经过多年大规模滚动式开采,合水油田地层压力亏空,无法满足油田开采需求。为了及时弥补地层压力,实现油田高产稳产,近年来陆续进行了注水处理,注水井占比高达29%,增产效果显著。
然而,随着原油含水率增加,地面生产设施腐蚀环境恶化,管线及设备频繁出现了结垢与腐蚀问题。这不仅会导致管线或设备因腐蚀失效而停产,造成严重的经济损失,更会引发油气泄漏,造成环境污染甚至人员伤害事故。
以某采出水处理站为例,尽管站内除油沉降罐采用玻璃钢涂层进行防护,但在服役一段时间后内壁玻璃钢涂层发生脱落,内部布水管线腐蚀结垢严重,上部分水管甚至因结垢而堵塞,如下图所示。
图1 除油沉降罐内构件的腐蚀结垢情况
图2 除油沉降罐内布水管线腐蚀结垢情况
由图2可见:管线内壁靠近金属基体表面附着了多层硬质结垢物,且和基体金属结合紧密。清除垢层后,未在金属基体表面发现明显的局部腐蚀,但从管线截面环向壁厚来看,该管线环向壁厚分布不均,7点钟位置存在明显减薄,说明在长期服役过程中管线发生了严重的腐蚀减薄。这不仅缩短了设备的运行周期,还可能给设备的安全生产带来隐患。
因此,中国石油天然气股份有限公司长庆油田分公司第十二采油厂和安科工程技术研究院(北京)有限公司的技术人员通过一系列分析手段,对腐蚀结垢原因进行了深入剖析,并探讨了有效防止或减轻水处理系统腐蚀结垢的配套措施,以期为油田正常生产提供理论支撑。
水质分析
采用瑞士万通881离子色谱、岛津UV-2600紫外可见分光光度仪及化学滴定法测试水样中Na+、K+、Ca2+、Mg2+、Sr+、Ba2+、Fe2+等阳离子与Cl-、SO42-、HCO3-等阴离子的含量。由分析结果可知:前端处理站1和2采出水中含有较多Sr2+、Ba2+与SO42-、HCO3-,混合后Ba2+、SO42-、HCO3-含量大幅下降,说明介质混合后形成了BaSO4与BaCO3结垢物。
利用HD1000溶解氧测试仪,对水处理站内主要生产节点位置水质中的溶解氧含量进行了测试;参照标准SY/T 5329-1994《碎屑岩油藏注水水质推荐指标及分析方法》,采用细菌测试瓶,利用绝迹稀释法进行细菌含量测试。由测试结果可知:生产介质水相中溶解氧含量为1.00~1.53mg/L,细菌含量较少,仅检测出了9个/mL腐生菌(TGB);未检测到硫酸盐还原菌(SRB)与铁细菌(IB),这可能是因为除油沉降罐中添加了杀菌剂,导致注入水及后续的产出系统中细菌含量较低。
综上可知,来自于不同层位的生产介质混合后会发生结垢,结垢物的沉积会导致垢下腐蚀。此外,较高含量的溶解氧势必会导致地面生产管线及设备发生氧腐蚀,存在较高的氧腐蚀风险。
腐蚀产物分析
借助X′Pert PRO粉末X射线衍射仪对布水管线中沉积的结垢物进行物相分析。由分析结果可见:除油沉降罐内主要的结垢物为BaSO4、BaCO3,还含有少量SrSO4。
利用TESCAN VEGA3扫描电子显微镜与配套的能谱仪对布水管线内壁腐蚀产物的微观形貌与化学成分进行表征。由分析结果可见:布水管线内壁结垢物结构紧密,存在分层现象,主要元素为Fe、Ba、O、S,推测结垢物中主要成分为BaSO4与铁氧化物。机械清除垢层后,管道内壁表面主要元素为Fe、O。
由此可知,布水管线内主要的堵塞物为BaSO4、BaCO3结垢物与铁氧化物,导致除油沉降罐及内构件腐蚀的主要原因为垢下腐蚀与氧腐蚀。
腐蚀结垢原因
由上述测试可知,来自于不同前端处理站的采出水矿化度高,溶解氧含量也较高,具有较强的腐蚀性,会发生电化学腐蚀,形成FeOOH、Fe2O3、Fe3O4等铁氧化物。
同时,由于采出水中含有成垢离子,如Ba2+、Sr2+、SO42-与HCO3-等,含不同成垢离子的采出液混合后,成垢离子相互补充,很快达到BaSO4与BaCO3的溶度积,形成过饱和溶液。
当过饱和度较高时,成垢离子对会聚集形成较大的粒子,溶液中开始出现一些不易溶解的、体积较大的BaSO4与BaCO3固体成核粒子,即所谓的晶核。所形成的BaSO4与BaCO3晶核会吸附在凹凸不平的管道表面,并以其为中心,在过饱和度的驱动下不断长大,成为肉眼可见的晶体。
由于水处理系统是比较复杂的多相体系,含有较多的悬浮物、腐蚀产物等杂质且管道表面较粗糙,为垢的生长提供了足够的相界面和杂质。
因此,析出的BaSO4与BaCO3会以悬浮物、腐蚀产物等为载体,快速形核,并吸附在除油沉降罐等设备内部附件表面生长。在晶核形核与吸附、长大的循环作用下,除油沉降罐等设备内部附件表面形成结垢层。结垢物一旦在金属管线或设备表面形成,由于其疏松程度与分布情况不同,导致采出水介质在金属表面的流动和介质扩散受到限制,造成结垢致密区域金属表面介质化学成分与其他区域有很大差别,两者之间形成电位差,发生微电偶腐蚀,促进局部区域腐蚀加速,形成局部腐蚀坑。
一旦局部腐蚀坑形成,受垢层掩蔽效应的影响,腐蚀坑内反应形成的Fe2+富集。为保证电位平衡,外部溶液中离子半径较小的Cl-会通过垢层扩散至蚀坑内部,形成FeCl2。FeCl2易发生水解,形成H+,导致局部酸化,pH下降。H+的增加会促进腐蚀坑内金属的活性溶解,加速腐蚀。腐蚀进一步会产生更多的Fe2+,导致腐蚀坑内富集更多的Fe2+,促使更多的Cl-迁入,引起pH降低,即通常所说的“酸化自催化作用”。在酸化自催化作用下,腐蚀坑会不断发展、长大,直至管线与设备发生腐蚀穿孔。
由此可知,导致采出水处理站原油沉降罐腐蚀主要是由于具有较高结垢倾向的高矿化采出水与高浓度溶解氧的存在。
腐蚀防治措施
针对水处理系统的腐蚀问题,结合现场生产情况,可通过添加适宜的药剂进行腐蚀防治。根据油田在用药剂的性能评价结果,选取了SW-188阻垢剂、KEW-227缓蚀剂、HZG-30杀菌剂与Na2SO3除氧剂作为处理药剂,通过加药罐连续向除油沉降罐中加注药剂,各药剂加入量如下:140mg/L SW-188、60mg/L KEW-227、30mg/L HZG-30杀菌剂,30mg/L Na2SO3。
针对该加药方案,在除油沉降罐内安装挂环进行加药效果的现场评价试验,试验周期30天。
(a)加药前 (b)加药后
图5 加药前后试样的宏观腐蚀形貌
由图5可见:加药前,试样表面大部分区域附着有结垢物,内外表面均有连片大腐蚀坑、腐蚀严重,均匀腐蚀速率为1.01mm/a;加药后挂环试样表面结垢物减少,腐蚀坑面积减少,均匀腐蚀速率大幅降低,降至0.15mm/a。
由此可知,通过连续加药,可有效控制除油沉降罐内构件及后续水处理设备、工艺管线的腐蚀结垢进程,从而降低水处理系统因腐蚀结垢导致的停产、维修频次,保障油气生产的安全、稳定运行。
结论
(1) 合水油田采出水腐蚀性强,水质略偏酸性(pH为6.5~7.0),矿化度高,含有较多的Ba2+、Sr2+、SO42-与HCO3-等成垢离子,存在较高的结垢风险与氧腐蚀风险。
(2) 导致采出水处理站除油沉降罐发生腐蚀的主要原因为高矿化采出水与高浓度溶解氧的存在,导致除油罐内壁与分水管等内附件发生垢下腐蚀与氧腐蚀。
(3) 向水处理系统中的除油沉降罐管内连续加注阻垢剂、缓蚀剂、除氧剂及杀菌剂,可有效缓解水处理系统设备及管线的腐蚀结垢,降低因腐蚀结垢导致的停产、维修频次,保障油气生产的安全。
免责声明:本网站所转载的文字、图片与视频资料版权归原创作者所有,如果涉及侵权,请第一时间联系本网删除。
相关文章
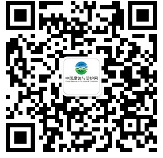
官方微信
《中国腐蚀与防护网电子期刊》征订启事
- 投稿联系:编辑部
- 电话:010-62316606-806
- 邮箱:fsfhzy666@163.com
- 中国腐蚀与防护网官方QQ群:140808414
点击排行
PPT新闻
“海洋金属”——钛合金在舰船的
点击数:7607
腐蚀与“海上丝绸之路”
点击数:6107