摘要: 采用盐溶液刻蚀和水浴处理的方法,结合氟硅烷的表面修饰,在5083 铝合金基体上制备出了超双疏表面。采用场发射扫描电子显微镜(FE-SEM)、X 射线衍射(XRD)、X 射线光电子能谱(XPS)、接触角测量和电化学测试等方法研究了超双疏铝合金表面的微观形貌、化学成分、疏水疏油性和耐蚀性。结果表明,水和乙二醇在该表面上的接触角分别为 158°和154.3°,展现出良好的超双疏性能;与基体相比,超双疏试样的腐蚀电位明显正移,腐蚀电流密度由4.016×10-6 A·cm-2 下降至1.531×10-7 A·cm-2;在3.5% NaCl溶液中浸泡5d 后,超双疏试样的电荷转移电阻仍明显高于基体,提高了5083 铝合金基体的耐蚀性。
关键词: 铝合金、刻蚀、超双疏表面、耐蚀性
铝合金以其优异的物理、化学和力学性能广泛应用于板壳构件、焊接构件、船舶设备等[1]。然而,铝合金表面含有Mg、Zn 等其他金属元素,化学活性更强,尤其是在富含活性Cl-和溶解氧的海洋环境中更易遭受腐蚀,这一腐蚀敏感性严重限制了其使用寿命和应用领域,因此,开展铝合金在海洋环境中的腐蚀防护研究具有重要的经济和现实意义。
在工业上,涂层技术[2]、机械合金化[3]和阳极氧化[4]等多种工艺被应用于提高金属在海水中的耐蚀性。然而,喷涂的涂层与金属基底的结合力差,且含有重金属离子的涂层会污染环境;阳极氧化方法制备过程中经常使用盐酸、硫酸、草酸等对操作者具有一定的安全隐患。尽管这些方法有其优点,但都有一定的局限性。与这些传统方法相比,超双疏表面因其具有特殊的表面润湿性,可以通过降低界面间的相互作用[5]而受到广泛关注,特别是在耐腐蚀[6-8]、防冰[9]、防污[10]和油水分离[10-12]等领域。因此,可以通过采用制备超双疏表面的方法来提高铝合金的耐蚀性。目前已经提出了多种超疏水/超疏油表面的制备方法[13-17]用于铝基材料在海洋环境中的腐蚀防护,例如,Tuo 等[18]采用激光蚀刻和喷涂PTFE/FS-61 涂层的方法,在铝基板上制备了具有分层微纳米粗糙结构的超双疏表面,该表面对于表面张力大于30 mN/m 的液体(如水、乙二醇等),CAs 高于159°,SAs 低于6°,具有一定的耐蚀性和减阻效果。Zhang 等[19]提出了一种在六水硝酸铈和六烷酸组成的电解液中,通过一步电沉积制备具有微/纳米级乳头状结构的超疏水铝的方法,研究了所制备表面的防腐性能。电化学结果表明,与铝基体相比,超疏水试样的腐蚀电流密度降低了两个数量级以上,在3.5 wt.% NaCl溶液中浸泡72 h 后,水的接触角从最初的167.4°下降为162°,表现出良好的耐蚀性和稳定性。以铝合金为基体,采用制备超双疏表面的方法研究其耐蚀性的报道相对较少,因此,本文采用化学刻蚀法制备5083 铝合金超双疏表面并研究其耐腐蚀性能。
1 实验方法
商业用 5083 铝合金片(20 mm×10 mm×2 mm),质量分数为94.9%Al 和3.2 %Mg,产自上海一谦贸易有限公司;全氟癸基三乙氧基硅烷(质量分数96%)产自上海麦克林生化科技有限公司;五水合硫酸铜,氯化钠,丙酮,乙二醇,和无水乙醇,均为分析纯级试剂,购自国药集团化学试剂有限公司。
采用简单方便的化学刻蚀法来制备超双疏铝合金表面,制备工艺如图1 所示。将20mm×10 mm×2 mm 的5083 铝合金试样依次用800 #,1200 #,2000 #砂纸进行打磨和抛光,分别用丙酮,无水乙醇和去离子水超声清洗10 min 去除表面的油污和杂质,并用N2 吹干。将预处理后的铝合金片置于0.7 mol/L CuSO4 和1 mol/L NaCl 的混合盐溶液中刻蚀2 min,然后置于去离子水中超声清洗10 min 去除试样表面的杂质。用N2 吹干后将试样置于200 ml96℃去离子水中进行恒温水浴处理4 min。用乙醇清洗后,将试样置于50 mL,1%(体积分数)全氟癸基三乙氧基硅烷的乙醇溶液中修饰40 min,取出后在100 ℃真空干燥箱中干燥30min。
图1 超双疏表面的制备流程
在室温下,用接触角测量仪(JC2000C1)测量不同液体在不同试样表面的接触角(CAs),每滴测试液的体积约为4 μL,在试样表面选取五个不同的位置进行接触角测量,取测试结果的平均值作为试样表面接触角的最终测量值,采用量角法对接触角的数据进行分析。采用场发射型扫描电子显微镜(FE-SEM,JSM-6701F)对铝合金试样表面的微观形貌进行表征。通过X 射线衍射仪 (XRD,D8 ADVANCE)和X 射线光电子能谱(XPS,Thermo ScientificK-Alpha)表征试样的物相组成和表面化学成分。利用CHI600E 型电化学工作站测定基体和超双疏试样的动电位极化曲线以及电化学阻抗谱,采用三电极体系,将测试样品制成暴露面积为1 cm2 的工作电极,铂片 (1 cm×2 cm) 作为对电极,Ag/AgCl 电极作为参比电极。测试温度为室温,电解质溶液为3.5%(质量分数) NaCl 溶液。动电位极化曲线测试的扫描范围相对开路电位-0.5~0.5 V,扫描速率为1 mV/s。在开路电位 (OCP) 下进行电化学阻抗测试,扫描频率为105~1 Hz,正弦扰动幅值为±10 mV,使用 ZSimDemo 软件对 EIS 数据进行拟合分析。
2 结果与讨论
2.1 表面形貌及润湿性分析
图2 是不同处理条件下试样表面的微观形貌。由图2a 可以看出,未经处理的基体表面相对平整,没有出现特征结构。经过CuSO4 和NaCl 混合盐溶液刻蚀2 min 后,试样表面不再光滑,而是呈现出直径和深度约为1~2 μm 的微米级阶梯状结构(图2b 所示),这些微米结构使铝合金表面产生大量的空隙,增大了铝合金表面的粗糙度,有利于包裹空气层,改变试样表面的润湿性。由图2c 观察到,试样表面经过水浴处理4 min 后,表面形貌发生变化,原有阶梯状表面生长出了绒片状物质。高倍率下的图像(图2d)显示,在微米级结构上生长出几十纳米厚的片状结构且紧密排布,形成了特殊的微纳米级复合结构,这种结构对提高试样表面的疏油性起着至关重要的作用,有利于形成最终的超双疏表面[10, 20]。图3 为水和乙二醇在基体和超双疏试样表面的光学图像,从图可知,水和乙二醇在该表面上的静态接触角分别为158°和154.3°,基体的润湿性发生了明显改变,由在基体上的亲水亲油态转变为超疏水超疏油态,所制备的铝合金表面呈现出超双疏特性。
图2 不同处理方法下试样的表面形貌
图3 水滴和乙二醇在基体和超双疏表面的光学图像
2.2 表面物相及成分分析
图4 是基体经过不同处理方式后试样表面的 XRD 图谱。经过盐刻蚀和修饰后的基体表面仅出现了Al 的特征衍射峰,结果表明,盐溶液刻蚀过程仅改变了基体的表面形貌;在刻蚀过程后进行水浴处理制备的超双疏表面也仅检测到了Al 的衍射峰,其中2θ=38.4°,44.7°,65.3°,78.2°的衍射峰分别对应Al(111),(200),(220)和(311)晶面[JCPDS #89-2837]。结合SEM 图像,水浴过程不仅改变了试样的表面形貌,在原有结构上生成了紧密排列的纳米片状物质,并且Al 与水在特定的温度范围内发生反应生成AlO(OH),即勃姆石或假勃姆石[21]。但从XRD 图谱来看,并没有检测到AlO(OH)的特征衍射峰。
图4 不同处理方式后试样表面的 XRD 图谱
利用XPS 进一步对试样表面的化学成分进行表征分析。图5 是试样在经过氟硅烷修饰前的XPS 图谱。从图5a 全谱中可以发现,谱图中出现的两个信号峰,分别是O1s 和Al2p。从O1s 窄谱(图5b)可以看到,在530.4 和531.9 V 出现了两个峰值,分别对应Al-O 和Al-OH,结果表明,试样表面可能生成了勃姆石或者假勃姆石。二者虽然有着相同的晶体结构,但假勃姆石具有更低的结晶度、更大的晶体尺寸和更高的羟基比例[22]。而勃姆石中预期的氧(Al-O-Al)和羟基(Al-O-H)的比例应该接近1:1。但是从图5b 结果来看,氧(Al-O-Al)和羟基(Al-O-H)的比例小于1:1,晶体中少量的氧原子被羟基或者水分子取代,因此样品表面可能生成了假勃姆石。Al2p 的分谱中只出现了一个74.4 V 的峰值,对应AlO(OH)[22],与O1s 分谱结果相一致,证明了假勃姆石的存在。
图5 氟硅烷修饰前试样的XPS 谱图
图6 为铝合金试样经过盐溶液刻蚀,水浴处理以及氟硅烷修饰后的XPS 图谱。图6a 可以观察到,样品表面含有F、O、C、Si、Al。从图6b 可以观察到C-F3(293.7 eV),C-F2(291.4eV),C-C(284.9 eV)[23], C-O(286.2 eV),CH2-CF2(288.74 eV)和C-Si(281.6 eV)[24]6 种成分。图6d Si2p 窄谱结果表明,在结合能为102.4、100.9 和103.2 V 出现的能级峰分别对应Si-O键、Si-C 键[25]和Si-OH 键[24]。XPS 图谱结果表明,氟硅烷分子成功修饰到样品表面。
图6 氟硅烷修饰后试样的XPS 图谱
2.3 耐蚀性分析
通过电化学测试,测定试样的极化曲线是探究试样腐蚀行为和机理的有效手段。图7为铝合金基体和超双疏试样在3.5 % NaCl 溶液中的动电位极化曲线,采用Tafel 外推法得到的电化学拟合参数如表1 所示。通常,更低的腐蚀电流密度(Icorr)和更高的腐蚀电位(Ecorr),表明材料的耐腐蚀性更强[26]。由图7 可知,基体在腐蚀介质中的极化曲线出现了一个钝化区,是由于铝合金表面容易自然形成钝化膜,随着电极电位的正移,氧化膜溶解,暴露出来的铝合金基体发生电极反应Al→Al3++3e-,使电流密度急剧增大。而超双疏试样的极化曲线出现的钝化区与表面的双疏膜层有关。表1 结果表明,基体和超双疏试样的 Icorr 分别为4.016×10-6 和1.531×10-7 A·cm-2,相对于基体,超双疏试样的Icorr 降低了一个数量级,腐蚀电位由原始的-0.8829 V 正移至-0.4665 V,腐蚀速率降低。根据缓蚀效率(IE)的计算公式(1)
IE=(1-Icorr2/Icorr1)×100% (1)
其中,Icorr1 和Icorr2 分别为基体和超双疏试样的腐蚀电流密度,经计算得到超双疏试样的缓蚀效率达96.29%,由于超双疏表面特殊的微纳米结构可以包裹空气形成空气层,减少了腐蚀性介质与基体的接触,因而有效地减弱了界面间的相互作用,降低了基体的腐蚀速率,提高了基体表面的耐蚀性。
图7 基体和超双疏试样的动电位极化曲线
表1 动电位极化曲线拟合参数
为了进一步研究超双疏试样在模拟海水环境下的耐蚀性和防护能力,将超双疏试样放入3.5% NaCl 溶液中浸泡不同时间,对其进行定期的电化学阻抗谱测试。图8 为基体和不同浸泡时间下超双疏试样的Nyquist 图。以SA(0 d)为例,SA 为超双疏试样,(0 d)代表试样在3.5% NaCl 溶液中浸泡0 d。图8 的Nyquist 图谱显示,基体在高频区出现一个代表铝合金基体与溶液之间双电层行为的容抗弧,对应于5083 铝合金基体的溶解过程,并且由于基体表面自然形成了一层薄的氧化膜,所以出现了一段不太明显的扩散尾,阻挡溶解氧的扩散。超双疏试样(0 d)在高频区出现的容抗弧与试样表面的双疏膜层有关。并且基体的容抗弧远小于超双疏试样(0 d)。容抗弧越大,象征着试样表面与腐蚀介质界面的电子转移过程越困难,即电荷转移电阻越大,试样的耐蚀性越好[27]。上述结果表明,试样表面双疏膜层的存在提高了基体的耐蚀性。
图8 基体和不同浸泡时间下超双疏试样的Nyquist 图
通过对电化学阻抗谱进行拟合得到了基体和超双疏试样(0 d)在3.5%NaCl 溶液中的两个有效电路,如图9 所示。图中Rs 为溶液电阻,Rct 和Cdl 分别为试样/NaCl 溶液界面形成的电荷转移电阻和双电层电容,CPEf 和Rf 分别代表膜层电容的常相位角元件和膜层电阻,W 为扩散电阻,Rp 为极化电阻,具体拟合参数见表2。表2 结果表明,超双疏试样(0 d)的电荷转移电阻Rct 比基体增大了一个数量级,且该试样保护膜层的电阻较大,电容较小,具有良好的耐蚀性,对基体起到良好的保护作用,EIS 图谱所得到结果与极化曲线得到的结果具有一致性。
图9 基体和超双疏试样的等效电路图
表2 基体和不同浸泡时间下超双疏试样的电路拟合参数
由图8 Nyquist 图可以观察到,在浸泡期间,超双疏试样的容抗弧呈现出先减小后增大再减小的变化趋势,结合表2 的具体参数,这一变化趋势与Rp 的变化趋势相一致。以上结果表明,在浸泡前期(1~2 d),由于水分子的渗入量逐渐增加,超双疏表面微观结构中包裹的空气被挤出[28],超双疏膜层遭到破坏,溶液中的水和CI-透过双疏膜的微孔渗入到基体并与基体发生反应,开始生成氧化物,使得超双疏试样的容抗弧减小,Rct 和膜层电阻Rf 明显减小,耐蚀性降低。与浸泡2 d 相比,当浸泡时长为3 d 时,试样的Rf 减小,而Rct 显著增大,这表明双疏膜层的防护性能下降,生成的氧化物和双疏膜层共同起保护作用;当浸泡时长为4 d 时,试样的Rf 明显减小,Rp 略有增大,表面的双疏膜层基本失效,产生的腐蚀产物堵塞空隙,阻碍了腐蚀性介质的进一步渗透,起到了主要的保护作用,使Rct 增大,试样的耐蚀性有所提高;到浸泡后期(5~6 d),由于表面生成的氧化物膜发生脱落和溶解而变得疏松,使Rp 减小,试样的腐蚀防护性能随着浸泡时间的延长明显降低。相比于基体,试样在腐蚀性介质中浸泡5 d 仍具有较高的阻抗值。浸泡测试结果表明:超双疏试样在3.5% NaCl溶液中浸泡5 d 后,仍有一定的腐蚀防护性能。
3 结论
(1) 采用CuSO4 和NaCl 混合盐溶液刻蚀、高温水浴处理以及氟硅烷修饰的方法,在5083 铝合金基体上成功制备出超双疏表面。最佳工艺条件为:混合盐溶液刻蚀2 min,96 ℃高温水浴处理4 min,全氟癸基三乙氧基硅烷修饰40 min。
(2) 试样经过盐溶液刻蚀后,表面呈现出单一微米级的阶梯状结构;高温水浴处理后,试样的表面形貌发生变化,在微米级阶梯状结构上生长出纳米片状物质,形成了微纳米的复合结构,进一步增加了表面粗糙度;试样经氟硅烷修饰后,表面呈现出超双疏性。
(3) 试样经过高温水浴处理后生长出的纳米片状物质为AlO(OH),所形成的特殊微纳米复合结构是实现超双疏的关键,这种结构有利于包裹更多的空气,提高基体的耐蚀性。
(4) 与基体相比,超双疏试样在3.5%NaCl 溶液中的Icorr 由4.016×10-6 A·cm-2 降低至1.531×10-7 A·cm-2,腐蚀速率降低,电荷转移电阻Rct 增大了一个数量级,表现出良好的耐蚀性,且该试样在3.5%NaCl 溶液中浸泡5d 后仍具有一定的腐蚀防护性。
参考文献:
[1] Liu H, Huang J Y, Li F Y, et al. Multifunctional superamphiphobic fabrics with asymmetric wettability for one-way fluid transport andtemplated patterning [J]. Cellulose, 2017, 24(2): 1129
[2] Xiang T F, Chen D P, Lv Z, et al. Robust superhydrophobic coating with superior corrosion resistance [J]. J. Alloys Compd, 2019, 798:320
[3] Gandel D S, Easton M A, Gibson M A, et al. The influence of zirconium additions on the corrosion of magnesium [J]. Corros. Sci.,2014, 81: 27
[4] Zhang B, Xu W, Zhu Q, et al. Mechanically robust superhydrophobic porous anodized AA5083 for marine corrosion protection [J].Corros. Sci., 2019, 158: 108083
[5] George J E, Rodrigues V R M, Mathur D, et al. Self-cleaning superhydrophobic surfaces with underwater superaerophobicity [J].Mater. Des., 2016, 100: 8
[6] Huang P, Gao R J, Liu W B, et al. Fabrication of Superamphiphobic Surface for Nickel-plate on Pipeline Steel by Salt SolutionEtching and Its Anti-corrosion Properties [J]. Chin. Soc. Corros. Prot., 2021, 41(1): 96(黄鹏, 高荣杰, 刘文斌等. 盐溶液刻蚀-氟化处理制备X65 管线钢镀镍超双疏表面及其耐蚀性研究[J]. 中国腐蚀与防护学报,2021, 41(1): 96)
[7] Guo C L, Ding H, Xie M X, et al. Multifunctional superamphiphobic fluorinated silica with a core-shell structure for anti-fouling andanti-corrosion applications [J]. Colloids Surf., A., 2021, 615: 126155
[8] Wei J F, Li B C, Jing L Y, et al. Efficient protection of Mg alloy enabled by combination of a conventional anti-corrosion coating and asuperamphiphobic coating [J].Chem. Eng. J., 2020, 390: 124562
[9] Xu Z Y, Qi H B, Cheng Y Y, et al. Nanocoating: Anti-icing superamphiphobic surface on 1060 aluminum alloy mesh [J]. Appl. Surf.Sci., 2019, 498: 143827
[10] Ghaffari S, Aliofkhazraei M, Barati Darband G, et al. Review of superoleophobic surfaces: Evaluation, fabrication methods, andindustrial applications [J]. Surf. Interfaces, 2019, 17: 100340
[11] Teisala H, Butt H J, Hierarchical Structures for Superhydrophobic and Superoleophobic Surfaces [J]. Langmuir, 2019, 35(33): 10689
[12] Lian Z X, Xu J K, Yu P, et al. Oil-Repellent and Corrosion Resistance Properties of Superhydrophobic and SuperoleophobicAluminum Alloy Surfaces Based on Nanosecond Laser-Textured Treatment [J]. Met. Mater. Int., 2019, 26(11): 1603
[13] Zhang D J, Wu G Q, Li H, et al. Superamphiphobic surfaces with robust self-cleaning, abrasion resistance and anti-corrosion [J].Chem. Eng. J., 2021, 406: 126753
[14] Chao J Q, Feng J K, Chen F Z, et al. Fabrication of superamphiphobic surfaces with controllable oil adhesion in air [J]. ColloidsSurf., A, 2021, 610: 125708
[15] Zhang B B, Zeng Y X, Wang J, et al. Superamphiphobic aluminum alloy with low sliding angles and acid-alkali liquids repellency [J].Mater. Des., 2020, 188: 108479
[16] Lv Z X, Yu S R, Song K X, et al. A two-step method fabricating a hierarchical leaf-like superamphiphobic PTFE/CuO coating on6061Al [J]. Prog. Org. Coat., 2020, 147: 105723
[17] Zhong Y X, Hu J, Zhang Y F, et al. The one-step electroposition of superhydrophobic surface on AZ31 magnesium alloy and itstime-dependence corrosion resistance in NaCl solution [J]. Appl. Surf. Sci., 2018, 427: 1193
[18] Tuo Y J, Zhang H F, Chen L, et al. Fabrication of superamphiphobic surface with hierarchical structures on metal substrate [J].Colloids Surf., A, 2021, 612: 125983
[19] Zhang B B, Xia Z, Li Y T, et al. Fabrication of durable anticorrosion superhydrophobic surfaces on aluminum substrates via a facileone-step electrodeposition approach [J]. Rsc. Adv., 2016, 6(42): 35455
[20] Song J L, Huang S, Hu K, et al. Fabrication of superoleophobic surfaces on Al substrates [J]. J. Mater. Chem. A, 2013, 1(46): 14783
[21] Geiculescu A C, Strange T F, A microstructural investigation of low-temperature crystalline alumina films grown on aluminum [J].Thin Solid Films, 2003, 426(1-2): 160
[22] Kloprogge J T, Duong L V, Wood B J, XPS study of the major minerals in bauxite: Gibbsite, bayerite and (pseudo-) boehmite [J]. J.Colloid Interface Sci., 2006, 296(2): 572
[23] Saleema N, Farzaneh M, Paynter R W, et al. Prevention of Ice Accretion on Aluminum Surfaces by Enhancing Their HydrophobicProperties [J]. Adhes. Sci. Technol., 2012, 25(1-3): 27
[24] Deng R, Hu Y M, Wang L, et al. An easy and environmentally-friendly approach to superamphiphobicity of aluminum surfaces [J].Appl. Surf. Sci., 2017, 402: 301
[25] Laoharojanaphand P, Lin T J, Stoffer J O, Glow discharge polymerization of reactive functional silanes on poly(methyl methacrylate)[J]. J. Appl. Polym. Sci., 1990, 40(3-4): 369
[26] Hu J M, Liu L, Zhang J Q, et al. Electrodeposition of silane films on aluminum alloys for corrosion protection [J]. Prog. Org. Coat.,2007, 58(4): 265
[27] Li X W, Zhang Q X, Guo Z, et al. Low-cost and large-scale fabrication of a superhydrophobic 5052 aluminum alloy surface withenhanced corrosion resistance [J]. Rsc. Adv., 2015, 5(38): 29639
[28] Ren J D, Gao R J, Zhang Y, et al. Fabrication of amphiphobic surface of pipeline steel by acid etching and its anti-corrosionproperties [J]. J. Chin. Soc. Corros. Prot., 2017, 37: 233(任继栋, 高荣杰, 张宇等. 混酸刻蚀-氟化处理制备X80 管线钢双疏表面及其耐蚀性研究 [J]. 中国腐蚀与防护学报, 2017,37: 233)
免责声明:本网站所转载的文字、图片与视频资料版权归原创作者所有,如果涉及侵权,请第一时间联系本网删除。
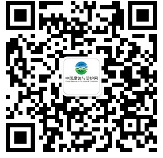
官方微信
《腐蚀与防护网电子期刊》征订启事
- 投稿联系:编辑部
- 电话:010-62316606-806
- 邮箱:fsfhzy666@163.com
- 腐蚀与防护网官方QQ群:140808414