铝基复合材料具有高比强度、高比模量、良好的阻尼性能以及较低的膨胀系数[1~3],在航空、航天、航海和尖端武器等高科技领域显示出十分广阔的应用前景,一些种类的铝基复合材料已经走向工业化规模的应用。按照增强相的添加方式,铝基复合材料的制备方法可分为外加法和原位自生2种。由于原位自生法克服了外加法存在的应力集中、颗粒表面易污染,颗粒与基体界面结合力差等问题,已逐渐成为铝基复合材料制备技术的研究热点。其中,原位自生TiB2颗粒增强铝(TiB2/Al)基复合材料因其具有优异的力学性能和物理性能、较低的生产成本、颗粒强化效果显著等特点受到了普遍的重视。目前,原位自生TiB2/Al基复合材料的制备方法主要有:放热弥散法[4]、接触反应法[5]、混合盐反应法[6~8]等。放热弥散法因预制块中的原位自生颗粒尺寸和含量难以控制,且稀释重熔的过程中原位自生颗粒难以分散均匀,在实际生产应用中受到限制。采用接触反应法制备的TiB2/Al基复合材料所形成的增强颗粒尺寸较大,且反应过程难以控制。混合盐反应法制备的TiB2/Al基复合材料,制备工艺简单、可操作性强,且自生颗粒尺寸小,有利于材料液态成型,适合于大规模工业化生产。
上海交通大学材料科学与工程学院特种材料研究所多年来潜心研究采用混合盐反应法原位合成TiB2/Al基复合材料并攻克了熔体反应控制、熔体纯净化处理等关键难题[9]。所制备的TiB2颗粒在熔体中直接反应生成,其尺寸细小(纳米和亚微米级),外形圆整,且颗粒与基体间具有良好的相容性。颗粒与基体界面干净、无任何界面反应物,使得该材料具有高强度、高模量、良好铸造性,实现了大型构件和复杂构件的直接铸造成形[10,11]。同时,具有良好塑性成形性和机械加工性能的变形铝基复合材料通过轧制、锻造、挤压工艺可实现各种零件近净成形[12]。近年来,增材制造用原位自生TiB2/Al基复合材料粉末、线材以及大型构件也逐渐在复杂结构轻量化中发挥作用。在此基础上,原位自生TiB2/Al基复合材料具有良好的切削加工性和可焊性,进一步扩大了此类铝基复合材料的应用范围。目前,此类原位自生TiB2/Al基复合材料的应用范围已涉及航空、航天、航海、武器装备、轨道交通、汽车轻量化等领域[9]。
然而,原位自生TiB2/Al基复合材料中增强相的存在使其内部组织结构不均匀,TiB2增强相与基体之间的电位差、杂质相的析出、增强相与基体界面的高密度位错,以及材料制备过程中形成的缺陷等问题,导致复合材料在使用过程中易形成腐蚀微电池,而遭受点蚀、剥蚀、磨蚀等不同形式的破坏[13,14], 极大地限制了复合材料在潮湿空气、海洋等腐蚀环境中的有效应用。这显然不能满足原位自生TiB2/Al基复合材料日益增长的应用需求。因此,探索原位自生TiB2/Al基复合材料的表面防护方法,提高其耐腐蚀性能,具有重要的应用价值。同时,原位合成TiB2/Al基复合材料腐蚀与防护的机理也是材料科学中的一个重要研究方向。
本文对国内外原位自生TiB2/Al基复合材料的表面处理及腐蚀防护技术现状作简要评述,包括原位自生TiB2/Al基复合材料的腐蚀机理研究、原位自生TiB2/Al基复合材料表面处理方法(主要包括:阳极氧化+稀土转化膜技术、低温熔盐沉积技术、微弧氧化技术、激光表面合金化技术、冷喷涂等)与防护效果、未来表面改性技术在相关重点领域的展望等方面。
1 原位自生TiB2/Al基复合材料的耐蚀特点
原位自生TiB2/Al基复合材料作为一类极具应用价值的金属基复合材料,其耐腐蚀性能也是影响进一步应用的重要因素。因此,详细了解TiB2/Al基复合材料的抗腐蚀性能,研究其在特定环境中的腐蚀机理,掌握复合材料腐蚀原因及影响腐蚀的相关因素,对于推进新材料产业化具有重大现实意义。尤其是准确掌握此类复合材料的腐蚀特性,有利于制定切实可靠、经济有效的腐蚀防护工艺。
例如,Sun等[15]借助电化学阻抗和动电位极化技术,对原位自生TiB2/A356复合材料(主要组成相为α-Al、Si和TiB2)电化学腐蚀行为进行研究,通过对比A356合金(主要成分为Al-7.0%Si-0.35%Mg)、5%TiB2/A356 (质量分数,下同)和15%TiB2/A356复合材料试样在3.5%NaCl (质量分数,下同)溶液中的电化学阻抗谱(图1a[15]),发现复合材料表面天然氧化膜层的电阻随着材料中颗粒含量增加而降低,材料腐蚀速率随颗粒含量的增加而逐渐增大。此外,从Bode图(图1b[15])中可以更清晰比较出,复合材料的阻抗比基体低近1个数量级。因此,认为复合材料中的TiB2和与其聚集在一起的短棒状Si (图1g和i[15])能够破坏材料表面氧化膜的完整性,削弱其对材料基体的保护作用,而TiB2颗粒与活性Al基体间的微电偶腐蚀是导致该复合材料耐蚀性差的主要原因。极化曲线的测试结果(图1c[15])进一步说明在3.5%NaCl溶液中复合材料比基体具有更高的腐蚀敏感性,且其耐蚀性随着颗粒含量的增加而降低。极化腐蚀试样表面形貌(图1d~i[15])揭示出复合材料的电化学腐蚀主要发生在有大量TiB2颗粒聚集的晶间位置,且沿晶间区域延伸到Al基体内部。
图1 A356铝合金和不同TiB2含量复合材料的Nyquist图、Bode图、极化曲线以及极化后试样腐蚀形貌[15]
在此基础上,Huang等[16]系统研究了原位自生TiB2/7050Al基复合材料在不同pH值(pH = 4、6、7和10) NaCl溶液中的耐蚀性行为。从Nyquist图(图2a[16])可见,复合材料耐腐蚀性随着pH值降低而变差,酸性和碱性条件都会降低复合材料抗腐蚀能力。但在pH = 7的NaCl溶液中,复合材料阻抗远大于其他条件,腐蚀程度最低。极化曲线(图2c[16])结果表明腐蚀电位(Ecorr)随着pH值增加而降低。同时,腐蚀电流密度(icorr)在pH = 7时呈现最小值,表明复合材料在中性NaCl溶液中的腐蚀性最小。在酸性和碱性溶液中,腐蚀电流密度都增大,腐蚀行为加剧。静态浸泡测试结果显示,复合材料在酸性NaCl溶液中由于H+作用而表现出明显腐蚀现象;在碱性NaCl溶液中,OH-对于Al基体的强化学溶解也会使复合材料产生明显腐蚀;在中性或近中性NaCl溶液中,复合材料腐蚀性最小。在复合材料中,点蚀倾向于在TiB2颗粒富集带发生,TiB2颗粒主要作为有效的电偶阴极相,增加复合材料腐蚀速率。不同pH值环境下其腐蚀行为也并不相同,在酸性环境中(图2d~f[16])点蚀是主要的腐蚀形式;在中性环境中(图2g[16]),点蚀和均匀腐蚀会形成;而在碱性环境中(图2h和i[16])则主要以均匀腐蚀为主。
图2 原位自生TiB2/7050Al在不同pH值溶液中的Nyquist图、Bode图、极化曲线及不同pH值条件下静态浸泡8 d后试样腐蚀形貌[16]
所以,原位自生TiB2/Al基复合材料在NaCl溶液中极易发生腐蚀,是由于TiB2颗粒与Al基体之间的微电偶反应。因此,研发并采用抑制TiB2和Al之间电偶腐蚀的表面技术是提高复合材料耐蚀性的关键。目前,铝基复合材料的表面处理研究大多集中在SiC/Al体系,而对于TiB2/Al体系的研究还有待于进一步的发展。由于TiB2颗粒具有一定导电性,其亚微米粒径比微米级SiC颗粒尺寸小得多,将现有铝基复合材料防护方法直接应用于TiB2/Al基复合材料将存在一定的问题。对于不同种类以及在不同使用环境中的复合材料,相同的防护方法往往表现出迥异的防护效果,并且单一的方法可能存在一定局限性。因此,研究行之有效的防护方法以提高原位自生TiB2/Al基复合材料的耐蚀能力已经成为该领域一项重要工作。
2 阳极氧化和稀土转化膜技术
铝合金阳极氧化是将铝合金作为阳极置于适当的电解液当中,并向铝合金施加阳极电流,使其表面生成一层蜂窝状非晶态Al2O3膜层。由于原位自生TiB2/Al基复合材料组织的复杂性特点,使得氧化膜的均匀性和完整性受到很大影响。因此,单一阳极氧化处理可能无法为原位自生TiB2/Al基复合材料提供良好耐蚀性保护。另一方面,阳极氧化膜层孔隙率较高,采用合适的封孔工艺是进一步提高其耐蚀性的重要方法。Hinton等[17]发现7075铝合金在含有少量CeCl3的NaCl溶液中腐蚀速率显著下降,这一现象引起了科研工作者们对铝合金表面稀土转化封孔膜研究的兴趣。Mansfield等[18~20]率先展开铝基复合材料表面稀土转化封孔膜的研究,为复合材料应用寻求了一条很有应用价值的防腐途径。Yu等[21]采用稀土盐对SiC/6061Al阳极氧化膜进行封闭处理,发现稀土封孔处理氧化膜与铬酸盐封闭处理氧化膜的耐腐蚀性具有可比性,且稀土盐价格低、无毒害作用。这些优势使得该处理工艺具有很大应用潜力。Hu等[22]研究了Al18B4O33/6061Al浸入添加不同含量H2O2的CeCl3溶液中制备铈转化膜层的组织形貌和成分,并采用电化学方法比较各转化膜抗腐蚀效果,发现转化膜层主要由Ce4+化合物组成。该膜层抑制了复合材料在含Cl-溶液中的阳极反应,显著改善了材料耐蚀性。
对于原位自生10%TiB2/A356复合材料,利用阳极氧化和稀土转化封孔处理2种途径可提高其耐蚀性[23]。复合材料阳极氧化后表面Al2O3膜形貌如图3a和b[23]所示,氧化膜呈现多孔结构,孔尺寸在20 nm左右。该Al2O3膜并不平整,局部表面存在一些凹坑(A)和孔洞(B) (见图3a[23])。这些凹坑和孔洞主要是由于TiB2颗粒和Si粒子从氧化膜表面脱离造成。此外,多孔结构也在氧化膜凹坑中形成,即阳极氧化膜可以绕过一些粒子或聚集物向复合材料内部生长。经过化学沉积后的铈转化膜形貌如图3c和d[23]所示,许多球形颗粒覆盖了整个氧化膜表面,颗粒尺寸都在100 nm左右,而且大颗粒之间存在许多尺寸较小颗粒。化学沉积法得到的球形颗粒不但封闭了氧化膜多孔结构,同时有效地覆盖了氧化膜表面大部分凹坑、裂纹和孔洞,从而在复合材料表面获得一层由阳极氧化膜和铈转化膜所共同组成的完整复合防护膜层。此稀土铈转化膜主要成分为Ce2O3、Ce(OH)4和Ce(OH)3等(图3e[23])。
图3 原位自生TiB2/A356复合材料氧化膜形貌,阳极氧化膜表面化学沉积铈转化膜形貌,复合材料表面铈转化膜的XPS Ce3d谱,复合材料、表面阳极氧化膜以及铈转化膜极化曲线,以及铈转化膜形成示意图[23,24]
原位自生10%TiB2/A356复合材料表面稀土铈转化膜的形成机理如图3g[24]所示。由于H2O2的加入导致溶液中Ce3+发生如下氧化反应[24]:
当TiB2/A356复合材料被浸入到铈盐溶液中,材料表面的Al就开始发生溶解。同时,H2O2也在阳极Al上发生分解反应:
TiB2颗粒是一种导电性较好的陶瓷,在稀土转化膜形成过程中是还原反应生成OH-的有利位置,还原反应方程如下:
随着上述还原反应在阴极TiB2颗粒上不断进行,复合材料表面区域pH值逐渐升高,当pH值达到或者超过8,一些氢氧化物就会在其表面形成并沉积成膜,可能发生的化学反应如下:
Si是原位自生TiB2/A356复合材料中非常重要的组成相,导电性差的特点使其不是转化膜沉积的有利位置。但Si相大都与TiB2颗粒聚集在一起,高浓度OH-也存在于Si颗粒周围,具有较高Ce含量的稀土转化膜层就在聚集有大量TiB2颗粒和Si相的晶间区域形成。转化膜干燥后,部分Ce的氢氧化物就会发生脱水反应,生成氧化物CeO2和Ce2O3。另外,转化膜外表面的部分含Ce4+化合物,可能是由于膜层中Ce3+氧化形成,不稳定的Ce3+化合物与空气中O2接触就会自动转化为含Ce4+化合物[25]。相比于复合材料基体,阳极氧化和封孔后的铈转化膜均能降低腐蚀电流密度(图3f[23])。但是,铈转化膜的腐蚀电流密度最小(1.045 × 10-7 A/cm2),比复合材料基体(2.633 × 10-5 A/cm2)降低2个数量级,表现出更加优异的耐蚀性。
此外,采用阳极氧化+阴极电解沉积方法在原位自生15%TiB2/A356复合材料表面制备铈沉积膜的复合膜层,亦能提升材料耐腐蚀性能[26]。沉积膜层主要分为2种区域,一种是图4a[26]中A位置的浅色区域,另一种是B位置的深色区域。从放大图(图4b和c[26])可知,A区由许多球形颗粒组成,颗粒尺寸约100 nm,与化学沉积膜形貌相似;而B区域形成的稀土膜呈现平板状组织,仅有少量球形颗粒沉积。B区域Ti和Si元素含量高于TiB2颗粒聚集区。同时,在B区域的Ce元素含量(43.78%,质量分数,下同)要远大于A区(7.42%),即电解沉积过程中铈膜更容易在阻碍氧化膜生长的TiB2颗粒聚集物上形核。在凹坑C位置,球形铈化物颗粒也有效地沉积到了氧化膜上(图4d[26])。由此推测因为铈沉积膜下面的氧化膜不完整、不均匀导致了阴极电解沉积在不同位置的形成机制不同。
图4 阳极氧化TiB2/A356复合材料表面阴极电解沉积铈膜形貌以及铈沉积膜在不连续复合材料氧化膜表面形成过程示意图[26]
铈沉积膜在不连续复合材料氧化膜表面形成过程如图4e~h[26]所示。由于复合材料中TiB2颗粒和Si相形成的聚集物严重阻碍了氧化膜生长并破坏了氧化膜连续性,当阴极电压作用于聚集物上时方程(5)更容易在这些具有电负性的聚集物上发生。随着复合材料表面OH-浓度不断增加,导致铈盐溶液的pH值不断增加,并在氧化膜附近形成OH-浓度梯度(图4f[26])。当复合材料附近pH值增加到8时,化学沉积反应将在多孔表面和未成膜聚集物上发生方程(9)。如果OH-浓度达到更高,铈膜沉积将按照方程(10)进行[26]:
方程(9)和方程(10)中化学反应快速发生,导致大量细小铈化合物在聚集物位置快速形核并紧密沉积在一起,最终在聚集物的附近形成大厚度平板态膜层组织(图4g[26])。同时,氧化膜表面高OH-浓度会导致Al2O3膜发生如方程(11)所示化学溶解。随着电解沉积时间的延长,稀土沉积膜生成速率将超过氧化膜化学溶解速率。氧化膜溶解被彻底抑制,使得多孔氧化膜被电解沉积生成的铈化合物颗粒逐渐封闭,稀土化合物不断沉积,导致膜层厚度增加(如图4h[26]所示)。随着稀土化合物不断沉积,聚集物逐渐被覆盖,沉积膜形核速率大幅减慢,导致少量大尺寸铈化合物颗粒也在板状膜层上沉积。此外,阴极电化学沉积的铈膜具有与阳极氧化膜相当的腐蚀电位,但腐蚀电流密度(5.957 × 10-7 A/cm2)远小于单一阳极氧化膜并且比复合材料基体要低2个数量级。在阳极氧化TiB2/A356复合材料表面采用阴极电解沉积制备稀土膜的方法,成膜时间短,比化学沉积方法更适合于工业生产应用,尤其适合综合力学性能优异的高颗粒含量原位自生TiB2/Al复合材料的表面防护。
3 低温熔盐沉积技术
现有铝基复合材料的腐蚀防护技术,尤其以传统阳极氧化为代表,会因TiB2颗粒增强体存在而降低生成氧化膜层的完整性和平整度。因此,研究一种耐蚀性能较好且完整而连续的防腐膜层,对有效提高原位自生TiB2/Al基复合材料抗腐蚀能力具有重要意义[27]。金属电沉积是利用金属离子阴极电化学还原作用使固体材料表面附着一层完整、连续镀膜的工艺。该镀膜可起到防止腐蚀、增强导电、反光及增进美观等效果。Al表面能够天然地形成一层保护性氧化膜,使其具有较高耐腐蚀性能;另外,Al与铝基复合材料的基体元素相同,如果能将铝层镀覆于原位自生TiB2/Al复合材料表面,将有效提高复合材料耐蚀性能[27]。目前,Al及铝合金电沉积的体系主要包括有机溶剂、无机熔盐和有机熔盐(即离子液体) 3种体系[28,29]。其中,AlCl3-NaCl-KCl熔盐体系是研究最多的无机熔盐体系。该体系熔盐制备简单、电导率高、使用周期长、Al的沉积速率快,可获得均匀且不容易剥落的沉积层。此外,AlCl3型无机熔盐(AlCl3-NaCl、AlCl3-NaCl-KCl无机熔盐)相对NaCl-KCl无机熔盐来说为低温熔盐(98℃左右)[28,29],其电沉积温度较低,不会影响基体材料力学性能,并且生产成本低,具有节能降耗的特点。
Huang等[30]创新性地采用熔盐电沉积铝的方法,通过优化低温AlCl3-NaCl-KCl无机熔盐电沉积液及铝层制备工艺,在原位自生TiB2/A356复合材料表面成功制备出致密、均匀和完整的铝镀层。系统研究了沉积时间对铝层组织的影响,发现Al在复合材料表面电沉积的初期是有选择性地优先沉积在TiB2和Si表面(图5a[30]A区域和图5a1[30])。随着电沉积时间延长(图5b和b1[30]),TiB2和Si相全被铝层覆盖后,基体中的Al相也逐渐沉积上铝层。铝层在逐渐生长,铝层大致覆盖住基体表面。当电沉积45 min时,基体表面全部沉积上了连续、致密、完整的铝层,如图5d和d1[30]所示。对这种选择性沉积机制进行了深入研究,并将其主要归因于如下3个因素:(1) 阴极复合材料表面TiB2和Si相凸起处增加了局部电流密度,加速了铝沉积[31];(2) TiB2和Al之间存在着很大电位差,铝层会在电位较高的相(TiB2和Si相)上优先沉积并向四周扩展;(3) Al、Si和TiB2相表面能影响铝的电沉积。金属表面总是以最稳定的状态呈现,最稳定的晶面是原子最密排面,而Al相比TiB2或Si有更低的表面能[32~35],电沉积铝层在TiB2和Si表面生成所需的激活能要比在Al上生成铝层所需激活能小得多。综上,铝层在沉积初期优先在TiB2和Si相表面沉积。
图5 电沉积铝层在不同沉积时间下的SEM像及其对应的形成机制,基体上形成的二维和三维铝晶核示意图,纯Al、A356、TiB2/A356复合材料和TiB2/A356复合材料电沉积铝层在3.5%NaCl溶液中的极化曲线[30]
电沉积铝晶粒的生长模式如图5e和f[30]所示。由于界面能越小,临界晶核尺寸越小,相应形成的沉积层晶粒尺寸就越小,反之亦然[36]。因此,二维生长的铝层表面形成的新铝晶粒比直接在基体表面生成铝层晶粒细小(如图5d[30]所示)。极化曲线测试结果(图5g[30])表明,TiB2/A356复合材料表面电沉积铝后的耐蚀性能相比原始复合材料有很大提高,并接近纯Al的耐腐蚀性。这是因为复合材料表面发生了Al的选择性沉积,有效减缓了TiB2和基体复合材料中Al之间的电偶反应,从而提高了复合材料的耐蚀性能。
为了进一步提高原位自生TiB2/Al复合材料表面熔盐沉积铝层耐蚀性,Huang等[37]将低温熔盐沉积技术与后续阳极氧化技术相结合,将连续、致密铝层转化为Al2O3膜层以提高其耐蚀性。如图6a[37]电沉积铝层与基体的截面形貌所示,铝层完整、平整、连续且厚度均匀(约9.1 μm),与基体结合良好。复合材料表面的铝层(图6b[27])经过阳极氧化后的表面保留了氧化前的大致轮廓且存在纳米级的不规则孔洞,生成的氧化膜连续、无缺陷存在。这避免了对原始复合材料直接进行阳极氧化时,因TiB2和Si相的存在而生成完整性和致密性较差的氧化膜。相比于只经过阳极氧化的复合材料(图6c和d[37]),由低温熔盐沉积结合阳极氧化后复合材料的耐蚀性得到了进一步提高(腐蚀电位:-0.686 V,腐蚀电流密度:4.236 × 10-7 A/cm2),并具有与阳极氧化后的纯Al (腐蚀电位:-0.685 V,腐蚀电流密度:4.055 × 10-7 A/cm2)相似的耐腐蚀性能。
图6 铝层和基体截面形貌[37],TiB2/A356复合材料表面电沉积铝层阳极氧化膜形貌[27],阳极氧化后复合材料、电解沉积铝层以及纯Al的Bode图[37],阳极氧化后复合材料、电解沉积铝层以及纯Al的极化曲线[37]
4 微弧氧化技术
由于铝基材料硬度较低、耐磨性较差,在高速流体中会出现较为严重的空泡腐蚀现象[38]。因此,当材料用于高速水流工况下时,铝基复合材料需要具备较高的耐空泡腐蚀和耐Cl-侵蚀的能力,这对该材料表面防护提出了严峻的挑战。本文中阳极氧化+稀土转化膜和低温熔盐沉积的2种工艺都能够显著提高TiB2/Al基复合材料的耐蚀性能,但氧化膜层硬度较低,在空泡作用下容易被破坏。陶瓷材料具有较高硬度,在耐空泡腐蚀方面具有很大优势[39]。微弧氧化(MAO)是一种将Al、Mg等金属置于电解液中(主要为碱性)并作为阳极,将材料从Faraday放电区提升到火花放电以及弧光放电区,在高压放电的作用下发生复杂的化学、电化学和等离子化学变化,并在材料表面生成一层晶态陶瓷膜层的表面处理技术[40,41]。微弧氧化技术可在复合材料表面形成一层连续的高硬度陶瓷氧化膜层[42]。因此,对原位自生的TiB2/Al基复合材料表面进行微弧氧化处理有望同时提高其耐蚀性和耐空泡腐蚀性能。
张弘斌[43]采用微弧氧化工艺在原位自生TiB2/A201复合材料表面以铝酸钠溶液为电解液体系,制备出的微弧氧化膜层孔隙率为3%,表面硬度达到1265 HV。将TiB2/A201复合材料与约50 μm厚的微弧氧化膜层进行耐空泡腐蚀实验,空泡腐蚀5、10、15、30、60和120 min后复合材料和氧化膜层宏观形貌如图7[43]所示。复合材料(图7a[43])经过5 min空泡腐蚀后表面失去了金属光泽。随着空蚀时间的延长,腐蚀区域的颜色逐渐变得暗淡,且粗糙度也有所增加。空蚀120 min后,试样表面还出现肉眼可见的蚀坑。微弧氧化膜层(图7b[43])经过5 min的空蚀后,膜层颜色加深,并且膜层出现了少量破损,露出了基底颜色。随着空蚀时间的延长,试样表面膜层脱落情况加剧;在经过120 min的空蚀后,空蚀区域的微弧氧化膜层脱落殆尽,且也出现了肉眼可见的蚀坑。
图7 TiB2/A201复合材料和微弧氧化膜层空泡腐蚀后的宏观形貌[43]
膜层经过空泡腐蚀后的微观形貌如图8a~e和a1~e1[43]所示。空蚀5 min后,试样表面出现了少量的空蚀坑,试样表面多数的“瘤状物”和“火山口”被破坏剥离,留下碎石状的陶瓷表面。空蚀10 min后,表面空蚀坑数量增多,并且其尺寸也有所增加。随着空蚀时间进一步延长,膜层表面空蚀坑数量增多,尺寸增大,“瘤状物”和“火山口”基本消失。空蚀120 min后,膜层基本被剥离,留下裸露的基底,表面存在大量空蚀坑。从失重量和空泡腐蚀时间的关系曲线(图8f[43])可以看出,试样在空泡腐蚀初期(0~10 min)质量损失较为明显,之后失重速率减小。此后,空蚀进入上升期,试样表面出现由空蚀针孔聚集而形成的空蚀坑,并且逐步扩展到整个表面,失重率达到最大值。空蚀30 min后,微弧氧化膜层已基本失去对基底的保护作用,空蚀主要对象逐渐由微弧氧化膜层转变为膜层下方的复合材料基底。微弧氧化膜层硬度显著高于Al基体,但是在空泡腐蚀30 min后就基本失去了对基底的保护作用,推测这主要是由于微弧氧化膜层中存在许多微裂纹等缺陷所导致。
图8 微弧氧化膜层空泡腐蚀不同时间后微观形貌,累计失重量与空蚀时间关系曲线,TiB2/A201复合材料和微弧氧化膜层在3.5%NaCl溶液中极化曲线,以及微弧氧化膜层截面图[43]
TiB2/A201复合材料和在3种电流密度(6、10和15 A/dm2)下制备微弧氧化膜的极化曲线(图8g[43])显示经过微弧氧化处理后,其自腐蚀电流密度出现了显著下降,并且在阳极极化过程中电流密度上升的趋势被显著抑制,这说明微弧氧化膜层有效地阻碍了复合材料阳极极化过程。在10 A/dm2电流密度下制备的膜层的自腐蚀电流密度最低,为3.1 × 10-8 A/cm2;10 A/dm2电流密度下制备的微弧氧化膜层缺陷较少(图8h和h1[43]),没有平行于基底的裂纹存在,且只有少数细小的垂直于基底裂纹存在,其抗腐蚀能力最强;15 A/dm2电流密度下制备的膜层自腐蚀电流密度最高,为1.6 × 10-6 A/cm2,但仍比TiB2/A201复合材料的自腐蚀电流密度(4.2 × 10-6 A/cm2)降低了约2.6倍[43]。所以,微弧氧化膜层有效地减少了腐蚀介质与基底接触,使自腐蚀电流密度大大降低,进而抑制复合材料基底在阳极极化过程中的进一步腐蚀。
表面处理工艺除了可以提高材料的耐蚀性、耐磨性以外,所赋予的颜色也能够在医学识别、光学吸收、航天器应用等领域起到装饰性和功能性的作用。Wang等[44]在AZ91D镁合金上制备了不同颜色(黑色、白色以及灰色)微弧氧化膜层;通过在多磷酸电解液中添加TiO2溶胶,在Mg-Li合金表面也获得了耐蚀性良好蓝色微弧氧化膜。Han等[45]报道了通过碱性硅酸盐溶液在钛合金表面可制备一层黑色的微弧氧化膜;而Jiang等[46]在钛合金表面通过微弧氧化实现了一种新型黄色陶瓷膜层制备。目前,关于原位自生TiB2/Al基复合材料表面着色膜报道很有限,各种彩色陶瓷薄膜研究对其实际应用具有重要价值。Xia等[47]采用微弧氧化工艺,通过向碱性电解液中添加KMnO4,在原位自生TiB2/7050Al复合材料表面制备了棕色薄膜。由碱性电解液(9 g/L Na2SiO3 + 4 g/L NaOH + 2 g/L EDTA-2Na)经过微弧氧化制备膜层的宏观形貌呈现灰白色(图9a[47]),膜层表面孔洞(图9c[47])平均尺寸约1.1 ?m,孔隙率为4.23%。当电解液中添加KMnO4后,MnO
在碱性溶液中很容易被还原为MnO
(方程(12))。在此过程中薄膜颜色逐渐变为棕色[48],并在电场力驱动下转移到阳极,然后还原为MnO (方程(13))。随着微弧氧化反应的进行,更多MnO沉积在放电外层,最后薄膜呈现棕褐色(图9b[47])。
图9 碱性电解质中添加和不添加KMnO4的微弧氧化膜层,微弧氧化膜层的XPS分析,添加KMnO4膜层的Mn2p图谱[47]
棕褐色膜层微观形貌与灰白色膜层相似(图9d[47]),平均孔隙率减小为1.79%。此外,对比添加和不添加KMnO4的膜层表面的X射线光电子能谱(XPS)结果(图9e和f[47]),说明大部分的MnO
在微弧氧化过程中被还原为MnO。相比之下,棕褐色膜层具有最低的腐蚀电流密度(2.452 × 10-6 A/cm2),表现出优异耐蚀性。电流密度的降低表明表面形成的膜层限制了腐蚀性离子的渗透,有效降低了金属-电解质界面中离子传输。另外,在需要耐腐蚀和装饰的领域如手机壳、笔记本壳、体育用品等,原位自生TiB2/Al基复合材料表面制备的有色薄膜有着良好的应用前景[47]。
5 其他表面处理技术
基于高能量输入、良好冶金结合以及灵活的加工性等优势,激光表面改性正逐渐发展为一种可替代传统表面处理的新方法。比如,Man等[49]采用激光合金化在6061铝合金表面融化NiCrBSi混合粉末,通过调节Ni-Al金属间化合物的细枝晶状结构显著提高了涂层的硬度和耐腐蚀能力。由于添加TiC、SiC、TiB2、SiO2等陶瓷增强体的金属基复合涂层有望获得更高的强度、耐磨性等综合性能,通过激光表面合金化在铝合金表面制备含陶瓷相的金属基复合涂层逐渐成为重要研究方向。Tomida等[50]采用激光合金化在Al-Mg合金表面制备了TiC-Cu复合涂层,通过调节Cu含量和TiC体积分数可使复合涂层的最高硬度达到600 HV,耐磨性是Cu基体的近6倍。为了提高A6061铝合金的耐磨性,Chi等[51]使用铁基合金、B4C和Ti的混合粉末,通过激光合金化的方式在铝合金表面原位制备了TiB2-TiC增强的Fe-Al复合涂层,发现TiC在棒状的TiB2表面发生不均匀形核,2者界面处的失配度仅为1.049%,能够形成良好的结合。同时,复合涂层平均硬度约为520 HV (约为基体的7倍),磨损体积相比基体减少了92.8%,耐磨性得到了显著提高。目前关于采用激光表面合金化制备原位自生TiB2/Al基复合材料表面涂层的研究还未见报道,激光的高能量密度不可避免地会对低熔点的铝合金复合材料基体产生明显的热影响区等不利影响。因此,合理控制参数范围和选取与铝合金复合材料熔点相近的涂层材料体系显得尤为重要。
不同于激光表面合金化的方法,冷喷涂工艺是通过将粉末原料加速到超音速后沉积在基体表层并通过颗粒间的塑性变形而形成机械咬合或者冶金结合并最终形成涂层的过程[52,53]。在这个过程中,颗粒与颗粒以及颗粒与基体的结合是由动能所产生的塑性变形实现。因此,冷喷涂被认为可最大限度地减少或消除涂层残余热应力、氧化和相变[54,55],在提高铝合金表面耐蚀性和耐磨性等领域有着较好应用前景。Meydanoglu等[56]研究发现,在冷喷涂的7075铝合金涂层中通过外加陶瓷颗粒会增加涂层内部塑性变形区域,从而为腐蚀行为提供更多活性位点,增大了复合涂层腐蚀速率。为了尽量避免这种现象,Xie等[57]使用原位TiB2/7075Al复合粉末作为冷喷涂的新原料,在7075铝合金表面制备了含TiB2纳米颗粒增强的复合涂层。但是,经过电化学测试研究发现,相比于冷喷涂的纯7075Al合金涂层,TiB2颗粒增强体与Al基体之间的电偶腐蚀也增大了复合涂层的腐蚀速率。此外,还发现低温退火处理(230℃、6 h)引起的晶格应变和位错湮灭有助于耐蚀性的提升,但高温固溶处理形成的晶粒长大和析出相的形成会显著恶化其耐蚀性。
基于能够有效地细化晶粒、节能高效以及可避免如气孔、开裂、变形等凝固缺陷的优势,搅拌摩擦焊在铝合金上的应用越来越广泛[58,59]。Sharma等[60]采用搅拌摩擦焊的方法对原位自生TiB2/Al基复合材料表面进行加工后,相比铸态的复合材料(晶粒尺寸(16.8 ± 2.4) μm)显著地细化了表面的晶粒尺寸((5.3 ± 2.3) μm);此外,搅拌摩擦焊处理和铸态的TiB2/Al基复合材料均比SiC/Al基复合材料、B/Al基复合材料以及石墨/Al基复合材料更能抵御点蚀的发生。此外,搅拌摩擦焊处理后的样品表面细小的晶粒尺寸和高密度的小角晶界减小了晶间腐蚀形成的倾向,但是膜层表面出现的TiB2和Al3Ti颗粒会削弱其保护作用并在长时间的浸泡实验中发生晶间腐蚀。
高熵合金作为由5种或5种以上元素按照等原子比或近等原子比所组成的简单结构的固溶体材料,被Yeh等[61]和Cantor等[62]发现并问世以来,因其特有的高熵效应、晶格畸变效应、缓慢扩散效应以及鸡尾酒效应等赋予了此类材料优异的物理及机械性能,比如高的强度和硬度、良好的热稳定性、优异的耐磨性和耐腐蚀性等[63,64]。另外,由3到4种组元所构成的中熵合金兼具高熵合金的优势,但相比于高熵合金具有更低的理论密度,应用前景也较为广阔。基于高熵/中熵合金的优异综合性能,关于这2类材料涂层的研究也引起了广大科研工作者的重视[65~67]。目前的研究[68~71]表明,激光表面合金化是制备高熵/中熵合金涂层的主流技术且大部分基体以钢和钛合金为主。铝合金及铝基复合材料表面高熵/中熵合金涂层的报道相对较少。铝合金和此类合金间的高熔点差异是限制它们在铝合金表面应用的难点。不同于主流的高熵/中熵合金涂层制备方法,Zhao等[72]创新性地采用电阻缝加工的方法在6061铝合金表面快速地实现了AlFeCrCoNi高熵合金涂层的制备。该技术不同于激光或电子束等高能量密度的无差别式加热,它是利用粉末间电流的Joule效应(Q = I2Rt,其中Q为Joule热,I为电流,R为粉末电阻,t为作用时间)而自发形成高熵合金涂层, 且制备过程不会对铝合金基体产生明显的热影响区等不利影响。高熵合金涂层在腐蚀性环境中表现出优异的耐磨蚀性。此外,Zhao等[73]进一步将该技术应用于镁合金并大幅度提高了其在不同环境介质下的耐磨性。采用电阻缝加工的方法制备原位自生TiB2/Al基复合材料表面高熵/中熵合金涂层的方法(如图10所示),在原位自生TiB2/Al基复合材料表面高性能的高熵/中熵合金制备有着良好的研究与应用价值。
图10 电阻缝加工法制备原位自生TiB2/铝合金基复合材料表面高/中熵合金涂层示意图
6 总结与展望
过去几十年,有关原位自生TiB2/Al基复合材料表面处理及其腐蚀防护技术已取得了重要进展。主要体现在以下几个方面。(1) 阳极氧化结合稀土转化膜技术很好地封闭了氧化膜的不连续区域和多孔结构,填补氧化层中的孔洞和裂纹;相比于单一阳极氧化膜层,复合膜层的耐蚀性得到了进一步提高;化学沉积和阴极电解沉积稀土膜的形成都是由于阴极区的pH值升高引起的化学或电化学沉积过程,但电解沉积速率快,成膜时间短,更适合工业应用。(2) 低温熔盐沉积技术主要借助AlCl3-NaCl-KCl无机熔盐电沉积,在原位自生TiB2/Al复合材料表面实现致密、均匀和完整铝层的制备,复合材料的耐蚀性能有很大提高,性能接近于纯Al;其次,对TiB2/Al复合材料电沉积的铝层进行阳极氧化封孔处理,可进一步提高复合材料的耐蚀性能且非常接近纯Al阳极氧化封孔试样。(3) 微弧氧化技术在TiB2/Al复合材料表面制备的氧化膜层能与基底形成良好的冶金结合且硬度较高,膜层可极大提高复合材料的耐Cl-侵蚀能力,有效抑制复合材料的阳极过程;但是,脆性的微弧氧化膜层不能经受长时间的空泡腐蚀,膜层中的微裂纹等缺陷也会加剧涂层的剥离;此外,通过合理设计电解液成分,借助微弧氧化工艺可在原位自生TiB2/Al复合材料表面制备兼具耐腐蚀性和装饰性的有色薄膜并有着良好的应用前景。(4) 众多新型表面处理工艺的开发与应用,将有助于提升原位自生TiB2颗粒增强铝基复合材料的腐蚀防护性能,对推动新材料的广泛应用起到重要支撑作用。
为进一步拓宽原位自生TiB2/Al基复合材料的应用范围,未来其表面腐蚀防护技术急需开展的工作包括:(1) 开发适用于原位自生TiB2/Al基复合材料表面处理及腐蚀防护的新技术,制备可与基体形成冶金结合的大厚度(> 400 ?m)、高致密性(致密度> 99%)的涂层,彻底解决TiB2颗粒引起的微电偶腐蚀及自然膜层或氧化膜层不连续的问题,大幅度提高复合材料的耐蚀性;(2) 简化表面改性工艺流程,加快涂层制备速率,降低涂层工艺的成本,加快工业化应用进程;(3) 使用高性能的涂层材料(例如特定成分的高熵合金或中熵合金),赋予原位自生TiB2/Al基复合材料表面兼具优异耐腐蚀性、耐空泡腐蚀性和耐磨性、自润滑等多功能性的涂层;(4) 深入研究并完善原位自生TiB2/Al基复合材料表面处理、腐蚀防护的理论及相应的成套技术,促进原位自生TiB2/Al基复合材料的应用与发展。
参考文献
1 Bhuvaneswari V, Rajeshkumar L, Nimel Sworna Ross K. Influence of bioceramic reinforcement on tribological behaviour of aluminium alloy metal matrix composites: Experimental study and analysis [J]. J. Mater. Res. Technol., 2021, 15: 2802
2 Zhao S L, Zhang H M, Cui Z S, et al. Superplastic behavior of an in-situ TiB2 particle reinforced aluminum matrix composite processed by elliptical cross-section torsion extrusion [J]. Mater. Charact., 2021, 178: 111243
3 Dong B X, Li Q, Wang Z F, et al. Enhancing strength-ductility synergy and mechanisms of Al-based composites by size-tunable in-situ TiB2 particles with specific spatial distribution [J]. Composites, 2021, 217B: 108912
4 Taheri-Nassaj E, Kobashi M, Choh T. Fabrication and analysis of an in situ TiB2Al composite by reactive spontaneous infiltration [J]. Scr. Mater., 1996, 34: 1257
5 Tee K L, Lu L, Lai M O. Synthesis of in situ Al-TiB2 composites using stir cast route [J]. Compos. Struct., 1999, 47: 589
6 Lu L, Lai M O, Chen F L. Al-4 wt% Cu composite reinforced with in-situ TiB2 particles [J]. Acta Mater., 1997, 45: 4297
7 Ma Z Y, Tjong S C. High temperature creep behavior of in-situ TiB2 particulate reinforced copper-based composite [J]. Mater. Sci. Eng., 2000, A284: 70
8 Han Y F, Liu X F, Bian X F. In situ TiB2 particulate reinforced near eutectic Al-Si alloy composites [J]. Composites, 2002, 33A: 439
9 Wang H W. Preparation and application of in-situ ceramic particles reinforced Al matrix composites [J]. Aeronaut. Manuf. Technol., 2021, 64(16): 14
9 王浩伟. 原位自生陶瓷颗粒增强铝基复合材料制备及应用 [J]. 航空制造技术, 2021, 64(16): 14
10 Le Y K. Study on in-situ A356/TiB2 composite and its solid-state phase transformation process [D]. Shanghai: Shanghai Jiao Tong University, 2006
10 乐永康. 原位合成A356/TiB2复合材料及其固态相变过程的研究 [D]. 上海: 上海交通大学, 2006
11 Zhang Y J. High-damping and high-strength cast aluminum-based composite material [D]. Shanghai: Shanghai Jiao Tong University, 2006
11 张亦杰. 高阻尼高强度铸造铝基复合材料 [D]. 上海: 上海交通大学, 2006
12 Chen D. Preparation and properties of in-situ TiB2/7055 aluminum matrix composite [D]. Shanghai: Shanghai Jiao Tong University, 2008
12 陈 东. 原位合成TiB2/7055铝基复合材料的制备与性能 [D]. 上海: 上海交通大学, 2008
13 He C L, Cai Q K. Recent developments in research on corrosion of aluminum metal matrix composites [J]. Mater. Rep., 2003, 17(1):45
13 贺春林, 才庆魁. 铝金属基复合材料的腐蚀研究进展 [J]. 材料导报, 2003, 17(1): 45
14 Nie J F, Wang F, Chen Y Y, et al. Microstructure and corrosion behavior of Al-TiB2/TiC composites processed by hot rolling [J]. Results Phys., 2019, 14: 102471
15 Sun H H, Chen D, Li X F, et al. Electrochemical corrosion behavior of Al-Si alloy composites reinforced with in situ TiB2 particulate [J]. Mater Corros., 2009, 60: 419
16 Huang J, Chen D, Wu Y, et al. Corrosion behavior of in-situ TiB2/7050Al composite in NaCl solution at different pH values [J]. Mater. Res. Express, 2019, 6: 056541
17 Hinton B R W, Arnott D R, Ryan N E. The inhibition of aluminium alloy corrosion by cerous cations [J]. Met. Forum., 1984, 7: 211
18 Mansfeld F, Lin S, Kim K, et al. Pitting and surface modification of SIC/Al [J]. Corros. Sci., 1987, 27: 997.
19 Mansfeld F, Lin S, Kim S, et al. Corrosion protection of Al alloys and Al-based metal matrix composites by chemical passivation [J]. Corrosion, 1989, 45: 615
20 Mansfeld F, Lin S, Kim S, et al. Pitting and passivation of Al alloys and Al-based metal matrix composites [J]. J. Electrochem. Soc., 1990, 137: 78
21 Yu X W, Cao C A, Yao Z M. Application of rare earth metal salts in sealing anodized aluminum alloy [J]. J. Mater. Sci. Lett., 2000, 19: 1907
22 Hu J, Zhao X H, Tang S W, et al. Corrosion protection of aluminum borate whisker reinforced AA6061 composite by cerium oxide-based conversion coating [J]. Surf. Coat. Technol., 2006, 201: 3814
23 Sun H H, Ma N H, Chen D, et al. Fabrication and analysis of anti-corrosion coatings on in-situ TiB2p reinforced aluminum matrix composite [J]. Surf. Coat. Technol., 2008, 203: 329
24 Sun H H, Wang H W, Chen D, et al. Conversion-coating treatment applied to in situ TiB2p reinforced Al-Si-alloy composite forcorrosion protection [J]. Surf. Interface Anal., 2008, 40:1388
25 Dabalà M, Armelao L, Buchberger A, et al. Cerium-based conversion layers on aluminum alloys [J]. Appl. Surf. Sci., 2001, 172: 312
26 Sun H H, Li X F, Chen D, et al. Enhanced corrosion resistance of discontinuous anodic film on in situ TiB2p/A356 composite by cerium electrolysis treatment [J]. J. Mater. Sci., 2009, 44: 786
27 Huang W M. Study on low temperature molten salt deposition of anticorrosive aluminum layer in in-situ TiB2/Al matrix composite material [D]. Shanghai: Shanghai Jiao Tong University, 2013
27 黄文貌. 原位自生TiB2/铝基复合材料低温熔盐沉积防腐铝层研究 [D]. 上海: 上海交通大学, 2013
28 Chen Z P. Special Electroplating Technology [M]. Beijing: Chemical Industry Press, 2004: 1
28 陈祝平. 特种电镀技术 [M]. 北京: 化学工业出版社, 2004: 1
29 Kan H M. Study on low temperature aluminium electrolysis [D]. Shenyang: Northeastern University, 2007
29 阚洪敏. 低温铝电解的研究 [D]. 沈阳: 东北大学, 2007
30 Huang W M, Liu B, Wang M L, et al. Study on the initial electrodeposition behavior of aluminum on TiB2/A356 composite [J]. Mater. Corros., 2014, 65: 502
31 Kunieda M, Katoh R, Mori Y. Rapid prototyping by selective electrodeposition using electrolyte jet [J]. CIRP Ann., 1998, 47: 161
32 Qin X J, Shao G J. Study on the initial electro-deposition behavior of Ni-P alloy [J]. J. Chin. Soc. Corros. Prot., 2004, 24(1): 6
32 秦秀娟, 邵光杰. 电沉积Ni-P合金初期沉积行为的研究 [J]. 中国腐蚀与防护学报, 2004, 24(1): 6
33 Wang C L, Zhou L H, Hu X H, et al. Density functional theory on characteristics of TiB2(0001) surface [J]. Chin. J. Nonferrous Met., 2008, 18: 145
33 王春雷, 周理海, 胡雪慧 等. TiB2(0001)表面性质的密度泛函理论 [J]. 中国有色金属学报, 2008, 18: 145
34 Yang J, Chen Q J, Lin Z D, et al. An experimental study: Heteroepitaxial growth of diamond thin films on silicon (111) surface [J]. Prog. Nat. Sci., 1995, 5: 233
35 Plitzko J, R?sler M, Nickel K G. Heteroepitaxial growth of diamond thin films on silicon: Information transfer by epitaxial tilting [J]. Diam. Relat. Mater., 1997, 6: 935
36 Shao G J, Chen L, Wang F Y, et al. Study on the initial electrodeposition behavior of Ni-P alloys [J]. Mater. Chem. Phys., 2005, 90: 327
37 Huang W M, Zhou C, Liu B, et al. Improvement in the corrosion resistance of TiB2/A356 composite by molten-salt electrodeposition and anodization [J]. Surf. Coat. Technol., 2012, 206: 4988
38 Zhang S, Zhang C H, Zhang L T, et al. Cavitation erosion and microstructure of laser surface cladding MMC of SiCp on AA6061 aluminium alloy [J]. J. Mater. Eng., 2002, (2): 47
38 张 松, 张春华, 张录廷 等. 铝合金表面激光熔覆SiC颗粒增强表层金属基复合材料的组织及空泡腐蚀性能 [J]. 材料工程, 2002, (2): 47
39 Yang Z, Tian J M. Cavitation erosion of structural ceramics [J]. J. Funct. Mater., 2003, 34: 200
39 杨 政, 田杰谟. 结构陶瓷的空蚀性研究 [J]. 功能材料, 2003, 34: 200
40 Sah S P, Tsuji E, Aoki Y, et al. Cathodic pulse breakdown of anodic films on aluminium in alkaline silicate electrolyte—Understanding the role of cathodic half-cycle in AC plasma electrolytic oxidation [J]. Corros. Sci., 2012, 55: 90
41 Wang D Y, Dong Q, Chen C Z, et al. Recent progress of micro-arc oxidation technique [J]. J. Chin. Ceram. Soc., 2005, 33: 1133
41 王德云, 东 青, 陈传忠 等. 微弧氧化技术的研究进展 [J]. 硅酸盐学报, 2005, 33: 1133
42 Xue W B, Jin Q, Zhu Q Z, et al. Anti-corrosion microarc oxidation coatings on SiCp/AZ31 magnesium matrix composite [J]. J. Alloys Compd., 2009, 482: 208
43 Zhang H B. Study on the preparation and corrosion resistance of the micro-arc oxidation film of in-situ TiB2/A201 composite [D]. Shanghai: Shanghai Jiao Tong University, 2017
43 张弘斌. 原位自生TiB2/A201复合材料微弧氧化膜层的制备及其耐蚀性能研究 [D]. 上海: 上海交通大学, 2017
44 Wang L Q, Zhou J S, Liang J, et al. Thermal control coatings on magnesium alloys prepared by plasma electrolytic oxidation [J]. Appl. Surf. Sci., 2013, 280: 151
45 Han J X, Cheng Y L, Tu W B, et al. The black and white coatings on Ti-6Al-4V alloy or pure titanium by plasma electrolytic oxidation in concentrated silicate electrolyte [J]. Appl. Surf. Sci., 2018, 428: 684
46 Jiang Y L, Wang J K, Hu B, et al. Preparation of a novel yellow ceramic coating on Ti alloys by plasma electrolytic oxidation [J]. Surf. Coat. Technol., 2016, 307: 1297
47 Xia C J, Huang J, Tao J M, et al. The preparation and properties of the brown film by micro-arc oxidized on in-situ TiB2/7050Al matrix composites [J]. Coatings, 2020, 10: 615
48 Li K, Li W F, Zhang G G, et al. Preparation of black PEO layers on Al-Si alloy and the colorizing analysis [J]. Vacuum, 2015, 111: 131
49 Man H C, Zhang S, Yue T M, et al. Laser surface alloying of NiCrSiB on Al6061 aluminium alloy [J]. Surf. Coat. Technol., 2001, 148: 136
50 Tomida S, Nakata K, Saji S, et al. Formation of metal matrix composite layer on aluminum alloy with TiC-Cu powder by laser surface alloying process [J]. Surf. Coat. Technol., 2001, 142-144: 585
51 Chi Y M, Gong G H, Zhao L J, et al. In-situ TiB2-TiC reinforced Fe-Al composite coating on 6061 aluminum alloy by laser surface modification [J]. J. Mater. Process. Technol., 2021, 294: 117107
52 Rokni M R, Nutt S R, Widener C A, et al. Review of relationship between particle deformation, coating microstructure, and properties in high-pressure cold spray [J]. J. Therm. Spray Technol., 2017, 26: 1308
53 Raoelison R N, Xie Y, Sapanathan T, et al. Cold gas dynamic spray technology: A comprehensive review of processing conditions for various technological developments till to date [J]. Addit. Manuf., 2018, 19: 134
54 Li W Y, Zhang C, Guo X P, et al. Study on impact fusion at particle interfaces and its effect on coating microstructure in cold spraying [J]. Appl. Surf. Sci., 2007, 254: 517
55 Xie X L, Chen C Y, Ji G, et al. A novel approach for fabricating a CNT/AlSi composite with the self-aligned nacre-like architecture by cold spraying [J]. Nano Mater. Sci., 2019, 1: 137
56 Meydanoglu O, Jodoin B, Kayali E S. Microstructure, mechanical properties and corrosion performance of 7075 Al matrix ceramic particle reinforced composite coatings produced by the cold gas dynamic spraying process [J]. Surf. Coat. Technol., 2013, 235: 108
57 Xie X L, Hosni B, Chen C Y, et al. Corrosion behavior of cold sprayed 7075Al composite coating reinforced with TiB2 nanoparticles [J]. Surf. Coat. Technol., 2020, 404: 126460
58 De P S, Mishra R S. Friction stir welding of precipitation strengthened aluminium alloys: Scope and challenges [J]. Sci. Technol. Weld. Joining, 2011, 16: 343
59 Nandan R, DebRoy T, Bhadeshia H K D H. Recent advances in friction-stir welding—Process, weldment structure and properties [J]. Prog. Mater. Sci., 2008, 53: 980
60 Sharma R, Singh A K, Arora A, et al. Effect of friction stir processing on corrosion of Al-TiB2 based composite in 3.5 wt.% sodium chloride solution [J]. Trans. Nonferrous Met. Soc. China, 2019, 29: 1383
61 Yeh J W, Chen S K, Lin S J, et al. Nanostructured high‐entropy alloys with multiple principal elements: Novel alloy design concepts and outcomes [J]. Adv. Eng. Mater., 2004, 6: 299
62 Cantor B, Chang I T H, Knight P, et al. Microstructural development in equiatomic multicomponent alloys [J]. Mater. Sci. Eng., 2004, A375-377: 213
63 Zhang Y, Zuo T T, Tang Z, et al. Microstructures and properties of high-entropy alloys [J]. Prog. Mater. Sci., 2014, 61: 1
64 George E P, Raabe D, Ritchie R O. High-entropy alloys [J]. Nat. Rev. Mater., 2019, 4: 515
65 Li J C, Huang Y X, Meng X C, et al. A review on high entropy alloys coatings: Fabrication processes and property assessment [J]. Adv. Eng. Mater., 2019, 21: 1900343
66 Li W, Liu P, Liaw P K, Microstructures and properties of high-entropy alloy films and coatings : A review [J]. Mater. Res. Lett., 2018, 6: 199
67 Yan X H, Li J S, Zhang W R, et al. A brief review of high-entropy films [J]. Mater. Chem. Phys., 2018, 210: 12
68 Lu J B, Wang B F, Qiu X K, et al. Microstructure evolution and properties of CrCuFe x NiTi high-entropy alloy coating by plasma cladding on Q235 [J]. Surf. Coat. Technol., 2017, 328: 313
69 Li X F, Feng Y H, Liu B, et al. Influence of NbC particles on microstructure and mechanical properties of AlCoCrFeNi high-entropy alloy coatings prepared by laser cladding [J]. J. Alloys Compd., 2019, 788: 485
70 Tüten N, Canadinc D, Motallebzadeh A, et al. Microstructure and tribological properties of TiTaHfNbZr high entropy alloy coatings deposited on Ti-6Al-4V substrates [J]. Intermetallics, 2019, 105: 99
71 Tian Y, Shen Y F, Lu C Y, et al. Microstructures and oxidation behavior of Al-CrMnFeCoMoW composite coatings on Ti-6Al-4V alloy substrate via high-energy mechanical alloying method [J]. J. Alloys Compd., 2019, 779: 456
72 Zhao D C, Yamaguchi T, Shu J F, et al. Rapid fabrication of the continuous AlFeCrCoNi high entropy alloy coating on aluminum alloy by resistance seam welding [J]. Appl. Surf. Sci., 2020, 517: 145980
73 Zhao D C, Yamaguchi T, Tusbasa D, et al. Fabrication and friction properties of the AlFeCrCo medium-entropy alloy coatings on magnesium alloy [J]. Mater. Des., 2020, 193: 108872
免责声明:本网站所转载的文字、图片与视频资料版权归原创作者所有,如果涉及侵权,请第一时间联系本网删除。
-
标签: 原位自生TiB2/Al基复合材料, 表面处理, 腐蚀防护, 涂层
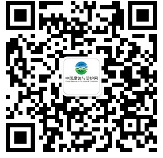
官方微信
《腐蚀与防护网电子期刊》征订启事
- 投稿联系:编辑部
- 电话:010-62316606-806
- 邮箱:fsfhzy666@163.com
- 腐蚀与防护网官方QQ群:140808414