铝合金结构外型美观、耐腐蚀性强,具有广泛的应用前景。然而,关于铝合金结构在高腐蚀性环境下的行为尚无系统研究,限制了其在复杂恶劣环境下的应用。
随着材料科学和结构工程的不断发展,铝合金逐渐成为一种常用的建筑材料,已较广泛地应用在空间网格结构、人行天桥、门式刚架中。铝合金材料的自重约为钢材的三分之一,强度和低碳钢相近,具有良好的耐腐蚀性能,是一种性能良好的绿色建筑材料。
金属结构在使用过程中,受到服役环境的影响,会出现各种各样的损伤,其中腐蚀是较为常见的一种损伤形式。金属腐蚀现象普遍存在于国民经济建设的各个领域,危害极其严重,会造成重大的经济损失,甚至导致安全事故。
众所周知,铝是一种非常活泼的金属,其表面能自然形成一层致密的氧化膜,这使得铝材料在普通大气环境下表现出优良的耐腐蚀性;并且还可以在工厂对成型构件进行表面处理,进一步提高其耐腐蚀性。因此,作为一种在腐蚀性环境中性价比较高的选择,铝合金结构具有较好的耐久性,能显著降低结构服役期间的维护费用。
近年来,随着铝合金建筑结构的不断发展和应用,针对铝合金结构在极端恶劣大气环境中的耐久性研究需求日益凸显。
铝合金大气腐蚀特点
铝合金具有优良的耐腐蚀性能,但并不意味着完全不会出现腐蚀现象。飞机常用铝合金材料制造,充分利用了铝合金轻质高强的特点,然而在高盐高湿环境介质的作用下却又具有相当的腐蚀敏感性。例如1981年,台湾民航客机B-737遭遇空难,之后查明是该机经常运输海鲜,机身下部铝合金结构多处发生严重的晶间腐蚀、剥蚀,导致出现裂纹和孔洞,在空中增压时引发爆破解体。
从腐蚀的外观形貌来看,金属的腐蚀可分为均匀腐蚀和局部腐蚀。对于铝合金来说,其表面存在的氧化膜具有良好的保护性,故均匀腐蚀现象非常轻微,甚至不会出现。然而,在某些极端条件下,则可能出现局部腐蚀现象,并会造成一定的危害。铝合金在海洋大气环境下的局部腐蚀主要包括点蚀、电偶腐蚀、缝隙腐蚀、剥落腐蚀、晶间腐蚀和应力腐蚀等。
现有的研究证明,在卤素离子含量高的潮湿大气环境中,空气中的卤素离子(如氯离子)会侵蚀铝合金材料表面的氧化膜,破坏防护层,形成腐蚀坑。尤其是在沿海、多雨、潮湿、高温和工业污染较为严重的地区,应特别注意铝合金材料的腐蚀,避免出现严重的安全事故和经济损失。此外,在实际施工过程中,构件不可避免地会出现碰撞、划擦和磨损,这些都会破坏铝合金构件表面的氧化膜,降低其耐腐蚀性。另外,铝合金结构在服役过程中,受到的外荷载也可能使其表面的氧化膜开裂,从而降低其耐腐蚀性。
铝和铝合金的耐腐蚀性能主要取决于其表面钝化膜的性质及其在各种环境中的稳定性。腐蚀现象的影响因素非常复杂,受到气候条件、空气中污染物浓度和材料本身性质等各种因素的影响,而且各因素之间还有耦合效应。这也造成了铝合金的各种腐蚀破坏形式之间存在一定的关联,比如点蚀会逐步发展为晶间腐蚀和剥落腐蚀,而各种局部腐蚀又会成为应力腐蚀的裂纹源。
铝合金腐蚀试验研究现状
现有的关于铝合金腐蚀的研究,基本都集中在材料科学中。通过各种电化学测量技术,评定铝合金的耐腐蚀性能。但是对于铝合金腐蚀后力学性能的相关研究非常少。另外,值得注意的是,铝合金牌号繁多,从1×××系至9×××系,各种各样的合金成分对铝合金本身的耐腐蚀性能影响很大。例如,常用的高强铝合金2×××系铝合金(以铜为主要合金元素)和7×××系铝合金(以锌为主要合金元素)的强度较高,但是其耐腐蚀性较差;3×××系铝合金(以锰为主要合金元素)、5×××系铝合金(以镁为主要合金元素)和6×××铝合金(以镁和硅为主要合金元素)则具有更好的耐腐蚀性能,属于中等强度铝合金。
通常来说,铝合金桥梁中建议使用5×××系和6×××系铝合金,原因在于其强度和耐腐蚀性能更加适合工程应用。我国《铝合金结构设计规范》(GB 50427—2007)中也规定,铝合金结构型材宜采用5×××系和6×××系铝合金,板材宜采用3×××系和5×××系铝合金。建筑结构用铝合金牌号的选用充分考虑了材料的强度和耐久性要求。
腐蚀试验是探究金属大气腐蚀规律的有效手段。目前金属腐蚀试验研究一般通过室外大气暴露试验和室内模拟加速试验来进行。衡量金属腐蚀程度的指标包括年失重率或年增重率,孔蚀坑的深度、面积和密度分布,以及腐蚀后力学性能损失量等。观察腐蚀形貌和腐蚀产物时,可以使用扫描电子显微镜、原子力显微镜、激光扫描共聚焦显微镜等。另外也可以采用电化学工作站、扫描开尔文探针技术等电化学测量手段来研究金属腐蚀。
1 室外大气暴露腐蚀试验研究现状
室外大气暴露试验是将所研究的金属材料或试件放置在实际使用环境下进行暴露试验,是最直接的研究方法。铝合金耐候性的研究由来已久。对于均匀腐蚀的金属来说,如铁、锌等,腐蚀失重率或平均损失厚度是具有相当可信度的衡量腐蚀程度的指标;但是对于铝合金这类具有明显局部腐蚀特征的金属,这两种指标并不能完全反映腐蚀程度。因此,采用蚀坑深度和分布密度及剩余力学性能可更好地反映腐蚀损伤程度。表1给出了部分文献中的室外暴露腐蚀试验数据。可以看出铝合金耐大气腐蚀性能良好,蚀坑深度基本处于微米级别。下文将对表1给出的部分文献中的试验数据进行阐述。
01 短期室外大气暴露腐蚀试验
通过短期的室外暴露试验能够探究铝合金的初期大气腐蚀行为。HERN NDEZ等在西班牙特内里费岛进行了大气暴露试验。该试验并未说明采用了何种牌号铝合金,根据其合金成分推测为5×××铝合金,半年后试件表面出现了点蚀现象,即使是在最严酷的腐蚀环境下,蚀坑平均深度不超过60μm。
国内王沙沙等在青岛对6061-T651铝合金进行了海洋-工业大气环境下的室外暴露试验。一年后,其屈服强度和抗拉强度降低幅值均在5%以内;之后又进行了6061-T6铝合金与30CrMnSiNi2A结构钢电偶连接件的室外暴露试验,证明了异种金属接触会显著降低铝合金的耐腐蚀性,且空气中硫化物会促进沿晶腐蚀的发展。
ELOLA等也在西班牙的5个试验点对A1050铝合金进行了长达4年的大气暴露试验。最终发现,在海洋-工业大气环境下,铝合金的腐蚀情况最严重;而在大陆性气候的乡村地区,铝合金的腐蚀情况最轻微。随时间延长,腐蚀坑密度遵循线性增长规律,而腐蚀坑平均深度和最大深度遵循双对数规律。
SURNAM等在毛里求斯岛上对A1050铝合金进行了为期1.5年的暴露试验,得到最大腐蚀深度约为50μm;并采用幂指函数拟合了最大蚀坑深度增长曲线。
02 中、长期室外大气暴露腐蚀试验
短期铝合金室外暴露腐蚀试验证明了其腐蚀具有点分布的特征,且铝合金在大气中暴露一段时间后的腐蚀速率会迅速降低。鉴于铝合金在大气中腐蚀速率低、发展慢,而且国际上普遍认为材料自然腐蚀数据需要8~10年以上才有真正的应用价值,所以中、长期的腐蚀试验是必需的,这对于认识铝合金结构在整个寿命周期内的承载性能变化具有重要的参考意义。
早在20世纪20年代,美国Alcoa实验室进行了相当广泛的铸造铝合金和变形铝合金的暴露试验,大约有25000个试件。从20世纪四五十年代,法国和意大利也相继开展了铝和铝合金的大气暴露试验。我国起步较晚,从20世纪80年代才开始进行相关的试验。
GHALI给出了6061-T铝合金在海洋大气环境(巴拿马)下的中、长期腐蚀情况,暴露试验持续了16年,测得每年平均腐蚀深度为17.3μm。
FUENTE等通过试验发现,在工业或海洋大气中,铝合金的腐蚀情况最严重,暴露16年后观察到大约100μm深的腐蚀坑;根据该试验所用合金成分,推断为1×××系铝合金。以上两类试验都证明了铝合金具有较好的长期耐腐蚀性能。
铝及铝合金在不同环境下的腐蚀敏感性差异很大,在我国不同自然环境下的腐蚀率相差6~15倍,而相对易腐蚀环境为海洋大气、湿润工业环境、工业污染环境。郑弃非等对10种铝合金在我国7个典型大气试验站进行了10年暴露试验。得出结论:影响铝合金中、长期腐蚀的环境因素中,污染物因素是主要的,气候因素是次要的;其中,空气中SO2含量的影响最为显著。大量研究均表明,铝合金大气腐蚀最敏感的环境是海洋和工业大气环境。
铝合金在腐蚀发展过程中腐蚀速率的变化基本遵循“先快后慢”的特点。WALTON等进行了各种Alcoa变形铝合金和铸造铝合金的长期大气耐候性试验。结果表明,铝合金在大气中暴露1~2年后,腐蚀速率迅速衰减,表现出“自停止”的现象。即使是耐腐蚀性较差的铝合金,在严酷海洋大气环境下,腐蚀坑深度每年增长小于50μm;在普通大气环境下,每年增长小于25μm。
文邦伟等在万宁试验站进行了10年的大气暴露试验,研究了纯铝、防锈铝、锻铝和硬铝的耐腐蚀性,1年平均腐蚀深度约为0.2~0.45μm/a,10年后的年平均腐蚀深度为0.08~0.25μm/a,表明腐蚀速率随时间迅速减缓。
文邦伟等和林德源均指出铝合金的腐蚀产物会堆积在金属表面,具有一定的防腐作用。
03 腐蚀规律模型
通过对试验数据的总结分析,学者们试图建立各种数学模型来描述铝和铝合金在不同大气环境下的腐蚀行为。
最常见的腐蚀模型为幂指函数模型,AZIZ等提出采用幂指函数来表达蚀坑深度增长规律。幂指函数增长规律的表达式为:
式中:C为腐蚀程度;t为暴露腐蚀时间;k为与材料和环境相关的参数。
其中,指数n在SURNAM等试验模型(S模型)中约为0.2,而在Godard模型(G模型)中则为1/3。相比于G模型,S模型能更好地代表毛里求斯大气环境下的铝合金最大腐蚀深度增长规律,从中可以得出:针对不同的大气环境和材料属性,k和n均应通过大量试验数据确定,以得到符合当地气候条件的腐蚀深度增长规律。
MELCHERS调查了大量铝合金腐蚀试验数据,认为相比幂指函数模型,双峰函数模型更适用于描述蚀坑深度增长规律。
OTERO等根据腐蚀规律推断蚀坑深度的增长遵循半对数曲线,且推测在100年后最大蚀坑深度不会超过第1年的5倍。
ELOLA等则根据试验数据拟合了描述蚀坑深度发展规律的双对数曲线。半对数函数模型和双对数函数模型的表达式分别为:
式中:C为腐蚀程度;t为暴露腐蚀时间;a和b均为与腐蚀因素相关的拟合参数。
以上腐蚀模型的曲线如图1所示。
图1 腐蚀模型
铝合金腐蚀发展的影响因素众多,主要包括材料化学成分、材料微观结构、暴露温度、暴露时间、局部溶液条件和应力状态等。此外,适用于短期腐蚀规律的模型未必适用于长期腐蚀。因此要建立统一且具有相当可信度的腐蚀模型是非常困难的。面对诸多的铝合金类型和复杂的大气环境,铝合金的大气腐蚀发展规律存在明显的差别,必须通过足够的现场试验数据对腐蚀规律模型的参数进行校准。换句话说,对于特定的铝合金牌号和大气环境,需要对其腐蚀模型参数进行专门的校准,这就会耗费大量的时间和经济成本。
2 室内模拟加速腐蚀试验研究现状
因室外腐蚀试验周期长、耗费大,室内模拟加速腐蚀试验成为研究海洋大气腐蚀的主要手段。加速试验必须满足模拟性、重现性和加速性3个要求,直接影响到室内模拟试验和室外暴露试验的相关性。常见的室内模拟加速腐蚀试验有盐雾试验、干湿周浸循环试验等。表2给出了部分文献中的室内模拟加速腐蚀试验数据。
张琦对LC4和LY12两种铝合金均进行了间歇盐雾和周期轮浸加速试验,并与广州和海南琼海的现场试验进行对比,发现采用pH=3.0的5%NaCl+0.5%(NH4)2SO2为溶液的间歇盐雾试验对于大气暴露腐蚀具有较好的模拟性和加速性。
王洁采用干湿循环盐雾试验的方法对7075铝合金(1mm厚)的腐蚀性能进行了研究,发现5个周期后铝合金强度下降约20%~30%。强度衰减较大的原因有两个:一是7075铝合金本身的耐腐蚀性较差;二是该试验中试件厚度太薄。铝合金原始试件的厚度对其剩余力学性能存在较大的影响。在腐蚀深度相同的情况下,与较厚的铝合金试件相比,较薄试件会表现出更明显的强度降低。
由于铝合金本身强度较低,故紧固件一般采用强度较高的其他金属材料,如不锈钢、碳素钢等。在高湿、高盐雾浓度的海洋环境下,异种金属之间的接触会导致电偶腐蚀。铝合金的电位较低,通常作为阳极金属而被加速腐蚀;不过,此类接触一般会形成“大阳极-小阴极”的原电池,相对“小阳极-大阴极”来说较为安全。
MREMA等对常用的建筑用铝合金6061-T6的耐腐蚀性能进行了详细研究。首先通过连续中性盐雾试验研究安装各种紧固件的铝合金板的电偶腐蚀情况,预腐蚀时间为1000小时。结果表明,紧固件表面处理防腐性能从高到低依次为GEOMET镀锌涂层→绝缘衬套→镀层垫圈(氯乙烯)→未表面处理。对于无保护层的铝合金6061-T6(铝板和紧固件均未表面处理),蚀坑最大深度为0.5mm。之后,继续研究了在含氯环境中,埋置在水泥砂浆中的A6061-T6铝合金板(9mm厚)的腐蚀行为,采用干湿循环加速腐蚀试验方法,所有预腐蚀试件的强度几乎无损。
最后,MREMA等在冲绳的宫古岛进行室外暴露试验,得出结论:1000小时连续盐雾试验大概对应于直接大气暴露试验的1~3年中的某个时间点。另外,若紧固件进行了GEOMET表面处理,大气暴露3年后毫无腐蚀。
除盐雾试验外,干湿周浸循环和氙灯辐射试验也是模拟海洋大气环境的方式。杨浪等对去除氧化膜后的6061-T651铝合金在模拟工业-海洋大气环境下的腐蚀进行了研究。通过氙灯老化(59h)和周期浸润(48h)试验,经8个循环周期后,铝合金出现点蚀和晶间腐蚀,其屈服强度和抗拉强度分别降低4.1%和5.6%,这表明试样的腐蚀没有对强度造成明显影响。
冯驰等采用与杨浪等相同的试验方法研究了不同表面处理下6061铝合金和30CrMnSiA 结构钢的电偶腐蚀。腐蚀8个周期后,采用环氧聚酰胺底漆和丙烯酸聚氨酯面漆的复合防护涂层的6061铝合金强度和塑性损失较小,抗拉强度和断后伸长率分别下降约6%和5%;而仅采用表面阳极氧化处理的6061铝合金的抗拉强度和断后伸长率分别下降了约24.2%和13.4%。该试验中腐蚀溶液为具有强氧化性的酸性溶液,故大大加快了腐蚀速率,使得强度降低率约为1年青岛海洋-工业大气环境下的4倍;不过该试验结果是否能够重现长期暴露试验中的腐蚀规律也未可知。
为探究加速腐蚀试验方法的模拟性和加速性,刘明等对比分析了连续盐雾、循环盐雾、周期浸泡、周期降雨共四种模式的加速试验,认为循环盐雾试验及周期降雨可较好地模拟琼海大气环境下2A12铝合金的腐蚀规律。
郝美丽等认为通过盐雾、干燥、湿热、干燥、浸渍(NaHSO3溶液)的复合循环试验可用于模拟LY12铝合金在海南万宁试验站的大气腐蚀行为。
韩德盛等设计了模拟海洋大气腐蚀的“溶液浸泡-气氛暴露”加速试验,且与间歇盐雾和周期浸泡进行对比,为进一步改进试验方法提供了参考。因此,模拟加速腐蚀试验方法需要针对具体的大气环境进行特定的设计,以更好地重现腐蚀发展规律;但是目前该方面的研究尚无突破性的进展。
3 讨论与小结
总的来说,腐蚀试验是研究金属腐蚀的主要途径。室外大气暴露试验得到的结果数据真实可靠,最符合实际情况。短期室外大气暴露试验的周期较短,能较早地观察到金属腐蚀现象,但是只能反映腐蚀初期行为;长期室外大气暴露试验能得到更准确、更长时间内的金属腐蚀行为规律,却存在人力、物力耗费大和试验周期长的缺点。从本文搜集的数据来看,试验周期短则1~2年,长则20年;而过长的试验周期必然会增加试验过程中的不可控因素,造成试验组织困难。
室内模拟加速腐蚀试验能在实验室条件下使用设备模拟腐蚀环境,加速腐蚀过程,预测真实大气环境中的长期腐蚀行为,节约人力、物力,因此成为主要的腐蚀试验手段。但是目前尚无任何加速试验能够准确地重现室外大气暴露下的自然腐蚀情况。即便如此,室内模拟加速腐蚀试验仍是研究腐蚀规律不可缺少的一种手段,具有重要意义。
在各种加速腐蚀试验方法中,盐雾试验是模拟大气腐蚀的最主要方法。不过,单一的连续盐雾试验对大气暴露的模拟性并不好,而以干湿交替为基础的加速腐蚀试验则能更好地再现真实大气环境,其结果更接近自然腐蚀情况。为探究多种腐蚀因素的影响,较准确地模拟金属的腐蚀行为,学者们开始致力于研究多因子复合循环加速腐蚀试验,如北京航空材料研究所研制的8因子加速试验装置,与自然暴露试验相比具有良好的一致性。
总而言之,室外大气暴露试验仍需持续进行,以完善腐蚀数据库。室内腐蚀试验方法的研究方向应考虑多环境因子复合影响,有针对性地设计各类大气环境下的室内加速腐蚀试验。
既有铝合金结构的腐蚀评价
腐蚀试验能够根据研究目的灵活设计,更准确地表现出铝合金的腐蚀特性,但是时间和经济成本很高。故通过对现有铝合金结构进行腐蚀程度评定检测,是一种有效的评价铝合金结构耐久性的手段。
1 铝合金结构腐蚀案例分析
相比于建筑结构,铝合金应用于桥梁结构的历史更为悠久。铝合金最早用在桥梁上是在1933年建成的匹兹堡史密斯菲尔德街大桥(图2),该桥使用铝制桥面板替换重型钢木桥面,桥梁自重的降低使桥梁的承载力得到显著提高。2014-T6铝制桥面板一直使用到1967年,然后被更耐腐蚀的6061-T6铝合金桥面板所取代,该桥面板一直使用到1995年。
图2 史密斯菲尔德街大桥
1983年,ALISON调查了7座铝合金桥梁服役20~30年后的损伤情况。其中,除加拿大Arvida桥(图3)外,其余6座桥梁均使用6061-T6和5083-H113铝合金。通过目测方法调查发现:腐蚀情况很少,大部分结构基本无腐蚀,轻微点蚀也不影响结构的安全性能。因腐蚀损伤而需要维护的只有Arvida桥,该桥建于1950年,位于乡村地区。由于冰雪季节长(4~5个月),因而附近道路上使用除冰盐较多,服役环境恶劣。经检查发现,树叶、草和泥土进入了箱形柱并聚集在柱底造成排水孔堵塞,致使铝合金墩柱底部出现剥落腐蚀;且在北部的底部水平横梁上发现了一些小面积的剥落或分层(图4a),支撑桥面的梁有微小腐蚀。最主要的腐蚀原因是采用了耐腐蚀性较差的2014-T6铝合金,且未作任何防腐处理。后采用耐腐蚀性能更好的6061-T51铝合金对桥墩进行修复(图4b),并采用6061-T6和6061-T651铝合金对桥梁横撑和主梁进行替换。目前该结构已服役近70年,情况良好。
图3 加拿大Arvida铝合金桥
图4 加拿大Arvida铝合金桥桥墩修复前、后
20世纪60年代,位于纽约长岛的两座铝合金桥建成通车。服役约20年后,铝合金结构无腐蚀现象。但是该桥有一个潜在隐患,上部铝合金结构和下部钢支座之间直接接触,在潮湿环境下易发生电偶腐蚀。在1996年的检查中发现了这一现象,随后对其进行了维修。
1956年,德国的Schwansbell铝合金桥梁(图5)建成,该桥采用AlMgSi1 F32铝合金,即相当于现在的EN AW 6082-T6铝合金。为验证铝合金桥梁在高腐蚀性工业大气环境下的耐腐蚀性,该桥表面未作任何表面处理。约服役50年后,除结构表面呈现暗灰色外,各部件的承载力和使用功能均未受到影响,表现出优异的稳定性和耐久性(图6)。
图5 德国Schwansbell铝合金桥
图6 服役50年后Schwansbell铝合金桥表面
1961年,日本现存时间最长的铝合金桥——金庆桥建成(图7)。该桥位于日本内陆,空气中盐分较少,但是环境潮湿,冬季会在道路上使用除冰盐,所处环境较为恶劣。主体结构自建成后未进行过任何维修。服役56年后,在铝合金制主梁、腹板、剪刀撑、横梁以及这些构件的连接部位(焊接、铆接部位)上出现大范围细小的腐蚀坑,但腐蚀深度浅,对结构安全没有影响。
图7 日本金庆桥
2009年,上海崇明岛建成一座铝合金通信塔(图8),该塔距海边仅30m左右。笔者在2019年3月底观察该通信塔的腐蚀问题,发现结构表面无明显腐蚀痕迹,连接处也未发现腐蚀迹象,主体结构完好,表明铝合金结构在近海地区仍表现出很强的耐腐蚀性能。
图8 上海铝合金通信塔
近百年的铝合金结构发展史,充分证明了铝合金结构在复杂严酷环境下良好的耐久性。铝合金即使未作表面处理,其在海洋大气环境下的耐腐蚀性也比经表面处理后的钢材的耐腐蚀性更为优良。在海洋大气环境中发生的轻微点蚀也基本不会影响结构整体承载力。
考虑到维修养护成本,严酷环境下铝合金比钢材更具性价比。但是,材料牌号的选取不当、异种金属的接触以及连接处缝隙密封不良等情况,均可能导致电偶腐蚀和缝隙腐蚀的发生,必须在设计和施工过程中予以避免。值得庆幸的是,电偶腐蚀通常不会出现在乡村或非沿海地区的铝合金结构中。
2 铝合金结构大气腐蚀现场检测方法
开展铝合金结构腐蚀情况的现场检测,对于服役结构的安全性评价、检修具有重要意义。因场地等条件限制,诸多实验室检测手段无法应用在现场检测中,影响了铝合金结构腐蚀现场检测的精度和效率。目前铝合金结构腐蚀检测的主要项目有外观检查、腐蚀深度检查、腐蚀产物分析和附着盐分测量等;可采用的手段主要有目视检测、涡流检测、超声检测、渗透检测、X射线检测、电化学检测等。
目前应用最广泛、效率最高的就是目视检测。该方法依赖于工程师的经验和主观判断,无法量化腐蚀程度。本文所涉及的工程案例均采用了此方法来调查结构的腐蚀情况。目视检测作为最基本的检测方法,可快速地判断服役结构的腐蚀外观,为进一步的检测提供指导。
因铝合金独特的材料性质,局部腐蚀或点蚀是最常见的腐蚀形式。故腐蚀深度是一项重要的检测项目,可采用涡流检测、超声检测、X射线检测等方法。除此以外,附着盐分测量、腐蚀产物分析也在以上工程案例中有所采用,可用来分析大气腐蚀的起因和类型。
通过腐蚀图像可分析腐蚀原因、判断腐蚀类型,对于评定结构腐蚀程度具有重要意义。为此,部分学者开展了基于图像处理技术的铝合金腐蚀评价方法。该方法通过对腐蚀图像进行提取、处理,得到二值图像特征,最后可据此评定铝合金的腐蚀等级,是一种应用前景广阔的现场检测手段。
3 讨论与小结
因传统观念中认为铝合金结构耐腐蚀性强,对于铝合金结构的防腐和腐蚀评定未给予足够的重视。然而,既有结构的腐蚀检测表明,在高腐蚀性环境下,施工中操作不当会引起铝合金结构的腐蚀,并引发结构安全问题,如加拿大Arvida铝合金桥。因此,有必要发展铝合金结构的大气腐蚀现场检测技术。
值得一提的是,航空航天领域中关于铝合金腐蚀的研究更为广泛和深入,对铝合金建筑结构腐蚀检测评定的相关研究具有重要的借鉴意义。但应注意,建筑用和航空用铝合金结构的腐蚀之间存在巨大的差别,如服役环境、连接形式、材料种类、表面处理技术等。此外,有关铝合金结构腐蚀等级评价的相关研究尚未见诸报端,需在大量腐蚀试验和检测调查的基础上扩展相关研究。
结 论
(1) 铝合金自身防腐性能优越,即使未作任何表面处理,其耐腐蚀性也比经表面处理后的钢材的耐腐蚀性更为优良;但在极端大气环境和施工操作不当的情况下,仍可能会产生危害结构安全性的腐蚀现象。
(2) 相对于铝合金牌号的种类繁多,目前国内外对铝合金的室外大气暴露腐蚀试验研究远远不足,有必要进行更长时间跨度和更多大气环境下的腐蚀试验,以完善腐蚀数据库。
(3) 室内加速模拟腐蚀试验方法并不能完全模拟真实环境下的铝合金腐蚀情况,因此有必要改进和创新室内加速模拟腐蚀试验方法,以期能够尽可能地再现真实大气环境中材料的腐蚀过程,更加准确地预测铝合金的中、长期腐蚀行为。
(4) 影响铝合金腐蚀的因素众多且相互耦合,对腐蚀环境下多因素的铝合金腐蚀模型的研究还有待进一步开展;电偶腐蚀和缝隙腐蚀造成的危害更为明显,因此铝合金连接件的耐腐蚀性能有待深入研究,以得到不同紧固件对铝合金连接耐腐蚀性能造成的影响。
(5) 大量已建铝合金结构的调查结果表明,铝合金具有良好的耐腐蚀性能;但是,材料牌号选取不当、异种金属的接触以及连接处缝隙密封不良均可能造成铝合金的腐蚀,进而影响结构的安全性。
(6) 铝合金结构大气腐蚀现场检测技术和腐蚀评价标准尚未成熟,无法量化腐蚀程度对铝合金结构服役寿命和承载力的影响。
免责声明:本网站所转载的文字、图片与视频资料版权归原创作者所有,如果涉及侵权,请第一时间联系本网删除。
相关文章
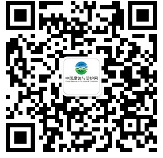
官方微信
《腐蚀与防护网电子期刊》征订启事
- 投稿联系:编辑部
- 电话:010-62316606-806
- 邮箱:fsfhzy666@163.com
- 腐蚀与防护网官方QQ群:140808414
点击排行
PPT新闻
“海洋金属”——钛合金在舰船的
点击数:8237
腐蚀与“海上丝绸之路”
点击数:6558