青铜器是中国文物宝藏中一颗光彩夺目的明珠,现存大部分青铜器经过漫长时间的地下埋藏,受到不同程度的腐蚀,关于其腐蚀过程和机制已经有大量研究报道,且有多种腐蚀模型。另有大量文献研究了含氯环境对青铜合金的腐蚀影响,其表面腐蚀产物主要为铜的氧化物和氯化物。大量文献利用现存青铜器分析推导了青铜的腐蚀过程,而直接利用青铜材料研究青铜器腐蚀行为的报道较少。考古发现的青铜器大多为铅锡青铜,本工作选用仿古工艺浇铸了高锡高铅青铜材料,对其在酸性土壤模拟溶液中的腐蚀行为进行了研究。
试验方法
试验用青铜材料采用仿古工艺浇铸而成,主要含金属铜(66.35%)、锡(17.81%)和铅(15.84%) ,属于高锡高铅青铜,厚度为3 mm。
浸泡腐蚀试验和XRD分析用试样尺寸为20 mm×10 mm×3 mm,表面用砂纸(400~1000号)逐渐打磨并除油后,在无水乙醇中进行超声波清洗,烘干称量后置于干燥器内保存备用。试验前,再次称量试样。用于显微组织观察和初期腐蚀萌生试样的尺寸为10 mm×10 mm×3 mm,选取一个10 mm×10 mm的面作为观察面,用砂纸(600~5000号)逐级打磨后用1.5 μm抛光膏抛光后,采用10%三氯化铁盐酸酒精溶液侵蚀试样。电化学阻抗试验用试样尺寸为10 mm×10 mm×3 mm,保留一个10 mm×10 mm工作面,背面焊接铜导线,使用环氧树脂将非工作面绝缘封闭。进行阻抗测试前将工作面用砂纸(600~1000号)逐级打磨,随后用去离子水和酒精清洗吹干后备用。
用Leica DM2700M型金相显微镜观察试样的显微组织,利用SmartLab SE型X射线衍射仪分析试样的腐蚀产物。采用场发射扫描电子显微镜及配套能谱仪对试样腐蚀形貌及腐蚀产物成分进行观察及表征。
采用去离子水和分析纯试剂配制江西鹰潭地区酸性土壤模拟溶液,提高了试验溶液中的NaCl含量,以加速腐蚀。采用NaOH调节溶液pH为5.0,溶液组成为:0.157 g/L NaCl,0.0493 g/L CaCl2·2H2O,0.0476 g/L Na2SO4,0.1353 g/L MgSO4·7H2O,0.0982 g/L KNO3,0.0506 g/L NaHCO3。
初期腐蚀萌生试验过程如下:将试样置于溶液中分别腐蚀30分钟和60分钟后,观察试样表面的腐蚀情况。
连续浸泡腐蚀试验过程如下:将试样悬挂浸泡于溶液中10,30,60,180天后进行腐蚀质量损失测量和腐蚀产物观察分析。其中,腐蚀速率按v=(W0-W1)/ST计算,其中,W0为原始试样质量,W1为腐蚀后试样的质量,S为试样表面积,T为浸泡时间。
电化学阻抗测试在Corr Test CS310电化学工作站上进行,采用常规三电极体系,电解液为配制的江西鹰潭地区酸性土壤模拟溶液。工作电极为电化学试样,参比电极为饱和氯化钾甘汞电极(SCE),辅助电极为铂电极。待试样在试验溶液中的开路电位稳定后进行EIS测试,频率为0.1 Hz~100 kHz,电压为10 mV。所有测试均在室温下进行。用ZSimpWin软件对EIS谱进行拟合。
显微组织
图1 试样的显微组织
由图1可见:试样由α相(白亮区域)、(α+δ)共析相(灰色区域)和游离态Pb相(黑色颗粒)组成。α相整体较为平整均匀,(α+δ)共析相中共析α相细小无规则,被共析δ相包裹。游离态Pb由于本身性质的原因在抛光腐蚀过程中脱落或溶解,位于形貌图中空洞处。
腐蚀速率
(a) 平均腐蚀失重曲线
(b) 腐蚀失重速率曲线
图2 腐蚀浸泡试验结果
由图2可见:在试验溶液中,材料腐蚀质量损失整体呈上升趋势,腐蚀速率随浸泡时间延长整体呈减小趋势,当浸泡时间为10天时,试样的腐蚀速率最大(1.6034 g/m2·d),当浸泡时间为10~30天时,腐蚀速率迅速减小,浸泡时间为30~180天时,腐蚀速率趋于平缓。这可能是因为浸泡初期试样表面发生腐蚀后形成的腐蚀产物覆盖于试样表面阻碍了腐蚀介质接触基体,并且随浸泡时间延长溶液中的氧逐渐消耗,也在一定程度上对腐蚀速率产生影响。
电化学阻抗谱
(a) Nyquist图
(b) Bode图
图3 试样在试验溶液中浸泡不同时间后的EIS谱
由图3可见:在试验溶液中浸泡不同时间后,Nyquist图表现出相似的电容回路。这意味着不同腐蚀时间下的腐蚀机制相同,但腐蚀速率可能会有所不同。另外,在Bode图中观察到一个相位角峰值,它对应于电荷转移和双电层电容的时间常数。图3中插图为拟合EIS谱的等效电路,其中Rs表示欧姆溶液电阻,Rct对应于电荷转移电阻,Qdl表示试样与溶液之间存在的双电层电容,W表示韦伯(Warburg)阻抗。Qdl是一个恒相位元件(CPE),可以解释双电容层的非理想行为,它的阻抗(ZCPE)表达式如下:
ZCPE = Y0-1 (jω)-n
式中,Y0是与频率无关的导纳,j是-1的平方根,ω是角频率,n是CPE的指数。表1给出了EIS谱等效电路中各元件的拟合参数。chi-squared(χ2)值均在10-3这一量级,表明该等效电路可行,且质量较好。
表1 EIS拟合结果
由表1可见:导纳Qdl总体上随腐蚀时间延长而减小,表明试样与电解液界面面积增大,指数n同样随腐蚀时间延长总体呈减小趋势,这两个参数的变化与试样在腐蚀过程中表面粗糙度的增大相关。通常,Rct与腐蚀速率成反比,表中Rct在腐蚀0~10天过程中随腐蚀时间延长而减小,即腐蚀速率随腐蚀时间延长而增大,Rct在腐蚀10~180天过程中随腐蚀时间延长而增大,表明腐蚀速率随腐蚀时间延长而减小。W值与材料耐蚀性相关,W越大材料耐蚀性越好,表中W值的变化趋势与Rct的类似。Rct与W结果表明试样在试验溶液中的腐蚀速率变化过程如下:试验0~10天,腐蚀速率随试验时间延长而增加,试验10~180天,腐蚀速率随试验时间延长而减少。EIS结果与浸泡试验结果吻合。
腐蚀形貌及腐蚀产物
(a) 整体表面形貌
(b) 局部表面形貌
(c) 局部腐蚀形貌
(d) EDS分析结果
图4 试样在试验溶液中浸泡30分钟后的表面腐蚀形貌及EDS分析结果
由图4可见:经过30分钟腐蚀后,试样表面部分区域发生腐蚀,腐蚀产物为颗粒状和针片状;图4b中Pb颗粒表面及周围出现絮状腐蚀产物;图4c中Pb颗粒处出现较深腐蚀坑,周围存在颗粒状和针片状产物。α相和(α+δ)相未发生明显的腐蚀溶解。对图中不同特征的腐蚀形貌进行EDS点扫描分析,结果表明腐蚀产物中含有Pb,O,Cu,Cl等元素,Pb含量最高,很明显Pb颗粒发生腐蚀溶解并且腐蚀产物呈扩散分布。
(a) 整体腐蚀形貌
(b) 针状腐蚀产物
(c) 絮状腐蚀产物
(d) EDS图谱
图5 试样在试验溶液中浸泡3小时后的表面腐蚀形貌及EDS分析结果
由图5可见:在试验溶液中腐蚀3小时后,试样表面分布了大量针状腐蚀产物和絮状腐蚀产物;针状腐蚀产物的EDS结果表明其中包含Pb,O,Cl三种元素,且Pb含量最高;絮状产物的主要元素组成有Pb,Cu,Sn,O,且Pb含量最高。
图6 在试验溶液中浸泡不同时间(0,10,30,60,180天)后试样的表面宏观形貌
由图6可见:在酸性土壤模拟溶液中浸泡后,试样表面几乎被白色腐蚀产物全面覆盖,该腐蚀产物结构较为疏松。且白色腐蚀产物下方材料表面也发生颜色和形貌的改变, Pb颗粒的位置出现明显的腐蚀坑。腐蚀初期,试样表面变化最大,随着浸泡时间的延长,试样表面腐蚀产物无明显变化。
更多内容请点击: 阅读原文
免责声明:本网站所转载的文字、图片与视频资料版权归原创作者所有,如果涉及侵权,请第一时间联系本网删除。
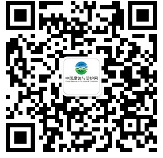
官方微信
《腐蚀与防护网电子期刊》征订启事
- 投稿联系:编辑部
- 电话:010-62316606-806
- 邮箱:fsfhzy666@163.com
- 腐蚀与防护网官方QQ群:140808414