织结构、腐蚀产物的表征方法种类繁多,有表面光度仪、扫描电镜 (SEM)、光学显微镜、透射电镜 (TEM)、X射线光电子能谱 (XPS)、X射线衍射仪 (XRD)、Raman光谱等,不同的表征方法有不同的适用范围。值得注意的是,近年来,声发射技术被逐渐应用于材料的冲刷腐蚀过程的表征,如Burstein和Sasaki[29]通过测量电化学腐蚀电流的瞬变和声发射信号的瞬变关系研究了流体冲击角对304不锈钢的冲刷腐蚀的影响;Frederic等[30]利用声发射技术对碳钢在浓硫酸中冲刷腐蚀的活化钝化转变过程进行了研究,结果表明流体流速超过临界值后,钝化膜破坏,声信号也随之急剧增大;Mohamed等[31]对碳钢弯头的冲刷腐蚀过程进行了声发射技术监测,得到实验条件下冲刷腐蚀的振幅范围和频率;Ukpai等[32,33]利用声发射法研究了X65钢的冲刷腐蚀,发现冲刷腐蚀速率与声发射能量随时间的变化规律比较同步,声发射能量随流速、含沙量的增大而增加。
2.2 数值模拟法
随着计算机技术的快速发展,数值模拟方法在冲刷腐蚀的研究中被越发广泛地应用。数值模拟研究是基于连续相流场计算,通过对流态进行数值仿真模拟计算,从而得出管道中流体速度场、压力场、温度场、固体颗粒和冲刷腐蚀区域的分布,达到预测冲刷腐蚀的方法[28]。与单纯的理论计算相比,数值模拟在研究流体力学问题时可以得到数值解,更能适应研究复杂工程问题的需要。与实验相比,数值模拟不会受到实验条件的种种限制,能够很好地指导实验,更能大幅度节省实验费用和时间,特别是对实验难以完成的某些测量,则可以用计算机进行数值模拟。在管道的冲刷腐蚀研究方面,数值模拟的优点还在于能够清晰地观察到易腐蚀部位的流场情况,方便提取流动参数,如压力、剪切应力和紊流度等,可结合流动情况和参数变化规律深入分析腐蚀原因,同时还能较为直观地给出颗粒相的运动信息,如颗粒对过流部件壁面的碰撞作用等,进而对冲刷腐蚀速率进行计算和预测,这有利于进一步揭示多相流中冲刷腐蚀的规律及机理[28]。
目前,开展冲刷腐蚀数值模拟的主要方式有借助商用计算机流体动力学 (CFD) 软件和自行开发模拟仿真软件两种。Ferng等[34]借助CFD方法计算获得了管线内的流动参数,并将其与实测的局部壁面减薄数据对比,通过两者之间的关系进行研究和拓展,为管壁检测方案的设计提供指导。Davis等[35]利用CFD计算了O在流体中的扩散及向反应面转移的特点,研究了收缩-扩张几何模型内的冲刷腐蚀情况,获得的冲刷腐蚀与实验结果取得较好的一致性。Bozzini等[36]运用CFD软件模拟了两种互不相容液体、气体、固体颗粒等四相流对管道弯头的冲刷腐蚀,分别研究了气相体积分数、流体流速、固相含量等因素对腐蚀的影响。Hu等[37]借助CFD模拟得到弯曲及焊接点部位的流动行为,从而辅助分析了管道失效的原因。北京化工大学团队利用自行编制的程序分别开展了层流、紊流条件下,单相或两相流中,碳钢、不锈钢等材料的流动腐蚀数值研究,探讨了表面剪切力与腐蚀速率的关系,得到的结果与实测值有较好的一致性[38-41]。
在应用数值模拟法开展冲刷腐蚀研究中,也存在一定的问题,主要为边界假设和模型依赖。
边界假设:数值模拟计算模拟的边界条件设定需要基于一定的假设,如颗粒的形状是球形且直径一致、忽略颗粒间的相互作用,因而要求介质中颗粒的含量要低。在颗粒含量较低时,固相对平板的冲击不会影响到主流场;流体中各相是均匀混合的等[28]。而这些假设几乎与实际情况不符,得到的结果也会有偏差。
模型依赖:数值模拟中腐蚀与冲刷的计算均要基于一定的计算模拟,如双相流中腐蚀动力学模型,固体颗粒对金属表面冲刷的模型等。而随着研究体系与研究条件的不同,模型外推能力和适用性有限,因此目前还没有一套通用的模型用于计算。此外,由于协同机制的认识有限且因材料而异,因此目前尚未提出一个考虑了冲刷和腐蚀协同作用的计算模型,也就无法开展协同作用的数值模拟计算[42,43]。
3 Cu-Ni合金海水冲刷腐蚀机理
在冲刷腐蚀过程中,材料的流失有腐蚀和冲刷两种方式,腐蚀是材料以离子形式离开材料表面,而冲刷则是材料表面的腐蚀产物以固体颗粒形式脱离材料表面。冲刷腐蚀是材料受冲刷和腐蚀协同作用的结果,而不是冲刷作用和腐蚀作用两者分别发生时的简单叠加,在大多数的冲刷腐蚀过程中,材料的总失重要大于纯冲刷与纯腐蚀引起的失重之和[44,45]。纯冲刷和纯腐蚀之间的协同作用包括两方面:一是冲刷的发生促进腐蚀反应,二是腐蚀也促进冲刷过程,其作用机制概括为如下两种模式。
(1) 冲刷对腐蚀的影响
冲刷加速了传质过程,促进去极化剂到达材料表面,促进腐蚀产物从材料表面剥落,从而引起加速腐蚀。冲刷过程中,冲刷介质会对材料表面施加一定的切应力。在冲刷的力学作用下,材料表面的钝化膜将减薄或破裂,使得材料基体表面暴露在腐蚀介质中,加速了新的钝化膜的形成,随后这层钝化膜又被冲刷作用所破坏,如此这两个过程交替进行。如果材料形成钝化膜的速率小于冲刷作用导致其剥离的速率,则由于冲刷造成的失重将非常显著。
冲刷会导致材料产生一定程度的塑形变形、位错的聚集和局部能量升高,形成应变电池。特别是当腐蚀介质中含有固体相时,冲刷作用会造成材料表面形成凹凸不平的冲蚀坑,进而增加材料的比表面积,即使腐蚀速率保持不变,也会因暴露面积增加而加剧腐蚀。
(2) 腐蚀对冲刷的影响
腐蚀将粗化材料表面,使材料表面的腐蚀不均匀,尤其是在材料相界面或缺陷处,容易出现局部腐蚀,造成微湍流的形成,进而促进冲刷过程;对于含碳化物作为基体的界面,相界面处由于腐蚀作用而较容易被流动介质冲刷剥落。
腐蚀将弱化材料的晶界、相界,破坏材料的表面结构,使其耐磨的硬化相暴露,或者溶解材料表面的加工硬化层,凸出基体表面,降低材料的力学性能及基体疲劳强度,使其易折断甚至脱落,减小了冲刷时所受的阻力,进而促进冲刷。另外,腐蚀所形成的氧化层附着在材料表面,较易被高流速的流体所冲去,从而使腐蚀速率增大。
目前,对液/固两相流冲刷腐蚀的组成形成了比较一致的观点[46-52]:金属的冲刷腐蚀总失重由纯腐蚀、纯冲刷、腐蚀对冲刷的影响和冲刷对腐蚀的影响4部分组成,即:
式中,T为总失重速率,通过失重测量得到;C为总腐蚀速率,通过电化学阻抗谱或极化曲线计算得到;E为总冲刷速率;C0为纯腐蚀速率,通过测定试片在不含固体颗粒的静止溶液中的失重得到[49,53],也可通过测定试片在不含固体颗粒的流动溶液中的失重得到[54];E0为纯冲刷速率,在试片施加阴极保护条件下,通过测定试片失重获得;Ce为冲刷加速腐蚀的速率;Ec为腐蚀加速冲刷的速率。
Stack等[55,56]对冲刷腐蚀交互作用机理做了进一步研究,根据冲刷磨损与电化学腐蚀在整个冲刷腐蚀中的贡献程度,将冲刷腐蚀机制分为以下4类:(1) C/E<0.1时为冲刷磨损控制;(2) 0.1≤C/E<1.0时为冲刷磨损-电化学混合控制;(3) 1.0≤C/E<10.0时为电化学-冲刷磨损混合控制;(4) C/E≥10.0时为电化学控制。
4 Cu-Ni合金海水冲刷腐蚀影响因素
冲刷腐蚀的协同作用使其过程变得异常复杂,影响因素众多,主要因素有材料自身因素,如材料本身的化学成份、力学性能 (特别是硬度)、组织结构、耐蚀性能、表面粗糙度等;液相因素,如腐蚀介质的温度、溶解氧、pH值、各种活性离子的浓度、粘度、密度、固相和气相在液相中的含量、固相颗粒硬度和粒度等;流体力学因素,如管道弯头部位、流体的流速和流态等均会在材料表面产生不同的力学效果,进而影响材料的冲刷腐蚀。
4.1 材料因素的影响
4.1.1 合金成分 Crousier等[57]研究了不同Ni含量的Cu-Ni合金在NaCl溶液中的电化学行为,发现纯Cu和Cu-Ni合金的极化曲线在阳极极化部分均出现了电流平台,且随Ni含量的增加,电流平台值降低;当Ni含量在10%时,合金的电流平台较宽,表明合金钝态性能稳定;当Ni含量为30%时,电流平台值与纯Ni的钝化电流值相近,结果表明,Ni是导致Cu-Ni合金钝化现象的主要原因。研究人员[58,59]对不同Fe含量的Cu-Ni合金的耐海水腐蚀性能进行测试,结果表明,添加0.5%~2%的Fe可以显著改善Cu-Ni合金的耐流动海水冲刷腐蚀性能。Efird[60]对比研究了不同Ni和Fe含量的Cu-Ni合金在静态和高流速海水的腐蚀实验后发现,未添加Fe的合金形成的腐蚀产物中O含量高;添加一定量Fe的合金所形成的腐蚀产物Ni含量高。B30铜镍合金中添加0.5%~2%Fe能够明显改善材料在流动海水中的耐蚀性,并且在静态海水中也得到证实[24,58,59]。实际上,无论是B30铜镍合金还是B10铜镍合金均添加一定量Fe,添加少量的Fe有益于耐蚀性,其作用存在两种观点:一种观点认为固溶态Fe的作用在于形成含水氧化铁的腐蚀产物膜,这种化合物充当阳极抑制剂[58];另一种观点认为Fe和Ni一样,能够掺杂到缺陷的Cu2O点阵中,增加腐蚀产物膜的阳极和阴极阻力[61]。研究[24]表明,Mn能显著提高Cu-Ni合金抗冲击腐蚀性能,并且当Fe含量比较低时,Mn能起到替代Fe的作用;Mn还能消除Cu-Ni合金中过剩C的影响。另外微合金化可以提高Cu-Ni合金的耐冲蚀性,如添加微量的B[62,63]。
4.1.2 微观组织结构 从相图上看,Cu-Ni合金为无限互溶的连续固溶体。但在322 ℃以下,该合金存在一个产生亚稳分解的成分-温度区域。当添加某些合金元素如Fe、Mn等将改变亚稳分解的成分-温度区域的大小和位置。Fe在Cu-Ni合金中的溶解度很小,通常B30铜镍合金中Fe溶解量为0.5%~1.0%,B10铜镍合金中Fe溶解量为1.0%~1.5%。当Fe完全固溶时,合金表现出良好的耐蚀性;若合金出现沉淀态的Fe,所形成的腐蚀产物无Ni的富集且颜色变暗[64]。Cu-Ni合金在一定条件下沉淀出极小的Ni-Fe富集相,该Ni-Fe富集相不仅明显影响合金的强度,而且降低合金的耐蚀性[24]。在海水中长时间暴露结果表明:B10铜镍合金为均匀固溶体时腐蚀电位在活化方向略有变化,Rp-1值低且稳定,随Fe含量增加而增大;连续沉淀的合金腐蚀电位在活化方向出现一个电位跃迁,在某些情况下,电位跃迁之后观察到强烈的电位波动,Rp-1在含Fe量为2.0%和2.5%时达到最大;在晶界上存在不连续沉淀物的合金腐蚀电位在活化方向出现一个电位跃迁,并且Rp-1值始终较高且与含Fe量无关[24]。在海水中长时间暴露结果还表明,不连续沉淀的B10铜镍合金形成的黑色腐蚀产物膜厚且多孔疏松而易脱落,其下为桔黄色晶体[24]。Cu-Ni合金沉淀相析出的条件尚未清楚,目前还未找到有效地抑制Cu-Ni合金沉淀特别是不连续沉淀发生的途径。
4.2 液相因素的影响
4.2.1 温度 温度对Cu-Ni合金的影响主要表现在腐蚀反应的动力学参数、氧的扩散系数及溶解量等方面。其中腐蚀反应的动力学参数和氧的扩散系数随着温度的上升而逐渐增高,但是温度升高时,氧会逐渐析出,使氧的溶解量降低;而且Cu-Ni合金的表面膜特性及再钝化能力也会随着温度的变化而发生转变[26]。温度对Cu-Ni合金腐蚀行为影响的研究结果各异,即温度升高,Cu-Ni合金腐蚀速率减小、增加或保持不变。这些差异是由于实验条件不同造成的,包括水流、pH值变化、溶解氧等。Gat等[65]将材料按其冲刷腐蚀性能随着温度升高的变化趋势分为二类:第一类材料耐冲刷腐蚀性能随温度升高而降低;第二类材料耐冲刷腐蚀性能则随温度升高而增强。并认为冲刷腐蚀过程并不是由单一机制完成,而是几种机制共同完成的,但会有其中一种机制在冲刷腐蚀过程中占主导作用:因此,随着温度的升高,材料的冲刷腐蚀速率是增大还是减小取决于占主导作用的机制,而且主导机制也会随温度变化而发生变化。
4.2.2 pH值 国内外开展了众多pH值对Cu-Ni合金耐蚀性影响的研究,Pehkonen等[66]详细研究了溶液的pH值对白铜耐腐蚀性能的影响;Efird[67]对90-10和70-30 Cu-Ni合金在海水中的电位-pH值进行了研究,显示在特定的电位下,溶液pH值不同时合金的腐蚀规律可能不同;迟长云等[68]研究了pH值变化对B30铜镍合金腐蚀规律的影响;陈海燕等[69]研究了pH值变化对BFe30-1-1合金在NaCl溶液中的腐蚀规律。罗宗强等[70]研究了pH值对Cu-17Ni-3Al-X耐磨铸造铜合金腐蚀的影响,其研究结果表明在3.5%NaCl溶液中,随着溶液pH 值的升高,合金腐蚀速率逐渐降低;在中性和碱性溶液中,合金具有优异的耐蚀性;当溶液为强酸性 (pH值为3) 时,合金表面不易形成致密的保护膜;当溶液pH值为6,8和10时,合金表面产生Al、富Ni的Cu2O和Cu2(OH)3Cl腐蚀产物膜;当溶液为强碱性 (pH值为12) 时,合金容易形成致密的Cu2O膜。在不同pH值溶液中合金的腐蚀速率差异,主要是因为铜合金表面腐蚀膜的不同及铜合金电化学反应过程中阴极反应引起的;铜合金在酸性溶液中,于第二相附近出现晶间腐蚀[2]。
4.2.3 含砂量 海水含砂量对Cu-Ni合金冲刷腐蚀的影响主要表现在对切应力的影响,砂粒的硬度、粒径大小、锋利性以及浓度的变化均能改变海水对Cu-Ni合金表面的剪切应力的大小[26]。一般认为,砂粒硬度越大,对Cu-Ni合金表面的切应力也越大,Cu-Ni合金的腐蚀速率也越大。多角粒子的锋利度要比圆形粒子的大得多,因此,砂粒的菱角越多,海水对Cu-Ni合金表面的切应力也越大,Cu-Ni合金的腐蚀速率也越大。研究[71-73]表明,随着砂粒浓度增大,砂粒与Cu-Ni合金表面接触的频率和次数也逐渐增大,使Cu-Ni合金腐蚀速率也增大;但砂粒浓度进一步增大,在高浓度条件下,因砂粒之间的相互影响作用而产生了屏蔽效应,使对材料表面的切应力降低,反而使材料腐蚀速率降低。同时,由于砂粒的存在,使Cu-Ni合金表面附近的扩散层加剧了搅动,促进了海水中的离子与Cu-Ni合金表面的接触更加频繁,从而促进了腐蚀反应,使Cu-Ni合金腐蚀速率加大。
然而在含砂量较高,砂粒度较大的冷却水中,当流速较高时,由电化学腐蚀与砂的磨损引起材料流失的比例关系,仍存在争议。通常认为含砂量增加或砂粒度增大,腐蚀速率随之增大。
4.2.4 硫化物 硫化物进入海水中途径较多,如腐烂的动植物、工业废弃物、自然产生硫酸盐细菌还原等。硫化物加速Cu-Ni合金腐蚀的现象在自然海水和人工海水中都得到证实[74]。硫化物在海水中存在形式的多样性使硫化物对Cu-Ni合金腐蚀影响的研究复杂化。在无氧的情况下,海水中的硫化物使Cu-Ni合金腐蚀电位向活化方向迁移[75]。在活化电位时,阴极反应依赖于氢离子还原,因此,即使在无氧时,腐蚀反应仍能进行。Macdonald等[75]研究表明,在硫化物含量高达55 mg/L、流速为5 m/s的海水中合金的腐蚀速率并不很高。此结果无法解释舰船中Cu-Ni合金的早期失效行为。因此,Cu-Ni合金腐蚀加速的原因可能是由于其与硫化物的氧化物接触,而并不是简单的由硫化物单独作用产生的。硫化物及其氧化产物导致形成多孔的非保护性的Cu2S膜,它阻碍保护性的氧化膜的正常生长,从而使腐蚀加速[24]。
4.3 流体力学因素的影响
4.3.1 流速 Cu-Ni合金是一类耐冲刷腐蚀性能较为优良的海洋用工程材料,但一般认为其在海水中使用存在一个临界流速值,超过临界流速值,材料冲刷腐蚀率明显增大而快速失效。Cu-Ni合金相对临界流速值受诸多因素影响,难以精确测定[24,76]。
目前,学术界对冲刷腐蚀临界流速问题产生的机制存在一定的分歧,Efird[77]认为流动的海水在合金表面产生剪切应力,随流速的增加,剪切应力增加。剪切力超过一定值使得合金表面腐蚀产物膜机械分离。因此,腐蚀产物的力学性能决定了临界流速值,即临界流动速度对应的剪切应力略超过腐蚀产物膜与基体的结合力。Efird计算出了B10铜镍合金的临界剪切应力为43.1 Nm-2。Tuthill[78]测试了Cu-Ni合金在海水环境下不同管径下的临界剪切力值,发现管径越大,铜合金允许海水的流速越高。Bianchi等[79]认为高速流动的海水传质系数大,使得表面的pH值降低以及表面膜通过可溶性的Cu的化合物扩散使溶解度增加;在侵蚀腔内,局部腐蚀形成活化-钝化电池,这种电池具有自催化效应。Perkins等[80]认为在流动海水中,如果其中气泡的尺寸大于界面层的厚度,则气泡对保护层产生机械破坏作用。所产生的力可能破坏水力学上的界面层。再加上局部液体的直接冲击和保护层破坏等因素,使腐蚀不断发展。Syrett和Wing[81]认为Cu-Ni合金在流动的海水中存在一个临界的破裂电位Eb。即在极化曲线上阳极电流突然上升的电位。当开路电位Ec>Eb时发生局部腐蚀,腐蚀速率很高;反之,发生均匀腐蚀且腐蚀速率很低。此外,还测得了不同流速以及不同暴露时间下B10铜镍合金的自腐蚀电位和破裂电位,并且加以比较,结果表明:流速越高、暴露时间越长就越易发生局部腐蚀[24]。
4.3.2 冲击角 含沙流体中,流体冲刷作用对冲刷磨损影响较大[82]。流体冲刷角对冲刷腐蚀的影响主要表现为剪切应力和正应力。剪切应力通过削薄甚至移除钢表面的氧化膜而增强冲刷腐蚀过程。正应力则是通过撞击或损伤电极表面而产生孔洞。冲刷角小于45°时,剪切应力占主导地位;大于45°时,正应力占主导地位[83,84]。
Tang等[83]认为,冲刷角从30°增至45°时,腐蚀速率随冲刷角增大而增大,45°增至90°的过程中,冲刷腐蚀速率先随冲刷角增大而降低,然后随其增大而增大。研究[84,85]表明,冲刷角较小 (50°) 时,易产生较粗糙的电极表面,与光滑的金属表面相比,表面点蚀坑更深且直径更小,因此粗糙表面更容易产生可以发展到正常生长阶段的点蚀坑,从而降低点蚀电势;冲刷角较大 (90°) 时,更容易发生点蚀。
尹承军[26]研究了冲击角度对B10合金冲刷腐蚀行为的影响,结果表明在洁净海水冲刷腐蚀过程中,海水的流动性促进了腐蚀产物膜的形成与溶解过程;也增强了海水对材料表面的冲刷作用,使得表面腐蚀产物膜的形成与破坏为一动态过程。而在含砂条件下,砂粒的存在增强了海水对材料表面的冲刷作用,使材料表面产生冲击坑。且随着冲击角度的增大,冲击坑的形状逐渐由马蹄状转变为点状,稳定致密的膜层只能对B10合金在洁净海水冲刷过程中起保护作用。
5 展望
(1) 实际工况中,Cu-Ni合金管的冲刷腐蚀破坏容易发生在弯管处,且破坏形式更复杂,今后应更多致力于弯管等特殊管道部位的冲刷腐蚀的研究,深入研究冲刷腐蚀体系各参数的影响规律,定量研究金属管道的冲刷腐蚀。
(2) 创新发展实验研究方法,设计更符合现场管道实际工况的管流式试验装置,将声发射技术及原位观测技术等引入Cu-Ni合金实验研究中,实现对冲刷腐蚀过程的在线测量和动态观测,有助于揭示冲刷腐蚀机理。
(3) 目前在Cu-Ni合金的冲刷腐蚀研究中关于流速、攻角、固相颗粒、流体流态等因素研究较多,但如温度、压力、溶解氧等环境因素影响机理的研究开展较少,针对工业化发展的新要求,对于高速、高温、高盐、高压等极端严酷条件下Cu-Ni合金冲刷腐蚀的研究显得尤为匮乏。今后,对Cu-Ni合金冲刷腐蚀的研究将更加贴近实际工况,高速、高温、高盐、高压等极端严酷环境条件下Cu-Ni合金的冲刷腐蚀将成为研究重点。
The authors have declared that no competing interests eixt
免责声明:本网站所转载的文字、图片与视频资料版权归原创作者所有,如果涉及侵权,请第一时间联系本网删除。
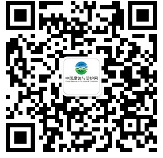
官方微信
《腐蚀与防护网电子期刊》征订启事
- 投稿联系:编辑部
- 电话:010-62316606-806
- 邮箱:fsfhzy666@163.com
- 腐蚀与防护网官方QQ群:140808414